Centrifugal Casting Services
Frigate excels in centrifugal casting and finish machining high-grade ferrous and non-ferrous products. Our components are used in various applications, including steel mills, power transmission lines, and elevators. We deliver precision and durability in every cast. Trust Frigate for superior quality and performance in your industrial needs.
Our Clients





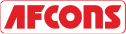

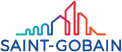


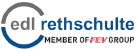

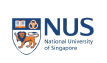
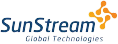

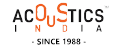




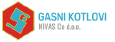
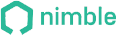
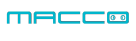












Advantages of Centrifugal Casting with Frigate
Superior Density and Strength
Centrifugal casting services produces components with a higher density and greater strength due to eliminating impurities and gas bubbles.
Enhanced Structural Integrity
The process ensures uniform grain structure, reducing the defect risk and enhancing the cast parts' overall structural integrity.
Improved Material Properties
Centrifugal casting allows for better control over the alloy composition, resulting in improved mechanical properties and increased wear resistance.
Reduced Waste
This method produces minimal waste material, making it more cost-effective and environmentally friendly.
Frigate's Approach to Centrifugal Casting
Centrifugal casting services is perfect for creating thin-walled cylinders. We use one die to produce items of the same size with different wall thicknesses. At Frigate, we work with various metals and alloys, including exotic high-strength, high-temperature materials. Precise control of metallurgy and grain structure ensures sound castings with smooth surfaces. The result? Excellent strength and toughness.

Get Your Quote Now
- Instant Quotation
- On-Time Delivery
- Affordable Cost
Our Centrifugal Casting Process






A cylindrical mold is selected or created based on the desired dimensions of the final product. These molds are typically made from steel or other durable materials to withstand high temperatures.
To avoid thermal shock when molten metal is added, the mold is prepared to a certain temperature. This step also helps achieve better surface quality and reduce defects.
Molten metal or alloy is poured into the rotating mold. The mold is spun quickly, usually on a horizontal or vertical axis. The molten metal is forced up against the mold's inner walls by the centrifugal force created by this spinning.
As the mold spins, the centrifugal force ensures that the molten metal fills the cavity uniformly, forming a dense and homogenous casting. Any impurities or inclusions are pushed towards the center, where they can be machined out later.
Once the metal has fully solidified, the mold is stopped, and the casting can cool further. The casting is then ejected from the mold.
To get the final specifications and intended qualities, the cast part is put through a variety of finishing procedures, including machining, heat treatment, and surface treatments.
Post-Processing Services in Centrifugal Casting
Centrifugal casting delivers high-quality metal components, but post-processing is essential to enhance strength, precision, and durability. Advanced heat treatment, machining, surface finishing, and coatings ensure components meet industry standards.
Automotive (engine sleeves), Aerospace (turbine rings)
Tolerance: ±0.005 mm
Surface Finish: Ra 0.4-3.2 µm
Oil & Gas (pipes, fittings), Marine (propeller sleeves)
Shot Peening (Almen intensity: 0.15-0.6 mmA)
Polishing (Ra 0.2-1.0 µm)
Defense (gun barrels), Medical (implants)
Power Generation (turbine casings), Railway (axle hubs)
Aerospace (landing gear), Automotive (brake drums)
Chemical (reactor linings), Marine (corrosion protection)
Hold time: 1 hour per 25 mm thickness
Cooling rate: 50-100°C/hr
Heavy Machinery (rollers), Oil & Gas (pump casings)
Methoding in Centrifugal Casting
Aerospace (jet engine rings), Automotive (cylinder liners)
Oil & Gas (drill collars), Power (rotor casings)
Marine (propeller hubs), Nuclear (reactor components)
Heavy Machinery (rollers), Mining (crusher rings)
Automotive (brake drums), Railway (axle hubs)
Energy (turbine casings), Chemical (reactor vessels)
Defense (missile casings), Aerospace (hollow shafts)
Power (generator housings), Industrial (pump impellers)
Foundry (steel pipes), Marine (shaft sleeves)
Automotive (engine blocks), Hydropower (turbine bearings)

Centrifugal Casting Materials
Our expertise in metallurgy and grain structure control guarantees that each casting we produce has the strength, durability, and precision our clients expect.
Known for its durability and versatility, carbon steel is a fundamental choice for many applications. It provides a good balance of strength and toughness, making it suitable for various industrial uses.
Offering excellent corrosion resistance and strength, stainless steel is ideal for environments that require high durability and cleanliness. It's commonly used in the food, pharmaceutical, and chemical industries.
Alloy steel includes a variety of metals that enhance its mechanical properties. These steels are ideal for demanding applications because of their exceptional strength, toughness, and wear resistance.
Alloys, such as bronze and brass, are valued for their excellent electrical & thermal conductivity and resistance to corrosion. They are often used in electrical components and plumbing fixtures.
They are renowned for their ability to withstand high temperatures and corrosive environments. They are often used in aerospace, chemical processing, and power generation industries.
Lightweight and highly machinable, aluminum is a popular choice where weight reduction is crucial. It also offers good corrosion resistance and excellent thermal and electrical conductivity.
Titanium is well known for having a high strength-to-weight ratio and an outstanding resistance to corrosion. It's used in aerospace, medical implants, and marine applications where performance and longevity are critical.
Superalloys are designed to maintain strength and stability at extremely high temperatures. They are essential in aerospace, gas turbines, and other high-performance industries.
Custom Centrifugal Casting Solutions at Frigate
Centrifugal casting allows us to create pieces tailored to each part’s needs. Without cores, we can produce items of any length, thickness, or diameter. This method ensures parts have rotational symmetry due to gravity, resulting in seamless and large-size components. The production cost is low because molds can be reused for parts with varying wall thicknesses. This casting is less appropriate for pieces that need unique shapes because it is usually used to make stock materials. Only cylindrical shapes can be made, and there may be a considerable wait time.

Compliance for Centrifugal Casting Services
Frigate adheres to the highest industry standards for Centrifugal Casting, ensuring products meet all necessary technical and safety specifications. Our centrifugal casting processes follow rigorous material and production requirements to achieve exceptional strength, precision, and durability. We maintain certifications from globally recognized bodies, guaranteeing that each component we produce fully complies with all regulatory and environmental standards.
Standard Specification for Wear-Resistant Cast Irons, ensuring high material quality and wear resistance.
Quality Management Systems certification for consistent and high-quality manufacturing practices.
Environmental Management certification, ensuring compliance with global environmental standards.
Compliance with the European Union regulation for the safe use of chemicals and materials.
Restriction of Hazardous Substances directive for environmental safety in electronic components.
Aerospace Quality Management System certification, meeting the aerospace industry's stringent requirements for safety and quality.
Accreditation for aerospace and defense processes, ensuring consistent quality in high-performance castings.
Compliance with Occupational Safety and Health Administration regulations to maintain safe working conditions.
Tonnage / Capacity in Centrifugal Casting
Centrifugal casting is used to produce high-strength, defect-free components across various industries. The casting capacity depends on mold size, rotational speed, and metal flow dynamics.
Aerospace (turbine rings), Marine (propeller hubs)
Oil & Gas (drill pipes), Power (turbine casings)
Heavy Machinery (rollers), Defense (barrel sleeves)
Automotive (brake drums), Railway (axle hubs)
Industrial (pump casings), Energy (nuclear components)
Foundry (steel pipes), Chemical (reactor vessels)
Aerospace (hollow shafts), Automotive (cylinder liners)
Oil & Gas (valve bodies), Mining (crusher rings)
Power Generation (generator housings), Marine (shafts)
Dimensions in Centrifugal Casting
Centrifugal casting enables the production of precision-engineered components with high structural integrity. The dimensions of cast parts depend on mold design, rotational speed, and material properties.
Aerospace (turbine rings), Oil & Gas (drill collars)
Marine (shaft sleeves), Power (rotor casings)
Heavy Machinery (rollers), Defense (gun barrels)
Railway (axle hubs), Industrial (pump casings)
Energy (turbine casings), Mining (crusher rings)
Automotive (brake drums), Marine (propeller hubs)
Power (generator housings), Oil & Gas (cylinder liners)
Chemical (reactor vessels), Foundry (steel pipes)
Aerospace (hollow shafts), Automotive (engine liners)

Tolerance for Centrifugal Casting Services
Precision tolerance for diameters, lengths, and overall dimensions, ensuring tight fits and assembly.
Variations in wall thickness that ensure consistent material strength and structural integrity.
Deviation from the ideal concentric alignment between the inner and outer diameters to ensure proper fit in assemblies.
Circularity tolerance affecting rotational performance and sealing applications.
Measurement of the surface roughness, critical for friction, corrosion resistance, and visual quality.
Deviation from a straight line, ensuring optimal assembly and functionality.
Hardness tolerance that affects wear resistance and material strength, crucial for high-stress environments.
Weight variation tolerance, ensuring consistent material distribution and density for uniform performance.
Tolerance for the variation in radial thickness across the casting, ensuring uniform strength and material properties.
Deviation in core placement, affecting internal geometry and fluid flow in applications like pumps or pipes.
Tolerance for the porosity level, affecting structural integrity and material strength.
Tolerance for casting defects, ensuring minimal impact on the structural performance and aesthetics.
Precision in the internal diameter to ensure proper assembly with other components, especially in pipe fittings and bearings.
Tolerance for material shrinkage during cooling, ensuring dimensional consistency and fitting precision.
Allowance for thermal expansion, critical for high-temperature applications such as exhaust systems.
Standard for ensuring uniform distribution of grains in high-performance castings, improving mechanical properties.
Deviation from a perpendicular angle between surfaces, important for assembly and function in geometrically critical parts.
Specific tolerance for vibration absorption, vital in high-performance applications like engine components.

Quality Testing Standards for Centrifugal Casting Services
Ensures the casting dimensions, including diameters, lengths, and wall thicknesses, are within specified tolerances.
Verifies proper bonding between different layers of material in multi-layer castings to prevent delamination.
Measures the thermal conductivity of the material, ensuring that castings perform optimally under heat-exposed conditions.
Provides detailed hardness measurements across the surface, ensuring material consistency and strength.
Measures casting density and checks for internal porosity, ensuring the material integrity and strength are not compromised.
Measures the casting's ability to resist deformation under prolonged stress, crucial for high-temperature applications.
Measures dimensional changes during solidification to anticipate and compensate for shrinkage during cooling.
Analyzes the distribution of stress within the casting, ensuring uniformity and preventing failure under operational loads.
Quantifies the concentration of alloying elements to confirm compliance with material specifications and desired properties.
Examines the casting's grain structure, assessing grain size, shape, and distribution to ensure material strength and uniformity.
Evaluates casting’s ability to withstand repeated loading conditions, crucial for parts subjected to dynamic forces.
Simulates environmental stress, ensuring castings perform under varying temperature and moisture conditions.
Detects casting defects like cracks, voids, or inconsistent material flow, ensuring a high level of casting integrity.
Measures the yield strength, providing information about the material’s ability to resist permanent deformation under stress.
Assesses the material’s ability to conduct magnetic fields, important for applications in motors, transformers, and sensors.
Evaluates the casting's resistance to corrosion in salt-laden environments, crucial for automotive and marine applications.
Ensures that castings used in electronics or aerospace applications meet electromagnetic compatibility standards.
Inspection Techniques in Centrifugal Casting
Value/Range - 0.5 mm – 300 mm depth penetration
Aerospace (turbine rings), Oil & Gas (drill collars)
Value/Range - Resolution up to 0.01 mm
Nuclear (reactor components), Automotive (cylinder liners)
Sensitivity: 0.1 mm defect size
Railway (axle hubs), Marine (propeller shafts)
Value/Range - Crack width ≥ 0.01 mm
Power (generator housings), Industrial (pump casings)
Depth: Up to 6 mm
Defense (missile casings), Aerospace (hollow shafts)
Value/Range - ±0.01 mm precision
Automotive (brake drums), Energy (turbine casings)
Value/Range - 100 – 700 HB, 20 – 70 HRC
Mining (crusher rings), Foundry (steel pipes)
Resolution: 0.1 µm
Chemical (reactor vessels), Hydropower (turbine bearings)
Tensile Strength: 300 – 1500 MPa
Heavy Machinery (rollers), Oil & Gas (valve bodies)
Value/Range - ±0.005 mm tolerance
Aerospace (engine rings), Automotive (engine blocks)


Industry Applications of Centrifugal Casting
Jet turbine rings, Missile casings, Exhaust nozzles
Reactor core components, Steam generator tubing
Drill risers, Pipeline connectors, Fracking components
Orthopedic implants, Medical centrifuge bowls
Wafer processing chambers, Vacuum pump rotors
Turbine shafts, Hydro-generator bearings
High-speed train brake discs, Suspension components
Submarine propulsion components, Ship rudder bearings
LNG storage tank linings, Cryogenic pump casings
Continuous casting rolls, Induction furnace liners
Unlock the Advantages of Centrifugal Casting with Frigate
Our centrifugal casting services offers a range of benefits that enhance your project’s outcomes. This method produces cast parts with finely compacted metal grains, resulting in superior strength and corrosion resistance. This not only improves machining and finishing but also reduces rejection rates.
Our process integrates seamlessly with automation, allowing precise control over molten metal preparation, pouring speed, and mold rotation, which ensures consistent, high-quality castings. Additionally, centrifugal casting’s versatility enables the production of symmetrical castings in various diameters and lengths, exhibiting excellent mechanical properties. Trust Frigate to leverage these advantages for reliable, high-performance components tailored to your needs.





Industries We Serve
- Solid Progress
Our Manufacturing metrics
Frigate brings stability, control, and predictable performance to your sourcing operations through a structured multi-vendor system.
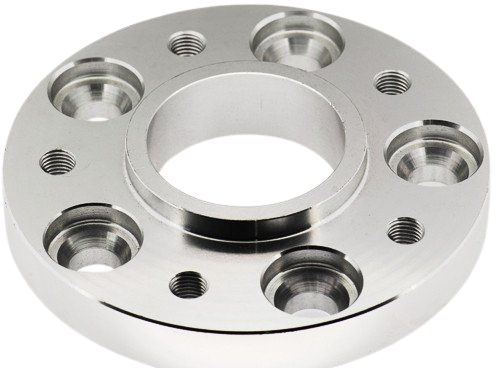
2.8X
Sourcing Cycle Speed
Frigate’s pre-qualified network shortens decision time between RFQ and PO placement.
94%
On-Time Delivery Rate
Structured planning windows and logistics-linked schedules improve project-level delivery reliability.
4X
Multi-Part Consolidation
We enable part family batching across suppliers to reduce fragmentation.
22%
Quality Rejection Rate
Multi-level quality checks and fixed inspection plans lower non-conformities.
30%
Procurement Costs
Optimized supplier negotiations and bulk order strategies reduce your overall sourcing expenses.
20%
Manual Processing Time
Automation of sourcing and supplier management significantly reduces time spent on manual tasks.
Centrifugal Casting Services for Automotive Excellence
We understand the demands of the automotive industry for precision and durability. Our centrifugal casting services are designed to meet these needs by producing metal parts with exceptional accuracy and superior surface finish. We specialize in creating components with intricate designs and thin wall sections crucial for automotive applications. Our process ensures high dimensional precision and excellent purity, translating to reliable performance and reduced production costs.

Get Clarity with our Manufacturing Insights
- Real Impact
Words from Clients
See how global OEMs and sourcing heads describe their experience with our scalable execution.
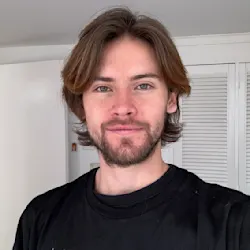
“Quick turnaround and solid quality.”
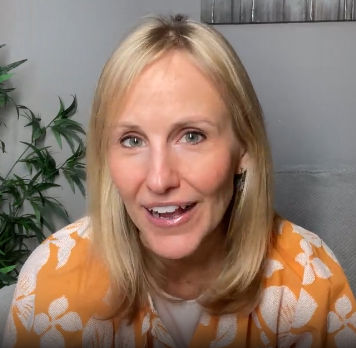
“The instant quote tool saved us time, and the parts were spot-on. Highly recommend Frigate!”
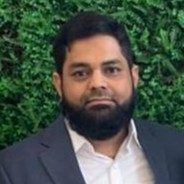
“I would strongly recommend Frigate to anyone who wants to do Rapid Prototyping, and take their ideas to manufacturing. One firm doing all kinds of Product Development!”
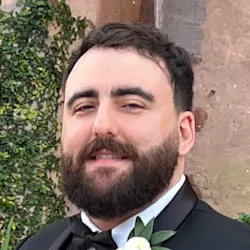
“Great service, fair price, and the parts worked perfectly in our assembly.”
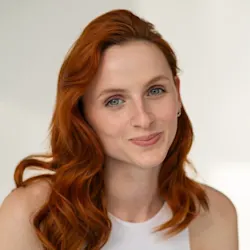
“Top-notch machining and fast shipping. Very satisfied with the results.”
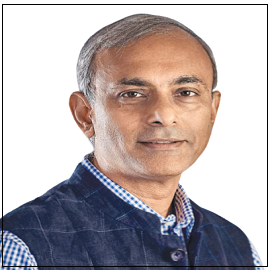
“The next disruption is happening in Prototyping & Manufacturing on-demand and Frigate is leading the way! I personally believe the Frigate's way of IIOT enabled cloud platform with Al.”
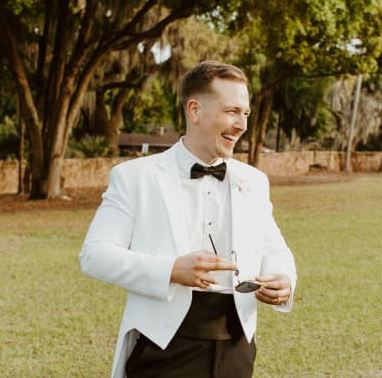
“Frigate delivered high-quality parts at a competitive price. The instant quote tool is a huge plus for us!”

“We appreciate the precision and quality of the machined components in the recent delivery—they meet our specifications perfectly and demonstrate Frigate’s capability for excellent workmanship.”
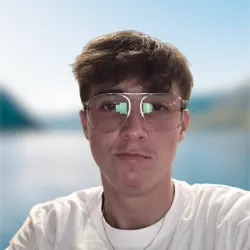
“Flawless execution from quote to delivery.”

“I am absolutely happy to work with supplier like Frigate who were quite proactive & result oriented . Frigate has high willingness team who has strong know how & their passion towards the products & process were absolutely thrilling.”
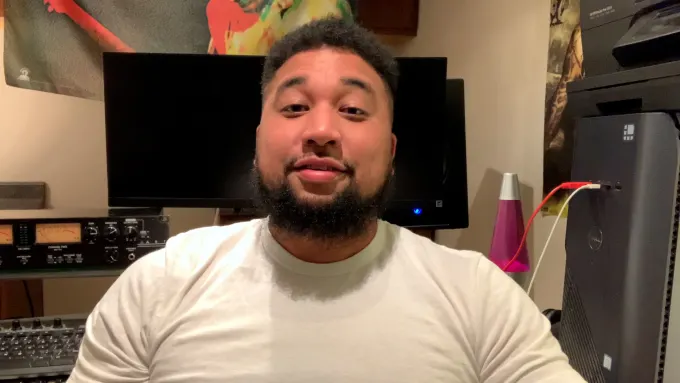
“The precision on these parts is impressive, and they arrived ahead of schedule. Frigate’s process really stands out!”
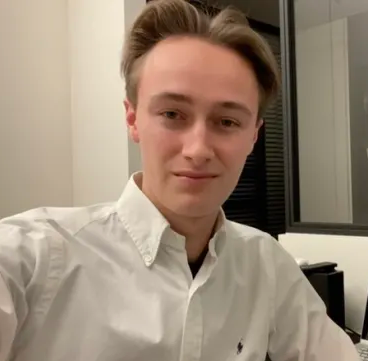
“Parts were exactly as spec’d, and the instant quote made budgeting a breeze.”
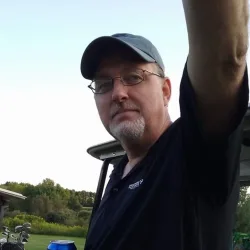
“Good value for the money.”
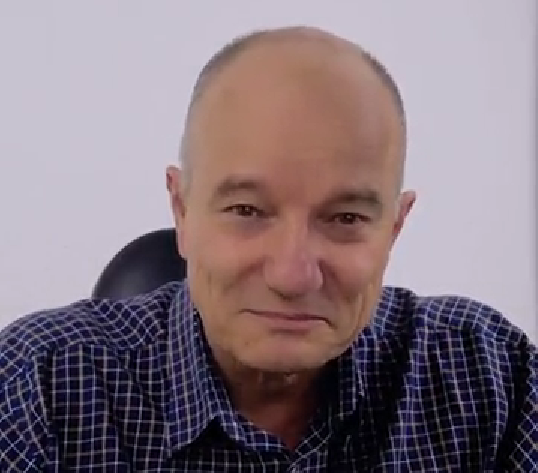
“The finish was perfect, and the team was easy to work with.”

“Working with Frigate has been great. Their proactive, results-driven approach and expertise shine through in every project. It's been a pleasure collaborating with them.”

"We are highly satisfied with the timely delivery and quality of the MIG Welding Cable from Frigate. Their attention to detail, secure packaging, and quick responsiveness stood out. We confidently recommend Frigate Engineering Services Pvt. Ltd. as a reliable manufacturing partner."
Having Doubts? Our FAQ
Check all our Frequently Asked Question
Centrifugal force helps to push molten metal against the mold wall during casting. This force creates a strong, dense material and reduces the chances of defects like porosity. The faster the mold spins, the greater the force, which improves the quality of the final product.
The cooling rate in centrifugal casting is crucial. Faster cooling can lead to finer grain structures, which enhance strength and hardness. Slower cooling can result in larger grains, affecting toughness. Controlling the cooling rate helps achieve the desired material properties for specific applications.
Centrifugal casting uses two main types of molds: permanent and expendable. Permanent molds are metal and can be reused, while expendable molds are made from materials like sand. The choice of mold affects the surface finish and dimensional accuracy. Metal molds generally provide better precision.
The viscosity of molten metal affects how well it fills the mold. Low-viscosity metals flow easily, ensuring complete mold filling and better details. High-viscosity metals may struggle to fill the mold, leading to defects. Selecting the right metal and temperature is essential for a successful casting.
Because of the centrifugal force, centrifugal casting is effective for creating complex shapes and thin-walled components. As the mold spins, the molten metal helps fill intricate details. This method allows for precise control over wall thickness, making it ideal for parts like pipes and tubes.
We'd love to Manufacture for you!
Submit the form below and our representative will be in touch shortly.
LOCATIONS
Global Sales Office
818, Preakness lane, Coppell, Texas, USA – 75019
Registered Office
10-A, First Floor, V.V Complex, Prakash Nagar, Thiruverumbur, Trichy-620013, Tamil Nadu, India.
Operations Office
9/1, Poonthottam Nagar, Ramanandha Nagar, Saravanampatti, Coimbatore-641035, Tamil Nadu, India. ㅤ
Other Locations
- Bhilai
- Chennai
- Texas, USA