Transfer Die Stamping Services
Frigate’s transfer die stamping offers precise, high-volume production of complex parts. Our process ensures consistent accuracy, optimal material use, and fast cycle times.
Our Clients





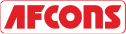

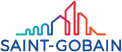


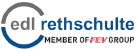

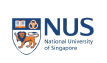
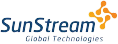

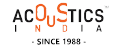




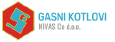
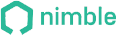
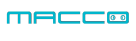












Advantages of Transfer Die Stamping Services
Reduced Tooling Costs
Transfer die stamping reduces tooling expenses by allowing multiple operations in one press, eliminating the need for separate dies.
Consistent Quality
The process offers consistent, high-quality results across all parts, minimizing defects and ensuring uniformity in large production batches.
Enhanced Strength
The method improves material strength through work hardening, resulting in more durable and resistant parts.
Lower Labor Costs
Automation in transfer die stamping minimizes manual intervention, reducing labor costs and enhancing overall production efficiency.
Custom Transfer Die Stamping for High-Precision Parts
Custom transfer die stamping provides a reliable solution for producing complex, high-precision parts. This process ensures tight tolerances and consistent quality across high-volume production runs. It allows for efficient material usage, reducing waste and optimizing cost-effectiveness. Transfer die stamping improves production efficiency with faster cycle times without compromising part integrity. The method is versatile and capable of handling various materials and intricate designs, making it ideal for industries requiring advanced components.

Get Your Quote Now
- Instant Quotation
- On-Time Delivery
- Affordable Cost
Our Transfer Die Stamping Process






The process begins with feeding a continuous strip of metal into the press, which is aligned for precision.
The first set of operations is performed on the metal strip using a progressive die, shaping the part's basic form.
A transfer mechanism moves the partially formed part from one die station to the next, ensuring accurate positioning.
Additional forming operations, such as bending or piercing, refine the part's shape at each die station.
The final die station performs the last stamping operation, completing the part with high precision and tight tolerances.
Once the part is fully formed, it is ejected from the die and ready for further processing or inspection.
Transfer Die Stamping Materials
Transfer die stamping requires precise control over material forming and shaping. Advanced techniques ensure consistent quality, high accuracy, and efficient production processes.
Cold-rolled steel offers high dimensional accuracy and a smooth surface finish. Its excellent formability makes it ideal for complex shapes and precision parts, often used in automotive and machinery components.
Stainless steel provides superior corrosion resistance. Type 304 is used for general automotive parts, Type 316 for marine and chemical applications, and Type 430 for decorative or structural components requiring magnetic properties.
HSLA steels offer high yield strength and fatigue resistance with reduced weight. These alloys are ideal for automotive structural parts, providing a lightweight solution for safety-critical applications.
Aluminum alloys like 6061, 5052, and 1100 are lightweight and corrosion-resistant. 6061 is used in aerospace and automotive, 5052 in marine environments, and 1100 for highly ductile parts requiring good formability.
Copper alloys, including brass and bronze, provide excellent conductivity and corrosion resistance. Brass is used for electrical parts, while bronze is ideal for wear-resistant applications like gears and bearings.
Titanium alloys, such as Ti-6Al-4V, are strong, lightweight, and corrosion-resistant. These alloys are used in high-performance industries, including aerospace, for parts like turbine blades and medical implants.
Nickel alloys like Inconel 625 and Hastelloy C-276 offer excellent high-temperature and corrosion resistance. They are used for high-stress, high-temperature parts in extreme environments, such as aerospace and chemical processing.
Due to their wear resistance and toughness, tool steels, such as D2, A2, and S7, are used to make stamping dies. These steels endure the high-stress conditions of high-volume production and ensure long-lasting die performance.
Maximize Efficiency and Reduce Cycle Time Without Compromising Quality
Frigate enhances cycle time through optimized die designs and precise tooling setups. Advanced material handling systems streamline the flow of parts between stamping stations, reducing delays. High-performance lubricants minimize friction, lowering tool wear and ensuring consistent part quality. Automated transfer mechanisms quickly move components, reducing human error and downtime. Efficient process control and real-time monitoring ensure that each part meets stringent quality standards.

Compliance for Transfer Die Stamping Services
Frigate’s Transfer Die Stamping Services adhere to strict compliance standards to ensure high-quality production while meeting industry regulations. Our commitment to precision, safety, and sustainability is reflected in our certifications. We use advanced technologies and robust quality control systems to guarantee that every part produced aligns with global industry standards and client expectations.
Ensures Frigate maintains a quality management system for consistent, defect-free stamping processes.
Meets automotive industry-specific requirements, focusing on defect prevention and continuous product quality improvement.
Confirms Frigate’s electrical components comply with safety standards for use in electrical products.
Verifies the exclusion of hazardous substances in materials, ensuring safety and regulatory adherence in manufacturing processes.
Manages environmental aspects, ensuring Frigate minimizes environmental impact through efficient, sustainable production practices.
Demonstrates compliance with EU health, safety, and environmental standards for product approval and market access.
Implements safety management practices to protect employee health and prevent workplace accidents during manufacturing.

Tolerance for Transfer Die Stamping Services
Tolerance on the wear of die surfaces over time, ensuring consistent part quality throughout production runs.
Ensures uniform material flow during stamping, avoiding defects like wrinkles or splits.
Precision tolerance on the alignment of tools in the die to avoid misalignment or part defects.
Ensures that the material is formed within its limit to avoid rupture or failure during stamping.
Tolerance on the clearance between the punch and die, ensuring smooth material flow and minimizing part defects.
Tolerance on the variation in force applied during stamping, ensuring consistent part formation.
Tolerance on the thickness of the lubrication film, ensuring adequate lubrication and preventing die wear.
Tolerance on any deformation of the part post-stamping, ensuring the part remains within the required specifications.
Tolerance on tooling temperature during stamping to prevent part defects due to thermal expansion or contraction.
Measurement of any twisting or torsional deformation in parts, ensuring dimensional stability after forming.
Ensures uniform shear force distribution during cutting to avoid irregularities in the cut edges.
Tolerance on the quality of edges post-punching, ensuring no excessive burrs or rough edges.
Tolerance in pressure distribution within the die cavity to ensure consistent stamping and material flow.
Variation in cycle time, ensuring consistent production rates without compromising quality.
Tolerance on material thickness after forming, ensuring uniformity and preventing defects like thinning or thickening in the material.

Quality Testing Standards for Transfer Die Stamping Services
Examines the surface integrity of tooling under high magnification to detect microcracks, wear, or defects.
Measures die surface temperature during stamping to ensure optimal thermal conditions and prevent overheating.
Measures variations in stamping force applied to ensure consistent material forming without overstress.
Monitors the wear rate of punches to assess tool life and maintain consistent part quality throughout production.
Measures material strain during forming to ensure the material remains within its elastic limits and avoids failure.
Measures the clearance between die and punch to ensure proper material flow and avoid part defects.
Measures the speed of material flow during forming to prevent excessive deformation or material defects.
Verifies the absence of die cavitation, ensuring that the die remains smooth and free of voids that could affect stamping quality.
Evaluates the stamped part’s resistance to peening and external impact forces, ensuring durability.
Measures the time-dependent reduction in stress in stamped parts, ensuring parts maintain structural integrity under load.
Analyzes how well the lubricant is distributed on the material to ensure consistent performance and part quality.
Detects residual stresses in stamped parts that could affect performance or cause deformation over time.
Measures die wear over time, ensuring it remains within acceptable limits to maintain part consistency.
Analyzes part deformation during stamping to identify areas of strain and prevent undesirable shape changes.
Assesses the wear performance of the tools under operational conditions to predict tool life and maintenance needs.
Verifies the integrity and uniformity of surface coatings applied to stamped parts for enhanced durability and corrosion resistance.
Transfer Die Stamping in Automotive Component Manufacturing
Producing high-precision automotive components requires consistent quality at high volumes. Transfer die stamping achieves this by utilizing advanced die designs to meet tight tolerances and complex geometries. Automated material handling systems reduce cycle time and improve production efficiency. Specialized tooling ensures part accuracy, while high-performance lubricants minimize friction, extending tool life. Real-time process monitoring maintains part consistency, even during high-volume production runs. This combination of precision, efficiency, and reduced downtime enhances the reliability and cost-effectiveness of automotive component manufacturing. Transfer die stamping streamlines production while ensuring high-quality, defect-free parts.






Industries We Serve
- Solid Progress
Our Manufacturing metrics
Frigate brings stability, control, and predictable performance to your sourcing operations through a structured multi-vendor system.
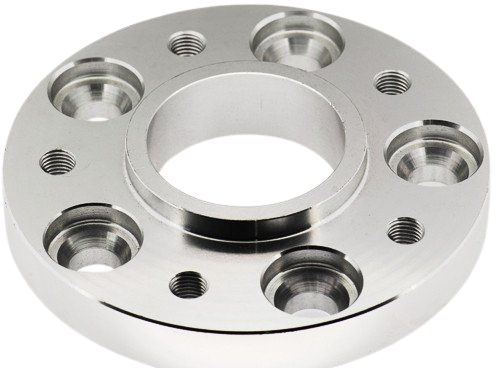
2.8X
Sourcing Cycle Speed
Frigate’s pre-qualified network shortens decision time between RFQ and PO placement.
94%
On-Time Delivery Rate
Structured planning windows and logistics-linked schedules improve project-level delivery reliability.
4X
Multi-Part Consolidation
We enable part family batching across suppliers to reduce fragmentation.
22%
Quality Rejection Rate
Multi-level quality checks and fixed inspection plans lower non-conformities.
30%
Procurement Costs
Optimized supplier negotiations and bulk order strategies reduce your overall sourcing expenses.
20%
Manual Processing Time
Automation of sourcing and supplier management significantly reduces time spent on manual tasks.
Scale High-Volume Production with Complex Specifications
Frigate’s advanced die designs and material handling systems allow for the efficient production of high-volume, complex parts. Specialized tooling ensures accuracy across intricate geometries and tight tolerances. Real-time monitoring ensures that all parameters, including pressure and temperature, remain within specified limits, preventing defects. Integrating automated systems minimizes human intervention, reducing the risk of variation in part quality. Process control adjustments are made as needed to maintain part integrity during large-scale runs.

Get Clarity with our Manufacturing Insights
- Real Impact
Words from Clients
See how global OEMs and sourcing heads describe their experience with our scalable execution.
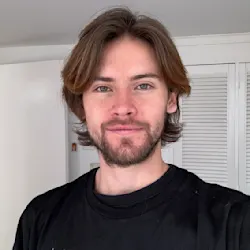
“Quick turnaround and solid quality.”
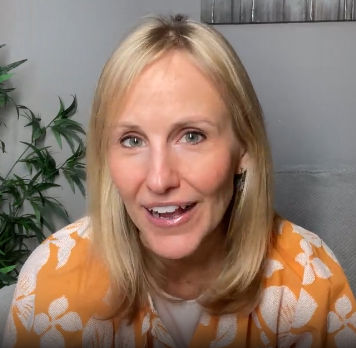
“The instant quote tool saved us time, and the parts were spot-on. Highly recommend Frigate!”
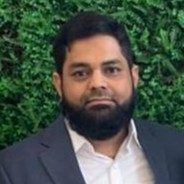
“I would strongly recommend Frigate to anyone who wants to do Rapid Prototyping, and take their ideas to manufacturing. One firm doing all kinds of Product Development!”
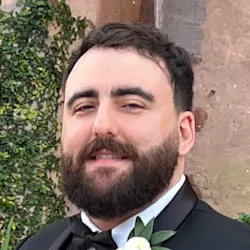
“Great service, fair price, and the parts worked perfectly in our assembly.”
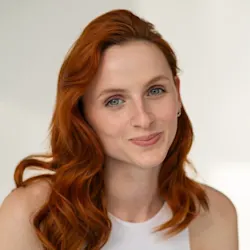
“Top-notch machining and fast shipping. Very satisfied with the results.”
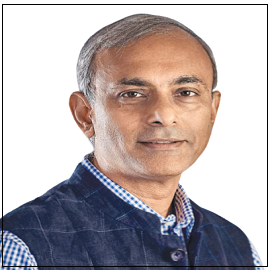
“The next disruption is happening in Prototyping & Manufacturing on-demand and Frigate is leading the way! I personally believe the Frigate's way of IIOT enabled cloud platform with Al.”
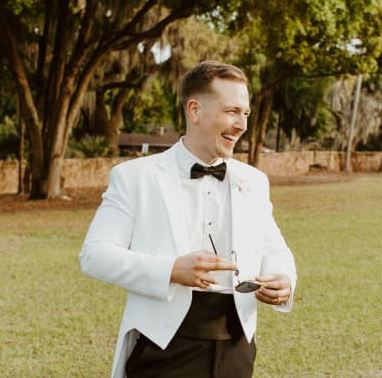
“Frigate delivered high-quality parts at a competitive price. The instant quote tool is a huge plus for us!”

“We appreciate the precision and quality of the machined components in the recent delivery—they meet our specifications perfectly and demonstrate Frigate’s capability for excellent workmanship.”
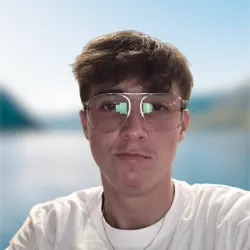
“Flawless execution from quote to delivery.”

“I am absolutely happy to work with supplier like Frigate who were quite proactive & result oriented . Frigate has high willingness team who has strong know how & their passion towards the products & process were absolutely thrilling.”
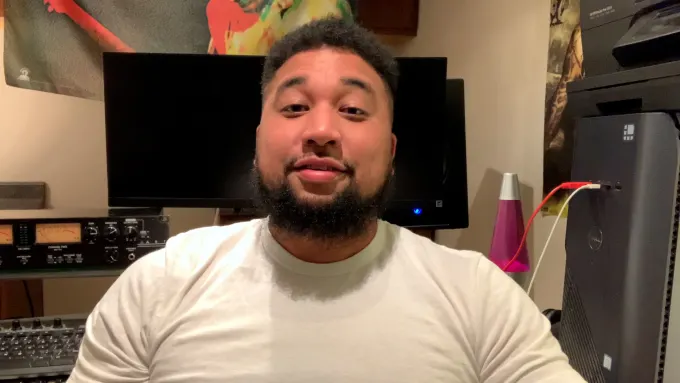
“The precision on these parts is impressive, and they arrived ahead of schedule. Frigate’s process really stands out!”
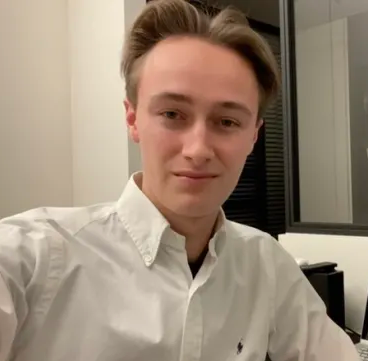
“Parts were exactly as spec’d, and the instant quote made budgeting a breeze.”
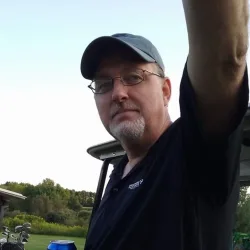
“Good value for the money.”
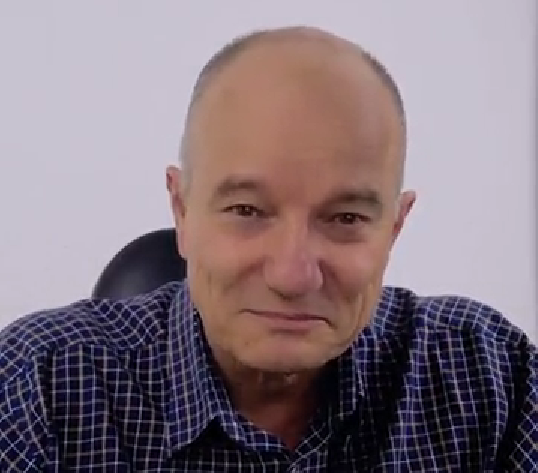
“The finish was perfect, and the team was easy to work with.”

“Working with Frigate has been great. Their proactive, results-driven approach and expertise shine through in every project. It's been a pleasure collaborating with them.”

"We are highly satisfied with the timely delivery and quality of the MIG Welding Cable from Frigate. Their attention to detail, secure packaging, and quick responsiveness stood out. We confidently recommend Frigate Engineering Services Pvt. Ltd. as a reliable manufacturing partner."
Having Doubts? Our FAQ
Check all our Frequently Asked Question
Transfer die stamping incorporates adaptive tooling and precise material feed mechanisms, ensuring consistent part quality despite variations in material thickness.
Springback is controlled through die design adjustments and specialized materials that minimize elastic recovery, ensuring accurate part geometry after stamping.
Part distortion is reduced by utilizing progressive dies with precise clearance settings and applying controlled stamping pressures to maintain part integrity.
Lubrication minimizes friction, reduces tool wear, and prevents material sticking, especially when working with high-performance alloys. It also improves stamping consistency and extends die life.
Multi-material components are handled using specialized die designs that form and shear different materials simultaneously, ensuring precise joint integrity and minimal defects.
We'd love to Manufacture for you!
Submit the form below and our representative will be in touch shortly.
LOCATIONS
Global Sales Office
818, Preakness lane, Coppell, Texas, USA – 75019
Registered Office
10-A, First Floor, V.V Complex, Prakash Nagar, Thiruverumbur, Trichy-620013, Tamil Nadu, India.
Operations Office
9/1, Poonthottam Nagar, Ramanandha Nagar, Saravanampatti, Coimbatore-641035, Tamil Nadu, India. ㅤ
Other Locations
- Bhilai
- Chennai
- Texas, USA