Prototype Molding Services
Prototype molding at Frigate utilizes advanced injection molding techniques to produce precise and functional parts for rapid prototyping. Our process ensures high dimensional accuracy and consistency, enabling efficient design iterations and accelerated product development cycles.
Our Clients





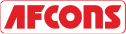

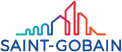


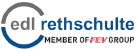

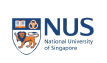
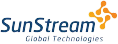

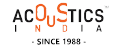




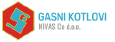
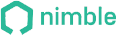
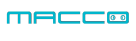












Advantages of Prototype Molding with Frigate
Rapid Turnaround Time
Prototype molding significantly reduces lead times by enabling quick part production and facilitating faster testing and design validation processes.
High Precision
This method provides exceptional dimensional accuracy, ensuring prototypes closely match final production specifications, which aids in effective product development.
Material Versatility
Prototype molding allows for the use of various materials, enabling the simulation of different properties and functionalities for diverse applications.
Cost-Effective Iterations
By allowing multiple design iterations at lower costs, prototype molding enables efficient exploration of design alternatives before full-scale production begins.
Optimizing Prototyping Precision and Efficiency
Frigate’s prototype molding services utilize the same advanced technologies, materials, and finishing options as those employed in full-scale plastic injection molding. This ensures consistent part quality without the constraints of minimum production runs. Project managers and engineers collaborate to assess each project’s specific needs, providing technical guidance to achieve optimal cost efficiency and faster lead times. The process is designed to maintain precision and flexibility, allowing for a seamless transition from prototyping to full production.

Get Your Quote Now
- Instant Quotation
- On-Time Delivery
- Affordable Cost
Our Prototype Molding Process






The initial step involves analyzing the 3D CAD model to ensure the design is suitable for molding and identifying potential issues with part geometry or manufacturability.
Materials are chosen for their mechanical, thermal, and chemical properties based on project requirements, ensuring the prototype meets functional specifications.
A prototype mold, typically made from aluminum or soft steel, is manufactured using CNC machining. This temporary mold is designed to handle limited production runs.
Molten plastic is injected into the mold under high pressure, filling the cavity and forming the desired part shape. Cooling allows the plastic to solidify.
Once molded, the part is inspected thoroughly to verify dimensional accuracy, surface finish, and structural integrity.
Design adjustments or material changes are made if necessary based on testing and performance evaluation, optimizing the part before moving to full-scale production.
Prototype Molding Materials
Prototype molding employs high-performance materials for accurate component replication. These materials ensure optimal performance and precise dimensional stability.
ABS is a thermoplastic known for its impact resistance and toughness. It's commonly used for parts that require strength and durability, such as enclosures and automotive components.
Polypropylene offers excellent chemical resistance and flexibility, making it ideal for parts that must withstand harsh environments or repeated flexing, such as containers and hinges.
Polycarbonate provides high strength and transparency, and it is often used in applications requiring optical clarity and impact resistance, such as lenses and protective covers.
Nylon is valued for its strength, wear resistance, and low friction, making it suitable for gears, bearings, and mechanical components exposed to movement and stress.
TPEs are flexible, rubber-like materials that offer both durability and elasticity. These are used for prototypes that simulate soft-touch parts like grips or gaskets.
Polyethylene has excellent chemical resistance and moisture barriers, making it ideal for consumer goods, packaging, and containers.
Tailored Prototype Molding Solutions
Custom prototype molding provides high-precision parts tailored to specific project needs. This service supports industries like automotive, aerospace, and medical devices by replicating production-quality parts for testing and development. With versatile materials and finishes, the process enables faster iterations, reduced costs, and informed decision-making before full-scale production.

Compliance for Prototype Molding Services
We leverage advanced simulation tools for precise material selection, ensuring compliance with environmental and safety regulations. Prototypes are tested to validate material properties, structural integrity, and dimensional accuracy. Our processes align with critical certifications to mitigate risks and ensure performance under real-world conditions. We monitor each phase, from design to production, maintaining compliance with regulatory frameworks. Frigate integrates data-driven insights to refine molding techniques, enhance sustainability, and precisely meet customer specifications.
Ensures rigorous quality management and streamlining prototype production to meet global industry standards.
Guarantees non-toxic, compliant prototype materials, ensuring environmental safety and regulatory alignment.
Certifies safe materials, eliminating risks of hazardous substances in compliance with EU regulations.
Meets stringent FDA standards for medical devices, ensuring safety, reliability, and precision in medical molding.
Validates flammability and safety of electronic components, ensuring compliance with safety standards for high-risk industries.
Confirms ethical sourcing practices, supporting responsible material procurement and compliance with global standards.

Tolerance for Prototype Molding Services
Accounts for material contraction during cooling, crucial for precise fit and function.
Ensures dimensional stability across varying temperatures, critical for high-precision parts.
Controls warping or distortion due to internal stresses and differential cooling.
Ensures precise placement of gates for optimal material flow and part integrity.
Guarantees alignment of mold cores during injection to maintain feature accuracy.
Maintains accurate corner radii, crucial for part strength and stress distribution.
Ensures uniformity in material properties across batches, critical for high-performance applications.
Controls torsional distortion, maintaining the integrity of geometrically complex parts.
Regulates material distribution within parts, optimizing strength and weight for specific use cases.
Specifies fine surface textures for applications requiring precision finishes or coatings.
Applies to features like threaded holes, locating pins, and small intricate geometries.
Ensures minimal ejection mark presence while maintaining structural integrity.
Critical for precision in multi-cavity molds, ensuring accurate replication of parts.
Controls the distance the material flows inside the mold, ensuring uniform fill.
Ensures easy ejection and minimizes damage to molded parts in high-precision designs.

Quality Testing Standards for Prototype Molding Services
Measures material deformation over time under constant stress, essential for high-performance applications.
Evaluates the material's stiffness, critical for parts subject to bending or stretching.
Assesses the ability of the prototype to maintain shape under a specified load over time.
Analyzes the microstructure of materials to assess grain structure, porosity, and inclusions.
Evaluates material performance under environmental conditions like chemicals, temperature, and humidity.
Measures the material's resistance to tension and its ability to return to its original shape.
Assesses the electrical insulating properties of materials under high-voltage conditions.
Tests material behavior under alternating high-temperature cycles to simulate extreme operating environments.
Determines the material's ability to absorb moisture, which affects stability and mechanical properties.
Tests the prototype’s ability to withstand repetitive mechanical vibrations, important for automotive or aerospace parts.
Measures the hardness of flexible materials and coatings, critical for parts subject to wear.
Determines the stress at which a material begins to permanently deform, critical for load-bearing components.
Evaluates the material’s resistance to the passage of gases, important for packaging or sealing applications.
Measures the ease of flow of molten polymer, providing insight into the material's processing characteristics.
Assesses the ability of the material to return to its original form after being deformed, important for shock-absorbing parts.
Evaluates the strength of adhesive bonds in prototype assemblies, ensuring reliable material cohesion.
Overcoming Aerospace Production Barriers
Aerospace manufacturing demands precision, lightweight materials, and rapid innovation, yet traditional methods can slow development cycles. Prototype molding accelerates component design by delivering highly accurate, functional parts that mimic final production quality. This process allows aerospace engineers to test and refine complex geometries and material properties before full-scale production. Using advanced thermoplastics and composites, the service ensures components meet strict weight, strength, and thermal resistance requirements, addressing key industry challenges in performance and efficiency.




Industries We Serve
- Solid Progress
Our Manufacturing metrics
Frigate brings stability, control, and predictable performance to your sourcing operations through a structured multi-vendor system.
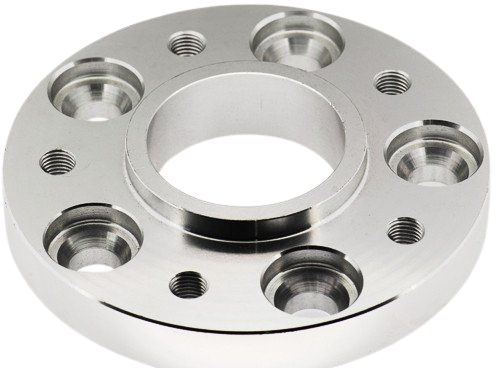
2.8X
Sourcing Cycle Speed
Frigate’s pre-qualified network shortens decision time between RFQ and PO placement.
94%
On-Time Delivery Rate
Structured planning windows and logistics-linked schedules improve project-level delivery reliability.
4X
Multi-Part Consolidation
We enable part family batching across suppliers to reduce fragmentation.
22%
Quality Rejection Rate
Multi-level quality checks and fixed inspection plans lower non-conformities.
30%
Procurement Costs
Optimized supplier negotiations and bulk order strategies reduce your overall sourcing expenses.
20%
Manual Processing Time
Automation of sourcing and supplier management significantly reduces time spent on manual tasks.
Bridging Concepts to Production
Frigate provides comprehensive solutions to transform concepts into tangible products. In addition to services like CNC machining and 3D printing for prototyping, prototype molding is available for those looking to elevate their prototyping efforts. This service facilitates the transition from initial prototypes to validated products ready for full-scale production runs, ensuring high precision and quality throughout development.

Get Clarity with our Manufacturing Insights
- Real Impact
Words from Clients
See how global OEMs and sourcing heads describe their experience with our scalable execution.
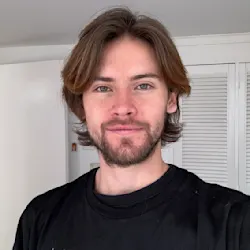
“Quick turnaround and solid quality.”
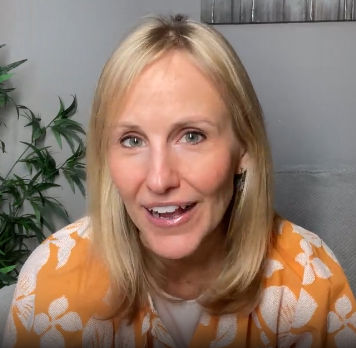
“The instant quote tool saved us time, and the parts were spot-on. Highly recommend Frigate!”
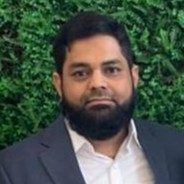
“I would strongly recommend Frigate to anyone who wants to do Rapid Prototyping, and take their ideas to manufacturing. One firm doing all kinds of Product Development!”
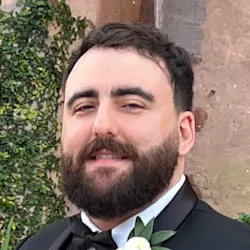
“Great service, fair price, and the parts worked perfectly in our assembly.”
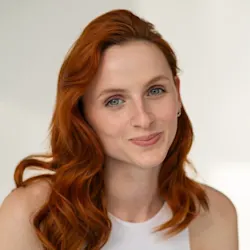
“Top-notch machining and fast shipping. Very satisfied with the results.”
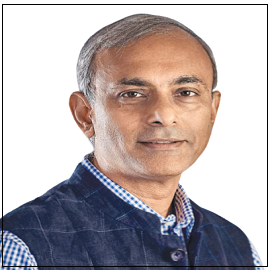
“The next disruption is happening in Prototyping & Manufacturing on-demand and Frigate is leading the way! I personally believe the Frigate's way of IIOT enabled cloud platform with Al.”
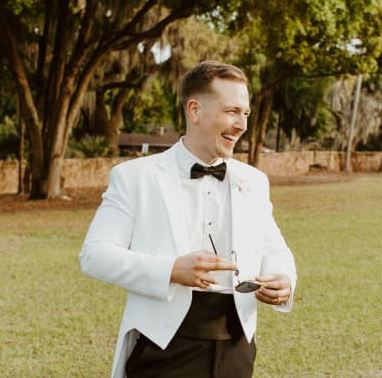
“Frigate delivered high-quality parts at a competitive price. The instant quote tool is a huge plus for us!”

“We appreciate the precision and quality of the machined components in the recent delivery—they meet our specifications perfectly and demonstrate Frigate’s capability for excellent workmanship.”
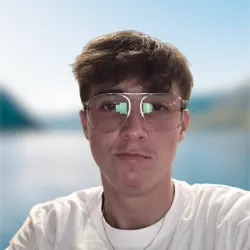
“Flawless execution from quote to delivery.”

“I am absolutely happy to work with supplier like Frigate who were quite proactive & result oriented . Frigate has high willingness team who has strong know how & their passion towards the products & process were absolutely thrilling.”
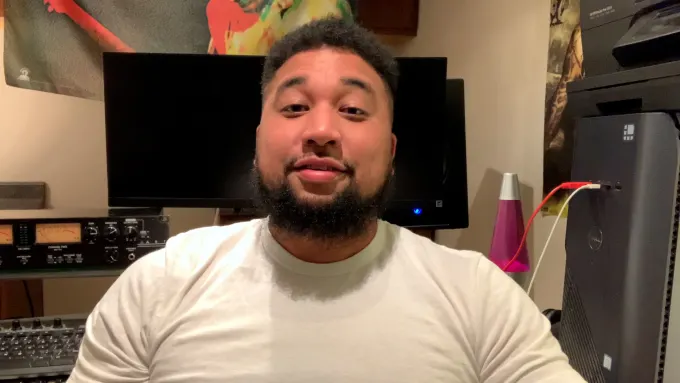
“The precision on these parts is impressive, and they arrived ahead of schedule. Frigate’s process really stands out!”
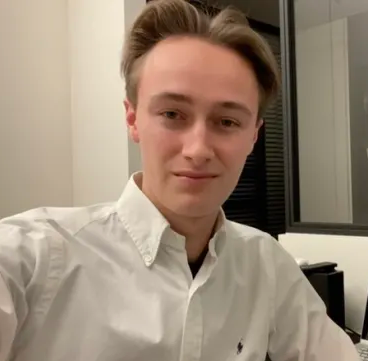
“Parts were exactly as spec’d, and the instant quote made budgeting a breeze.”
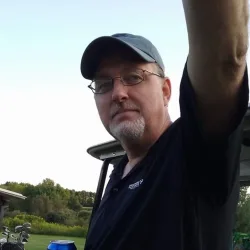
“Good value for the money.”
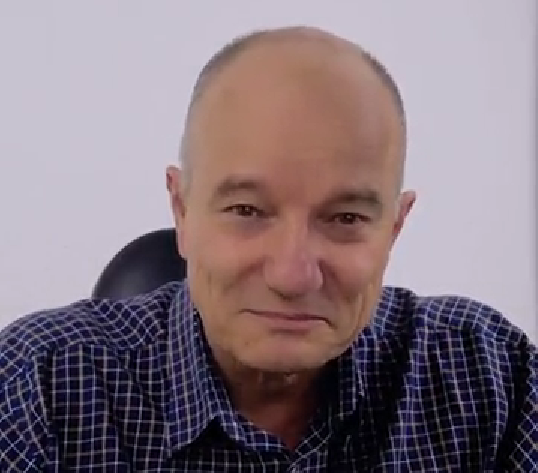
“The finish was perfect, and the team was easy to work with.”

“Working with Frigate has been great. Their proactive, results-driven approach and expertise shine through in every project. It's been a pleasure collaborating with them.”

"We are highly satisfied with the timely delivery and quality of the MIG Welding Cable from Frigate. Their attention to detail, secure packaging, and quick responsiveness stood out. We confidently recommend Frigate Engineering Services Pvt. Ltd. as a reliable manufacturing partner."
Having Doubts? Our FAQ
Check all our Frequently Asked Question
The selected material significantly influences the final part's mechanical properties, surface finish, and thermal stability. Different materials, such as ABS, nylon, or polycarbonate, provide varying strength, flexibility, and heat resistance levels, impacting the prototype's suitability for testing and functionality.
Key design factors include wall thickness, draft angles, and the presence of undercuts. Ensuring appropriate wall thickness promotes even cooling and strength, while draft angles facilitate easier mold release. Avoiding complex undercuts minimizes tooling challenges and production delays.
Adjusting mold design, material choice, and injection speed can optimize cooling time. Implementing cooling channels in the mold and selecting materials with favorable thermal properties can enhance heat dissipation, reducing cycle times and improving production efficiency.
The mold material determines the prototype's durability, precision, and cost-effectiveness. Common options like aluminum are suitable for lower-volume runs due to faster production and lower costs. At the same time, steel molds are preferred for high-volume production due to their longevity and resistance to wear.
Implementing iterative design changes involves using computer-aided design (CAD) software to quickly modify models and adjust mold designs. Rapid prototyping techniques allow for the swift production of updated prototypes, facilitating testing and refinement without significant delays in the overall development process.
We'd love to Manufacture for you!
Submit the form below and our representative will be in touch shortly.
LOCATIONS
Global Sales Office
818, Preakness lane, Coppell, Texas, USA – 75019
Registered Office
10-A, First Floor, V.V Complex, Prakash Nagar, Thiruverumbur, Trichy-620013, Tamil Nadu, India.
Operations Office
9/1, Poonthottam Nagar, Ramanandha Nagar, Saravanampatti, Coimbatore-641035, Tamil Nadu, India. ㅤ
Other Locations
- Bhilai
- Chennai
- Texas, USA