Drop Forging Services
Frigate’s drop forging process involves applying high-velocity hammers that deform metal under controlled strain rates. This ensures optimal mechanical properties and tight dimensional tolerances in complex geometries.
Our Clients





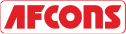

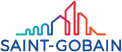


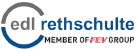

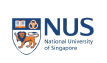
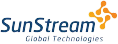

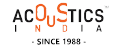




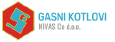
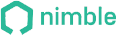
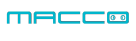












Advantages of Drop Forging with Frigate
Increased Strength
Drop forging aligns the grain structure of the metal, enhancing strength and durability compared to other forming processes. This results in stronger components.
Tight Tolerances
The drop forging process produces components with tight dimensional tolerances, reducing the need for extensive machining and ensuring precise fit and function.
Improved Impact Resistance
Components created through drop forging exhibit superior impact resistance due to the metal's refined microstructure, making them suitable for demanding applications.
Cost Efficiency
Drop forging can be more cost-effective for high-volume production, as it reduces material waste and minimizes secondary machining processes.
Solving Material Flow and Deformation Challenges
Understanding material flow and deformation behavior is essential in drop forging. It affects the final product’s quality and integrity. Controlling the forging process helps achieve the desired shape without defects. Advanced simulation techniques predict material performance under various conditions. Frigate utilizes these methods to optimize forging parameters, reducing the risk of cracking or voids. This expertise enhances mechanical properties and ensures components meet stringent specifications for reliable performance.

Get Your Quote Now
- Instant Quotation
- On-Time Delivery
- Affordable Cost
Our Drop Forging Process






The process begins with selecting the appropriate material, typically billets or bars. The choice of material affects the mechanical properties and performance of the final component.
The selected material is heated to a specific temperature, usually between 1,500 and 2,200°F. Heating improves flexibility, allowing the material to deform more easily during forging.
The heated material is placed in a die set of two halves. A high-velocity hammer or press strikes the material, forcing it to fill the die cavity and achieve the desired shape.
Once the forging operation is complete, the component is allowed to cool before being removed from the die. This cooling process can also involve controlled methods to ensure the material retains its desired properties.
After removal, excess material, such as flash or unwanted features, is trimmed off. Additional finishing processes like machining or surface treatment may be applied to achieve tight tolerances and specific surface finishes.
The final components undergo rigorous quality checks to ensure they meet specified standards. This may include dimensional inspections, mechanical property testing, and non-destructive evaluations to verify integrity and performance.
Drop Forging Materials
Drop forging utilizes high-strength metals to produce durable components with excellent integrity. This process minimizes defects and enhances performance, meeting rigorous industry standards.
Carbon steel is widely used for drop forging due to its strength and toughness. The carbon content can be adjusted to enhance properties such as hardness and flexibility. Different grades, like 4140 and 4340, provide varying mechanical properties, making carbon steel ideal for automotive and machinery components.
Alloy steels, which contain additional elements like chromium, nickel, or molybdenum, offer enhanced strength and wear resistance. These materials are often used in applications requiring high fatigue resistance and toughness. Common grades include 8620 and 9310, frequently used in gears and shafts.
It is known for its corrosion resistance and aesthetic appeal. It contains chromium and may also include nickel or molybdenum to improve durability. Grades such as 304 and 316 are often used in industries like food processing, pharmaceuticals, and marine applications where corrosion resistance is critical.
These metals are lightweight and have excellent corrosion resistance. Due to their high strength-to-weight ratio, they are often used in aerospace and automotive applications. Alloys like 7075 and 6061 provide good machinability and formability, making them suitable for complex shapes.
Titanium alloys offer an exceptional strength-to-weight ratio and outstanding corrosion resistance. These materials are often utilized in aerospace, medical, and high-performance applications. Grades like Ti-6Al-4V are commonly forged to produce lightweight, durable components that withstand extreme conditions.
Nickel alloys are designed for high-temperature applications and extreme environments. They have outstanding mechanical qualities and are resistant to corrosion and oxidation. Alloys like Inconel and Monel are often used in the aerospace and chemical processing industries for components that require exceptional performance under stress.
Excellent electrical conductivity and resistance to corrosion are two well-known qualities of copper and its alloys, which include brass and bronze. They are often used in electrical components, plumbing fittings, and decorative applications. Drop forging copper alloys allows for creating complex shapes while maintaining material integrity.
Unlocking Precision with Custom Drop Forging Solutions
Custom drop forging produces precise components to meet unique specifications. Tight tolerances are maintained while strength and durability are improved. Advanced techniques create complex geometries unattainable by standard methods. Adapting to specific requirements reduces material waste and improves efficiency. Customized components ensure reliable performance across diverse applications and withstand demanding conditions. This service enables innovative designs and optimized solutions, enhancing product functionality and longevity.

Compliance for Drop Forging Services
Our forging techniques are designed for demanding applications, including aerospace and automotive industries. We use advanced materials and state-of-the-art equipment, which ensures that all forged parts meet or exceed international standards for performance, safety, and environmental compliance. Each part is fully traceable, and we provide complete documentation of its material composition, heat treatment, and mechanical properties.
Ensures consistent product quality through rigorous quality management systems and continuous process improvement.
Sets requirements for the chemical composition and mechanical properties of materials used in drop forging.
Restricts the use of hazardous substances like lead, mercury, and cadmium in forged components.
Implements environmentally sustainable practices to minimize the ecological impact of manufacturing processes.
Confirms the safety of electrical components and systems for specific forged products used in industrial applications.
Specifies the heat treatment processes required for drop-forged aerospace materials to ensure optimal performance under stress.

Tolerance for Drop Forging Services
Ensures proper directional flow of grain for mechanical strength.
Variation in hardness across the forged part to maintain strength and durability.
Tolerance for non-uniform sections based on forging design.
Ensures smooth transitions without cracks or stress concentrators.
Roughness of the surface after forging, critical for functional fit and performance.
Tolerance for hole diameters after forging, important for precise fit during assembly.
Tolerance to maintain concentricity and proper fit in rotating components.
Ensures plates are flat to prevent deformation under stress.
Ensures length remains consistent between part ends after forging.
Controls thermal variance during the forging process to maintain material properties.
Maintains precise pressure during the final forming step for part integrity.
Variation in material hardening after forging, important for wear resistance.

Quality Testing Standards for Drop Forging Services
Measures the material's resistance to deformation during forging, indicating its workability.
Assesses the ease with which a material can be forged, considering flow characteristics and temperature.
Evaluates the thickness of oxide layers formed on the surface during forging, which could affect part quality.
Measures the uniformity of the forged material, detecting any internal voids or inclusions.
Assesses the material’s ability to maintain its strength at elevated temperatures during forging.
Evaluates the stiffness and elastic behavior of the molded part under applied loads.
Assesses the material’s ability to be welded after forging, critical for components requiring post-forging assembly.
Measures the material’s ability to deform under stress without cracking, important for parts subjected to high loads.
Ensures that hardness and material properties are uniform across different sections of the forged part.
Measures the material’s resistance to cracking or failure when exposed to thermal cycling, critical for engine components.
Assesses the material’s ability to undergo significant deformation during forging without failure.
Measures the distribution of residual stresses across the forged component, ensuring no stress concentrations that could lead to failure.
Assesses the rate of wear on forging dies and tools, which affects the quality and precision of the final part.
Driving Performance in Automotive Manufacturing
The automotive industry faces challenges like the demand for lightweight, durable components and high production costs. Upset forging addresses these issues by creating high-strength parts with exceptional dimensional accuracy, such as axles and crankshafts. This process reduces material waste while enhancing mechanical properties, supporting the trend towards lighter vehicles. Additionally, it streamlines production workflows, ensuring timely delivery of reliable components that meet performance and regulatory standards.





Industries We Serve
- Solid Progress
Our Manufacturing metrics
Frigate brings stability, control, and predictable performance to your sourcing operations through a structured multi-vendor system.
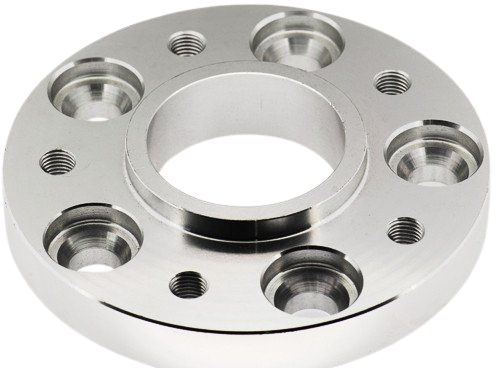
2.8X
Sourcing Cycle Speed
Frigate’s pre-qualified network shortens decision time between RFQ and PO placement.
94%
On-Time Delivery Rate
Structured planning windows and logistics-linked schedules improve project-level delivery reliability.
4X
Multi-Part Consolidation
We enable part family batching across suppliers to reduce fragmentation.
22%
Quality Rejection Rate
Multi-level quality checks and fixed inspection plans lower non-conformities.
30%
Procurement Costs
Optimized supplier negotiations and bulk order strategies reduce your overall sourcing expenses.
20%
Manual Processing Time
Automation of sourcing and supplier management significantly reduces time spent on manual tasks.
Balancing Production Rates and Quality
Balancing production rates with quality is a critical challenge in manufacturing. Buyers seek suppliers who maximize output while ensuring strict quality standards. Advanced techniques like automation and real-time monitoring enhance efficiency without sacrificing quality. Rigorous quality control, including inspections and testing, guarantees compliance with specifications. By utilizing cutting-edge technology and expertise, consistent production rates and superior quality can be achieved, effectively addressing buyer concerns.

Get Clarity with our Manufacturing Insights
- Real Impact
Words from Clients
See how global OEMs and sourcing heads describe their experience with our scalable execution.
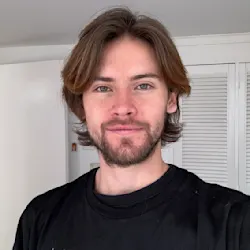
“Quick turnaround and solid quality.”
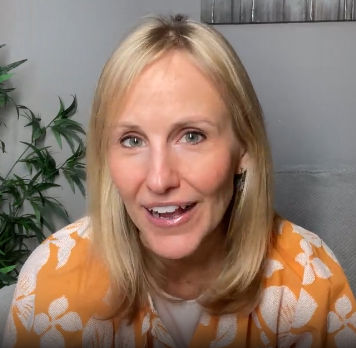
“The instant quote tool saved us time, and the parts were spot-on. Highly recommend Frigate!”
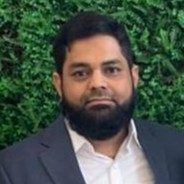
“I would strongly recommend Frigate to anyone who wants to do Rapid Prototyping, and take their ideas to manufacturing. One firm doing all kinds of Product Development!”
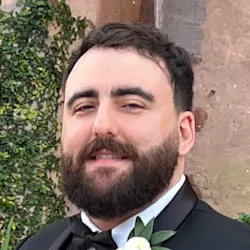
“Great service, fair price, and the parts worked perfectly in our assembly.”
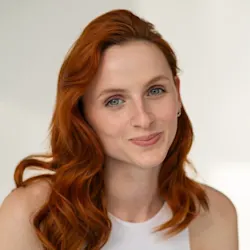
“Top-notch machining and fast shipping. Very satisfied with the results.”
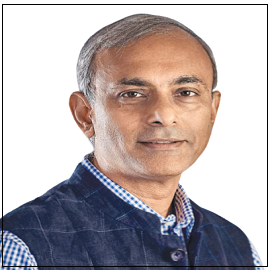
“The next disruption is happening in Prototyping & Manufacturing on-demand and Frigate is leading the way! I personally believe the Frigate's way of IIOT enabled cloud platform with Al.”
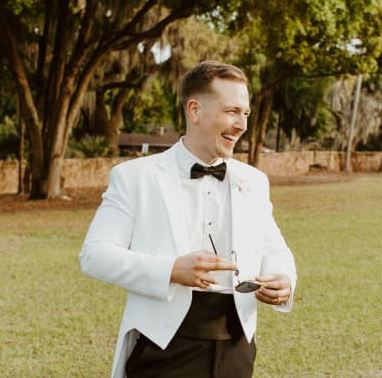
“Frigate delivered high-quality parts at a competitive price. The instant quote tool is a huge plus for us!”

“We appreciate the precision and quality of the machined components in the recent delivery—they meet our specifications perfectly and demonstrate Frigate’s capability for excellent workmanship.”
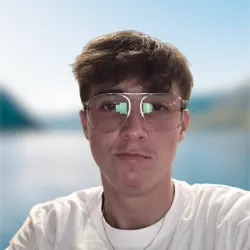
“Flawless execution from quote to delivery.”

“I am absolutely happy to work with supplier like Frigate who were quite proactive & result oriented . Frigate has high willingness team who has strong know how & their passion towards the products & process were absolutely thrilling.”
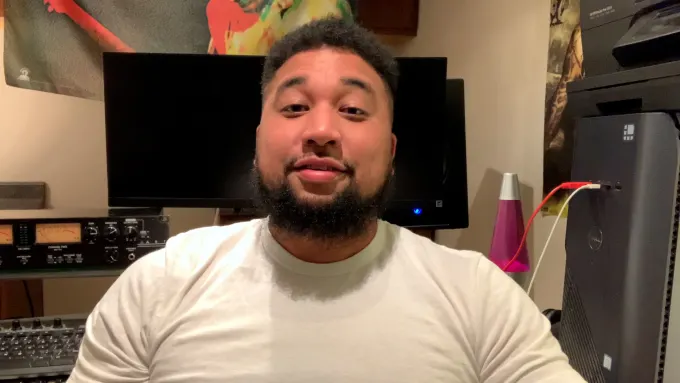
“The precision on these parts is impressive, and they arrived ahead of schedule. Frigate’s process really stands out!”
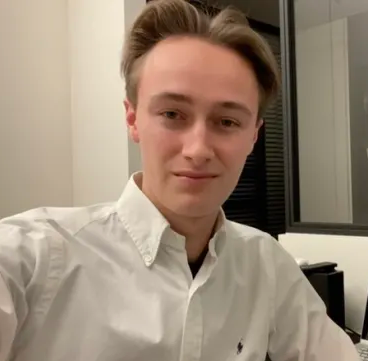
“Parts were exactly as spec’d, and the instant quote made budgeting a breeze.”
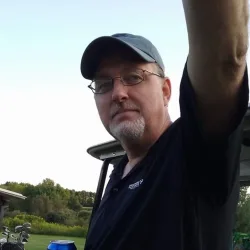
“Good value for the money.”
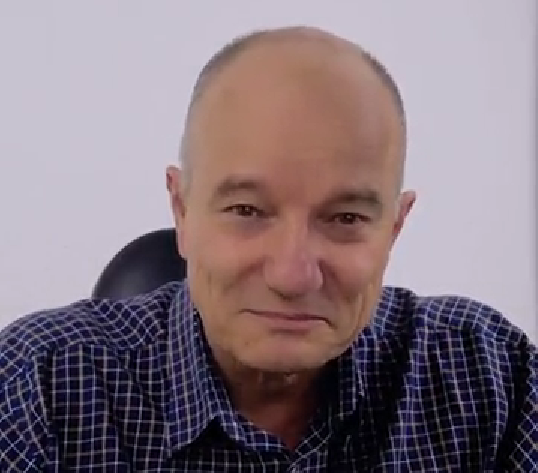
“The finish was perfect, and the team was easy to work with.”

“Working with Frigate has been great. Their proactive, results-driven approach and expertise shine through in every project. It's been a pleasure collaborating with them.”

"We are highly satisfied with the timely delivery and quality of the MIG Welding Cable from Frigate. Their attention to detail, secure packaging, and quick responsiveness stood out. We confidently recommend Frigate Engineering Services Pvt. Ltd. as a reliable manufacturing partner."
Having Doubts? Our FAQ
Check all our Frequently Asked Question
The temperature significantly influences the flexibility of the metal. Heating the metal reduces its yield strength, making it easier to deform and fill the die cavity, ensuring precise shaping without cracking.
Die design is crucial for achieving optimal material flow and minimizing waste. Properly designed dies to facilitate uniform deformation, reduce the need for secondary machining, and ensure tight tolerances in the finished components.
Adjusting the strike force and die geometry controls the material flow. Accurate control of these parameters ensures that the material fills the die, minimizing defects and enhancing mechanical properties.
Post-forging treatments may include heat treatment, surface hardening, and machining. These processes improve the mechanical properties, such as tensile strength and fatigue resistance, while achieving the required surface finish.
Upset forging involves compressing the material in one direction, allowing for thicker sections in critical areas. This technique enhances mechanical properties in specific locations, improving strength and durability in high-stress concentration applications.
We'd love to Manufacture for you!
Submit the form below and our representative will be in touch shortly.
LOCATIONS
Global Sales Office
818, Preakness lane, Coppell, Texas, USA – 75019
Registered Office
10-A, First Floor, V.V Complex, Prakash Nagar, Thiruverumbur, Trichy-620013, Tamil Nadu, India.
Operations Office
9/1, Poonthottam Nagar, Ramanandha Nagar, Saravanampatti, Coimbatore-641035, Tamil Nadu, India. ㅤ
Other Locations
- Bhilai
- Chennai
- Texas, USA