Many industries rely on strong, lightweight, and precise parts. These parts are used in cars, planes, electronics, and more. However, creating these parts can be challenging. Traditional methods often lead to defects and waste, which can be costly. Customers want better solutions that improve quality and reduce costs. That’s where advanced die-casting comes in. This blog will explore the latest innovations in advanced die-casting techniques, showing how they can help different industries thrive.
Key Innovations in Die-Casting Techniques
The landscape of die-casting is evolving rapidly. Innovations in technology and materials are pushing the boundaries of what is possible. These developments raise the standard of finished goods and increase the effectiveness of production processes. Let’s explore some of the most exciting innovations in die-casting techniques today.
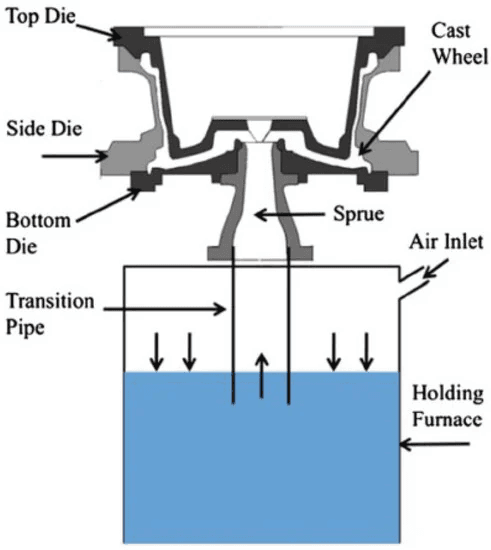
Metal 3D Printing Integration
One exciting innovation is the integration of metal 3D printing with die casting. In the past, making prototypes could take weeks. Now, companies can print metal parts quickly. This method allows engineers to create complex shapes that are hard to achieve.
For example, a company might need unique housing for a new gadget. Instead of machining it from a block of metal, they can print it directly, saving time and materials. A study found that 3D printing can reduce production costs by up to 70% and shorten lead times by 80%. This integration into advanced die-casting makes processes faster and more efficient.
Vacuum Die Casting
This method reduces the air trapped in the metal. By using a vacuum, manufacturers can eliminate defects like porosity, making the final parts stronger and more reliable.
Strong parts are crucial in the automotive industry. For example, car manufacturers often use vacuum die casting for engine components. This process helps ensure that these parts can withstand high pressure and temperatures. Studies show that vacuum die casting can improve the strength of components by up to 30%, which is why more companies are turning to this advanced technique.
High-Pressure Die Casting (HPDC) with Advanced Alloys
High-pressure die casting (HPDC) is another key area of innovation. Traditionally, aluminum and zinc were common materials. Now, manufacturers are using advanced alloys like magnesium and aluminum-lithium. These materials are lightweight yet very strong.
The automotive industry benefits significantly from these innovations. For instance, lightweight parts made from advanced alloys can help reduce a car’s overall weight. A lighter car uses less fuel. Reducing vehicle weight by just 10% can lead to a 5-7% improvement in fuel efficiency. This is a critical advantage for manufacturers looking to meet new environmental standards.
Smart Die Casting Technology
The future is smart! Smart die-casting technology uses sensors and the Internet of Things (IoT) to monitor real-time processes. These sensors can detect temperature changes, pressure levels, and even the material’s quality.
With this technology, manufacturers can make adjustments instantly, leading to better quality and less waste. For example, a study showed that implementing smart technology in die-casting can reduce defects by 40%. This is a game-changer for many industries, including aerospace and electronics.
Sustainable Die Casting Innovations
Sustainability is becoming a major manufacturing focus. Innovative sustainable die-casting techniques include using recycled materials and energy-efficient processes. Manufacturers are also exploring ways to recycle metal scrap generated during production.
Using recycled materials can cut costs and reduce production’s carbon footprint. A report from the World Economic Forum states that using recycled aluminum saves 95% of the energy needed to produce new aluminum. As a result, more companies are adopting sustainable practices in their advanced die-casting processes.
Industry Applications of Innovations in Die Casting
As these innovations continue to develop, various industries are finding new and improved ways to utilize advanced die-casting techniques. Understanding how these innovations apply in different sectors highlights their versatility and significance. Let’s explore how various industries benefit from the latest die-casting advancements.
Automotive Industry
The automotive industry is one of the largest users of advanced die-casting techniques. Innovations like high-pressure die casting and lightweight alloys help create strong, light parts.
Manufacturers can produce components such as engine blocks, transmission housings, and wheels. These parts need to meet strict safety standards while also being efficient. Advanced die-casting allows for complex designs that improve performance and safety features.
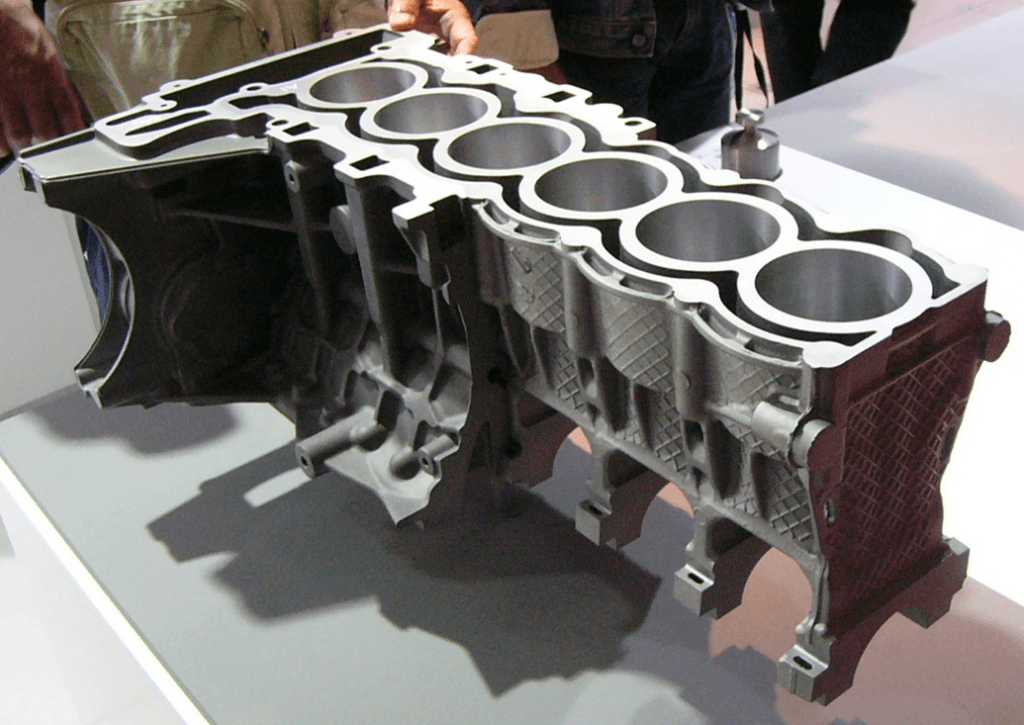
Aerospace Industry
The aerospace sector demands the highest quality components. Innovations like vacuum die casting and smart technology help meet these requirements.
For example, airplane parts must be lightweight yet strong. Using advanced alloys and vacuum techniques ensures these parts can withstand flight stress. Advanced die-casting in aerospace has been shown to reduce the weight of components by up to 20%. This not only improves performance but also saves fuel.
Electronics Industry
In the electronics industry, manufacturers need precision and durability. Advanced die-casting techniques help create device enclosures and housings. Metal 3D printing allows for rapid prototyping, speeding up new product development.
For instance, smartphone manufacturers often need custom housings. Advanced die-casting methods allow them to achieve complex designs while maintaining high quality. This results in better thermal management, leading to longer-lasting devices.
Industrial Equipment and Machinery
Industrial equipment relies on durable parts that can handle heavy use. Advanced die-casting provides the strength needed for these applications.
Smart monitoring can predict when equipment may fail, allowing maintenance before problems arise. This reduces downtime and saves money. Studies indicate that predictive maintenance can cut maintenance costs by up to 30%, which is vital for manufacturers that rely on heavy machinery.
Future Trends in Die Casting Innovations
Looking ahead, the die-casting industry is poised for even more transformative changes. Emerging technologies and practices are set to redefine how die-casting processes operate. By monitoring these developments, manufacturers can maintain their competitiveness and satisfy their businesses’ changing needs. Let’s delve into the future trends shaping the world of die-casting.
Advancements in Automation and Robotics
The future of die-casting will likely include more automation. Fully automated die-casting cells can increase efficiency. These cells can handle everything from feeding raw materials to finishing the parts.
Automation lowers expenses by reducing the demand for manual labor. It also minimizes human error, improving quality. According to the International Federation of Robotics, by 2025, 4 million industrial robots will be in use. This change will significantly impact advanced die-casting.
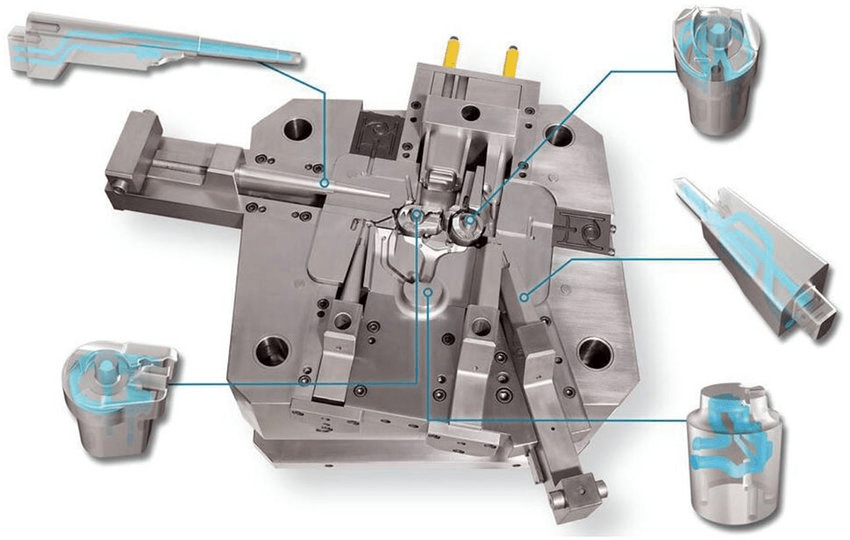
Nanotechnology in Die Casting Materials
Nanotechnology is revolutionizing material science. Through nanoscale material manipulation, producers can improve attributes like robustness and longevity.
Using nanomaterials in die-casting could lead to lighter yet stronger parts. This can revolutionize industries like aerospace, where every gram counts. For example, using nanotechnology in alloys could improve strength by 50%, making aircraft parts safer and more efficient.
AI and Machine Learning in Process Optimization
Artificial Intelligence (AI) and machine learning (ML) are changing manufacturing processes. These technologies can analyze data from die-casting processes to find ways to improve them.
For instance, AI can predict defects before they happen, allowing manufacturers to adjust processes in real-time. A study found that using AI in manufacturing can reduce defects by up to 30%. This is a significant advantage for companies looking to enhance their advanced die-casting capabilities.
Conclusion
Innovations in advanced die-casting techniques are transforming manufacturing. From metal 3D printing to smart technology, these advancements are making processes faster, more efficient, and more sustainable. Industries like automotive, aerospace, electronics, and industrial machinery are already reaping the benefits. By adopting these new techniques, manufacturers can improve quality and reduce costs.
Are you ready to embrace the future of manufacturing? At Frigate, we specialize in advanced die-casting solutions tailored to your needs. Contact us today to learn how we can help you achieve excellence in your products!