Embossing and Coining Services
Frigate offers precise embossing and coining with high-definition metal surface impressions. These techniques ensure durable, accurate designs within strict industry tolerances.
Our Clients





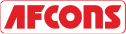

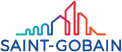


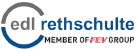

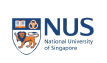
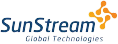

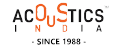




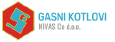
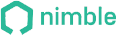
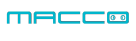












Advantages of Embossing and Coining Services
Superior Dimensional Accuracy
Embossing and coining achieve sub-micron precision in creating complex features, ensuring consistent part dimensions and strict tolerances across large volumes.
Enhanced Surface Integrity
The process preserves material properties, minimizing distortion while providing excellent surface finish quality and sharp, defined patterns on metal surfaces.
Minimized Tool Wear
Coining, with its controlled pressure application, reduces tool degradation, resulting in extended tool life and reduced maintenance costs.
Optimized Material Flow
Both techniques ensure uniform material distribution, preventing defects like cracking or warping and enhancing the structural integrity of stamped parts.
Custom Embossing and Coining Services
Custom embossing and coining services provide the solution when precise, durable, and high-quality designs are critical. Achieving sharp, intricate patterns on metal surfaces can be challenging without the right technique. These processes eliminate the risk of inconsistent results and material distortion, offering clear, repeatable impressions that meet strict tolerances. With custom embossing and coining, you ensure exceptional detail, durability, and efficiency, allowing for high-volume production with minimal tool wear and reduced costs. For industries requiring top-tier precision, this service guarantees strong, reliable results.

Get Your Quote Now
- Instant Quotation
- On-Time Delivery
- Affordable Cost
Our Embossing and Coining Process






Custom dies are designed to match the desired pattern, ensuring precision. The dies are then mounted in the machine for operation.
The metal surface is cleaned and prepped for embossing or coining to ensure smooth, defect-free impressions.
The dies are precisely aligned with the material to ensure accurate positioning of the design before any pressure is applied.
The material is placed between the upper and lower dies. Controlled force is applied to create a permanent, high-definition impression.
For certain materials, heat may be applied to reduce stress and improve material flow, ensuring a clearer impression.
After the process, parts undergo a rigorous inspection to confirm dimensional accuracy, surface finish, and compliance with all specifications.
Embossing and Coining Materials
Embossing and coining are precise methods for creating detailed metal patterns. These processes ensure accuracy and durability for demanding industrial applications.
Lightweight and highly malleable, aluminum alloys are commonly used for embossing and coining. Their excellent formability ensures sharp, clear impressions, making them ideal for high-precision applications, including automotive and aerospace components.
Copper and its alloys, including brass and bronze, are favored for their exceptional conductivity and corrosion resistance. These materials provide a smooth surface that holds intricate designs well, making them ideal for decorative and functional applications.
Stainless steel is a durable choice for embossing and coining due to its strength and corrosion resistance. Its high tensile strength ensures long-lasting impressions, making it suitable for industrial parts requiring precision and durability.
Zinc-based alloys are widely used due to their low melting point and ease of molding. They offer excellent surface detail and are commonly used for creating detailed, high-volume parts like connectors and electrical components.
These alloys offer superior resistance to corrosion, making them suitable for harsh environments. Nickel is ideal for creating precise, durable impressions, especially in applications requiring high resistance to wear and thermal stability.
Titanium’s strength-to-weight ratio and corrosion resistance make it ideal for aerospace & medical applications. Embossing and coining titanium alloys require specialized equipment but deliver highly durable, precise results.
Ensuring Consistent Quality with Post-Process Precision
Frigate employs advanced monitoring systems throughout the embossing and coining process to ensure consistent quality in every part. Tracking each stage of production detects potential inconsistencies early, allowing for immediate corrective action. This minimizes the need for additional finishing or deburring, ensuring uniform surface finishes and precise dimensional accuracy. Regular calibration and tool maintenance maintain consistent quality, producing reliable, high-quality outputs with minimal variation.

Compliance for Embossing and Coining Services
Embossing and coining processes require strict adherence to industry standards to ensure precision and reliability in the final components. These techniques involve high-pressure forming that must meet exact specifications for surface quality, dimensional accuracy, and material integrity.
Ensures a robust quality management system for consistent production and customer satisfaction. Regular audits maintain compliance.
This certification is mandatory for aerospace applications, emphasizing traceability, risk management, and strict control over high-precision manufacturing processes.
A global standard for automotive parts, ensuring defect prevention and quality improvement in embossing and coining processes.
Demonstrates environmental responsibility by ensuring sustainable practices and minimal waste during production.
Sets guidelines for material hardness, ensuring performance under operational stress without deformation.
Ensures proper part identification and traceability, critical for defense and high-security applications.
Guarantees that embossed and coined parts are free from hazardous materials like lead and mercury.
Establishes tolerance limits for dimensional accuracy, critical in achieving flawless results in high-precision applications.
Controls material composition to ensure safety and environmental compliance during manufacturing.
Focuses on maintaining a safe workplace by minimizing risks associated with embossing and coining operations.

Tolerance for Embossing and Coining Services
Ensures even depth distribution across the embossed surface for consistent visual and functional performance.
Guarantees uniform grain structure post-forming to prevent weak points or cracks.
Controls deviation over large surfaces, critical for parts requiring planar precision.
Ensures precise pressure application to avoid material over-compression or under-formation.
Manages material expansion during heat treatment to maintain dimensional accuracy.
Limits height-to-width ratios to prevent deformation or instability in intricate features.
Strict control over burr formation to enhance part quality and reduce post-processing needs.
Ensures even stress distribution to prevent warping or cracking under operational loads.
Guarantees exact replication of die patterns for intricate and detailed designs.
Limits residual stress to maintain part durability and avoid premature failure.
Controls material layering accuracy for multi-step embossing or coining processes.
Maintains precise temperature control to avoid thermal stress and ensure consistent material properties.

Quality Testing Standards for Embossing and Coining Services
Measures the uniformity of pressure across the die to ensure consistent forming and avoid material overloading.
Evaluates die surface wear to ensure it doesn’t affect part quality or precision over time.
Measures the rate at which material hardens under the applied forming pressure, ensuring optimal material behavior.
Verifies precise alignment of dies and tools to ensure correct feature placement during embossing and coining.
Measures the extent to which the material returns to its original shape after pressure is released, ensuring minimal deformation.
Determines the friction between the die and material to optimize forming conditions and prevent material sticking.
Measures material’s ability to relax internal stresses over time, ensuring stability in long-term use.
Simulates material flow during the coining or embossing process to optimize tooling and process parameters.
Verifies the material's strength after embossing or coining to ensure it meets mechanical load requirements.
Measures the heat generated during the forming process to prevent overheating and material damage.
Evaluates the material's ability to undergo plastic deformation without cracking, ensuring suitable material selection.
Monitors die temperature to ensure the optimal working range is maintained throughout the embossing or coining process.
Streamlining Medical Device Production with Advanced Embossing and Coining
Manufacturing medical components with tight tolerances can be challenging. Embossing and coining provide precise, high-quality results for critical parts like surgical instruments and implants. These techniques ensure exceptional dimensional accuracy and fine detail, meeting strict regulatory standards. Embossing and coining also enhance functionality and traceability by accurately replicating features like threads, logos, and serial numbers. High-strength materials processed through these methods ensure component integrity, improving safety and reliability in medical devices.






Industries We Serve
- Solid Progress
Our Manufacturing metrics
Frigate brings stability, control, and predictable performance to your sourcing operations through a structured multi-vendor system.
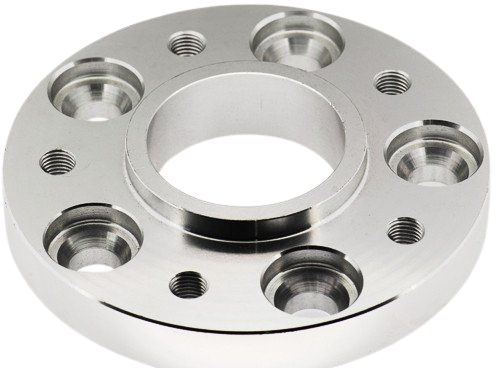
2.8X
Sourcing Cycle Speed
Frigate’s pre-qualified network shortens decision time between RFQ and PO placement.
94%
On-Time Delivery Rate
Structured planning windows and logistics-linked schedules improve project-level delivery reliability.
4X
Multi-Part Consolidation
We enable part family batching across suppliers to reduce fragmentation.
22%
Quality Rejection Rate
Multi-level quality checks and fixed inspection plans lower non-conformities.
30%
Procurement Costs
Optimized supplier negotiations and bulk order strategies reduce your overall sourcing expenses.
20%
Manual Processing Time
Automation of sourcing and supplier management significantly reduces time spent on manual tasks.
Minimizing Downtime with Proactive Tooling Maintenance
Frigate’s proactive tooling maintenance strategy minimizes downtime and boosts production efficiency. Regular tool inspections are scheduled to detect wear early. Tool replacements are handled before they disrupt the manufacturing process. This reduces unexpected production halts and ensures continuous operation. High-performance tooling materials extend tool life. Precise monitoring and maintenance keep the embossing and coining processes running smoothly. This approach ultimately improves uptime and reduces costs.

Get Clarity with our Manufacturing Insights
- Real Impact
Words from Clients
See how global OEMs and sourcing heads describe their experience with our scalable execution.
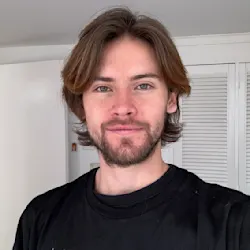
“Quick turnaround and solid quality.”
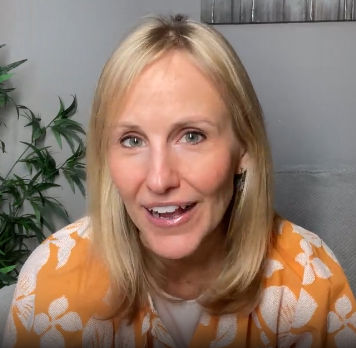
“The instant quote tool saved us time, and the parts were spot-on. Highly recommend Frigate!”
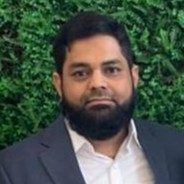
“I would strongly recommend Frigate to anyone who wants to do Rapid Prototyping, and take their ideas to manufacturing. One firm doing all kinds of Product Development!”
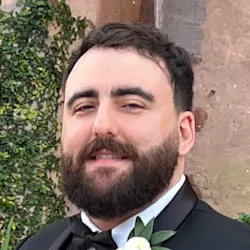
“Great service, fair price, and the parts worked perfectly in our assembly.”
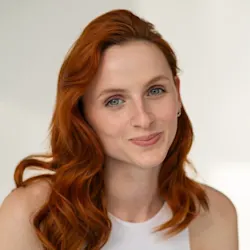
“Top-notch machining and fast shipping. Very satisfied with the results.”
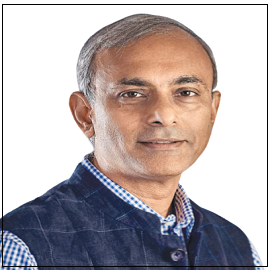
“The next disruption is happening in Prototyping & Manufacturing on-demand and Frigate is leading the way! I personally believe the Frigate's way of IIOT enabled cloud platform with Al.”
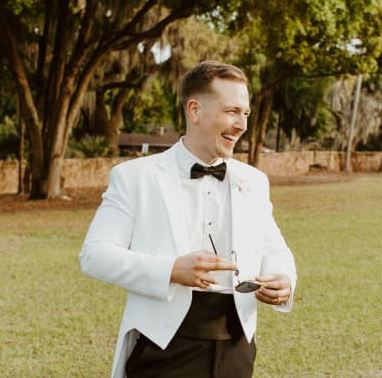
“Frigate delivered high-quality parts at a competitive price. The instant quote tool is a huge plus for us!”

“We appreciate the precision and quality of the machined components in the recent delivery—they meet our specifications perfectly and demonstrate Frigate’s capability for excellent workmanship.”
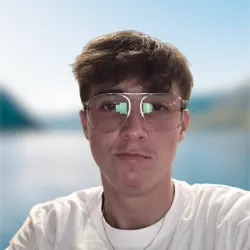
“Flawless execution from quote to delivery.”

“I am absolutely happy to work with supplier like Frigate who were quite proactive & result oriented . Frigate has high willingness team who has strong know how & their passion towards the products & process were absolutely thrilling.”
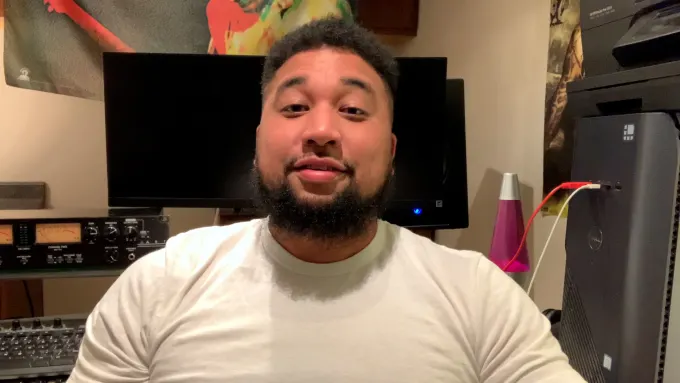
“The precision on these parts is impressive, and they arrived ahead of schedule. Frigate’s process really stands out!”
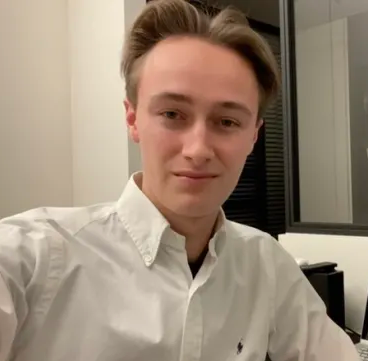
“Parts were exactly as spec’d, and the instant quote made budgeting a breeze.”
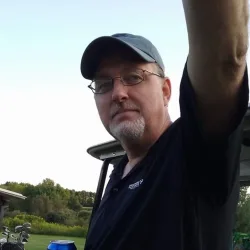
“Good value for the money.”
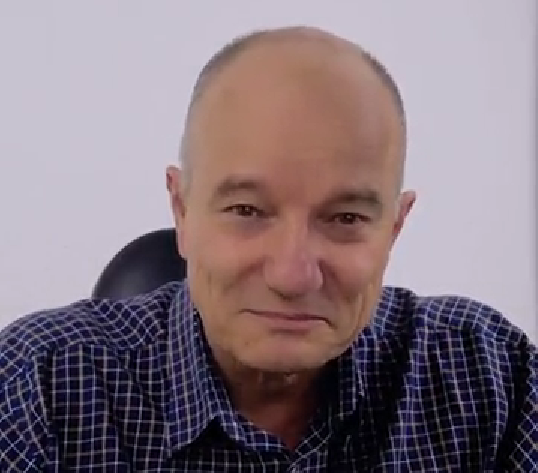
“The finish was perfect, and the team was easy to work with.”

“Working with Frigate has been great. Their proactive, results-driven approach and expertise shine through in every project. It's been a pleasure collaborating with them.”

"We are highly satisfied with the timely delivery and quality of the MIG Welding Cable from Frigate. Their attention to detail, secure packaging, and quick responsiveness stood out. We confidently recommend Frigate Engineering Services Pvt. Ltd. as a reliable manufacturing partner."
Having Doubts? Our FAQ
Check all our Frequently Asked Question
Frigate employs advanced tooling materials and optimizes process parameters, including pressure and temperature, to reduce die wear and maintain consistent precision over multiple production cycles.
Factors such as die design, material properties, applied pressure, and machine calibration influence dimensional accuracy. Frigate ensures precision by controlling these variables throughout the embossing and coining processes.
Frigate utilizes high-pressure machinery and fine-tuned dies, which allow for consistent depth and sharpness across intricate and detailed designs and maintain high-definition patterns on the material surface.
Temperature control is critical to maintaining material consistency, preventing thermal distortion, and optimizing the metal's flow during embossing and coining. Frigate precisely manages this to enhance part quality and consistency.
Frigate carefully designs and adjusts die geometries, pressures, and material feed rates to ensure optimal flow and avoid defects such as uneven patterns or material cracking during the embossing and coining.
We'd love to Manufacture for you!
Submit the form below and our representative will be in touch shortly.
LOCATIONS
Global Sales Office
818, Preakness lane, Coppell, Texas, USA – 75019
Registered Office
10-A, First Floor, V.V Complex, Prakash Nagar, Thiruverumbur, Trichy-620013, Tamil Nadu, India.
Operations Office
9/1, Poonthottam Nagar, Ramanandha Nagar, Saravanampatti, Coimbatore-641035, Tamil Nadu, India. ㅤ
Other Locations
- Bhilai
- Chennai
- Texas, USA