Sand Casting Services
Frigate is a leading global manufacturer offering top-quality sand casting solutions. Sand casting is one of the industry’s most cost-effective, efficient, and widely used methods, ideal for reducing lead times and costs.
Our Clients





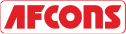

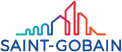


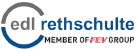

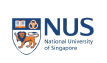
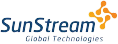

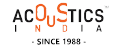




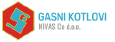
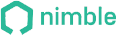
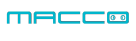












Advantages of Sand Casting with Frigate
Flexible Product Shapes
Sand castings offer great flexibility when it comes to product shapes. The main restriction involves the need for draft angles on flat surfaces that run perpendicular to the parting line. With the right patterns, tooling, molding sands, and careful foundry techniques, even intricate details can be achieved using various metal alloys.
Dimensional Control
Sand castings' dimensional control and consistency typically range from ±0.030 to ±0.125 inches (0.8 to 3.2 mm). These tolerances depend on the size and design of the parts, with the more lenient tolerances usually found across the parting line.
Surface Finishes
Surface finishes for sand castings range between 300 and 500 µin (7.7 - 12.9 µm) RMS. Common finishes include machine finish, shot blast, painted (hand, spray, or dipped), powder coating, chrome, tin plating, acid etching, anodizing, galvanizing, and durable polyamide coatings like Rilsan.
Cost-Effective Process
Compared to other manufacturing methods, sand casting is relatively inexpensive. It can accommodate almost any metal, and depending on customer requirements, parts can be delivered in their raw state or fully machined and coated.
Custom Aluminum Sand Casting Solutions
We create custom patterns in wood or aluminum for use in the sand casting process, allowing us to produce both new and legacy metal parts. Whatever your industry, Frigate can deliver the metal components you need. Contact us today to schedule a consultation or request a quote!

Get Your Quote Now
- Instant Quotation
- On-Time Delivery
- Affordable Cost
Our Sand Casting Process







A replica of the desired part is made, usually from wood, plastic, or metal.
The pattern is placed into the sand, and the sand is tightly packed around it to form a mold.
Once the mold is set, the pattern is carefully removed, leaving a cavity in the shape of the part.
Molten metal is poured into the mold cavity.
The metal is left to cool and solidify within the mold.
After the metal hardens, the mold is broken to retrieve the casting.
The casting is cleaned, and additional finishing or machining is done to achieve the desired final product.
Post-Processing Services in Sand Casting
Post-processing enhances the quality, durability, and performance of sand-cast components. From surface finishing to precision machining, these processes refine raw castings to meet industry standards. Proper post-processing ensures improved mechanical properties, dimensional accuracy, and extended component lifespan.
Media: Steel Grit, Aluminum Oxide, Glass Beads
Automotive (engine blocks, transmission cases), Aerospace (housings)
Wheel Grit Size: 24-60
General Manufacturing (pump housings, brackets)
Soaking Time: 1-10 hrs
Cooling Rate: Air/Oil/Water
Automotive (gearboxes, crankshafts), Industrial (valve bodies)
Cutting Speed: 100-500 m/min (varies by material)
Aerospace (turbine components), Automotive (brake calipers)
Process: Powder Coating, Anodizing, Zinc Plating
Marine (propellers), Industrial Equipment (pumps, compressors)
Vacuum Level: -28 inHg, Resin Penetration: 90%+
Automotive (manifolds), Hydraulic Systems (valve bodies)
Ultrasonic (Freq: 1-10 MHz)
Dye Penetrant (Sensitivity: Level 3)
Aerospace (critical parts), Oil & Gas (pressure fittings)
Methoding in Sand Casting
Automotive (engine blocks, gear housings), Aerospace (structural parts)
Heavy Machinery (pump casings, turbine housings)
Industrial Equipment (compressor parts, motor housings)
Aerospace (thin-wall castings), Marine (propellers)
High-Precision Castings (medical devices, turbine blades)
Foundry Optimization (reducing turbulence & metal wastage)
Automotive & Industrial Components (reducing metal oxidation)
Aerospace (heat-resistant alloys), Tooling (die inserts)
Automotive (cylinder heads), Energy Sector (turbine casings)
Precision Components (gearboxes, aircraft fittings)

Sand Casting Materials
Frigate Sand Casting Services provides sand casting for aluminum, steel, iron, brass, and other materials. We handle everything from specialty parts to high-volume production runs. Sand casting is a fast, cost-effective solution for efficiently producing metal parts.
It is Lightweight & corrosion-resistant, ideal for automotive and aerospace parts.
Strong and durable, used in heavy machinery and structural components.
Cast iron offers excellent wear resistance and is suitable for engine blocks and pipes.
Corrosion-resistant with good electrical conductivity, often used in plumbing and electrical components.
Known for its strength and resistance to wear, it is used in bearings and gears.
Lightweight and strong, it is commonly used in the automotive and aerospace industries.
Great electrical and thermal conductivity, ideal for electrical parts.
Versatile Products Made with Sand Casting
Sand casting is perfect for producing large parts and offers flexibility in metal alloy choices. You can select from various available materials and part sizes, all at an affordable manufacturing cost. The process also features low setup costs, making mold modifications inexpensive. It’s preferred in aerospace, construction, automotive, manufacturing, and marine industries.

Compliance for Sand Casting Services
Frigate fully complies with industry standards for its Sand Casting services. It follows strict material specifications, process controls, and environmental guidelines. The company prioritizes quality and safety at every step, ensuring that each casting is precise and reliable. Our certifications demonstrate its commitment to customer satisfaction and operational excellence.
Key Compliance Standards
Certification for ductile iron castings, ensuring material strength and performance.
Quality management system certification, ensuring consistency and product traceability.
Environmental management certification, ensuring sustainable production practices.
Workplace safety compliance, following the Occupational Safety and Health Administration's standards.
Ensuring all sand casting materials meet the Restriction of Hazardous Substances Directive.
Tonnage / Capacity in Sand Casting
Understanding tonnage and capacity in sand casting is crucial for producing high-quality components across various industries. Factors such as casting weight, pouring temperature, and metal flow rate determine the precision, strength, and efficiency of the final product
Heavy Machinery (engine blocks, pump housings), Aerospace (structural parts)
Automotive (gear housings, brackets), Industrial (valve bodies)
Aerospace (aluminum castings), Oil & Gas (stainless steel valves)
Automotive (cylinder heads), Railway (wheel hubs)
High-precision castings for turbines, Marine (propellers)
Engine Components (cylinder heads, manifolds)
Aerospace (high-precision housings), Automotive (engine blocks)
Large Castings (industrial turbines, ship components)
Foundries producing large-scale industrial parts
Dimensions in Sand Casting
Precision in sand casting depends on accurate dimensional control to ensure high-performance components. Factors like mold size, casting thickness, and shrinkage allowance impact the final product’s quality and functionality.
Heavy Machinery (engine blocks, pump casings), Marine (ship components)
Aerospace (thin-wall turbine blades), Automotive (lightweight brackets)
Industrial Equipment (valve bodies, compressor housings)
Hydraulic Systems (fluid passages), Oil & Gas (pipeline fittings)
Automotive (gear housings), Aerospace (precision castings)
Die Molds (tooling components), Heavy Equipment (structural parts)
Industrial Machinery (machine beds), Railway (wheel hubs)
Automotive (engine components), Aerospace (aircraft fittings)
Medical Devices (implant housings), Power Generation (turbine frames)

Tolerance for Sand Casting Services
Accuracy based on part geometry, mold design, and material flow.
Tolerance on wall thickness and sections, affected by casting method and cooling rate.
Variation due to material and mold material used during cooling.
Deviation in core alignment, depending on part complexity and mold design.
Allowance for post-casting machining, including grinding or turning.
Measurement of voids or air pockets within the casting, depending on material and cooling.
Consistency of material distribution across the casting, influenced by mold venting and gating system.
Deviation of opposite walls from being parallel, influenced by mold setup and material shrinkage.
Variance in mold alignment during pouring, affecting dimensional accuracy.
The amount of gas retained in the core, impacting casting surface and integrity.
The average roughness of the surface, critical for fit and finish in some applications.
The uniformity of the sand grains affects the casting surface and mold strength.

Quality Testing Standards for Sand Casting Services
Detects internal porosity and voids that may compromise structural integrity or performance under load.
Measures the maximum tensile and yield strength of the material to ensure the casting can withstand applied forces without failure.
Evaluates the toughness of the casting by measuring its resistance to sudden impact or shock loading.
Assesses the casting’s ability to withstand cyclic loading without cracking or failing, critical for high-stress applications.
Determines the hardness of the casting material, providing insight into its wear resistance and ability to withstand deformation.
Tests the strength and integrity of the core material, ensuring it can endure the casting process without failure.
Measures the compressive and shear strength of the mold to ensure it maintains shape and support during casting and cooling.
Evaluates the material’s response to temperature changes, ensuring dimensional stability during the cooling phase.
Detects surface and near-surface cracks or defects that can affect the casting’s strength and longevity.
Measures the amount of gas released by the core material during casting, which could impact the quality of the final product.
Determines the density of the casting and detects any variations or inconsistencies in material distribution.
Inspection Techniques in Sand Casting
Value/Range - Qualitative (manual & automated)
Automotive (engine blocks), Machinery (pump housings)
Value/Range - ± 0.2 – ± 3 mm
Aerospace (structural components), Medical Devices (implant casings)
Value/Range - 1% – 5% defect sensitivity
Aerospace (turbine blades), Power Generation (turbine housings)
Value/Range - 1 – 10 MHz frequency range
Marine (ship propellers), Heavy Machinery (gear housings)
Value/Range - Detects 0.5 mm cracks & above
Automotive (brake calipers), Industrial Equipment (compressor bodies)
Value/Range - 0.1 mm defect detection
Medical (surgical instruments), Aerospace (aircraft brackets)
Value/Range - 50 – 400 HB / 10 – 70 HRC
Defense (armor casings), Automotive (cylinder heads)
Value/Range - 100 – 900 MPa (material-dependent)
Energy Sector (wind turbine components), Aerospace (aircraft fittings)
Value/Range - ASTM E112 standards
High-Performance Alloys (tool steel, aerospace alloys)
Value/Range - 0.1 – 10 bar pressure range
Automotive (engine covers), Oil & Gas (pipeline valves)


Industry Applications of Precision Die Casting
High strength-to-weight ratio, thermal efficiency, precision
Extreme durability, tight tolerances, resistance to high temperatures
Excellent EMI shielding, thermal management, miniaturization
Biocompatibility, corrosion resistance, micro-scale precision
Superior signal integrity, lightweight, electromagnetic shielding
High wear resistance, dimensional stability, lightweight design
Corrosion resistance, heat dissipation, structural reliability
Saltwater corrosion resistance, durability in extreme environments
Aesthetic finishes, high mechanical integrity, ultra-precise detailing
Growing Markets, Limitless Possibilities
We offer cutting-edge sand casting solutions for the aerospace industry, ensuring precision and durability in every component. Our advanced sand mixtures and high-quality patterns create molds that meet stringent aerospace standards, accommodating complex geometries and large parts for aircraft, engine, and structural components. We maintain tight dimensional tolerances and superior surface finishes, with rigorous quality controls to meet industry certifications. Our process supports a range of metals, including aluminum alloys and titanium, and is designed for large-scale production and custom specifications, delivering exceptional performance and reliability.






Industries We Serve
- Solid Progress
Our Manufacturing metrics
Frigate brings stability, control, and predictable performance to your sourcing operations through a structured multi-vendor system.
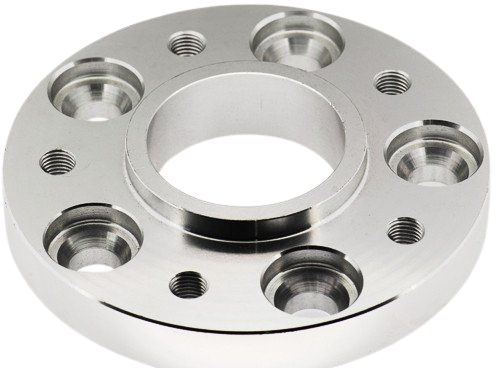
2.8X
Sourcing Cycle Speed
Frigate’s pre-qualified network shortens decision time between RFQ and PO placement.
94%
On-Time Delivery Rate
Structured planning windows and logistics-linked schedules improve project-level delivery reliability.
4X
Multi-Part Consolidation
We enable part family batching across suppliers to reduce fragmentation.
22%
Quality Rejection Rate
Multi-level quality checks and fixed inspection plans lower non-conformities.
30%
Procurement Costs
Optimized supplier negotiations and bulk order strategies reduce your overall sourcing expenses.
20%
Manual Processing Time
Automation of sourcing and supplier management significantly reduces time spent on manual tasks.
Custom Alloy Casting Solutions for Optimal Strength and Performance
Frigate offers alloy casting services across industries, ensuring components maintain high tensile strength. We consult with every customer to recommend the most suitable materials for their applications. Over the years, we’ve handled projects using manganese bronze, aluminum bronze, red brass, and more.
We aim to provide expert advice on lightweight alloy castings tailored to your industry. With a deep understanding of machinability, hardness, and yield properties, we simplify the material selection process, ensuring the best fit for your needs.

Get Clarity with our Manufacturing Insights
- Real Impact
Words from Clients
See how global OEMs and sourcing heads describe their experience with our scalable execution.
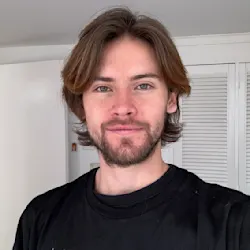
“Quick turnaround and solid quality.”
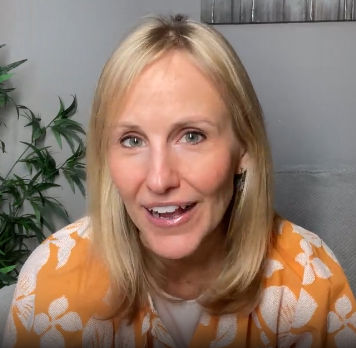
“The instant quote tool saved us time, and the parts were spot-on. Highly recommend Frigate!”
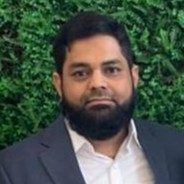
“I would strongly recommend Frigate to anyone who wants to do Rapid Prototyping, and take their ideas to manufacturing. One firm doing all kinds of Product Development!”
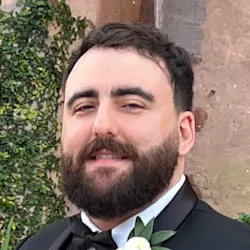
“Great service, fair price, and the parts worked perfectly in our assembly.”
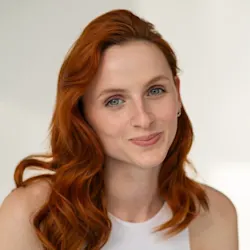
“Top-notch machining and fast shipping. Very satisfied with the results.”
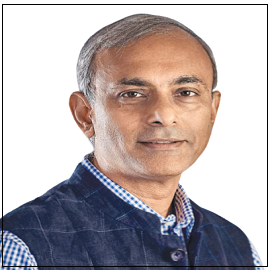
“The next disruption is happening in Prototyping & Manufacturing on-demand and Frigate is leading the way! I personally believe the Frigate's way of IIOT enabled cloud platform with Al.”
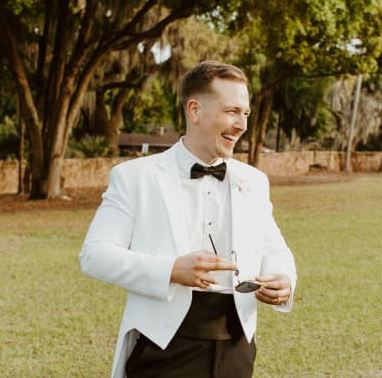
“Frigate delivered high-quality parts at a competitive price. The instant quote tool is a huge plus for us!”

“We appreciate the precision and quality of the machined components in the recent delivery—they meet our specifications perfectly and demonstrate Frigate’s capability for excellent workmanship.”
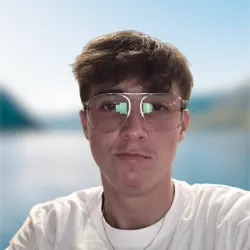
“Flawless execution from quote to delivery.”

“I am absolutely happy to work with supplier like Frigate who were quite proactive & result oriented . Frigate has high willingness team who has strong know how & their passion towards the products & process were absolutely thrilling.”
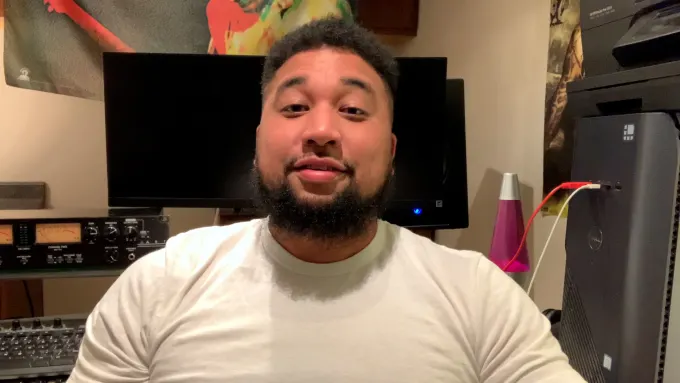
“The precision on these parts is impressive, and they arrived ahead of schedule. Frigate’s process really stands out!”
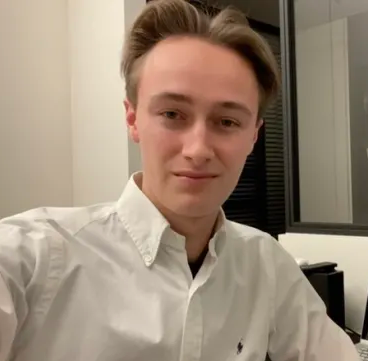
“Parts were exactly as spec’d, and the instant quote made budgeting a breeze.”
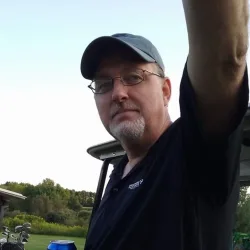
“Good value for the money.”
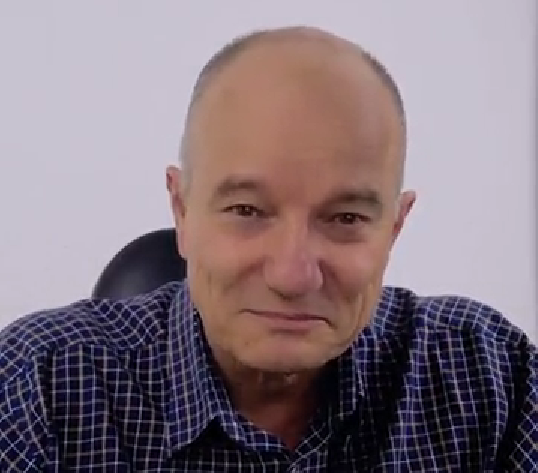
“The finish was perfect, and the team was easy to work with.”

“Working with Frigate has been great. Their proactive, results-driven approach and expertise shine through in every project. It's been a pleasure collaborating with them.”

"We are highly satisfied with the timely delivery and quality of the MIG Welding Cable from Frigate. Their attention to detail, secure packaging, and quick responsiveness stood out. We confidently recommend Frigate Engineering Services Pvt. Ltd. as a reliable manufacturing partner."
Having Doubts? Our FAQ
Check all our Frequently Asked Question
Sand grain size directly impacts the smoothness of the cast part. Finer grains produce a smoother surface but can reduce mold strength and permeability. Coarser grains create a rougher finish, allowing for better gas escape and stronger molds. The right balance depends on the part's design and performance needs.
Venting in sand casting molds allows gases to escape during metal pouring. Trapped gases can cause defects like gas porosity or blowholes in the cast part without vents. Proper venting ensures smooth metal flow and a defect-free final product.
A riser is a reservoir to feed molten metal into the mold as it solidifies, preventing shrinkage defects. The size and position of the riser are crucial. It won't supply enough metal if it's too small or placed incorrectly, leading to voids in the cast part. A well-designed riser ensures a uniform, solid casting.
Mold moisture content is critical for proper mold formation and part quality. Too much moisture can cause steam formation during pouring, leading to gas-related defects. On the other hand, too little moisture weakens the sand mold, causing collapse or poor definition. Maintaining optimal moisture levels ensures a solid, defect-free cast.
Cores are used to form internal cavities or complex geometries within a casting. The core's design, material, and placement are essential for achieving accurate internal shapes. Improper core design can lead to internal defects, misalignments, or structural weaknesses in the final product.
We'd love to Manufacture for you!
Submit the form below and our representative will be in touch shortly.
LOCATIONS
Global Sales Office
818, Preakness lane, Coppell, Texas, USA – 75019
Registered Office
10-A, First Floor, V.V Complex, Prakash Nagar, Thiruverumbur, Trichy-620013, Tamil Nadu, India.
Operations Office
9/1, Poonthottam Nagar, Ramanandha Nagar, Saravanampatti, Coimbatore-641035, Tamil Nadu, India. ㅤ
Other Locations
- Bhilai
- Chennai
- Texas, USA