Contract Manufacturing Services
Frigate combines advanced automation with expert craftsmanship to provide comprehensive contract manufacturing solutions. We ensure the seamless integration of complex processes, delivering high-performance components with exceptional precision and reliability.
Our Clients





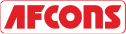

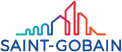


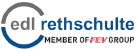

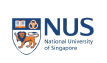
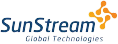

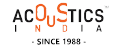




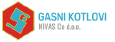
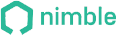
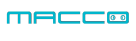












What We Do
Our Contract Manufacturing Offerings
Partner with Frigate Engineering and unlock new technical expertise for your Contract Manufacturing projects.
Get Your Quote Now
- Instant Quotation
- On-Time Delivery
- Affordable Cost
Custom Contract Manufacturing Solutions for Precise Production
Frigate offers custom contract manufacturing services focused on precision, efficiency, and quality. Advanced technologies and streamlined processes ensure that components meet exact specifications with consistent quality. Each stage of production, from initial prototyping through to full-scale manufacturing, is optimized to reduce costs while maintaining high standards.
With automation and expert craftsmanship, Frigate delivers reliable solutions for diverse industries. The tailored approach supports clients by enhancing production capabilities, meeting industry standards, and addressing specific requirements. Precision and efficiency are at the core of every project, providing long-term value and exceptional results.

Our Business Verticals
Automotive
Aerospace
Marine
Railway
Construction and Infrastructure
Energy and Power Generation
Industrial Machinery
Defense and Military Equipment
Achieving Consistent Tolerances Across High-Volume Production
High-precision measurement systems ensure that every component meets stringent tolerance requirements. These systems continuously monitor and adjust to minimize deviations during production.
Automated systems manage the production process, maintaining consistent conditions to control tolerances. This ensures uniformity across large production runs and reduces human error.
Real-time data collection and analysis allow for immediate detection of tolerance deviations. Adjustments are made instantly, ensuring all parts meet the specifications throughout the production cycle.

Mitigating Variability in Material Performance
Thorough testing of materials before and during production ensures they meet the necessary strength, durability, and performance requirements. These tests identify potential inconsistencies in material properties that could affect the end product.
Materials are sourced from trusted suppliers and are verified for consistency before use in manufacturing. This minimizes variability and ensures that materials perform as expected throughout production.
The material processing methods, such as heat treatment or alloy mixing, are fine-tuned to achieve desired properties. These optimized processes ensure that materials retain their intended strength and functionality in the final product.

Overcoming Challenges in Integrating Advanced Manufacturing Technologies
Advanced technologies like automation and robotics are integrated smoothly into existing production systems. This approach minimizes disruptions and ensures that new technologies complement current workflows efficiently.
Flexible manufacturing systems allow for quick adjustments when incorporating new technologies. This flexibility ensures that production remains efficient and adaptive to technological changes or production demands.
Using real-time data and analytics, production processes are continuously monitored and optimized. This ensures that integrating new technologies does not compromise production efficiency or product quality.

Casting Materials
Our casting services offer a fusion of precision and creativity, molding metals into bespoke designs with finesse. Whether it’s iron’s resilience or bronze’s fluidity, we bring your visions to life with expert craftsmanship.
Cast Metal Materials
Aluminum alloys are the most widely used for cast parts. Aluminum casting suppliers benefit from the total recyclability of the material and its ease of use. Due to the comparatively higher melting point, aluminum casting may require a cold chamber casting process. Engineers use cast aluminum parts primarily for their great strength-to-weight ratios, dimensional stability, and diverse finishing options. Some of the other common characteristics of cast aluminum alloys are:
- Withstand high operating temperatures
- Corrosion Resistance
- Good stiffness
- High thermal and electrical conductivity
Engineers and designers can choose from various alloys for their aluminum casting parts. Frigate offers the most popular aluminum casting alloys, including:
- A360.0
- A380.0
- A383.0 (ADC12)
- A413.0
Zinc is the easiest to cast material among the casting metals and is typically used in hot chamber processes. Molten zinc has exceptional casting fluidity and a lower melting point. Its strength and stiffness allow it to produce parts with thinner walls and highly detailed features and maintain tight tolerances. The low melting point of casting zinc alloys means the casted parts cool off and solidify more quickly, which results in the fastest production rates of the casting materials. Zinc is an all-around well-performing material due to its balance of mechanical and physical characteristics, which include,
Impact strength
High hardness
Great stability
High-quality surface finish and easily plated
Low melting point
Frigate offers the most popular types of Zamak and ZA casting zinc alloys. More specifically, those alloys include,
Zamak 2 (ZA-2)
Zamak 3 (ZA-3)
Managing Production Adjustments for Dynamic Demand
Fluctuations in demand often present challenges in maintaining consistent production capacity. Frigate offers flexible manufacturing systems designed to scale production up or down efficiently. Adjustments can be made rapidly without sacrificing quality or precision through automated systems and advanced process management.
Real-time monitoring and data-driven decisions support Frigate’s capacity to handle varying production volumes. This ensures that production lines can adapt seamlessly to changes in demand, whether increasing for large orders or reducing for smaller runs. This flexibility minimizes downtime and ensures continuity, regardless of order volume.

- Real Impact
Words from Clients
See how global OEMs and sourcing heads describe their experience with our scalable execution.
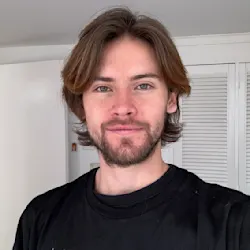
“Quick turnaround and solid quality.”
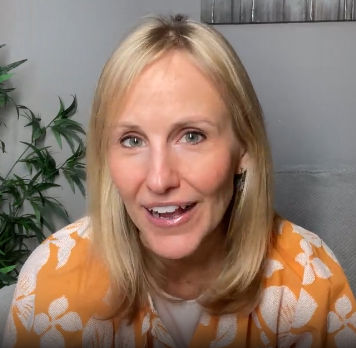
“The instant quote tool saved us time, and the parts were spot-on. Highly recommend Frigate!”
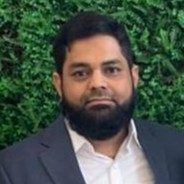
“I would strongly recommend Frigate to anyone who wants to do Rapid Prototyping, and take their ideas to manufacturing. One firm doing all kinds of Product Development!”
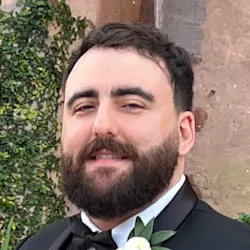
“Great service, fair price, and the parts worked perfectly in our assembly.”
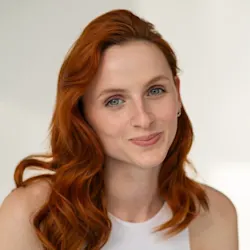
“Top-notch machining and fast shipping. Very satisfied with the results.”
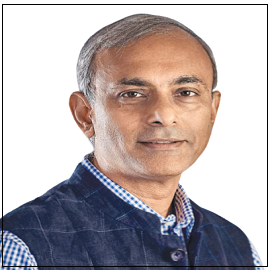
“The next disruption is happening in Prototyping & Manufacturing on-demand and Frigate is leading the way! I personally believe the Frigate's way of IIOT enabled cloud platform with Al.”
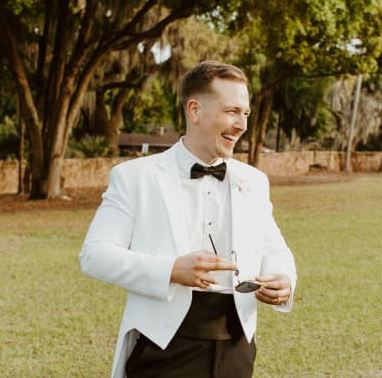
“Frigate delivered high-quality parts at a competitive price. The instant quote tool is a huge plus for us!”

“We appreciate the precision and quality of the machined components in the recent delivery—they meet our specifications perfectly and demonstrate Frigate’s capability for excellent workmanship.”
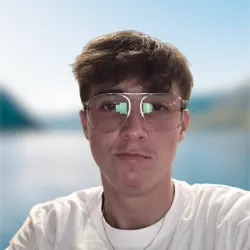
“Flawless execution from quote to delivery.”

“I am absolutely happy to work with supplier like Frigate who were quite proactive & result oriented . Frigate has high willingness team who has strong know how & their passion towards the products & process were absolutely thrilling.”
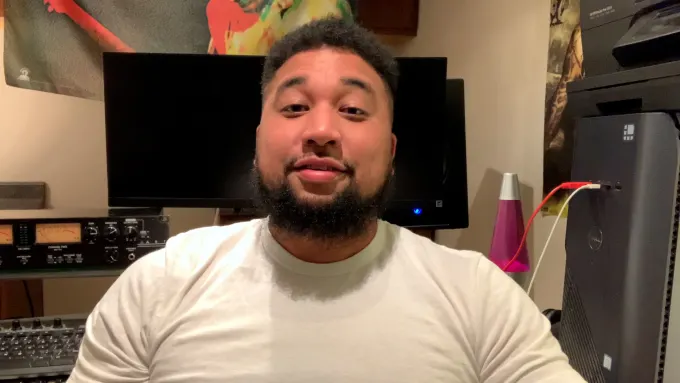
“The precision on these parts is impressive, and they arrived ahead of schedule. Frigate’s process really stands out!”
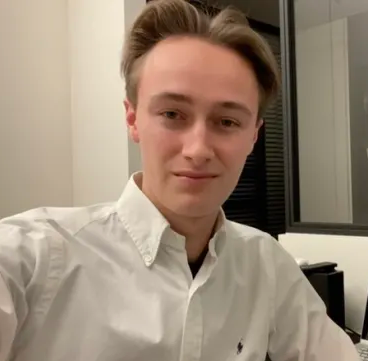
“Parts were exactly as spec’d, and the instant quote made budgeting a breeze.”
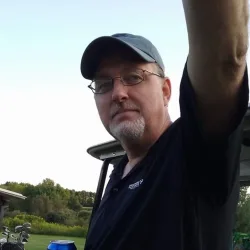
“Good value for the money.”
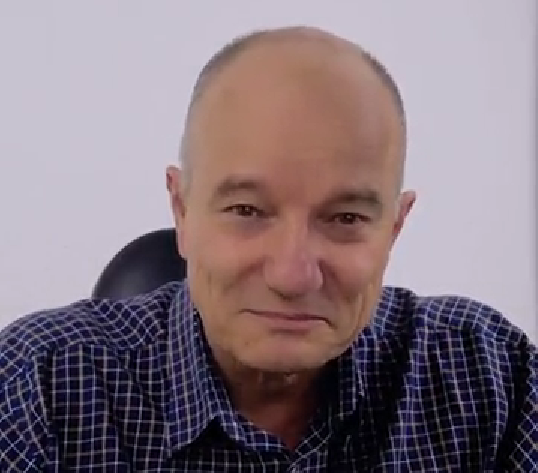
“The finish was perfect, and the team was easy to work with.”

“Working with Frigate has been great. Their proactive, results-driven approach and expertise shine through in every project. It's been a pleasure collaborating with them.”

"We are highly satisfied with the timely delivery and quality of the MIG Welding Cable from Frigate. Their attention to detail, secure packaging, and quick responsiveness stood out. We confidently recommend Frigate Engineering Services Pvt. Ltd. as a reliable manufacturing partner."
Having Doubts? Our FAQ
Check all our Frequently Asked Question
Frigate uses advanced CNC-controlled wire EDM machines that provide high precision and repeatability. These machines can cut intricate shapes and maintain tight tolerances, minimizing the risk of defects in complex parts while ensuring high-quality finishes.
Frigate employs automated wire EDM systems that streamline high-volume production processes. These systems ensure consistent performance, reduce human error, and maintain the quality and precision required for large batches, even under tight deadlines.
Frigate optimizes cutting parameters and uses high-quality wire materials to reduce wear during machining. By fine-tuning machine settings and implementing real-time monitoring, Frigate improves cutting efficiency, extends wire life, and lowers overall production costs.
Frigate employs multi-axis wire EDM machines with high-precision controls that allow tight tolerance control during every step of production. Rigorous in-process inspections and advanced measurement systems ensure that each component meets the requirements of dimensional accuracy and surface finish.
Frigate works with a wide range of specialized alloys, including hardened steels and exotic materials, ensuring compatibility with wire EDM machining. The team adjusts cutting parameters based on material properties, optimizing the machining process to preserve material integrity and achieve the desired part specifications.
Manufacturing Capability/Capacity
Ferrous casting
Mold size(max): 1m X 1m
Weight Range: 1 KG ~ 30 KGS
Mold size(max): 1.5m X 1.5m
Weight Range: 30 KG ~ 150 KGS
Mold size(max): 3m X 3m
Weight Range: 100 KG ~ 1000 KGS
Mold size(max): 500 MM X 500 MM
Weight Range: 0.250 KG ~ 20 KGS
Mold size(max): 500 MM X 500 MM
Weight Range: 0.100 KG X 20 KGS
Non-ferrous casting
Capacity: 5000 MT/a
Range of weight: 100 gm to 20 KGS
Mold size(max): 1 M X 1 M
Weight Range: 0.5 KG X 50 KGS
Mold size(max): 1 M X 1 M
Weight Range: 0.5 KG X 50 KGS
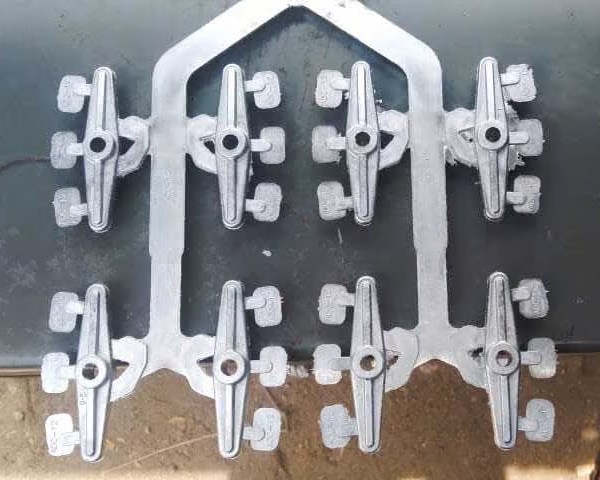
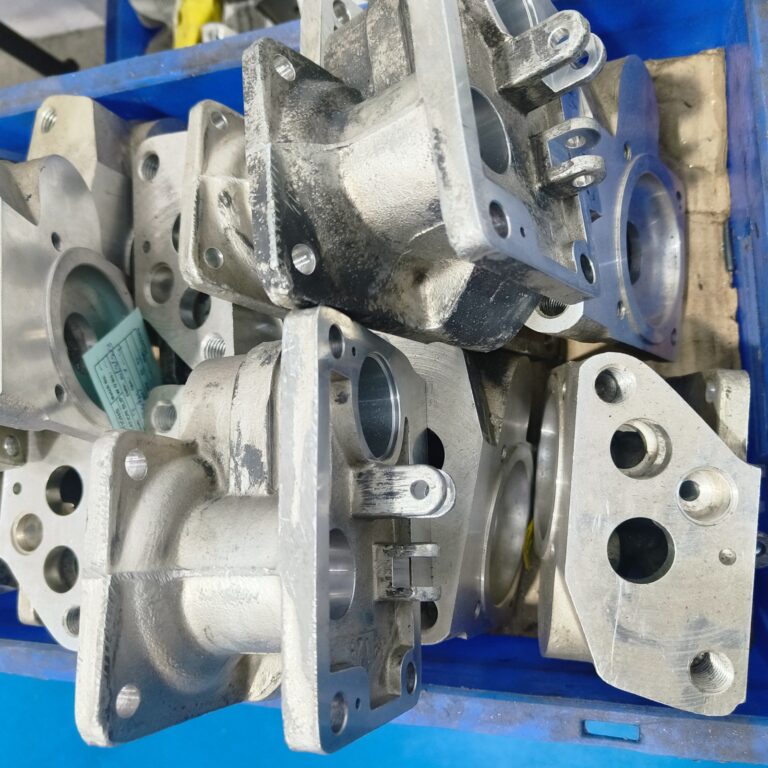
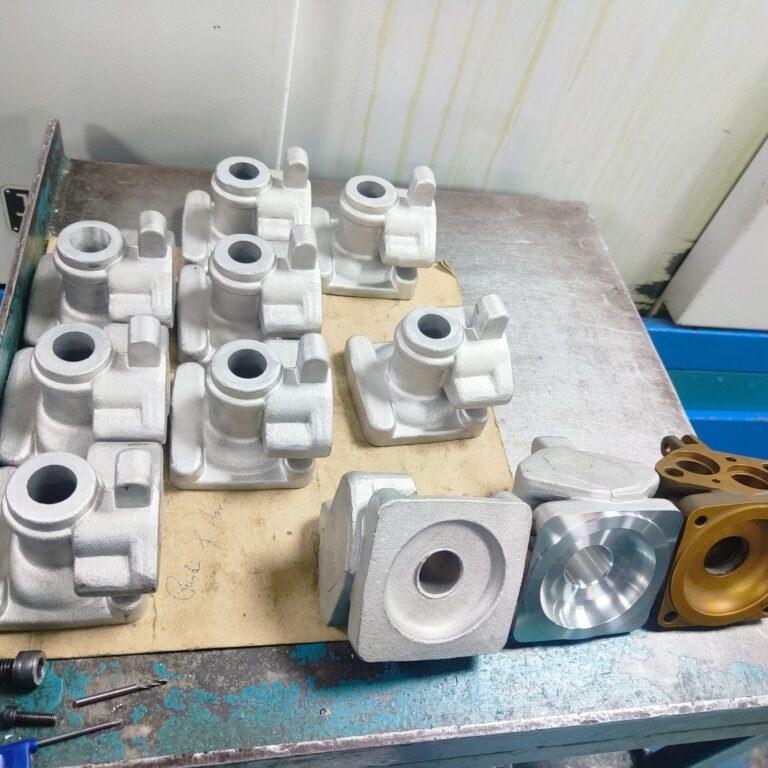
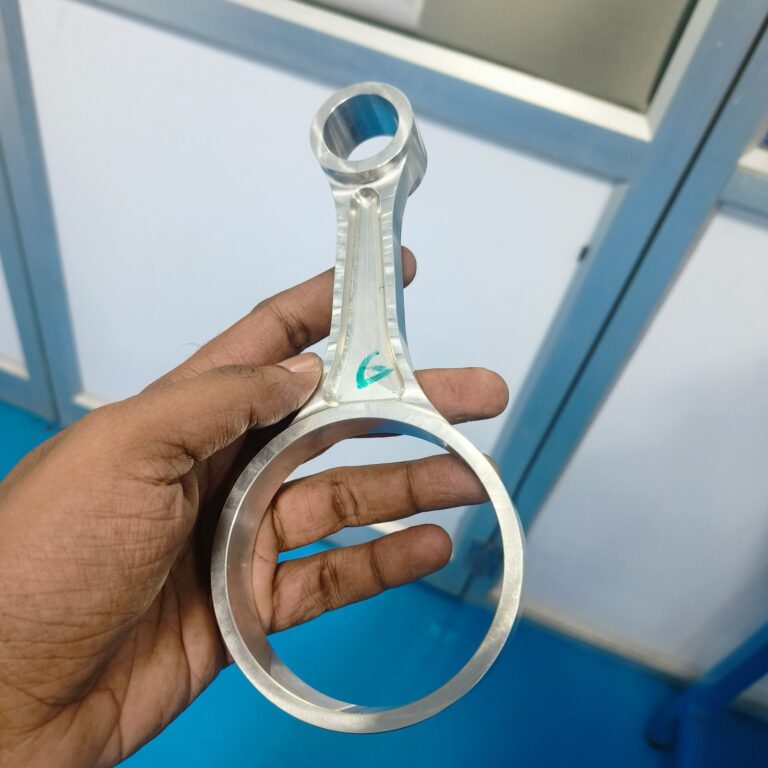
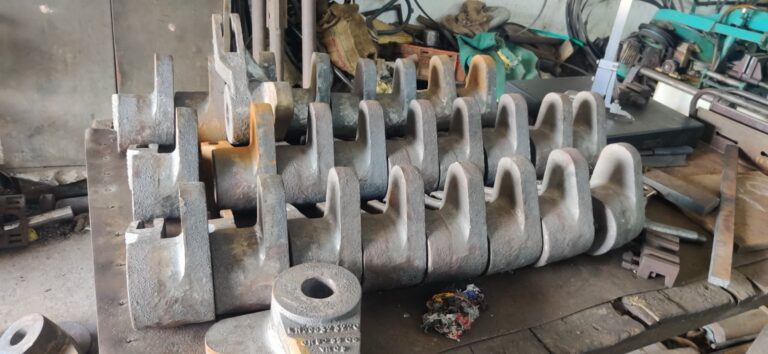
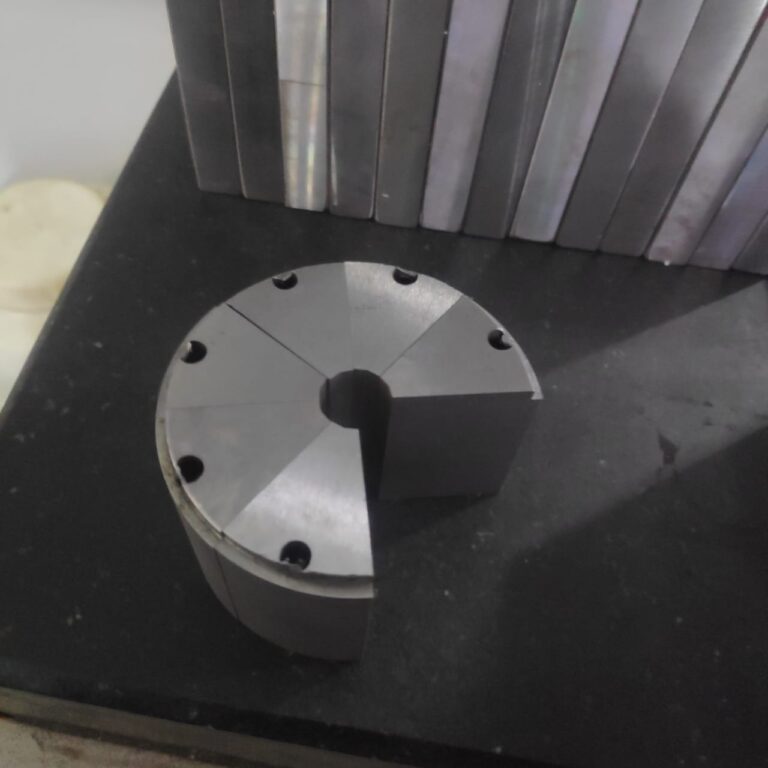
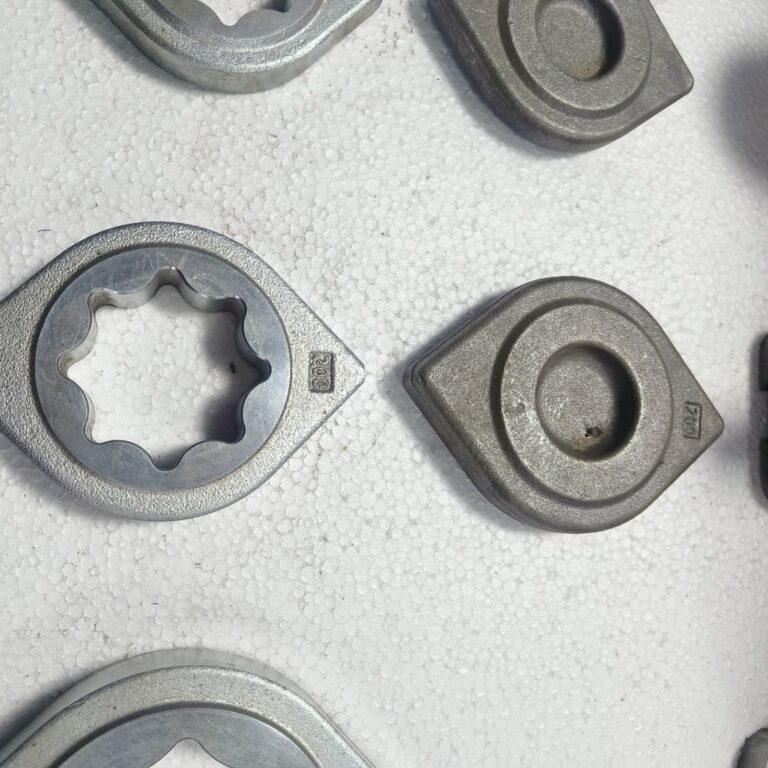
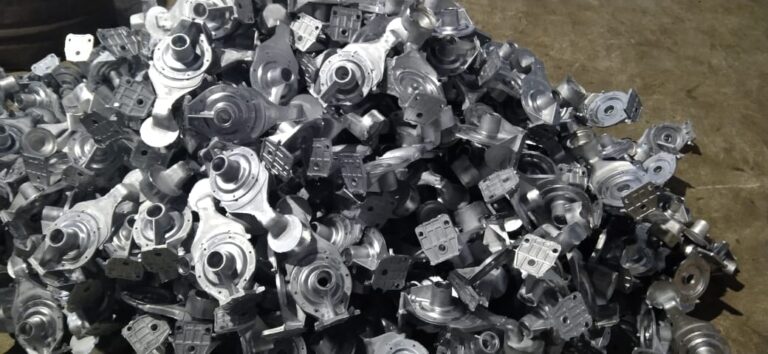
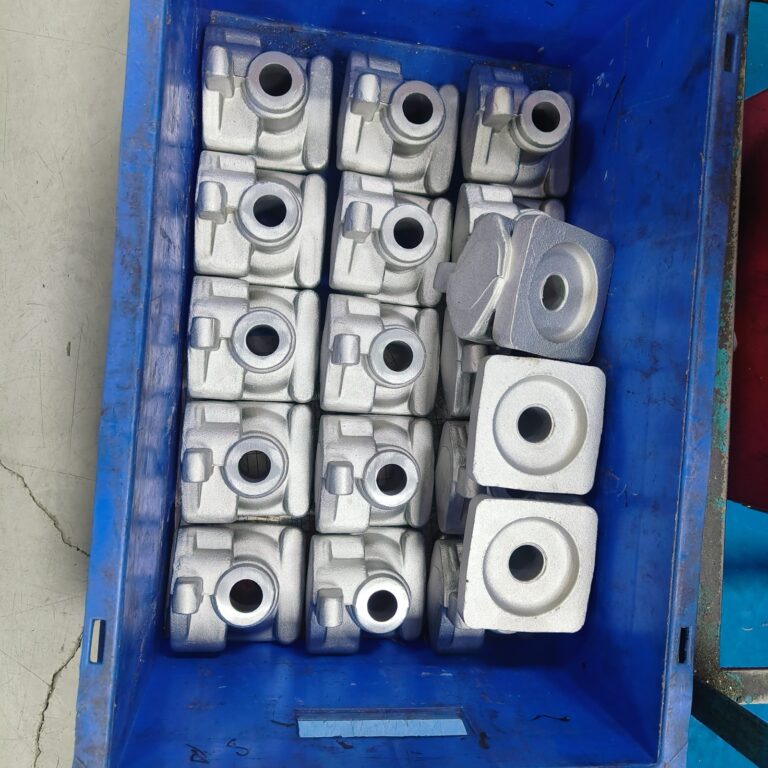
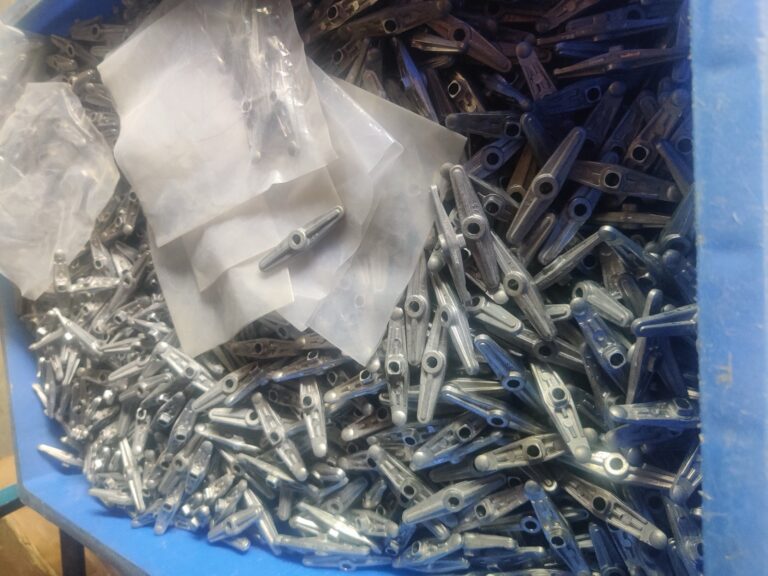
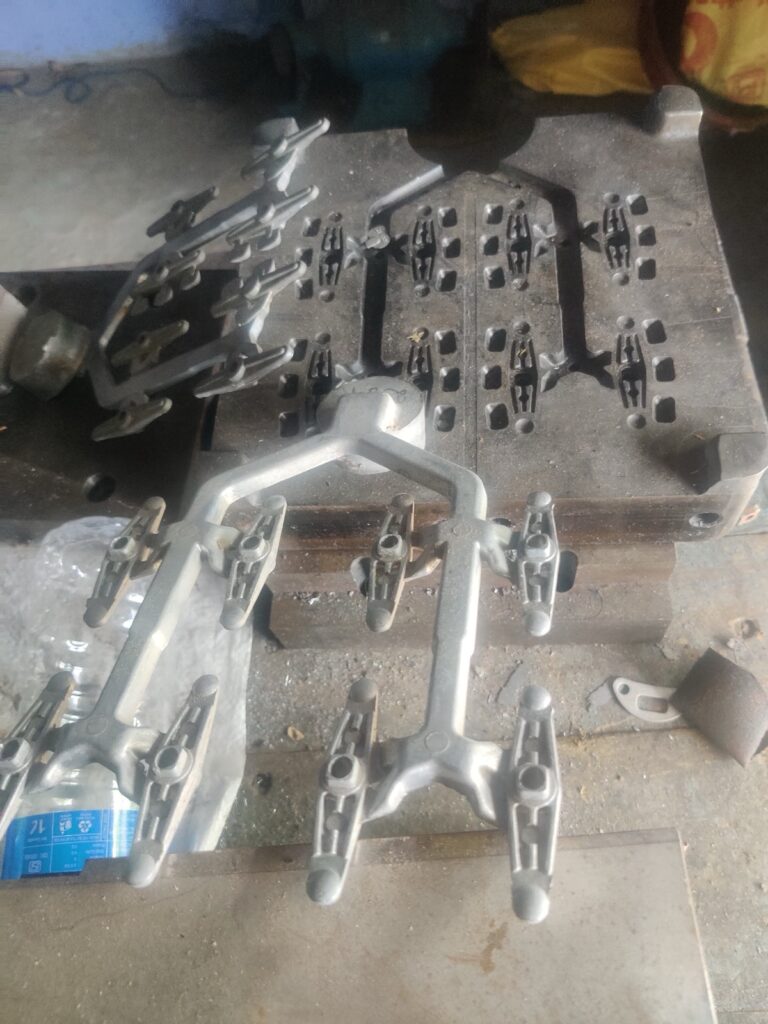
Forging
Capacity: 20,000 Tons per Annum
Range of weight: 300 KG to 1 Ton
Hammering: 5 Ton
Range of weight: 0.2 KG to 200 KGS
Hammering: 1600 Ton Hydraulic press
Ring size: 350 MM OD to 3000 MM OD
Range of weight: 15 KGS to 3200 KGS
Materials
Carbon Steel, Stainless Steel (AUSTENITE), Alloy Steel, Stainless Steel (MARTENSITE), etc.
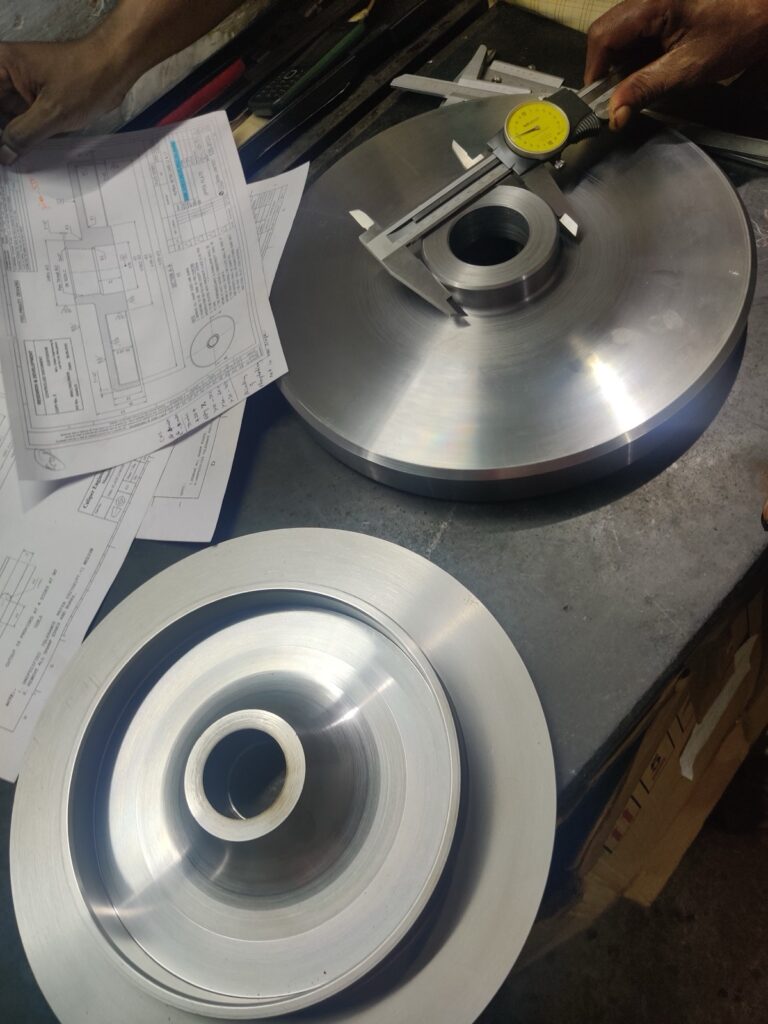
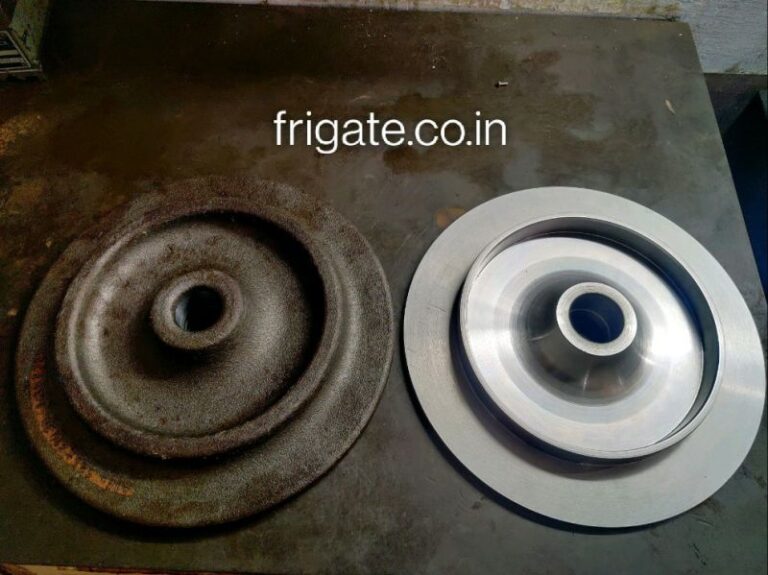
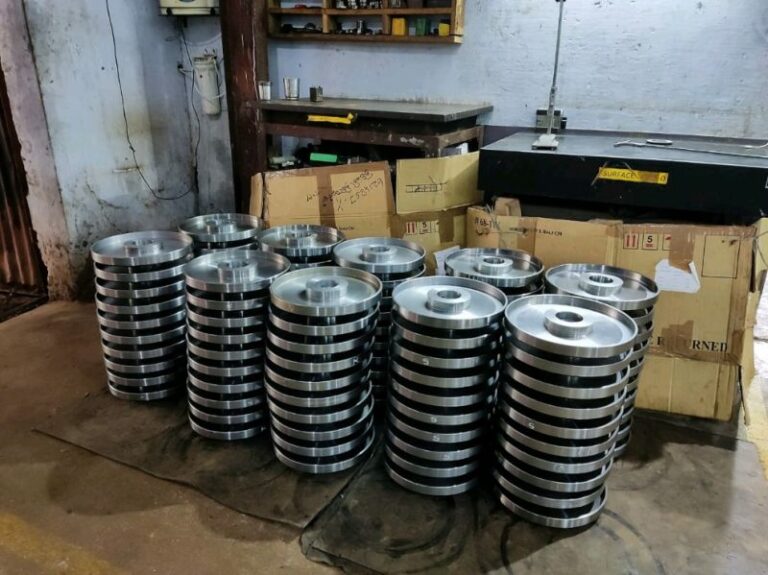
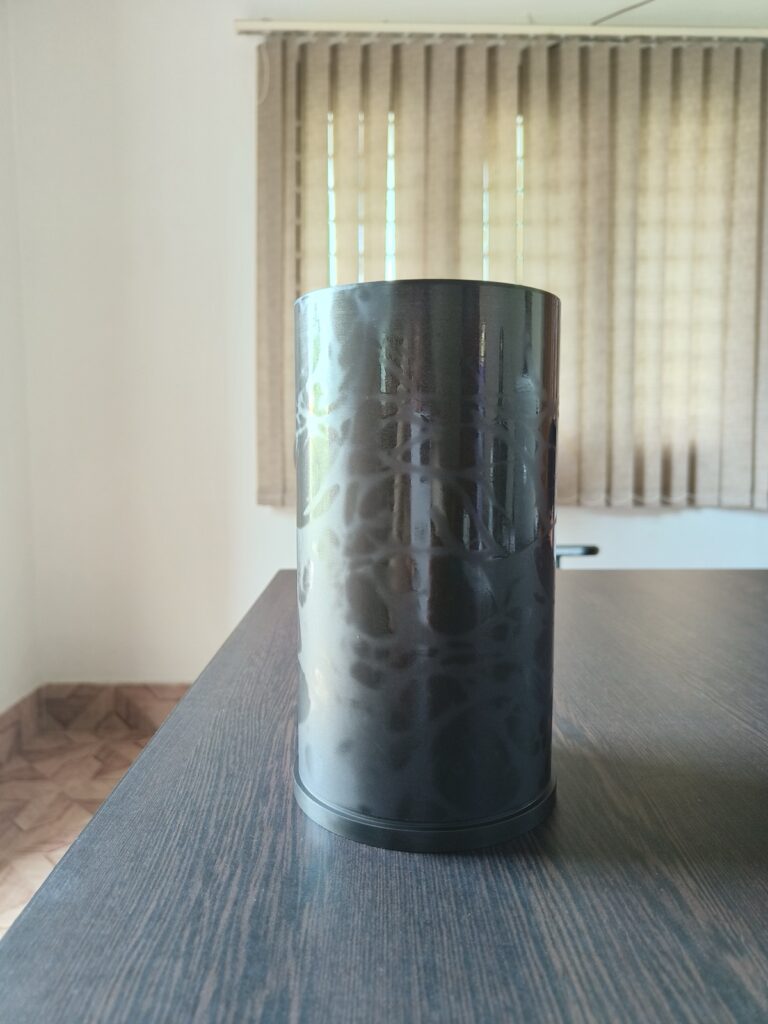
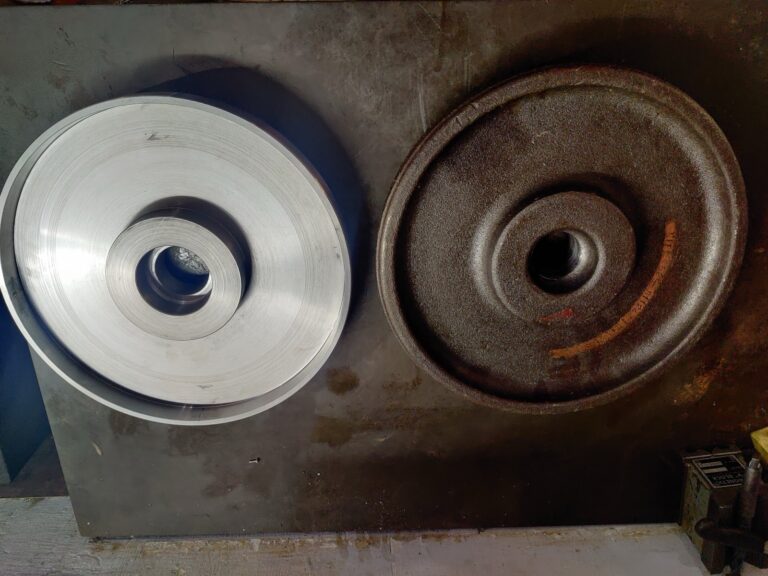
Machining
1 to 1000 MM
1 to 1000 MM
1 to 1000 MM
Materials
Steel, Aluminum, Brass, Copper, Titanium, Nickel Alloys, Tungsten Carbide, etc.
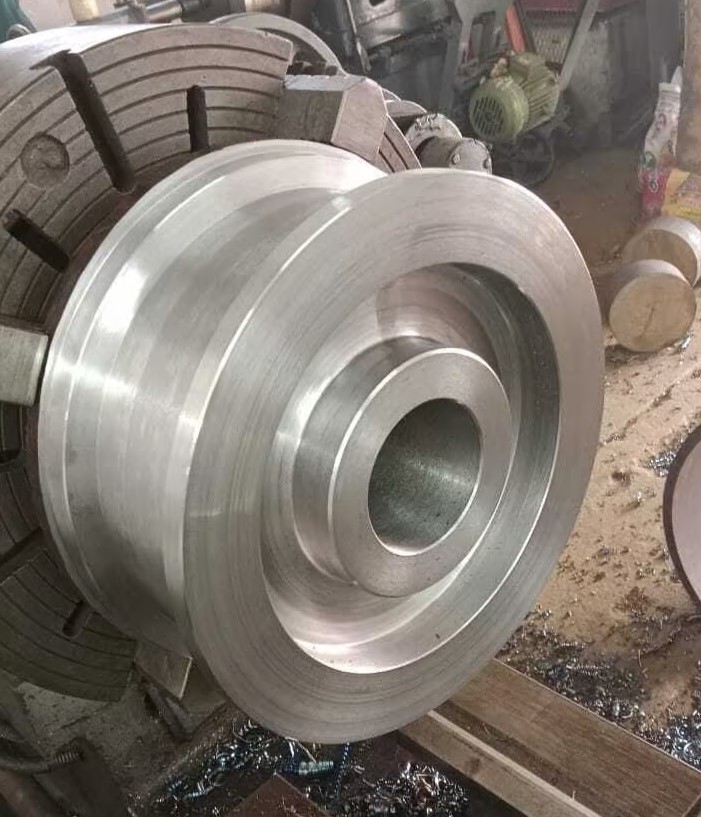
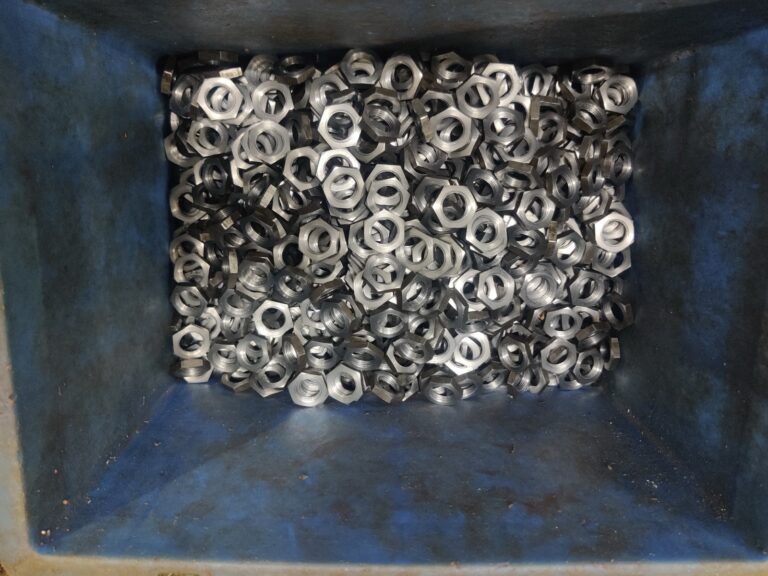
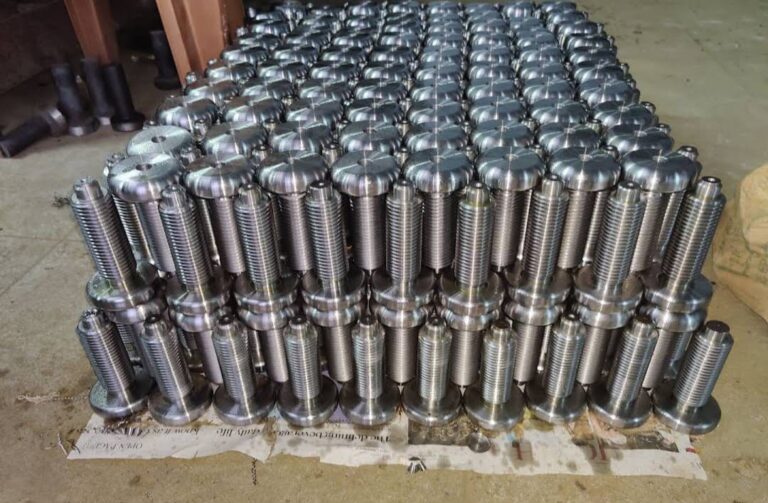
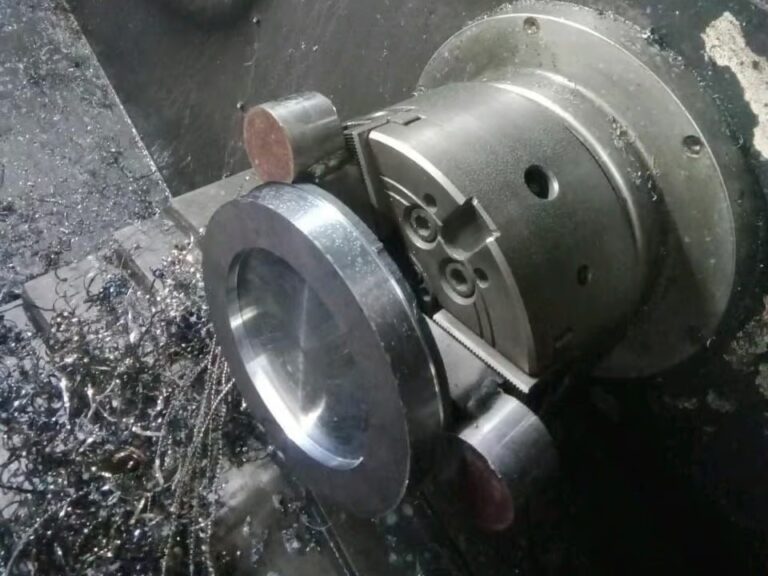
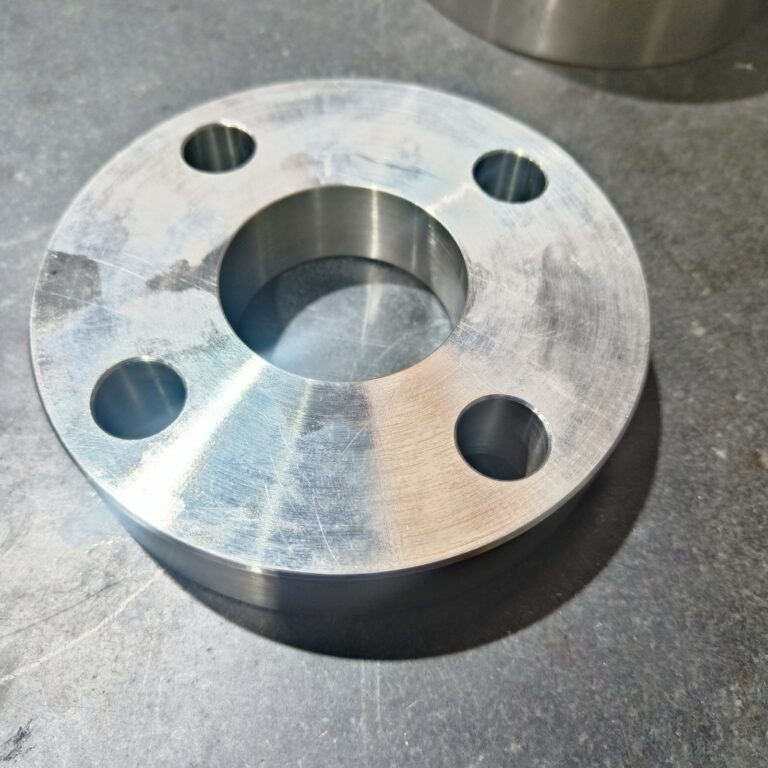
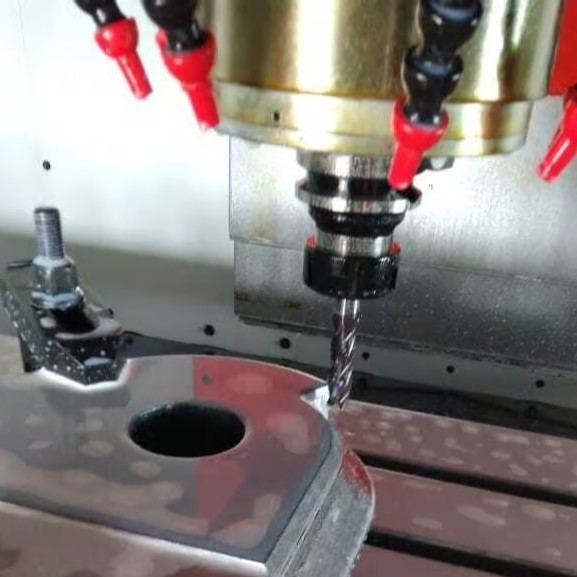
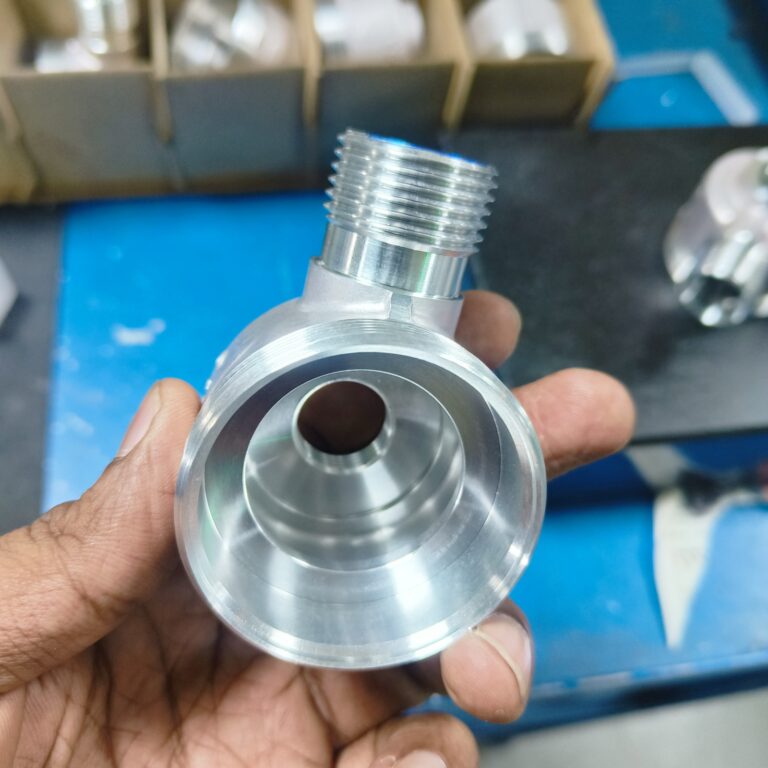
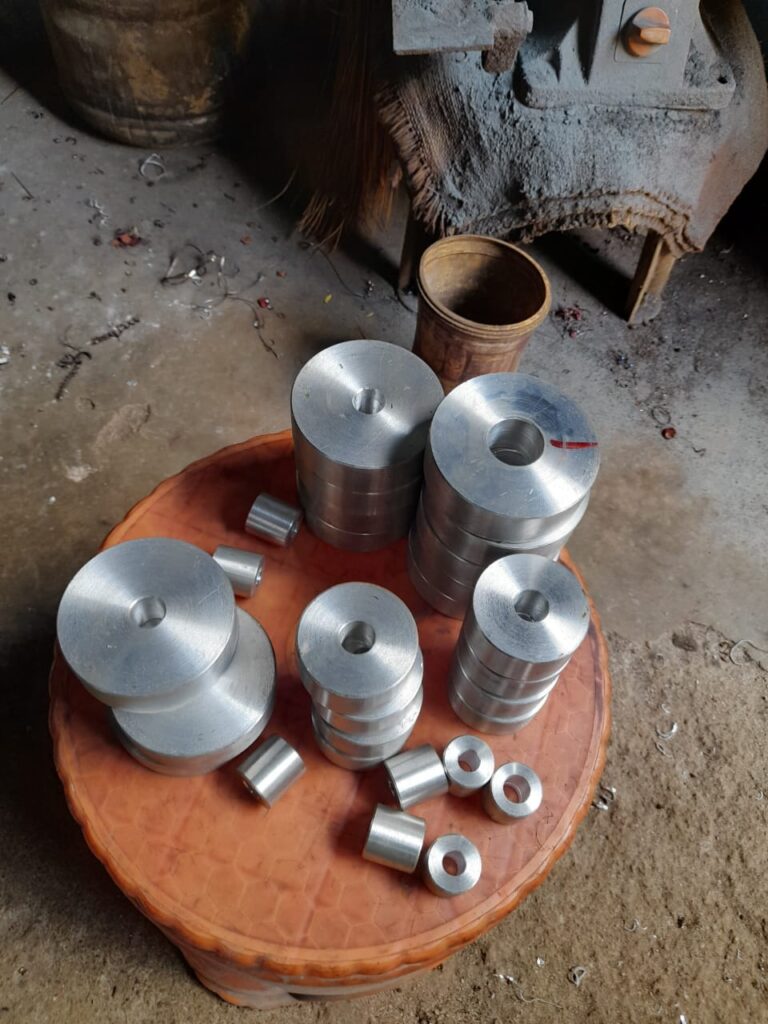
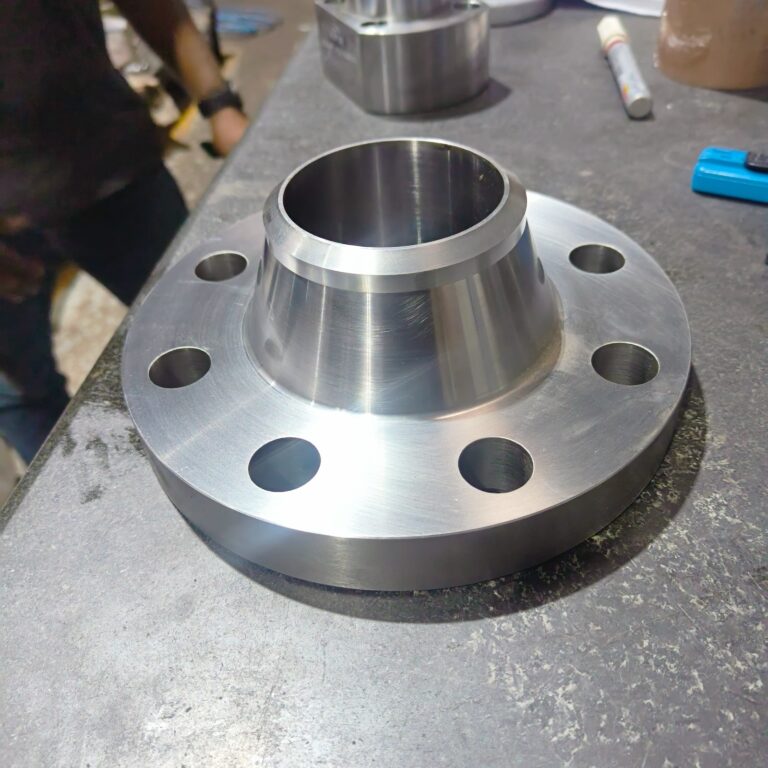
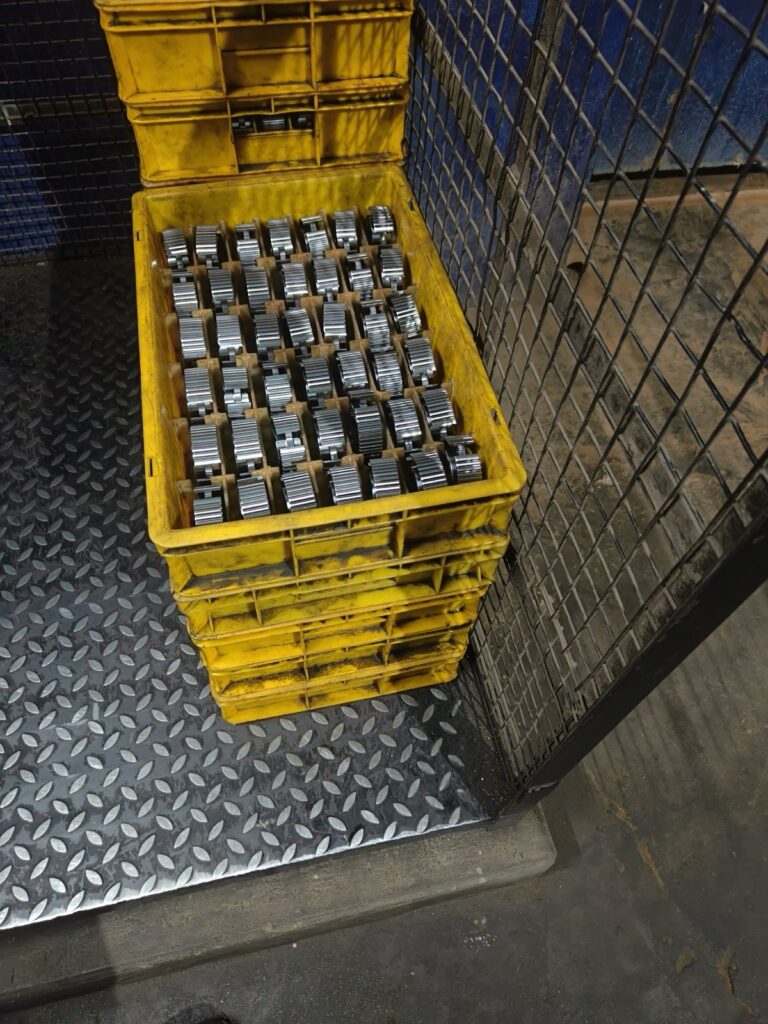
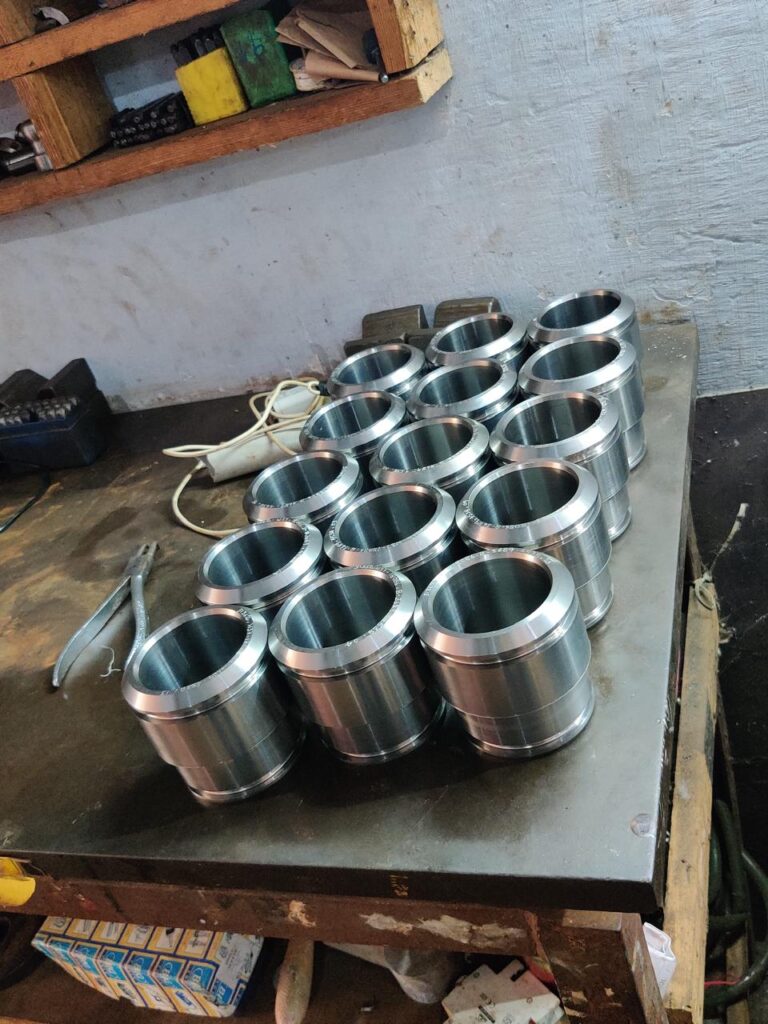
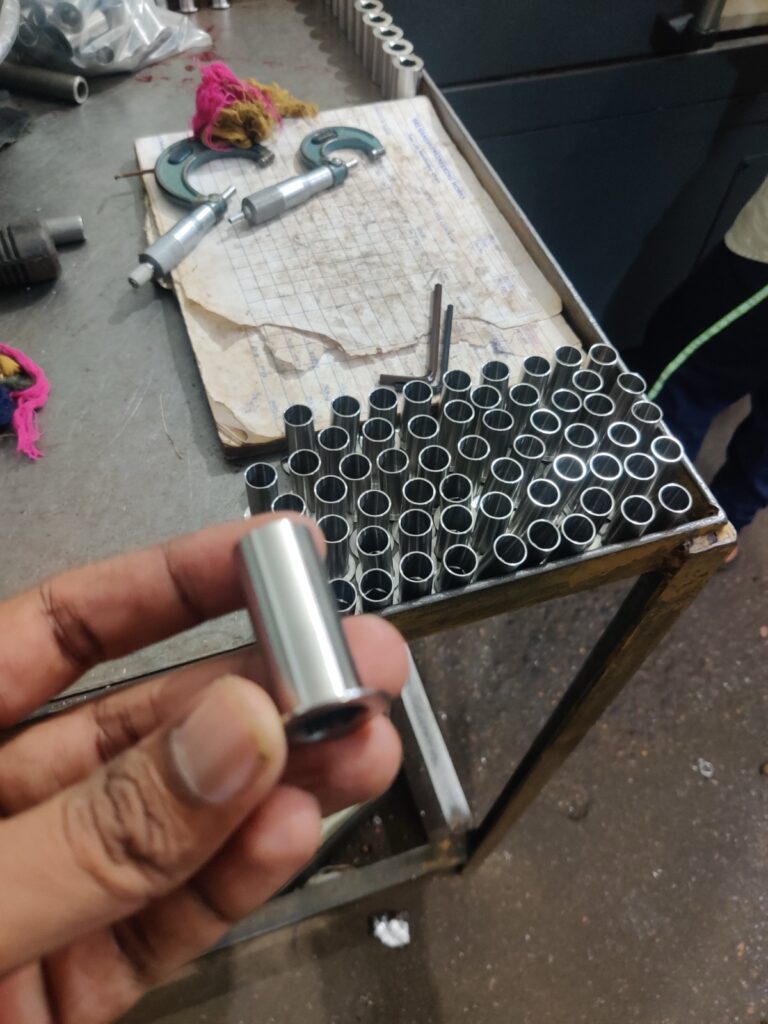
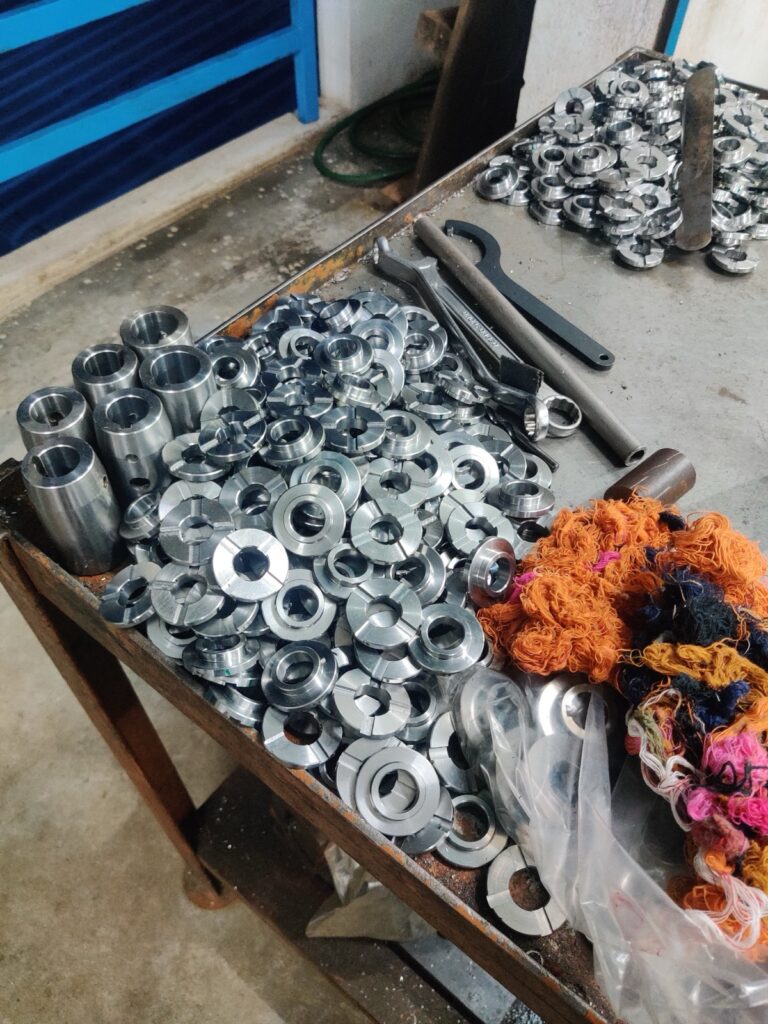
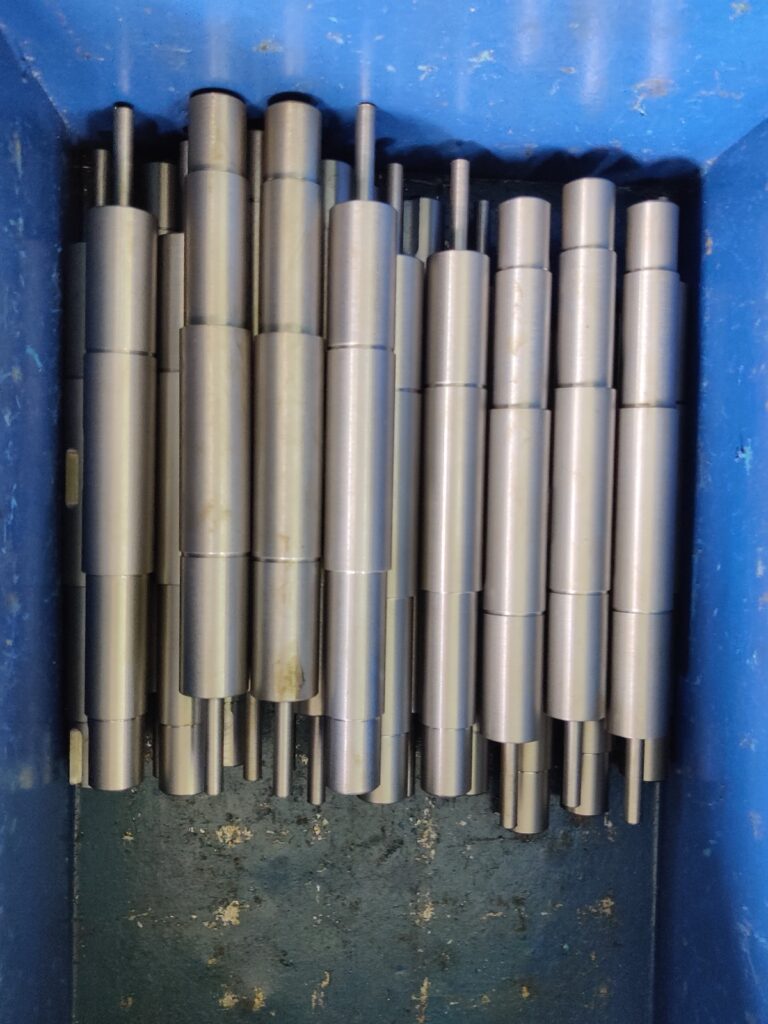
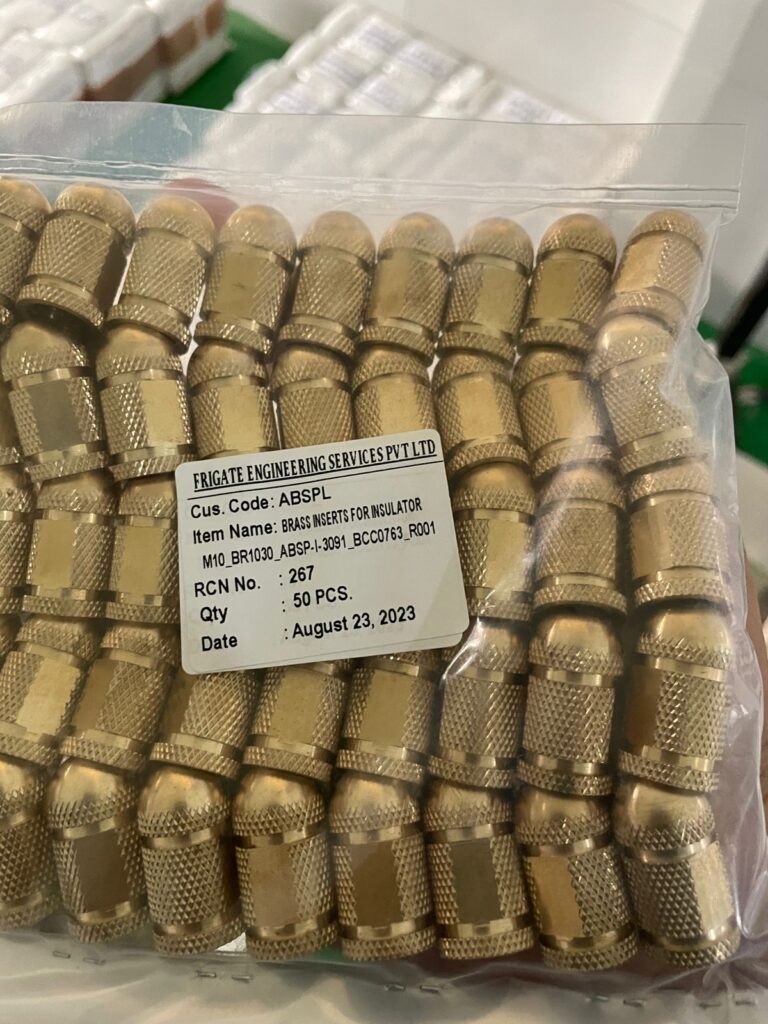
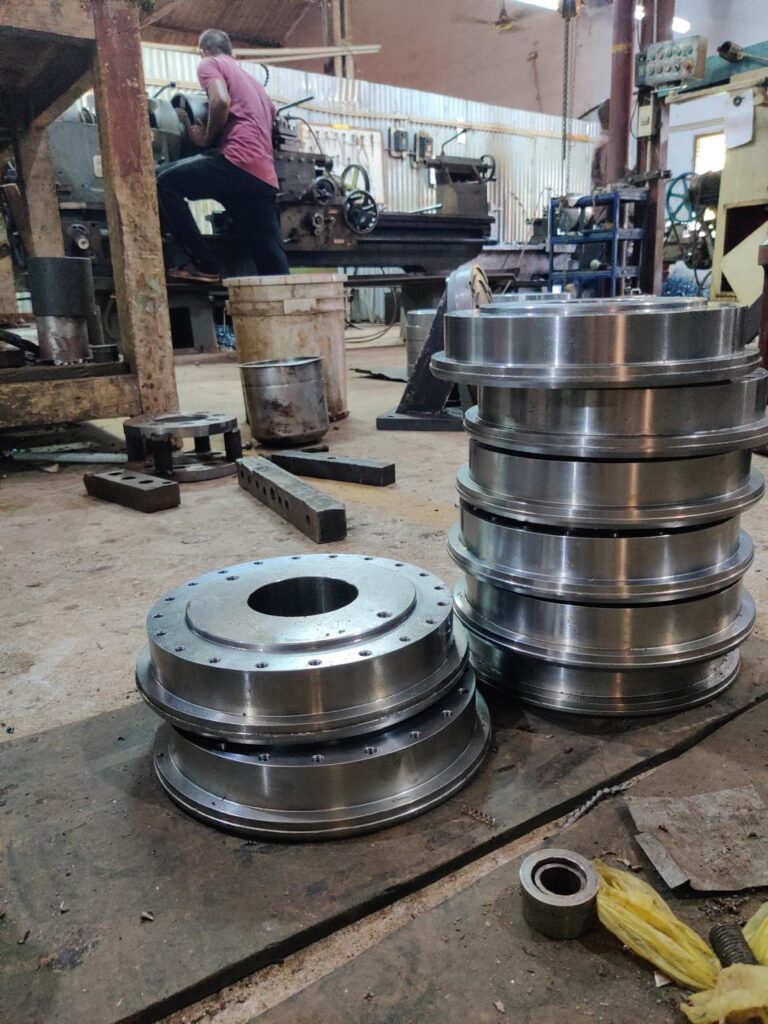
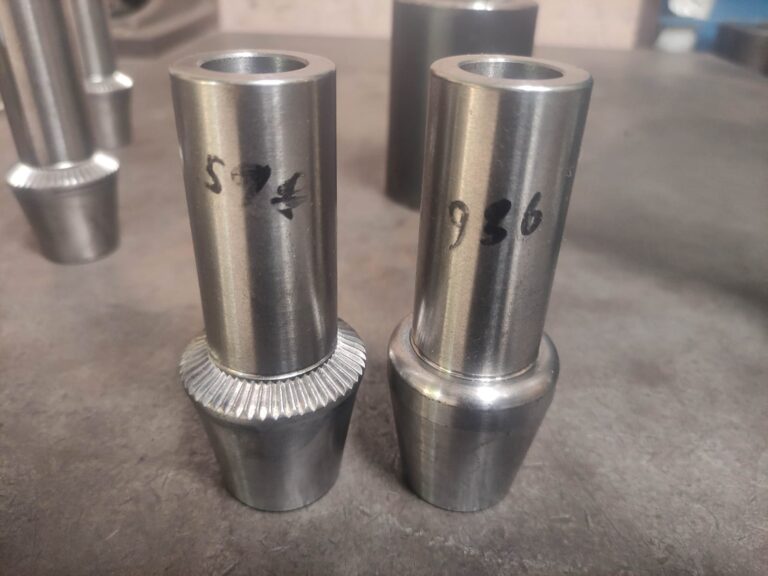
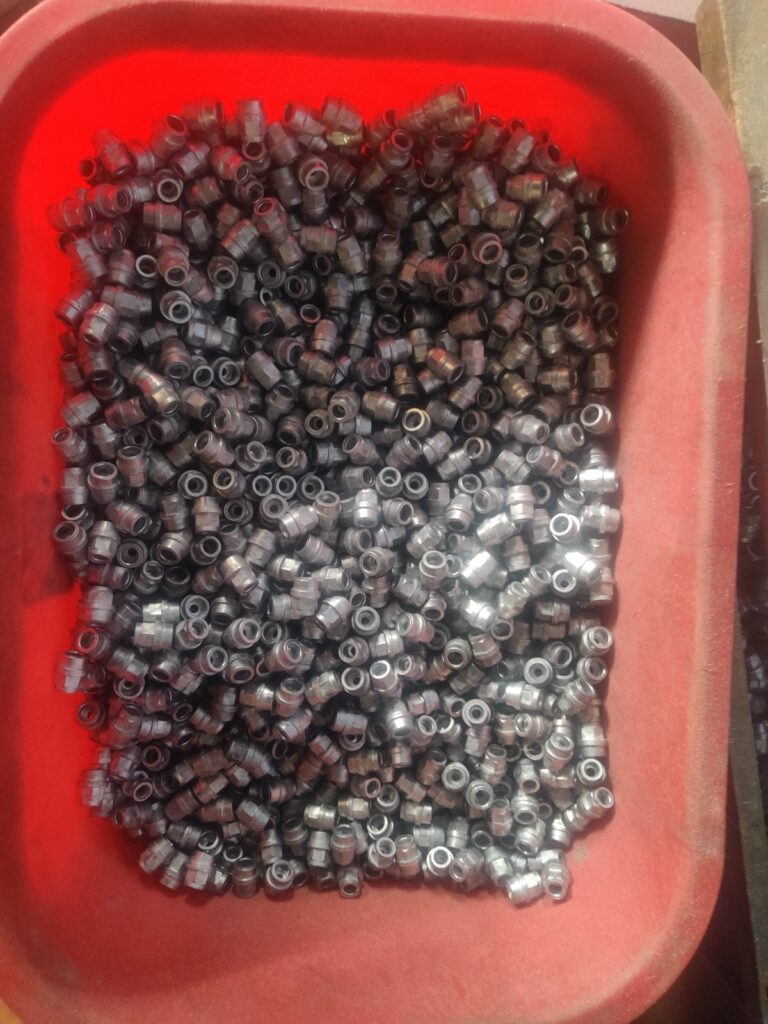
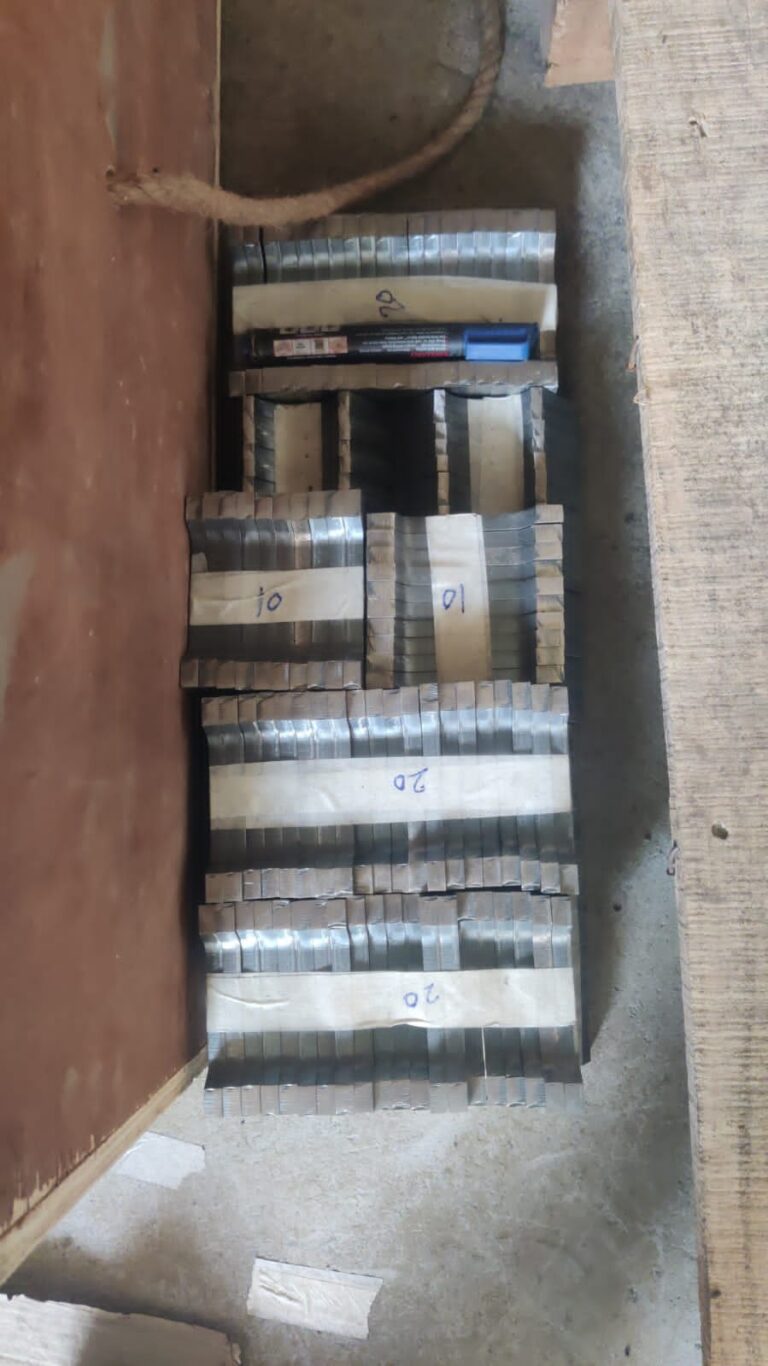
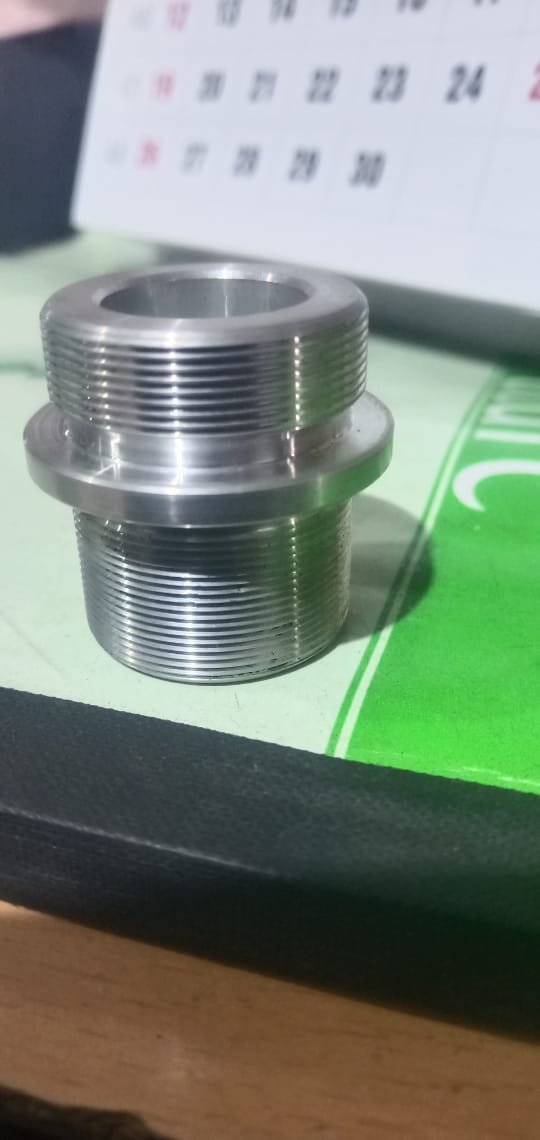
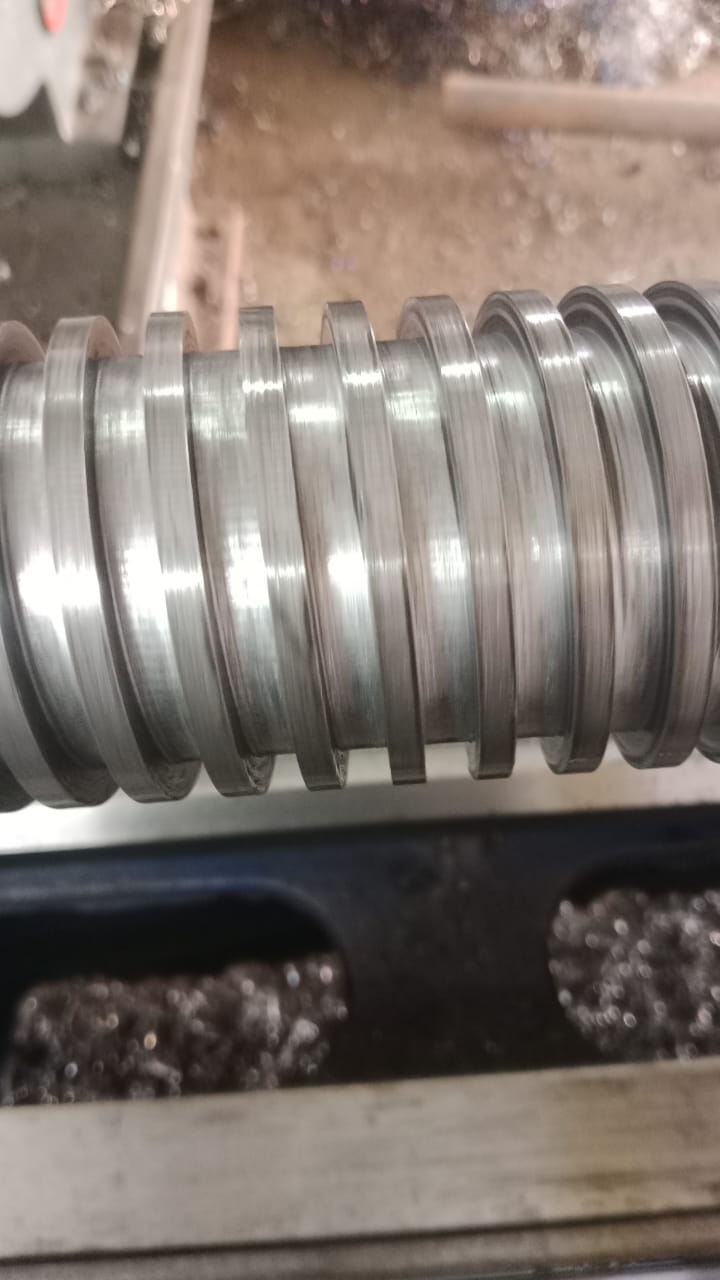
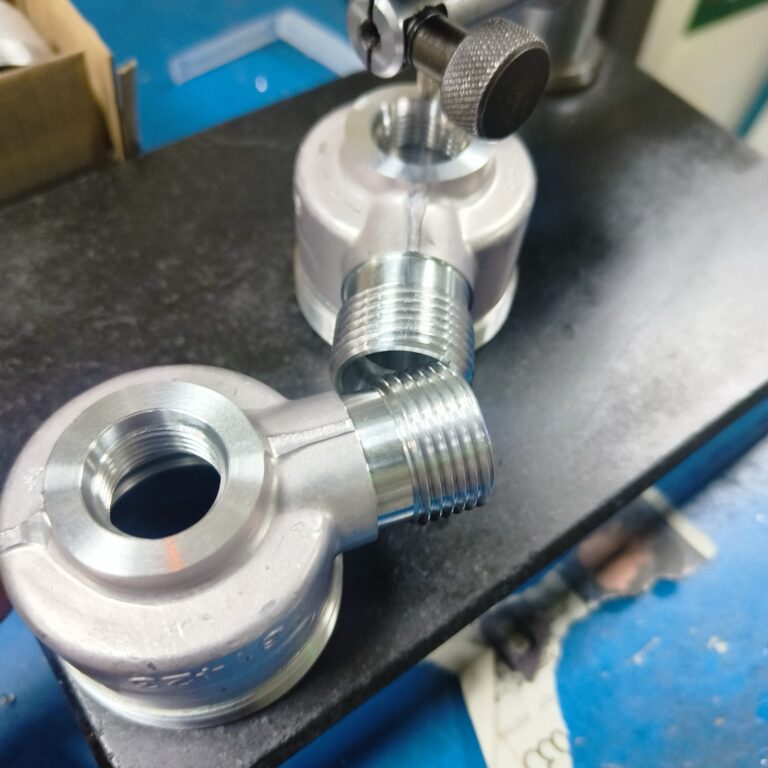
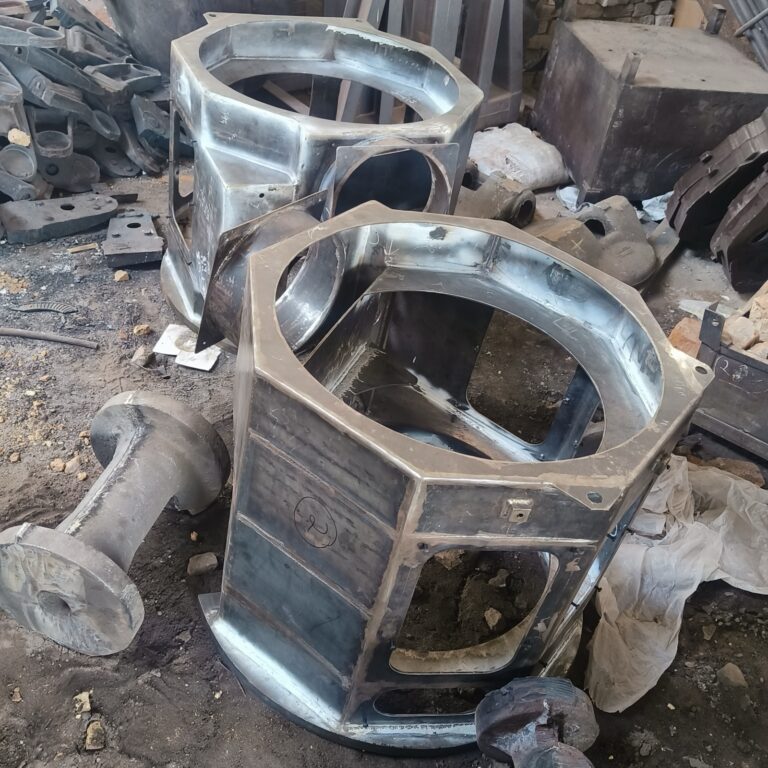
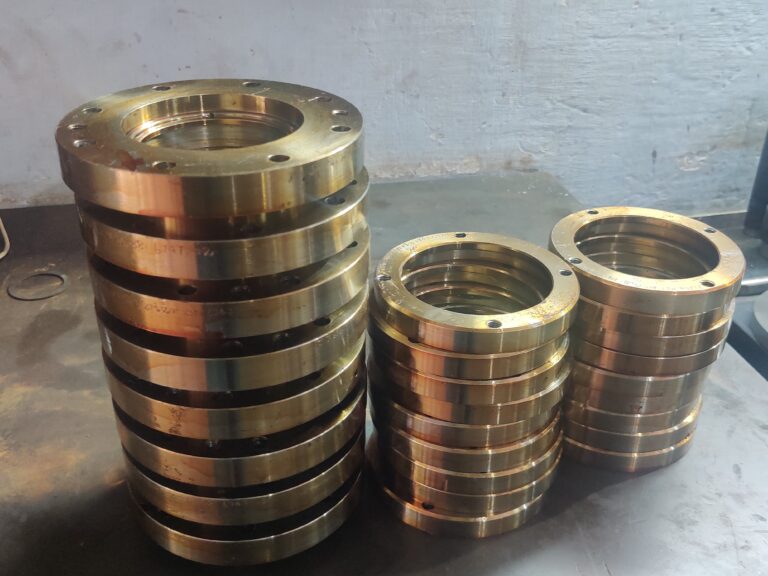
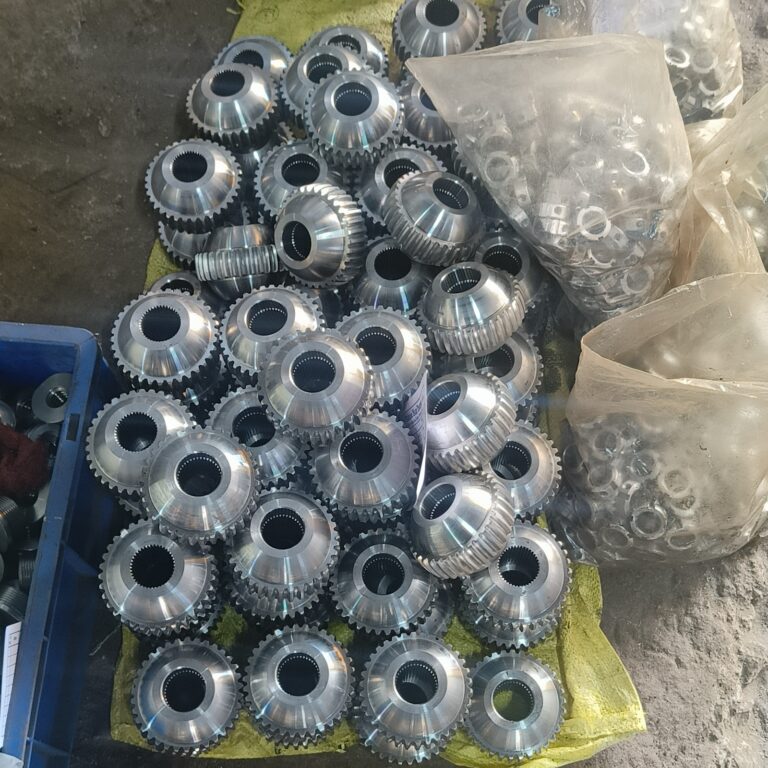
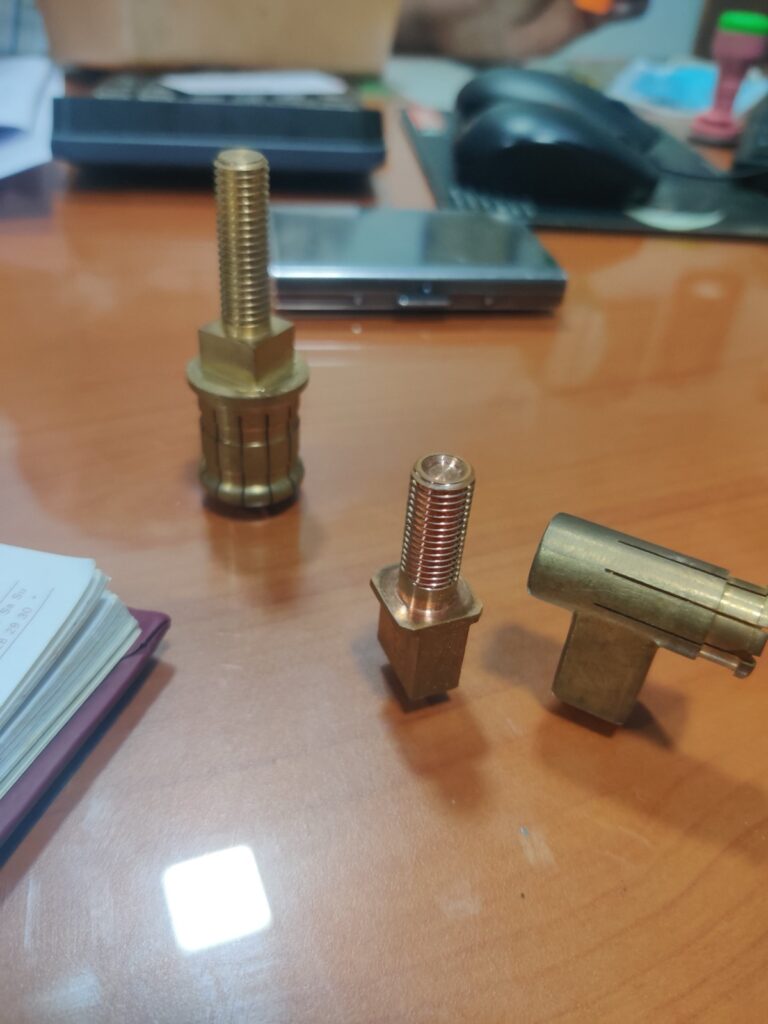
Plastics
Materials
1250 X 1250 MM
Within 10 microns
Engineering Plastics, Polyethylene, Polypropylene, Polyvinyl chloride, Polyethylene terephthalate, Bioplastics, etc.
Rubber
Materials
Natural rubber, Styrene-Butadiene Rubber, Nitrile Butadiene Rubber, Silicone Rubber, Fluorocarbon Rubber, Recycled Rubber, etc.
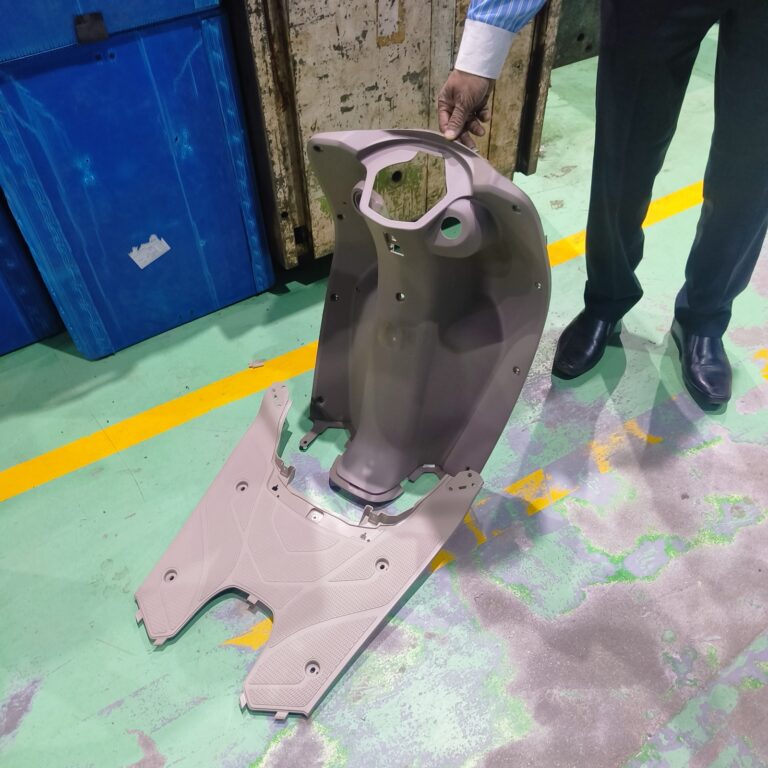
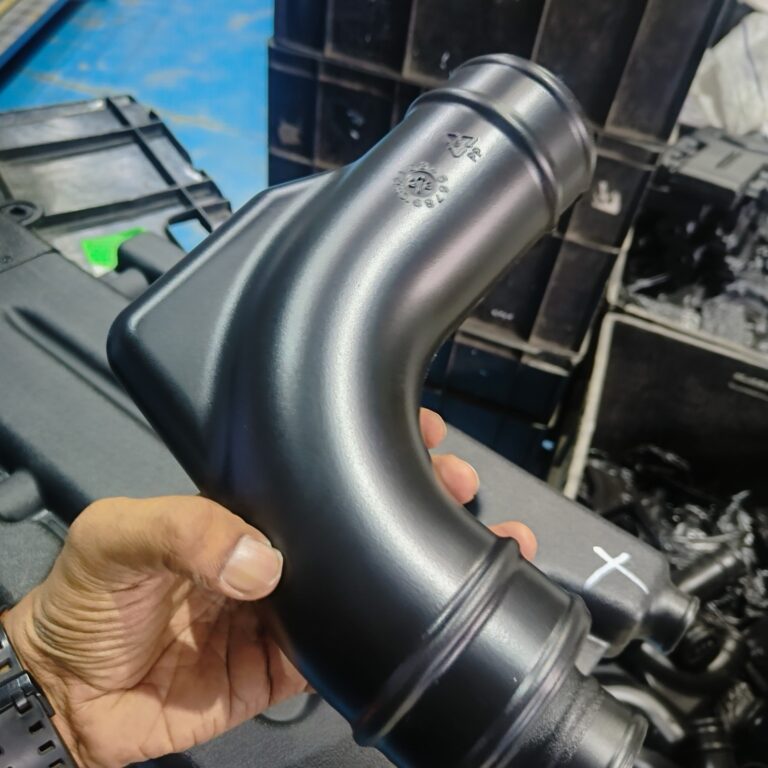
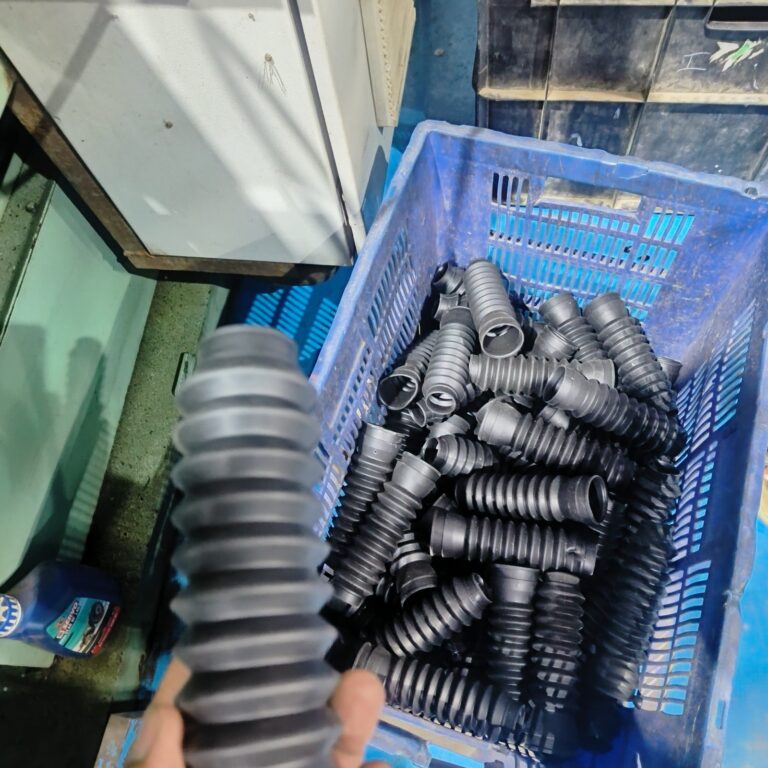
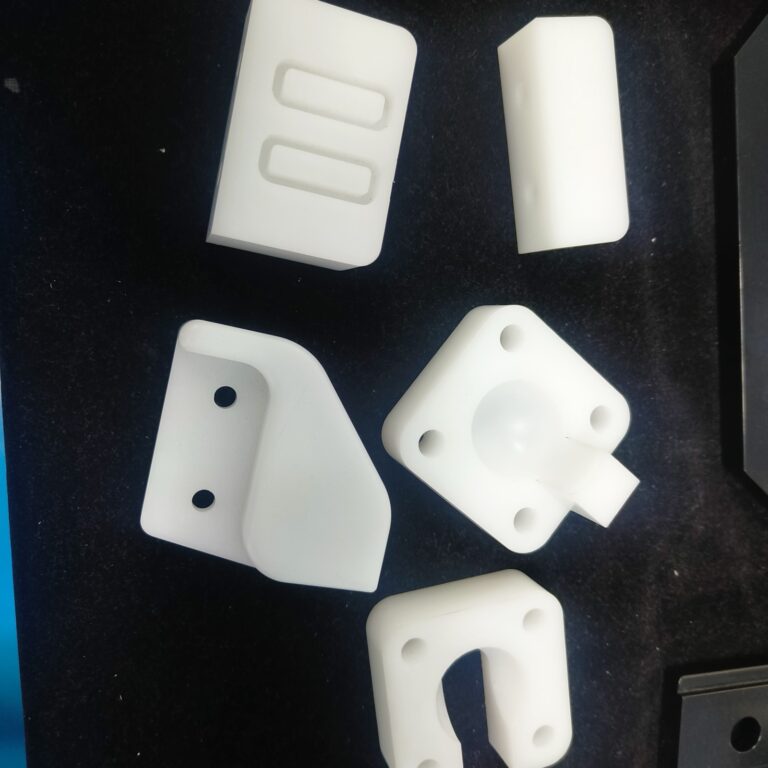
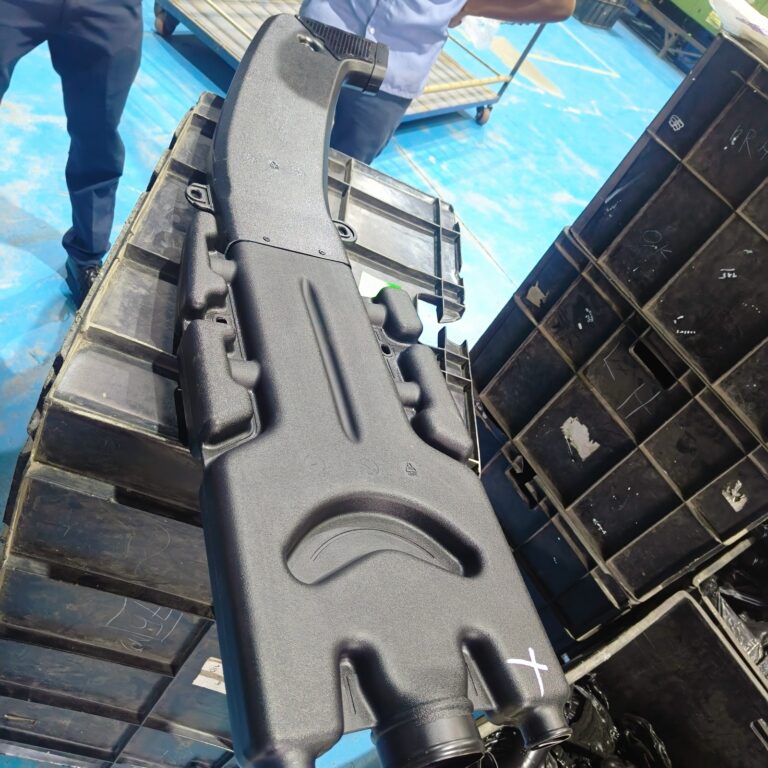
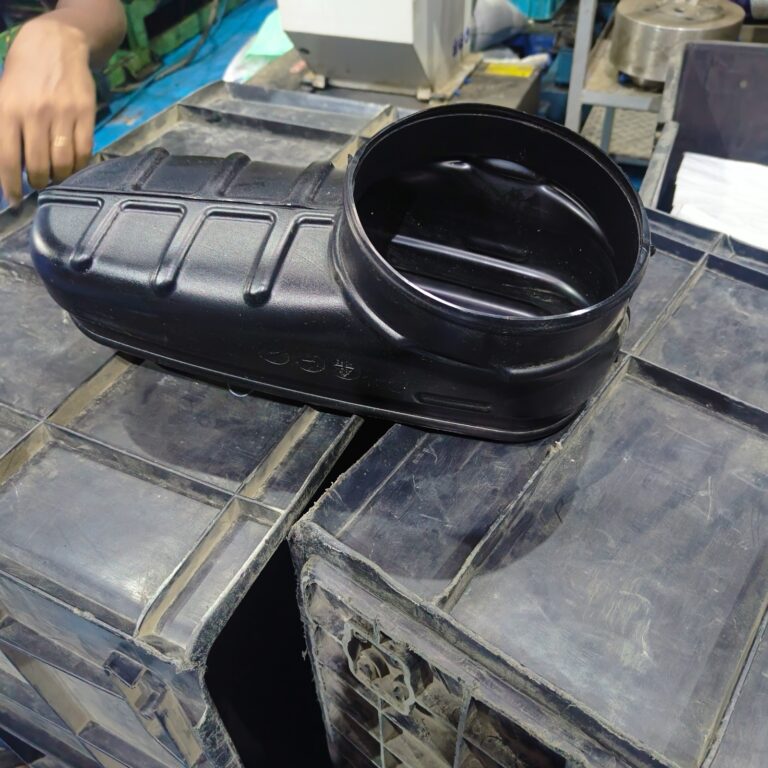
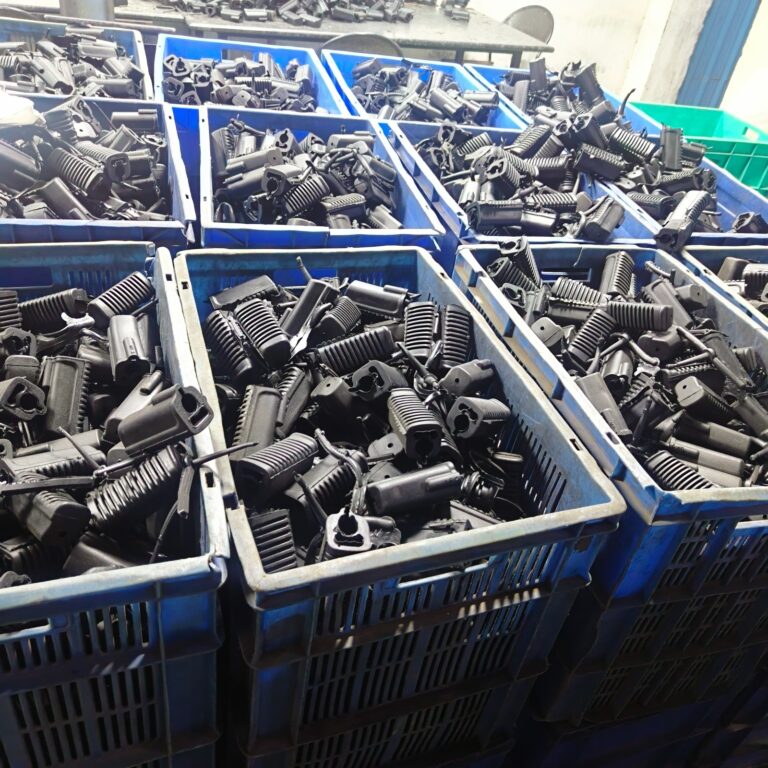
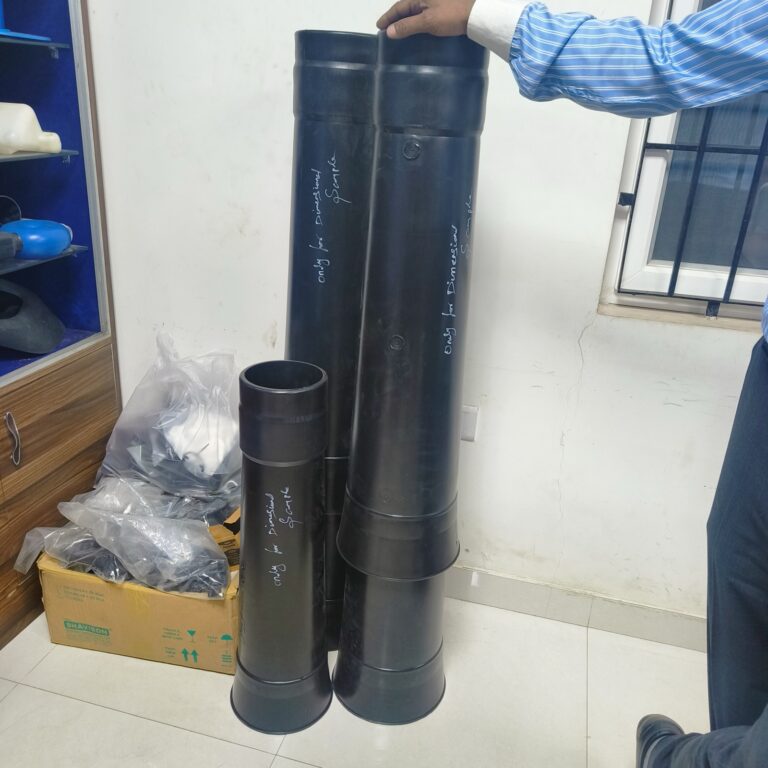
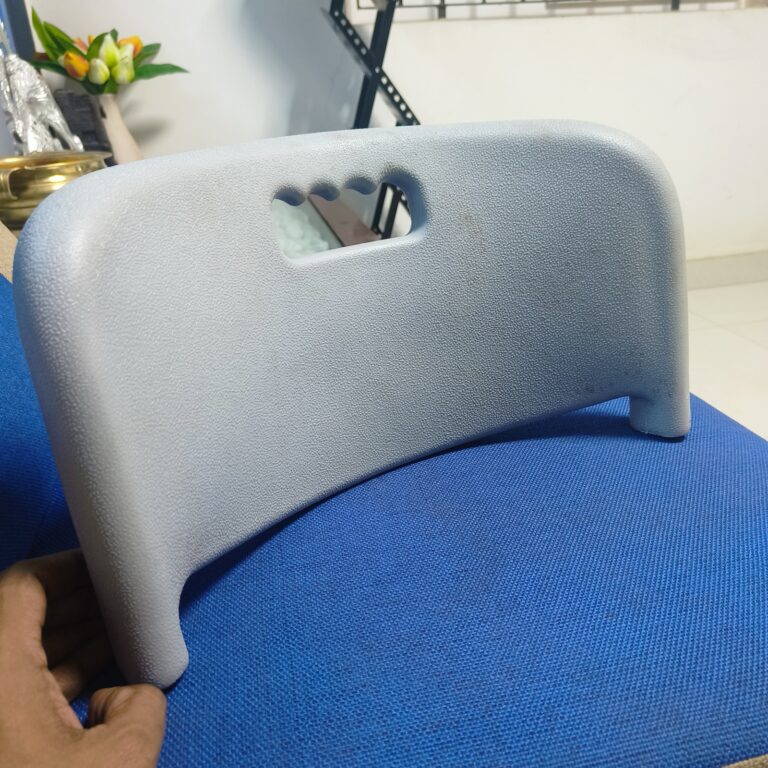
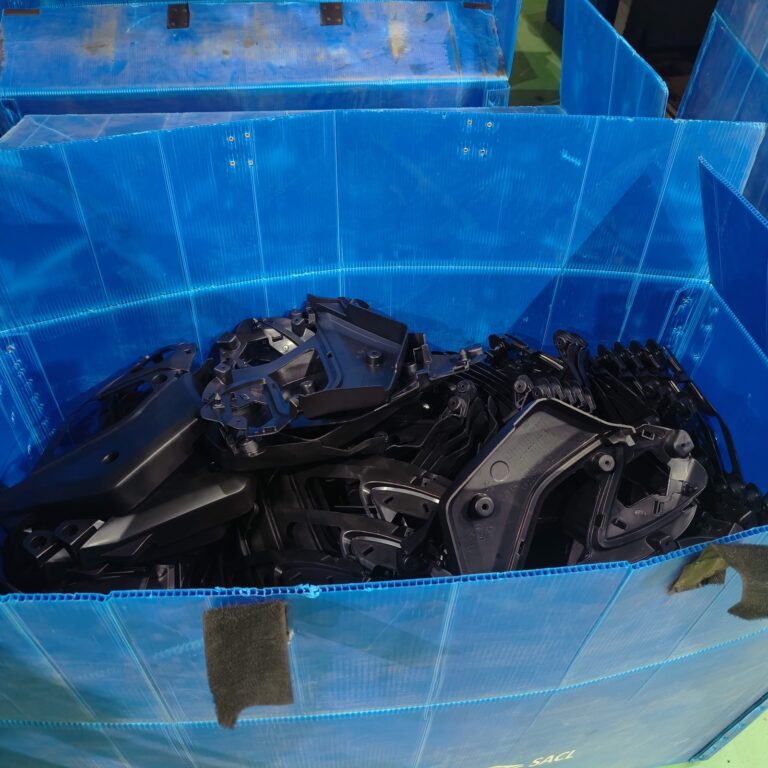
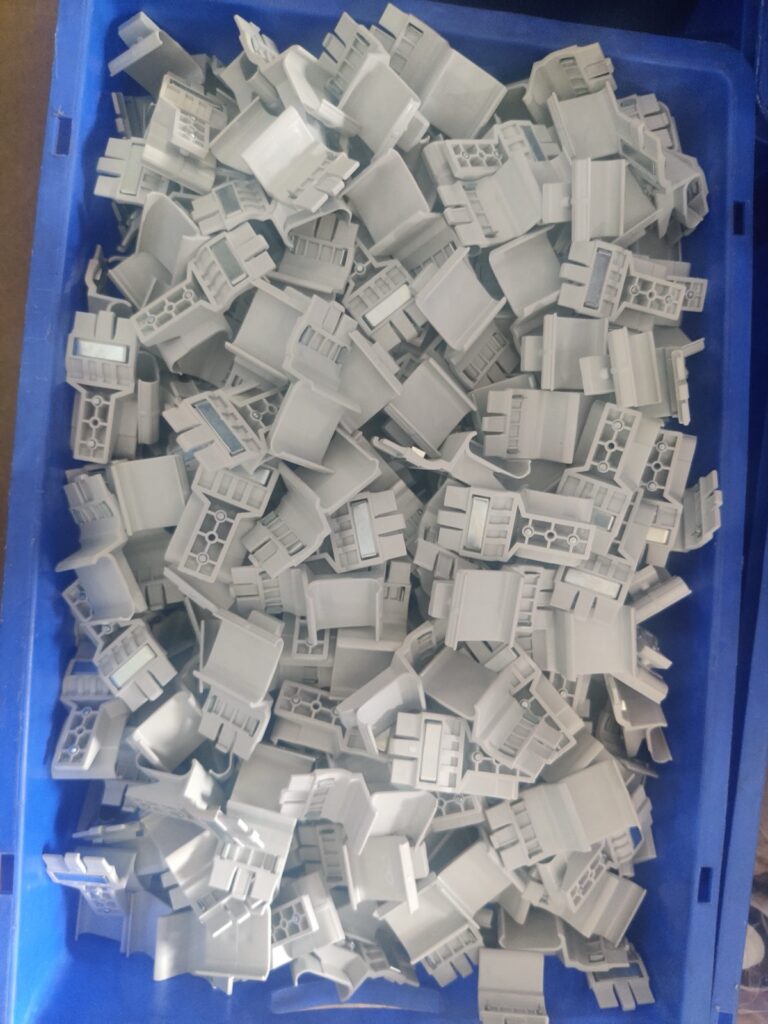
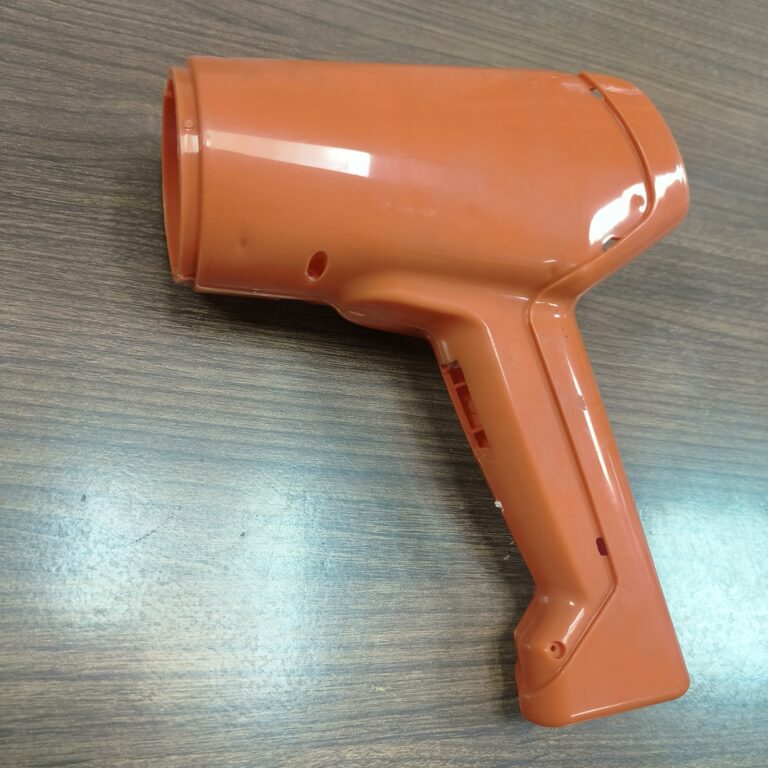
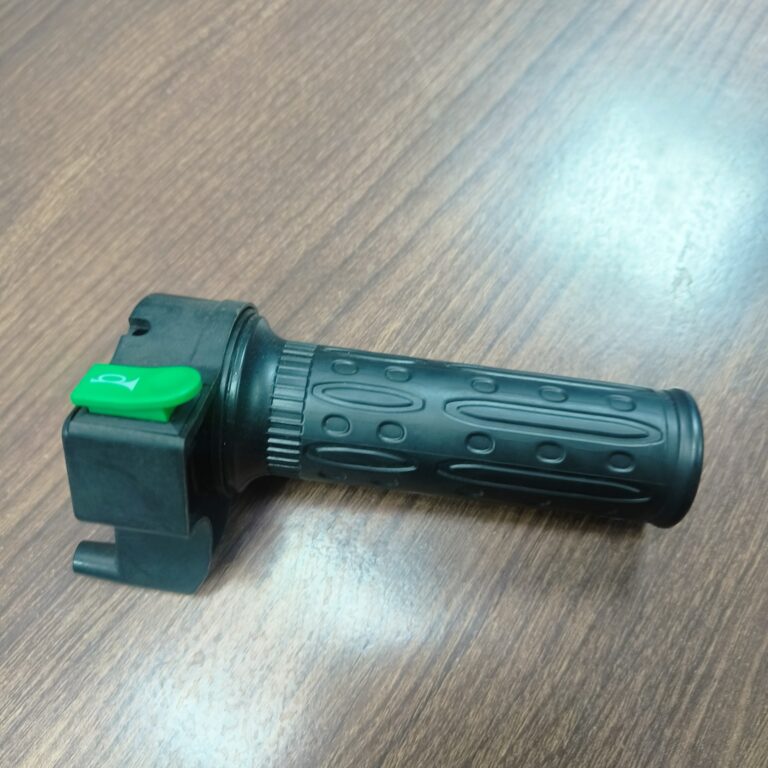
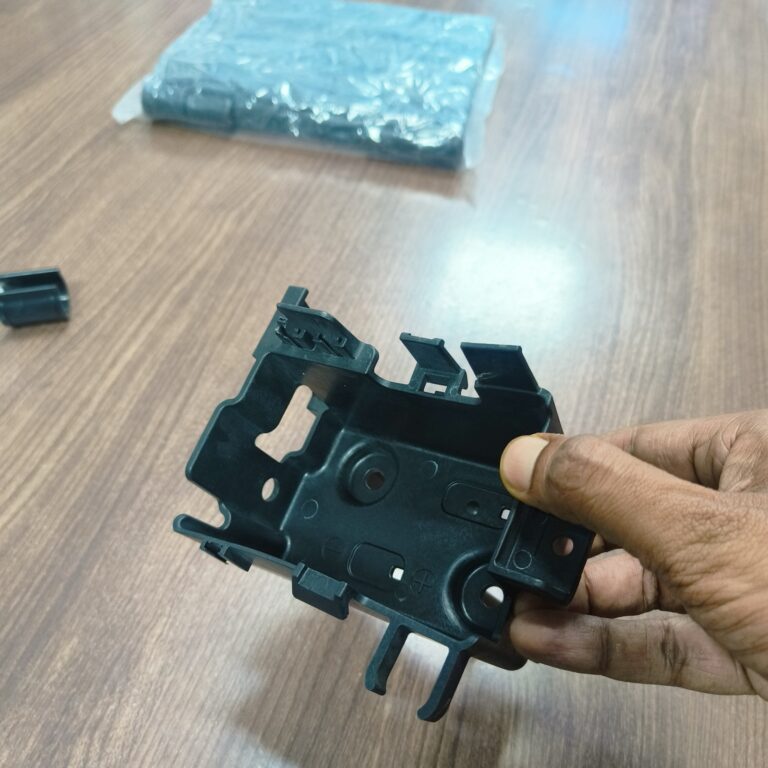
Heavy Fabrication
24000 MT/a
Materials
CS / MS, Alloy steel, Stainless Steel, etc.
Sheet Metal Fabrication
0.8 to 25 mm
Materials
Mild Steel, Stainless Steel, Aluminum, Brass, Copper, etc.


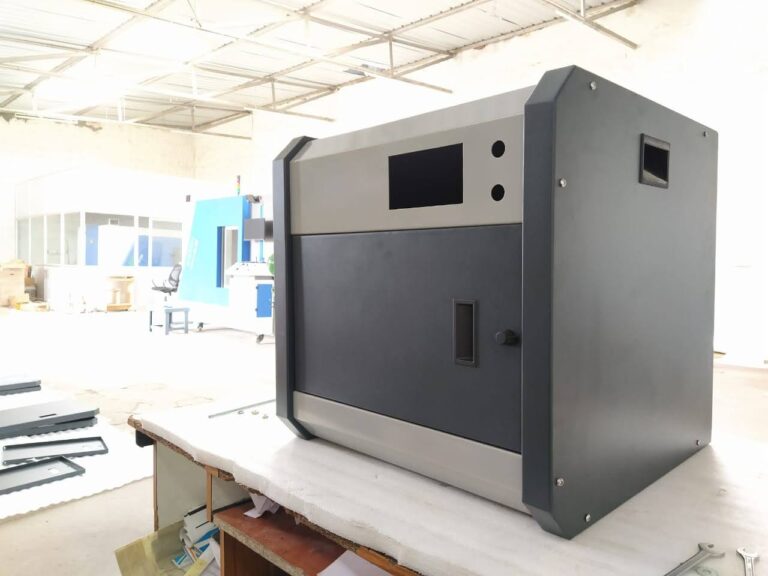


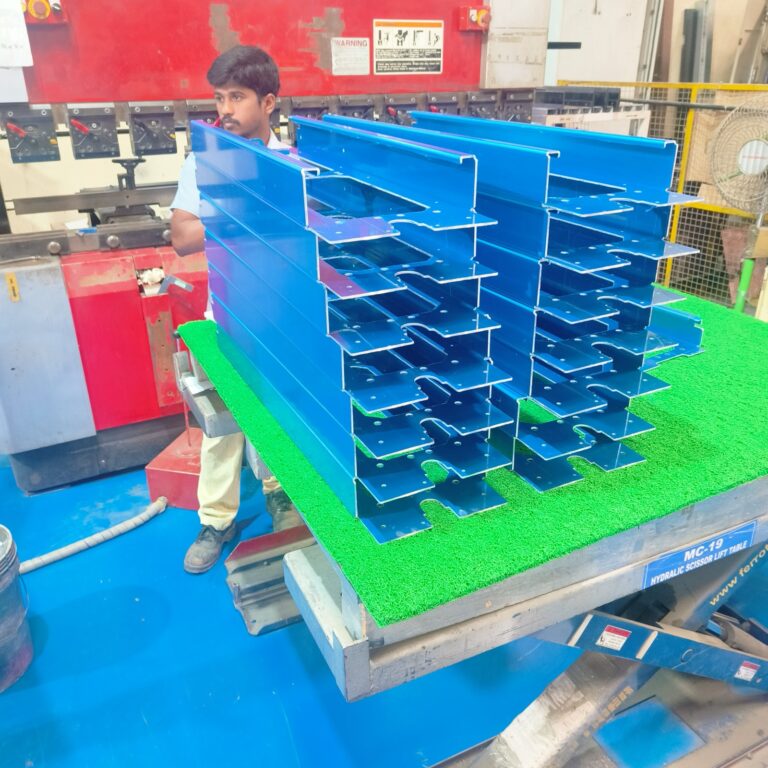
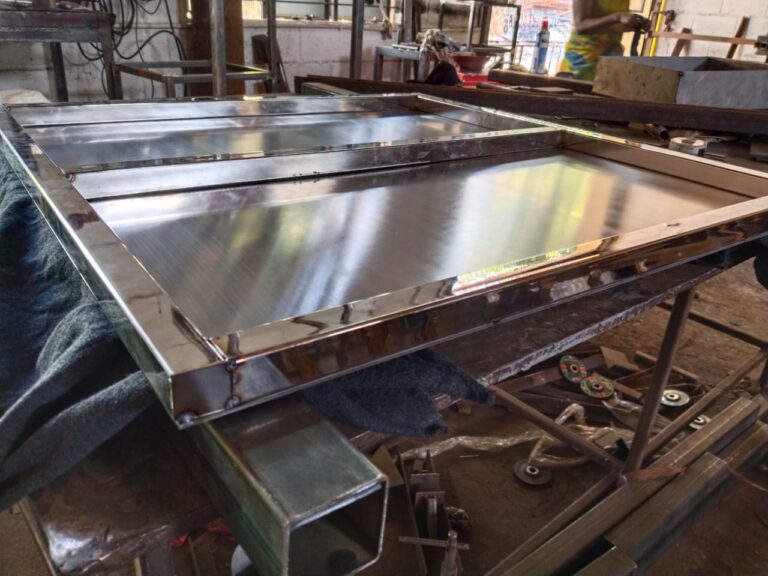
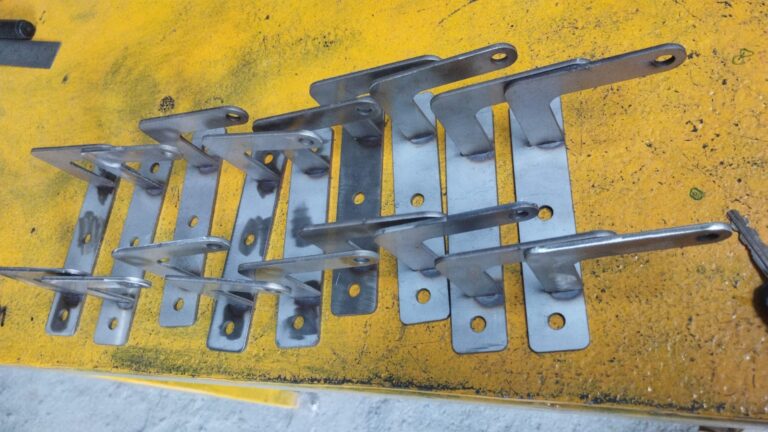
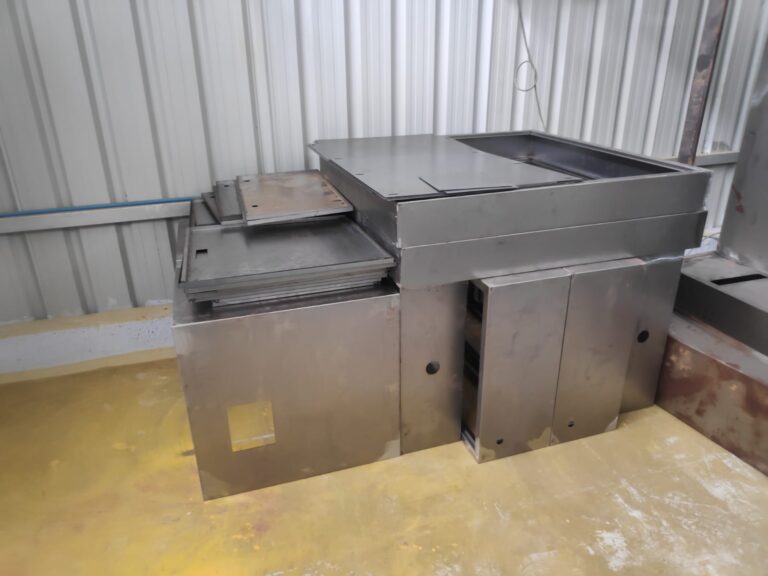
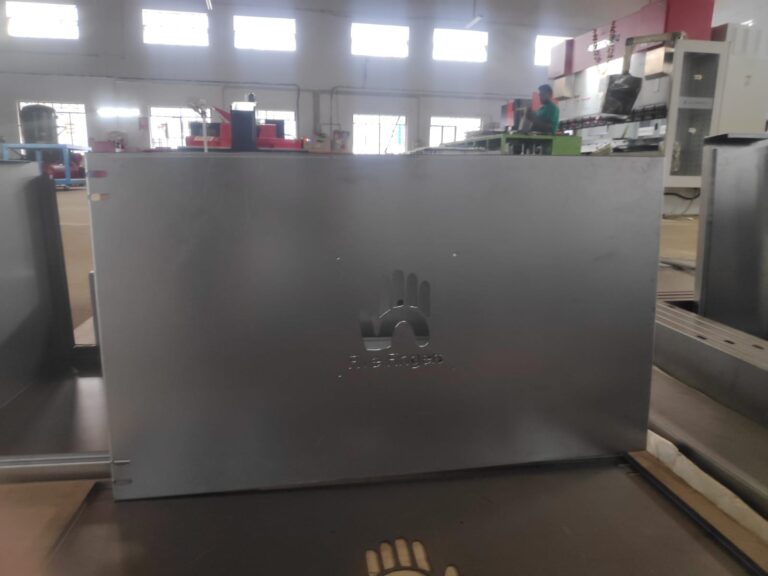
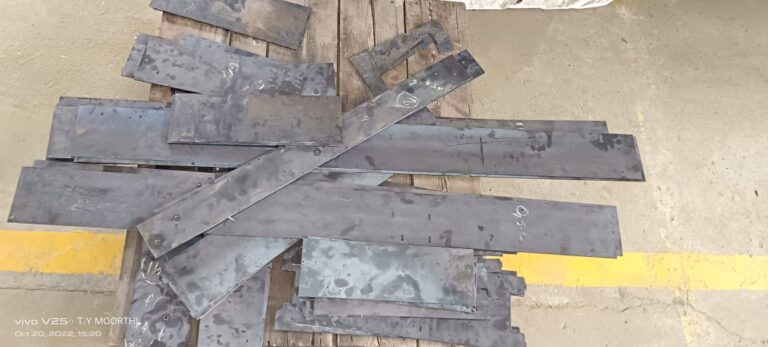
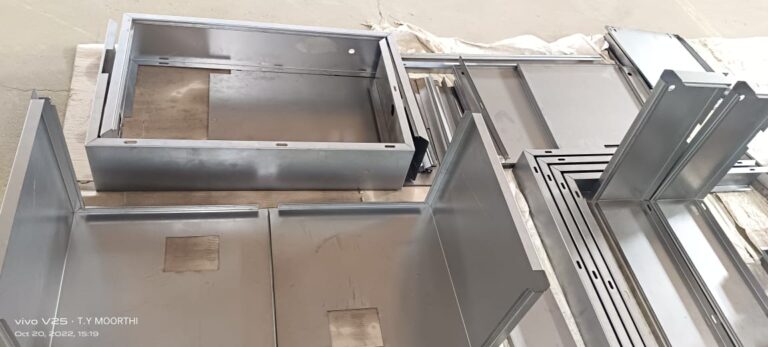
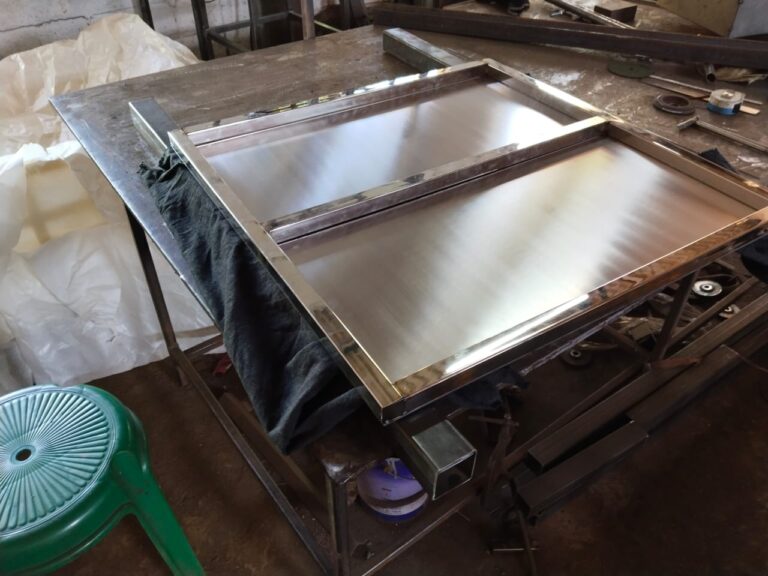
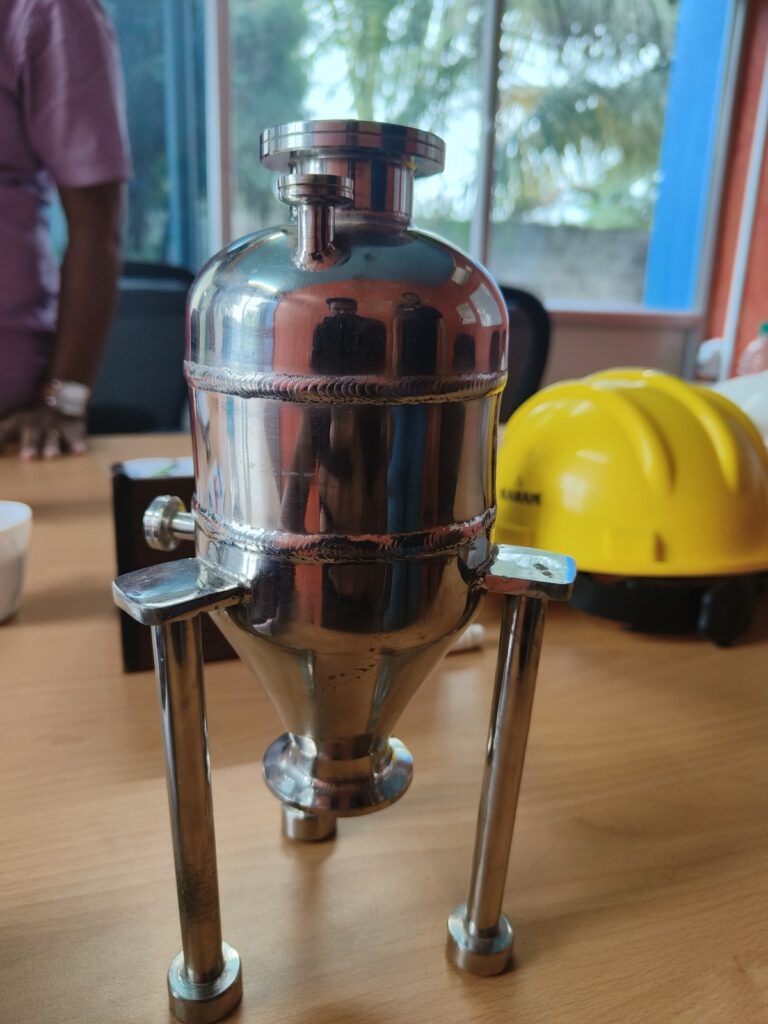
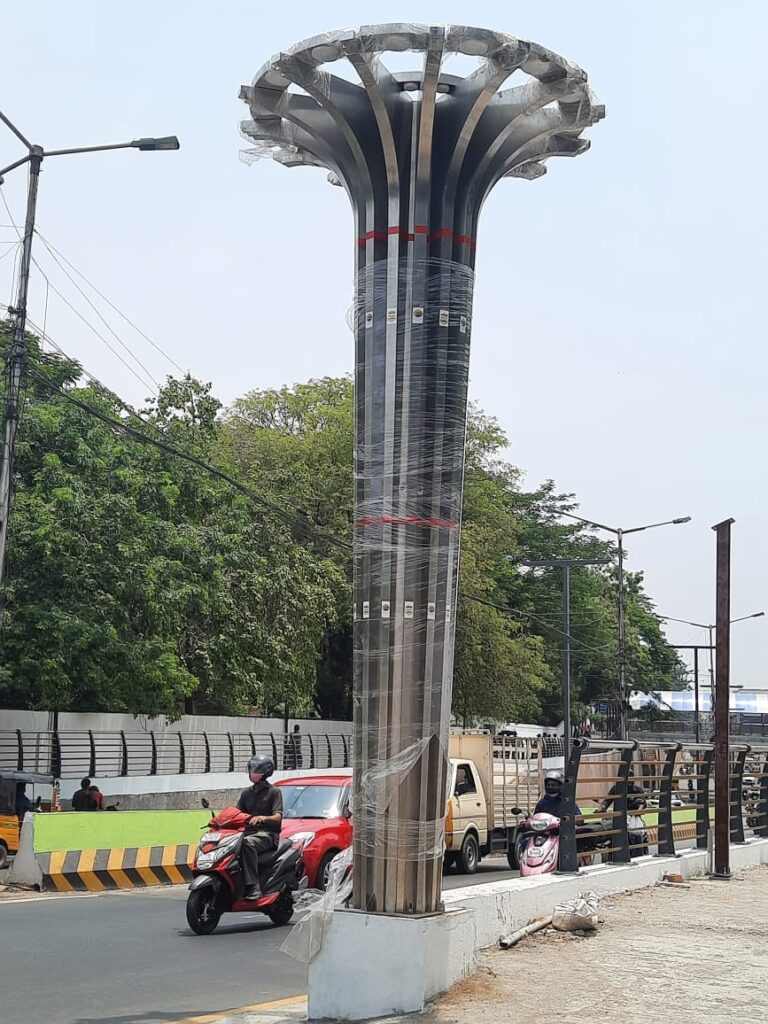
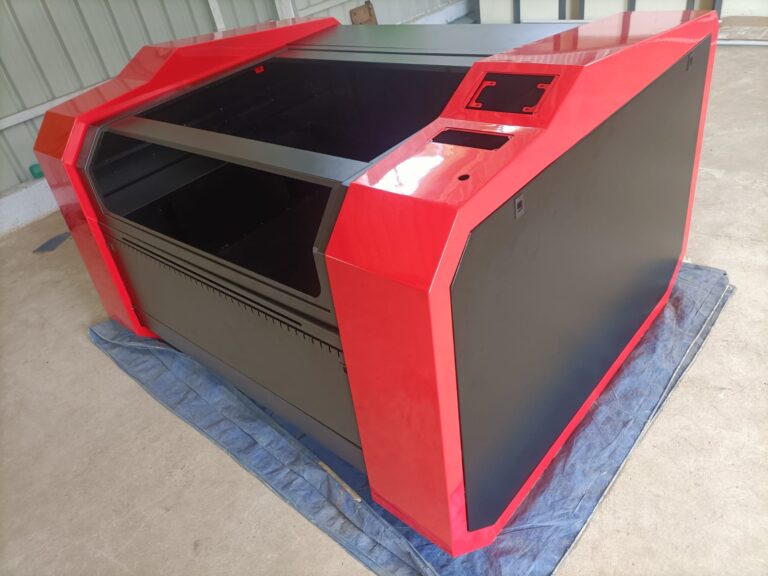
We'd love to Manufacture for you!
Submit the form below and our representative will be in touch shortly.
LOCATIONS
Registered Office
10-A, First Floor, V.V Complex, Prakash Nagar, Thiruverumbur, Trichy-620013, Tamil Nadu, India.
Operations Office
9/1, Poonthottam Nagar, Ramanandha Nagar, Saravanampatti, Coimbatore-641035, Tamil Nadu, India. ㅤ
Other Locations
- Bhilai
- Chennai
- Texas, USA