Roll Forging Services
Frigate employs roll forging to produce high-strength, precise metal components. Our process enhances material properties, ensuring tight tolerances and improved mechanical performance.
Our Clients





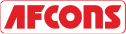

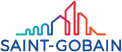


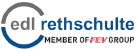

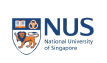
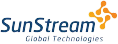

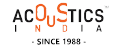




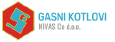
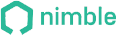
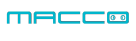












Advantages of Roll Forging Services
Improved Surface Finish
Roll forging provides a smooth surface finish, minimizing the need for additional finishing processes and improving part quality.
Increased Strength-to-Weight Ratio
This technique helps produce lightweight components without sacrificing strength, making it ideal for the aerospace and automotive industries.
Faster Production Cycles
The high-speed nature of roll forging allows for rapid production rates, leading to quicker lead times and improved operational efficiency.
Reduced Residual Stresses
By gradually shaping the material, roll forging minimizes residual stresses, improving the structural integrity and longevity of the component.
Custom Roll Forging Services for Precision and Efficiency
Custom roll forging is highly efficient for producing precise, high-strength components with superior material properties. The process enhances mechanical performance, ensuring improved wear resistance and durability. With tight dimensional control, it minimizes the need for additional machining and reduces production time. Roll forging enables complex geometries with high material utilization, including tapered and contoured shapes. This technique also provides excellent surface finishes, ensuring a smooth and consistent product. It is ideal for industries requiring fast production, minimal waste, and enhanced component strength.

Get Your Quote Now
- Instant Quotation
- On-Time Delivery
- Affordable Cost
Our Roll Forging Process
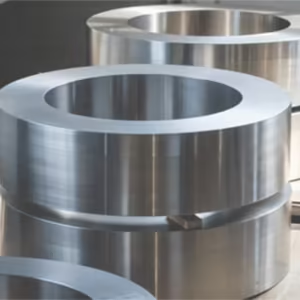





The process begins with selecting and preparing the metal, typically in bar or billet form, heated to the required temperature for optimal plasticity.
The heated metal is fed into the roll forging machine, which is compressed between rotating rolls. This gradually reduces its cross-sectional area while elongating its length.
As the material passes through the rolls, it is shaped into the desired profile, which can be tapered, contoured, or uniform in section, depending on the design.
The rolls apply continuous pressure to reduce the thickness of the material, elongating it to the required dimensions while maintaining tight tolerances.
The forged part is cooled once the desired shape and dimensions are achieved. Depending on the material and specifications, cooling can occur naturally or may be controlled.
The final forged part is inspected for quality, ensuring it meets strength, dimensional accuracy, and surface finish specifications. Any additional machining or trimming can be performed if necessary.
Roll Forging Materials
Roll forging is a precision process that enhances material properties through controlled deformation. It produces high-strength components with excellent dimensional accuracy and surface quality.
Carbon steel, with varying carbon content, offers a balance of strength, hardness, and flexibility. It’s used in parts requiring high tensile strength and impact resistance, such as gears, shafts, and automotive components.
Alloy steels, like 4140 and 4340, are enhanced with chromium, molybdenum, and vanadium to improve hardenability, strength, and resistance to fatigue. These alloys are used in heavy-duty machinery and high-stress applications.
Stainless steel, particularly grades like 304 and 316, is selected for its corrosion resistance and strength. It's crucial for environments where resistance to oxidation, corrosion, and extreme temperatures is needed, such as chemical processing and marine equipment.
Aluminum alloys like 7075 and 2024 are chosen for their excellent strength-to-weight ratios and corrosion resistance. Commonly used in aerospace and transportation, these alloys provide strength while minimizing weight, which is critical for high-performance parts.
Copper alloys, including brass and bronze, are highly conductive and corrosion-resistant. Due to their excellent thermal and electrical conductivity, they are commonly used for electrical components, heat exchangers, and marine applications.
Titanium alloys, such as Ti-6Al-4V, offer high strength-to-weight ratios and superior fatigue resistance. These materials are ideal for aerospace, medical implants, and high-performance applications where weight reduction is critical.
Magnesium alloys, such as AZ31 and AZ61, are lightweight and exhibit good machinability and strength. They are used in automotive and aerospace industries where reducing weight is crucial without sacrificing structural integrity.
Nickel alloys like Inconel and Monel provide exceptional high-temperature performance and resistance to oxidation and corrosion. These materials are typically used in turbine engines, chemical processing, and other high-temperature applications.
Minimized Material Waste and Reduced Scrap
Traditional forging methods often result in material wastage due to inefficient shaping and extra machining steps. Frigate’s roll forging process minimizes scrap by using continuous pressure to shape the metal, reducing the need for excessive trimming or machining. This leads to improved material utilization and lower production costs. The process ensures that more raw material is used in the final product, providing a cost-effective solution while maintaining high-quality standards.

Compliance for Roll Forging Services
Roll forging requires adherence to strict compliance standards for material quality, process control, and product performance. We ensure all processes are rigorously monitored to meet high standards. Compliance ensures the integrity, reliability, and safety of the roll-forged components used in critical industries like aerospace, automotive, and heavy machinery. These certifications and standards guarantee that our products meet both regulatory requirements and customer expectations.
Ensures consistent quality management and continuous improvement of production processes for high-quality roll-forged products.
Establishes specifications for steel forgings, ensuring proper mechanical properties and quality in the final roll-forged parts.
Requires certified material test reports, ensuring traceability and verification of mechanical properties for each roll-forged batch.
Aerospace quality management standard ensuring compliance with strict requirements for manufacturing precision and reliability in aerospace components.
Ensures that all materials used are compliant with European Union regulations on hazardous chemicals, prioritizing environmental safety.
Ensures that all materials used are compliant with European Union regulations on hazardous chemicals, prioritizing environmental safety.
Focuses on environmental management systems to minimize environmental impact during roll forging, ensuring sustainable practices.

Tolerance for Roll Forging Services
Tolerance on the reduction in cross-sectional area of the material.
Deviation of the part from a true perpendicular angle between surfaces.
Precision of thread relief length when roll forging components with threads.
Variation in the radius of fillets or bends in roll-forged components.
Deviation from the designed profile in parts with complex geometries.
Tolerance on the consistency of material flow during the forging process, affecting part uniformity.
Maximum distortion in the surface profile due to heat and pressure during forging.
Deviation in concentricity between opposing ends of a forged part, critical for rotational symmetry.
Ensures uniform thickness across the length and width of the part, crucial for structural integrity.
Deviation in twist or rotational alignment along the length of the part.
Measurement of resistance to deformation under operational stress, ensuring parts maintain dimensional integrity.
Tolerance on the dimensions of keyways in shafts or other components, ensuring proper fitment and alignment.
Deviation in cross-sectional geometry (such as elliptical or rectangular shapes) during the roll forging process.
Precision in achieving a flat surface after forging, essential for applications requiring precise contact surfaces.
Precision in the contour of edges, critical for parts that require precise fit and alignment.

Quality Testing Standards for Roll Forging Services
Measures the average size of the crystalline grains in the material, critical for determining strength and ductility.
Measures the hardness at small points, particularly useful for testing localized regions of the roll-forged material.
Detects the amount of magnetic flux retained after forging, important for applications requiring non-magnetic properties.
Assesses the wear resistance of the material by simulating the frictional forces it will experience in service.
Tests the material’s ability to resist deformation under constant stress at elevated temperatures over time.
Evaluates the material's strength relative to its weight, essential for parts in aerospace or automotive applications.
Measures the material's resistance to elastic deformation under stress, important for parts under dynamic loads.
Assesses the material's ability to conduct heat, critical for components used in high-heat applications.
Measures how the material interacts with electromagnetic fields, crucial for electrical components.
Tests the material's ability to form complex shapes without cracking, important for intricate designs in forging.
Assesses the material's ability to resist oxidation at high temperatures, critical for parts in harsh environments.
Determines the material's vulnerability to hydrogen absorption, which can cause brittleness in metals.
Measures the material’s ability to resist bending or flexural stress, crucial for load-bearing components.
Tests the material's resistance to crack propagation under stress, important for critical structural applications.
Measures the uniformity of thickness throughout the length of the forged part to ensure dimensional accuracy.
Transforming Renewable Energy Manufacturing
A significant challenge in renewable energy manufacturing is achieving high-strength, durable components while minimizing production costs. Roll forging addresses these issues by efficiently shaping materials, reducing waste, and improving lead times. The process enhances properties like strength, fatigue resistance, and dimensional accuracy, making it ideal for critical components such as wind turbine shafts and solar mounting systems. Frigate’s roll forging services provide precision and reliability, enabling manufacturers to meet the demanding performance and cost requirements of the renewable energy sector.






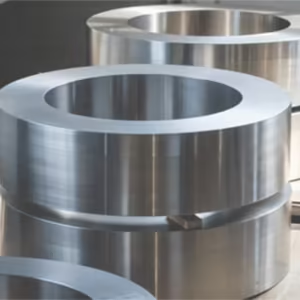
Industries We Serve
- Solid Progress
Our Manufacturing metrics
Frigate brings stability, control, and predictable performance to your sourcing operations through a structured multi-vendor system.
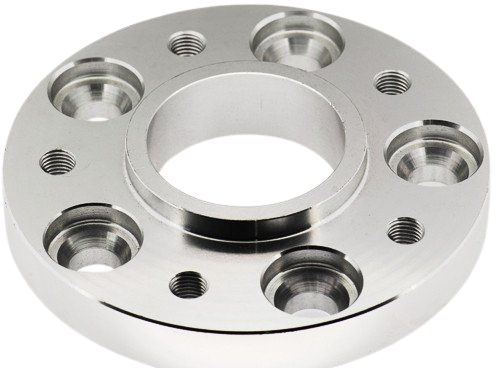
2.8X
Sourcing Cycle Speed
Frigate’s pre-qualified network shortens decision time between RFQ and PO placement.
94%
On-Time Delivery Rate
Structured planning windows and logistics-linked schedules improve project-level delivery reliability.
4X
Multi-Part Consolidation
We enable part family batching across suppliers to reduce fragmentation.
22%
Quality Rejection Rate
Multi-level quality checks and fixed inspection plans lower non-conformities.
30%
Procurement Costs
Optimized supplier negotiations and bulk order strategies reduce your overall sourcing expenses.
20%
Manual Processing Time
Automation of sourcing and supplier management significantly reduces time spent on manual tasks.
Faster Production for Complex Geometries
Creating complex parts with traditional forging methods can lead to lengthy production cycles due to multiple tooling setups and extensive post-processing. Roll forging streamlines this process by allowing the production of intricate shapes with fewer tool changes and reduced need for secondary operations. This approach shortens lead times and ensures parts are produced to precise specifications. Frigate’s roll-forging capability provides quicker turnaround times while maintaining dimensional accuracy, meeting the needs of industries with tight deadlines.

Get Clarity with our Manufacturing Insights
- Real Impact
Words from Clients
See how global OEMs and sourcing heads describe their experience with our scalable execution.
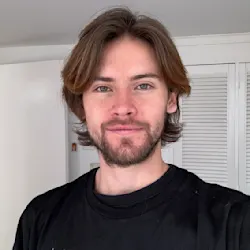
“Quick turnaround and solid quality.”
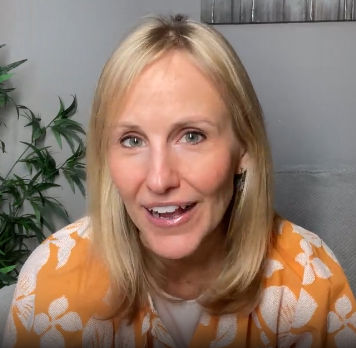
“The instant quote tool saved us time, and the parts were spot-on. Highly recommend Frigate!”
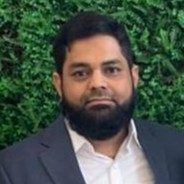
“I would strongly recommend Frigate to anyone who wants to do Rapid Prototyping, and take their ideas to manufacturing. One firm doing all kinds of Product Development!”
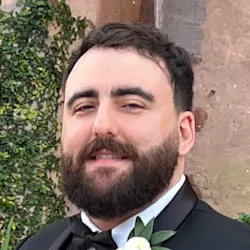
“Great service, fair price, and the parts worked perfectly in our assembly.”
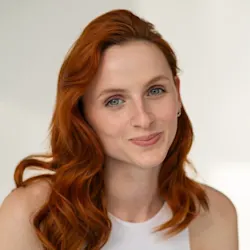
“Top-notch machining and fast shipping. Very satisfied with the results.”
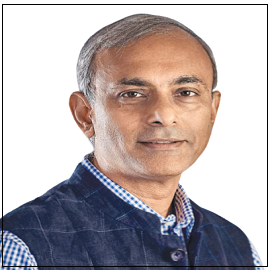
“The next disruption is happening in Prototyping & Manufacturing on-demand and Frigate is leading the way! I personally believe the Frigate's way of IIOT enabled cloud platform with Al.”
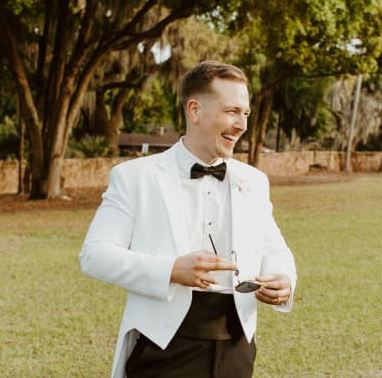
“Frigate delivered high-quality parts at a competitive price. The instant quote tool is a huge plus for us!”

“We appreciate the precision and quality of the machined components in the recent delivery—they meet our specifications perfectly and demonstrate Frigate’s capability for excellent workmanship.”
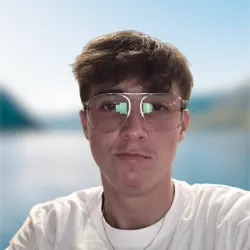
“Flawless execution from quote to delivery.”

“I am absolutely happy to work with supplier like Frigate who were quite proactive & result oriented . Frigate has high willingness team who has strong know how & their passion towards the products & process were absolutely thrilling.”
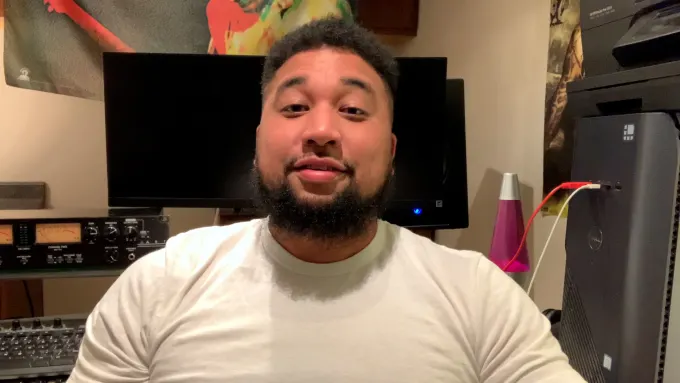
“The precision on these parts is impressive, and they arrived ahead of schedule. Frigate’s process really stands out!”
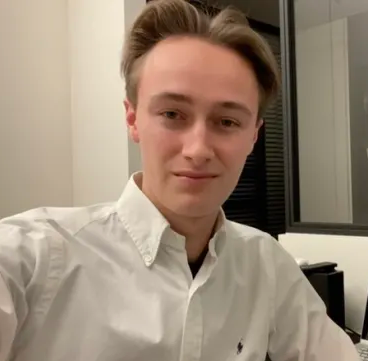
“Parts were exactly as spec’d, and the instant quote made budgeting a breeze.”
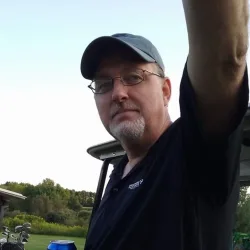
“Good value for the money.”
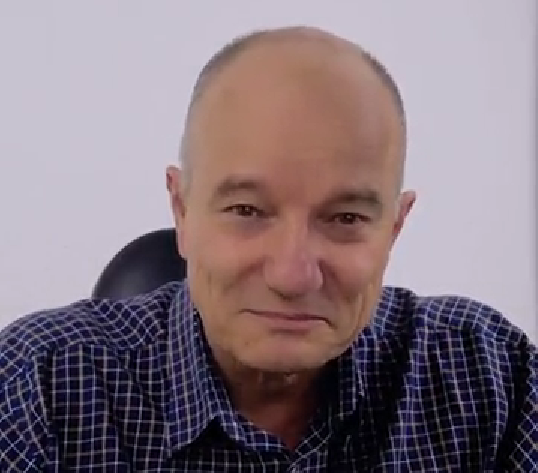
“The finish was perfect, and the team was easy to work with.”

“Working with Frigate has been great. Their proactive, results-driven approach and expertise shine through in every project. It's been a pleasure collaborating with them.”

"We are highly satisfied with the timely delivery and quality of the MIG Welding Cable from Frigate. Their attention to detail, secure packaging, and quick responsiveness stood out. We confidently recommend Frigate Engineering Services Pvt. Ltd. as a reliable manufacturing partner."
Having Doubts? Our FAQ
Check all our Frequently Asked Question
Roll forging applies uniform pressure across the material, ensuring even grain flow and consistent material properties throughout. This minimizes variability in large production runs, ensuring high-quality, repeatable results.
Temperature control is critical in roll forging, as it affects material flow and hardness. Materials are heated to optimal temperatures to improve flexibility and ensure uniform deformation without compromising strength or integrity.
Roll forging is more energy-efficient than traditional forging methods due to its continuous deformation process, which reduces the need for excessive heat input and lowers overall energy consumption in high-volume production.
Yes, roll forging can be adapted to handle high-performance alloys like titanium and nickel-based materials. It offers enhanced workability at elevated temperatures and produces parts with superior mechanical properties.
Roll forging aligns the material’s grain structure, enhancing its ability to resist cyclic loading and fatigue. This results in parts that exhibit superior durability and performance in demanding applications such as aerospace and automotive.
We'd love to Manufacture for you!
Submit the form below and our representative will be in touch shortly.
LOCATIONS
Global Sales Office
818, Preakness lane, Coppell, Texas, USA – 75019
Registered Office
10-A, First Floor, V.V Complex, Prakash Nagar, Thiruverumbur, Trichy-620013, Tamil Nadu, India.
Operations Office
9/1, Poonthottam Nagar, Ramanandha Nagar, Saravanampatti, Coimbatore-641035, Tamil Nadu, India. ㅤ
Other Locations
- Bhilai
- Chennai
- Texas, USA