Sheet Metal Bending Services
Frigate excels in precision sheet metal bending services using advanced CNC technology. We deliver tight tolerances and high-quality bends in various materials.
Our Clients



































Advantages of Sheet Metal Bending Services
High Structural Integrity
Sheet metal bending services enhances the strength and durability of parts by aligning the grain structure, improving load-bearing capacity.
Complex Geometries
Advanced bending techniques, such as air bending or bottoming, allow for creating intricate shapes with tight dimensional accuracy.
Repeatability and Consistency
CNC-controlled bending ensures highly repeatable results with minimal variation, which is crucial for precision-critical applications in the aerospace and automotive industries.
Optimized Material Utilization
Bending minimizes material waste by enabling precise, near-net-shape production, leading to cost-effective manufacturing and sustainable practices.
Precision Custom Sheet Metal Bending for Your Complex Needs
Custom sheet metal bending services at Frigate provide the perfect solution for High-precision results delivered for complex shapes and intricate geometries. Advanced CNC technology ensures parts with tight tolerances and excellent repeatability. Every component will meet your exact specifications. The bending process works with aluminum, stainless steel, and other materials. It reduces waste, cuts production time, and guarantees cost efficiency. Achieve the quality and consistency required for aerospace, automotive, and industrial applications.

Get Your Quote Now
- Instant Quotation
- On-Time Delivery
- Affordable Cost
Our Sheet Metal Bending Process






The first step is choosing the appropriate sheet metal, such as aluminum, steel, or stainless steel, based on the application’s requirements.
A precise design specifies the bend angles, radii, and dimensions, ensuring accuracy in the final product.
An accurate bend allowance and compensation for material spring back are calculated to achieve the desired angles and dimensions.
Bending tools, such as dies and punches, are selected and set up in the CNC machine, tailored to the material and design.
The sheet metal is placed in the machine, and the punch applies force to bend the metal into the desired shape with tight tolerances.
After bending, parts are inspected for dimensional accuracy, and any necessary finishing processes, such as deburring, are applied to ensure a high-quality result.
Sheet Metal Bending Materials
Material selection is key to achieving strength, durability, and precision. The right material ensures optimal performance and efficient bending results in every project.
Lightweight and corrosion-resistant, aluminum is commonly used in aerospace, automotive, and industrial applications. It offers excellent formability and is ideal for complex shapes and tight tolerances. Aluminum alloys like 6061 and 5052 are popular due to their balance of strength & workability.
Known for its durability and resistance to corrosion, stainless steel is widely used in harsh environments. Its high strength makes it suitable for heavy-duty applications. Stainless steel alloys like 304 and 316 are commonly chosen for their excellent corrosion resistance and formability.
Carbon steel is a cost-effective material with good strength and hardness. It’s used in structural and manufacturing components where strength is key. Carbon steel alloys like A36 and 1018 provide good weldability and workability but may require coatings to prevent rust.
Copper’s excellent electrical and thermal conductivity makes it ideal for electrical, plumbing, and HVAC applications. It is easy to bend and form but can be prone to corrosion, so it is often alloyed with other metals to enhance its properties.
Brass is a copper-zinc alloy that balances strength, corrosion resistance, and machinability. Due to its attractive appearance and electrical conductivity, it’s often used for decorative and electrical components.
Galvanized steel is highly corrosion-resistant and coated with a layer of zinc. It’s commonly used in construction, automotive, and outdoor applications where protection against rust is crucial. It’s also highly formable, making it suitable for bending without compromising its protective coating.
Streamlined Production Process for Faster Turnarounds
Automated CNC bending systems at Frigate significantly reduce manual setup time, improving overall production efficiency. These systems deliver quick, precise bends with minimal downtime by optimizing production flow, ensuring consistent, high-quality output. Real-time adjustments and continuous monitoring enhance precision, allowing for tighter tolerances and reducing the risk of defects.

Compliance for Sheet Metal Bending Services
Compliance for sheet metal bending services at Frigate ensures strict adherence to industry regulations, guaranteeing precision, safety, and environmental responsibility. Our certified processes meet the highest standards for quality and efficiency, ensuring that every bend is accurate and safe.
Key compliance certifications
Ensures consistent quality management, improving operational efficiency and customer satisfaction.
Confirms materials are free from hazardous substances, protecting health and the environment.
Ensures materials meet specific performance and testing criteria for structural steel used in bending.
Guarantees safety protocols are followed to protect workers from risks associated with bending operations.
This ensures that all environmental regulations are met, minimizing waste and emissions during the manufacturing process.
Certifies compliance with European Union product safety and environmental requirements for export.

Tolerance for Sheet Metal Bending Services
The difference between the unfolded length and final bent length, accounting for material springback.
The angle change that occurs after bending due to material elasticity, adjusted based on material properties.
The radius of the punch used in the bending operation, impacting the accuracy of the bend.
A factor that accounts for material deformation, adjusting the bend allowance for accurate flat patterns.
The amount of material required to form a bend, based on material thickness, radius, and angle.
Ensures the bend direction (concave or convex) is within tolerance for proper fitment.
Precision on the length of flanges formed during bending, ensuring tight dimensional control.
Tolerance on the radius of internal corners, affecting material flow and bend consistency.
Tolerance for the external radius of the bend, affecting part appearance and fitment.
Control over material grain direction to avoid distortion and ensure consistent bending performance.
Tolerance on the extension of material beyond the bend, critical for ensuring correct part dimensions.
Compensation for tool wear over time to maintain bending precision and minimize variations.

Quality Testing Standards for Sheet Metal Bending Services
Tests the material's ability to withstand deformation without failure or cracks.
Measures how the material flows during bending, ensuring uniform deformation.
Tests the residual stress patterns in the material after bending, impacting part durability.
Examines the microstructure changes in the material after bending, especially when heated during forming.
Measures any micro-cracks, scratches, or deformations in the surface after bending, which could affect functionality.
Measures the precision of angle reversals after bending, ensuring consistent results in multi-axis bending.
Detects cracks or fractures at the bend area under high magnification, ensuring the integrity of the bend.
Tests the localization of strain around the bend zone to ensure uniform distribution of deformation.
Measures the material's ability to return to its original shape after bending, impacting part flexibility.
Tests the material's resistance to deformation, ensuring it doesn’t weaken excessively during bending.
Evaluates how material behaves when bent along different axes (e.g., longitudinal vs. transverse), ensuring flexibility in design.
Ensures the 3D geometry of the bent part matches the design specifications with high accuracy.
Ensures that the material can resist corrosion along grain boundaries after bending, especially for high-alloy metals.
Accelerating Automotive Manufacturing with Precision Bending
Achieving precise, high-quality automotive parts can be challenging, especially when dealing with complex geometries. Sheet metal bending services solves this problem by delivering accurate, repeatable bends for intricate automotive components. Advanced CNC bending technology ensures tight tolerances, minimizing defects and guaranteeing a perfect fit for every part. This process reduces material waste, speeds up production, and enhances the strength and durability of automotive components.








Industries We Serve
- Solid Progress
Our Manufacturing metrics
Frigate brings stability, control, and predictable performance to your sourcing operations through a structured multi-vendor system.

2.8X
Sourcing Cycle Speed
Frigate’s pre-qualified network shortens decision time between RFQ and PO placement.
94%
On-Time Delivery Rate
Structured planning windows and logistics-linked schedules improve project-level delivery reliability.
4X
Multi-Part Consolidation
We enable part family batching across suppliers to reduce fragmentation.
22%
Quality Rejection Rate
Multi-level quality checks and fixed inspection plans lower non-conformities.
30%
Procurement Costs
Optimized supplier negotiations and bulk order strategies reduce your overall sourcing expenses.
20%
Manual Processing Time
Automation of sourcing and supplier management significantly reduces time spent on manual tasks.
Achieving Complex Geometries with Custom Tooling Solutions
Frigate’s custom-designed tooling allows for the precise production of intricate shapes and tight radii that conventional methods cannot achieve. This specialized tooling enables the accurate bending of complex geometries, ensuring exact alignment with design specifications. It provides the flexibility to create highly detailed parts with enhanced functionality, meeting the unique needs of various industries.

Get Clarity with our Manufacturing Insights
- Real Impact
Words from Clients
See how global OEMs and sourcing heads describe their experience with our scalable execution.
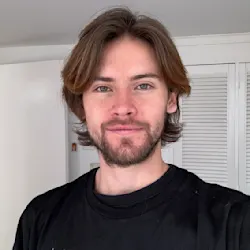
“Quick turnaround and solid quality.”
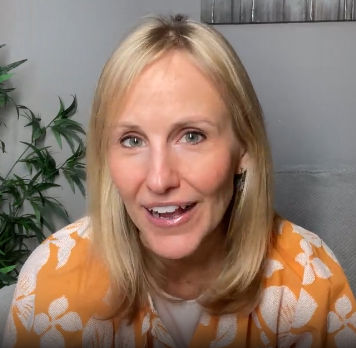
“The instant quote tool saved us time, and the parts were spot-on. Highly recommend Frigate!”
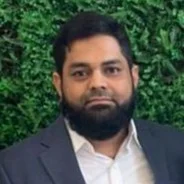
“I would strongly recommend Frigate to anyone who wants to do Rapid Prototyping, and take their ideas to manufacturing. One firm doing all kinds of Product Development!”
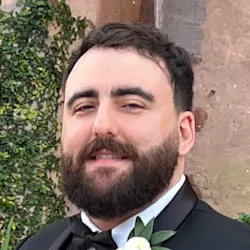
“Great service, fair price, and the parts worked perfectly in our assembly.”
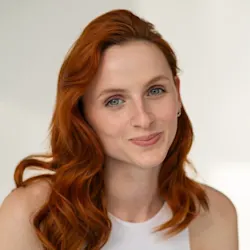
“Top-notch machining and fast shipping. Very satisfied with the results.”
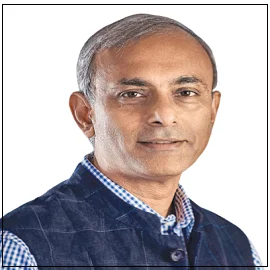
“The next disruption is happening in Prototyping & Manufacturing on-demand and Frigate is leading the way! I personally believe the Frigate's way of IIOT enabled cloud platform with Al.”
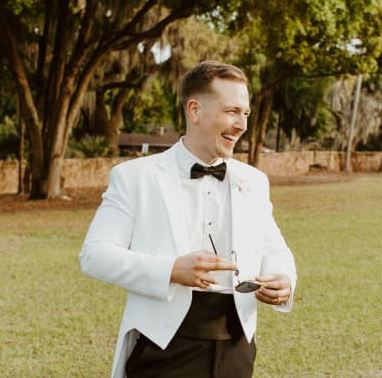
“Frigate delivered high-quality parts at a competitive price. The instant quote tool is a huge plus for us!”

“We appreciate the precision and quality of the machined components in the recent delivery—they meet our specifications perfectly and demonstrate Frigate’s capability for excellent workmanship.”
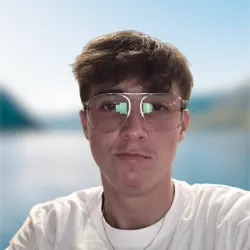
“Flawless execution from quote to delivery.”

“I am absolutely happy to work with supplier like Frigate who were quite proactive & result oriented . Frigate has high willingness team who has strong know how & their passion towards the products & process were absolutely thrilling.”
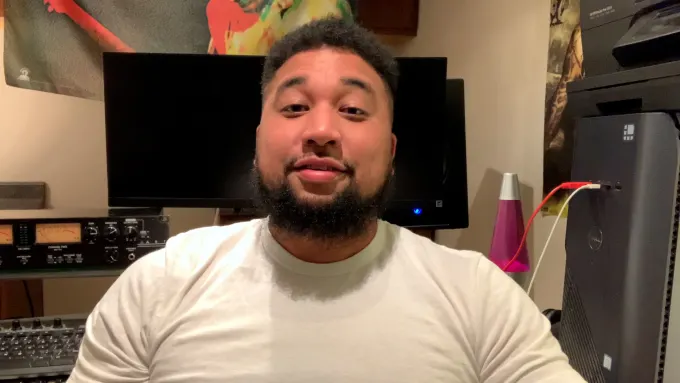
“The precision on these parts is impressive, and they arrived ahead of schedule. Frigate’s process really stands out!”
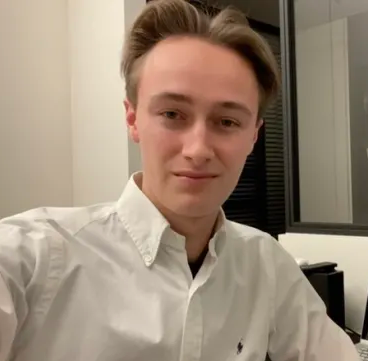
“Parts were exactly as spec’d, and the instant quote made budgeting a breeze.”
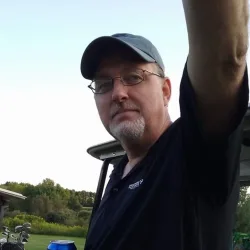
“Good value for the money.”
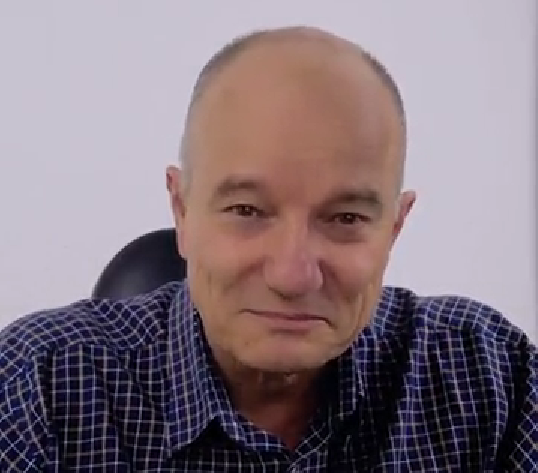
“The finish was perfect, and the team was easy to work with.”

“Working with Frigate has been great. Their proactive, results-driven approach and expertise shine through in every project. It's been a pleasure collaborating with them.”

"We are highly satisfied with the timely delivery and quality of the MIG Welding Cable from Frigate. Their attention to detail, secure packaging, and quick responsiveness stood out. We confidently recommend Frigate Engineering Services Pvt. Ltd. as a reliable manufacturing partner."
Having Doubts? Our FAQ
Check all our Frequently Asked Question
Frigate employs advanced finite element analysis (FEA) simulations to predict material behavior during bending. This allows for precise adjustments in tooling and process parameters, minimizing material deformation and ensuring consistent results across complex geometries.
The grain direction significantly affects the metal’s strength and flexibility during bending. Frigate carefully considers the grain orientation to optimize bend quality, reduce cracking, and maintain part integrity, especially in high-strength alloys like stainless steel.
Frigate utilizes robotic automation and real-time process monitoring in its CNC bending systems. This ensures high repeatability and minimal variation in bend angles and radii, even in large batches, by continuously adjusting for material inconsistencies and tool wear.
Frigate uses specialized algorithms in CNC software to calculate the required pre-bend force, compensating for the spring-back effect. This ensures that high-strength materials, like titanium and high-carbon steels, retain their intended shape after bending without distortion.
Frigate uses precise control of bending forces and carefully selected tooling to minimize surface contact and avoid damage. Frigate employs protective coatings and optimized bending techniques to preserve the material’s surface integrity for materials sensitive to scratches or markings, such as aluminum or brass.
We'd love to Manufacture for you!
Submit the form below and our representative will be in touch shortly.
LOCATIONS
Global Sales Office
818, Preakness lane, Coppell, Texas, USA – 75019
Registered Office
10-A, First Floor, V.V Complex, Prakash Nagar, Thiruverumbur, Trichy-620013, Tamil Nadu, India.
Operations Office
9/1, Poonthottam Nagar, Ramanandha Nagar, Saravanampatti, Coimbatore-641035, Tamil Nadu, India. ㅤ
Other Locations
- Bhilai
- Chennai
- Texas, USA