Blow Molding Services
Frigate’s blow molding technology produces durable plastic components with minimal scrap. We ensure precise control over part dimensions and wall thickness throughout production.
Our Clients



































Advantages of Blow Molding Services
Rapid Tooling and Setup
The blow molding process allows for faster tooling and setup times than other molding techniques, speeding up production schedules.
Lightweight Components
Blow molding produces lightweight plastic parts without sacrificing strength, making it ideal for applications in the automotive and packaging industries.
Low Scrap Rate
The blow molding process has a low scrap rate due to precise material control, which reduces waste and improves sustainability.
Design Flexibility
Blow molding offers design flexibility, allowing for varied wall thicknesses, internal voids, and complex shapes, all in one part.
Custom Blow Molding Services for Precision and Efficiency
Inconsistent part quality and slow production can hinder manufacturing processes. Custom blow molding provides precise, high-quality parts with fast production cycles. This process ensures uniform wall thickness, complex geometries, and minimal material waste, making it suitable for high-volume runs. With a range of material options, custom blow molding meets specific technical requirements for durability and performance. It offers efficient, repeatable production while maintaining tight tolerances, making it ideal for industries requiring consistent and reliable plastic components.

Get Your Quote Now
- Instant Quotation
- On-Time Delivery
- Affordable Cost
Our Blow Molding Process






Thermoset materials are mixed with curing agents or hardeners before injection, ensuring they are ready for molding.
The prepared thermoset material is injected into a mold cavity under high pressure, ensuring complete filling.
Once the material fills the mold, it undergoes heat curing. This causes the thermoset material to chemically cross-link, hardening it permanently.
After curing, the part is cooled in the mold. This helps solidify the material further, ensuring it retains its shape and strength.
Once fully cured and cooled, the part is ejected from the mold. The ejection process is done carefully to avoid damage.
Some thermoset parts may undergo additional post-curing to enhance their physical properties. This step ensures maximum durability and performance.
Blow Molding Materials
Blow molding is a highly efficient manufacturing process for creating hollow parts. It offers precise control over part design, thickness, and production speed.
HDPE offers an excellent strength-to-weight ratio, high impact resistance, and chemical durability. It is ideal for rigid containers and industrial applications, and it resists environmental stress and maintains shape under pressure.
PET has superior dimensional stability, high clarity, and strong moisture and gas barriers. Due to its thermal resistance and recyclability, it is ideal for food and beverage packaging.
PP is excellently resistant to chemicals, has low moisture absorption, and is highly resistant to heat. It’s used in automotive components and containers that require high-temperature performance and durability.
PVC offers rigidity, UV resistance, and electrical insulation. It is commonly used for medical devices, piping, and weather-resistant containers, providing stability in harsh environments.
ABS provides high-impact resistance and toughness, even at low temperatures. It is ideal for automotive parts, electrical enclosures, and consumer products that require strength and durability.
Nylon offers excellent wear resistance, low friction, and high-temperature stability. It is used in automotive, industrial, and electrical applications that require durable, high-performance parts.
PS is lightweight, rigid, and easy to process. While commonly used for disposable packaging, it has limited impact and chemical resistance, making it suitable for low-stress applications.
TPE combines rubber-like flexibility with thermoplastic processing. It is used for durable, flexible parts like seals and gaskets, offering excellent abrasion resistance and low-temperature performance.
Efficient Cycle Time Reduction for Enhanced Productivity
Optimizing cycle time is essential for improving production efficiency while maintaining consistent part quality. Frigate addresses this through precise temperature control, advanced mold cooling systems, and optimized material flow management. By fine-tuning the mold design and cooling process, cycle time is reduced without compromising the integrity of the part. This approach allows for faster production rates while ensuring the desired mechanical properties and dimensional accuracy, increasing overall productivity and reducing operational costs.

Compliance for Blow Molding Services
Blow molding at Frigate meets specific technical certifications critical to material safety, production accuracy, and environmental standards. Each compliance ensures precise tolerances, chemical compatibility, and durability under operational conditions. This approach supports advanced manufacturing needs and regulatory obligations.
Certifies polyethylene and polypropylene for direct food and medical contact, ensuring chemical resistance and hygienic material properties.
Enforces traceability and defect controls in manufacturing processes, ensuring consistent blow-molded product quality.
Defines impact resistance for thermoplastics, ensuring materials meet performance standards for structural and safety-critical applications.
Regulates chemical exposure in plastics, prohibiting harmful additives and ensuring worker and consumer safety.
Limits hazardous substances, ensuring suitability for electronics and environmentally conscious industries.
UL 746C evaluates the long-term thermal aging of polymeric materials, ensuring performance under prolonged exposure to heat and stress.
Specifies environmental requirements for blow molding, emphasizing energy efficiency and reduced waste.

Tolerance for Blow Molding Services
Controls the thickness of the extruded parison to ensure even wall thickness and minimal material waste.
Ensures consistency in round features like bottle necks or containers to prevent deformation under load.
Monitors resin flow during processing for uniform material distribution and structural integrity.
Controls draft angles to facilitate part ejection without surface defects or dimensional distortion.
Ensures flat surfaces remain within tolerance to prevent assembly issues or leakage in critical seals.
Validates the integrity of weld lines formed during molding to withstand operational stresses.
Ensures molded parts can withstand specified internal pressures without failure for liquid or gas storage.
Maintains consistent channel dimensions in complex geometries to optimize material flow and cooling.
Ensures precision in corner radii to enhance strength and reduce stress concentration points.
Monitors mold temperature uniformity to ensure dimensional accuracy and prevent surface imperfections.

Quality Testing Standards for Blow Molding Services
Verifies uniform parison heating to avoid material inconsistencies and ensure optimal flow.
Detects internal stresses in molded parts to prevent premature failure under operational loads.
Measures deformation over time under sustained loads, ensuring durability for extended use.
Identifies defects during resin extrusion to optimize process parameters for smoother finishes.
Assesses weld line strength and bonding quality in critical structural areas.
Quantifies emissions to ensure compliance with environmental and health standards.
Simulates repeated stress to evaluate part performance under real-world operating conditions.
Determines material behavior under specified loads at elevated temperatures.
Assesses light transmission for transparent or semi-transparent blow-molded parts.
Evaluates bonding between multi-layer materials for strength and delamination resistance.
Ensures part stability and integrity under dynamic load conditions.
Measures barrier properties for gases to ensure suitability for food, beverage, or medical uses.
Optimizing Performance and Sustainability in Automotive Components
Balancing cost efficiency with high-performance standards in automotive manufacturing can be challenging. Blow molding offers a solution by enabling the production of lightweight, durable components with complex geometries. The process ensures precise control over material distribution and wall thickness, minimizing material waste and defects. Its fast production cycles meet tight manufacturing timelines while maintaining high-quality standards. Additionally, blow molding supports sustainability by using recyclable materials while ensuring the required strength and functionality for automotive components.









Industries We Serve
- Solid Progress
Our Manufacturing metrics
Frigate brings stability, control, and predictable performance to your sourcing operations through a structured multi-vendor system.

2.8X
Sourcing Cycle Speed
Frigate’s pre-qualified network shortens decision time between RFQ and PO placement.
94%
On-Time Delivery Rate
Structured planning windows and logistics-linked schedules improve project-level delivery reliability.
4X
Multi-Part Consolidation
We enable part family batching across suppliers to reduce fragmentation.
22%
Quality Rejection Rate
Multi-level quality checks and fixed inspection plans lower non-conformities.
30%
Procurement Costs
Optimized supplier negotiations and bulk order strategies reduce your overall sourcing expenses.
20%
Manual Processing Time
Automation of sourcing and supplier management significantly reduces time spent on manual tasks.
Precision Control for Thin-Walled Parts with Maximum Strength
Ensuring high precision in thin-walled blow-molded parts is achieved through advanced mold engineering and precise control of material distribution. Frigate utilizes specialized techniques to control material flow and cooling rates, ensuring uniform wall thickness and structural integrity. These methods allow for the production of thin-walled components that meet stringent tolerance requirements while maintaining the necessary strength. This solution is particularly effective for industries like automotive and packaging, where high precision and durability are critical.

Get Clarity with our Manufacturing Insights
- Real Impact
Words from Clients
See how global OEMs and sourcing heads describe their experience with our scalable execution.
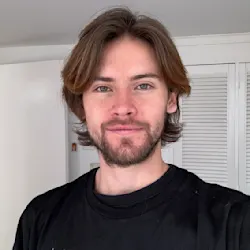
“Quick turnaround and solid quality.”
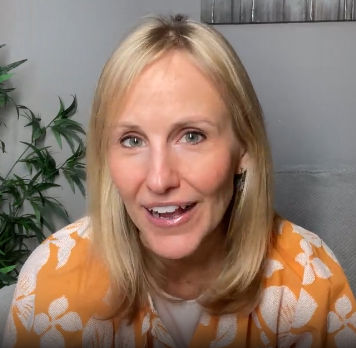
“The instant quote tool saved us time, and the parts were spot-on. Highly recommend Frigate!”
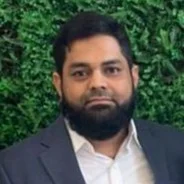
“I would strongly recommend Frigate to anyone who wants to do Rapid Prototyping, and take their ideas to manufacturing. One firm doing all kinds of Product Development!”
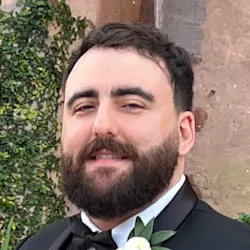
“Great service, fair price, and the parts worked perfectly in our assembly.”
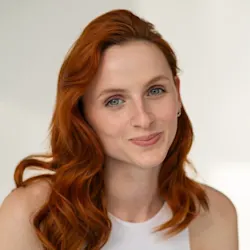
“Top-notch machining and fast shipping. Very satisfied with the results.”
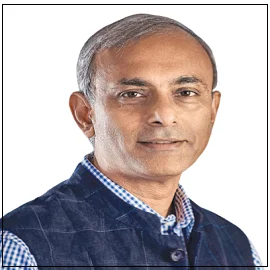
“The next disruption is happening in Prototyping & Manufacturing on-demand and Frigate is leading the way! I personally believe the Frigate's way of IIOT enabled cloud platform with Al.”
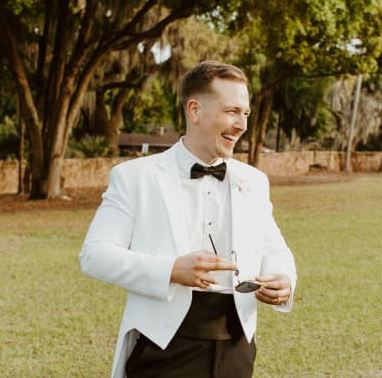
“Frigate delivered high-quality parts at a competitive price. The instant quote tool is a huge plus for us!”

“We appreciate the precision and quality of the machined components in the recent delivery—they meet our specifications perfectly and demonstrate Frigate’s capability for excellent workmanship.”
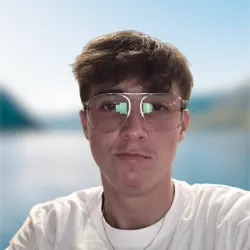
“Flawless execution from quote to delivery.”

“I am absolutely happy to work with supplier like Frigate who were quite proactive & result oriented . Frigate has high willingness team who has strong know how & their passion towards the products & process were absolutely thrilling.”
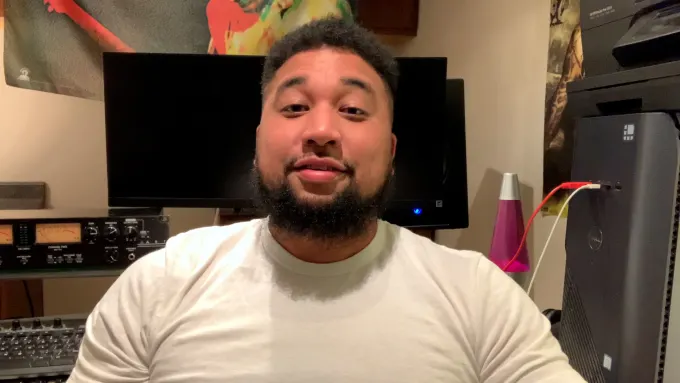
“The precision on these parts is impressive, and they arrived ahead of schedule. Frigate’s process really stands out!”
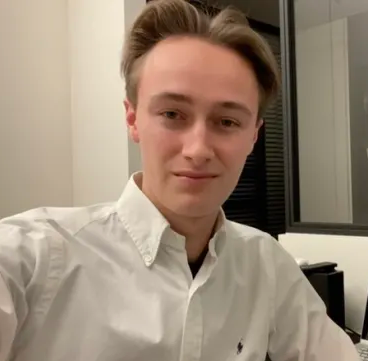
“Parts were exactly as spec’d, and the instant quote made budgeting a breeze.”
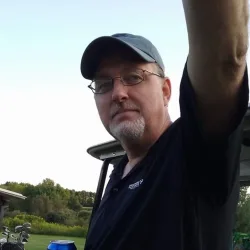
“Good value for the money.”
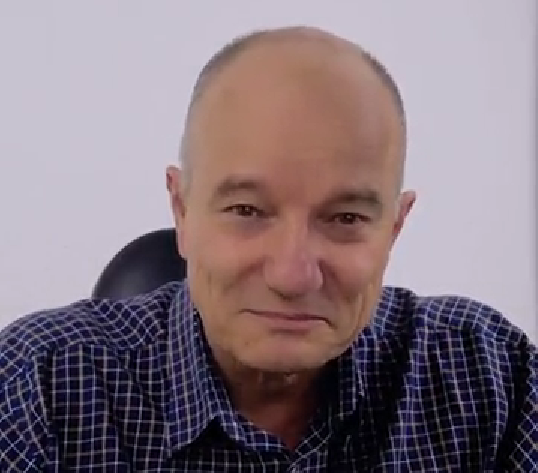
“The finish was perfect, and the team was easy to work with.”

“Working with Frigate has been great. Their proactive, results-driven approach and expertise shine through in every project. It's been a pleasure collaborating with them.”

"We are highly satisfied with the timely delivery and quality of the MIG Welding Cable from Frigate. Their attention to detail, secure packaging, and quick responsiveness stood out. We confidently recommend Frigate Engineering Services Pvt. Ltd. as a reliable manufacturing partner."
Having Doubts? Our FAQ
Check all our Frequently Asked Question
Blow molding allows for precise control over wall thickness and part dimensions, ensuring complex geometries are accurately produced with tight tolerances. The process utilizes specialized molds and pressure regulation to maintain consistency throughout production.
Material shrinkage is accounted for during mold design to ensure parts retain dimensional accuracy. Blow molding uses precise temperature control and mold compensation to minimize shrinkage, especially in larger or more intricate parts.
Blow molding maintains consistent wall thickness by regulating air pressure during molding and optimizing material flow. This ensures uniformity, even in large or asymmetrical parts, reducing material waste and improving structural integrity.
Blow molding can improve strength through material selection, multi-layer designs, or post-processing techniques like heat treatment. Specific formulations can enhance impact resistance, tensile strength, and thermal stability, ensuring long-lasting performance.
Blow molding minimizes material waste through precise material control and efficient molding cycles. Many blow-molded parts are made from recyclable materials, allowing for easy post-production recycling and reducing environmental impact.
We'd love to Manufacture for you!
Submit the form below and our representative will be in touch shortly.
LOCATIONS
Global Sales Office
818, Preakness lane, Coppell, Texas, USA – 75019
Registered Office
10-A, First Floor, V.V Complex, Prakash Nagar, Thiruverumbur, Trichy-620013, Tamil Nadu, India.
Operations Office
9/1, Poonthottam Nagar, Ramanandha Nagar, Saravanampatti, Coimbatore-641035, Tamil Nadu, India. ㅤ
Other Locations
- Bhilai
- Chennai
- Texas, USA