Multi-Axis Machining Services
Frigate’s Multi-Axis Machining delivers high precision for complex geometries and features. It combines advanced tool control with dynamic movement for intricate designs.
Our Clients





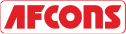

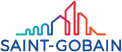


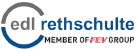

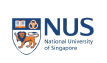
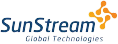

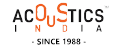




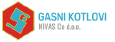
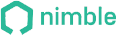
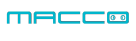












Advantages of Multi-Axis Machining Services
Complex Feature Integration
Multi-axis machining allows for simultaneous movement across multiple axes, enabling the production of intricate geometries with enhanced feature integration.
Minimized Tool Wear
Using multiple axes, tools engage with the material at optimal angles, reducing wear and increasing tool life during extended machining operations.
Enhanced Material Utilization
The ability to machine from various angles minimizes waste and optimizes material use, improving yield and cost-effectiveness.
Higher Efficiency in Manufacturing
Multi-axis systems reduce the need for multiple setups, streamlining production workflows and significantly decreasing cycle times for complex parts.
Maximize Accuracy with Custom Multi-Axis Machining
Custom Multi-Axis Machining delivers precise solutions for complex parts, eliminating the need for multiple setups. Whether it’s high accuracy, reduced cycle times, or intricate geometries, this service allows for efficient, high-quality results with minimal material waste. By machining from multiple angles, you achieve superior surface finishes and tighter tolerances that traditional methods can’t provide. Say goodbye to time-consuming setups and costly rework—embrace the precision and efficiency of custom multi-axis machining for your most challenging projects.

Get Your Quote Now
- Instant Quotation
- On-Time Delivery
- Affordable Cost
Our Multi-Axis Machining Process






The process begins with creating a 3D CAD model of the part to be machined. This model defines all the geometrical features and dimensions required for precise machining.
Once the model is ready, the toolpath is generated using CAM (Computer-Aided Manufacturing) software. This path guides the machine in moving the cutting tools along multiple axes to shape the part.
The workpiece is securely mounted on the multi-axis machining center. Fixtures or clamps hold the part in place while ensuring accurate positioning for all axes.
The machine starts the machining process, with the cutting tool moving across multiple axes (typically 3 to 5). This enables the tool to access the part from different angles, machining complex features in a single setup.
As machining progresses, the operator monitors the process for accuracy, adjusting feed rates, speeds, and cutting depths to maintain precision and surface finish.
After the machining process, the part undergoes inspection to ensure it meets design specifications. Any necessary finishing, such as deburring or surface smoothing, is performed to complete the part.
Multi-Axis Machining Materials
Multi-axis machining creates complex, precise components by moving the tool across multiple axes. This process ensures high efficiency and accuracy for intricate geometries and tight tolerances.
Lightweight, corrosion-resistant, and highly versatile, aluminum alloys like 6061 and 7075 are commonly used for multi-axis machining. These alloys offer excellent machinability, making them ideal for aerospace, automotive, and precision engineering applications. Their low density also contributes to faster machining speeds.
It is known for its strength, durability, & resistance to corrosion; stainless steel is often used in industries requiring high-performance parts. Grades such as 304 and 316 are commonly machined using multi-axis machines due to their toughness and ability to withstand harsh environments. It makes them ideal for medical, automotive, and food processing industries.
Titanium and its alloys, such as Ti-6Al-4V, are strong yet lightweight metals with excellent resistance to corrosion and high temperatures. These properties make them perfect for aerospace, medical, and high-performance manufacturing, although due to their strength and hardness, they are more difficult to machine.
Brass and copper are used for applications that require good conductivity, corrosion resistance, and a smooth surface finish. These materials are easier to machine than harder metals and are widely used in electrical, plumbing, and precision mechanical components.
It is one of the lightest metals, offering high strength-to-weight ratios and excellent machinability. Commonly used in automotive and aerospace industries, magnesium alloys are ideal for parts that require weight reduction without compromising strength.
Advanced thermoplastics like PEEK and composites reinforced with carbon or glass fibers can be machined using multi-axis machines. These materials are known for their high strength-to-weight ratios, chemical resistance, and electrical properties, making them ideal for industries like electronics, aerospace, and medical devices.
Nickel-based alloys, including Inconel and Hastelloy, are known for their high strength, toughness, and resistance to extreme temperatures. They are commonly used in the aerospace and energy sectors, where components must withstand high-stress environments and corrosive conditions.
Efficiently Achieve Complex Geometries with Multi-Axis Machining
Due to limited access from various angles, traditional machining methods struggle with intricate parts. Multi-axis machining at Frigate enables simultaneous movement along multiple axes, allowing for precision machining of complex features in a single setup. This reduces the need for repositioning the workpiece, which minimizes errors and improves part accuracy. The ability to machine intricate geometries in one operation ensures greater detail and efficiency, meeting tight tolerances for advanced designs.

Compliance for Multi-Axis Machining Services
We strictly adhere to industry standards to ensure the highest quality and precision in our Multi-axis Machining services. We follow rigorous regulations that ensure the reliability, safety, and sustainability of every component produced. Our machining processes align with key certifications guaranteeing consistent performance across aerospace, automotive, and medical industries.
Certification No. 12345678: A quality management system for process control and customer satisfaction.
Certification No. 23456789: Aerospace industry-specific quality management standards for high-precision components.
Certification No. EU-123456: Restriction of hazardous substances to ensure environmental safety.
Certification No. 34567890: Environmental management system for sustainable manufacturing practices.
Registration No. M12345678: Compliance with export control regulations for defense-related products.

Tolerance for Multi-Axis Machining Services
Controls deviation of a rotating part’s surface, ensuring uniformity in circular motion.
Ensures that holes and features are positioned within a specified tolerance relative to datum points.
Specifies how flat a surface is, essential for ensuring contact and sealing surfaces are true.
Ensures that two features are at a 90-degree angle with high accuracy, preventing misalignment in assemblies.
Controls the parallel alignment between two surfaces or axes to ensure uniform gap or contact.
Ensures that the center of two or more circular features are aligned to a common center point.
Specifies the micro-texture of the surface, critical for functional and aesthetic requirements.
Measures the angular difference between two surfaces or features to ensure proper orientation.
Ensures that both sides of a part are evenly distributed, critical for balanced load-bearing components.
Specifies the amount of chamfer or fillet at part edges to prevent stress concentrations and improve handling.
Precision in the distance between threads for consistent mating with fasteners or components.
Controls the deviation in the helix angle of threaded components, ensuring precise fitment and performance.
Ensures that hole diameters are produced with exact precision, critical for press fits or fastener alignment.
Ensures that cylindrical or circular features remain within tolerance, preventing deviations in rotating parts.
Defines the rate at which material is removed during machining, directly impacting production efficiency and finish quality.

Quality Testing Standards for Multi-Axis Machining Services
Measures the machine’s ability to follow a precise circular path, ensuring accurate curve generation.
Verifies the synchronization between multiple axes during multi-axis machining to prevent misalignment.
Assesses the condition of tools in real-time to detect wear, which can affect machining accuracy and surface finish.
Measures temperature-induced changes in the workpiece or machine tool to assess the effects of heat on precision.
Monitors machine vibrations during operation to ensure smooth machining, preventing errors in part geometry.
Assesses the effectiveness of chip removal processes to ensure they do not affect part quality or machining efficiency.
Identifies the presence of burrs or sharp edges on machined parts, which may affect functionality or safety.
Measures and compensates for any mechanical backlash in the machine’s movement to improve accuracy in part production.
Tests the deflection of cutting tools under load to ensure machining precision and part integrity.
Verifies the accuracy of the machine’s helical motion, essential for parts with complex spiral features.
Measures the machine's ability to consistently reproduce the same part with minimal deviation between cycles.
Assesses the operational condition of the spindle, ensuring that it maintains high performance without excessive runout or instability.
Measures the torsional stiffness of the machine and tools, ensuring resistance to twisting forces that can affect machining precision.
Non-destructive testing to detect internal flaws like cracks or voids in machined parts, ensuring structural integrity.
Measures any distortion or warping of the workpiece during machining, ensuring it remains within tolerance.
Reduce Costs and Improve Quality in Aerospace Components
Aerospace parts require complex geometries and tight tolerances. Traditional machining methods struggle to meet these needs. This leads to longer production times and higher costs. Multi-axis machining solves these issues by enabling precise, efficient machining in a single setup. It allows for greater design flexibility and faster turnaround times. Reduced material waste is another key benefit. Working across multiple axes improves accuracy and surface finish. This ensures high-quality, high-performance components for aerospace applications.








Industries We Serve
- Solid Progress
Our Manufacturing metrics
Frigate brings stability, control, and predictable performance to your sourcing operations through a structured multi-vendor system.
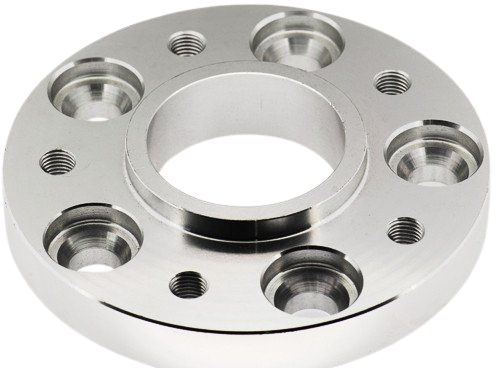
2.8X
Sourcing Cycle Speed
Frigate’s pre-qualified network shortens decision time between RFQ and PO placement.
94%
On-Time Delivery Rate
Structured planning windows and logistics-linked schedules improve project-level delivery reliability.
4X
Multi-Part Consolidation
We enable part family batching across suppliers to reduce fragmentation.
22%
Quality Rejection Rate
Multi-level quality checks and fixed inspection plans lower non-conformities.
30%
Procurement Costs
Optimized supplier negotiations and bulk order strategies reduce your overall sourcing expenses.
20%
Manual Processing Time
Automation of sourcing and supplier management significantly reduces time spent on manual tasks.
Reduce Lead Times and Setup Costs with Streamlined Multi-Axis Machining
Multiple setups in conventional machining increase production time and costs. Multi-axis machining at Frigate consolidates these operations into one setup, reducing the need for repositioning and handling. This approach minimizes the chances of misalignment and tooling errors, improving both efficiency and consistency. The ability to complete more operations per setup cuts lead times and lowers overall production costs, making the process more cost-effective.

Get Clarity with our Manufacturing Insights
- Real Impact
Words from Clients
See how global OEMs and sourcing heads describe their experience with our scalable execution.
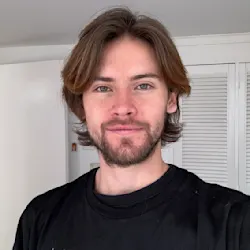
“Quick turnaround and solid quality.”
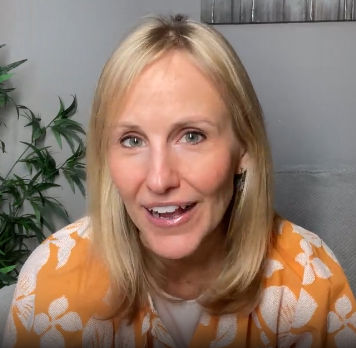
“The instant quote tool saved us time, and the parts were spot-on. Highly recommend Frigate!”
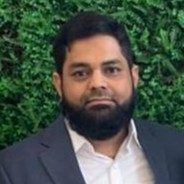
“I would strongly recommend Frigate to anyone who wants to do Rapid Prototyping, and take their ideas to manufacturing. One firm doing all kinds of Product Development!”
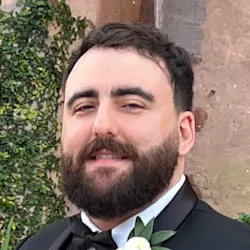
“Great service, fair price, and the parts worked perfectly in our assembly.”
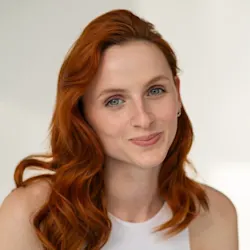
“Top-notch machining and fast shipping. Very satisfied with the results.”
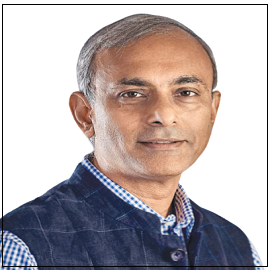
“The next disruption is happening in Prototyping & Manufacturing on-demand and Frigate is leading the way! I personally believe the Frigate's way of IIOT enabled cloud platform with Al.”
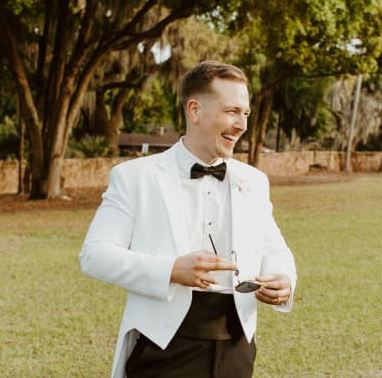
“Frigate delivered high-quality parts at a competitive price. The instant quote tool is a huge plus for us!”

“We appreciate the precision and quality of the machined components in the recent delivery—they meet our specifications perfectly and demonstrate Frigate’s capability for excellent workmanship.”
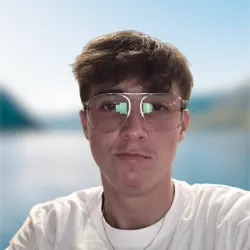
“Flawless execution from quote to delivery.”

“I am absolutely happy to work with supplier like Frigate who were quite proactive & result oriented . Frigate has high willingness team who has strong know how & their passion towards the products & process were absolutely thrilling.”
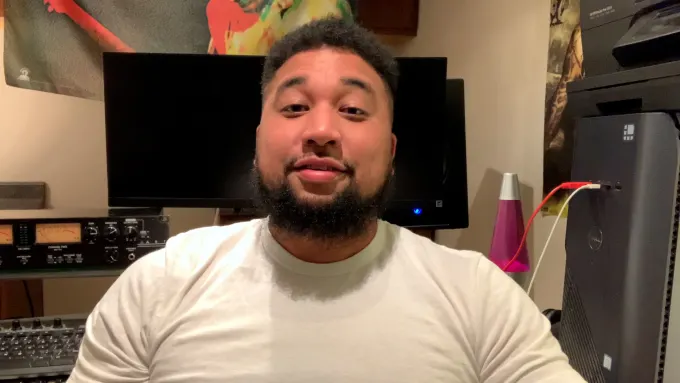
“The precision on these parts is impressive, and they arrived ahead of schedule. Frigate’s process really stands out!”
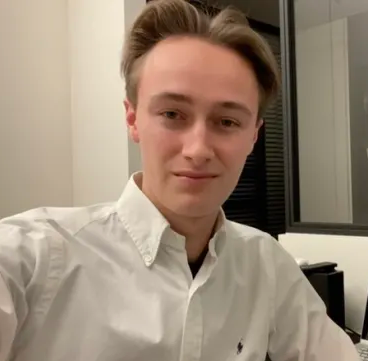
“Parts were exactly as spec’d, and the instant quote made budgeting a breeze.”
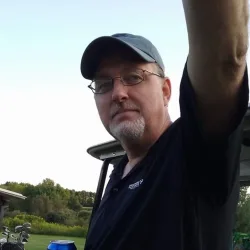
“Good value for the money.”
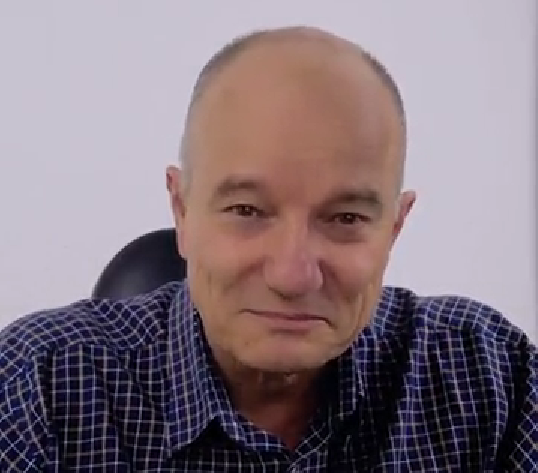
“The finish was perfect, and the team was easy to work with.”

“Working with Frigate has been great. Their proactive, results-driven approach and expertise shine through in every project. It's been a pleasure collaborating with them.”

"We are highly satisfied with the timely delivery and quality of the MIG Welding Cable from Frigate. Their attention to detail, secure packaging, and quick responsiveness stood out. We confidently recommend Frigate Engineering Services Pvt. Ltd. as a reliable manufacturing partner."
Having Doubts? Our FAQ
Check all our Frequently Asked Question
Multi-axis machining at Frigate minimizes the need for part repositioning, reducing the risk of misalignment. Holding the workpiece in a fixed position while machining from multiple angles ensures precise geometry and tight tolerances, improving overall accuracy and reducing setup errors.
Multi-axis machining at Frigate allows for simultaneous tool movement across multiple axes, enabling the production of intricate aerospace components. This capability allows the machining of parts with multiple features, such as complex contours and deep pockets, in a single setup, reducing lead times and improving production efficiency.
Frigate’s multi-axis machining reduces production time by eliminating the need for multiple setups. By machining complex features and angles in one operation, this technology streamlines the process, minimizes downtime, and enhances efficiency, allowing for faster delivery of high-precision parts.
Frigate’s multi-axis machining enhances surface finish and overall part quality by using precise movements and advanced cutting tools. The ability to machine from different angles ensures smoother surfaces, better detail, and reduced post-processing, which is essential for high-performance components in aerospace and medical manufacturing industries.
Multi-axis machining at Frigate optimizes material usage by machining parts in fewer steps, reducing scrap material. The ability to create complex geometries in a single setup reduces the need for excess material, lowering both material waste and overall production costs and making it a more cost-effective solution for complex parts.
We'd love to Manufacture for you!
Submit the form below and our representative will be in touch shortly.
LOCATIONS
Global Sales Office
818, Preakness lane, Coppell, Texas, USA – 75019
Registered Office
10-A, First Floor, V.V Complex, Prakash Nagar, Thiruverumbur, Trichy-620013, Tamil Nadu, India.
Operations Office
9/1, Poonthottam Nagar, Ramanandha Nagar, Saravanampatti, Coimbatore-641035, Tamil Nadu, India. ㅤ
Other Locations
- Bhilai
- Chennai
- Texas, USA