Robust Manufacturing Solutions for the Oil & Gas Industry
Enhance Upstream and Downstream Operations with Corrosion-Resistant Alloys and Scalable CNC-Machined Solutions for Demanding Environments
Frigate platform is designed to revolutionize your supply chain
Precision Tolerance Control
Utilize multi-axis CNC machining and CMM inspection to achieve ±0.001" tolerances for critical components under high-pressure operating conditions.
Sour Service Materials
Apply NACE-compliant alloys and controlled machining practices to prevent sulfide stress cracking in H₂S-rich, sour gas service environments.
Complex Geometry Manufacturing
Employ 5-axis machining, EDM, and CAM integration to produce intricate geometries for multiphase and subsea flow control components.
Our Clients
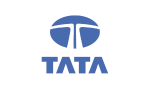
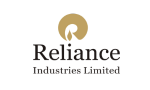


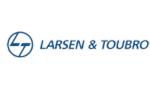
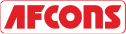


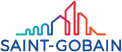

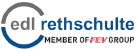

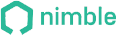
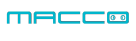









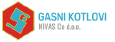
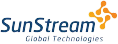

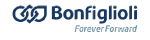


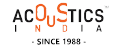
Ensure Thermal Stability in HPHT Conditions
Maintaining material integrity under fluctuating thermal loads is critical for oil and gas components in downhole, topside, and subsea environments.
Solution annealing, normalizing, and quenching processes are applied using tightly regulated temperature profiles to refine grain structure and improve uniformity in mechanical properties.
Thermal treatments are tailored to eliminate residual stresses from machining or welding operations, particularly in components with variable wall thickness or high-stress concentration areas.
Thermal stabilization increases resistance to long-term deformation and fatigue cracking, especially in nickel-based alloys and duplex stainless steels subjected to cyclic HPHT exposure.

Validate Integrity with Advanced NDT Techniques
Assuring internal and surface integrity without altering part performance is essential for mission-critical components deployed in hazardous or inaccessible environments.
Phased Array UT and Digital Radiographic Testing enable the detection of embedded flaws, porosity, and delaminations in welds, castings, and forgings with high resolution.
All testing procedures conform to ASME Section V, API 1104, and ISO 9712 standards, ensuring global compliance and repeatability in qualification results.
Inspection data is digitally stored and traceable, offering complete audit trails for pressure boundaries, rotating parts, and other safety-critical components.

Extend Service Life with Weld Overlay and Cladding
Extending service life in corrosive and erosive applications requires metallurgical enhancements beyond base material capability, particularly for pressure-retaining and flow-control equipment.
Hot-wire GTAW, SAW, and plasma transferred arc (PTA) process ensure consistent deposition of corrosion-resistant alloys over critical surfaces with low dilution and high bond strength.
CRA cladding using Inconel, Monel, or 316L stainless steel enables compatibility with aggressive media such as CO₂, H₂S, and seawater, particularly in sour and subsea environments.
Final heat treatments and CNC finishing operations are applied post-cladding to restore mechanical properties, eliminate hardness gradients, and ensure dimensional conformance.
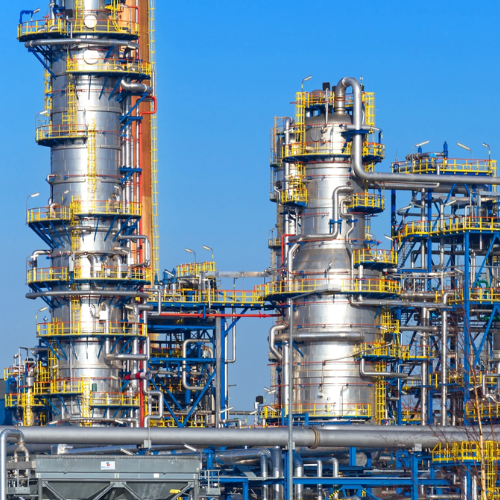
Our Oil & Gas Products
100,000+
Parts Manufactured
250+
Frigaters
2000+
Machines
450+
Materials
25+
Manufacturing Process
Industries We Also Serve
Having Doubts? Our FAQ
Check all our Frequently Asked Question
Yes. Frigate uses marine-grade stainless steel and specially coated carbon steel. Anti-corrosive surface treatments like hot-dip galvanizing (per ASTM A123) or fluoropolymer coatings are applied. Salt spray testing and cyclic corrosion testing validate durability in saline and sand-loaded air environments.
Frigate applies thermal compensation models during extrusion to prevent distortion. Post-processing includes CNC straightening and laser-guided dimensional inspection. Aluminum profiles are machined under tightly controlled clamp setups to avoid deflection and maintain ±0.2 mm flatness over 3–5 meter lengths.
Frigate uses robotic MIG and TIG welding systems with real-time arc monitoring. Welds are validated using ultrasonic and dye-penetrant testing. Fatigue testing is performed on joint samples following IEC 62817 tracker durability protocols to ensure 25+ years of structural performance.
Yes. Frigate maintains full part traceability with digital records of material certs, mechanical tests, and inspection reports. Manufacturing follows ISO 9001, and critical parts are produced to comply with standards like UL 2703 (mounting systems) and IEC 61215 (mechanical load compliance for PV modules).
Frigate performs FEA-based thermal expansion analysis for aluminum-steel or steel-copper joints. Insulating spacers and anodized coatings are used to prevent galvanic corrosion. Joint designs are evaluated with finite element modeling to reduce stress concentration and material migration under thermal cycling.
- Real Impact
Words from Clients
See how global OEMs and sourcing heads describe their experience with our scalable execution.
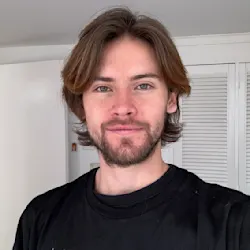
“Quick turnaround and solid quality.”
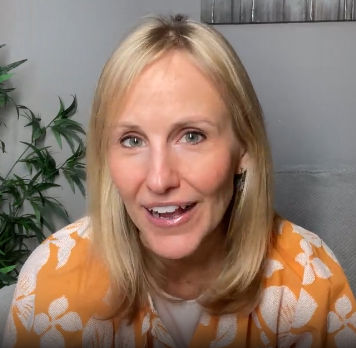
“The instant quote tool saved us time, and the parts were spot-on. Highly recommend Frigate!”
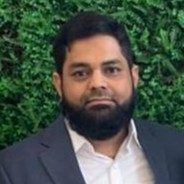
“I would strongly recommend Frigate to anyone who wants to do Rapid Prototyping, and take their ideas to manufacturing. One firm doing all kinds of Product Development!”
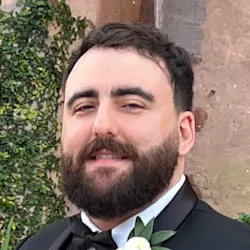
“Great service, fair price, and the parts worked perfectly in our assembly.”
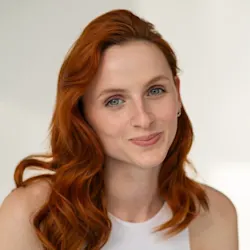
“Top-notch machining and fast shipping. Very satisfied with the results.”
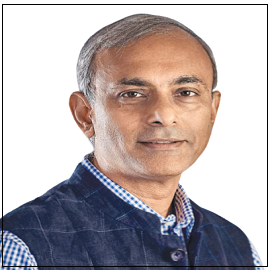
“The next disruption is happening in Prototyping & Manufacturing on-demand and Frigate is leading the way! I personally believe the Frigate's way of IIOT enabled cloud platform with Al.”
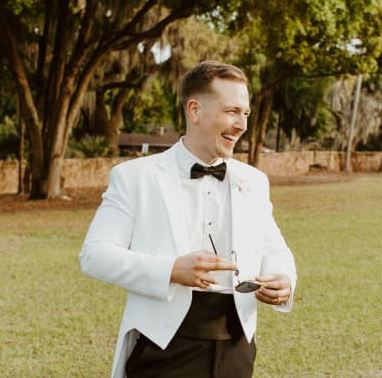
“Frigate delivered high-quality parts at a competitive price. The instant quote tool is a huge plus for us!”

“We appreciate the precision and quality of the machined components in the recent delivery—they meet our specifications perfectly and demonstrate Frigate’s capability for excellent workmanship.”
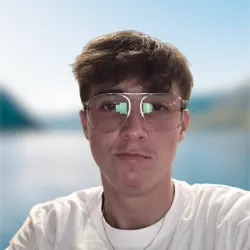
“Flawless execution from quote to delivery.”

“I am absolutely happy to work with supplier like Frigate who were quite proactive & result oriented . Frigate has high willingness team who has strong know how & their passion towards the products & process were absolutely thrilling.”
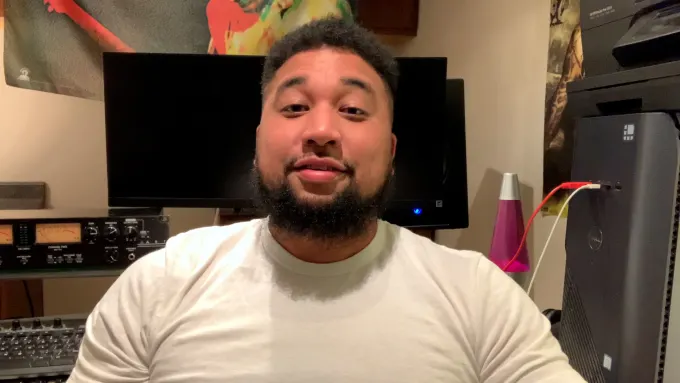
“The precision on these parts is impressive, and they arrived ahead of schedule. Frigate’s process really stands out!”
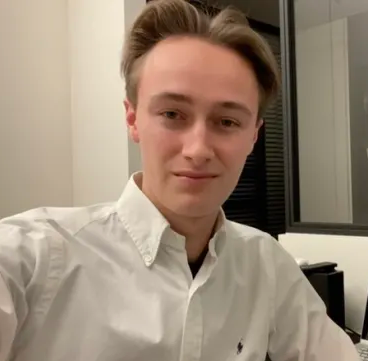
“Parts were exactly as spec’d, and the instant quote made budgeting a breeze.”
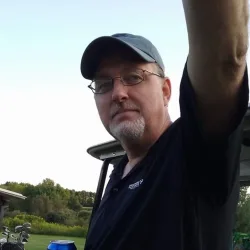
“Good value for the money.”
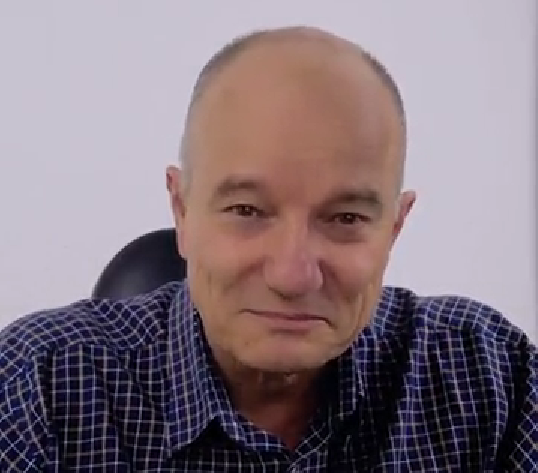
“The finish was perfect, and the team was easy to work with.”

“Working with Frigate has been great. Their proactive, results-driven approach and expertise shine through in every project. It's been a pleasure collaborating with them.”

"We are highly satisfied with the timely delivery and quality of the MIG Welding Cable from Frigate. Their attention to detail, secure packaging, and quick responsiveness stood out. We confidently recommend Frigate Engineering Services Pvt. Ltd. as a reliable manufacturing partner."
We'd love to Manufacture for you!
Submit the form below and our representative will be in touch shortly.
LOCATIONS
Registered Office
10-A, First Floor, V.V Complex, Prakash Nagar, Thiruverumbur, Trichy-620013, Tamil Nadu, India.
Operations Office
9/1, Poonthottam Nagar, Ramanandha Nagar, Saravanampatti, Coimbatore-641035, Tamil Nadu, India. ㅤ
Other Locations
- Bhilai
- Chennai
- USA
- Germany