How can industries ensure the production of high-quality aluminum components? What strategies address the complex landscape of production challenges? Many face issues like quality control, production efficiency, material sourcing, and cost management. These challenges are critical. Minor defects in aluminum components can lead to significant failures in applications, which impacts product performance and overall safety.
This blog explores aluminum gravity die-casting services, addressing common challenges and showcasing the advantages of this specialized manufacturing process. Understanding the technical aspects and benefits of gravity die casting helps make informed decisions that enhance production capabilities.
What is Aluminum Gravity Die Casting?
Aluminum gravity die casting involves pouring molten aluminum into a reusable steel mold, known as a die. This method uses gravity to fill the mold and create components with high dimensional accuracy and smooth surface finishes. Here are the key technical aspects of this process:
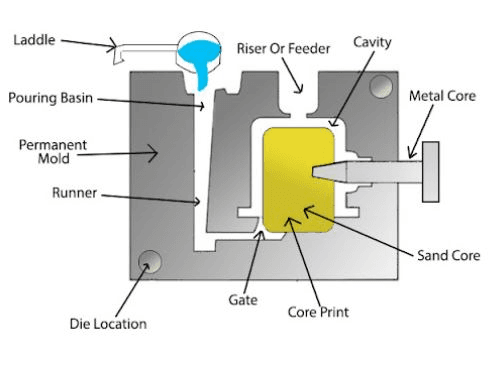
What is Gravity Die Casting?
In gravity die casting, molten aluminum enters the die solely by gravitational force. This technique offers several advantages:
- High Precision: Gravity ensures uniform mold filling, which leads to fewer defects like air pockets or voids.
- Good Surface Finish: Steel molds provide a smooth surface that transfers to the final product, often reducing the need for additional machining.
Why Use Aluminum?
Aluminum is the ideal choice for many industries due to its unique properties:
- Lightweight – At about one-third the weight of steel, aluminum parts help lower overall product weight. This is important in industries like automotive and aerospace.
- Corrosion Resistance – Aluminum’s natural oxide layer protects it from corrosion, making it suitable for outdoor applications.
- Strength – Aluminum exhibits a strong strength-to-weight ratio. It can withstand significant loads while remaining lightweight.
Key Challenges in Aluminum Gravity Die Casting
While aluminum gravity die-casting services offer many advantages, they also have challenges to address. Recognizing these challenges is crucial for successful project outcomes.
Quality Control Issues
Ensuring consistent quality in cast parts is vital. Common quality concerns include:
- Porosity – As the metal solidifies, gas bubbles can form, compromising the part’s integrity. To minimize porosity, manufacturers can optimize pouring temperature and speed and employ vacuum techniques to reduce gas entrapment.
- Shrinkage – As aluminum cools, it contracts. If the mold lacks appropriate allowances, this can lead to dimensional inaccuracies. Mold designers must account for thermal expansion and contraction to mitigate shrinkage issues.
- Inclusions – Foreign particles may become trapped in the molten aluminum during pouring. Utilizing filtration systems and maintaining clean environments in casting areas can help prevent inclusions.
Production Efficiency
Speed and efficiency in production are vital for maintaining competitive pricing. Factors affecting efficiency include:
- Machine Setup – The time required to set up die-casting machines can vary significantly. This is especially true when switching between different part designs. Effective scheduling and the use of standardized tools can help reduce setup times.
- Cycle Times – Cycle time encompasses the entire process, from pouring to cooling. Manufacturers can enhance throughput by optimizing cooling rates through advanced temperature management techniques without sacrificing part quality.
- Maintenance – Regular maintenance of casting machines is crucial. Preventing unplanned breakdowns through predictive maintenance practices can help identify issues before they cause downtime.
Material Sourcing
Reliable sourcing of high-quality aluminum is essential. Key considerations include:
- Alloy Quality – Different aluminum alloys (6061 or 7075) offer varying mechanical properties. The appropriate alloy is critical for achieving the desired strength and performance characteristics.
- Supply Chain Reliability – Maintaining production schedules requires a steady supply of quality aluminum. Establishing relationships with multiple suppliers can help mitigate risks associated with material shortages.
Cost Management
Managing costs while ensuring high quality can be challenging. Key factors include:
- Labor Costs – Skilled labor is essential for operating complex machines and ensuring quality control. Investment in training programs helps maintain a skilled workforce. This ultimately reduces long-term costs.
- Operational Costs – Efficient processes minimize overhead expenses. Implementing energy-efficient practices and optimizing material usage can lead to substantial savings.
Features of Comprehensive Aluminum Gravity Die Casting Services
To successfully navigate the challenges of aluminum gravity die casting, it’s important to focus on the features that enhance quality and efficiency. These features are essential for ensuring that the casting process meets industry standards.
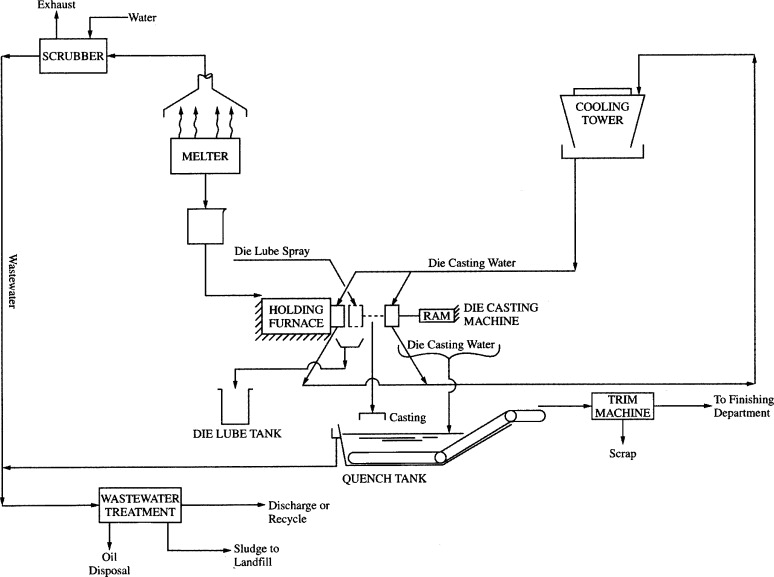
Advanced Technology and Equipment
Utilizing modern technology significantly improves the quality of cast parts. Here are some important considerations:
- State-of-the-Art Machines – High-precision gravity die-casting machines control the pouring process with accuracy. Features like automated pouring systems help maintain consistent quality across batches.
- Automated Processes—Automation reduces human error and enhances safety. Robotic systems assist with part removal and inspection, streamlining production workflows.
Customization Options
Every project is unique. Comprehensive casting services offer customization to meet specific requirements. Service providers can adjust mold designs and alloy compositions to accommodate diverse applications.
Advanced tooling techniques enable the production of intricate designs. Skilled mold designers can create molds that accommodate complex geometrical shapes, expanding design possibilities.
Prototyping and Testing
Prototyping before mass production minimizes risks. Technologies such as 3D printing allow manufacturers to create prototypes quickly, enabling the evaluation of designs before proceeding to full production.
Conducting rigorous tests on prototypes helps identify potential issues early. Mechanical testing, such as tensile and impact testing, assesses the performance characteristics of components.
Environmental Considerations
The importance of sustainability in manufacturing continues to grow. Aluminum gravity die-casting services can adopt eco-friendly practices to minimize environmental impact while maintaining efficiency.
Aluminum gravity die casting services can incorporate environmentally friendly practices, such as:
- Waste Reduction Techniques – Minimizing waste during casting is crucial. Recycling scrap aluminum back into the process conserves resources and reduces costs.
- Compliance with Environmental Regulations – Meeting industry standards helps minimize environmental impact. This includes managing emissions and waste according to local regulations.
Case Studies and Applications
Understanding the application of aluminum gravity die casting illustrates its benefits. Case studies provide insights into real-world applications and the advantages they bring.
Automotive Industry
Reducing component weight is crucial for enhancing fuel efficiency in the automotive sector. A leading automobile manufacturer employed aluminum gravity die casting for engine blocks, reducing their weight by approximately 10%. The outcome was improved fuel economy and vehicle performance.
Aerospace Industry
The aerospace sector demands high-quality parts that meet strict safety and performance standards. An aerospace company utilized aluminum gravity die casting for structural components. This enabled complex geometries while achieving a weight reduction of about 20%. The result was improved fuel efficiency and operational performance.
Electronics Industry
In the electronics sector, precision is vital for ensuring product reliability. A technology firm utilized aluminum gravity die casting for housing components. This approach enhanced durability while allowing for intricate designs that meet modern aesthetic standards. The product withstood impacts while maintaining an appealing appearance.
Choosing the Right Partner for Aluminum Gravity Die Casting
Selecting the right casting service provider is crucial for success. Carefully evaluating potential partners ensures that project requirements are met effectively and efficiently.
Factors to Consider
- Technical Expertise: Companies with a strong track record in aluminum gravity die casting are preferable. Experience in similar projects indicates the ability to meet quality standards.
- Equipment Capabilities: Ensure the provider possesses modern, high-quality equipment. Advanced machinery plays a significant role in producing precise and consistent parts.
- Customer Service: Effective communication is essential. A responsive partner can quickly address challenges, ensuring a smoother production process.
Successful projects rely on collaboration. Close work with the casting service provider maintains open lines of communication. Regular updates and feedback sessions help keep projects on track, leading to improved outcomes.
Conclusion
Aluminum gravity die casting services provide numerous advantages, including precision, cost-effectiveness, and customization. However, navigating potential challenges such as quality control, production efficiency, and material sourcing remains essential. By selecting the right service provider and understanding the casting process, companies can overcome challenges and reap the benefits of aluminum gravity die casting.
For high-quality aluminum gravity die casting services tailored to specific needs, contact Frigate today. Their expertise and commitment to excellence ensure that casting requirements are met with precision and care.