Near-Net Shape Forging Services
Frigate’s Near-Net Shape Forging reduces material waste and minimizes machining requirements. We ensure high precision, enhanced mechanical properties, and superior structural integrity.
Our Clients





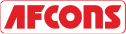

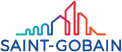


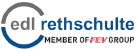

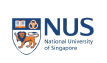
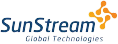

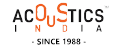




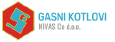
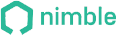
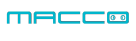












Advantages of Near-Net Shape Forging Services
Uniform Grain Structure
Near-net shape Forging produces a more uniform grain structure, improving the material's mechanical properties, such as toughness and fatigue resistance.
Increased Load-Bearing Capacity
The forging process aligns the grain flow with the part’s geometry, enhancing its ability to withstand high stress and load conditions.
Energy Efficiency
The process requires less energy than traditional forging, as fewer steps are involved in shaping the part, leading to lower operational costs.
Design Flexibility
Near-net shape Forging allows complex shapes to be formed, offering greater flexibility in design without compromising strength or quality.
Custom Near-Net Shape Forging Services
Custom Near-Net Shape Forging produces parts that closely match the final dimensions, reducing the need for extensive machining. This process ensures high dimensional accuracy and consistent material properties, improving overall part strength and performance. Minimizing material waste and machining time enhances cost efficiency and accelerates production cycles. Ideal for complex geometries, Near-Net Shape Forging delivers precision and reliability, meeting the demands of various industrial applications while optimizing resource use.

Get Your Quote Now
- Instant Quotation
- On-Time Delivery
- Affordable Cost
Our Near-Net Shape Forging Process






The process begins by selecting the material, typically metal alloys, based on the part's required properties and application.
The selected material is heated to a specific temperature to make it malleable, allowing easier shaping during forging.
The heated material is placed into a die or mold and subjected to controlled pressure to shape it near the final dimensions.
The material is carefully shaped to match the design, minimizing the need for additional machining and reducing material waste.
Once the part is shaped, it can cool, solidifying the material and maintaining its desired mechanical properties.
The forged part undergoes rigorous testing and quality checks to meet the required tolerances, strength, and durability standards.
Near-Net Shape Forging Materials
Near-Net Shape Forging is a precise process that reduces material waste. It ensures high-performance parts with minimal need for further machining.
Carbon steel, primarily composed of iron and carbon, offers high tensile strength and toughness. It’s ideal for general-purpose applications in industries like automotive and construction due to its cost-effectiveness and ability to resist wear under moderate stress.
Alloy steels, alloyed with chromium, nickel, and molybdenum, enhance mechanical properties like hardness, toughness, and wear resistance. These steels are used in demanding applications such as high-pressure vessels and aerospace components where strength and fatigue resistance are critical.
Stainless steel, containing at least 10.5% chromium, provides exceptional corrosion resistance and high strength. It’s suitable for harsh environments like chemical processing, food industries, and high-temperature applications, where resistance to oxidation and stress corrosion is essential.
Aluminum alloys, such as 2024 and 7075, offer a high strength-to-weight ratio and excellent corrosion resistance. They are commonly used in aerospace and automotive applications, where weight reduction is critical while maintaining the component's structural integrity.
Titanium alloys, like Ti-6Al-4V, are prized for their outstanding strength-to-weight ratio, high corrosion resistance, and ability to perform under high temperatures. They are commonly used in aerospace, medical implants, and marine applications, requiring extreme strength and resistance to heat.
Brass, mainly composed of copper and zinc, and bronze, typically copper with tin, offer high machinability, wear, and corrosion resistance. These alloys are ideal for applications like electrical connectors, marine components, and bearings, where low friction and durability are needed.
Nickel alloys, like Inconel, are known for their ability to withstand extreme temperatures and corrosion, making them suitable for high-performance applications like turbine blades and heat exchangers in the aerospace and power generation industries.
Maximize Efficiency in High-Volume Production Runs
Near-Net Shape Forging significantly improves production efficiency by reducing material waste and eliminating excessive post-forging machining. The process allows for closer-to-final part dimensions, which reduces cycle times and increases throughput. By minimizing the need for additional machining, parts can be produced faster while maintaining consistent quality across large quantities. This ensures high-volume production without sacrificing precision. Frigate’s capabilities in Near-Net Shape Forging ensure that industries requiring large-scale production, such as automotive or aerospace, can maintain cost-effectiveness and high-quality standards.

Compliance for Near-Net Shape Forging Services
Frigate’s near-net shape forging process complies with industry standards to ensure high-quality, reliable, and efficient components. These certifications confirm our commitment to maintaining precision, reducing waste, and meeting the strictest regulatory and environmental requirements. Each step in our forging process follows specific guidelines to guarantee optimal performance and safety.
Ensures robust quality management systems to monitor and optimize every stage of the forging process.
Defines material specifications for carbon steel forgings used in pressure systems, ensuring high strength and durability.
Certifies that all forged components meet environmental standards by being free from hazardous materials like lead and cadmium.
Guarantees secure handling and manufacturing of components for defense and aerospace industries, protecting national security.
Ensures compliance with environmental management practices, minimizing waste and energy consumption in forging operations.
Certification for quality management systems in aerospace manufacturing, ensuring adherence to strict standards for safety and performance.
Verifies high-performance standards in specialized forging processes for aerospace and military applications.

Tolerance for Near-Net Shape Forging Services
Precision in the outer diameter for shafts and rings to ensure tight fits in assemblies.
Ensures the central axis of the forged part is aligned, crucial for rotating components.
Maintains uniform wall thickness across complex geometries to prevent weak spots.
Deviation from perfect circularity to ensure uniform stress distribution in cylindrical parts.
Controls deviation in the rotation axis, critical for high-precision parts like gears.
Precision in tapered features, critical for parts that require specific angles for fitting.
Ensures smooth transitions in corners to reduce stress concentration and improve durability.
Controls distortion in complex shapes to maintain geometric integrity under stress.
Ensures holes are dimensionally accurate for proper fitment of fasteners or shafts.
Critical for components requiring a high degree of flatness, such as flanges and seals.
Ensures the consistent distance between holes or features for parts like flanged joints.
Precision in internal diameters for parts such as bushings and sleeves to ensure interference fits.

Quality Testing Standards for Near-Net Shape Forging Services
Tests the component's ability to maintain shape and integrity under repeated loading cycles.
Simulates stress and strain on the part to identify weak points in complex geometries.
Measures internal stresses within the material that may cause distortion or failure over time.
Evaluates the change in dimensions of the forged part under high temperature conditions.
Verifies the strength of bonds between different material layers, ensuring proper adhesion.
Assesses the component's resistance to corrosion in a controlled saline environment.
Measures the material’s ability to resist high-velocity impacts, especially at low temperatures.
Measures the friction coefficient and wear rate to evaluate the component's performance under mechanical stress.
Determines the thermal conductivity of the forged material to ensure proper heat dissipation.
Evaluates the material's ability to be deformed without cracking, ensuring suitability for future processes.
Verifies the change in hardness and tensile properties after the material undergoes aging treatment.
Examines the microstructure and grain flow to verify proper directional strength in the forged part.
Non-destructive technique to analyze internal voids and porosity distribution throughout the component.
Revolutionizing Engine Component Manufacturing with Near-Net Shape Forging
Achieving precise tolerances while reducing material waste and machining costs is challenging in engine component manufacturing. Near-Net Shape Forging addresses these issues by producing engine parts closer to their final shape, reducing the need for extensive post-forging machining. This results in faster production cycles and higher efficiency. The process also improves material utilization, minimizing waste and enhancing cost-effectiveness. By optimizing grain flow and part geometry, Near-Net Shape Forging ensures high-strength, durable engine components that meet the demanding performance requirements of the automotive and aerospace industries.






Industries We Serve
- Solid Progress
Our Manufacturing metrics
Frigate brings stability, control, and predictable performance to your sourcing operations through a structured multi-vendor system.
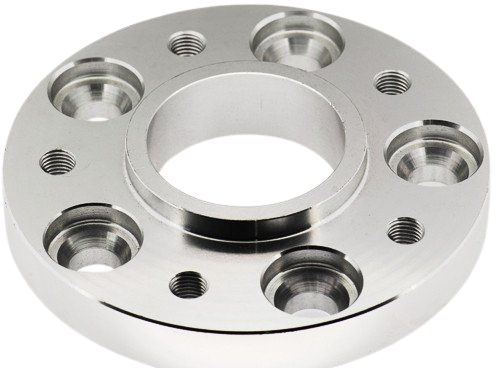
2.8X
Sourcing Cycle Speed
Frigate’s pre-qualified network shortens decision time between RFQ and PO placement.
94%
On-Time Delivery Rate
Structured planning windows and logistics-linked schedules improve project-level delivery reliability.
4X
Multi-Part Consolidation
We enable part family batching across suppliers to reduce fragmentation.
22%
Quality Rejection Rate
Multi-level quality checks and fixed inspection plans lower non-conformities.
30%
Procurement Costs
Optimized supplier negotiations and bulk order strategies reduce your overall sourcing expenses.
20%
Manual Processing Time
Automation of sourcing and supplier management significantly reduces time spent on manual tasks.
Produce Lightweight, Durable Components with Enhanced Strength
Near-net shape Forging enables the creation of lightweight, high-strength components by optimizing material distribution. The forging process aligns the grain structure to enhance mechanical properties, resulting in parts with excellent strength-to-weight ratios. This approach minimizes excess material and eliminates the need for additional machining steps. The result is stronger, lighter components that meet demanding performance standards in industries such as aerospace and automotive. Frigate’s expertise in Near-Net Shape Forging ensures precise control over material flow and part geometry to achieve optimal results.

Get Clarity with our Manufacturing Insights
- Real Impact
Words from Clients
See how global OEMs and sourcing heads describe their experience with our scalable execution.
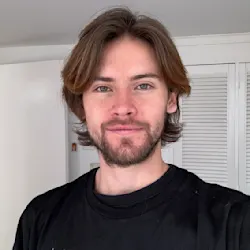
“Quick turnaround and solid quality.”
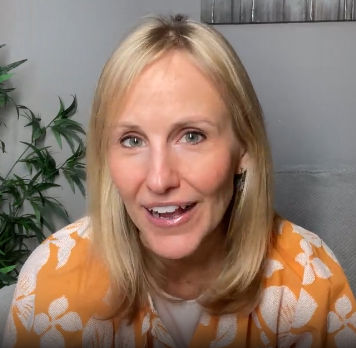
“The instant quote tool saved us time, and the parts were spot-on. Highly recommend Frigate!”
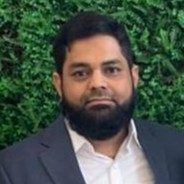
“I would strongly recommend Frigate to anyone who wants to do Rapid Prototyping, and take their ideas to manufacturing. One firm doing all kinds of Product Development!”
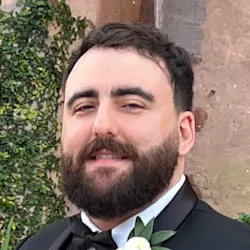
“Great service, fair price, and the parts worked perfectly in our assembly.”
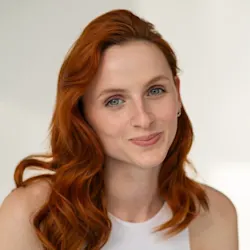
“Top-notch machining and fast shipping. Very satisfied with the results.”
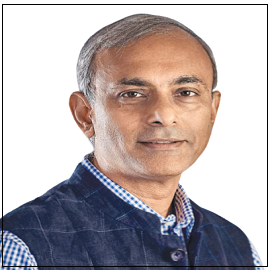
“The next disruption is happening in Prototyping & Manufacturing on-demand and Frigate is leading the way! I personally believe the Frigate's way of IIOT enabled cloud platform with Al.”
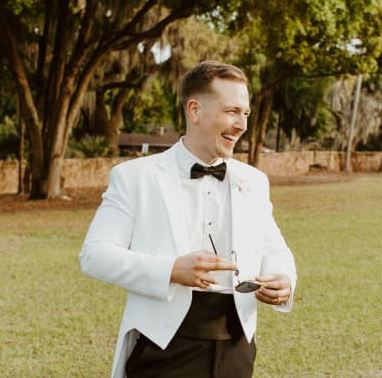
“Frigate delivered high-quality parts at a competitive price. The instant quote tool is a huge plus for us!”

“We appreciate the precision and quality of the machined components in the recent delivery—they meet our specifications perfectly and demonstrate Frigate’s capability for excellent workmanship.”
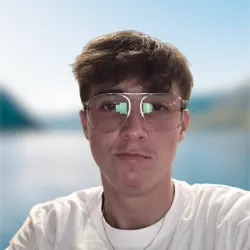
“Flawless execution from quote to delivery.”

“I am absolutely happy to work with supplier like Frigate who were quite proactive & result oriented . Frigate has high willingness team who has strong know how & their passion towards the products & process were absolutely thrilling.”
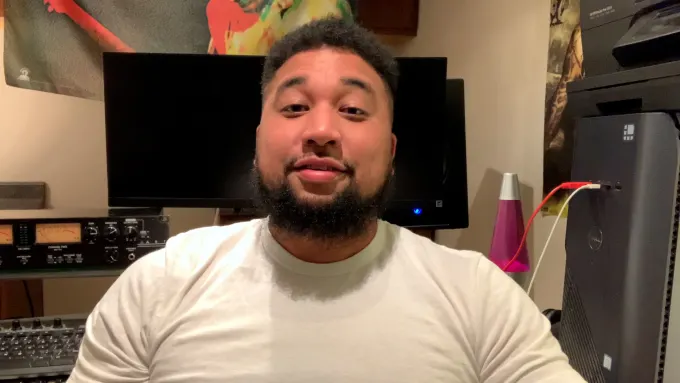
“The precision on these parts is impressive, and they arrived ahead of schedule. Frigate’s process really stands out!”
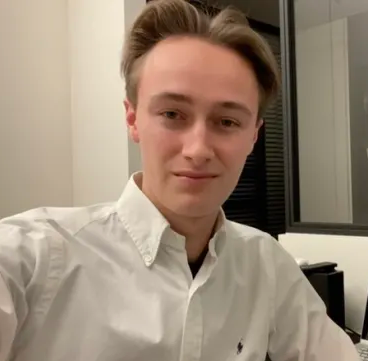
“Parts were exactly as spec’d, and the instant quote made budgeting a breeze.”
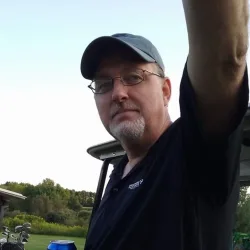
“Good value for the money.”
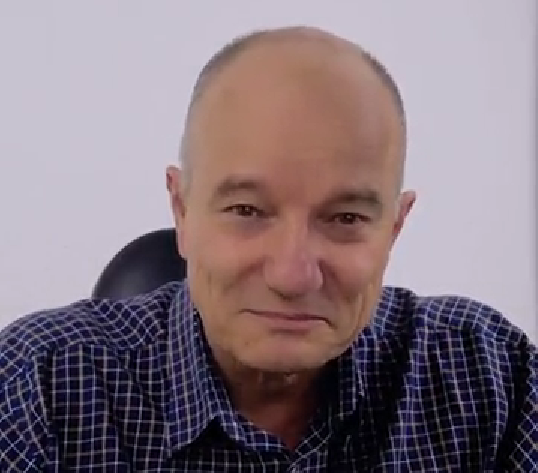
“The finish was perfect, and the team was easy to work with.”

“Working with Frigate has been great. Their proactive, results-driven approach and expertise shine through in every project. It's been a pleasure collaborating with them.”

"We are highly satisfied with the timely delivery and quality of the MIG Welding Cable from Frigate. Their attention to detail, secure packaging, and quick responsiveness stood out. We confidently recommend Frigate Engineering Services Pvt. Ltd. as a reliable manufacturing partner."
Having Doubts? Our FAQ
Check all our Frequently Asked Question
The process aligns the grain structure along the part’s geometry, optimizing strength and fatigue resistance, especially in high-stress applications like aerospace and automotive parts.
Die design is crucial for achieving tight tolerances and minimizing material flow issues. Advanced simulation tools often optimize die geometry for consistent, high-precision results.
Controlled heating and cooling cycles during forging ensure optimal microstructure formation, improving hardness, toughness, and resistance to thermal distortion in the final part.
When properly executed, Near-Net Shape Forging can produce parts with the desired mechanical properties, reducing or eliminating the need for post-forging heat treatments.
The controlled forging process, combined with precise temperature and pressure management, helps reduce common defects like porosity, cracking, and misalignment, ensuring high-quality parts.
We'd love to Manufacture for you!
Submit the form below and our representative will be in touch shortly.
LOCATIONS
Global Sales Office
818, Preakness lane, Coppell, Texas, USA – 75019
Registered Office
10-A, First Floor, V.V Complex, Prakash Nagar, Thiruverumbur, Trichy-620013, Tamil Nadu, India.
Operations Office
9/1, Poonthottam Nagar, Ramanandha Nagar, Saravanampatti, Coimbatore-641035, Tamil Nadu, India. ㅤ
Other Locations
- Bhilai
- Chennai
- Texas, USA