Bridge Molding Services
Bridge molding is a rapid, cost-efficient solution for transitioning from prototyping to full-scale production. Frigate ensures seamless scalability with minimal tooling adjustments, reducing lead times for high-volume manufacturing.
Our Clients





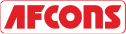

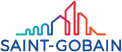


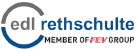

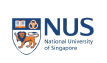
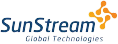

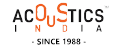




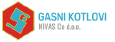
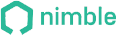
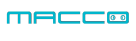












Advantages of Bridge Molding with Frigate
Tooling Optimization
Bridge molding uses low-cost, temporary tooling that mimics final production molds, allowing for design validation without fully investing in hardened steel molds.
Dimensional Precision
Bridge molding ensures tight tolerances and accurate geometries, offering near-production-quality parts that meet end-use applications' specifications.
Material Compatibility
Bridge molding accommodates a range of engineering-grade thermoplastics and elastomers, providing flexibility for high-performance materials in demanding applications.
Iterative Refinement
It allows engineers to refine product designs and validate part functionality in real-world conditions before committing to final, costly production tooling.
Minimizing Extended Lead Times
Extended lead times in bridge molding arise from complex tooling setups and development processes. These delays often hinder customers from achieving faster time-to-market. Frigate addresses this challenge by implementing rapid tooling techniques using prototype molds, significantly reducing setup times. Advanced manufacturing processes and streamlined production workflows enable quicker part production, ensuring faster lead times. This allows parts to be manufactured while the final tooling is developed, effectively reducing delays.

Get Your Quote Now
- Instant Quotation
- On-Time Delivery
- Affordable Cost
Our Bridge Molding Process






The process begins with detailed part design and CAD modeling, ensuring precise specifications and requirements for the intended application.
Temporary tooling is created using low-cost materials. It is a prototype mold designed to produce initial parts without needing expensive, permanent molds.
Suitable materials are chosen based on the part requirements, considering factors like strength, flexibility, and thermal properties to ensure optimal performance.
The selected material is heated and injected into the temporary mold under controlled conditions, allowing it to fill the cavity and take the desired shape.
After the material cools and solidifies, the molded part is removed from the mold. This step ensures that the part retains its intended geometry and dimensional accuracy.
Each part undergoes rigorous inspection to verify dimensional tolerances and surface finish. Adjustments are made as necessary to ensure the part meets all quality standards before moving to full production.
Bridge Molding Materials
Bridge Molding utilizes advanced thermoplastic materials for optimal performance and durability. Our selection ensures superior strength, precision, and chemical resistance for diverse applications.
ABS is known for its strength and impact resistance. It is commonly used for durable parts in automotive, electronics, and consumer products. It offers good dimensional stability and is easy to mold.
Polypropylene is a lightweight, flexible material with excellent chemical resistance. It's ideal for durable parts in harsh environments, such as medical devices and automotive components.
Polycarbonate is highly transparent, with excellent toughness and heat resistance. Due to its clarity and strength, this material is commonly used in optical devices, lighting components, and safety applications.
Nylon provides high mechanical strength and wear resistance, making it suitable for parts exposed to friction or high-stress environments. It's widely used in gears, bushings, and structural components.
TPEs combine the flexibility of rubber with the processability of plastics, allowing for soft-touch components. These are used in grips, seals, and over-molded parts where flexibility and comfort are essential.
Polyethylene offers excellent chemical resistance and low moisture absorption, making it ideal for packaging, containers, and insulation. It is also used in parts requiring lightweight and flexibility.
Polystyrene is a low-cost material with good dimensional stability and ease of molding. It is often used in consumer products, medical devices, and packaging.
PBT is a strong, heat-resistant material used in automotive parts, electrical components, and industrial applications. It has excellent wear resistance and dimensional stability under heat.
Custom Bridge Molding for Enhanced Manufacturing Efficiency
Custom bridge molding offers a rapid transition from prototype to production, ensuring high precision in part manufacturing. This process utilizes low-cost, temporary tooling mimics final production molds, minimizing upfront investment. Quick design validation and functional testing are integral to the approach, allowing for iterative refinement before full-scale production. The technique streamlines workflows, significantly reducing lead times and costs while maintaining dimensional accuracy. Custom bridge molding facilitates scalability, efficiently and flexibly bridging the gap between initial concepts and mass production.

Compliance for Bridge Molding Services
Bridge molding requires precise engineering and adherence to strict industry standards, ensuring safety, performance, and reliability in critical applications. Frigate meets high compliance standards for every part produced, focusing on stringent material properties, process control, and dimensional accuracy. Our commitment ensures that each molded component meets the exacting demands of industries such as aerospace and automotive.
Specifies strict quality management for defect control, ensuring consistent production and customer satisfaction in complex molding projects.
Regulates hazardous substances in polymers and alloys, ensuring components are environmentally compliant and safe for global markets.
Enforces secure manufacturing and documentation for defense-related bridge molds, safeguarding sensitive data and export-controlled items.
Requires certified sourcing of specialty metals for military use, ensuring compliance with U.S. defense material standards.
Ensures precise dimensioning and tolerancing for complex geometries, which is crucial for maintaining part integrity and tight tolerances.
Validates molding processes through detailed documentation and testing, ensuring part consistency and readiness for large-scale production.
Standardizes nickel and cobalt alloy properties, ensuring reliability in high-temperature bridge molding applications.
Governs hard chrome plating, ensuring wear resistance and durability for molded parts subjected to extreme stress.

Tolerance for Bridge Molding Services
Precision control for linear measurements to ensure accurate fitment in complex bridge structures and assemblies.
High precision required for critical hole diameters, ensuring compatibility with fasteners and other mating components.
Precision in angles for molded parts, critical for correct component assembly and alignment in bridge molds.
Tight control of wall thickness to prevent distortion during molding and maintain the strength of the final part.
Ensures accurate thread depths for fastener compatibility and maintaining structural integrity in molded parts.
Control of cavity dimensions to ensure uniformity in molding, preventing defects or weak points in the final product.
Ensures that holes or features are precisely aligned along a common axis, critical for component functionality.
Ensures that surfaces, especially for mating parts, are flat within tight tolerances, improving performance and reducing wear.
Ensures that rotating parts are perfectly aligned during assembly, reducing potential for defects in high-performance applications.
Ensures that surfaces are perpendicular to specified features, ensuring correct part assembly and alignment.
Tolerance that controls the overall form of a surface, crucial for components with complex shapes that must fit seamlessly together.
Ensures accurate radii and fillets for stress distribution and part durability, especially for high-stress components in bridge molds.
Accounts for material shrinkage during cooling, ensuring final dimensions stay within tolerance and function as designed.
Control of the surface finish, critical for reducing friction and wear in high-contact areas of the molded components.
Ensures parallel walls to minimize distortion during molding, preventing defects in tight tolerance applications.

Quality Testing Standards for Bridge Molding Services
Measures the deformation of a material under constant stress over time to ensure long-term dimensional stability in high-stress environments.
Tests material’s ability to withstand thermal fluctuations without structural damage, ensuring reliable performance in extreme temperature conditions.
Ensures that parts do not emit electromagnetic interference or are susceptible to it, critical for electronic and communications systems.
Measures how the material expands and contracts with temperature changes, ensuring dimensional stability during temperature fluctuations.
Assesses the absorption of moisture in materials, which can impact the mechanical properties, ensuring performance in humid environments.
Evaluates the wear resistance of materials by simulating real-world frictional wear, ensuring durability in moving components.
Ensures parts can withstand vibrational stresses without failure, critical for applications in aerospace, automotive, and heavy machinery.
Exposes materials to salt mist to simulate corrosion over time, ensuring durability in harsh outdoor or marine environments.
Measures the material’s stiffness (modulus) under tensile stress, important for assessing load-bearing capacity under dynamic conditions.
Assesses the ability of materials to be molded into complex shapes without failure, critical for intricate designs in bridge molding.
Measures the decrease in stress over time at constant strain, helping to evaluate materials under long-term loading conditions.
Evaluates the strength of bonds between different materials or coatings, ensuring secure bonding during the molding process.
Measures the hardness at specific points on small or complex features, critical for assessing wear and durability in intricate molding designs.
Measures the ability of materials to stretch without breaking, ensuring parts can undergo deformation without failure.
Detects high-frequency sound waves generated by material stress or defects, used for early detection of potential failures in molded parts.
Accelerating Automotive Innovation
The automotive industry often struggles with high production costs and long lead times. Bridge molding solves these issues by enabling rapid production of prototypes and low-volume parts using temporary tooling, which reduces upfront costs significantly. This process allows for quick design validation and adjustments, ensuring parts meet specifications before mass production. By streamlining the development cycle, bridge molding enhances efficiency and accelerates time-to-market, resulting in high-quality components that meet industry demands.




Industries We Serve
- Solid Progress
Our Manufacturing metrics
Frigate brings stability, control, and predictable performance to your sourcing operations through a structured multi-vendor system.
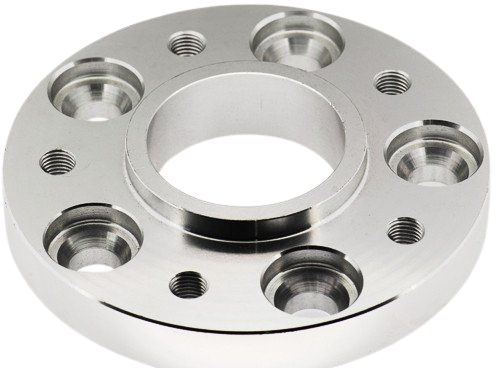
2.8X
Sourcing Cycle Speed
Frigate’s pre-qualified network shortens decision time between RFQ and PO placement.
94%
On-Time Delivery Rate
Structured planning windows and logistics-linked schedules improve project-level delivery reliability.
4X
Multi-Part Consolidation
We enable part family batching across suppliers to reduce fragmentation.
22%
Quality Rejection Rate
Multi-level quality checks and fixed inspection plans lower non-conformities.
30%
Procurement Costs
Optimized supplier negotiations and bulk order strategies reduce your overall sourcing expenses.
20%
Manual Processing Time
Automation of sourcing and supplier management significantly reduces time spent on manual tasks.
Mitigating High Initial Tooling Costs in Molding Processes
High initial tooling costs in traditional molding can hinder production commitments and lead to financial risks if designs fail to meet market needs. Frigate offers prototype molding solutions using temporary tooling, allowing for lower-cost initial investments and rapid production of test parts. This approach enables design validation before committing to expensive, permanent molds, reducing financial risk and enhancing efficiency in the development process.

Get Clarity with our Manufacturing Insights
- Real Impact
Words from Clients
See how global OEMs and sourcing heads describe their experience with our scalable execution.
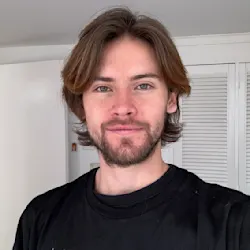
“Quick turnaround and solid quality.”
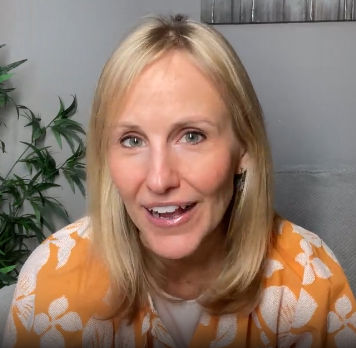
“The instant quote tool saved us time, and the parts were spot-on. Highly recommend Frigate!”
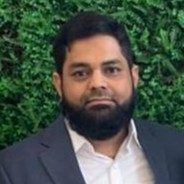
“I would strongly recommend Frigate to anyone who wants to do Rapid Prototyping, and take their ideas to manufacturing. One firm doing all kinds of Product Development!”
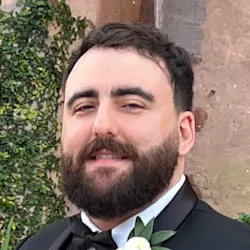
“Great service, fair price, and the parts worked perfectly in our assembly.”
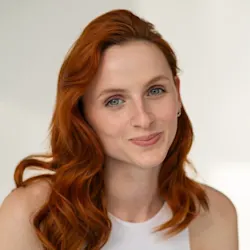
“Top-notch machining and fast shipping. Very satisfied with the results.”
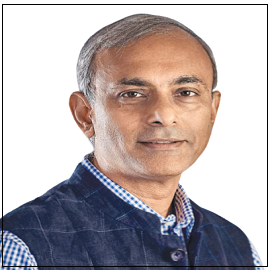
“The next disruption is happening in Prototyping & Manufacturing on-demand and Frigate is leading the way! I personally believe the Frigate's way of IIOT enabled cloud platform with Al.”
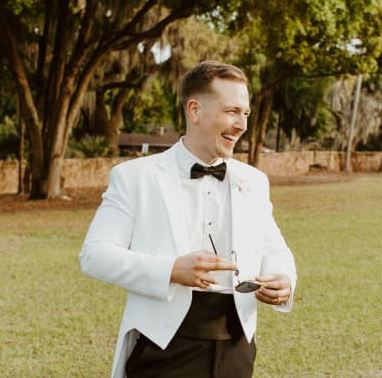
“Frigate delivered high-quality parts at a competitive price. The instant quote tool is a huge plus for us!”

“We appreciate the precision and quality of the machined components in the recent delivery—they meet our specifications perfectly and demonstrate Frigate’s capability for excellent workmanship.”
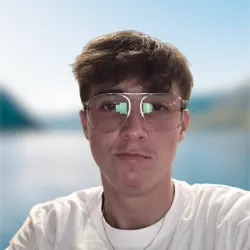
“Flawless execution from quote to delivery.”

“I am absolutely happy to work with supplier like Frigate who were quite proactive & result oriented . Frigate has high willingness team who has strong know how & their passion towards the products & process were absolutely thrilling.”
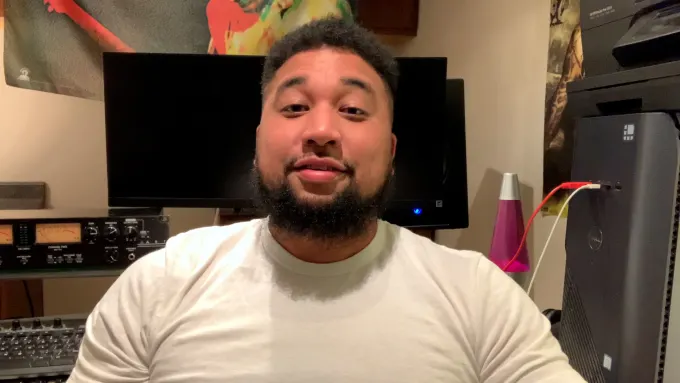
“The precision on these parts is impressive, and they arrived ahead of schedule. Frigate’s process really stands out!”
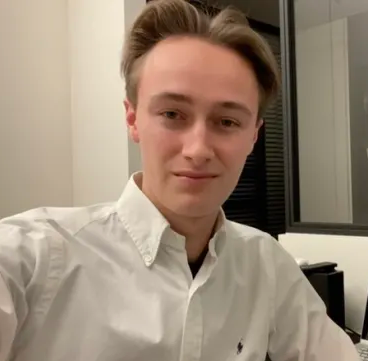
“Parts were exactly as spec’d, and the instant quote made budgeting a breeze.”
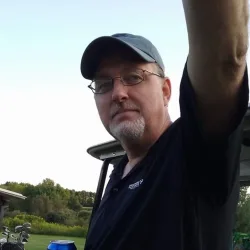
“Good value for the money.”
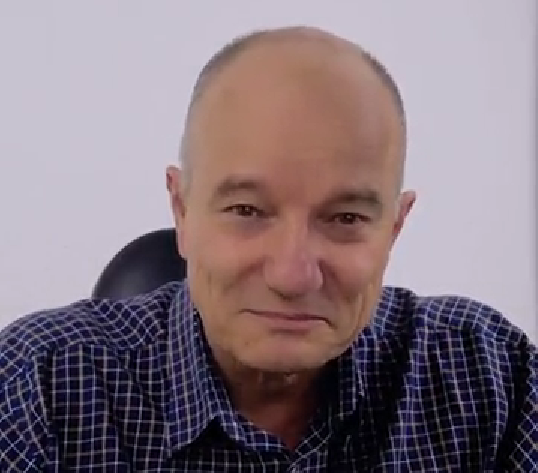
“The finish was perfect, and the team was easy to work with.”

“Working with Frigate has been great. Their proactive, results-driven approach and expertise shine through in every project. It's been a pleasure collaborating with them.”

"We are highly satisfied with the timely delivery and quality of the MIG Welding Cable from Frigate. Their attention to detail, secure packaging, and quick responsiveness stood out. We confidently recommend Frigate Engineering Services Pvt. Ltd. as a reliable manufacturing partner."
Having Doubts? Our FAQ
Check all our Frequently Asked Question
Lead times for bridge molding can range from a few days to several weeks, depending on the complexity of the part and the tooling required. Rapid prototyping techniques help significantly minimize these times.
Bridge molding uses temporary tooling to produce parts quickly and cost-effectively, while traditional injection molding relies on permanent molds that require significant upfront investment. This allows for faster design validation in bridge molding.
Suitable materials for bridge molding include thermoplastics like ABS, polypropylene, and nylon. These materials provide the necessary strength and flexibility while being easy to process within temporary molds.
When designing parts for bridge molding, it's essential to consider wall thickness, draft angles, and tolerances. These factors influence moldability and ensure that parts can be produced accurately and efficiently.
Yes, bridge molding can handle complex geometries, although certain limitations may apply due to the temporary tooling. Designers should collaborate closely with engineers to ensure intricate features can be effectively produced without compromising quality.
We'd love to Manufacture for you!
Submit the form below and our representative will be in touch shortly.
LOCATIONS
Global Sales Office
818, Preakness lane, Coppell, Texas, USA – 75019
Registered Office
10-A, First Floor, V.V Complex, Prakash Nagar, Thiruverumbur, Trichy-620013, Tamil Nadu, India.
Operations Office
9/1, Poonthottam Nagar, Ramanandha Nagar, Saravanampatti, Coimbatore-641035, Tamil Nadu, India. ㅤ
Other Locations
- Bhilai
- Chennai
- Texas, USA