Forging Services
Frigate uses the latest Forged techniques to draw on decades of experience and mechanized innovation. From a single piece to large quantities, we ensure your parts are manufactured on time.
What We Offer
Our Forging Offerings
Partner with Frigate’s forging experts, who understand your unique needs and challenges and have deep industry knowledge.
Get Your Quote Now
- Instant Quotation
- On-Time Delivery
- Affordable Cost
Frigate's Forging Expertise
Custom Forging Solutions
We are dedicated custom manufacturers and offer our customers the best-forged components. Our technical expertise guarantees the best microstructure, a longer lifespan, increased strength, and less material waste while providing cost-effective pricing.
At Frigate, forging components for severe service applications is our speciality. Whether small steel forgings for off-highway vehicles, defense, and agricultural equipment, or aerospace components in high-temperature alloys, we cover it all.


Forging services improve material strength with precise tolerances and minimal waste.
Our Clients






























Our Business Verticals
Defense
Aerospace
Construction
Railroad
Oil & Gas
Automotive
Agriculture
Energy Sector
Integrated Manufacturing Solutions
We prepare metal billets and blanks using hot and cold pre-forming processes. This helps us shape metals perfectly before forging. We also use advanced techniques to keep the temperature even during forging, which reduces stress and improves quality.

Approved to the highest standards
Our forging furnaces are approved to the highest specifications and standards, meeting all the demands of the aerospace and defense sectors. This allows us to manufacture various materials, ensuring our forging portfolio is second to none, ranging from basic carbon steels and super alloys to high-integrity nickel alloys.

Advanced Forging Capabilities for Unique Designs
We hold a wide range of superior-quality materials and can design bespoke grades of components to meet different and demanding specifications to satisfy your project needs. With our unrivaled range of forging equipment, we cannot limit what we can make. We thrive on manufacturing complex solutions that others cannot.

Supply Chain and Logistics Management
We manage our supply chain efficiently to reduce lead times and costs. Our global network ensures we get high-quality materials from reliable sources worldwide. We use just-in-time inventory systems to keep everything running smoothly.

Our Forging Process






Key Compliance for Injection Molding Services
The metal is heated to specific temperatures to optimize its plastic deformation characteristics and refine its microstructure, ensuring high mechanical strength in the final product.
Custom dies are designed with advanced CAD/CAM systems to achieve tight tolerances and accommodate complex geometries, ensuring consistent quality and repeatability.
Forging equipment, such as hydraulic or mechanical presses, applies controlled, high-force impacts to shape the material while maintaining its grain flow for superior strength.
The process aligns the material's grain structure with the part's shape, significantly enhancing directional strength and fatigue resistance.
Components are cooled in controlled environments to manage thermal gradients, minimizing residual stresses and preventing structural distortions.
Heat treatments like annealing, quenching, or tempering are applied to improve hardness, toughness, or wear resistance, tailored to the application requirements.
Forging Materials
We use diverse high-performance materials to deliver superior forging solutions for various industries’ specific demands. Our expertise in material science ensures that each component shows exceptional performance and durability.
Carbon steel is heated and hammered or pressed into the desired shape. It is known for its strength and is used in tools and structural components. It has properties like high strength and wear resistance.
Alloy Steel involves heating and forging steel mixed with chromium, nickel, and vanadium. This enhances properties like toughness and resistance to wear and corrosion. This material consists of enhanced mechanical properties and improved hardenability.
Tool steel is forged to produce dies, molds, and cutting tools. It requires precise temperature control to maintain its cutting edge. Tool steel is also highly hard, wear resistant, and can hold a sharp edge.
Aluminum is lighter and requires lower forging temperatures. It is used in aerospace, automotive, and lightweight structural applications. It also has a good strength-to-weight ratio and excellent corrosion resistance.
Stainless steel is forged for its corrosion resistance and is commonly used in medical devices, food processing equipment, and marine applications. Its properties include corrosion resistance, strength, and aesthetic appeal.
Duplex steel, a mix of austenitic and ferritic stainless steels, is forged for high strength and corrosion resistance and is often used in chemical processing and offshore applications. It is high in strength, has excellent corrosion resistance, and is weldable.
Copper is forged for electrical components, plumbing, and decorative items. It requires careful control to avoid oxidation. Copper has various properties, such as excellent electrical conductivity, corrosion resistance, and flexibility.
Brass, an alloy of copper and zinc, is forged for fittings, valves, and decorative hardware. It is known for its workability and aesthetic qualities.
Titanium is forged under precise conditions to produce strong, lightweight components in aerospace, medical implants, and high-performance applications. This material's properties include a high strength-to-weight ratio, corrosion resistance, and biocompatibility.
Frigate's Approach
Innovative Forging Solutions for Custom and Complex Requirements
Our seasoned and skilled team at Frigate ensures that every forged component meets exact specifications. We understand that the initial phases of product development require meticulous attention to detail, and we deliver exactly that.
Every industry has unique requirements; not all projects fit into one standard mold. We excel in crafting forged products tailored to your individual needs. Whether you’re looking for a specialized part, a limited edition run, or a product with distinct characteristics, we are the right choice for your next project.

Compliance for Forging Services
Frigate ensures its forging services align with globally recognized certifications and regulatory standards. Our processes are built on rigorous quality control, material traceability, and adherence to technical specifications, ensuring metallurgical integrity and mechanical reliability.
Key Compliance Standards with Certification Numbers
Establishes a structured framework for maintaining process control and traceability, ensuring consistency in forging tolerances, defect minimization, and adherence to customer specifications.
Defines quality management requirements for aerospace applications, including stringent control of material properties, dimensional accuracy, and traceability in high-performance forged components.
Certifies compliance in specialized processes such as heat treatment and surface enhancement, ensuring consistent metallurgical properties, hardness, and material performance for aerospace and defense forgings.
Sets requirements for environmental management, ensuring that forging operations, such as furnace emissions and waste handling, meet global sustainability standards without compromising metallurgical quality.
Ensures restricted use of hazardous substances in alloys and coatings, maintaining material compliance for environmentally sensitive applications, particularly in electronics and precision machinery.
Specifies technical requirements for steel forgings, covering chemical composition, mechanical properties, non-destructive testing, and grain structure uniformity.
Regulates the safe operation of forging presses and equipment, mandating safeguards, regular inspections, and personnel training to reduce the risk of workplace accidents.
Sets technical requirements for quality management systems in automotive forging, emphasizing process capability, defect prevention, and material conformance for safety-critical components.
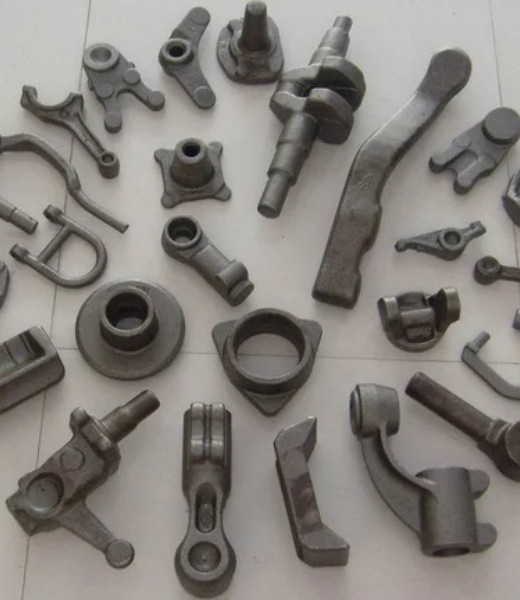
Tolerance for Forging Services
Varies by part size, die wear, and forging process (open or closed die).
Determined by material flow and die precision during compression.
Critical for shafts and circular parts; adjusted for material properties.
Influenced by cooling rate and die alignment.
Depends on die surface and material; secondary machining may improve it.
Managed through strict material control and forging cavity filling.
Ensures proper geometry of inclined or angled surfaces.
Critical for ensuring functional fit of holes, slots, and keyways.
Controlled by uniform material flow during the forging operation.
Consistent with design specifications to prevent stress concentrations.
Precision maintained for components requiring shafts or bearings.
Critical for preventing fatigue and ensuring smooth transitions.
Required for easy removal of forged parts from dies; varies by geometry.
Ensures alignment between internal and external features.
Maintains even spacing between parallel faces for load distribution.
Tolerance for slots, grooves, and cavities.
Considered for high-temperature forgings to manage post-cooling changes.
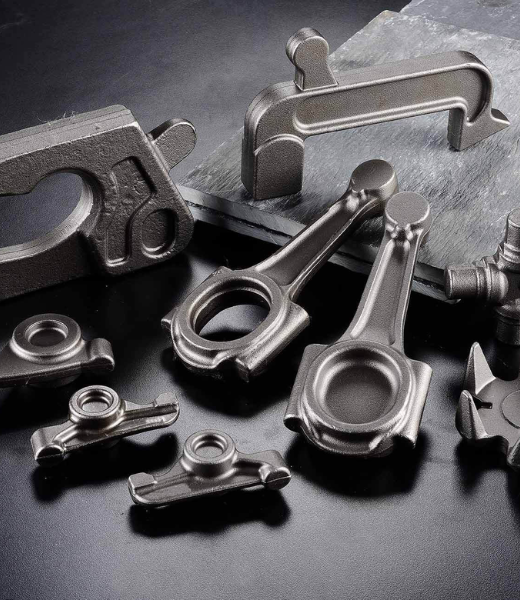
Quality Testing Standards for Forging Services
Confirms proper grain flow for enhanced mechanical properties.
Measures stress distribution within the component.
Quantifies surface texture for adherence to finish specifications.
Detects internal voids and gas porosity in the material.
Evaluates resistance to crack propagation under stress.
Simulates friction and wear conditions to assess durability.
Measures heat transfer capabilities of forged materials.
Detects surface and near-surface discontinuities in ferromagnetic materials.
Identifies surface and subsurface cracks in conductive materials.
Determines stiffness and elasticity of the material.
Simulates high-temperature deformation to predict forging behavior.
Identifies localized variations in chemical composition.
Measures the depth of carbon loss from the surface.
Assesses the material’s suitability for post-forging welding.
Evaluates susceptibility to cracking due to trapped hydrogen.
Measures electrical properties for conductivity-specific applications.
Determines oxide film uniformity for corrosion resistance.
- Real Impact
Words from Clients
See how global OEMs and sourcing heads describe their experience with our scalable execution.
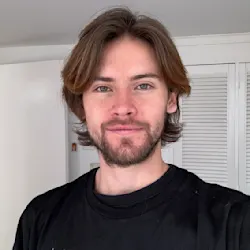
“Quick turnaround and solid quality.”
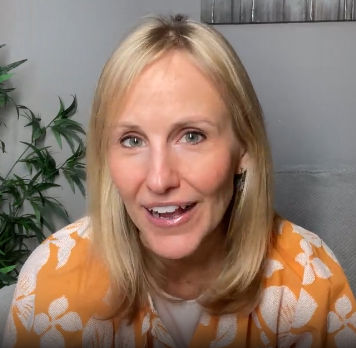
“The instant quote tool saved us time, and the parts were spot-on. Highly recommend Frigate!”
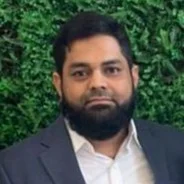
“I would strongly recommend Frigate to anyone who wants to do Rapid Prototyping, and take their ideas to manufacturing. One firm doing all kinds of Product Development!”
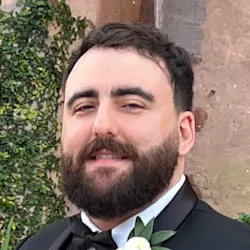
“Great service, fair price, and the parts worked perfectly in our assembly.”
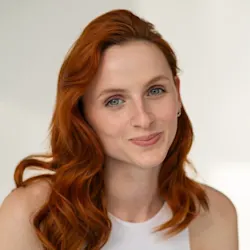
“Top-notch machining and fast shipping. Very satisfied with the results.”
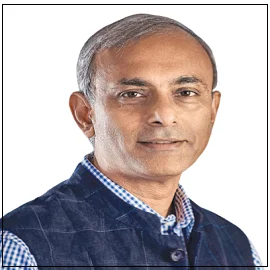
“The next disruption is happening in Prototyping & Manufacturing on-demand and Frigate is leading the way! I personally believe the Frigate's way of IIOT enabled cloud platform with Al.”
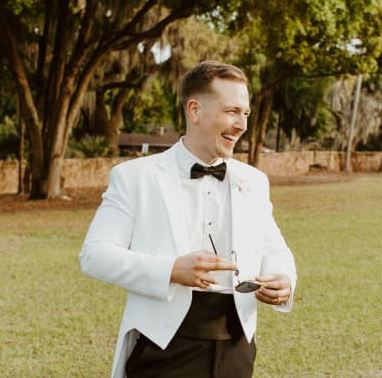
“Frigate delivered high-quality parts at a competitive price. The instant quote tool is a huge plus for us!”

“We appreciate the precision and quality of the machined components in the recent delivery—they meet our specifications perfectly and demonstrate Frigate’s capability for excellent workmanship.”
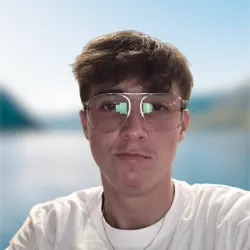
“Flawless execution from quote to delivery.”

“I am absolutely happy to work with supplier like Frigate who were quite proactive & result oriented . Frigate has high willingness team who has strong know how & their passion towards the products & process were absolutely thrilling.”
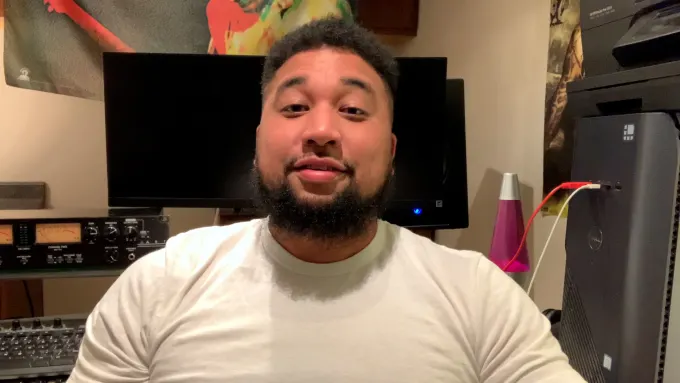
“The precision on these parts is impressive, and they arrived ahead of schedule. Frigate’s process really stands out!”
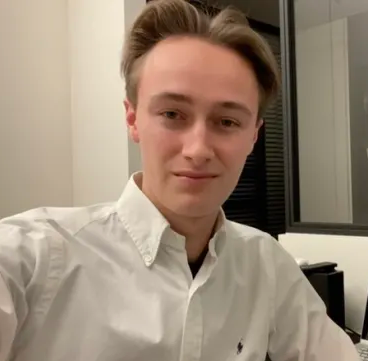
“Parts were exactly as spec’d, and the instant quote made budgeting a breeze.”
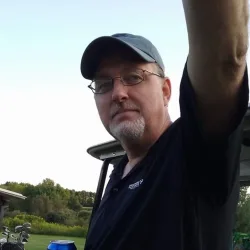
“Good value for the money.”
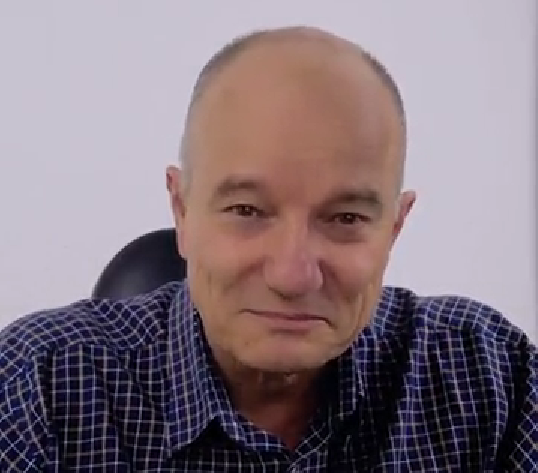
“The finish was perfect, and the team was easy to work with.”

“Working with Frigate has been great. Their proactive, results-driven approach and expertise shine through in every project. It's been a pleasure collaborating with them.”

"We are highly satisfied with the timely delivery and quality of the MIG Welding Cable from Frigate. Their attention to detail, secure packaging, and quick responsiveness stood out. We confidently recommend Frigate Engineering Services Pvt. Ltd. as a reliable manufacturing partner."
Having Doubts? Our FAQ
Check all our Frequently Asked Question
We manage residual stresses and distortion in forged parts by using special heat treatments and precise cooling methods. After forging, we carefully heat the metal and then cool it down in a controlled way. This helps to relieve stresses and prevent the parts from bending or warping. We also use advanced machines to measure and adjust the parts, ensuring they stay in the right shape and are strong and reliable.
We use special high-strength metals like titanium, aluminum alloys, and superalloys for aerospace-grade forgings. These materials are very strong and lightweight, which makes them perfect for aerospace components.
We can forge a wide range of standard parts, like gears and brackets, and custom parts designed just for you. Whether you need a common shape or something unique and complex, we have the tools and expertise to make it.
At Frigate, we meet the high-volume demands of automotive manufacturing by using powerful machines that can make many parts quickly and accurately. We have big presses that can handle large amounts of metal and use robots to move and shape the metal fast.
We use detailed planning and advanced tools for complex shapes and multi-step processes. We often use special dies and perform several steps to carefully shape the metal into the right form, allowing us to create detailed and intricate parts exactly as needed.
Manufacturing Capability/Capacity
Ferrous casting
Mold size(max): 1m X 1m
Weight Range: 1 KG ~ 30 KGS
Mold size(max): 1.5m X 1.5m
Weight Range: 30 KG ~ 150 KGS
Mold size(max): 3m X 3m
Weight Range: 100 KG ~ 1000 KGS
Mold size(max): 500 MM X 500 MM
Weight Range: 0.250 KG ~ 20 KGS
Mold size(max): 500 MM X 500 MM
Weight Range: 0.100 KG X 20 KGS
Non-ferrous casting
Capacity: 5000 MT/a
Range of weight: 100 gm to 20 KGS
Mold size(max): 1 M X 1 M
Weight Range: 0.5 KG X 50 KGS
Mold size(max): 1 M X 1 M
Weight Range: 0.5 KG X 50 KGS











Forging
Capacity: 20,000 Tons per Annum
Range of weight: 300 KG to 1 Ton
Hammering: 5 Ton
Range of weight: 0.2 KG to 200 KGS
Hammering: 1600 Ton Hydraulic press
Ring size: 350 MM OD to 3000 MM OD
Range of weight: 15 KGS to 3200 KGS
Materials
Carbon Steel, Stainless Steel (AUSTENITE), Alloy Steel, Stainless Steel (MARTENSITE), etc.

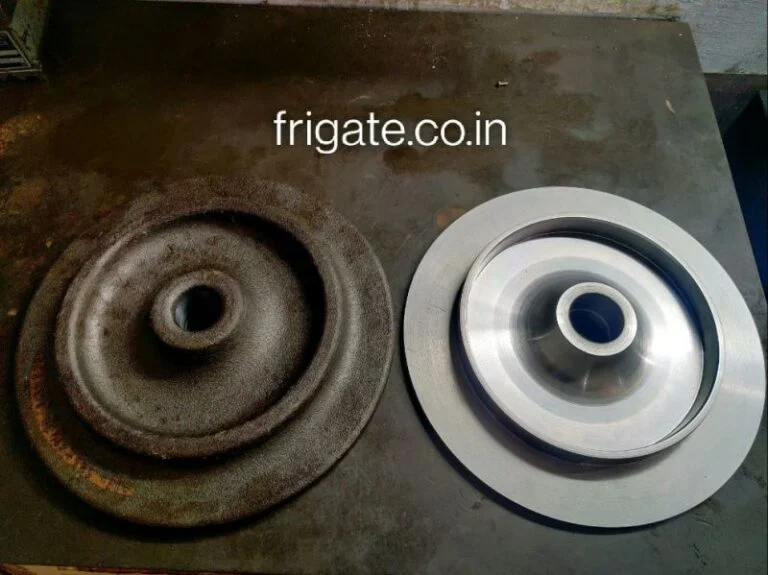
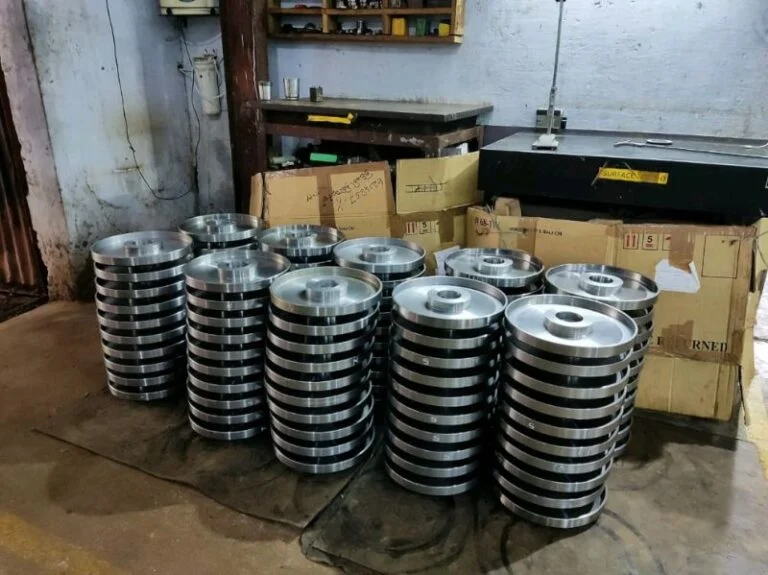


Machining
1 to 1000 MM
1 to 1000 MM
1 to 1000 MM
Materials
Steel, Aluminum, Brass, Copper, Titanium, Nickel Alloys, Tungsten Carbide, etc.







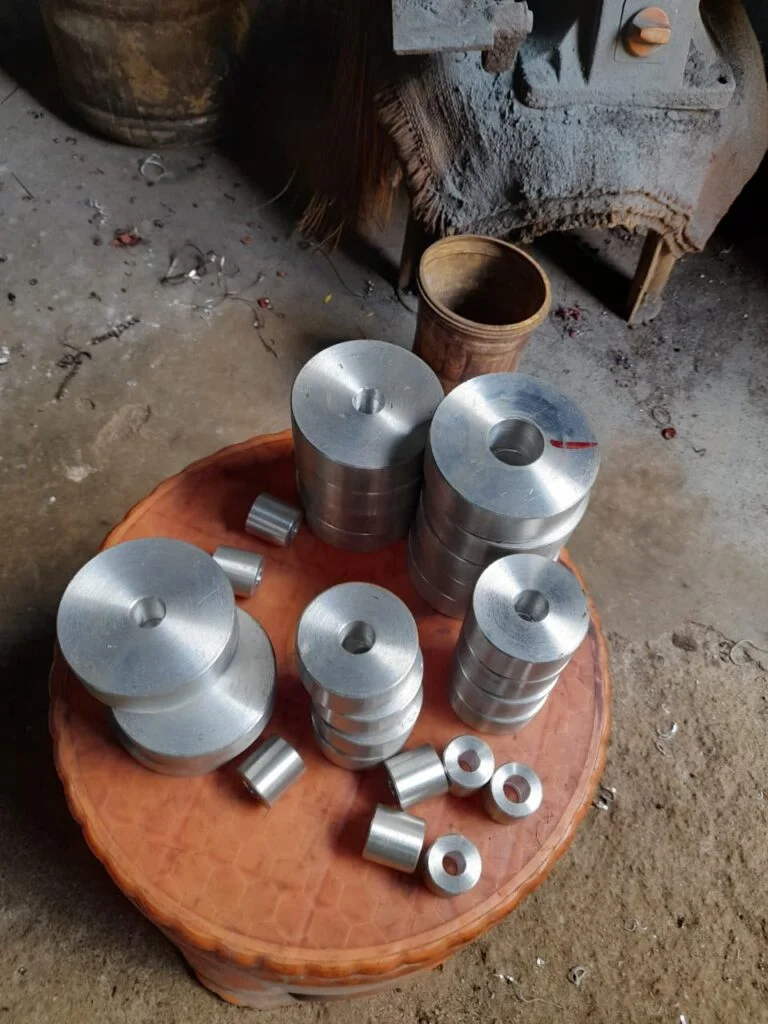


















Plastics
Materials
1250 X 1250 MM
Within 10 microns
Engineering Plastics, Polyethylene, Polypropylene, Polyvinyl chloride, Polyethylene terephthalate, Bioplastics, etc.
Rubber
Materials
Natural rubber, Styrene-Butadiene Rubber, Nitrile Butadiene Rubber, Silicone Rubber, Fluorocarbon Rubber, Recycled Rubber, etc.














Heavy Fabrication
24000 MT/a
Materials
CS / MS, Alloy steel, Stainless Steel, etc.
Sheet Metal Fabrication
0.8 to 25 mm
Materials
Mild Steel, Stainless Steel, Aluminum, Brass, Copper, etc.















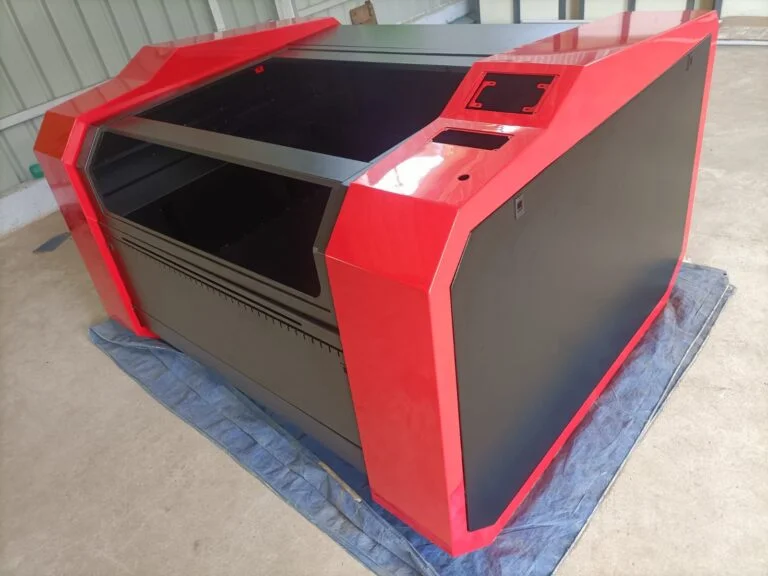
We'd love to Manufacture for you!
Submit the form below and our representative will be in touch shortly.
LOCATIONS
Global Sales Office
818, Preakness lane, Coppell, Texas, USA – 75019
Registered Office
10-A, First Floor, V.V Complex, Prakash Nagar, Thiruverumbur, Trichy-620013, Tamil Nadu, India.
Operations Office
9/1, Poonthottam Nagar, Ramanandha Nagar, Saravanampatti, Coimbatore-641035, Tamil Nadu, India. ㅤ
Other Locations
- Bhilai
- Chennai
- Texas, USA