When working on a complex project, one of the biggest questions is: How do I select the right forging supplier? Whether looking for the best forging supplier for a small batch or a large-scale production, the process can be challenging. Many buyers face common issues like quality concerns, high costs, and missed deadlines. These issues can lead to project delays, increased expenses, and an overall drop in product performance.
This blog will explore how selecting the right forging supplier can make or break your project. This guide will highlight key factors to consider when choosing a supplier, the common pain points of supplier selection, and how to address these issues effectively.
Key Pain Points in Supplier Selection
Selecting a forging supplier is not a straightforward process. Several factors must be considered to ensure the supplier meets your project requirements. Some of the most common challenges faced by buyers when selecting a forging supplier include:
Quality Assurance Challenges
One of the biggest pain points when selecting a forging supplier is ensuring consistent quality. Forging parts must meet exact specifications, or they may not perform as expected. Poor-quality forged parts can result in product failures, expensive rework, and loss of customer trust.
Common quality issues can stem from inconsistent material properties, poor forging techniques, or inadequate quality control processes. For instance, materials not correctly heated or forged can result in weak points, making them less reliable in demanding applications. This is particularly crucial in industries like aerospace or automotive, where the performance and safety of forged parts are essential.
Lead Time Concerns
Another issue many buyers face is long lead times. The time it takes to produce forged parts can significantly impact a project’s timeline. If a forging supplier cannot meet your required delivery dates, your entire production schedule can be delayed, leading to missed deadlines and costly delays.
Lead time concerns arise from inefficient production scheduling, limited production capacity, or a lack of process optimization. Buyers need to select a forging supplier who can consistently meet deadlines without compromising on quality.
Cost Management and Budget Overruns
Selecting the best forging supplier also comes down to managing costs. Many buyers experience frustration when a supplier’s initial quote is low, but hidden fees and unexpected costs arise later. Overruns can occur due to issues like changes in material prices, unaccounted-for labor costs, or expensive shipping.
The cost of a forged part should be predictable and transparent. If a supplier has an unclear pricing structure or is not transparent about costs, it can lead to overspending. This can significantly impact a project’s overall budget, especially when the costs stack up over multiple orders or long-term contracts.
Supplier Reliability and Communication Gaps
Communication is key when selecting a right forging supplier. A reliable supplier should keep buyers informed at every stage of the project. This includes providing updates on production progress, addressing concerns quickly, and ensuring the quality of parts meets expectations.
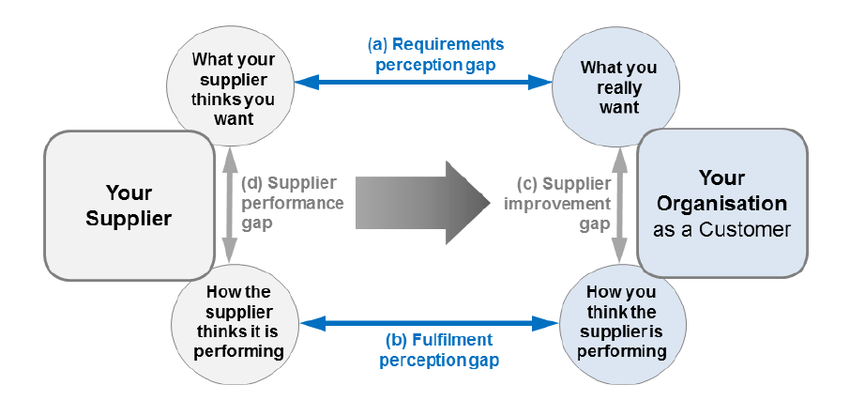
When unclear or delayed, misunderstandings can occur, leading to mistakes, delays, and frustration. Buyers must ensure that their chosen supplier is responsive, reliable, and easy to work with.
Key Considerations When Selecting a Forging Supplier
Now that we’ve identified the pain points in selecting the right forging supplier, it’s time to look at the factors that should guide the decision-making process. The right forging supplier should be able to address these challenges and deliver on the project’s specific requirements.
Technical Expertise and Specialization
One of the first factors to consider when selecting a right forging supplier is their technical expertise. Forging is a complex process that requires knowledge of metallurgy, forging techniques, and the behavior of different materials under pressure and heat.
When choosing a supplier, it is essential to verify their experience with specific forging processes, such as hot or cold forging, and the types of materials they specialize in, such as steel, aluminum, or titanium. The best forging supplier will deeply understand the forging process and the necessary equipment to produce parts to precise specifications.
For example, specialized expertise in producing parts with tight tolerances and unique material properties is essential in high-demand industries like aerospace or automotive. A supplier without this expertise may struggle to deliver quality parts or meet specific project requirements.
Capacity and Scalability
Another important factor in selecting the right forging supplier is assessing their capacity to handle your order size. Suppliers vary in terms of their production capabilities. Some may specialize in small batch runs, while others are equipped to handle large volumes of parts.
The best forging supplier should be able to scale production according to your project needs. This means having enough equipment and workforce to increase production when demand rises or the flexibility to handle smaller, custom orders without compromising on quality or lead times.
Certifications and Compliance with Industry Standards
A reliable right forging supplier should adhere to industry standards and hold certifications demonstrating their commitment to quality and compliance. For example, suppliers with ISO 9001 certification have demonstrated their ability to meet strict quality control standards, which ensures that parts are consistently produced to the required specifications.
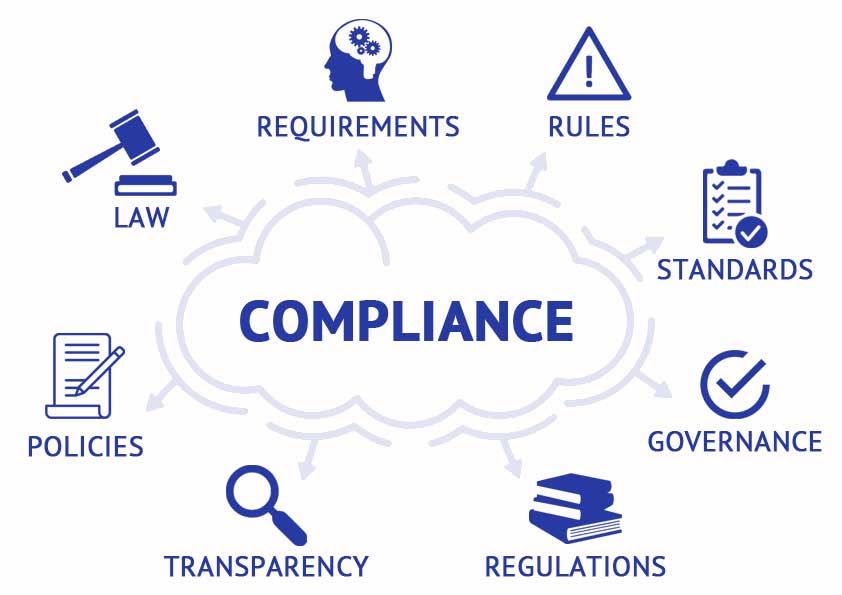
When selecting a right forging supplier, it is important to look for certifications like ASTM (American Society for Testing and Materials) or specific automotive or aerospace standards. These certifications prove that the supplier has the necessary processes to meet industry-specific requirements and ensure the supplier’s reliability and quality.
Innovation and Technological Capabilities
Technology plays a significant role in modern forging processes. The best forging suppliers invest in advanced technologies and equipment to improve the quality of their products and streamline production. This includes automated die-casting, precision control systems, and advanced testing methods.
Innovative suppliers can offer better solutions for complex projects and reduce errors in the production process. For instance, using advanced equipment can result in more precise forging and faster production times, directly contributing to improved lead times and reduced costs.
Supplier Transparency and Relationship Building
Transparency is a key factor in selecting a right forging supplier. A supplier who is open about their processes, timelines, and pricing is far more reliable than one who is vague or hard to reach. Transparent suppliers will be upfront about any challenges, cost adjustments, or delays that may arise during the production process.
Building a long-term relationship with a reliable forging supplier is also crucial. A supplier who understands your needs and goals can become a trusted partner in future projects, ensuring smoother processes and better outcomes.
How Frigate’s Capabilities Align with Optimal Supplier Selection
Frigate Die Casting Services understands the challenges of selecting the best forging supplier for your project. With decades of experience in the industry, Frigate is equipped to meet each client’s unique needs. Here’s how Frigate’s capabilities align with key considerations when selecting a forging supplier.
Expertise in Advanced Forging Processes
Frigate specializes in hot and cold forging processes, allowing clients to choose the best method for their requirements. The company’s technical team is skilled in handling various materials, including aluminum, zinc, and copper alloys, ensuring that parts meet the highest standards.
Frigate’s experience with precision forging also ensures that tight tolerances are met for applications in the automotive, aerospace, and electronics industries.
Commitment to Timely Delivery and Lead Time Optimization
Frigate understands the importance of meeting deadlines. With an optimized production process, Frigate can reduce lead times and deliver products on schedule, even for large and complex orders. Their efficient scheduling system ensures that each project is completed within the agreed timeline, helping clients avoid costly delays.
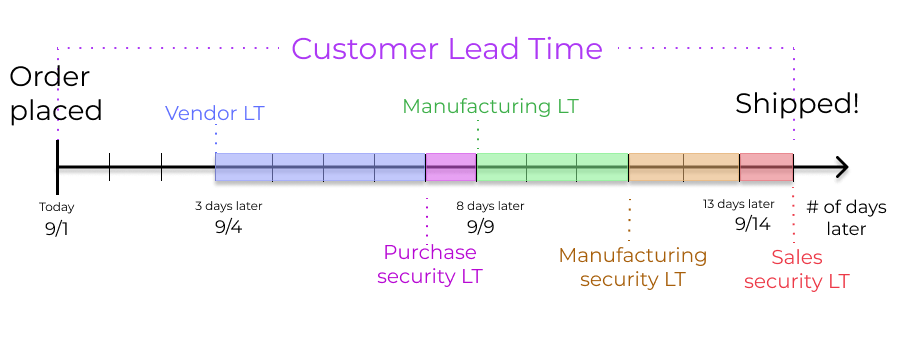
Cost-effective solutions with Transparent Pricing
Frigate offers clear and competitive pricing structures, allowing clients to manage their budgets effectively. The company’s transparent approach to pricing ensures that clients are never surprised by hidden fees or unexpected cost increases.
Frigate also offers solutions designed to optimize production costs without compromising quality, making it easier for clients to stay within budget while still getting the best results.
Industry Certifications and Compliance
Frigate is ISO 9001 certified, ensuring that all processes meet rigorous quality control standards. The company also adheres to various industry standards, making it a trusted partner for automotive, aerospace, and defense clients.
Innovative Capabilities and Technological Advancements
Frigate continually invests in advanced forging technology and equipment to improve production efficiency and quality. Frigate can offer clients enhanced precision and faster production times with cutting-edge machinery and a focus on innovation.
Strong Client Relationships and Communication
At Frigate, client satisfaction is a top priority. The company ensures clear communication throughout the project, keeping clients informed every step of the way. Frigate can offer tailored solutions that meet each client’s needs by building strong, long-term relationships.
Conclusion
Selecting the right forging supplier for your project is essential to ensuring quality, timely delivery, and cost-effectiveness. By considering factors such as technical expertise, production capacity, certifications, and innovation, you can make an informed decision that will set your project up for success.
Frigate Die Casting Services is committed to providing high-quality, reliable forging solutions focusing on customer satisfaction. With decades of experience and a proven track record, Frigate is the ideal partner for your forging needs.
If you’re looking for a trusted, reliable right forging supplier, contact Frigate today to learn how they can help bring your project to life.