When it comes to large, complex projects, precision and accuracy are critical. Companies often face challenges in finding the right solutions to manufacture large components that require tight tolerances. This is especially true in aerospace, energy, and automotive industries, where even the smallest error can lead to significant delays, added costs, and safety issues. These industries demand parts that are not only massive but also need to fit perfectly within assemblies or machines. Traditional machining methods often fail to meet these demands.
This is where large CNC machining services come in, providing the perfect solution for large-scale, intricate parts. With advanced technology and specialized machines, these services allow companies to get high-quality, precise components, no matter how big the project. Let’s dive into the technical details of how large CNC machining services offer the precision and efficiency needed for these projects.
How Large CNC Machining Solves Major Project Challenges
Before diving into the technical detailing, it’s important to understand why large CNC machining services are essential for big projects. Many industries face common challenges, such as maintaining precision on large parts, handling complex designs, working with tough materials, and meeting tight deadlines.
Traditional machining methods often struggle with these issues. Large parts are hard to machine accurately, complex geometries require specialized tools, and materials like titanium or stainless steel can be difficult to work efficiently.
Large CNC machining services use advanced machinery, precision software, and automation to solve these problems. They offer the accuracy, flexibility, and efficiency needed to easily handle large-scale, complex components. Now, let’s explore the capabilities that make this possible.
Capabilities of Large CNC Machines
Large CNC machines are designed to handle oversized workpieces that would be impossible for standard machines. These machines often come with multi-axis configurations, such as 5-axis machining, which allows for machining complex geometries in a single setup. With axis movements that cover vast areas, large CNC machines can work on parts that measure several meters in length and width.
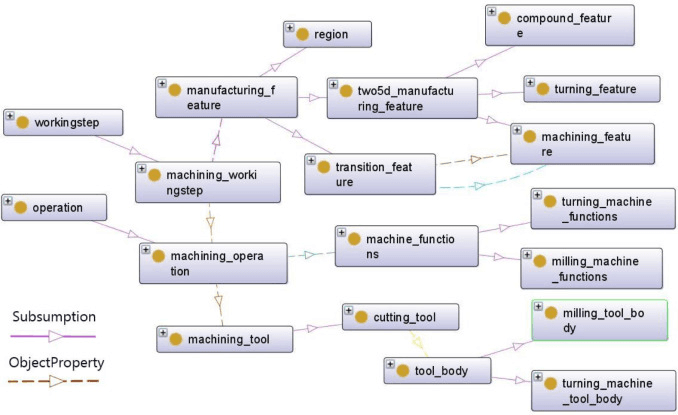
For instance, horizontal and vertical milling machines are commonly used in large CNC machining services. Horizontal machines offer stability when working on larger parts, while vertical machines allow flexibility in cutting angles. These machines use CAD/CAM software to generate precise tool paths, ensuring that even the most intricate cuts are handled accurately.
Handling Complex, Large Parts: Precision Meets Scale
One of the biggest challenges in large projects is maintaining precision while scaling up. Large components, such as turbine blades, ship parts, or aerospace fuselage pieces, must be machined with extreme accuracy. Even a minor measurement error can result in parts that don’t fit together, leading to costly repairs or delays.
Large CNC machining services excel at maintaining tight tolerances on massive parts. These machines can machine within microns, ensuring that the final product fits perfectly within the assembly. For example, a 20-meter-long wind turbine blade may have sections requiring millimeter-perfect cuts. The machine’s advanced control systems ensure that every cut is made with precision, regardless of the size of the part.
A company manufacturing aerospace components needed precision milling of a 10-meter-long fuselage. Using large CNC machines, the company achieved tight tolerances, reducing assembly errors and improving overall product quality.
Material Versatility for Large CNC Machining
Handling big projects requires working with a wide variety of materials. In industries like aerospace and energy, parts are often made from high-strength alloys, stainless steel, titanium, or composite materials. Each material has different properties, such as strength, heat resistance, and hardness, which present unique machining challenges.
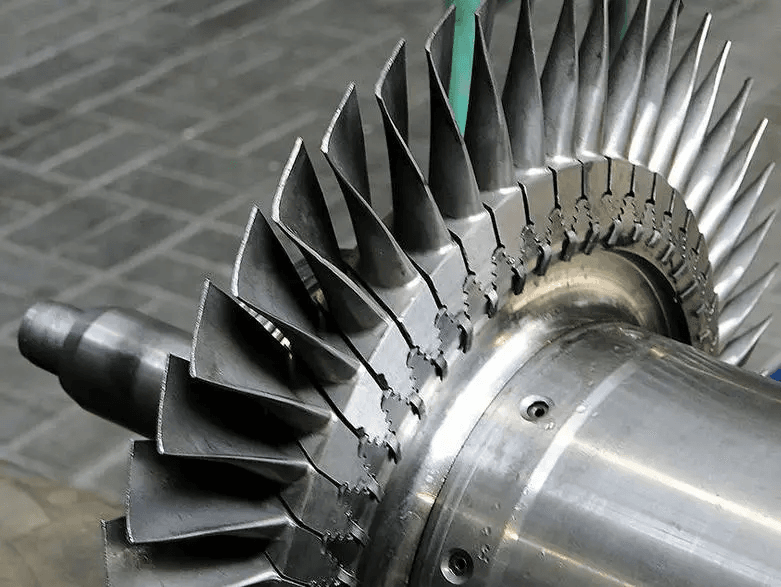
Large CNC machining services are equipped to handle these materials with precision. For example, titanium is known for its high strength-to-weight ratio, but it is also difficult to machine due to its tendency to heat up during cutting. CNC machines use specialized cooling systems and high-speed tools to ensure that titanium components are machined without losing structural integrity.
Similarly, stainless steel, commonly used in heavy industries, requires precise cutting tools to avoid tool wear and ensure smooth finishes. CNC machines are programmed to adjust feed rates and cutting speeds based on the material properties, ensuring optimal performance.
Efficiency and Turnaround for Large Projects
In big projects, time is often of the essence. Delays in component manufacturing can cause entire production lines to stall, leading to missed deadlines and increased costs. One key benefit of large CNC machining services is their ability to significantly reduce lead times for large projects.
Large CNC machines are designed for efficiency. They often feature multi-tasking capabilities, allowing for multiple operations, such as drilling, milling, and turning, to be performed in one setup. This reduces the need for multiple machine setups and shortens production time. Additionally, advanced machines support “lights-out” machining, where the machine operates unattended, even overnight, further speeding up the process.
Quality Control in Large CNC Machining
Quality control is critical for large-scale projects. Even the smallest deviation from the design can result in parts that don’t meet industry standards. Large CNC machining services ensure quality by incorporating advanced inspection technologies, including Coordinate Measuring Machines (CMM) and laser scanning.
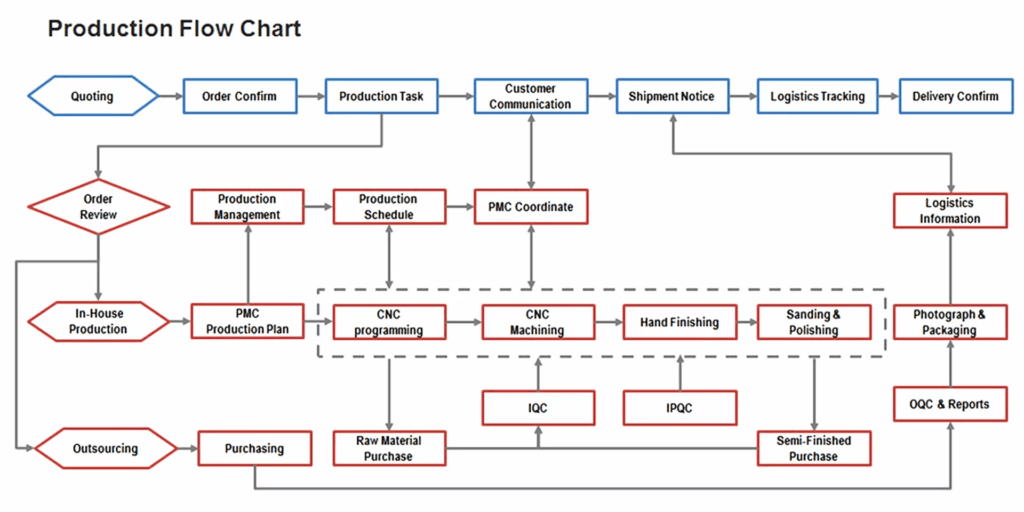
These tools inspect parts for dimensional accuracy, surface finish, and quality. For example, CMMs use precise probes to measure the geometry of machined parts down to the micron level. Laser scanning allows for non-contact measurement, which is particularly useful for complex geometries. These technologies ensure that every part meets the required specifications before it leaves the workshop.
Key Industries Benefiting from Large CNC Machining
Many industries rely on Large CNC machining services to produce their essential components. Some of the key industries include:
- Aerospace: Large CNC machines manufacture fuselages, wings, and engine components, all of which require precision and durability.
- Energy: In the energy sector, large CNC machines are used to produce wind turbine blades, nuclear power plant components, and oil rig parts.
- Automotive: Large CNC machining services are essential in the automotive industry for producing engine blocks, frames, and other large components.
- Construction and Heavy Equipment: Construction projects often require large, heavy-duty parts, such as crane components and excavator arms, machined with precision using large CNC equipment.
The global demand for CNC machining in the aerospace and defense sector is expected to grow by 6.5% annually, highlighting the increasing reliance on precision machining.
Saving Money on Big Projects
One of the biggest advantages of using large CNC machining services is the cost efficiency they provide. While the initial setup for CNC machining might be expensive, the overall cost savings are significant in the long run. This is especially true for large projects where material waste, manual labor, and post-production processes are minimized.
CNC machines reduce material waste using precision cutting techniques that only remove the necessary material. This saves on raw material costs and ensures that the final product requires minimal post-processing. Additionally, the automation of CNC machines reduces the need for manual labor, further lowering production costs.
A manufacturer switched to large CNC machining to produce turbine blades and reduced their material waste by 20%, saving thousands of dollars on raw material costs.
Choosing the Right Large CNC Machining Partner
Selecting the right partner for large CNC machining services is critical to the success of any big project. Companies should look for a machining service provider with experience, advanced equipment, and a proven track record of delivering high-quality parts on time. It is also essential to choose a provider that can handle both one-off custom parts and high-volume production runs.
A good partner will offer technical support throughout the project, helping with design optimizations, material selection, and ensuring the final product meets all specifications. Working with an experienced provider will improve the quality of your parts and reduce lead times and overall project costs.
Conclusion
The future of large CNC machining is bright, with advancements in technology making it easier and faster to handle big projects with precision. Working with the right machining partner is crucial if your company needs high-quality, large-scale components. Frigate offers state-of-the-art Large CNC machining services that guarantee precision, efficiency, and quick turnaround times. Whether you’re in aerospace, energy, or construction, we have the expertise and equipment to deliver components that meet your exact specifications.
Contact Frigate today to learn how we can help you complete your next big project with precision and efficiency!