Cold Rolling Services
Frigate’s cold rolling process ensures precise thickness control and enhanced properties. We optimize materials for demanding industrial applications with superior surface finishes.
Our Clients





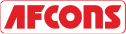

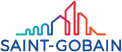


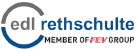

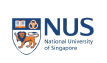
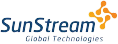

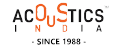




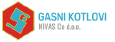
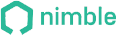
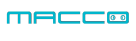












Advantages of Cold Rolling Services
Increased Durability
The strain hardening effect during cold rolling enhances material fatigue resistance, extending the lifespan of components in high-stress environments.
Better Formability
Cold rolling improves the workability of metals, allowing for better shaping and bending without compromising strength or integrity.
Enhanced Surface Hardness
The process increases surface hardness, making cold-rolled materials more resistant to wear, corrosion, and other environmental factors.
Improved Grain Structure
Cold rolling refines metals' grain structure, increasing uniformity and improving overall material performance for precise applications.
Custom Cold Rolling Services for Precision and Consistency
Frigate offers custom cold rolling services that ensure precise thickness control and consistent material quality. The process enhances mechanical properties, increasing strength and durability for demanding applications. Cold rolling achieves tight dimensional tolerances, improving accuracy across all components. The smooth, uniform surface finish reduces the need for additional processing. With custom cold rolling, you can achieve superior material performance and efficiency tailored to your specific requirements.

Get Your Quote Now
- Instant Quotation
- On-Time Delivery
- Affordable Cost
Our Cold Rolling Process






To ensure smooth processing, the metal is first cleaned and preheated to the desired temperature before entering the rolling mill.
The metal is fed into the cold rolling mill, passing through a series of rollers that apply pressure.
The rollers compress the metal, reducing its thickness to the desired specifications while maintaining material strength and shape.
As the metal is compressed, it undergoes strain hardening, which increases its strength and hardness for enhanced performance.
The process smooths the material's surface, creating a uniform finish free from defects and imperfections.
After cold rolling, the material is inspected for quality, ensuring it meets tight tolerances and specifications before being cut or further processed.
Cold Rolling Materials
Cold rolling is a precision process that enhances material strength and surface quality. It provides tight tolerances and improved mechanical properties for critical applications.
Cold-rolled low-carbon steel offers high formability and is ideal for producing thin gauges with tight dimensional tolerances. It’s commonly used in automotive body panels and appliances.
Cold-rolling high carbon steel enhances its hardness and strength, making it suitable for components that require wear resistance, such as springs and cutting tools.
Cold-rolled stainless steel is processed for a smooth, uniform finish and enhanced corrosion resistance. It is used in harsh environments like chemical processing and marine applications.
Cold-rolled aluminum alloys, like the 1000, 3000, and 5000 series, offer a balance of strength and corrosion resistance. These are used in industries where weight reduction and durability are crucial, such as aerospace and automotive.
Cold-rolling copper and its alloys (like bronze and brass) improve dimensional control and surface finish while maintaining electrical conductivity. It is used in electrical wiring, heat exchangers, and HVAC systems.
Cold-rolled titanium alloys, typically grade 2 or 5, retain their high strength-to-weight ratio and resistance to corrosion, making them essential in aerospace and medical device manufacturing.
Magnesium alloys are cold-rolled to achieve fine grain structure and enhanced mechanical properties, focusing on lightweight performance in the automotive and aerospace sectors.
Cold-rolled nickel-based alloys, such as Inconel, maintain high strength and oxidation resistance at high temperatures. These materials are vital in power generation, chemical processing, and aerospace applications.
Maximizing Performance in High-Strength Alloy Rolling
Rolling high-strength alloys demands precise control to avoid cracking and tool wear. Frigate uses advanced equipment and carefully calibrated parameters to manage these alloys’ unique characteristics. Control over reduction ratios, temperature, and rolling speed ensures the material deforms uniformly without excessive strain. Specialized rolling tools and techniques are implemented to extend tool life, maintain dimensional accuracy, and ensure optimal material performance. This method minimizes defects, ensuring the alloys meet the required strength and durability for demanding applications.

Compliance for Cold Rolling Services
Frigate’s cold rolling processes are precisely controlled to ensure consistent thickness, smooth finishes, and tight tolerances by managing rolling speed, temperature, and reduction ratios. We monitor mechanical properties such as tensile strength, yield strength, and elongation to maintain quality while controlling the grain structure to optimize hardness and flexibility. Our advanced tension control systems guarantee uniformity, and we efficiently manage energy use and waste to minimize environmental impact.
Certifies consistent production quality, effective process controls, and continuous improvement in manufacturing practices.
Ensures materials meet specifications for mechanical properties, dimensional accuracy, and surface finish in cold rolling.
Compliance ensures no hazardous substances are used to produce cold-rolled products.
Certifies the safe use of chemicals and materials in cold rolling, meeting EU standards for environmental safety.
Adherence to SAE standards for cold-rolled steel used in automotive, aerospace, and industrial applications.
Ensures sustainable manufacturing processes, minimizing environmental impact throughout the cold rolling process.
Establishes safety protocols to protect employees and prevent hazards in the cold rolling facility.

Tolerance for Cold Rolling Services
Variation in thickness along the length of the strip, critical for consistent mechanical properties.
Deviation in the longitudinal axis of the strip, influencing handling and subsequent processing.
Allowable edge cracking width, minimizing risk during further processing or forming.
Deviation in material yield strength, important for ensuring consistent forming performance.
Variability in tensile strength to meet required material strength standards for different applications.
Tolerance in material elongation percentage, ensuring suitability for forming and stretching processes.
Deviation from flatness across the length of the material, crucial for high-precision applications.
Width variation along the length, ensuring accurate fit and processing for components.
Surface texture tolerance, critical for applications requiring smooth, uniform finishes.
Tolerance in the shape and smoothness of edges to ensure compatibility with downstream processes.
Variation in thickness from center to edge, controlled to maintain uniform material properties.
Tolerance on the increase in hardness due to strain during rolling, impacting material formability.
Allowable variation in residual stress within the material, affecting performance in subsequent forming or machining.

Quality Testing Standards for Cold Rolling Services
Measures how the material responds to different strain rates, critical for dynamic loading conditions.
Assesses the material’s rate of work hardening during deformation, influencing processability and strength.
Measures the material's resistance to crack propagation, vital for applications under high stress.
Determines the temperature at which material transitions from ductile to brittle behavior.
Assesses the material’s different mechanical properties in various directions, important for forming processes.
Evaluates susceptibility to hydrogen-induced cracking, critical for materials exposed to hydrogen environments.
Analyzes the crystallographic orientation of grains, influencing material strength and ductility.
Assesses the material's ability to resist oxidation at high temperatures, important for automotive and aerospace applications.
Measures phase changes in materials, such as transformation under heat, which affects final material properties.
Measures the material's elasticity, which is crucial for predicting how it will deform under stress.
Evaluates the material’s surface adhesion properties, relevant for coating or joining processes.
Ensures the integrity and durability of coatings on cold-rolled material, preventing peeling or corrosion.
Measures the material’s ability to conduct heat, important for thermal processing and applications involving heat transfer.
Determines the material’s ability to withstand repeated cyclic stresses without failure.
Assesses the material’s resistance to wear, critical for components exposed to abrasive conditions.
Cold Rolling’s Role in Consumer Goods Components Manufacturing
Achieving precise material properties and consistent finishes is critical in consumer goods production. Cold rolling improves material strength, reduces thickness variation, and ensures uniform surface quality. The process refines the material’s microstructure, enhancing durability, corrosion resistance, and formability. Tight dimensional control achieved through cold rolling helps meet the stringent requirements of consumer goods components. This enables the production of high-quality, reliable parts that perform consistently over time. Cold rolling ensures fast, efficient production while maintaining high precision and material performance standards.






Industries We Serve
- Solid Progress
Our Manufacturing metrics
Frigate brings stability, control, and predictable performance to your sourcing operations through a structured multi-vendor system.
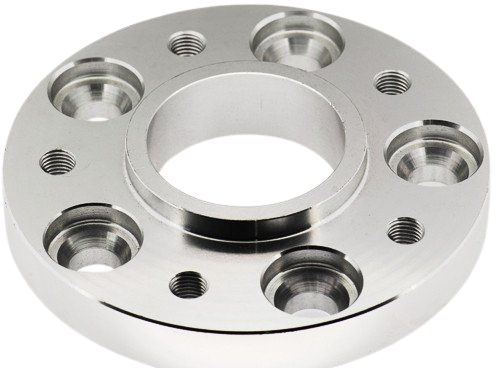
2.8X
Sourcing Cycle Speed
Frigate’s pre-qualified network shortens decision time between RFQ and PO placement.
94%
On-Time Delivery Rate
Structured planning windows and logistics-linked schedules improve project-level delivery reliability.
4X
Multi-Part Consolidation
We enable part family batching across suppliers to reduce fragmentation.
22%
Quality Rejection Rate
Multi-level quality checks and fixed inspection plans lower non-conformities.
30%
Procurement Costs
Optimized supplier negotiations and bulk order strategies reduce your overall sourcing expenses.
20%
Manual Processing Time
Automation of sourcing and supplier management significantly reduces time spent on manual tasks.
Achieving Consistent Flatness for Thin and High-Strength Materials
Maintaining consistent flatness during cold rolling requires advanced process control, especially for thin or high-strength materials. To ensure uniformity, frigate addresses this by employing precision leveling techniques, such as roll gap adjustments and tension leveling. The rolling process is carefully monitored to minimize warping and maintain flatness across the material. These controls help mitigate distortion risks, ensuring that the final product meets strict flatness specifications and is suitable for subsequent processing or end-use applications.

Get Clarity with our Manufacturing Insights
- Real Impact
Words from Clients
See how global OEMs and sourcing heads describe their experience with our scalable execution.
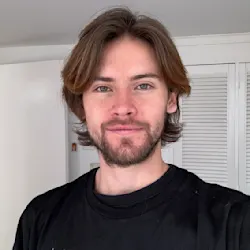
“Quick turnaround and solid quality.”
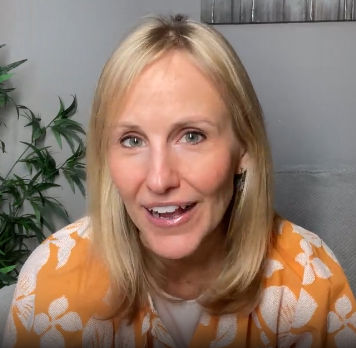
“The instant quote tool saved us time, and the parts were spot-on. Highly recommend Frigate!”
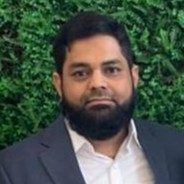
“I would strongly recommend Frigate to anyone who wants to do Rapid Prototyping, and take their ideas to manufacturing. One firm doing all kinds of Product Development!”
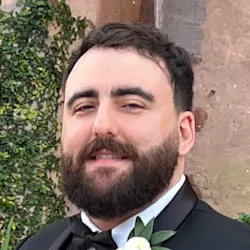
“Great service, fair price, and the parts worked perfectly in our assembly.”
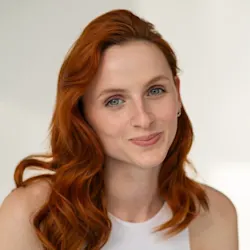
“Top-notch machining and fast shipping. Very satisfied with the results.”
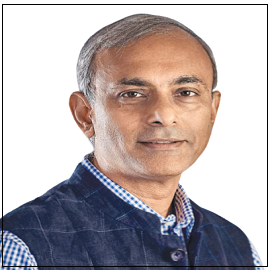
“The next disruption is happening in Prototyping & Manufacturing on-demand and Frigate is leading the way! I personally believe the Frigate's way of IIOT enabled cloud platform with Al.”
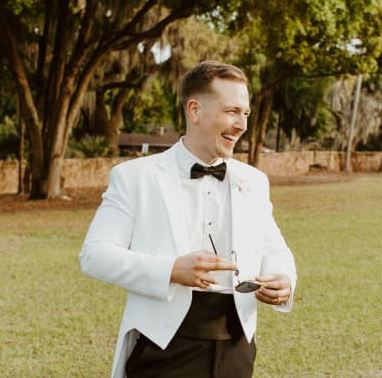
“Frigate delivered high-quality parts at a competitive price. The instant quote tool is a huge plus for us!”

“We appreciate the precision and quality of the machined components in the recent delivery—they meet our specifications perfectly and demonstrate Frigate’s capability for excellent workmanship.”
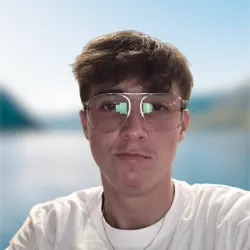
“Flawless execution from quote to delivery.”

“I am absolutely happy to work with supplier like Frigate who were quite proactive & result oriented . Frigate has high willingness team who has strong know how & their passion towards the products & process were absolutely thrilling.”
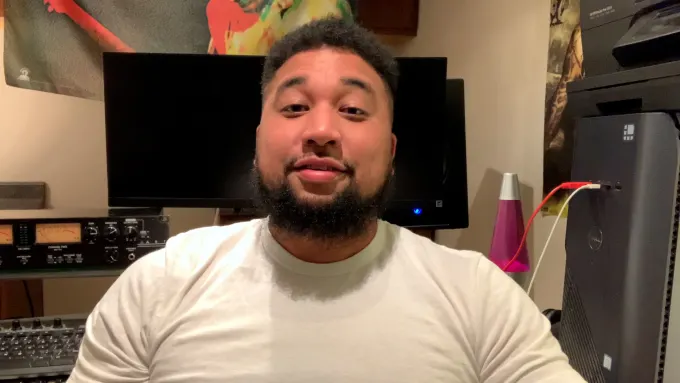
“The precision on these parts is impressive, and they arrived ahead of schedule. Frigate’s process really stands out!”
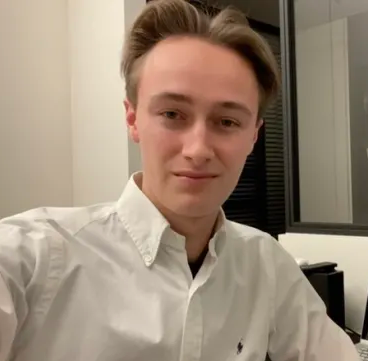
“Parts were exactly as spec’d, and the instant quote made budgeting a breeze.”
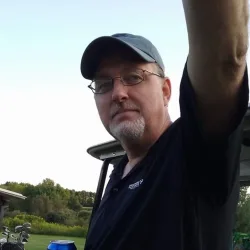
“Good value for the money.”
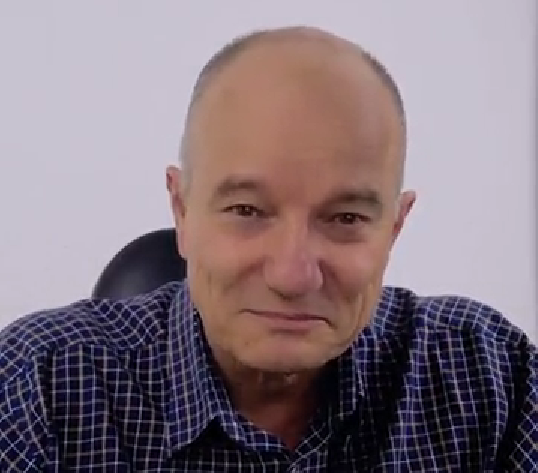
“The finish was perfect, and the team was easy to work with.”

“Working with Frigate has been great. Their proactive, results-driven approach and expertise shine through in every project. It's been a pleasure collaborating with them.”

"We are highly satisfied with the timely delivery and quality of the MIG Welding Cable from Frigate. Their attention to detail, secure packaging, and quick responsiveness stood out. We confidently recommend Frigate Engineering Services Pvt. Ltd. as a reliable manufacturing partner."
Having Doubts? Our FAQ
Check all our Frequently Asked Question
Cold rolling induces compressive residual stresses on the surface, which enhance fatigue resistance while managing internal stresses to prevent warping or distortion.
Strain rate influences the deformation mechanisms and material behavior, affecting the rolled material's final microstructure, hardness, and mechanical properties.
Cold rolling refines the metal's crystallographic texture, aligning grains in a preferred orientation and enhancing the final product's strength and directional properties.
Yes, cold rolling effectively refines the microstructure of AHSS, enhancing properties such as tensile strength, formability, and resistance to deformation during subsequent processes.
The reduction ratio and rolling speed directly impact the material’s hardness, tensile strength, and surface finish, allowing fine-tuning for specific applications with desired mechanical properties.
We'd love to Manufacture for you!
Submit the form below and our representative will be in touch shortly.
LOCATIONS
Global Sales Office
818, Preakness lane, Coppell, Texas, USA – 75019
Registered Office
10-A, First Floor, V.V Complex, Prakash Nagar, Thiruverumbur, Trichy-620013, Tamil Nadu, India.
Operations Office
9/1, Poonthottam Nagar, Ramanandha Nagar, Saravanampatti, Coimbatore-641035, Tamil Nadu, India. ㅤ
Other Locations
- Bhilai
- Chennai
- Texas, USA