As industries strive to meet tighter product development timelines, a significant challenge arises – balancing the demands for speed with the essential need for quality. In manufacturing, especially in sectors like automotive, aerospace, and electronics, there is a constant push to accelerate production cycles while maintaining strict quality controls. The core issue buyers and sellers face is the tension between delivering quickly and ensuring Quick Turn Molding Quality.
This blog explores high-level technical strategies that can mitigate the inherent risks associated with tight timelines and rapid production schedules, ensuring quality is not compromised. It delves into advanced production techniques, materials, and process controls that help achieve quick turnaround times without sacrificing quality in molding processes.
The Impact of Tight Deadlines on Manufacturing Operations
In a fast-paced production environment, manufacturers are often forced to balance the competing demands of speed and quality. With shorter deadlines, the pressure to speed up production processes can result in unforeseen challenges. These tight deadlines ripple throughout manufacturing operations, affecting everything from tooling design to material choice and product quality. Manufacturers face significant risks, including production bottlenecks, compromised part accuracy, and quality degradation, which can delay timelines even further.
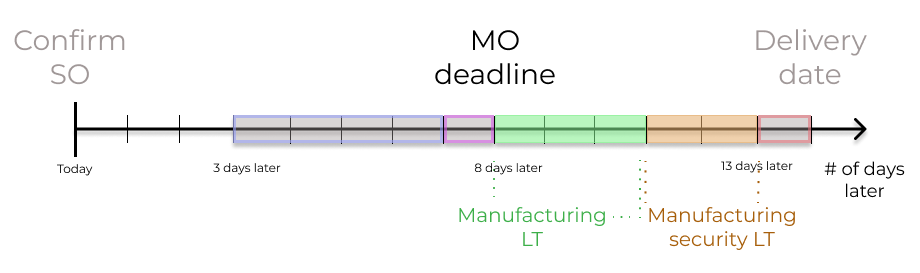
Speed vs. Quality – The Critical Trade-off
Manufacturers are often caught between the need to meet compressed schedules and the pressure to deliver defect-free, high-quality products. The risk of sacrificing quality for speed becomes increasingly prominent when –
- Production Bottlenecks – In a high-pressure environment, the continuous rush to meet deadlines often results in underperforming equipment or improperly maintained machinery, causing potential defects in molded parts.
- Design-Change Management – Iterative design changes are common in rapid-turnaround environments. However, adapting quickly without compromising the integrity of molds requires robust processes and tools to handle these revisions without introducing errors.
Industries like automotive and electronics demand high precision, especially when parts are responsible for complex systems like airbag modules or critical electronic components. A shift in focus towards “Quick Turn Molding Quality” is imperative to keep up with production schedules while ensuring consistent quality in every part produced.
Cost Implications of Compromised Quality
In fast-paced manufacturing settings, errors in molding can lead to –
- Increased scrap rates – Mistakes result in wasted raw materials, leading to increased production costs and inefficiencies.
- Extended Lead Times – Rework and error correction take additional time, disrupting delivery timelines.
- Damage to Reputation – Failed product quality, especially in industries like medical devices and automotive, can lead to significant reputational damage and costly recalls.
Minimizing defects and maximizing production efficiency through optimized processes is key to ensuring that Quick Turn Molding Quality remains uncompromised.
The Critical Role of Quick Turn Molding in Accelerated Production
Quick-turn molding plays a critical role in meeting the demands of industries that operate under strict time constraints. The ability to rapidly produce high-quality parts allows manufacturers to stay competitive in fast-evolving markets. However, speed should not come at the expense of precision, which is why achieving Quick-Turn Molding Quality requires a sophisticated approach.
Leveraging Advanced Mold Design for Speed and Accuracy
In quick-turn molding, precision tooling and mold design are crucial for ensuring rapid production and high-quality output. Advanced CAD and CAM (Computer-Aided Manufacturing) systems can optimize the mold design process, ensuring that parts are produced with exact tolerances and minimal lead time.
- Tooling Design Considerations – Efficient mold designs must account for material flow, cooling efficiency, and part ejection systems. Properly designed molds minimize cycle times, reduce wear, and improve part consistency.
- Rapid Tooling Technologies – Techniques such as additive manufacturing and rapid prototyping allow for quicker production of mold tools. These technologies reduce the time spent on traditional tooling methods and ensure faster turnaround without compromising Quick Turn Molding Quality.
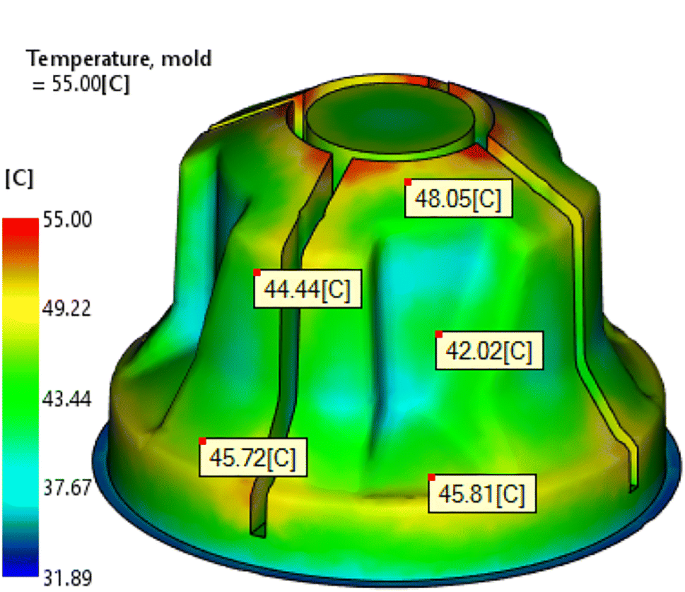
Simulation-Driven Production for High Accuracy
Simulation tools, such as mold flow analysis, simulate material flow and thermal cycles within the mold. This process helps identify potential issues such as uneven filling, air traps, and hot spots before production begins, enhancing quality control.
- Filling Simulation – Advanced simulations predict how materials flow into the mold, ensuring that parts are filled evenly and meet dimensional specifications.
- Thermal Management Simulation – Heat distribution during molding plays a key role in controlling part defects. Simulating the cooling process helps optimize cycle times while ensuring uniform cooling, thus preserving Quick Turn Molding Quality.
Prototype to Production Seamlessness
Quick-turn molding enables a rapid transition from prototype to full-scale production. This requires molding materials and design flexibility, allowing manufacturers to meet tight deadlines while adhering to quality expectations. By using tools such as multi-cavity molds and accelerated curing processes, manufacturers can ensure the part is produced quickly and meets all mechanical and aesthetic specifications required for high-performance products.
Key Technical Strategies for Ensuring High-Quality Production Under Tight Deadlines
For manufacturers delivering within compressed timelines, having a set of technical strategies is essential to achieving both speed and Quick Turn Molding Quality. These strategies must optimize every aspect of the production process, from material selection to automation and real-time monitoring.
Material Science Innovation for Quick Turn Molding
Choosing the right material is crucial when performing quick-turn molding while maintaining high-quality results. Advanced material science has led to the development of high-performance polymers and composites that provide the necessary strength and durability while enabling faster molding cycles.
- High-Performance Polymers – Materials such as PEEK (Polyether ether ketone) or PEI (Polyetherimide) offer excellent strength-to-weight ratios and thermal stability, making them ideal for rapid molding processes without sacrificing performance.
- Lightweight Alloys for High Durability – In applications where weight and strength are crucial, such as automotive and aerospace, lightweight alloys like magnesium, aluminum, and titanium are used. These materials facilitate faster cooling times and reduced cycle times while maintaining Quick-Turn Molding Quality.
Material selection directly impacts the part’s mechanical properties and surface finish, essential for ensuring that the final product meets specifications.
High-Precision Tooling and CAD Integration
Integrating CAD with CAM and CAE (Computer-Aided Engineering) ensures precise tooling and mold designs, which lead to better parts and faster production cycles. High-precision tooling ensures that the molds will replicate exact features without frequent reworking.
- Tooling Tolerances – For quick-turn molding, the tooling must maintain tight tolerances to prevent dimensional deviations, which could compromise part fit and function.
- Automated Process Controls – Integrating automated process controls, such as real-time temperature monitoring and automated cycle adjustments, allows manufacturers to monitor molding conditions continuously and adjust them dynamically to optimize Quick Turn Molding Quality.
Optimizing Cycle Times with Automation
Automation in injection molding helps achieve faster cycle times without compromising quality. High-speed robots and automated material handling systems work seamlessly to reduce manual intervention, speeding up the entire molding process.
- Robotic Molding Systems – Robots can handle parts during cooling and ejection, significantly reducing cycle times and improving precision.
- Automated Quality Inspections – Inline inspection systems using machine vision and laser measurement technology ensure that every part is checked for dimensional accuracy. This ensures Quick Turn Molding Quality throughout the production process.
The ability to perform high-quality production with reduced labor requirements correlates with maintaining quick turnaround times while preserving part quality.
Mitigating Risks in Quick Turn Molding
The pressure to meet tight deadlines can introduce numerous risks in quick turn molding. However, these risks can be mitigated by adopting a proactive process control, quality assurance, and supply chain management approach.
Tolerance Management and Quality Assurance Protocols
Maintaining strict tolerances is essential in high-quality molding, especially when quick production is necessary. Effective tolerance management ensures that parts meet precise specifications without costly rework or rejection. This requires robust quality assurance protocols and in-line measurement systems.
- Closed-Loop Feedback Systems – Automated feedback from measurement systems to molding machines allows for real-time adjustments during the molding process. If a part deviates from the desired tolerance, corrective actions can be taken immediately to maintain quality.
- Statistical Process Control (SPC) – Implementing SPC ensures consistent quality by monitoring and controlling the molding process using real-time data analytics. This helps ensure all parts are produced within tight tolerances and meet performance expectations.
By integrating tolerance management and quality assurance, manufacturers ensure that Quick Turn Molding Quality remains consistent, even under pressure to meet deadlines.
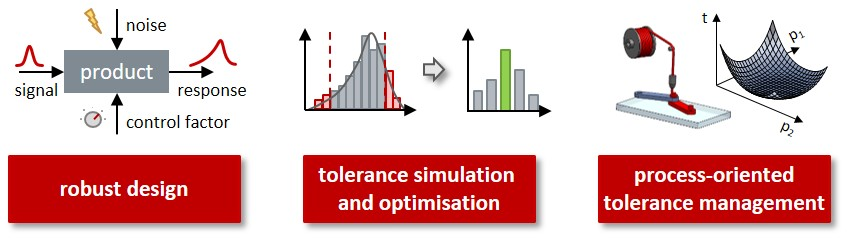
Supply Chain Synergies and Lean Manufacturing
The efficiency of the supply chain directly impacts the speed and quality of production. A lean approach to manufacturing ensures that resources are used effectively without overburdening the system. Lean practices minimize waste, streamline processes, and ensure that parts are delivered on time.
- Supplier Integration – Working closely with material suppliers ensures that raw materials are delivered on time, allowing for uninterrupted production schedules.
- Optimized Workflow – By using tools like value stream mapping, manufacturers can identify bottlenecks and optimize workflows, improving the overall speed and efficiency of the molding process without sacrificing quality.
Lean manufacturing principles help optimize both speed and quality in quick turn molding.
Best Practices for Scaling Quick Turn Molding Operations Without Sacrificing Quality
To scale quick-turn molding operations while maintaining quality, manufacturers must implement efficient workflows, adopt advanced technologies, and foster collaboration across teams. Scaling without compromising Quick-Turn Molding Quality requires a careful approach to production processes and resource allocation.
Collaborative Design-to-Production Workflow
Collaboration between design, engineering, and production teams is key to ensuring that designs are feasible for quick-turn molding without sacrificing quality. Early involvement of production teams in the design process allows for better manufacturability, reduced rework, and improved production efficiency.
- Design for Manufacturability (DFM) – This principle focuses on designing parts that are easy to mold and assemble, reducing the chances of issues during the molding process and ensuring Quick Turn Molding Quality.
- Early Prototyping and Iteration – Rapid prototyping and testing help identify potential issues early in the process, allowing for quick iterations before full-scale production begins.
Smart Automation to Scale Production
Automation plays a crucial role in scaling production for quick-turn molding. The more a system can be automated, the faster parts can be produced while maintaining precision and quality. Automated systems also help manage the growing complexities of larger production runs, ensuring consistency in quality.
- Flexible Molding Systems – Modular molding machines that can quickly adapt to different parts and configurations allow manufacturers to scale up production without investing in entirely new tooling for each part.
- Automated Quality Control – Automated inspection systems help scale operations by ensuring every part meets quality standards before it leaves the facility.
Efficient Supply Chain Management
As production scales, managing materials, suppliers, and logistics becomes more complex. An efficient supply chain helps ensure that materials are delivered quickly, parts are produced on time, and customers receive their products as promised.
- Just-In-Time Delivery – By coordinating with suppliers and using real-time tracking systems, manufacturers can ensure that materials arrive precisely when needed, reducing inventory costs and maintaining production schedules.
- Strategic Partnerships – Building strong relationships with reliable suppliers and logistics partners helps mitigate risks and improve scalability without compromising Quick Turn Molding Quality.
Delivering Quality at Speed with Frigate’s Quick Turn Molding
At Frigate, we understand the challenges of balancing quick production timelines with the need for high-quality molded parts. Our team combines years of expertise with cutting-edge technology and world-class manufacturing practices to deliver Quick Turn Molding Quality with every part.
Precision Mold Manufacturing with Advanced Materials
- Precision Tooling – Frigate utilizes precision CNC and wire EDM (Electrical Discharge Machining) techniques to create molds with extremely tight tolerances. This ensures that each mold maintains consistent dimensional accuracy across high-volume runs, even with rapid production schedules.
- Advanced Mold Materials – We select specialized materials such as H13 tool steel, which provides excellent heat resistance and durability for quick-turn processes. This ensures molds withstand rapid cycles without degradation or failure.
Rapid Prototyping and Injection Molding Integration
- Rapid Prototyping for Design Validation – We use SLA (Stereolithography) and SLS (Selective Laser Sintering) 3D printing for rapid prototyping to validate part designs before committing to full-scale production. This allows for quick feedback and iterations, reducing lead times for the production of functional prototypes.
- In-Mold Automation – Besides basic automation, we integrate in-mold sensors to optimize part quality during production. These sensors can monitor pressure, temperature, and fill speed, adjusting mold conditions in real time to ensure uniform part quality with minimal waste.
Advanced Injection Molding Machines with High-Speed Capabilities
- High-Speed Injection Systems – Frigate uses injection molding machines with high-speed injection systems designed to inject molten material into molds at controlled speeds, ensuring even filling and minimizing cycle times. These systems provide excellent consistency and fast cycle times, even for intricate designs.
- Multi-Cavity Mold Design – To improve production throughput and minimize per-part cost, Frigate employs multi-cavity mold designs, enabling the production of several parts simultaneously in each mold cycle. This allows for efficient scaling of production while maintaining consistent part quality.
Comprehensive Process Control and Optimization
- Automated Cycle Time Optimization – By utilizing advanced software solutions that track and adjust cycle times in real time, we can optimize injection molding parameters dynamically, ensuring consistent part quality and minimizing cycle time, all while meeting tight deadlines.
- Temperature and Pressure Control – Temperature control units and specialized cooling systems are integrated into our molding processes to maintain optimal mold temperatures and pressure settings, reducing cycle time and minimizing part distortion. This process control enhances the consistency and precision of each molded part.
End-to-End Process Integration
- Closed-Loop Manufacturing – Frigate utilizes a closed-loop feedback system for manufacturing, integrating machine sensors with central control systems. This allows us to make real-time adjustments to machine settings, improving efficiency and quality with every cycle.
- Lean Manufacturing with Continuous Improvement – We adopt lean manufacturing principles and continuously monitor key performance metrics to identify and eliminate inefficiencies in production. This process allows us to maintain quick turnaround times while ensuring parts are produced with the highest quality standards.
High-Performance Quality Assurance
- Automated Inline Quality Checks – Our fully automated inspection systems conduct quality checks at every production stage, using technologies such as machine vision, laser scanning, and automated dimensional measurement systems. These systems detect any part defects or deviations before the parts leave the production floor.
- Material Traceability – Each batch of materials used in production is tracked using a real-time material traceability system. This ensures full traceability and quality control, enabling us to quickly identify and resolve any issues related to material defects or inconsistencies.
Conclusion
Ensuring Quick Turn Molding Quality under tight deadlines requires a holistic approach, encompassing everything from material selection to advanced tooling and automation. By implementing the right technical strategies and best practices, manufacturers can successfully meet the demands of accelerated production schedules without compromising on quality.
Contact Frigate today if you’re looking for a reliable partner that combines speed, quality, and innovation in quick-turn molding. Our technical expertise and commitment to excellence will help you stay ahead in a fast-paced market, ensuring your parts are delivered on time and to the highest standards.