Micro Injection Molding Services
Frigate delivers micro injection molding with precision tolerances down to ±5 microns. Our expertise ensures ultra-fine detail and accuracy in complex miniature components.
Our Clients





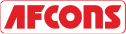

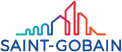


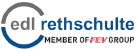

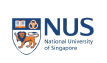
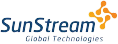

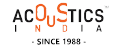




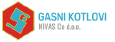
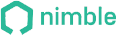
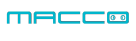












Advantages of Micro Injection Molding Services
Exceptional Surface Finish
Micro injection molding provides smooth surface finishes and high detail resolution, which are critical for optical and medical applications where clarity and accuracy are essential.
Thermal Stability in Processing
Micro injection molding can maintain thermal consistency, preventing warping or distortion, which is crucial for tiny parts with tight dimensional requirements.
Capability for Multi-Material Molding
It allows for integrating multiple materials in a single part, facilitating complex designs with different material properties for specific functional needs.
High-Strength Micro Parts
The process produces durable micro-components with consistent mechanical properties, supporting applications where small parts must withstand rigorous operational stresses.
Precision-Driven Custom Micro Injection Molding
Ultra-precise miniature components often suffer from inconsistent tolerances, poor material efficiency, and compromised performance. Custom micro injection molding addresses these issues by providing exact control over complex geometries, with tolerances as fine as ±5 microns. This advanced process reduces waste, ensures outstanding surface finishes, and maintains thermal stability, even in intricate designs with multiple materials. Custom micro injection molding ensures high-volume, repeatable production with precise specifications for medical, aerospace, and electronics applications.

Get Your Quote Now
- Instant Quotation
- On-Time Delivery
- Affordable Cost
Our Micro Injection Molding Process






Specialized micro-sized materials are selected and precisely preheated to the required viscosity for efficient flow during injection.
To shape the micro components, a highly detailed mold with fine tolerances is created. The mold is carefully set up for optimal precision.
The molten material is injected into the mold under high pressure through small nozzles, filling the tiny cavities accurately.
The injected material cools rapidly within the mold, solidifying it into the desired shape while maintaining fine details and dimensional accuracy.
Once cooled, the micro-component is ejected from the mold and ready for inspection and further processing.
Final steps such as trimming, surface finishing, or additional assembly are carried out to ensure the part meets strict technical specifications.
Micro Injection Molding Materials
Micro injection molding demands precision and reliability for producing miniature components. Choosing the right materials ensures optimal performance and durability in complex applications.
Glass-filled nylon (PA) and PEEK offer increased rigidity and dimensional stability, ideal for high-stress, high-temperature aerospace, automotive, and electronics applications.
Polyphenylene sulfide (PPS) and polyetherimide (PEI) maintain strength and dimensional stability at elevated temperatures and are suitable for industrial, aerospace, and electronics components.
Fluoropolymers provide excellent chemical resistance, low friction, and high thermal stability, which makes them ideal for medical, chemical processing, and food-grade applications.
Carbon-filled PEEK and polypropylene offer enhanced electrical conductivity, stiffness, and wear resistance, making them ideal for high-performance parts in aerospace, defense, and electronics.
Medical-grade polyethylene, polyurethane, and bio-based resins are used in medical devices and healthcare applications, meeting safety and non-toxicity standards for critical components.
TPEs combine flexibility with processability, offering abrasion resistance and long-term performance in automotive, medical, and consumer electronics applications.
Metal-filled thermoplastics, such as stainless steel or aluminum, combine strength and lightweight properties, which are ideal for sensors, connectors, and medical instruments requiring high performance.
Precision in Tight Tolerances for Complex Micro Parts
Micro injection molding requires precise control to meet tight tolerances down to the micron level. Frigate utilizes advanced injection molding systems and high-precision tooling to ensure dimensional accuracy. Optimized mold cavity design and high-quality materials minimize deviations from wear. Temperature, pressure, and velocity are tightly regulated to maintain consistency and avoid defects. These measures guarantee that each part meets the exact specifications of the aerospace, medical, and electronics industries.

Compliance for Micro Injection Molding Services
Micro Injection Molding demands precise control over material flow, pressure, and temperature to create high-precision components. Frigate maintains strict compliance with global standards to guarantee dimensional accuracy and reliability. Using advanced equipment and techniques, Frigate ensures consistent results, meeting the tight tolerances required in the medical, electronics, and automotive industries. These certifications ensure that the manufacturing process adheres to best practices in safety, quality, and environmental responsibility.
ISO 13485:2016 focuses on managing medical device quality, ensuring traceability, risk management, and compliance with stringent product specifications.
Verifies the flame-retardant properties of materials, ensuring they do not sustain combustion under specified testing conditions critical for electronic components.
Regulates using hazardous materials in components, limiting lead, mercury, and other harmful substances in products.
Defines the quality system regulation (QSR) for manufacturing medical devices, covering design, production, and post-market requirements.
Establishes criteria for quality management systems, emphasizing process control, corrective actions, and customer satisfaction metrics.
Requires manufacturers to register chemicals used in production, ensuring their safe use and reducing environmental impact.

Tolerance for Micro Injection Molding Services
Controls the pressure applied during the injection process to ensure material flow and mold filling.
Ensures consistent speed during injection, which affects the quality and uniformity of molded parts.
The total time taken for one cycle of injection, cooling, and ejection, critical for high-speed production.
Optimizes the temperature for both the mold and injected material to ensure uniform cooling and shrinkage.
Accounts for material contraction during cooling, which is important for achieving precise final dimensions.
Ensures proper flow and filling of the mold cavity for complex, fine features in micro-sized components.
Ensures sufficient force to eject molded parts from the cavity without damage to delicate micro components.
Determines the size and type of gate for optimal flow and minimal part defects during injection molding.
Ensures proper venting of trapped air in the mold, critical for avoiding defects like short shots.
The force needed to keep the mold halves together during injection, crucial for preventing flash or defects.
Ensures minimal deformation of the mold under clamping pressure, important for maintaining tight tolerances.
The rate at which the molded material cools, affecting cycle time, part strength, and final part quality.
Controls deformation of parts after cooling, important for maintaining dimensional accuracy in micro parts.
Controls the thickness of the unwanted material at the parting line, ensuring minimal flash in high-precision molding.
Ensures that very long, thin sections of the mold fill consistently, without voids or defects in micro-scale components.
Achieves ultra-fine surface finish, necessary for micro components, particularly in the medical or electronic industries.

Quality Testing Standards for Micro Injection Molding Services
Measures the time it takes for the mold cavity to fill, critical for optimizing cycle time and precision.
Evaluates the flow behavior of the material under varying shear rates, ensuring consistent material flow.
Assesses the tolerance of key features critical to the function of micro components.
Analyzes the uniformity of pressure applied across the mold cavity, ensuring consistent part quality.
Monitors and controls the temperature of the molten material to ensure optimal molding conditions.
Detects internal stress in molded parts, which can impact their strength and dimensional stability.
Measures the permanent deformation of materials after compression, assessing elasticity and recovery.
Monitors and compares cycle times to ensure repeatability and consistency across multiple production runs.
Measures the moisture content in the polymer, critical for preventing defects during molding.
Analyzes mold surfaces for wear, erosion, or corrosion, ensuring long-term accuracy in mold performance.
Measures the ability of the mold and material to transfer heat, ensuring efficient cooling and quality.
Analyzes the molecular weight distribution and chain integrity of the polymer, impacting part strength.
Tests the ability of coatings, inks, or adhesives to bond to the part surface, ensuring adhesion quality.
Detects internal micro-defects such as voids, cracks, or inclusions that can affect component strength.
Measures the material’s thermal expansion behavior, crucial for dimensional stability under temperature variations.
Detects defects along the parting line, critical for preventing parting flash or misalignment issues.
Maximizing Quality and Efficiency in Medical Component Fabrication
Manufacturing medical components require precision, consistency, and strict regulatory compliance. Micro injection molding meets these needs by producing intricate, small-scale parts with tight tolerances. It is vital for creating components like implants, surgical tools, and diagnostic devices, where accuracy and reliability are critical. Biocompatible materials are used, and material waste is minimized. This enhances production efficiency while maintaining high-quality standards. The process ensures each part meets the required specifications for safety and performance in medical applications.







Industries We Serve
- Solid Progress
Our Manufacturing metrics
Frigate brings stability, control, and predictable performance to your sourcing operations through a structured multi-vendor system.
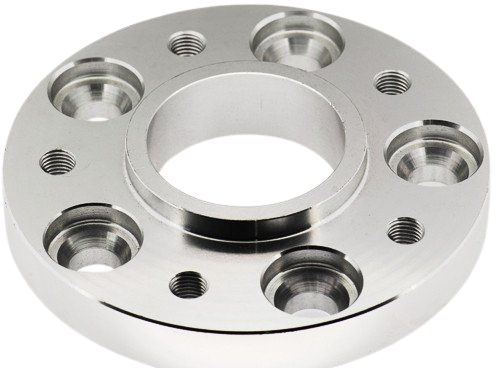
2.8X
Sourcing Cycle Speed
Frigate’s pre-qualified network shortens decision time between RFQ and PO placement.
94%
On-Time Delivery Rate
Structured planning windows and logistics-linked schedules improve project-level delivery reliability.
4X
Multi-Part Consolidation
We enable part family batching across suppliers to reduce fragmentation.
22%
Quality Rejection Rate
Multi-level quality checks and fixed inspection plans lower non-conformities.
30%
Procurement Costs
Optimized supplier negotiations and bulk order strategies reduce your overall sourcing expenses.
20%
Manual Processing Time
Automation of sourcing and supplier management significantly reduces time spent on manual tasks.
Reducing Material Waste for Efficient and Cost-Effective Production
Due to small part sizes, minimizing material waste is critical in micro injection molding. Frigate optimizes shot size to reduce excess material and employs cold-runner systems to direct material efficiently. Injection speed, holding pressure, and cooling rates are fine-tuned to minimize scrap. These practices ensure that material use is efficient, reducing costs while maintaining high-quality production.

Get Clarity with our Manufacturing Insights
- Real Impact
Words from Clients
See how global OEMs and sourcing heads describe their experience with our scalable execution.
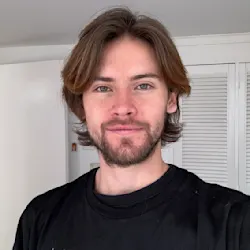
“Quick turnaround and solid quality.”
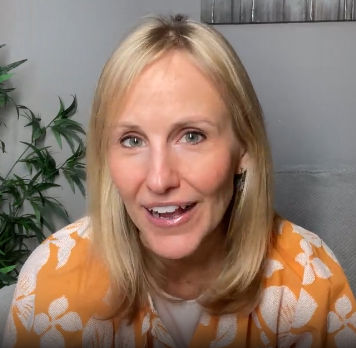
“The instant quote tool saved us time, and the parts were spot-on. Highly recommend Frigate!”
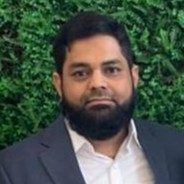
“I would strongly recommend Frigate to anyone who wants to do Rapid Prototyping, and take their ideas to manufacturing. One firm doing all kinds of Product Development!”
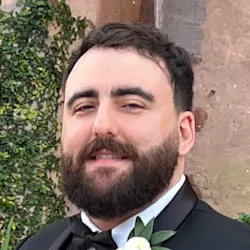
“Great service, fair price, and the parts worked perfectly in our assembly.”
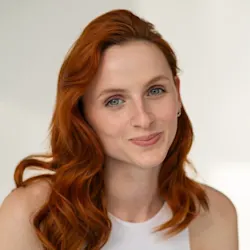
“Top-notch machining and fast shipping. Very satisfied with the results.”
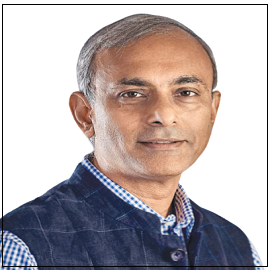
“The next disruption is happening in Prototyping & Manufacturing on-demand and Frigate is leading the way! I personally believe the Frigate's way of IIOT enabled cloud platform with Al.”
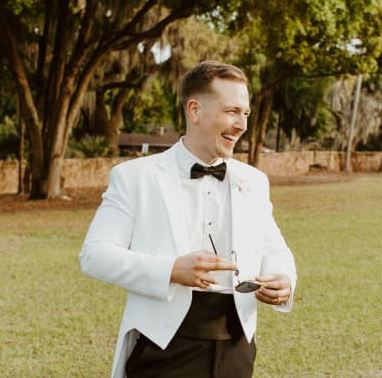
“Frigate delivered high-quality parts at a competitive price. The instant quote tool is a huge plus for us!”

“We appreciate the precision and quality of the machined components in the recent delivery—they meet our specifications perfectly and demonstrate Frigate’s capability for excellent workmanship.”
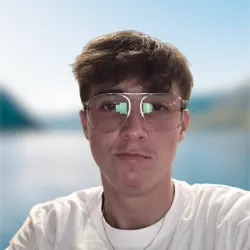
“Flawless execution from quote to delivery.”

“I am absolutely happy to work with supplier like Frigate who were quite proactive & result oriented . Frigate has high willingness team who has strong know how & their passion towards the products & process were absolutely thrilling.”
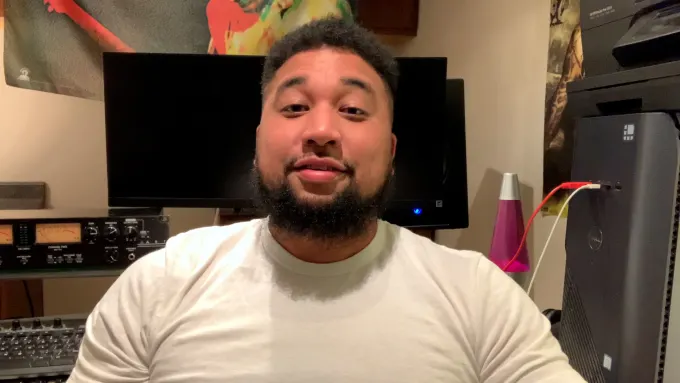
“The precision on these parts is impressive, and they arrived ahead of schedule. Frigate’s process really stands out!”
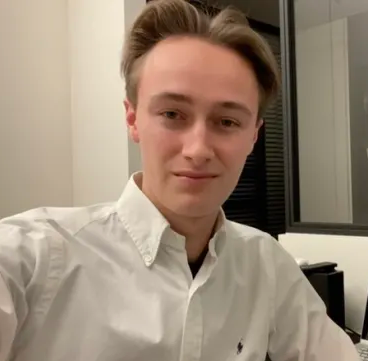
“Parts were exactly as spec’d, and the instant quote made budgeting a breeze.”
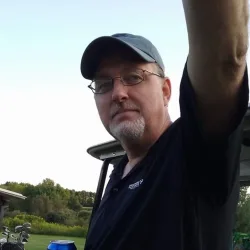
“Good value for the money.”
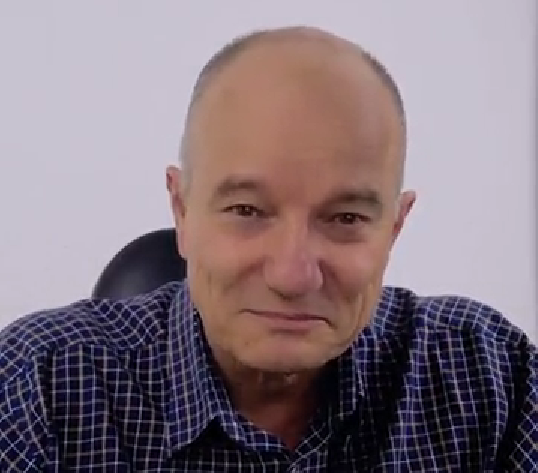
“The finish was perfect, and the team was easy to work with.”

“Working with Frigate has been great. Their proactive, results-driven approach and expertise shine through in every project. It's been a pleasure collaborating with them.”

"We are highly satisfied with the timely delivery and quality of the MIG Welding Cable from Frigate. Their attention to detail, secure packaging, and quick responsiveness stood out. We confidently recommend Frigate Engineering Services Pvt. Ltd. as a reliable manufacturing partner."
Having Doubts? Our FAQ
Check all our Frequently Asked Question
Micro injection molding uses specialized molds and precise injection techniques to achieve tolerances as small as ±5 microns. This ensures the production of complex, high-precision parts without compromising detail or structural integrity.
The process is highly efficient. By injecting precise amounts of material into the mold cavity, it optimizes material flow and minimizes waste. This ensures material conservation while maintaining the integrity and functionality of micro components.
Micro-injection molding can produce parts with excellent heat resistance and thermal stability by selecting high-performance thermoplastics and additives. This is crucial for aerospace, electronics, and medical applications where parts must function in harsh conditions.
Yes, multi-material molding enables the integration of different materials within a single component, enhancing functionality, flexibility, and performance. This is especially useful for micro parts requiring different material properties, such as electrical conductivity or flexibility.
Micro injection molding ensures high repeatability through precise control over the injection process, mold design, and material handling. This allows for consistent production of small batches and meets stringent quality requirements across every part.
We'd love to Manufacture for you!
Submit the form below and our representative will be in touch shortly.
LOCATIONS
Global Sales Office
818, Preakness lane, Coppell, Texas, USA – 75019
Registered Office
10-A, First Floor, V.V Complex, Prakash Nagar, Thiruverumbur, Trichy-620013, Tamil Nadu, India.
Operations Office
9/1, Poonthottam Nagar, Ramanandha Nagar, Saravanampatti, Coimbatore-641035, Tamil Nadu, India. ㅤ
Other Locations
- Bhilai
- Chennai
- Texas, USA