Custom Manufacturing on Demand for the New Energy Industry
Optimize and Power New Energy Projects with Precision Manufacturing, Scalable Supply Solutions, and End-to-End Production Support.
Unlock New Energy Potential with On-Demand Manufacturing
Supply Chain Optimization
Optimized supply chains, digital tracking, and just-in-time manufacturing ensure timely delivery of energy components, minimizing delays.
Regulatory Compliance Assurance
Advanced quality control, precision testing, and regulatory documentation ensure components meet ASME, ISO, and ASTM standards for energy applications.
Cost-Effective Scalability
Automated production, lean manufacturing, and optimized material selection enhance scalability while reducing costs for specialized energy components.
Our Clients
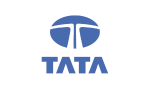
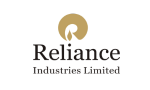


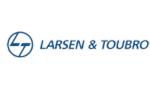
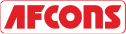


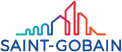

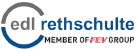

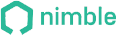
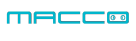









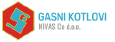
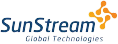

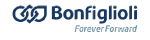


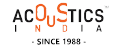
Advanced Manufacturing for Complex Components
Energy applications demand precision-engineered components with strict tolerances and intricate designs. Utilizing cutting-edge manufacturing technologies ensures durability, accuracy, and efficiency.
CNC, multi-axis milling, and advanced casting methods achieve intricate geometries while maintaining tight dimensional tolerances for critical energy components.
Real-time monitoring, laser scanning, and non-destructive testing (NDT) detect defects early, ensuring flawless production with minimal material waste.
Standardized workflows and process automation enhance repeatability, minimizing deviations and ensuring reliable performance across all manufactured components.

Scalable Production for High-Demand Projects
Large-scale energy infrastructure projects require flexible production capabilities to meet growing demand without delays or cost overruns. Scalable workflows optimize efficiency and delivery timelines.
Modular production lines and adaptable tooling allow quick adjustments to production volumes, reducing downtime between batch transitions.
Automated casting, forging, and assembly processes streamline production, reducing cycle times and minimizing resource consumption while maintaining precision.
Advanced batch processing and real-time scheduling optimize throughput, ensuring steady component availability for wind, solar, oil & gas, and nuclear applications.

Material Innovation for Enhanced Performance
Energy components operate in extreme conditions, requiring advanced materials and coatings to maximize lifespan, structural integrity, and efficiency.
Corrosion-resistant metals like stainless steel, titanium, and nickel alloys provide exceptional durability under high temperatures and pressure.
Thermal coatings, anodization, and anti-corrosive layers enhance wear resistance, preventing degradation in demanding environmental conditions.
Material selection is optimized for operational needs, ensuring components maintain strength, conductivity, and resistance against mechanical or chemical stressors.
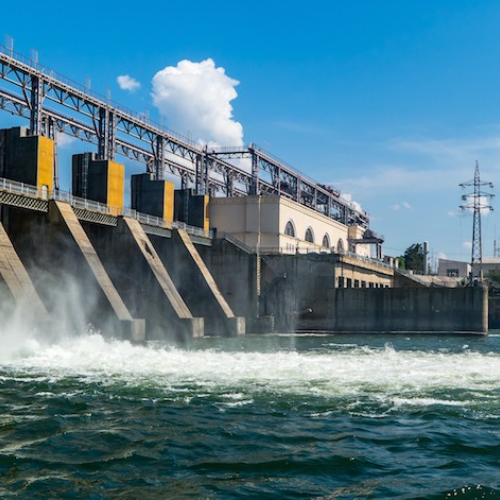
Our New Energy Products
100,000+
Parts Manufactured
250+
Frigaters
2000+
Machines
450+
Materials
25+
Manufacturing Process
Industries We Also Serve
Having Doubts? Our FAQ
Check all our Frequently Asked Question
Frigate utilizes advanced finite element analysis (FEA) to simulate wind loads, seismic activity, and mechanical stress on solar structures. High-strength materials like galvanized steel and aluminum alloys are selected for load-bearing capacity. Precision robotic welding and automated bolting systems enhance joint strength and long-term structural reliability.
Frigate employs precision extrusion, laser cutting, and CNC machining to achieve tight aluminum and composite panel frame tolerances. Automated anodization and powder coating processes enhance corrosion resistance, ensuring durability in extreme weather conditions. High-speed roll-forming technology enables rapid, scalable production without compromising frame precision.
Frigate utilizes high-purity copper and silver-plated aluminum for superior conductivity in solar panel interconnections. Advanced stamping and micro-welding techniques ensure low-resistance connections, reducing power loss. Electromagnetic interference (EMI) shielding and surface treatment processes enhance electrical performance and longevity.
Frigate uses hot-dip galvanization, zinc-aluminum-magnesium (Zn-Al-Mg) coating, and electroless nickel plating to protect steel components from corrosion. Nano-ceramic coatings provide hydrophobic and anti-reflective properties, improving efficiency in harsh climates. PVD (physical vapor deposition) coatings enhance wear resistance in tracking system gears and bearings.
Frigate applies specialized thermal barrier coatings (TBCs), diamond-like carbon (DLC), and PVD/CVD ceramic coatings to enhance wear and oxidation resistance. Plasma nitriding and anodizing techniques improve surface hardness, reducing friction and extending component lifespan in extreme aerospace environments.
- Real Impact
Words from Clients
See how global OEMs and sourcing heads describe their experience with our scalable execution.
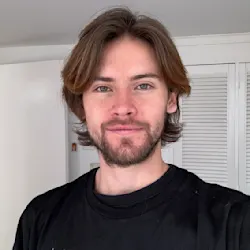
“Quick turnaround and solid quality.”
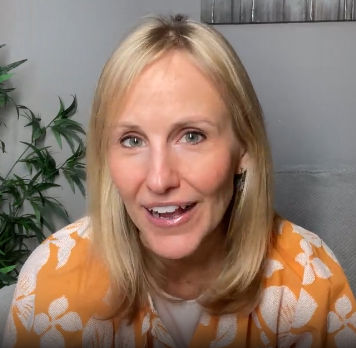
“The instant quote tool saved us time, and the parts were spot-on. Highly recommend Frigate!”
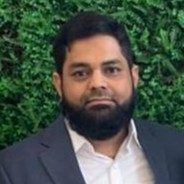
“I would strongly recommend Frigate to anyone who wants to do Rapid Prototyping, and take their ideas to manufacturing. One firm doing all kinds of Product Development!”
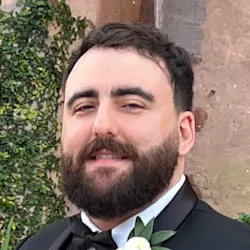
“Great service, fair price, and the parts worked perfectly in our assembly.”
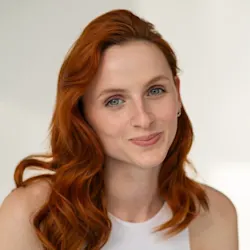
“Top-notch machining and fast shipping. Very satisfied with the results.”
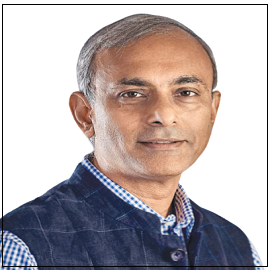
“The next disruption is happening in Prototyping & Manufacturing on-demand and Frigate is leading the way! I personally believe the Frigate's way of IIOT enabled cloud platform with Al.”
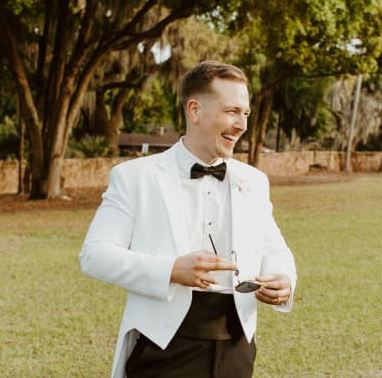
“Frigate delivered high-quality parts at a competitive price. The instant quote tool is a huge plus for us!”

“We appreciate the precision and quality of the machined components in the recent delivery—they meet our specifications perfectly and demonstrate Frigate’s capability for excellent workmanship.”
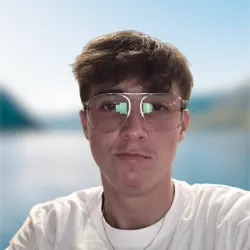
“Flawless execution from quote to delivery.”

“I am absolutely happy to work with supplier like Frigate who were quite proactive & result oriented . Frigate has high willingness team who has strong know how & their passion towards the products & process were absolutely thrilling.”
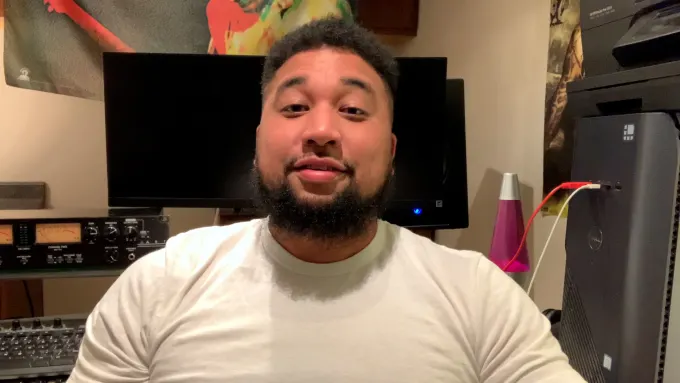
“The precision on these parts is impressive, and they arrived ahead of schedule. Frigate’s process really stands out!”
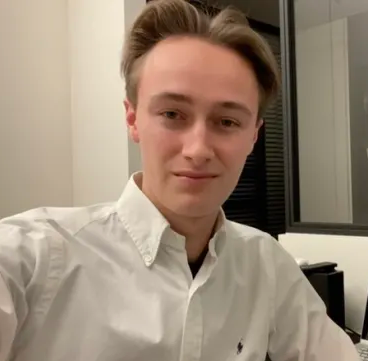
“Parts were exactly as spec’d, and the instant quote made budgeting a breeze.”
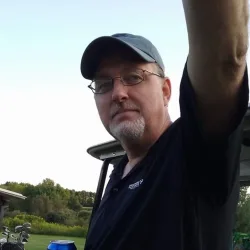
“Good value for the money.”
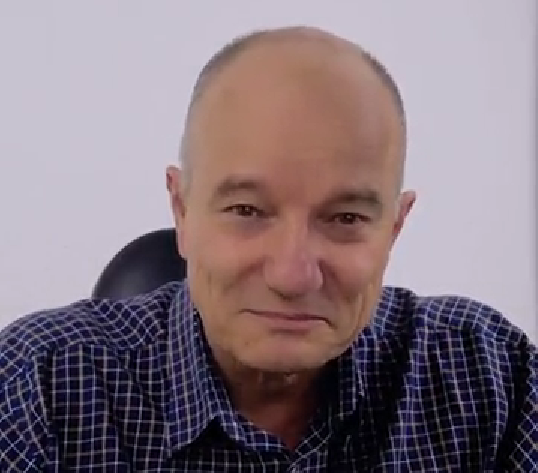
“The finish was perfect, and the team was easy to work with.”

“Working with Frigate has been great. Their proactive, results-driven approach and expertise shine through in every project. It's been a pleasure collaborating with them.”

"We are highly satisfied with the timely delivery and quality of the MIG Welding Cable from Frigate. Their attention to detail, secure packaging, and quick responsiveness stood out. We confidently recommend Frigate Engineering Services Pvt. Ltd. as a reliable manufacturing partner."
We'd love to Manufacture for you!
Submit the form below and our representative will be in touch shortly.
LOCATIONS
Registered Office
10-A, First Floor, V.V Complex, Prakash Nagar, Thiruverumbur, Trichy-620013, Tamil Nadu, India.
Operations Office
9/1, Poonthottam Nagar, Ramanandha Nagar, Saravanampatti, Coimbatore-641035, Tamil Nadu, India. ㅤ
Other Locations
- Bhilai
- Chennai
- USA
- Germany