Overmolding Services
Frigate specializes in overmolding, combining multiple materials for enhanced functionality. Our advanced techniques ensure precise bonding and optimal performance across industries.
Our Clients





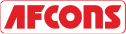

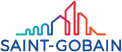


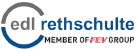

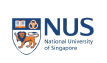
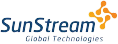

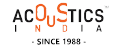




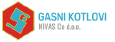
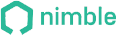
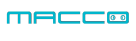












Advantages of Overmolding Services
Improved Durability
Overmolding enhances product durability by combining materials with different properties, offering better resistance to wear and environmental conditions.
Enhanced Ergonomics
Overmolding provides soft-touch surfaces, improving grip and comfort in products like handles and reducing user strain during operation.
Cost Efficiency
By integrating multiple functions into a single part, overmolding reduces assembly steps, lowering production costs and minimizing material waste.
Superior Sealing
Overmolding ensures a tight seal between materials, offering enhanced protection against water, dust, and other environmental contaminants.
Enhance Durability and Functionality with Custom Overmolding
Custom overmolding can solve these challenges by combining multiple materials into a seamless component. This process improves product durability, enhances ergonomics, and ensures superior sealing, providing better protection against water, dust, and harsh environments. By reducing the number of components and simplifying assembly, custom overmolding also helps lower production costs. With Frigate’s expertise, you can achieve high-performance, cost-efficient solutions tailored to meet specific industry needs.

Get Your Quote Now
- Instant Quotation
- On-Time Delivery
- Affordable Cost
Our Overmolding Process






Choose the base and overmold materials based on desired properties, such as flexibility, strength, and durability.
Create a precise mold with cavities for the base and overmold materials, ensuring accurate material placement.
Inject the base material into the mold, forming the core of the part. This material serves as the foundation for the overmolding process.
In some cases, preheat the base material to ensure optimal adhesion when the overmold material is applied.
Inject the overmolding material into the mold surrounding the base material. The overmold material bonds to the base for improved functionality.
Allow the part to cool and solidify, then eject it from the mold. The final product combines both materials, offering enhanced performance and durability.
Overmolding Materials
Overmolding combines multiple materials to improve product performance and functionality. It enhances flexibility, durability, and chemical resistance for specific applications.
ABS (Acrylonitrile Butadiene Styrene) offers high-impact resistance and dimensional stability. It bonds well with elastomers to create durable, flexible parts used in automotive and electronic housings.
Polycarbonate provides excellent impact strength and heat resistance. Overmolded with elastomers, it’s ideal for automotive housings and electrical connectors, offering high performance under stress.
TPE combines thermoplastic processability with rubber elasticity. It provides flexibility and comfort for soft-touch products commonly used in power tools, medical devices, and electronics.
Polyurethane offers high abrasion resistance and tensile strength. It’s used for seals, gaskets, and bushings, especially in industrial and automotive parts, enduring harsh conditions.
Polyethylene has excellent chemical resistance and low friction. It’s ideal for overmolding in medical devices, outdoor equipment, and applications needing durability in extreme environments.
Nylon provides high strength and wear resistance. It is often used in overmolding for structural integrity in automotive components and industrial machinery.
TPV blends rubber elasticity with thermoplastic processability. It's ideal for seals, gaskets, and vibration damping in automotive and industrial applications.
Silicone offers high-temperature stability and chemical resistance. It’s perfect for overmolding medical devices, food equipment, and automotive engine parts.
PTFE is resistant to high temperatures and chemicals. It’s used in high-performance applications like chemical processing equipment and electrical insulators.
Polypropylene is lightweight and chemically resistant. Overmolded with elastomers, it’s ideal for automotive parts requiring a balance of strength and flexibility.
Minimizing Surface Defects for Superior Finish
Surface imperfections like wrinkles, scratches, or tool marks can occur in pneumatic metal forming due to high-pressure contact between the material and the tool. Frigate minimizes these defects by controlling forming pressure, material flow, and tool design. Advanced tooling and process precision reduce surface issues, and secondary processes, such as polishing or grinding, are employed to refine the finish when necessary.

Compliance for Overmolding Services
Overmolding compliance integrates advanced material science, precision engineering, and regulatory adherence. It ensures polymer-metal bonding under complex geometries and extreme conditions. Thermal expansion rates, shrinkage factors, and adhesion properties are tightly controlled. Certifications validate the integrity of critical processes for aerospace, automotive, and medical industries.
Ensures advanced quality systems for traceable, repeatable processes, minimizing variability in multi-material overmolding.
Certifies biocompatible overmolding for medical devices, meeting stringent sterility and durability requirements.
Prohibits hazardous substances, ensuring overmolding in electronics meets environmental and health standards.
Regulates chemical exposure in plastics, prohibiting harmful additives and ensuring worker and consumer safety.
Regulates materials for overmolding in direct-contact pharmaceutical and food applications, ensuring safety under operational stress.
Establishes tensile and elongation properties of over-molded materials, optimizing performance under load.
Mandates secure production controls for overmolded parts in defense and aerospace, preventing unauthorized access.

Tolerance for Overmolding Services
Precise control of bonding layer thickness ensures uniform adhesion and optimal stress distribution.
Minimizes residual material at the gate for improved aesthetics and reduced secondary finishing.
Maintains alignment between overmolded features and base components for rotational applications.
Controls excess material at parting lines to prevent interference or post-molding cleanup.
Ensures precise positioning of metal or polymer inserts within the overmolded part.
Regulates mold temperature for consistent material flow and dimensional stability.
Monitors pressure consistency to avoid voids or weak bonding in overmolded areas.
Controls fiber alignment in reinforced polymers to maintain structural integrity and anisotropic properties.
Achieves specific surface textures critical for sealing, aesthetics, or friction control.
Precisely controls layer thickness to achieve desired mechanical and thermal properties.
Ensures uniform cooling to minimize warping and maintain dimensional accuracy.
Limits internal stresses within the overmolded part to prevent deformation or premature failure.
Controls mismatches in thermal expansion between materials to prevent delamination under thermal cycling.

Quality Testing Standards for Overmolding Services
Measures heat transfer efficiency through overmold materials for thermal management in electronic parts.
Evaluates polymer flow properties during molding to optimize processing conditions and prevent defects.
Identifies internal voids or inconsistencies within the overmolded component without destructive testing.
Tests susceptibility to cracking under combined stress and chemical exposure for long-term durability.
Assesses the ability of overmolded parts to endure vibrational forces in automotive or aerospace environments.
Determines electrical insulating properties of overmold materials under various frequencies and voltages.
Measures expansion rates of overmold materials to ensure compatibility with substrate during thermal cycling.
Tests the resistance of overmold materials to gas transmission for applications like sealed electronics.
Assesses material resistance to UV radiation to prevent degradation in outdoor applications.
Evaluates performance under repeated stress to predict long-term reliability of overmolded components.
Determines temperature at which overmold materials deform under a specified load.
Verifies mechanical integrity at weld lines formed during molding processes.
Detects and mitigates gas entrapment during molding, ensuring part consistency and adhesion quality.
Evaluates molecular-level bonding uniformity between overmold and substrate materials.
Streamlining Production of High-Performance Medical Parts
Medical component manufacturers often face challenges in achieving the perfect balance between durability, comfort, and functionality. Overmolding addresses these issues by combining rigid substrates with soft, biocompatible materials in a single part. This technique ensures superior grip, enhanced ergonomics, and reduced need for additional assembly. It also improves component durability, providing resistance to wear, chemicals, and environmental stress. Overmolding allows for more compact, efficient designs, increasing the reliability of medical devices and instruments.






Industries We Serve
- Solid Progress
Our Manufacturing metrics
Frigate brings stability, control, and predictable performance to your sourcing operations through a structured multi-vendor system.
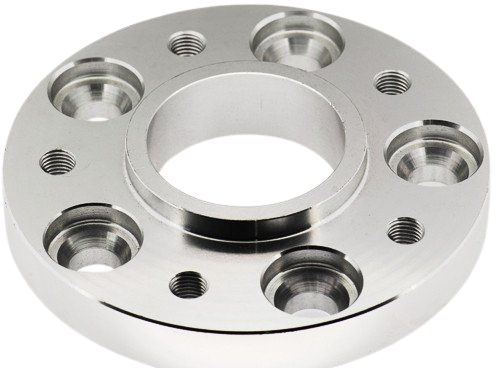
2.8X
Sourcing Cycle Speed
Frigate’s pre-qualified network shortens decision time between RFQ and PO placement.
94%
On-Time Delivery Rate
Structured planning windows and logistics-linked schedules improve project-level delivery reliability.
4X
Multi-Part Consolidation
We enable part family batching across suppliers to reduce fragmentation.
22%
Quality Rejection Rate
Multi-level quality checks and fixed inspection plans lower non-conformities.
30%
Procurement Costs
Optimized supplier negotiations and bulk order strategies reduce your overall sourcing expenses.
20%
Manual Processing Time
Automation of sourcing and supplier management significantly reduces time spent on manual tasks.
Managing Material Springback for Precise Dimensions
Springback occurs when materials partially return to their original shape after forming due to internal elasticity. Frigate addresses this by predicting springback during design and using simulations to adjust forming parameters accordingly. Real-time monitoring of pressure and temperature further reduces springback. If deviations occur, precise rework or secondary processes are applied to meet the required tolerances and ensure high precision.

Get Clarity with our Manufacturing Insights
- Real Impact
Words from Clients
See how global OEMs and sourcing heads describe their experience with our scalable execution.
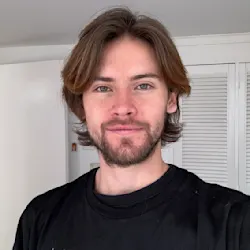
“Quick turnaround and solid quality.”
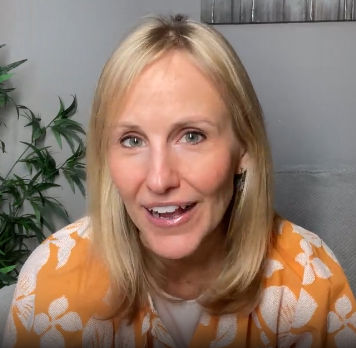
“The instant quote tool saved us time, and the parts were spot-on. Highly recommend Frigate!”
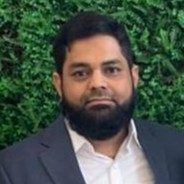
“I would strongly recommend Frigate to anyone who wants to do Rapid Prototyping, and take their ideas to manufacturing. One firm doing all kinds of Product Development!”
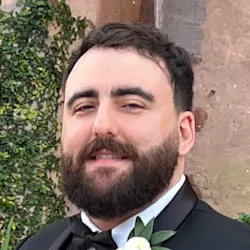
“Great service, fair price, and the parts worked perfectly in our assembly.”
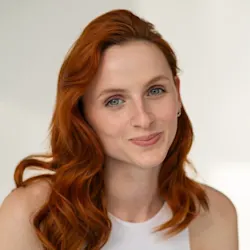
“Top-notch machining and fast shipping. Very satisfied with the results.”
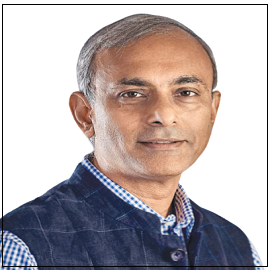
“The next disruption is happening in Prototyping & Manufacturing on-demand and Frigate is leading the way! I personally believe the Frigate's way of IIOT enabled cloud platform with Al.”
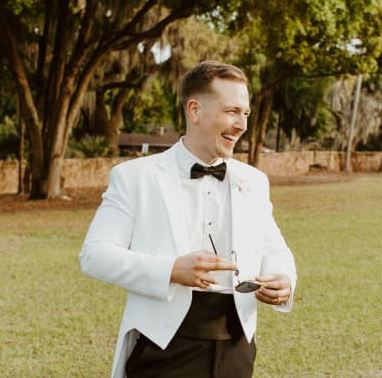
“Frigate delivered high-quality parts at a competitive price. The instant quote tool is a huge plus for us!”

“We appreciate the precision and quality of the machined components in the recent delivery—they meet our specifications perfectly and demonstrate Frigate’s capability for excellent workmanship.”
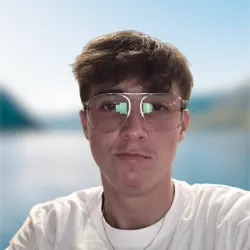
“Flawless execution from quote to delivery.”

“I am absolutely happy to work with supplier like Frigate who were quite proactive & result oriented . Frigate has high willingness team who has strong know how & their passion towards the products & process were absolutely thrilling.”
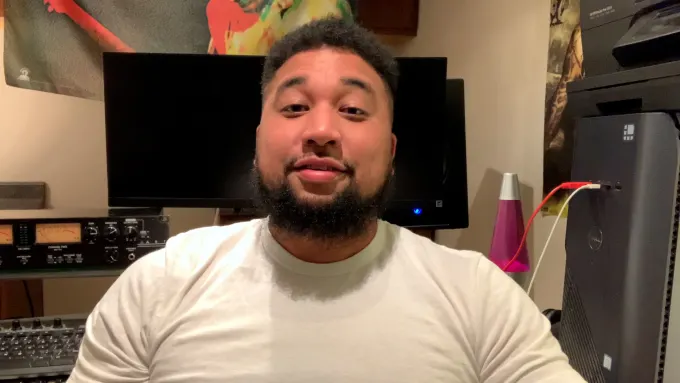
“The precision on these parts is impressive, and they arrived ahead of schedule. Frigate’s process really stands out!”
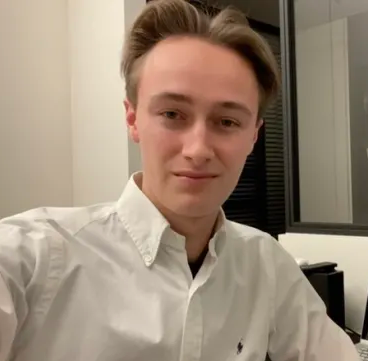
“Parts were exactly as spec’d, and the instant quote made budgeting a breeze.”
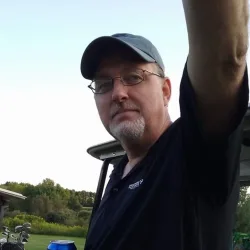
“Good value for the money.”
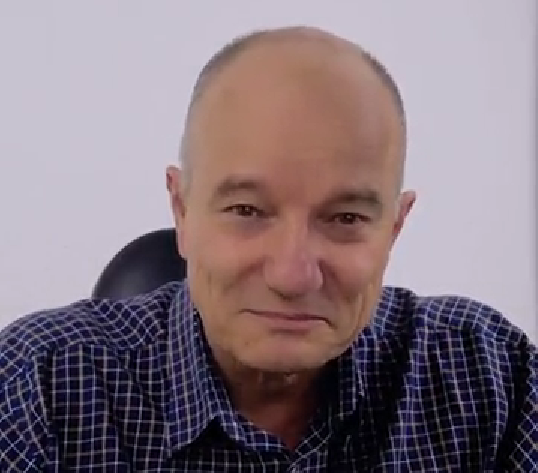
“The finish was perfect, and the team was easy to work with.”

“Working with Frigate has been great. Their proactive, results-driven approach and expertise shine through in every project. It's been a pleasure collaborating with them.”

"We are highly satisfied with the timely delivery and quality of the MIG Welding Cable from Frigate. Their attention to detail, secure packaging, and quick responsiveness stood out. We confidently recommend Frigate Engineering Services Pvt. Ltd. as a reliable manufacturing partner."
Having Doubts? Our FAQ
Check all our Frequently Asked Question
Overmolding uses precise injection techniques to fuse materials with different properties, ensuring strong adhesion. The process ensures seamless integration, minimizing the risk of delamination and increasing overall part strength.
Yes, overmolding allows for creating complex shapes while maintaining structural integrity. The multi-material injection process ensures that the base material’s strength is preserved, even with intricate designs.
Overmolding improves durability by combining materials that resist wear, chemicals, and environmental stress. The final product gains enhanced resistance to cracking, abrasion, and harsh conditions, extending its lifespan.
Overmolding materials with vastly different thermal expansion rates can lead to bonding issues. Precise temperature control during injection and cooling cycles ensures proper material adhesion and prevents warping.
Overmolding eliminates additional assembly steps by combining materials into one part. This streamlined process reduces labor costs, assembly time, and the risk of errors associated with multi-component assemblies.
We'd love to Manufacture for you!
Submit the form below and our representative will be in touch shortly.
LOCATIONS
Global Sales Office
818, Preakness lane, Coppell, Texas, USA – 75019
Registered Office
10-A, First Floor, V.V Complex, Prakash Nagar, Thiruverumbur, Trichy-620013, Tamil Nadu, India.
Operations Office
9/1, Poonthottam Nagar, Ramanandha Nagar, Saravanampatti, Coimbatore-641035, Tamil Nadu, India. ㅤ
Other Locations
- Bhilai
- Chennai
- Texas, USA