Accelerating EV Production with Custom Manufacturing
Accelerate Electric Vehicle Innovation with Precision Component Prototyping and Scalable On-Demand Manufacturing
Services specifically tailored to the unique demands of
Electric Vehicles production
Multi-Cavity Variance Minimization
Real-time cavity pressure monitoring and digital mold flow validation ensure dimensional uniformity across cavities, reducing statistical deviation in critical EV geometries.
Material System Compatibility
Corrosion-resistant alloys and compatible surface treatments ensure structural and electrical performance in high-voltage, mixed-metal, and moisture-exposed EV assemblies.
Thermal Warpage Control
Thermal simulation and optimized cooling strategies reduce warpage in large EV castings, ensuring flatness and sealing integrity without post-processing.
Our Clients
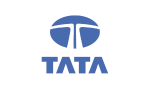
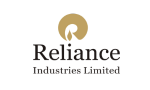


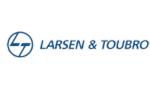
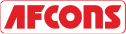


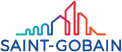

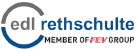

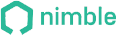
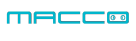









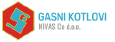
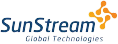

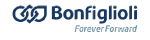


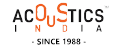
End-to-End Supply Chain Management
Simplify your supply chain with Frigate’s comprehensive management solutions. We leverage our global network of partners to source materials at competitive rates, manage inventory levels to avoid stockouts or overstocking, and oversee production to ensure on-time delivery. This allows you to focus on core competencies like design and engineering, while we handle the complexities of the supply chain.
Reducing Porosity in High-Pressure Cast EV Housings
Porosity in structural castings can compromise pressure resistance, often requiring leakage rates <10⁻⁴ mbar∙L/s in battery enclosures and inverter housings.
Controlled cavity vacuum levels under 50 mbar reduce gas entrapment, particularly in flow-restricted zones of box-shaped enclosures.
Gate velocity control within this range ensures proper mold filling without turbulence, a primary cause of gas entrapment and shrink voids.
Advanced CT scanning with 10–25 μm resolution is used to inspect critical sealing regions and validate internal integrity before assembly.

Controlling Flatness in Large-Scale Castings
Battery trays and drivetrain covers require flatness <0.1 mm over lengths exceeding 600 mm, which is difficult due to solidification shrinkage.
Precision thermal control across die faces maintains solidification symmetry, minimizing warping in wide or asymmetrical geometries.
Simulation platforms (e.g., MAGMASOFT or ProCAST) model temperature gradients and predict deformation zones to adjust tooling and cooling strategies pre-production.
Dies reinforced with steel cores and minimal deflection under injection pressures >1000 bar maintain consistent cavity form and flatness.

Achieving EMC Conformance in Conductive Enclosures
Power electronics housings must meet CISPR 25 and ISO 11452 standards, often requiring shielding effectiveness >60 dB in the 1–1000 MHz range.
Alloys such as AZ91D provide structural performance and electromagnetic shielding, reducing radiated emissions without additional coatings.
Integrated casting features for electrical continuity keep contact resistance low, ensuring robust grounding for PCB and chassis connections.
Electroless nickel or zinc plating enhances contact reliability at mating surfaces and improves RF shielding around sensitive electronics modules.
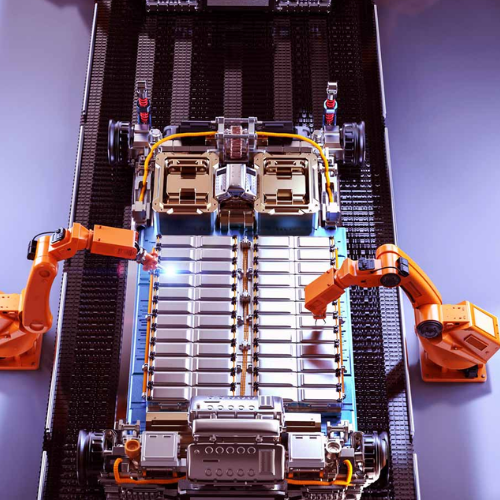
Our Electric Vehicles Products
100,000+
Parts Manufactured
250+
Frigaters
2000+
Machines
450+
Materials
25+
Manufacturing Process
Industries We Also Serve
Having Doubts? Our FAQ
Check all our Frequently Asked Question
Frigate uses die casting techniques that control surface roughness to Ra < 1.6 μm. This ensures tight interface between the cast housing and power modules. Flatness is controlled within 0.1 mm to reduce thermal resistance between components and heatsinks.
Yes. Frigate can cast components using alloys compatible with overmolding or insert molding. For example, busbars made of copper or brass are cast into aluminum housings. Interface bonding is enhanced using interlocking geometries and thermal preheating of inserts.
Frigate selects high-thermal-cycle-resistant alloys like A360 and uses directional solidification to reduce hot spots. Castings are validated with thermal shock tests from -40°C to 125°C, ensuring long life under real field conditions.
Frigate uses mold filling simulations to manage metal flow and solidification timing. Wall thicknesses as low as 1.5 mm are supported. Die temperatures are balanced within ±10°C to reduce cooling stress and ensure final parts are tolerable.
Frigate integrates grounding features directly into the casting with designated current paths. Resistance across grounding points is tested to remain under 10 mΩ. For enhanced performance, selective plating and post-cast machining ensure clean metal-to-metal contact.
- Real Impact
Words from Clients
See how global OEMs and sourcing heads describe their experience with our scalable execution.
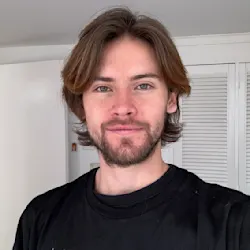
“Quick turnaround and solid quality.”
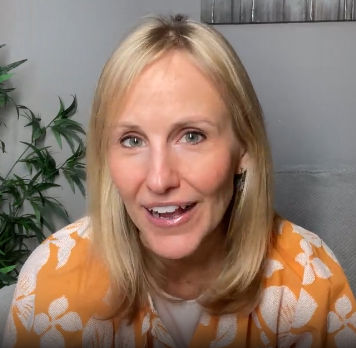
“The instant quote tool saved us time, and the parts were spot-on. Highly recommend Frigate!”
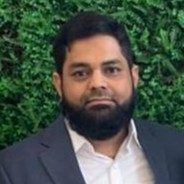
“I would strongly recommend Frigate to anyone who wants to do Rapid Prototyping, and take their ideas to manufacturing. One firm doing all kinds of Product Development!”
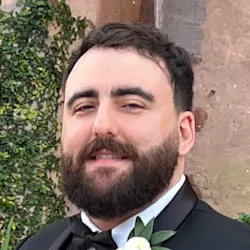
“Great service, fair price, and the parts worked perfectly in our assembly.”
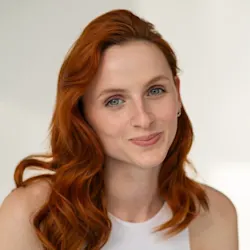
“Top-notch machining and fast shipping. Very satisfied with the results.”
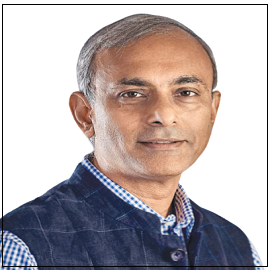
“The next disruption is happening in Prototyping & Manufacturing on-demand and Frigate is leading the way! I personally believe the Frigate's way of IIOT enabled cloud platform with Al.”
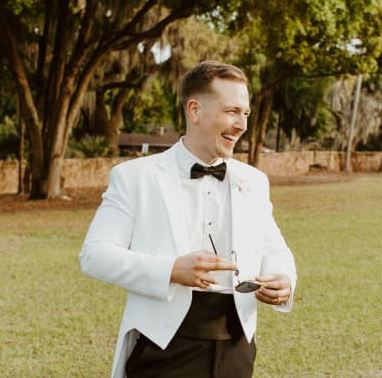
“Frigate delivered high-quality parts at a competitive price. The instant quote tool is a huge plus for us!”

“We appreciate the precision and quality of the machined components in the recent delivery—they meet our specifications perfectly and demonstrate Frigate’s capability for excellent workmanship.”
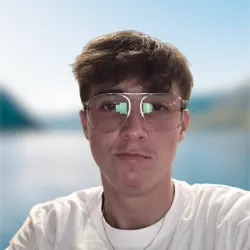
“Flawless execution from quote to delivery.”

“I am absolutely happy to work with supplier like Frigate who were quite proactive & result oriented . Frigate has high willingness team who has strong know how & their passion towards the products & process were absolutely thrilling.”
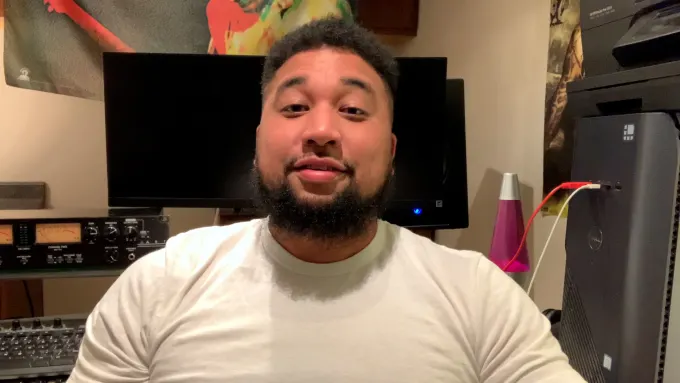
“The precision on these parts is impressive, and they arrived ahead of schedule. Frigate’s process really stands out!”
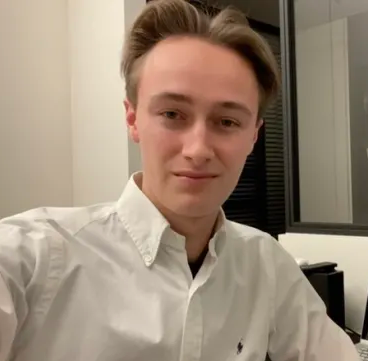
“Parts were exactly as spec’d, and the instant quote made budgeting a breeze.”
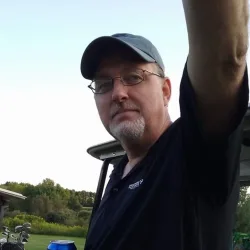
“Good value for the money.”
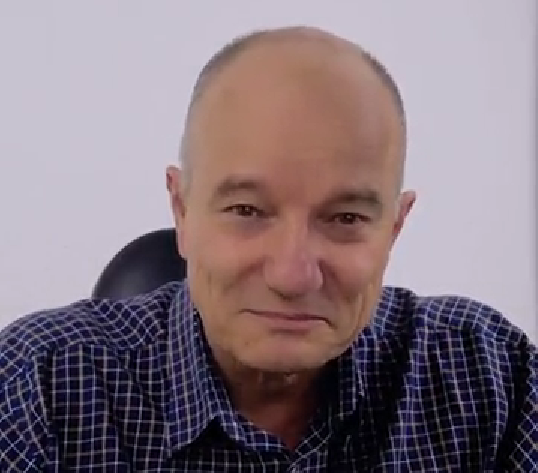
“The finish was perfect, and the team was easy to work with.”

“Working with Frigate has been great. Their proactive, results-driven approach and expertise shine through in every project. It's been a pleasure collaborating with them.”

"We are highly satisfied with the timely delivery and quality of the MIG Welding Cable from Frigate. Their attention to detail, secure packaging, and quick responsiveness stood out. We confidently recommend Frigate Engineering Services Pvt. Ltd. as a reliable manufacturing partner."
We'd love to Manufacture for you!
Submit the form below and our representative will be in touch shortly.
LOCATIONS
Registered Office
10-A, First Floor, V.V Complex, Prakash Nagar, Thiruverumbur, Trichy-620013, Tamil Nadu, India.
Operations Office
9/1, Poonthottam Nagar, Ramanandha Nagar, Saravanampatti, Coimbatore-641035, Tamil Nadu, India. ㅤ
Other Locations
- Bhilai
- Chennai
- USA
- Germany