Manufacturing Excellence for Critical Defense Operations
Streamline defense component engineering with CNC machining and scalable on-demand manufacturing
Your One-Stop Shop for Defense Manufacturing Needs
Compliance-Ready Manufacturing
Maintain regulatory alignment with ITAR, AS9100, and MIL-SPEC through structured documentation, traceable processes, and audit-ready quality systems.
Tolerance-Critical Production
Achieve dimensional accuracy and material integrity using calibrated equipment, certified alloys, and rigorous in-process quality inspection protocols.
Agile Part Development
Enable fast design iterations and small-batch production using flexible CNC machining, modular workflows, and adaptive digital manufacturing systems.
Our Clients






























Ensure Dimensional Integrity in Complex Assemblies
Defense-grade components demand inspection standards that go beyond conventional measuring tools. Maintaining dimensional accuracy is essential to prevent downstream failure in mission-critical systems.
Utilization of high-precision equipment such as Coordinate Measuring Machines (CMM), optical scanners, and surface profilometers enables accurate validation of complex geometries and micro-tolerances.
Full integration of Geometric Dimensioning and Tolerancing (GD&T) principles ensures components meet true position, flatness, and profile constraints as defined in the engineering drawings.
By validating critical dimensions at each stage, deviations that may cause interference, misalignment, or vibration in final assemblies are eliminated before deployment.

Optimize Short-Run Manufacturing for Defense Needs
Defense manufacturing often requires multiple low-quantity part types with differing materials, tolerances, and features—without compromising precision or repeatability.
Modular production cells and adaptable workflows enable fast changeovers, minimal downtime, and consistency across short production runs with varying specifications.
Using configurable fixturing, quick-change tooling, and standardized setup protocols allows the handling of diverse SKUs without excessive retooling effort or dimensional drift.
Integrating digital routers and part-specific work instructions ensures accurate process tracking and repeatability across unique, non-recurring part numbers.

Establish a Continuous Digital Thread Across Systems
Disconnected systems between design, production, and quality control introduce errors that compromise traceability, audit readiness, and end-use performance in defense applications.
Seamless integration between CAD, CAM, QA, and ERP platforms ensures every engineering change or tolerance update is reflected across all production stages.
Centralized digital systems manage file versions, work instructions, and inspection plans, minimizing the risk of outdated data being used in manufacturing or QC.
A connected digital thread enables real-time tracking of material sources, inspection outcomes, and part revisions—crucial for compliance, maintenance, and defense audits.
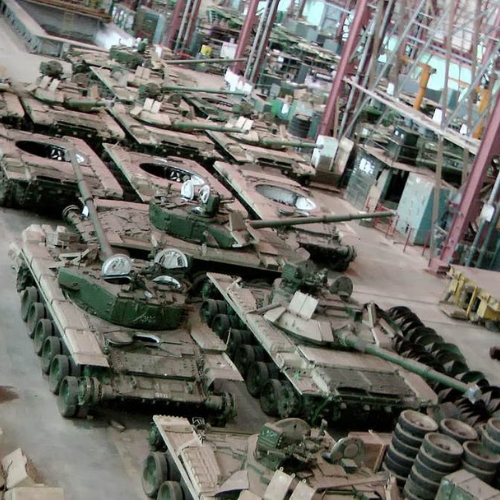
Our Defense Products
100,000+
Parts Manufactured
250+
Frigaters
2000+
Machines
450+
Materials
25+
Manufacturing Process
Industries We Also Serve
Having Doubts? Our FAQ
Check all our Frequently Asked Question
Frigate integrates CAD and ERP systems to link every job with the current revision. Once an ECO is approved, the updated model, toolpaths, and inspection plans are synced automatically. This prevents outdated files from reaching the shop floor and ensures that no obsolete version is used during machining or inspection.
Frigate operates under AS9100-aligned quality protocols. All parts undergo First Article Inspection (FAI), In-Process Inspection (IPI), and Final Inspection with full documentation. Quality data is logged digitally and retained to meet defense compliance and customer-specific document retention policies.
Frigate uses high-resolution 3D scanning and point cloud comparison to validate complex geometries. Parts with organic or freeform features are compared directly to CAD using deviation mapping, ensuring surface fidelity and critical functional interfaces are within spec.
Yes, Frigate embeds part-level serialization with barcoding or laser marking and links it to lot-specific material certs, process records, and inspection reports. This is critical for defense programs requiring cradle-to-grave traceability across aluminum, steel, and exotic alloy builds.
Frigate deploys part-specific inspection programs tied to each SKU. The QA system auto-loads the correct plan based on job ID, ensuring that unique GD&T, surface finish, and dimensional checks are applied correctly, even in mixed-run production environments.
- Real Impact
Words from Clients
See how global OEMs and sourcing heads describe their experience with our scalable execution.
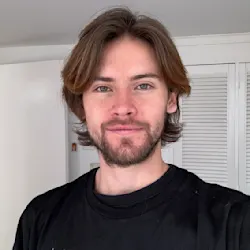
“Quick turnaround and solid quality.”
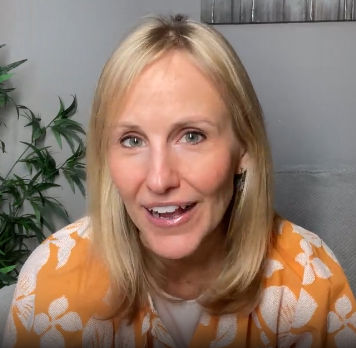
“The instant quote tool saved us time, and the parts were spot-on. Highly recommend Frigate!”
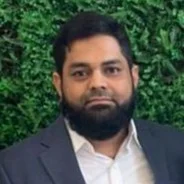
“I would strongly recommend Frigate to anyone who wants to do Rapid Prototyping, and take their ideas to manufacturing. One firm doing all kinds of Product Development!”
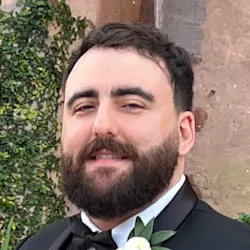
“Great service, fair price, and the parts worked perfectly in our assembly.”
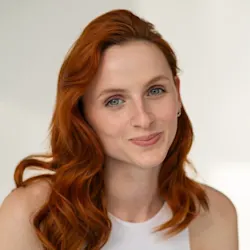
“Top-notch machining and fast shipping. Very satisfied with the results.”
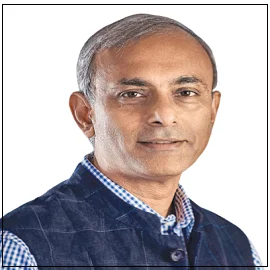
“The next disruption is happening in Prototyping & Manufacturing on-demand and Frigate is leading the way! I personally believe the Frigate's way of IIOT enabled cloud platform with Al.”
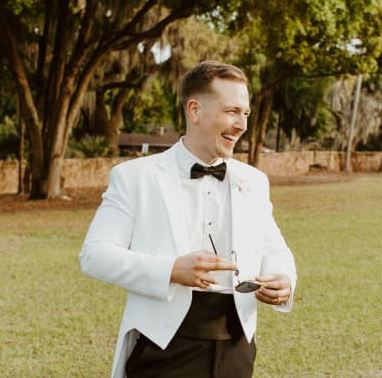
“Frigate delivered high-quality parts at a competitive price. The instant quote tool is a huge plus for us!”

“We appreciate the precision and quality of the machined components in the recent delivery—they meet our specifications perfectly and demonstrate Frigate’s capability for excellent workmanship.”
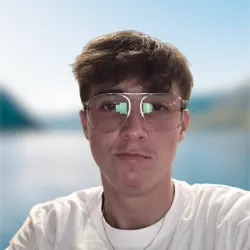
“Flawless execution from quote to delivery.”

“I am absolutely happy to work with supplier like Frigate who were quite proactive & result oriented . Frigate has high willingness team who has strong know how & their passion towards the products & process were absolutely thrilling.”
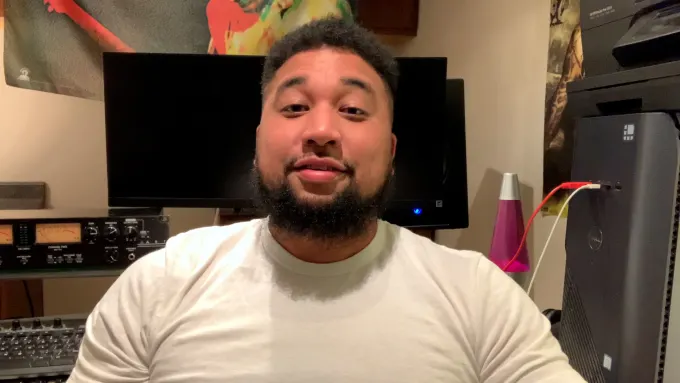
“The precision on these parts is impressive, and they arrived ahead of schedule. Frigate’s process really stands out!”
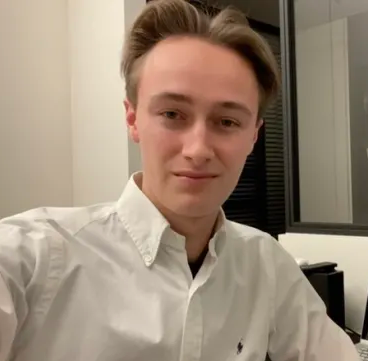
“Parts were exactly as spec’d, and the instant quote made budgeting a breeze.”
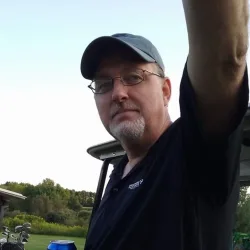
“Good value for the money.”
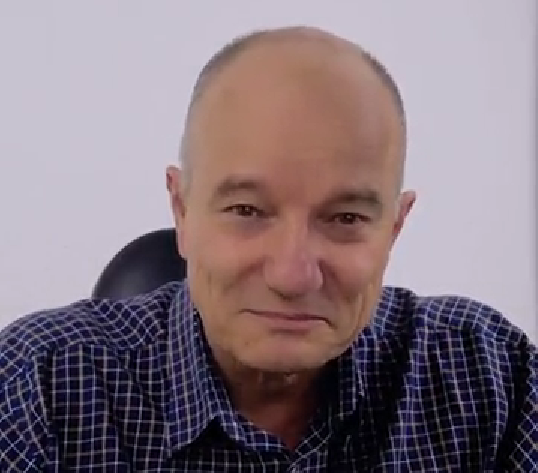
“The finish was perfect, and the team was easy to work with.”

“Working with Frigate has been great. Their proactive, results-driven approach and expertise shine through in every project. It's been a pleasure collaborating with them.”

"We are highly satisfied with the timely delivery and quality of the MIG Welding Cable from Frigate. Their attention to detail, secure packaging, and quick responsiveness stood out. We confidently recommend Frigate Engineering Services Pvt. Ltd. as a reliable manufacturing partner."
We'd love to Manufacture for you!
Submit the form below and our representative will be in touch shortly.
LOCATIONS
Registered Office
10-A, First Floor, V.V Complex, Prakash Nagar, Thiruverumbur, Trichy-620013, Tamil Nadu, India.
Operations Office
9/1, Poonthottam Nagar, Ramanandha Nagar, Saravanampatti, Coimbatore-641035, Tamil Nadu, India. ㅤ
Other Locations
- Bhilai
- Chennai
- Texas, USA