Bending and Forming Stamping Services
We at Frigate utilize CNC-controlled bending for precise, repeatable results. Our forming process ensures tight tolerances in complex, high-strength materials and alloys.
Our Clients



































Advantages of Bending and Forming Stamping Services
Minimized Material Deformation
Precision-controlled bending reduces internal stress, limits deformation, and maintains material properties, which is crucial for high-performance components in demanding environments.
Consistent Repeatability
Automated forming processes ensure uniformity across large production batches, which is crucial for industries requiring high reliability and component interchangeability.
High-Speed Production
Advanced stamping machinery enables rapid material processing, reducing cycle times while maintaining strict dimensional accuracy in complex parts.
Improved Surface Finish
Bending and forming techniques produce smooth, defect-free surfaces, reducing the need for additional finishing operations like polishing or coating.
Precision Custom Bending and Forming Stamping Services
Production delays and inconsistent parts lead to costly inefficiencies. Custom bending and forming stamping tackles these challenges with precision and efficiency. Advanced CNC machines deliver accurate bends, even in complex designs, ensuring each part meets strict specifications. A broad range of metals, including high-strength alloys, is processed with tight tolerances. Automated technology maintains consistency, which is essential for large-scale production and repeatable quality. This method strengthens components by reducing stress points and minimizing failures. Smooth surface finishes reduce the need for additional processing, saving time and cutting costs while maintaining quality standards.

Get Your Quote Now
- Instant Quotation
- On-Time Delivery
- Affordable Cost
Our Bending and Forming Stamping Process






Choose suitable metals or alloys based on strength, flexibility, and application requirements, ensuring compatibility with the desired forming process.
Prepare custom dies and tooling to match the part's specific geometry and tolerances, ensuring precision and repeatability.
Input precise bending and forming parameters into CNC machines, including angles, dimensions, and force, to control the forming operations accurately.
Bend and shape the metal using hydraulic or mechanical presses. The material is formed through high-pressure tools following the programmed specifications.
Inspect each component using dimensional analysis tools to verify accuracy, checking for consistency with design tolerances and specifications.
Perform any necessary surface finishing, such as deburring sharp edges or polishing, to ensure the final product meets quality and aesthetic standards.
Bending and Forming Stamping Materials
The bending and forming stamping process demands precise control over shape and tolerances. Accurate tooling and machine settings are essential for achieving consistent results.
It offers high tensile strength and corrosion resistance. Due to its durability under stress and resistance to harsh chemicals, it is ideal for medical, food processing, and marine applications.
6061 is known for its structural strength and good machinability, while 5052 provides excellent formability and corrosion resistance. Both are widely used in aerospace for lightweight and high-strength requirements.
Provide excellent strength-to-weight ratio and heat resistance. Common in aerospace and medical industries for critical components that demand low weight and high fatigue resistance.
It offers high malleability and good corrosion resistance. C360 brass is used for precision parts requiring tight tolerances, while C260 is suitable for decorative and conductive applications.
The low carbon content allows for easy bending without cracking. It is suitable for general-purpose applications requiring a balance of strength, ductility, and weldability.
The high carbon content delivers increased hardness and wear resistance. It is used in springs and cutting tools where a tough, resilient edge is needed.
Excellent strength at high temperatures and extreme environments. Utilized in aerospace and chemical processing for components exposed to heat, corrosion, and stress.
C110 offers superior electrical conductivity with good thermal properties. It is common in electrical connectors, while C101 is used in high-purity, high-conductivity applications like RF and microwave components.
Known for its fatigue resistance and spring qualities. Used in electrical switches, contacts, and corrosion-resistant applications where consistent flexibility is required.
Extremely lightweight with good machinability, it is used for weight-sensitive applications, especially in automotive and aerospace, requiring a high strength-to-weight ratio.
Ensure Precise Bending of High-Strength or Thick Materials
Bending high-strength alloys and thick materials requires precise control to avoid cracks and deformations. Frigate uses custom tooling and optimized machine settings to ensure uniform force distribution during bending. Advanced techniques, such as controlled bending speeds and tailored radii, reduce the risk of material failure. By adjusting process parameters based on material properties, Frigate ensures dimensional accuracy and maintains the structural integrity of parts, even with challenging materials.

Compliance for Bending and Forming Stamping Services
Compliance for bending and forming stamping at Frigate ensures the highest industry standards for precision, durability, and safety. Every production stage adheres to specific certifications that guarantee quality and regulatory adherence. We follow strict guidelines, ensuring that materials, processes, and finished products meet the required specifications for performance and safety.
Certifies consistent quality control, ensuring precise and reliable manufacturing practices throughout stamping.
Guarantees compliance with automotive industry specifications for the stamped parts' safety, performance, and durability.
Restricts hazardous materials in manufacturing, ensuring environmentally friendly production processes that meet safety and health regulations.
Establishes material strength requirements, ensuring that stamped parts meet structural integrity and performance industry standards.
Ensures continuous improvement and defect prevention in manufacturing automotive components for enhanced quality and safety.
Certifies compliance for parts used in electrical applications, ensuring safety in flame-resistant and fire-retardant materials.
Ensures the safe use of chemicals and materials, promoting environmental and human safety in stamping production.

Tolerance for Bending and Forming Stamping Services
Tolerance for the material’s tendency to return to its original shape after bending.
Variation in the final length due to the material stretch during the bending process.
Tolerance for the distance from the edge to the bend's tangent line, ensuring accuracy in geometry.
Tolerance for relief areas to avoid material stress at bend points, ensuring part integrity.
Precision in hole placement in relation to the bend, critical for functional features.
Precision tolerance in the depth of drawn or formed features, ensuring consistent profiles.
Tolerance for the perpendicularity of features to adjacent surfaces, ensuring proper part alignment.
Tolerance for the angle of draft on formed parts, ensuring smooth extraction from tooling.
Precision tolerance for the length of formed flanges, critical for part assembly.
Variation in wall thickness across the formed part, ensuring consistent strength and material distribution.
Tolerance ensuring that stamped parts maintain proper nesting for stacking or assembly.

Quality Testing Standards for Bending and Forming Stamping Services
Measure bend angles to ensure they meet specified tolerances.
Test for material springback after bending to ensure precision and compensation.
Test the consistency of the bend radius to ensure smooth, uniform curves.
Test thickness at various points to ensure uniformity and compliance with standards.
Measure length, width, and height to verify conformity with dimensional specifications.
Measure flatness across the part to check for warping or distortion.
Test the hole diameter for dimensional accuracy, ensuring they meet tolerance.
Verify hole locations relative to part features, ensuring accurate alignment.
Measure the depth of formed areas to ensure precise geometry.
Test the perpendicularity of edges and surfaces to ensure alignment.
Check the dimensions and position of formed flanges to meet specified tolerances.
Test the tensile strength of the material to ensure it can withstand expected loads.
Measure the part's ability to withstand shock loading without fracture.
Test for smoothness, roughness, or defects on the part's surface.
Test the material's ability to be welded without defects post-forming.
Bending and Forming Stamping in Aviation Component Manufacturing
Achieving tight tolerances and structural integrity in aerospace components requires precise processes. Bending and forming stamping services use advanced tooling to ensure accurate material shaping. Custom dies, and optimal force application minimizes material deformation. Real-time monitoring adjusts parameters to maintain dimensional accuracy throughout production. These methods reduce material waste and eliminate rework. These solutions produce complex aerospace parts with high precision, meeting stringent industry standards efficiently and cost-effectively.







Industries We Serve
- Solid Progress
Our Manufacturing metrics
Frigate brings stability, control, and predictable performance to your sourcing operations through a structured multi-vendor system.

2.8X
Sourcing Cycle Speed
Frigate’s pre-qualified network shortens decision time between RFQ and PO placement.
94%
On-Time Delivery Rate
Structured planning windows and logistics-linked schedules improve project-level delivery reliability.
4X
Multi-Part Consolidation
We enable part family batching across suppliers to reduce fragmentation.
22%
Quality Rejection Rate
Multi-level quality checks and fixed inspection plans lower non-conformities.
30%
Procurement Costs
Optimized supplier negotiations and bulk order strategies reduce your overall sourcing expenses.
20%
Manual Processing Time
Automation of sourcing and supplier management significantly reduces time spent on manual tasks.
Minimize Springback and Achieve Accurate Part Dimensions
Springback, where material tries to return to its original shape after bending, can cause parts to fall out of tolerance. To address this, Frigate employs overbending techniques, where the material is bent slightly beyond the desired angle to compensate for spring back. Precision tooling and real-time force adjustments further minimize this issue. These methods help ensure parts remain within specifications, reducing the need for costly rework and ensuring consistent quality throughout production.

Get Clarity with our Manufacturing Insights
- Real Impact
Words from Clients
See how global OEMs and sourcing heads describe their experience with our scalable execution.
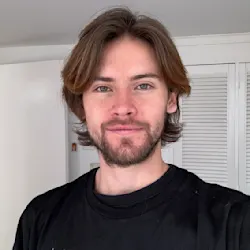
“Quick turnaround and solid quality.”
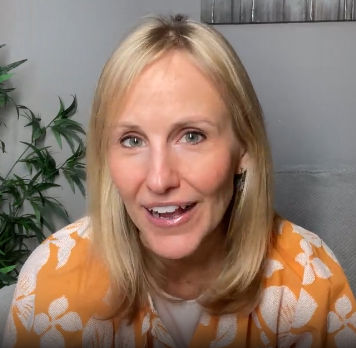
“The instant quote tool saved us time, and the parts were spot-on. Highly recommend Frigate!”
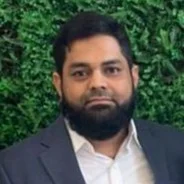
“I would strongly recommend Frigate to anyone who wants to do Rapid Prototyping, and take their ideas to manufacturing. One firm doing all kinds of Product Development!”
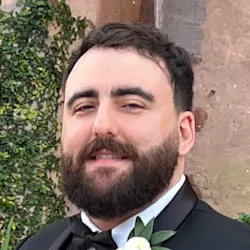
“Great service, fair price, and the parts worked perfectly in our assembly.”
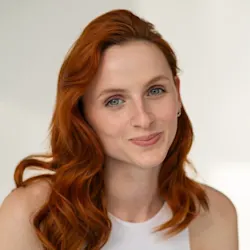
“Top-notch machining and fast shipping. Very satisfied with the results.”
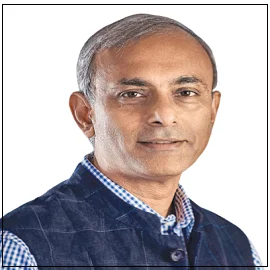
“The next disruption is happening in Prototyping & Manufacturing on-demand and Frigate is leading the way! I personally believe the Frigate's way of IIOT enabled cloud platform with Al.”
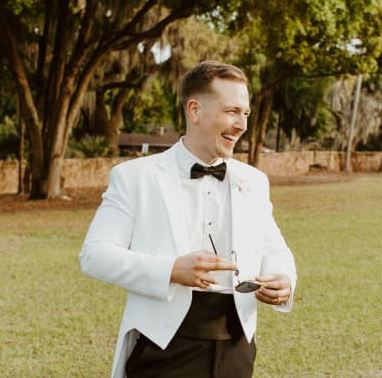
“Frigate delivered high-quality parts at a competitive price. The instant quote tool is a huge plus for us!”

“We appreciate the precision and quality of the machined components in the recent delivery—they meet our specifications perfectly and demonstrate Frigate’s capability for excellent workmanship.”
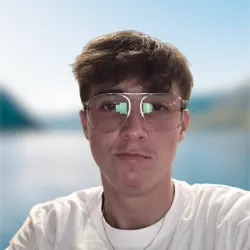
“Flawless execution from quote to delivery.”

“I am absolutely happy to work with supplier like Frigate who were quite proactive & result oriented . Frigate has high willingness team who has strong know how & their passion towards the products & process were absolutely thrilling.”
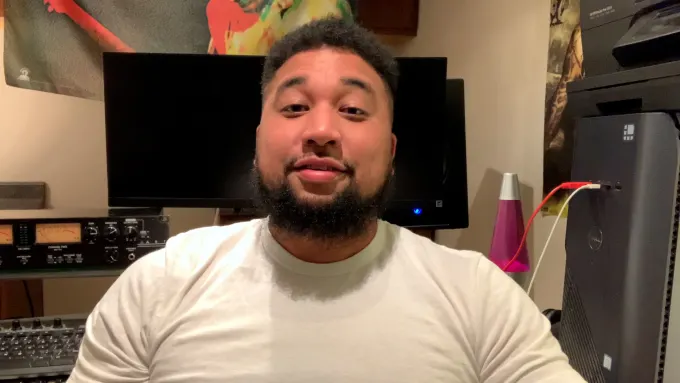
“The precision on these parts is impressive, and they arrived ahead of schedule. Frigate’s process really stands out!”
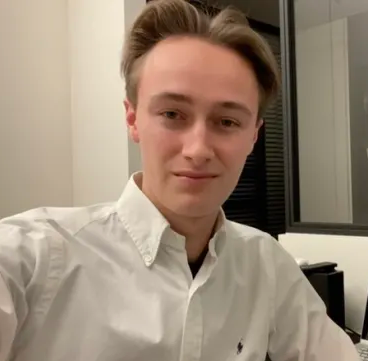
“Parts were exactly as spec’d, and the instant quote made budgeting a breeze.”
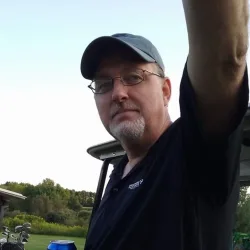
“Good value for the money.”
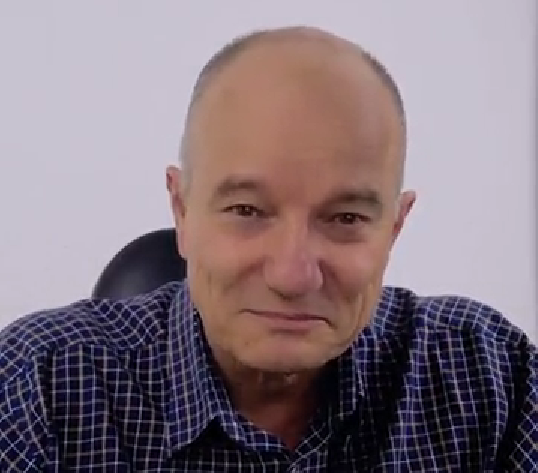
“The finish was perfect, and the team was easy to work with.”

“Working with Frigate has been great. Their proactive, results-driven approach and expertise shine through in every project. It's been a pleasure collaborating with them.”

"We are highly satisfied with the timely delivery and quality of the MIG Welding Cable from Frigate. Their attention to detail, secure packaging, and quick responsiveness stood out. We confidently recommend Frigate Engineering Services Pvt. Ltd. as a reliable manufacturing partner."
Having Doubts? Our FAQ
Check all our Frequently Asked Question
Precision bending and forming ensure parts retain their structural integrity by minimizing stress concentrations and maintaining material strength, which is crucial for aerospace, automotive, and heavy machinery applications.
Strain hardening increases material strength during bending and forming, enhancing part durability and resistance to wear while preventing deformation and ensuring long-term performance in demanding applications.
Adaptive tooling and variable pressure control compensate for thickness variations, ensuring uniform deformation across the part, preventing distortion, and maintaining consistent geometry throughout the forming process.
Techniques like overbending, precise control of tool radii, and real-time force feedback from advanced machinery minimize spring back, ensuring parts stay within the required specifications post-forming.
Material selection, combined with precise control of tool geometry and forming speed, reduces the risk of wrinkling and tearing by allowing for uniform material flow during complex deep-drawing operations.
We'd love to Manufacture for you!
Submit the form below and our representative will be in touch shortly.
LOCATIONS
Global Sales Office
818, Preakness lane, Coppell, Texas, USA – 75019
Registered Office
10-A, First Floor, V.V Complex, Prakash Nagar, Thiruverumbur, Trichy-620013, Tamil Nadu, India.
Operations Office
9/1, Poonthottam Nagar, Ramanandha Nagar, Saravanampatti, Coimbatore-641035, Tamil Nadu, India. ㅤ
Other Locations
- Bhilai
- Chennai
- Texas, USA