The world of metal casting is vast and complex, offering a variety of methods to bring your desired shape to life. Each casting process boasts its own strengths and weaknesses, and navigating the options to find the one that perfectly aligns with your project requirements can be a challenge. But worry not! This aims to shed light on the most common casting methods, with a particular focus on production costs.
Understanding Casting Costs
Before diving into specific methods, it’s crucial to understand the various factors that influence casting costs. Here are some key considerations:
- Upfront Costs – This includes the cost of tooling, patterns, and any specialized equipment required for the chosen casting process.
- Material Costs – The type and amount of material being cast will significantly impact the overall price.
- Labor Costs – The complexity of the casting process and the required level of skilled labor will affect labor costs.
- Volume – Generally, casting a larger quantity brings down the cost per unit.
Popular Casting Methods and Their Cost Considerations
Now, let’s explore some of the most popular casting methods and how they fare in terms of production costs:
- Sand Casting – This traditional method utilizes sand molds, making it relatively inexpensive for upfront costs. However, sand molds are not reusable, leading to higher material costs for projects requiring high-volume casting. Sand casting is a versatile process suitable for a wide range of metals and complexities, making it a good choice for projects with moderate production volumes.
- Investment Casting (Lost-Wax) – This process offers exceptional complexity and produces highly accurate castings with a smooth surface finish. However, the intricate nature of creating ceramic shells for each cast drives upfront costs and labor costs. Investment casting is ideal for intricate parts requiring high precision and a low production volume.
- Die Casting – This high-pressure method utilizes permanent metal dies, resulting in fast production times and consistent quality. The upfront costs for creating the dies can be significant, but die casting is highly cost-effective for high-volume production runs of simple to moderately complex parts.
- Centrifugal Casting – This process utilizes centrifugal force to distribute molten metal within a mold. It’s particularly well-suited for creating parts with a symmetrical cylindrical or tubular shape. Upfront costs can vary depending on the complexity of the mold design, but labor costs tend to be lower compared to some other methods. Centrifugal casting is a good option for producing high-quality parts with a good surface finish for moderate to high-volume production.
- Permanent Mold Casting (Gravity Casting) – This method utilizes reusable metallic molds, offering a balance between upfront costs and production speed. Permanent mold casting is faster than sand casting and more cost-effective for moderate production volumes, particularly for parts that require good dimensional accuracy.
- Lost Foam Casting – This process utilizes a vaporized polystyrene pattern to create a cavity in the mold. It’s a good option for intricate parts with a good surface finish, but upfront costs can be higher due to the specialized patterns required. Lost foam casting is suitable for low to moderate production volumes.
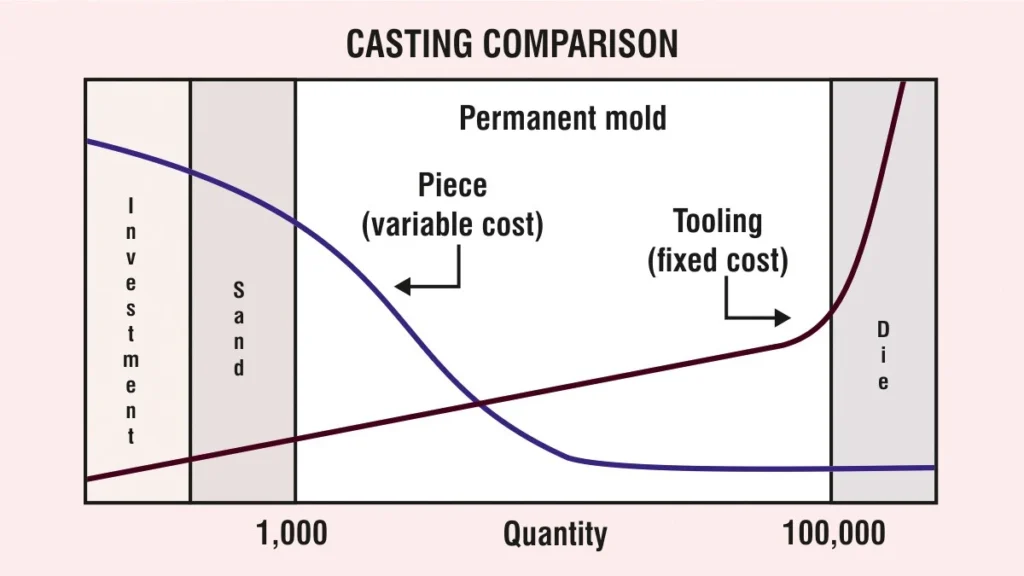
Choosing the Right Casting Method for Your Budget
There’s no one-size-fits-all answer when it comes to casting methods and their associated costs. The ideal choice depends on your specific project requirements, including:
- Desired Outcome – Consider the complexity of the parts, required tolerances, and desired surface finish.
- Production Volume – The number of castings you need will significantly impact the cost-effectiveness of each method.
- Material – The type of metal being cast can influence both upfront costs and the choice of casting method.
Stop Drowning in Casting Complexity – Choose Frigate as Your Trusted Partner
Are you facing mounting pressure to deliver high-quality castings on tight deadlines? Perhaps you’re struggling with unreliable casting suppliers or excessive upfront costs are squeezing your project budget.
Frigate offers a comprehensive casting solution designed to eliminate these challenges and streamline your entire casting process, from equipment procurement to part delivery. Our team of casting specialists possesses a wealth of experience in various casting methods, including sand casting, investment casting, die casting, and more. We leverage this expertise to recommend the most cost-effective and efficient solution for your specific needs, ensuring you receive top-notch castings that meet your exact specifications.
The Frigate Advantage – Your Path to Casting Success
Here’s how partnering with Frigate empowers you to achieve success in your casting projects:
- Reduced Costs – We work collaboratively with you to identify the most cost-effective casting method and procurement strategies with the potential to reduce your upfront costs. Our in-depth knowledge of capex procurements ensures you acquire the right equipment at the most competitive price, eliminating unnecessary expenditure.
- Guaranteed On-Time Delivery – Frigate prioritizes timely delivery, guaranteeing your castings will arrive at your doorstep within the estimated time of your order confirmation. This eliminates production delays and ensures a seamless workflow by providing the parts you need precisely when you need them.
- Uncompromising Quality – Our commitment to quality is unwavering throughout the entire casting process. We implement stringent quality control measures at every stage, and we only collaborate with qualified casting partners who adhere to the highest industry standards. This ensures you receive defect-free castings that meet your dimensional tolerances and deliver exceptional performance within your application.
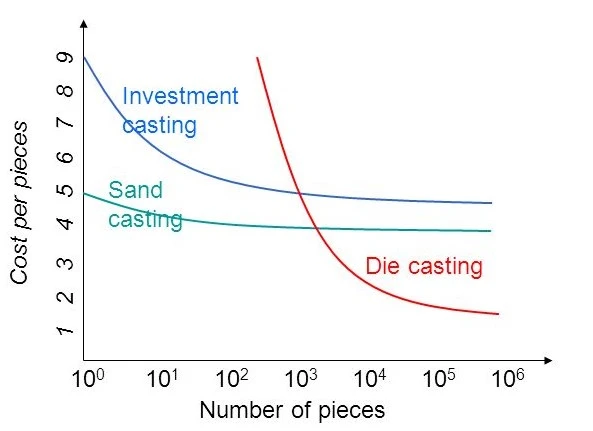
Ready to Streamline Your Casting Needs?
By understanding the various casting methods and their cost considerations, you can make an informed decision that aligns with your project’s budget and requirements. When faced with the challenge of choosing a casting method for your industry, Frigate can be your trusted partner. With extensive experience and expertise in all these casting processes, Frigate will help you identify the most cost-effective and efficient solution to bring your vision to life.
If you’re looking for a reliable partner to handle your casting requirements, Frigate is the ideal solution. Partner with Frigate today and experience the difference! Let us take the complexity out of casting and empower your success.
Contact us today to discuss your project and explore how our casting solutions can empower your success.