If you’re in manufacturing, you’ve probably faced the challenge of managing production costs. One major pain point for many is understanding injection molding costs. With so many factors at play, it can feel overwhelming. Is it the material, the mold, or maybe the size of the production run that drives up prices? Without a clear breakdown, you risk overpaying or getting hit with surprise costs later. This guide will explain the key elements that affect injection molding costs and how to manage them. By knowing these details, you’ll be better equipped to plan your budget and avoid unnecessary expenses.
Key Factors That Influence Injection Molding Costs
Now that we’ve identified the importance of understanding injection molding costs, let’s dive into the specific factors that determine these expenses. From material selection to production methods, several elements shape the overall cost. By breaking down these components, you’ll get a clearer picture of where your money is going and how to optimize your process for maximum efficiency.
Material Selection and Its Cost Implications
The first thing that affects injection molding costs is the material you choose. Different plastics have different prices. For example, standard materials like ABS or Polypropylene are cheaper than specialized ones like Nylon or thermoplastics with high heat resistance.
The choice of material isn’t just about the cost per kilogram. Some materials are easier to mold, which lowers production costs. Others may need more energy or longer cycle times, making them pricier.
Additives, like colorants or UV stabilizers, also raise material costs. Choosing the right material for your product is crucial, as it directly affects upfront and long-term expenses. Raw plastic materials typically account for about 30% of the overall injection molding costs.
Tooling Costs: The Largest Initial Investment
The tooling or mold creation cost is the most significant expense in injection molding. This upfront cost can range from a few thousand to hundreds of thousands of dollars, depending on the part’s complexity. Steel molds are expensive but last longer, making them ideal for high-volume production. On the other hand, aluminum molds are cheaper but wear out faster, so they’re better for smaller production runs.
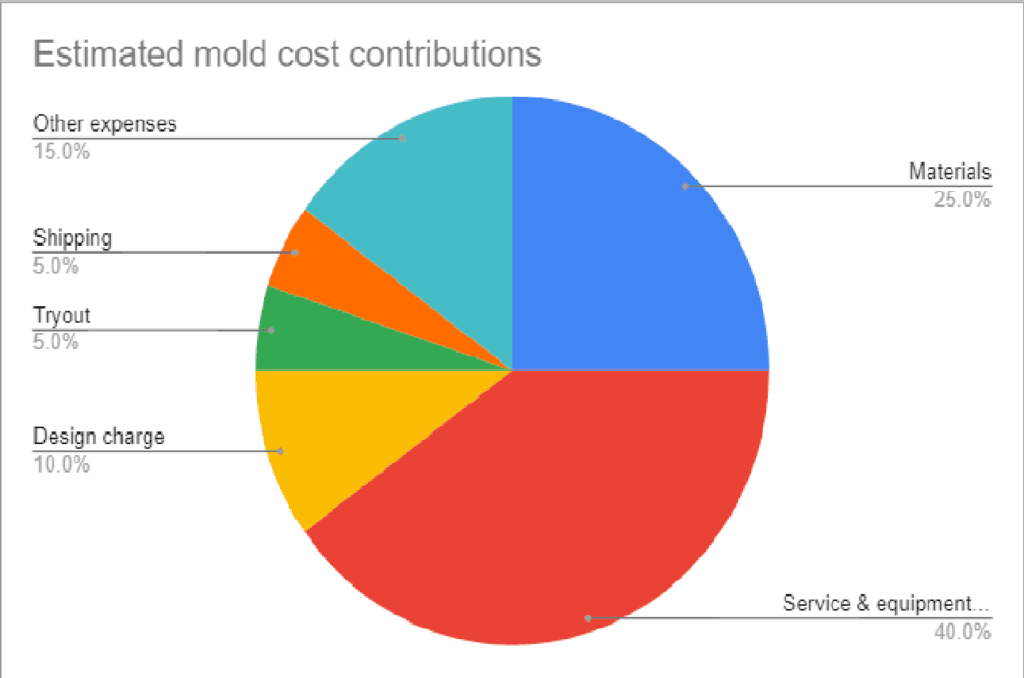
The mold’s design is also a huge factor. Complex designs with intricate details will require more expensive molds. However, investing in a high-quality mold can save money in the long run since it will last longer and reduce defects. A high-quality steel mold can last over 1 million cycles, spreading the cost over a longer period than cheaper molds.
Production Run Size and Economies of Scale
One key driver of injection molding costs is the size of your production run. The more units you produce, the lower your cost per part becomes. This is because fixed costs, like tooling and setup, are spread across more pieces. So, a small production run might have a higher cost per part than a larger one.
Economies of scale play a big role here. If you plan to produce thousands or millions of units, investing in a higher-quality mold and bulk material purchases will drive down your costs. Small runs, however, don’t have the same advantage, which can significantly increase the per-part price.
Cycle Time and Its Effect on Operational Costs
Cycle time refers to how long it takes to make one part from start to finish in the injection molding process. Shorter cycle times mean you can produce more parts in less time, which lowers your injection molding cost. However, complex parts or designs with thick walls will increase the cycle time and cost.
Minimizing cycle time is critical to controlling costs. Simple designs, thin-walled parts, and efficient cooling systems can all help reduce cycle time. Automated machines can also speed up the process, ensuring high production rates. A cycle time of 30 seconds versus 50 seconds can make a 40% difference in cost efficiency.
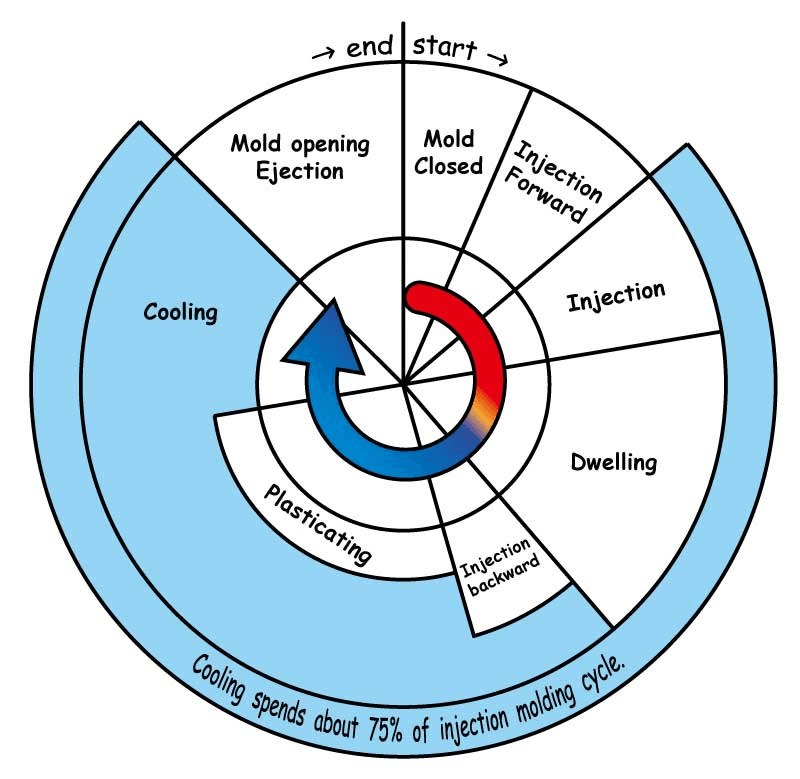
Labor and Machine Costs: The Hidden Factors
Labor and machine time are hidden costs that can sneak up on you. Injection molding machines vary in price based on size, tonnage, and complexity. Larger machines for bigger parts or more complex designs come with higher operational costs. These machines also consume more energy, which adds to your overall expense.
Additionally, manual labor for setup, mold maintenance, and part finishing contributes to costs. Automating the process can reduce labor expenses, often requiring a higher initial investment in advanced machinery. Ensuring that machines are properly maintained is essential for reducing downtime, which can significantly affect your budget. Labor and machine costs typically account for around 20% of total injection molding costs.
Secondary Processes and Their Additional Costs
Secondary processes, like painting, assembly, or ultrasonic welding, are often necessary to complete your part. However, these steps add extra costs to the overall project. If your part requires a post-molding process, it’s essential to account for the time, labor, and materials that will increase the overall injection molding costs.
For instance, a painted finish or heat treatment might require aesthetics or durability, but these steps increase per-unit expenses. Evaluating which secondary processes are essential and whether they align with your budget is important.
Shipping and Logistics: The Overlooked Expenses
Often overlooked, shipping and logistics can also contribute to the overall injection molding costs. The size of your part and where it’s manufactured can dramatically affect shipping rates. Large, bulky parts will cost more to ship, especially if produced overseas. Packaging is another consideration, as delicate parts may require custom packaging, increasing packaging and shipping costs.
Additionally, you must factor in warehousing costs if parts are stored in a warehouse before shipping. Efficient logistics management, such as shipping directly from the manufacturer to the customer, can help reduce these expenses.
Cost Optimization Strategies for Injection Molding
There are several strategies to optimize and reduce injection molding costs. First, focusing on part design is critical. By simplifying the design, you can reduce material usage and cycle time. Mold flow analysis tools can also help detect potential issues before production, preventing costly errors.
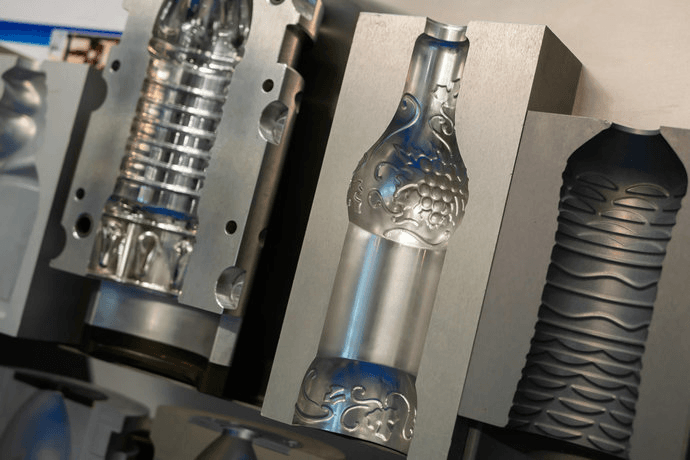
Material selection is another area where savings can be made. When possible, recycled materials or cheaper alternatives can significantly reduce material costs. Working with an experienced mold maker can also lead to savings. They can help design molds that last longer, require less maintenance, and produce fewer defective parts, reducing overall expenses.
Conclusion
Injection molding costs are influenced by multiple factors, including material selection, tooling, production run size, cycle time, labor, and secondary processes. By understanding these elements, manufacturers can better plan their budgets and avoid unexpected expenses. Simple design choices, efficient production planning, and smart material usage can all help bring down costs and improve profitability.
If you’re looking to optimize your injection molding process or need expert advice on cost management, Frigate can help. Contact us today to discuss your project and learn how we can deliver high-quality, cost-effective solutions tailored to your needs.