Custom Aerospace Industry Manufacturing with Unmatched Precision
Minimize Risk, Accelerate Launch, and Optimize Your Supply Chain with Rapid Prototyping and On-Demand Production
Launch your Aerospace parts with Frigate
Lightweight Structural Engineering
High-speed milling and additive manufacturing creates intricate, weight-optimized aerospace components while maintaining strength, stability, and aerodynamic efficiency.
Advanced Alloy Processing
Specialized tooling, controlled machining speeds, and adaptive cooling enable precise cutting of titanium, Inconel, and high-performance aerospace composites.
Extreme Precision Machining
Multi-axis CNC machining and real-time quality control ensure ±0.0001-inch accuracy, eliminating deviations and ensuring aerospace component reliability.
Our Clients






























Frigate - Where Excellence Meets the Demands of Aerospace
In the aerospace industry, even the smallest details can have a major impact. That’s why Frigate is committed to delivering unparalleled accuracy, precision, and reliability in every casting we produce.
Our cutting-edge facilities are equipped with state-of-the-art CMM (Coordinate Measuring Machine) and VMM (Vision Measuring Machine) technology. This allows us to achieve tolerances as low as 1 micron, ensuring your aerospace parts meet the most rigorous specifications.
100,000+
Parts Manufactured
250+
Frigaters
2000+
Machines
450+
Materials
25+
Manufacturing Process
Our Aerospace Products
First Article Inspection (FAI) for Aerospace Manufacturing
Comprehensive validation ensures manufacturing precision, material integrity, and process reliability before full-scale production, preventing deviations that impact performance and safety.
Workflows, tooling, and machining programs are evaluated to ensure consistency, eliminate deviations, and meet aerospace quality regulations.
CMM inspections, GD&T analysis, and laser scanning confirm tolerances within ±0.005 mm, preventing misalignment and structural instability.
Metallurgical analysis, microstructural evaluation, and surface roughness testing (Ra ≤ 0.8 µm) ensure aerospace-grade materials meet required standards.

End-to-End Product Development with Iterative Manufacturing
Before mass production, integrated prototyping and production ensure precision, performance optimization, and regulatory compliance.
CNC machining, additive manufacturing (DMLS, SLS), and hybrid fabrication enable part refinement before full-scale production.
Multi-axis machining, high-precision casting, and robotic assembly ensure repeatability and dimensional accuracy across production volumes.
Components undergo stress testing, thermal analysis (−65°C to 200°C), and aerodynamic simulations for compliance with aerospace standards.

Quality Certifications and Full Traceability Compliance
Certified processes guarantee regulatory adherence, defect prevention, and complete material traceability.
Facilities follow aerospace quality standards, integrating risk mitigation, controlled workflows, and stringent inspections.
CMM, X-ray imaging, ultrasonic testing, and spectrometry ensure zero defects, porosity detection up to 0.05 mm, and material integrity.
Aerospace-grade alloys, including aluminum, titanium, and superalloys, are tracked from sourcing to delivery with 100% documentation.
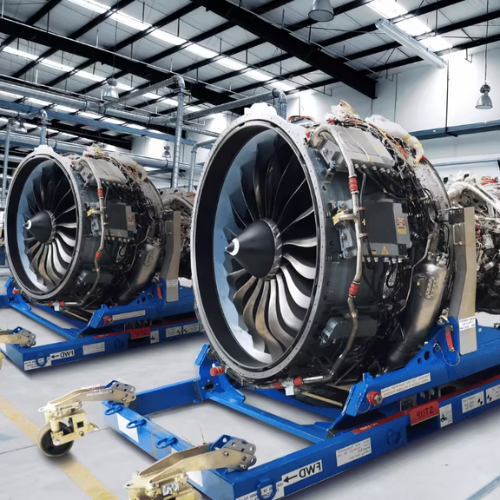
Industries We Also Serve
Having Doubts? Our FAQ
Check all our Frequently Asked Question
Frigate utilizes vacuum melting and controlled solidification techniques to maintain uniform grain structures in aerospace alloys. Advanced heat treatment processes, including solution annealing and precipitation hardening, optimize strength, fatigue resistance, and thermal stability. Spectrometry and microstructural analysis verify compliance with aerospace material standards.
Frigate applies high-pressure coolant delivery, ceramic and CBN cutting tools, and adaptive feed rate control to minimize tool wear when machining superalloys like Inconel and titanium. Dynamic toolpath adjustments and in-process monitoring prevent excessive heat generation and ensure extended tool life.
Frigate employs vacuum-assisted die casting, ceramic shell investment casting, and directional solidification to reduce porosity and shrinkage defects. Advanced mold flow simulations optimize gating and riser design, while X-ray inspection and CT scanning verify internal integrity before final processing.
Frigate integrates coordinate measuring machine (CMM) inspections, laser scanning, and real-time digital twin modeling to verify dimensional consistency across complex assemblies. Robotic metrology systems ensure precise alignment, while torque and vibration testing confirm mechanical stability under aerospace operating conditions.
Frigate applies specialized thermal barrier coatings (TBCs), diamond-like carbon (DLC), and PVD/CVD ceramic coatings to enhance wear and oxidation resistance. Plasma nitriding and anodizing techniques improve surface hardness, reducing friction and extending component lifespan in extreme aerospace environments.
- Real Impact
Words from Clients
See how global OEMs and sourcing heads describe their experience with our scalable execution.
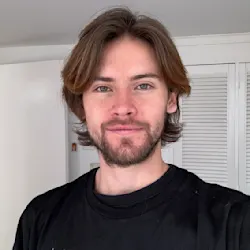
“Quick turnaround and solid quality.”
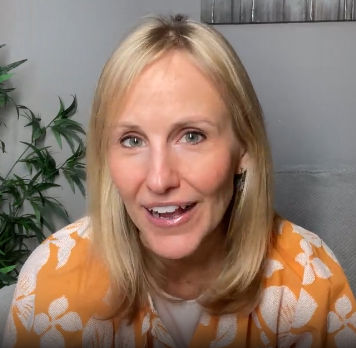
“The instant quote tool saved us time, and the parts were spot-on. Highly recommend Frigate!”
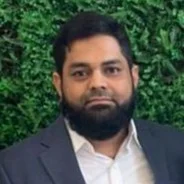
“I would strongly recommend Frigate to anyone who wants to do Rapid Prototyping, and take their ideas to manufacturing. One firm doing all kinds of Product Development!”
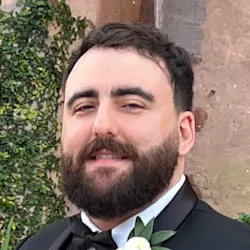
“Great service, fair price, and the parts worked perfectly in our assembly.”
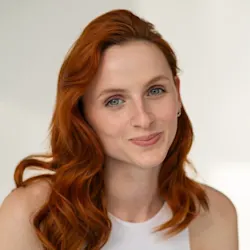
“Top-notch machining and fast shipping. Very satisfied with the results.”
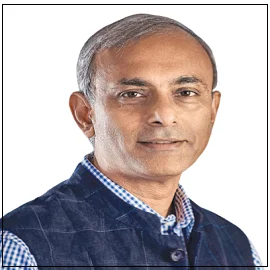
“The next disruption is happening in Prototyping & Manufacturing on-demand and Frigate is leading the way! I personally believe the Frigate's way of IIOT enabled cloud platform with Al.”
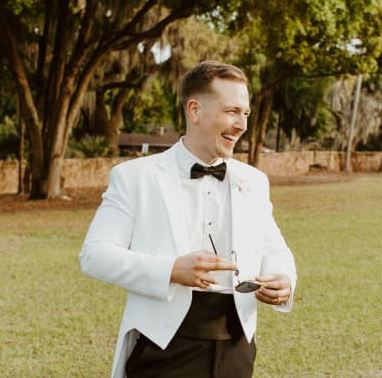
“Frigate delivered high-quality parts at a competitive price. The instant quote tool is a huge plus for us!”

“We appreciate the precision and quality of the machined components in the recent delivery—they meet our specifications perfectly and demonstrate Frigate’s capability for excellent workmanship.”
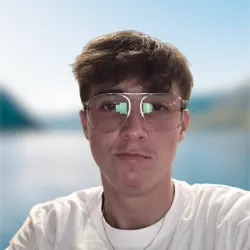
“Flawless execution from quote to delivery.”

“I am absolutely happy to work with supplier like Frigate who were quite proactive & result oriented . Frigate has high willingness team who has strong know how & their passion towards the products & process were absolutely thrilling.”
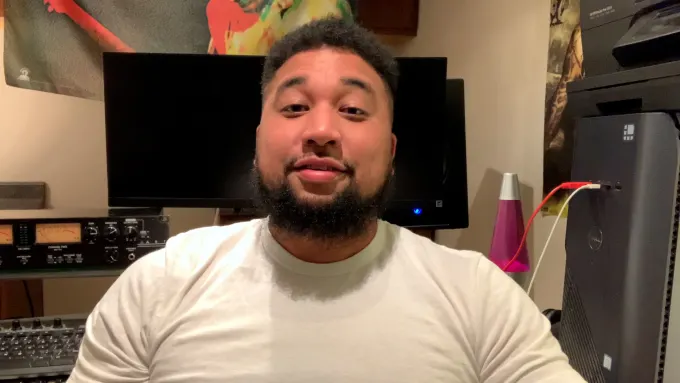
“The precision on these parts is impressive, and they arrived ahead of schedule. Frigate’s process really stands out!”
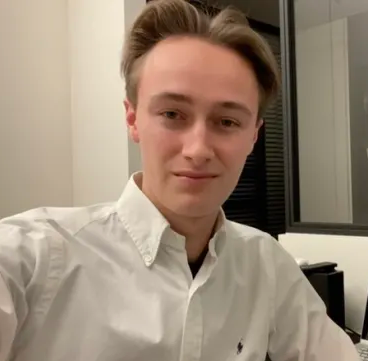
“Parts were exactly as spec’d, and the instant quote made budgeting a breeze.”
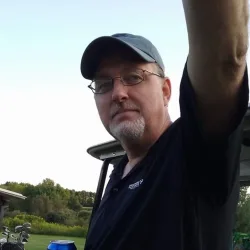
“Good value for the money.”
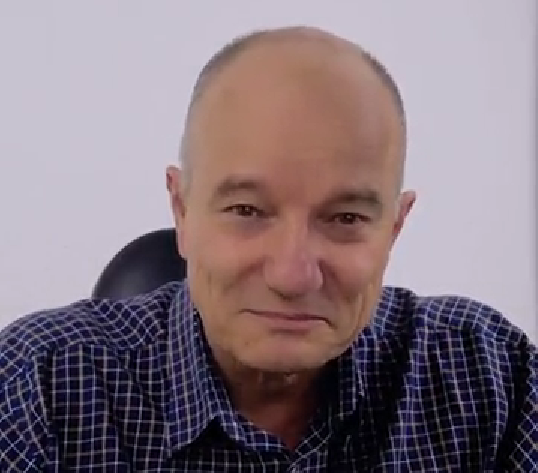
“The finish was perfect, and the team was easy to work with.”

“Working with Frigate has been great. Their proactive, results-driven approach and expertise shine through in every project. It's been a pleasure collaborating with them.”

"We are highly satisfied with the timely delivery and quality of the MIG Welding Cable from Frigate. Their attention to detail, secure packaging, and quick responsiveness stood out. We confidently recommend Frigate Engineering Services Pvt. Ltd. as a reliable manufacturing partner."
We'd love to Manufacture for you!
Submit the form below and our representative will be in touch shortly.
LOCATIONS
Registered Office
10-A, First Floor, V.V Complex, Prakash Nagar, Thiruverumbur, Trichy-620013, Tamil Nadu, India.
Operations Office
9/1, Poonthottam Nagar, Ramanandha Nagar, Saravanampatti, Coimbatore-641035, Tamil Nadu, India. ㅤ
Other Locations
- Bhilai
- Chennai
- Texas, USA