CNC machined shafts, custom shafts, and precision industrial parts are critical for ensuring machine performance, stability, and durability. These shafts are commonly used in aerospace, automotive, robotics, and heavy machinery, where precision is essential.
Even minor deviations in shaft dimensions can lead to imbalance, vibration, or mechanical failure. Research shows that misalignment in rotating shafts is responsible for over 50% of bearing failures in industrial machines. Selecting a supplier with strong technical capabilities is crucial for minimizing these risks.
To ensure CNC machined shafts meet design standards, it’s important to understand shaft types, technical challenges, and key supplier evaluation factors.
What Are Different Types of Shafts and Their Applications?
Shaft types vary based on their function, material properties, and design complexity. Each type demands specialized machining techniques to achieve the desired performance, precision, and durability. Below are key shaft types used in various industries and how Frigate ensures their quality.
Transmission Shafts
Transmission shafts are used in gearboxes, industrial drives, and conveyors to transfer torque. Precise alignment is crucial to prevent vibration and wear. Frigate manufactures CNC machined transmission shafts with pitch diameter accuracy within ±0.005 mm for smooth power transfer. Techniques like spline cutting and gear machining ensure precise profiles, while induction hardening enhances strength for improved load capacity and durability.
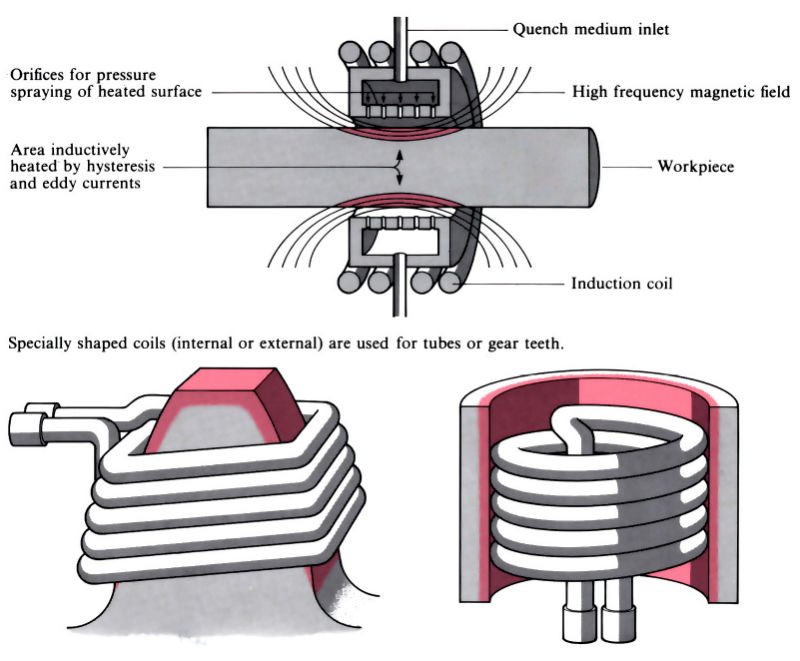
Spindle Shafts
Spindle shafts are essential in CNC machines, drills, and milling equipment. They require precise concentricity to avoid vibration during high-speed rotation. Frigate ensures spindle shafts meet ±0.002 mm concentricity tolerance with surface roughness values below Ra 0.2 µm. Advanced grinding and polishing techniques ensure friction-free motion, improving accuracy and extending shaft life.
Axle Shafts
Axle shafts are used in vehicles and heavy machinery to transmit torque while handling heavy loads. Precise diameter control is essential for proper bearing fit and rotation. Frigate manufactures CNC machined axle shafts with diameter tolerances within ±0.01 mm. Frigate applies induction hardening to improve wear resistance, achieving surface hardness up to 60 HRC for an extended lifespan.
Camshafts and Crankshafts
Camshafts and crankshafts control engine timing and piston movement. These shafts require precise profiles for accurate performance. Frigate ensures profile tolerances within ±0.01° using CNC grinding. Advanced finishing methods like superfinishing improve surface quality, reducing friction and enhancing durability in high-speed applications.
Linear Motion Shafts
Linear motion shafts guide precise movement in CNC machines and automation systems. Any deviation in straightness can reduce positioning accuracy. Frigate manufactures CNC machined linear shafts with straightness tolerances within ±0.01 mm per meter. Finishing techniques like honing and polishing ensure smooth motion and reduced friction for reliable performance.
What Are the Challenges in Buying High-Precision CNC Machined Shafts?
Industries that require CNC machined shafts, custom shafts, and precision industrial parts often face technical challenges affecting product performance and durability. Overcoming these challenges requires advanced machining techniques, strict quality control, and expertise in material science. Below are key challenges and how Frigate addresses them with high-level technical solutions.
Material Certification and Metallurgical Integrity
Material quality plays a vital role in shaft performance. CNC machined shafts often operate under extreme conditions, requiring materials with high tensile strength, heat resistance, and fatigue life. Low-quality materials may crack under stress or deform at high temperatures. Frigate ensures material reliability by sourcing certified alloys that meet industry standards, such as ASTM A29, AMS 6415, and DIN EN 10277.
Frigate conducts spectrographic analysis to confirm material integrity, ensuring precise alloy composition and chemical stability. For defect detection, ultrasonic testing (UT) is performed at frequencies up to 5 MHz, capable of identifying internal cracks or voids as small as 0.5 mm. Each shaft also undergoes hardness testing to confirm mechanical strength. For enhanced surface durability, Frigate applies case hardening to depths of up to 3 mm, ensuring surface hardness values exceeding 60 HRC without compromising the shaft’s core strength.
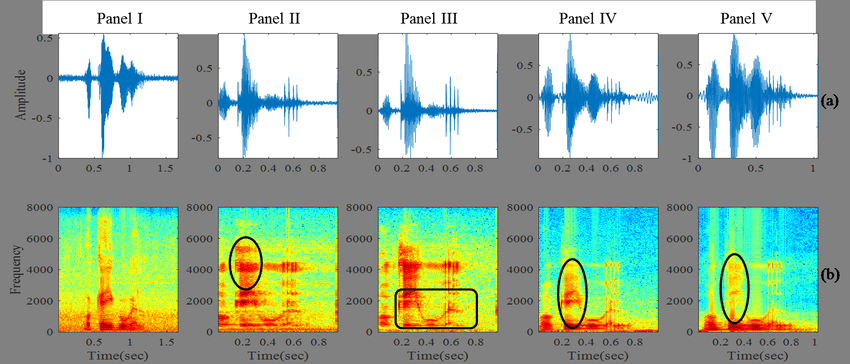
Precision Tolerances and Profile Consistency
Achieving precise dimensions is crucial for CNC machined shafts to ensure accurate alignment and stable operation. A deviation of 0.005 mm can cause vibration, bearing wear, or misalignment in rotating systems. Frigate addresses this using 5-axis CNC machining centers equipped with linear scales capable of measuring movements in increments as small as 0.0001 mm.
To maintain profile accuracy, Frigate’s CNC machines feature in-process probing systems that measure shaft dimensions directly during machining, ensuring errors are corrected in real-time. Frigate employs cylindrical grinding for critical diameter tolerances with runout control maintained within 2 µm, ensuring concentricity and uniform profile accuracy across the shaft length.
Surface Integrity and Fatigue Resistance
Surface finish is crucial for CNC machined shafts, as rough or uneven surfaces can create stress points that accelerate fatigue failure. Frigate ensures exceptional surface quality using diamond grinding wheels with grit sizes as fine as D3 (3 µm) to achieve surface roughness values below Ra 0.1 µm.
Frigate applies shot peening to improve fatigue resistance, which introduces controlled compressive stress on the shaft’s surface. This process enhances fatigue strength by up to 30% by reducing micro-cracks risk. For shafts requiring high surface hardness, Frigate performs plasma nitriding, diffusing nitrogen to depths of up to 0.5 mm and achieving hardness levels between 800–1200 HV.
Thermal Stability and Dimensional Control
Shafts exposed to elevated temperatures often face dimensional instability due to material expansion. Thermal distortion can alter shaft dimensions, compromising alignment and overall performance. Frigate addresses this by applying stress-relief annealing, where shafts are heated to 600–700°C before final machining to stabilize their structure.
Frigate performs cryogenic treatment for enhanced dimensional stability, cooling shafts to -196°C to refine the material’s microstructure and minimize internal stress. Controlled heat treatment ovens with temperature stability within ±3°C ensure hardness profiles remain uniform, minimizing distortion. These processes ensure CNC machined shafts retain precise dimensions even after prolonged exposure to high temperatures.
Dynamic Balancing and Vibration Control
Even minor imbalances in CNC machined shafts can generate excessive vibration, causing noise, mechanical wear, and bearing failure. This is especially critical in systems operating above 10,000 RPM. Frigate ensures optimal balance using dynamic balancing machines equipped with laser sensors to detect imbalance points with accuracy down to 0.1 g·mm.
Frigate applies precision counterweight correction techniques that restore uniform mass distribution to eliminate vibration risks. This ensures CNC machined shafts meet ISO G2.5 standards for balance quality, providing smooth and stable rotation at high speeds.
Complex Geometries and Multi-Step Machining
Shafts with intricate features like splines, keyways, and precision threads demand multi-step machining processes, increasing the risk of tolerance buildup. Frigate overcomes this by combining CNC turning, milling, and drilling in a single setup using multi-axis machining centers.
To ensure precise feature alignment, Frigate integrates CAD-CAM programming to generate optimized tool paths that minimize tool transitions and reduce tolerance errors. Automated tool changers ensure repeatable positioning accuracy during multi-step processes. Frigate ensures compliance with DIN 5480 standards for spline profiles, achieving precise pitch diameter, pressure angles, and flank profiles.
Process Control and Repeatability
Consistency in shaft dimensions across multiple production batches is critical in large-scale manufacturing. Even minor variations can cause assembly issues or mechanical failure. Frigate ensures repeatability by applying Statistical Process Control (SPC) to monitor and control machining parameters.
Frigate’s CNC machines feature automated tool calibration systems that measure tool offsets and adjust cutting paths to maintain precision. Frigate uses Coordinate Measuring Machines (CMMs) for final inspection to verify dimensions within ±0.001 mm. This ensures every CNC machined shaft matches design specifications with minimal variance.
Supply Chain Reliability and Risk Mitigation
Material shortages, shipment delays, or inconsistent supplier quality can disrupt production timelines. Frigate maintains a buffer inventory of essential raw materials to mitigate these risks, ensuring uninterrupted production during supply chain disruptions.
Frigate employs dual-sourcing strategies, sourcing materials from multiple certified suppliers to minimize risks. Frigate’s ERP-driven inventory system also tracks material usage in real-time, ensuring stock levels are managed efficiently. Frigate offers real-time order tracking for customer transparency, providing visibility on production progress and shipment status.
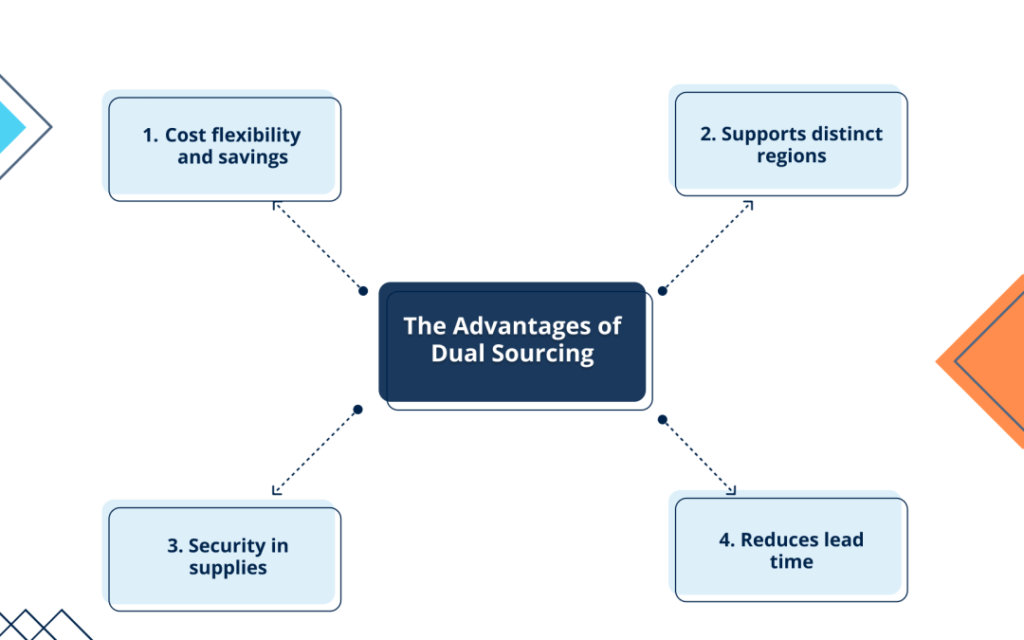
Conclusion
Sourcing high-precision CNC machined shafts, custom shafts, and precision industrial parts demands careful consideration of material quality, dimensional accuracy, and supplier reliability. Frigate addresses these technical challenges with advanced CNC machining capabilities, strict quality control, and robust supply chain management. Frigate delivers CNC machined shafts that enhance machine performance and reliability by ensuring precise tolerances, smooth finishes, and durable materials.
Get Instant Quote today for CNC machined shafts engineered to meet your technical specifications and ensure superior performance.