CNC Milling Services
Frigate offers custom-machined parts using advanced three-, four-, and five-axis CNC machining centers. Our skilled machinists create precise turned and milled parts from various plastic and metal materials, ensuring top-quality craftsmanship and adherence to your specifications.
Our Clients





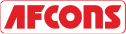

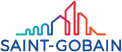


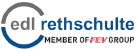

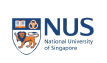
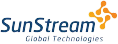

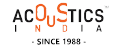




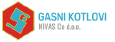
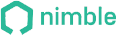
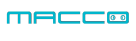












Advantages of CNC Milling Services
Rapid Turnaround
CNC milling ensures quick production times with automated processes and advanced machinery. This reduces lead times and offers faster delivery of high-quality parts, meeting tight deadlines efficiently.
High Precision Tolerances
CNC milling achieves exceptional accuracy with precise control over dimensions and tolerances, ensuring consistent, high-quality parts that meet exact specifications and stringent industry standards.
Complex Geometries
CNC milling easily handles intricate designs and complex geometries, producing parts that would be challenging or impossible with traditional machining. This enhances design flexibility and innovation.
High Production & Scalability
CNC milling supports large-scale production with consistent quality, making it ideal for high-volume manufacturing. It also maintains scalability for various production needs without compromising precision or efficiency.
Comprehensive CNC Milling Solutions for Diverse Industry Needs
At Frigate, our extensive network ensures we have the right shop and machinery to produce whatever your part requirements. We support 3-axis, 4-axis, 5-axis, and right-angle milling capabilities to quickly create designs, from simple lines to complex geometric shapes. We offer instant pricing, flexible lead times, and expert design-for-manufacturability feedback on materials and processes for your custom CNC milled parts, regardless of industry. Get your instant quote today.

Get Your Quote Now
- Instant Quotation
- On-Time Delivery
- Affordable Cost
Our CNC Milling Process







Engineers design the part using CAD (Computer-Aided Design) software. The design includes all dimensions and specifications.
The CAD design is converted into CNC code, often using CAM (Computer-Aided Manufacturing) software. This code tells the milling machine how to move and cut the material.
Operators prepare the CNC milling machine by securing the material (workpiece) and installing the appropriate cutting tools.
The CNC machine reads the code and starts milling. The cutting tool rotates and moves along multiple axes to remove material from the workpiece and shape it into the desired part.
The machine monitors the cutting operations throughout the process. Operators may make adjustments to ensure precision and quality.
After milling, the part may undergo additional processes like deburring or polishing to achieve the final specifications.
The finished part is thoroughly inspected to meet all design requirements and tolerances.
CNC Milling Materials
We use various materials for CNC milling to meet different project needs. Each material offers unique properties that make it suitable for specific applications, allowing us to deliver precise, high-quality parts tailored to your needs.
A2 Tool Steel is a high-carbon, high-chromium steel known for its toughness and wear resistance. It’s ideal for producing durable, high-strength parts that can withstand heavy use.
Acrylonitrile Butadiene Styrene (ABS) is a versatile plastic with good impact resistance and toughness. It’s commonly used for prototypes and parts requiring durability and easy post-processing.
Acrylic is a clear plastic with excellent optical clarity and weather resistance. It’s often used for displays and components where transparency and aesthetics are important.
Aluminum is a lightweight, corrosion-resistant metal with good machinability. Because of its strength-to-weight ratio, it’s commonly used in aerospace, automotive, and various industrial applications.
Brass is a copper-zinc alloy known for its machinability and corrosion resistance. It’s used for components requiring precise detailing and good mechanical properties.
Bronze is a copper-tin alloy with excellent wear resistance and strength. It’s often used for bushings, bearings, and other friction-prone components.
Cast Iron is known for its high wear resistance and machinability. It’s used in heavy-duty applications such as machinery parts and engine components.
Copper offers excellent thermal and electrical conductivity. It’s used in applications requiring heat dissipation or electrical conductivity, such as electronic components.
Delrin, or Polyoxymethylene (POM), is a high-performance plastic known for its low friction and high dimensional stability. It’s used for precision gears and mechanical parts.
Garolite G-10 is a fiberglass-reinforced epoxy laminate with high strength and electrical insulation properties. It’s ideal for components requiring high durability and electrical resistance.
High-density polyethylene (HDPE) is a durable, flexible plastic resistant to impact and chemicals. It’s used for containers, pipes, and various industrial applications.
Nylon is a strong, flexible plastic with excellent wear resistance and low friction properties. It’s commonly used for gears, bearings, and other mechanical parts.
Polyether Ether Ketone (PEEK) is a high-performance plastic with exceptional strength and chemical resistance. It’s used in demanding applications such as aerospace and medical devices.
Steel is a versatile material known for its strength and durability. It’s used in various applications, from construction to automotive parts.
Titanium is a lightweight, high-strength metal with excellent corrosion resistance. It’s used in aerospace, medical implants, and high-performance engineering applications.
Polycarbonate is a durable plastic with high impact resistance and optical clarity. It’s often used for protective covers and transparent components.
Polypropylene is a flexible plastic with good chemical resistance and impact strength. It’s used for a variety of industrial and consumer products.
Polyphenylene Sulfide (PPS) is a high-performance plastic with excellent chemical resistance and dimensional stability. It’s used in applications requiring high-temperature resistance.
Polytetrafluoroethylene (PTFE) is known for its non-stick properties and chemical resistance. It’s used in applications where low friction and resistance to harsh chemicals are required.
Stainless Steel offers high corrosion resistance and strength. It’s widely used in applications ranging from kitchen equipment to industrial machinery.
Ultra-high-molecular-weight polyethylene (UHMW) is a tough, abrasion-resistant plastic used for high-wear applications and components requiring low friction.
Ultem is a high-performance plastic known for its strength, heat resistance, and electrical insulation properties. It’s used in aerospace, medical, and electronics applications.
Solving Precision and Efficiency Challenges with CNC Milling at Frigate
At Frigate, CNC precision milling offers significant advantages, including producing complex, high-accuracy parts at lower production and setup costs. This advanced technology minimizes human error, ensuring precise and reliable results. Additionally, by automating much of the production process, our operators can focus more on quality assurance and project oversight, ensuring every detail meets your exact specifications and industry standards. This combination of precision and efficiency helps us deliver top-quality parts that meet the highest standards.

Compliance for CNC Milling Services
Frigate’s CNC Milling services strictly follow industry standards to guarantee precision and reliability in every part. Our processes are designed to meet the highest regulatory requirements, ensuring compliance with key certifications that uphold quality, safety, and performance across all sectors. We integrate advanced protocols, continuous audits, and detailed traceability to provide our clients with defect-free, high-quality components.
Certification Number: 12345-QMS for quality management and continuous improvement.
Certification Number: 67890-AS91 for aerospace quality management.
Certification Number: 98765-RH to restrict hazardous materials in manufacturing.
Certification Number: 11223-CE for meeting EU safety and environmental standards.
Certification Number: 44556-NAD for specialized processes like heat treatment and material testing.
Certification Number: 54321-TS for automotive industry quality standards.
Certification Number: 67890-UL for compliance with safety and environmental criteria in electrical components.

Tolerance for CNC Milling Services
Tolerance for the total variation in a circular feature during rotation, such as for shafts.
Tolerance for the alignment of two cylindrical features along a common axis.
Tolerance for deviation from a straight line in a part's edge or surface.
Tolerance for the actual location of a feature relative to its design position, crucial for hole patterns.
Tolerance for the roundness of a feature, ensuring uniformity in cylindrical parts.
Tolerance for the evenness of a flat surface, typically measured with a dial indicator.
Tolerance for parallelism between two opposing surfaces, ensuring the surfaces stay parallel.
Tolerance for angular cuts or bevels, ensuring precise angle cuts on edges.
Tolerance for the angle between a hole axis and a reference surface, ensuring holes are perpendicular.
Tolerance for alignment of a bored feature to the center of a part, ensuring precise hole placement.
Tolerance for the depth of threaded holes or inserts, critical for fastener engagement.
Tolerance for thread lead, ensuring consistent and precise movement along the thread axis.
Tolerance for radial variation from the center axis of a cylindrical feature during rotation.
Tolerance for the deviation of the surface from a perfect profile, typically for complex contoured parts.
Tolerance for the accuracy of circular motion during milling, ensuring precise arcs or circles.

Quality Testing Standards for CNC Milling Services
Assesses the precision of CNC machines by measuring positional accuracy and repeatability.
Monitors heat generation in the milling process to detect temperature-induced deformations.
Measures the tool diameter and condition to detect wear and ensure machining precision.
Monitors machine and tool vibrations that could affect precision during milling operations.
Measures the variation in the spindle axis to ensure consistent rotational accuracy.
Measures the forces during machining to assess stability and tool performance.
Verifies the accuracy of dynamic movements, especially during high-speed operations.
Measures the residual stresses in a machined part to predict material behavior and integrity.
Analyzes the grain structure and defects in materials to ensure uniformity and integrity after machining.
Measures deformation or distortion in parts due to internal stresses or process-induced factors.
Assesses material hardness to ensure machining tolerance and part strength.
Adaptable CNC Milling Solutions for Diverse Manufacturing Needs
CNC milling machines solve the challenge of achieving precision and consistency in manufacturing. Designed for exacting standards and repeatability, they excel in rapid prototyping and production runs of varying volumes. Whether you need to work with basic materials like aluminum and plastics or more specialized materials such as titanium, CNC mills provide the versatility and reliability required for nearly any project. This adaptability makes them the ideal solution for addressing diverse manufacturing needs efficiently and effectively.






Industries We Serve
- Solid Progress
Our Manufacturing metrics
Frigate brings stability, control, and predictable performance to your sourcing operations through a structured multi-vendor system.
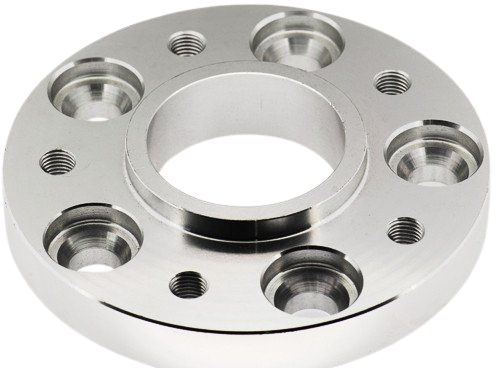
2.8X
Sourcing Cycle Speed
Frigate’s pre-qualified network shortens decision time between RFQ and PO placement.
94%
On-Time Delivery Rate
Structured planning windows and logistics-linked schedules improve project-level delivery reliability.
4X
Multi-Part Consolidation
We enable part family batching across suppliers to reduce fragmentation.
22%
Quality Rejection Rate
Multi-level quality checks and fixed inspection plans lower non-conformities.
30%
Procurement Costs
Optimized supplier negotiations and bulk order strategies reduce your overall sourcing expenses.
20%
Manual Processing Time
Automation of sourcing and supplier management significantly reduces time spent on manual tasks.
Streamlined Workflow from Prototyping to Full-Scale Production
CNC milling significantly improves workflows from prototyping to full-scale production. Initially, CNC mills quickly produce functional prototypes for testing, accelerating the development process. As demand grows, CNC milling scales efficiently to full production. This efficiency cuts turnaround times at every stage, helping companies reduce missed opportunities and adapt swiftly to market demands.

Get Clarity with our Manufacturing Insights
- Real Impact
Words from Clients
See how global OEMs and sourcing heads describe their experience with our scalable execution.
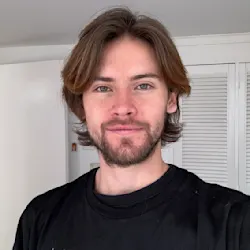
“Quick turnaround and solid quality.”
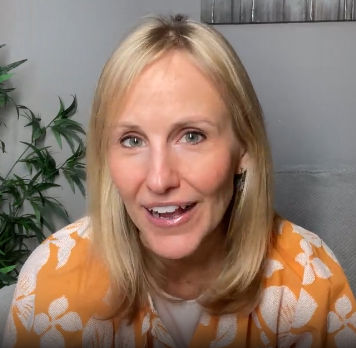
“The instant quote tool saved us time, and the parts were spot-on. Highly recommend Frigate!”
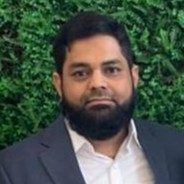
“I would strongly recommend Frigate to anyone who wants to do Rapid Prototyping, and take their ideas to manufacturing. One firm doing all kinds of Product Development!”
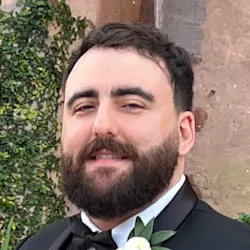
“Great service, fair price, and the parts worked perfectly in our assembly.”
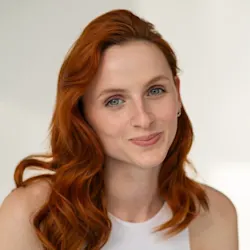
“Top-notch machining and fast shipping. Very satisfied with the results.”
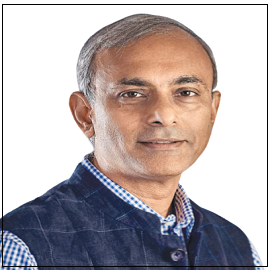
“The next disruption is happening in Prototyping & Manufacturing on-demand and Frigate is leading the way! I personally believe the Frigate's way of IIOT enabled cloud platform with Al.”
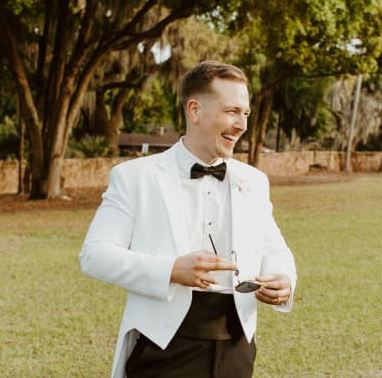
“Frigate delivered high-quality parts at a competitive price. The instant quote tool is a huge plus for us!”

“We appreciate the precision and quality of the machined components in the recent delivery—they meet our specifications perfectly and demonstrate Frigate’s capability for excellent workmanship.”
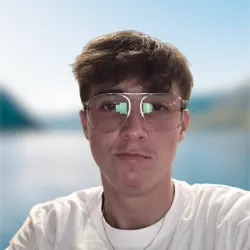
“Flawless execution from quote to delivery.”

“I am absolutely happy to work with supplier like Frigate who were quite proactive & result oriented . Frigate has high willingness team who has strong know how & their passion towards the products & process were absolutely thrilling.”
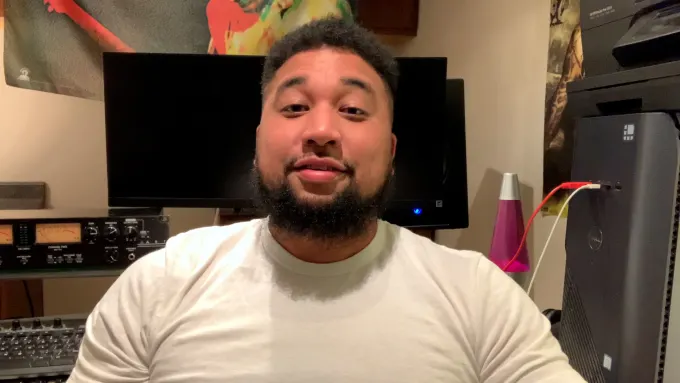
“The precision on these parts is impressive, and they arrived ahead of schedule. Frigate’s process really stands out!”
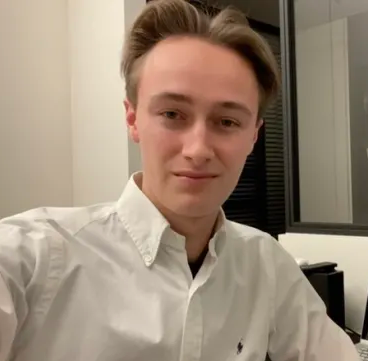
“Parts were exactly as spec’d, and the instant quote made budgeting a breeze.”
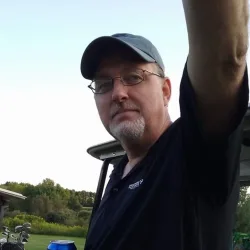
“Good value for the money.”
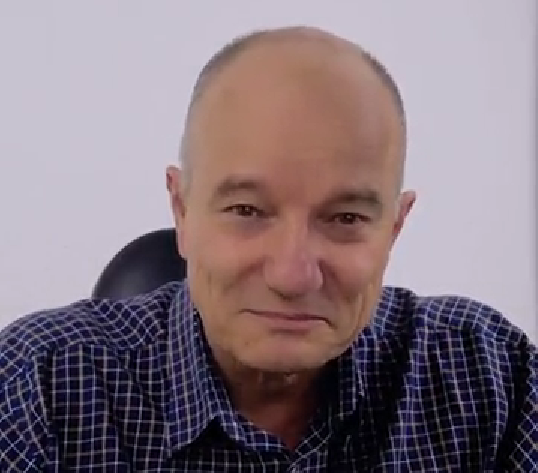
“The finish was perfect, and the team was easy to work with.”

“Working with Frigate has been great. Their proactive, results-driven approach and expertise shine through in every project. It's been a pleasure collaborating with them.”

"We are highly satisfied with the timely delivery and quality of the MIG Welding Cable from Frigate. Their attention to detail, secure packaging, and quick responsiveness stood out. We confidently recommend Frigate Engineering Services Pvt. Ltd. as a reliable manufacturing partner."
Having Doubts? Our FAQ
Check all our Frequently Asked Question
CNC milling can work with many materials, including metals like aluminum, steel, and titanium. It can also handle plastics, wood, and composites. The choice of material affects the tool used and the machining process.
Choosing the right tool is crucial. Different tools cut materials at varying speeds and with different finishes. For example, a carbide tool is great for hard metals, while high-speed steel works well for softer materials. The right tool helps achieve better accuracy and surface quality.
Feed rate is how fast the cutting tool moves through the material. A higher feed rate can speed production but may lead to less precision. On the other hand, a lower feed rate improves detail but takes more time. Finding the right balance is key to efficient milling.
CNC milling uses computer programs to control the machine's movements. This allows for precise cuts and intricate designs. The software can create complex geometries and maintain tight tolerances, ensuring that every part meets specifications accurately.
Multi-axis CNC milling machines can move in multiple directions, not just up and down. This allows cutting more complex shapes and angles without repositioning the material. It increases efficiency and reduces the time needed to complete complicated designs, leading to higher productivity.
We'd love to Manufacture for you!
Submit the form below and our representative will be in touch shortly.
LOCATIONS
Global Sales Office
818, Preakness lane, Coppell, Texas, USA – 75019
Registered Office
10-A, First Floor, V.V Complex, Prakash Nagar, Thiruverumbur, Trichy-620013, Tamil Nadu, India.
Operations Office
9/1, Poonthottam Nagar, Ramanandha Nagar, Saravanampatti, Coimbatore-641035, Tamil Nadu, India. ㅤ
Other Locations
- Bhilai
- Chennai
- Texas, USA