Precision Grinding Services
Frigate delivers precision grinding services with top-tier craftsmanship, ensuring accurate results that meet strict tolerances. Our reliability and expertise guarantee timely completion, tailored to your exact specifications.
Get Your Quote Now
- Instant Quotation
- On-Time Delivery
- Affordable Cost
Precision Grinding for Custom Requirements
Frigate’s precision grinding team brings years of expertise across various surface grinding techniques, ensuring each part meets exacting standards. Our specialists assess each project to determine the best grinding method for optimal results, adapting processes to suit complex or hard-to-grind surfaces. With extensive experience in all forms of surface grinding, we handle everything from simple flat surfaces to intricate components. Frigate is equipped to meet and exceed demanding expectations with precision and efficiency on every project.

Ensuring Consistency through Rigorous Process Control
Modern grinding machines equipped with advanced software allow for precise control over grinding parameters. This technology enables the achievement of ultra-fine finishes and micro-tolerances essential for high-performance applications.
Implementing stringent process control measures ensures consistency throughout the grinding operation. Regular monitoring and adjustment of parameters help maintain the required specifications, reducing variability and ensuring quality.
Employing specialized abrasive materials designed for specific applications enhances the grinding process. These materials are tailored to achieve desired surface finishes while maintaining the part's integrity.

Implementing Advanced Cooling Techniques to Mitigate Heat Effects
Creating tailored grinding strategies for hard and heat-sensitive materials minimizes the risk of defects. Approaches considering material properties and required tolerances lead to more effective grinding outcomes.
Utilizing precision cooling techniques during grinding operations helps manage heat generation. Effective cooling reduces the risk of thermal damage, preserving material properties and surface integrity.
Performing thorough material analysis before grinding ensures the selection of appropriate tools and techniques. Understanding material characteristics allows for better planning and execution of grinding processes.

Expanding Capabilities with Advanced Multi-Axis Equipment
Streamlining multi-axis grinding enhances productivity and reduces lead times. Optimizing workflows and using advanced programming techniques ensure intricate designs are processed efficiently.
Employing technicians with expertise in multi-axis grinding ensures effective use of advanced machinery. Their knowledge helps optimize processes and achieve precise results on complex components.
Offering ongoing training and development opportunities for operators enhances their skills in handling multi-axis operations. This commitment to personnel ensures high standards in precision grinding services at Frigate.

Precision Grinding Materials
Precision grinding is a critical manufacturing process that accurately removes material. It relies on appropriate techniques and equipment to meet specific requirements.
Metals
Tool steels' high hardness and wear resistance make them ideal for precision grinding applications. Various grades can be optimized for specific hardness and toughness requirements.
Corrosion resistance and strength are key properties of stainless steel. Precision grinding of these materials requires attention to heat generation and surface finish to prevent oxidation.
Lightweight and corrosion-resistant, aluminum alloys require specialized grinding techniques to achieve smooth finishes and precise dimensions without warping.
Ceramics
Materials like alumina are ground to achieve tight tolerances and excellent surface finishes, and they are often used in aerospace and medical applications.
These materials, such as silicon nitride, offer high strength and wear resistance, making them suitable for grinding applications in demanding environments.
Composites
Precision grinding of CFRP requires specialized techniques to prevent delamination and ensure dimensional accuracy. This material is often used in the aerospace and automotive industries.
Similar to CFRP, GFRP requires careful handling during grinding to maintain structural integrity and achieve desired finishes.
Hard Metals
These materials are typically ground using diamond wheels to achieve precise dimensions and fine surface finishes, which are essential for tooling applications.
Other Materials
Engineering plastics like nylon and PEEK can be ground for applications requiring tight tolerances and specific surface finishes. Proper grinding techniques must be applied to prevent melting or distortion.
Materials such as Inconel and Hastelloy are difficult to grind due to their toughness and heat resistance. Specialized grinding strategies are necessary to achieve the desired tolerances and finishes without compromising the material properties.
Enhancing Surface Quality and Tolerance Precision
Effective strategies are essential to achieving uniform surface quality and tight dimensional tolerances in precision grinding. Regular monitoring of grinding parameters is crucial for maintaining consistency. Implementing precise feed rate controls helps ensure even material removal, while proper coolant delivery minimizes heat generation, preventing thermal distortion of the workpiece.
Additionally, advanced grinding wheel technology can enhance cutting efficiency and extend tool life. Accurate machine calibration and setup play a vital role in ensuring precision. By focusing on these strategies, Frigate delivers high-quality precision grinding services that consistently meet performance and reliability standards.

- Real Impact
Words from Clients
See how global OEMs and sourcing heads describe their experience with our scalable execution.
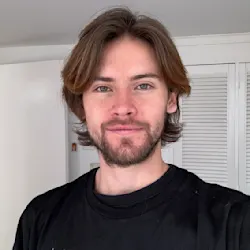
“Quick turnaround and solid quality.”
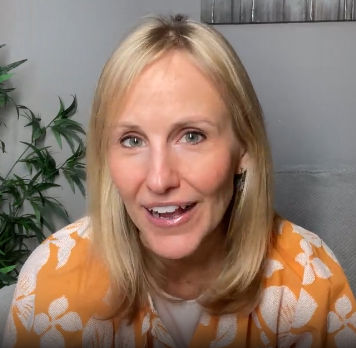
“The instant quote tool saved us time, and the parts were spot-on. Highly recommend Frigate!”
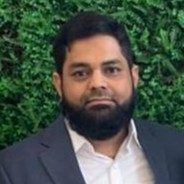
“I would strongly recommend Frigate to anyone who wants to do Rapid Prototyping, and take their ideas to manufacturing. One firm doing all kinds of Product Development!”
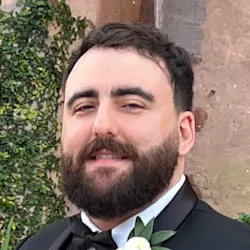
“Great service, fair price, and the parts worked perfectly in our assembly.”
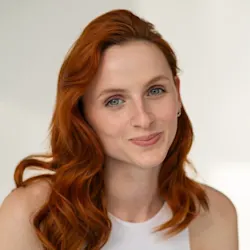
“Top-notch machining and fast shipping. Very satisfied with the results.”
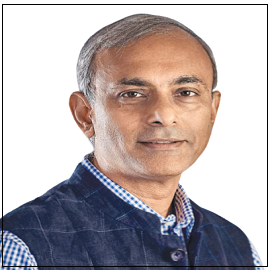
“The next disruption is happening in Prototyping & Manufacturing on-demand and Frigate is leading the way! I personally believe the Frigate's way of IIOT enabled cloud platform with Al.”
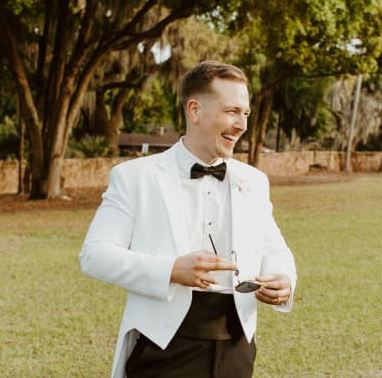
“Frigate delivered high-quality parts at a competitive price. The instant quote tool is a huge plus for us!”

“We appreciate the precision and quality of the machined components in the recent delivery—they meet our specifications perfectly and demonstrate Frigate’s capability for excellent workmanship.”
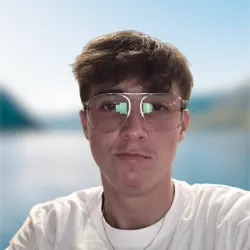
“Flawless execution from quote to delivery.”

“I am absolutely happy to work with supplier like Frigate who were quite proactive & result oriented . Frigate has high willingness team who has strong know how & their passion towards the products & process were absolutely thrilling.”
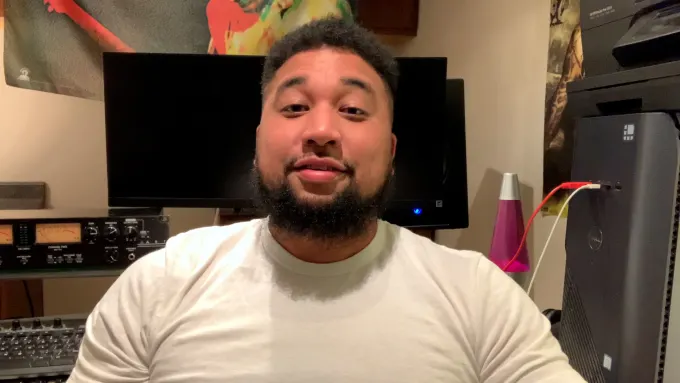
“The precision on these parts is impressive, and they arrived ahead of schedule. Frigate’s process really stands out!”
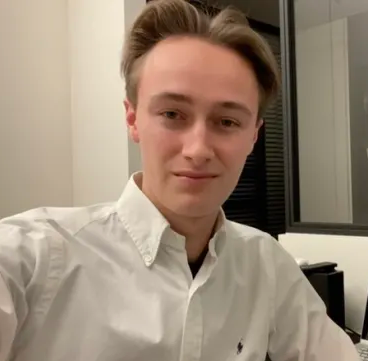
“Parts were exactly as spec’d, and the instant quote made budgeting a breeze.”
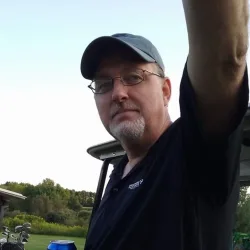
“Good value for the money.”
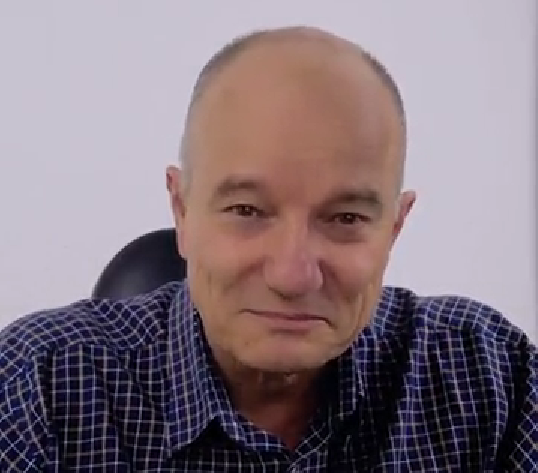
“The finish was perfect, and the team was easy to work with.”

“Working with Frigate has been great. Their proactive, results-driven approach and expertise shine through in every project. It's been a pleasure collaborating with them.”

"We are highly satisfied with the timely delivery and quality of the MIG Welding Cable from Frigate. Their attention to detail, secure packaging, and quick responsiveness stood out. We confidently recommend Frigate Engineering Services Pvt. Ltd. as a reliable manufacturing partner."
Having Doubts? Our FAQ
Check all our Frequently Asked Question
Tool wear can significantly affect precision grinding outcomes. Frigate employs advanced monitoring systems to track tool conditions in real time. This enables timely adjustments and replacements, ensuring consistent surface quality and dimensional accuracy throughout grinding.
Grinding complex geometries requires precise setups and specialized tooling. Frigate utilizes advanced multi-axis grinding machines and tailored fixtures to accommodate intricate designs. This approach minimizes errors and maintains tight tolerances, ensuring high-quality results for challenging components.
Excessive heat during grinding can lead to thermal distortion. At Frigate, effective coolant application and temperature monitoring are critical. High-performance coolant systems are implemented to maintain optimal temperatures, preserving the integrity and accuracy of the workpiece throughout the grinding process.
Different materials respond uniquely to grinding. Frigate employs specific grinding techniques tailored to each material type, including optimized feed rates and wheel selection. This ensures that surface finishes remain uniform and meet stringent specifications, regardless of material properties.
Maintaining tight tolerances requires meticulous calibration and process control. Frigate implements regular calibration of grinding machines and employs advanced measurement tools to monitor dimensions throughout the process. This rigorous approach guarantees that all components meet precise tolerances and quality standards.
Manufacturing Capability/Capacity
Ferrous casting
Mold size(max): 1m X 1m
Weight Range: 1 KG ~ 30 KGS
Mold size(max): 1.5m X 1.5m
Weight Range: 30 KG ~ 150 KGS
Mold size(max): 3m X 3m
Weight Range: 100 KG ~ 1000 KGS
Mold size(max): 500 MM X 500 MM
Weight Range: 0.250 KG ~ 20 KGS
Mold size(max): 500 MM X 500 MM
Weight Range: 0.100 KG X 20 KGS
Non-ferrous casting
Capacity: 5000 MT/a
Range of weight: 100 gm to 20 KGS
Mold size(max): 1 M X 1 M
Weight Range: 0.5 KG X 50 KGS
Mold size(max): 1 M X 1 M
Weight Range: 0.5 KG X 50 KGS
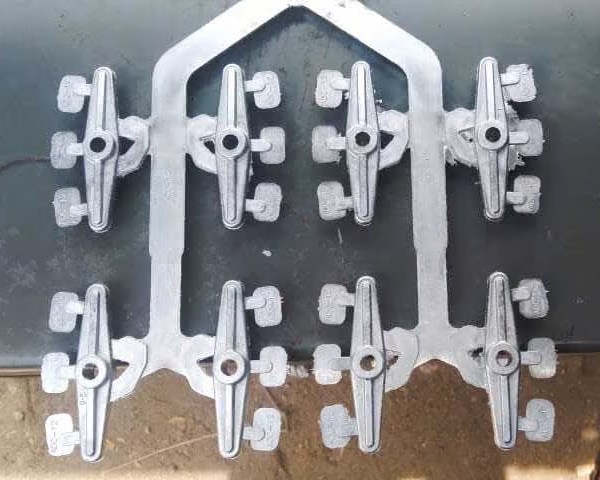
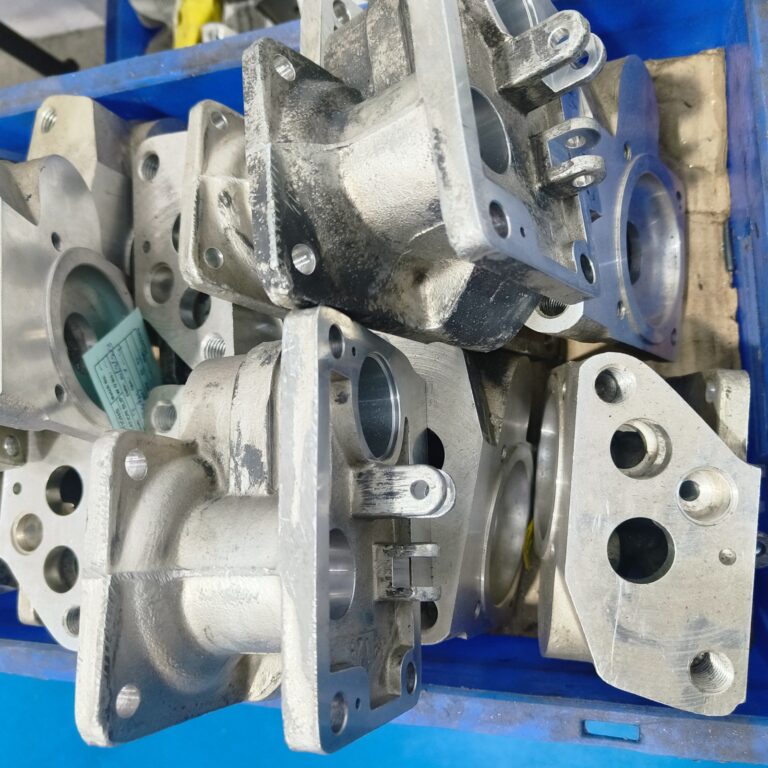
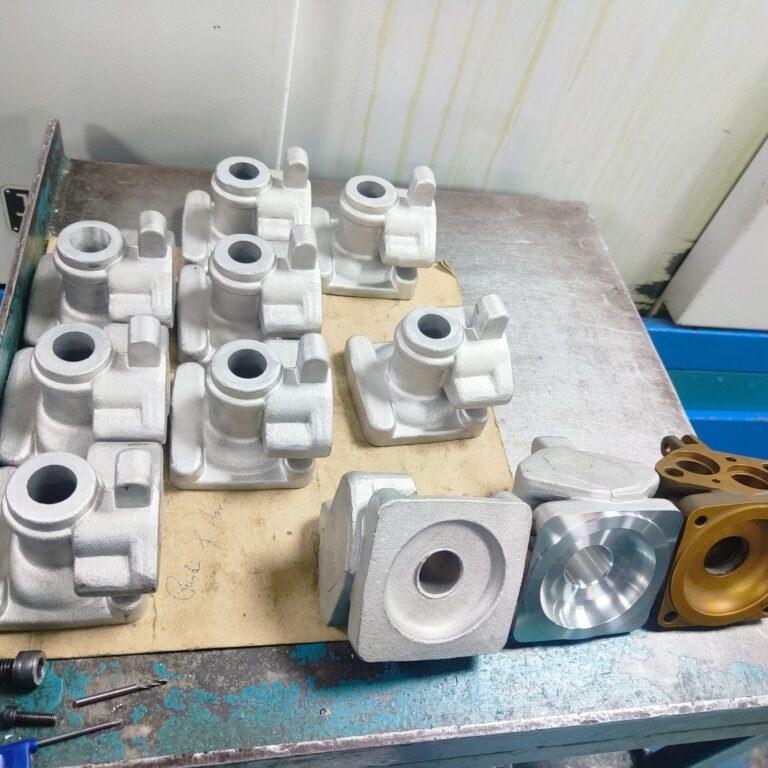
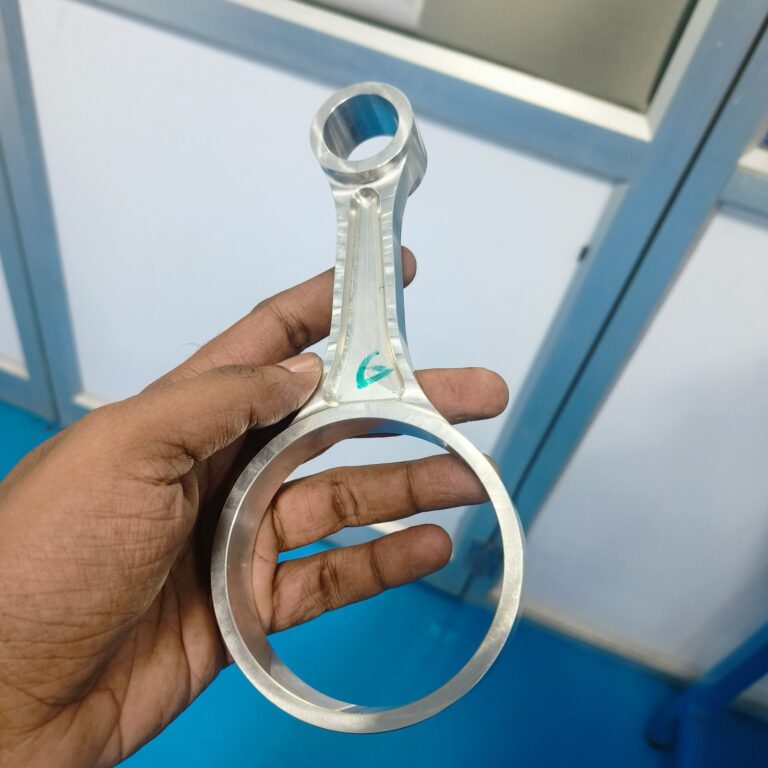
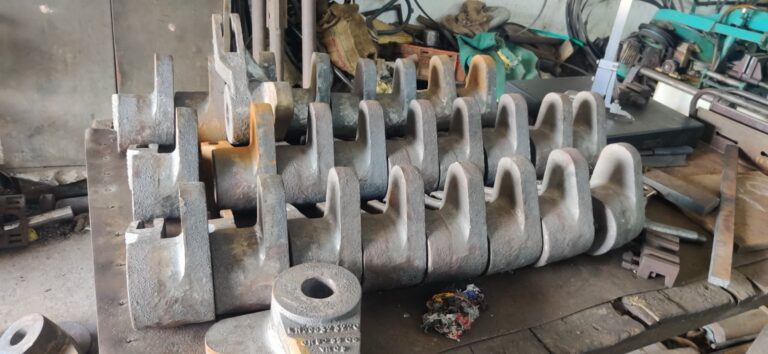
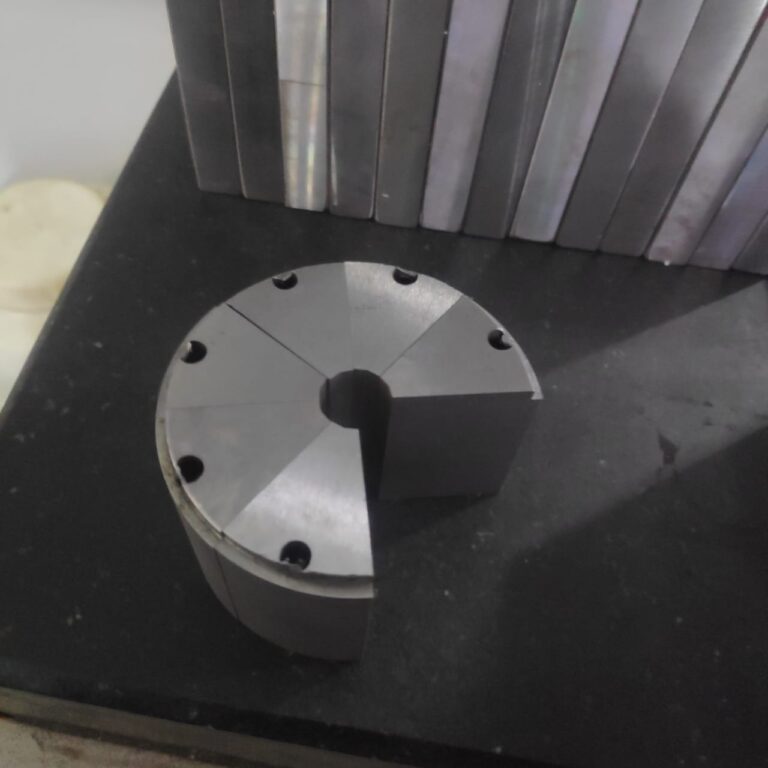
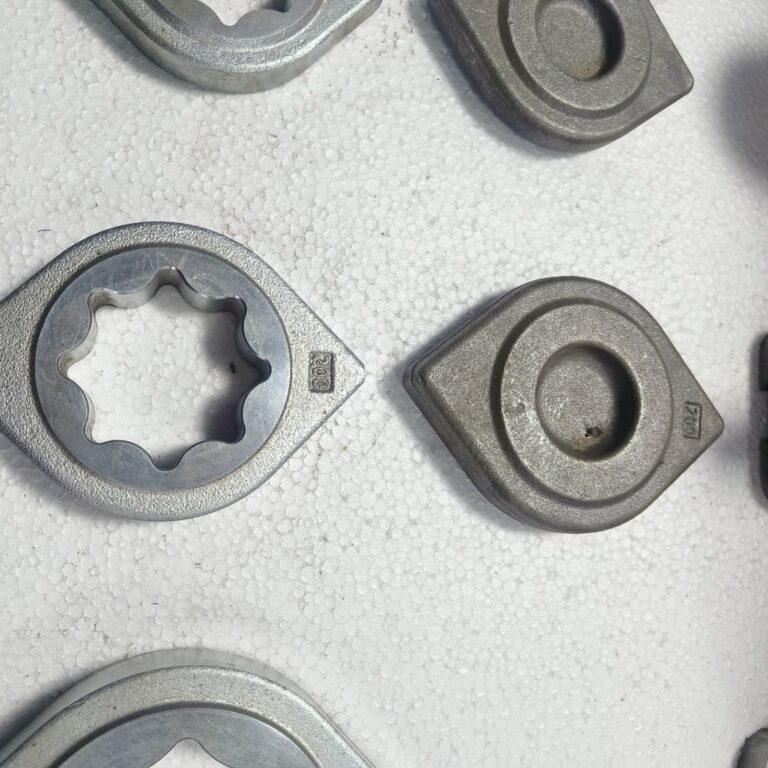
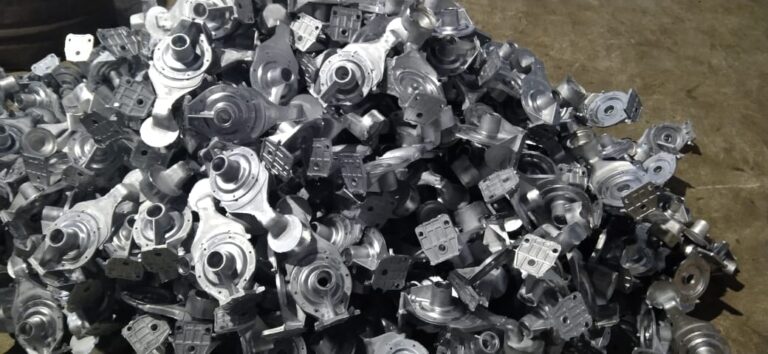
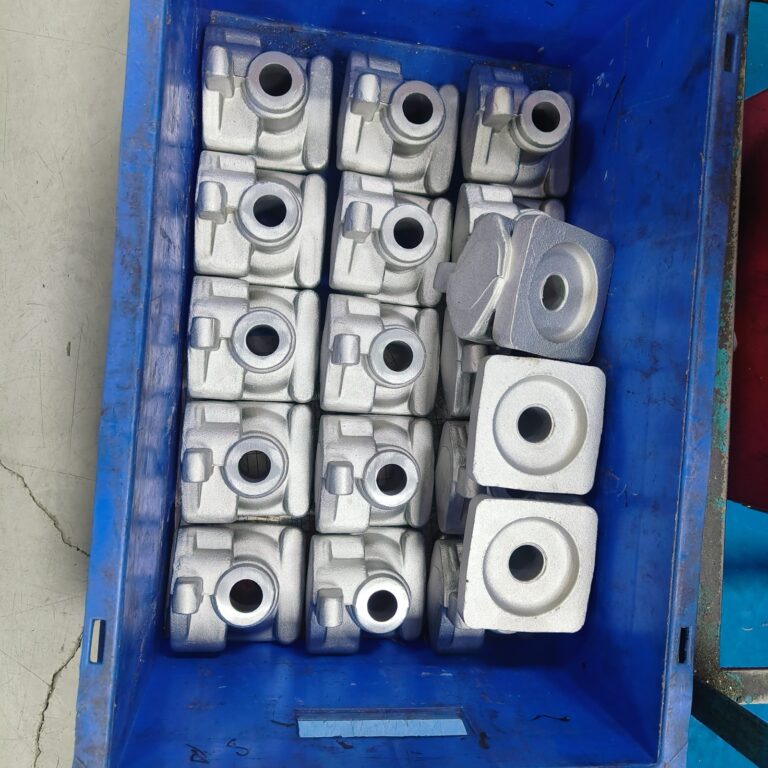
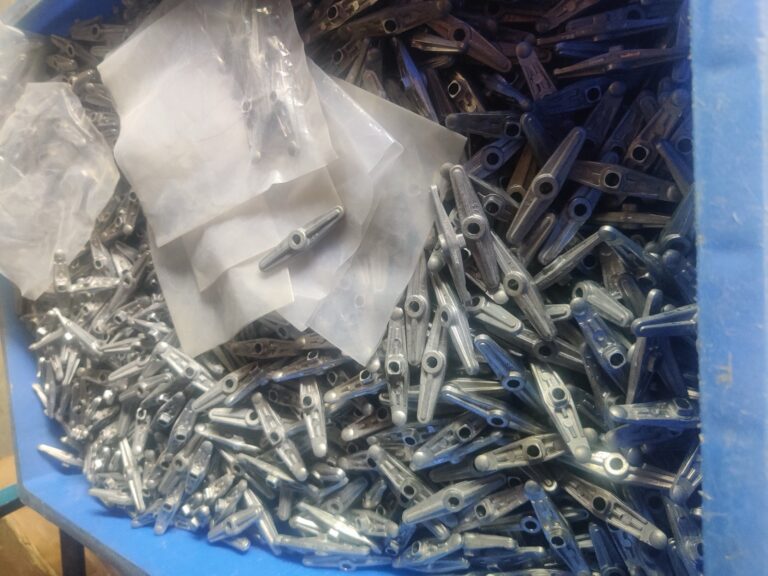
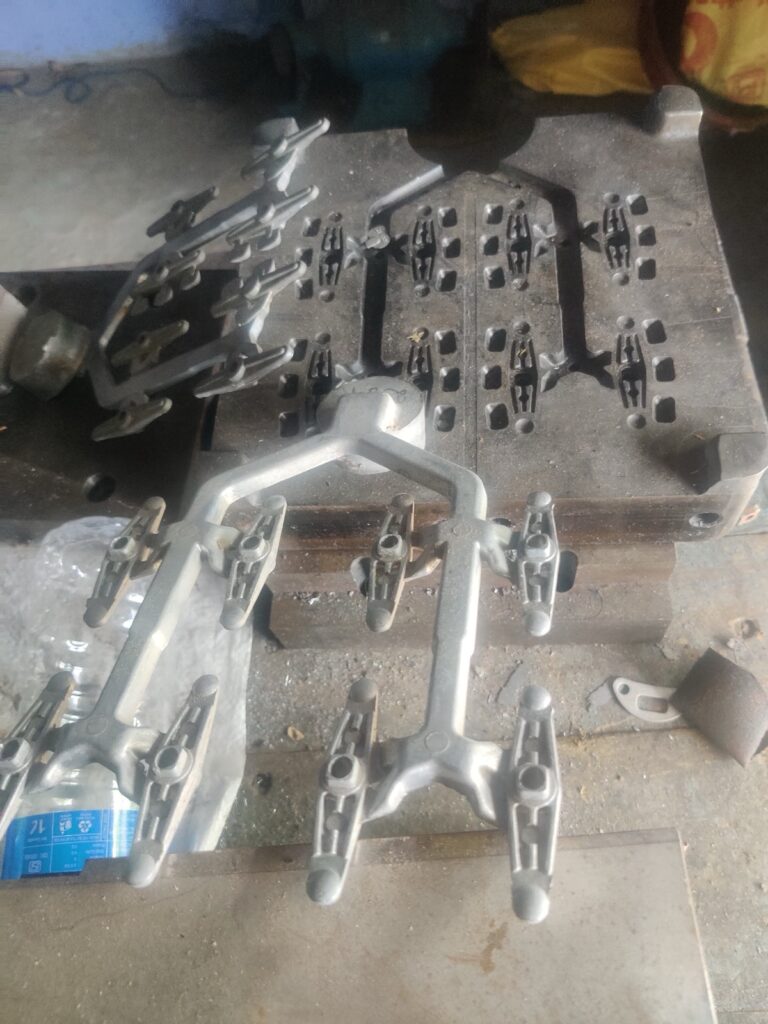
Forging
Capacity: 20,000 Tons per Annum
Range of weight: 300 KG to 1 Ton
Hammering: 5 Ton
Range of weight: 0.2 KG to 200 KGS
Hammering: 1600 Ton Hydraulic press
Ring size: 350 MM OD to 3000 MM OD
Range of weight: 15 KGS to 3200 KGS
Materials
Carbon Steel, Stainless Steel (AUSTENITE), Alloy Steel, Stainless Steel (MARTENSITE), etc.
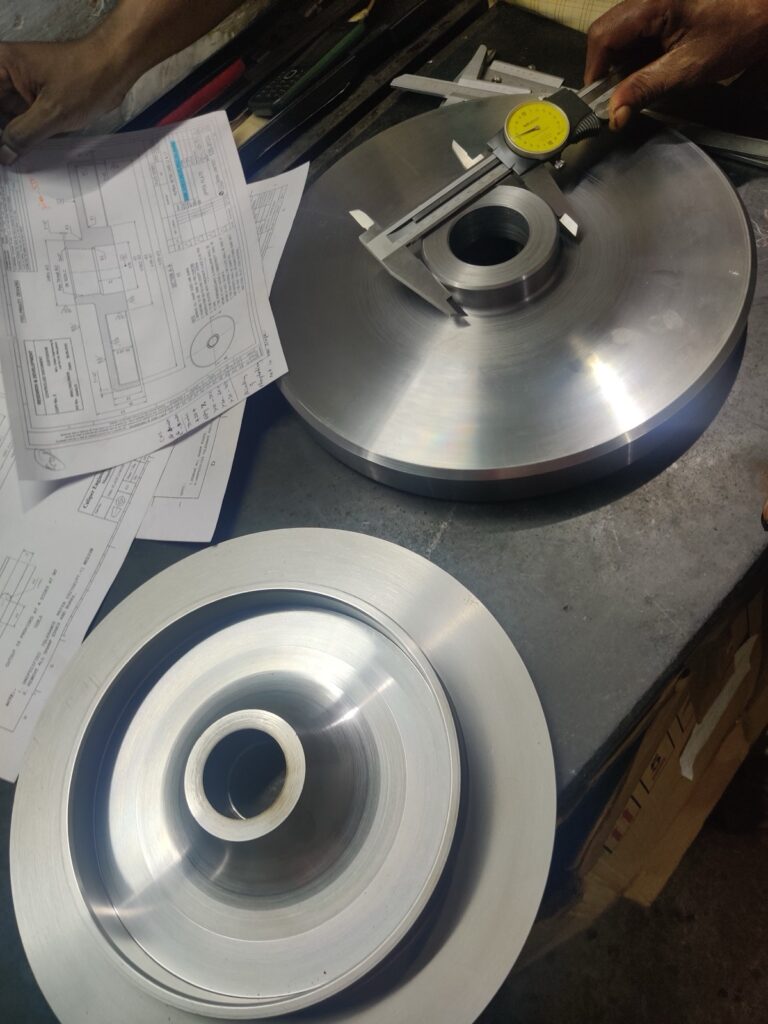
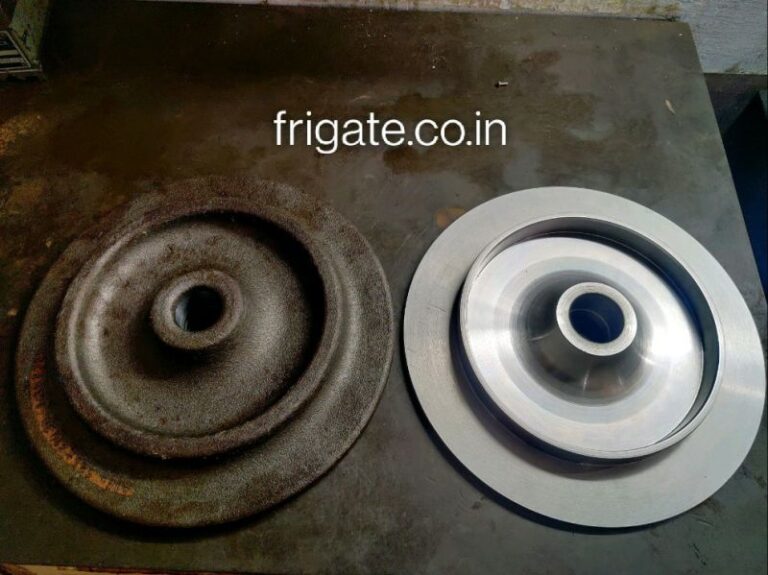
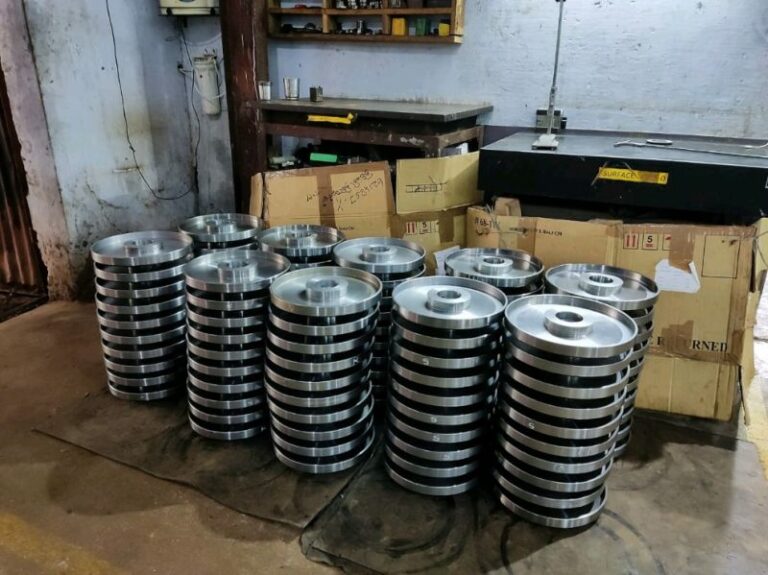
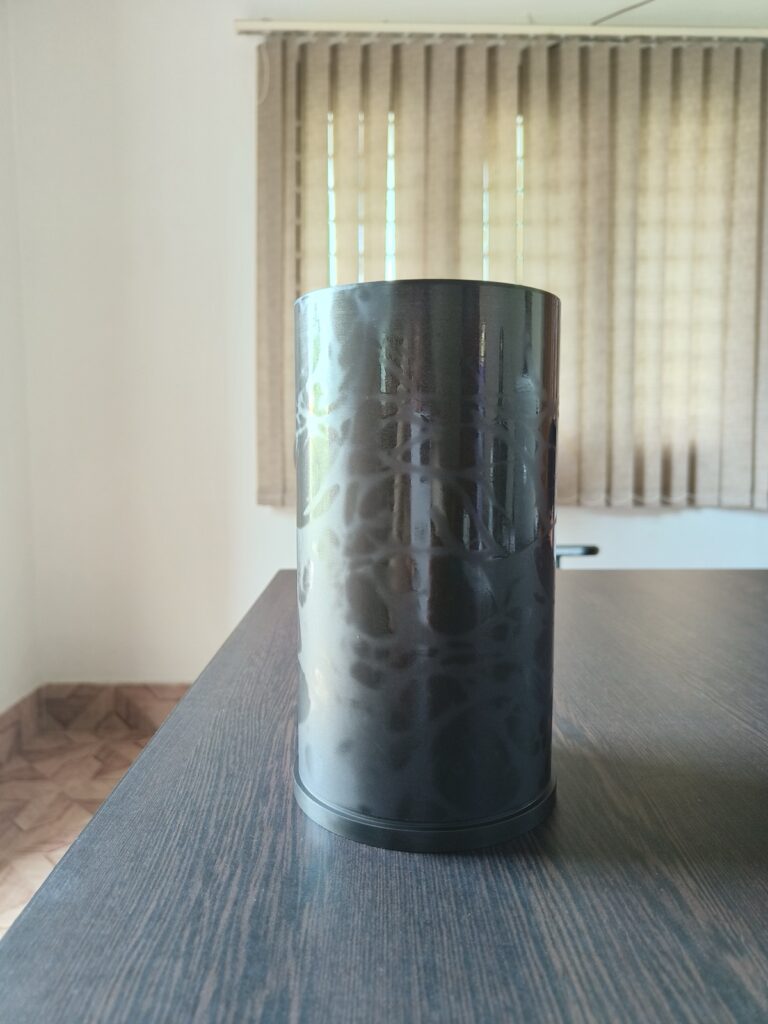
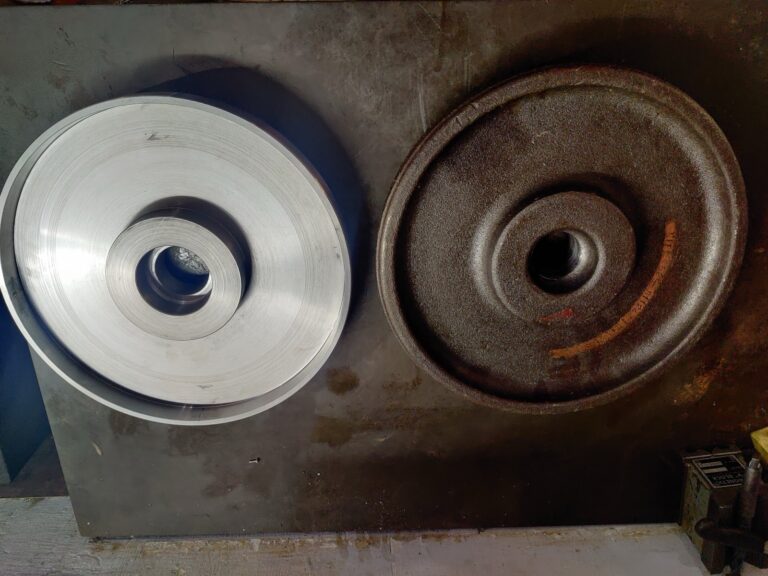
Machining
1 to 1000 MM
1 to 1000 MM
1 to 1000 MM
Materials
Steel, Aluminum, Brass, Copper, Titanium, Nickel Alloys, Tungsten Carbide, etc.
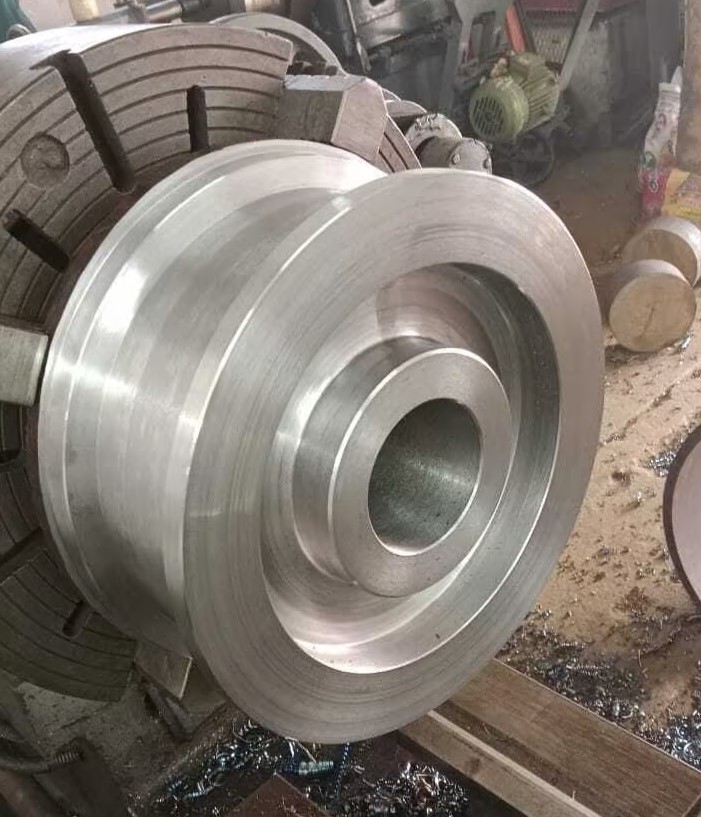
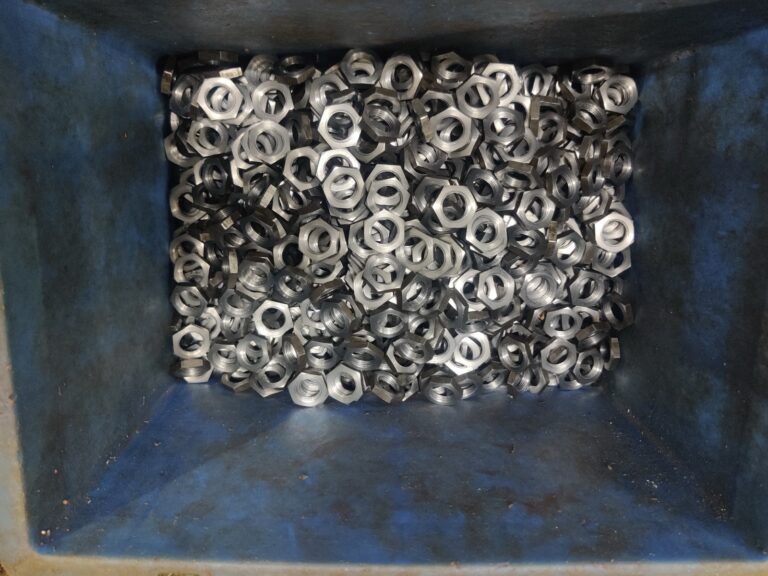
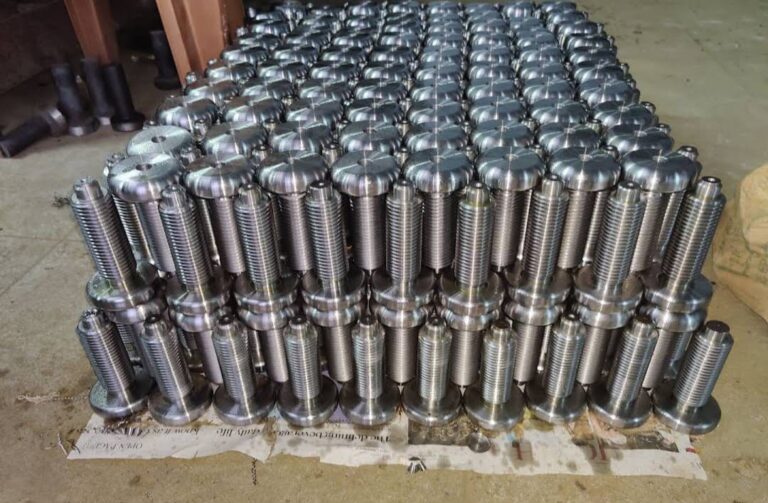
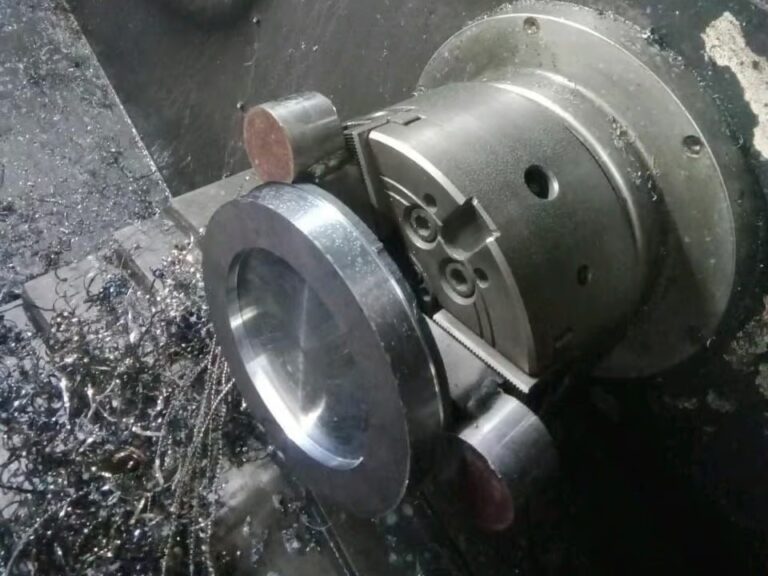
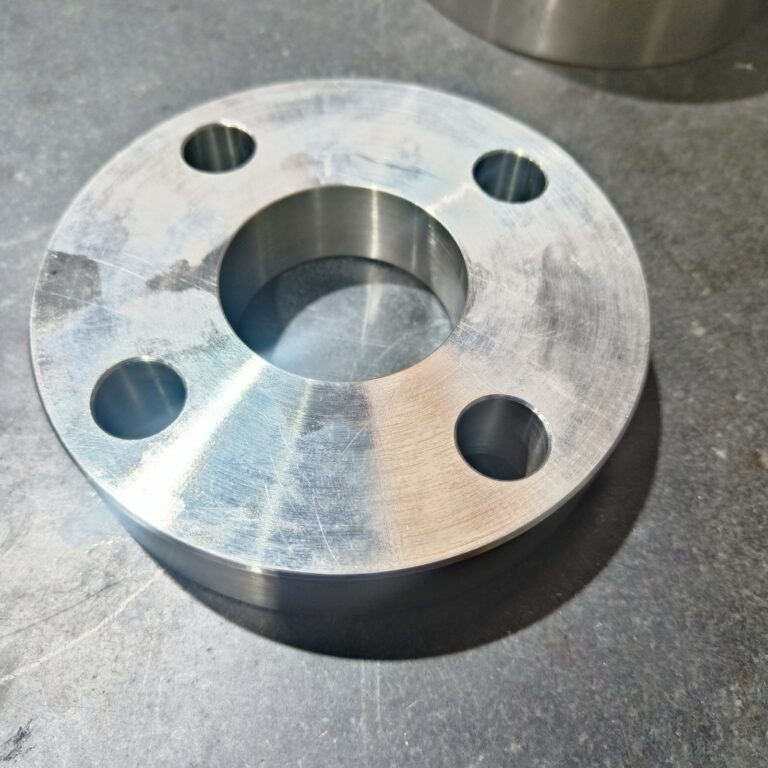
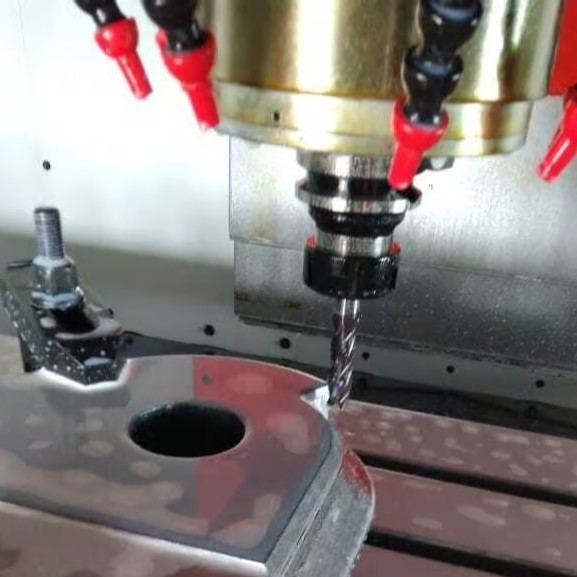
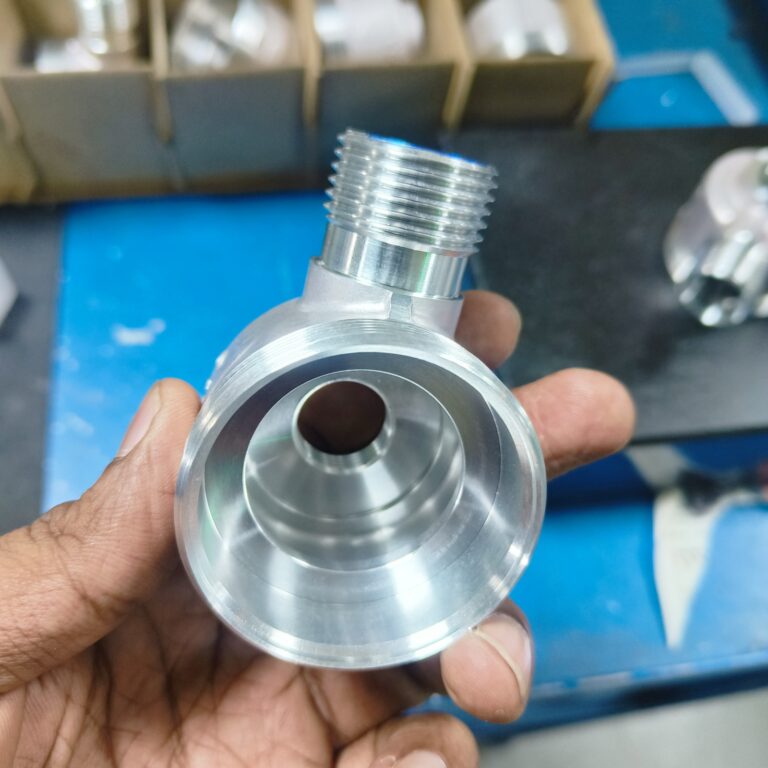
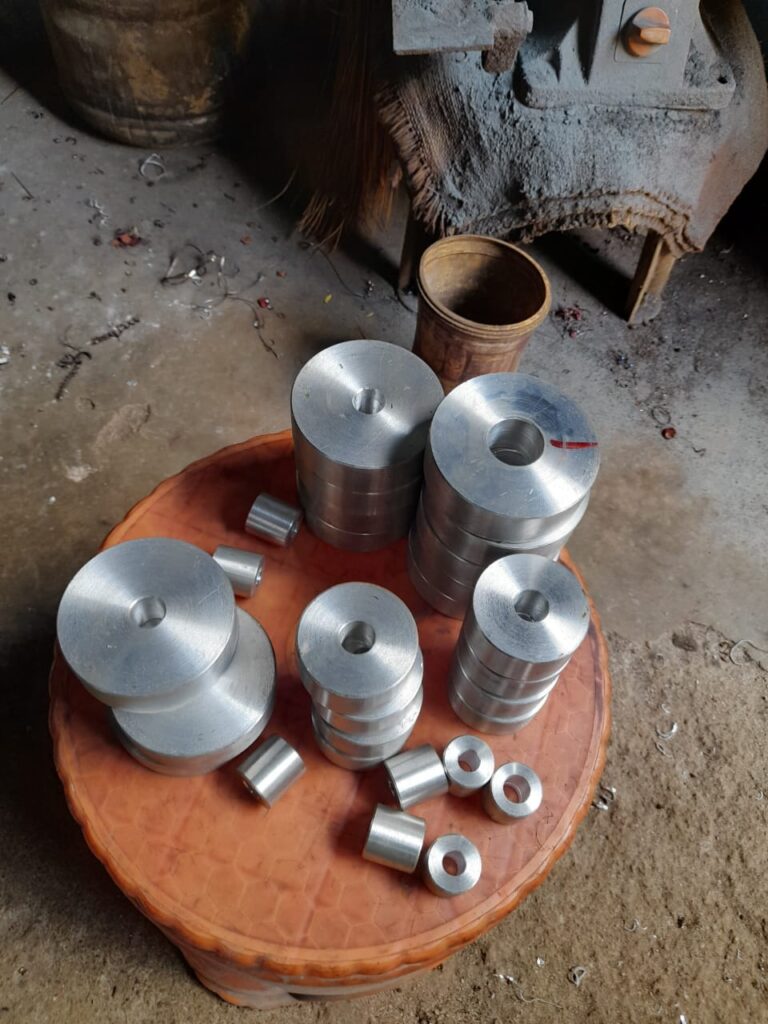
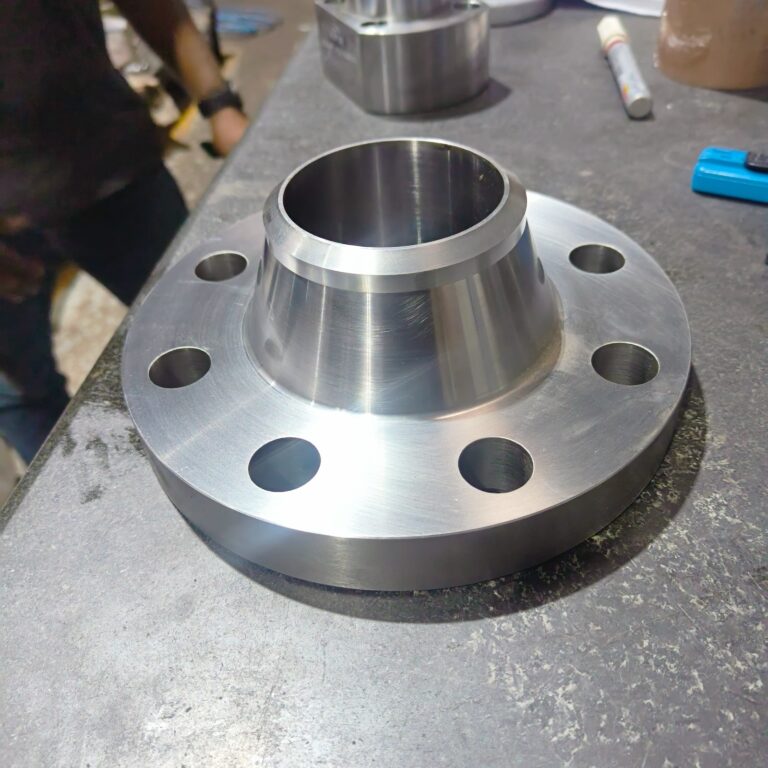
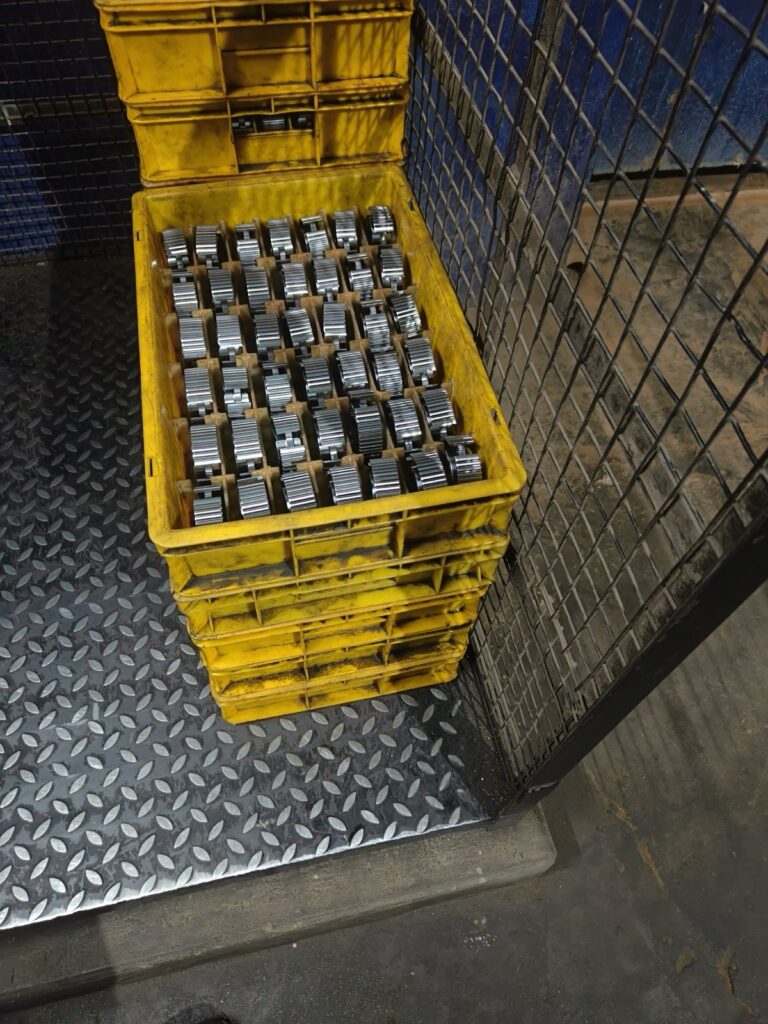
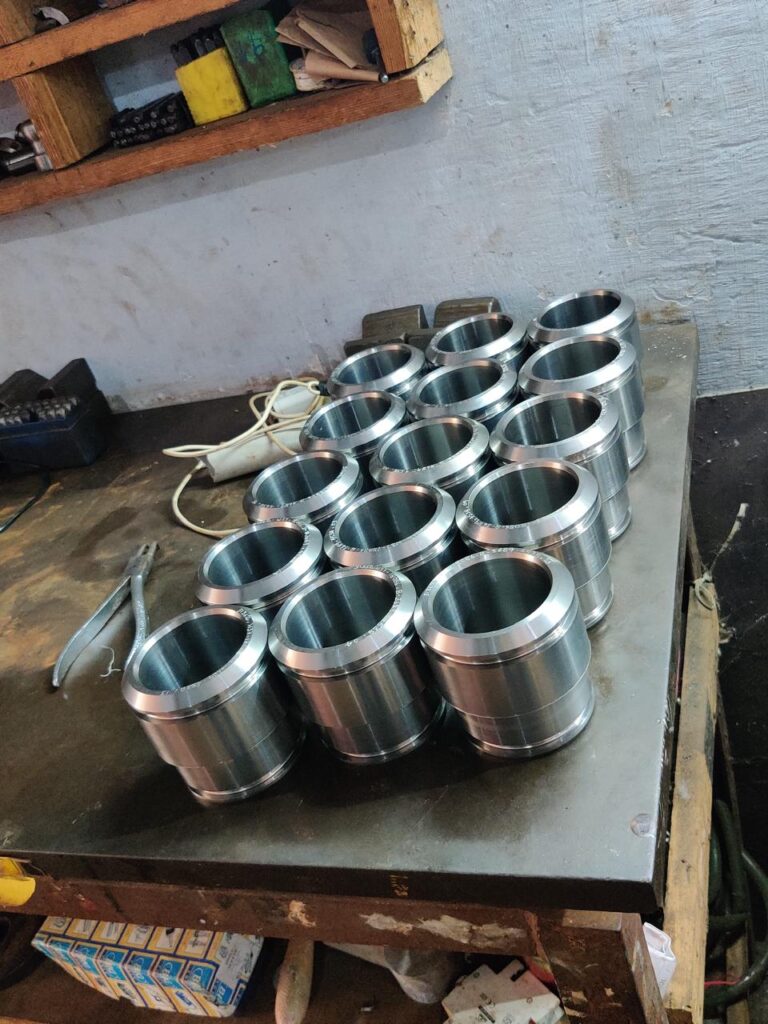
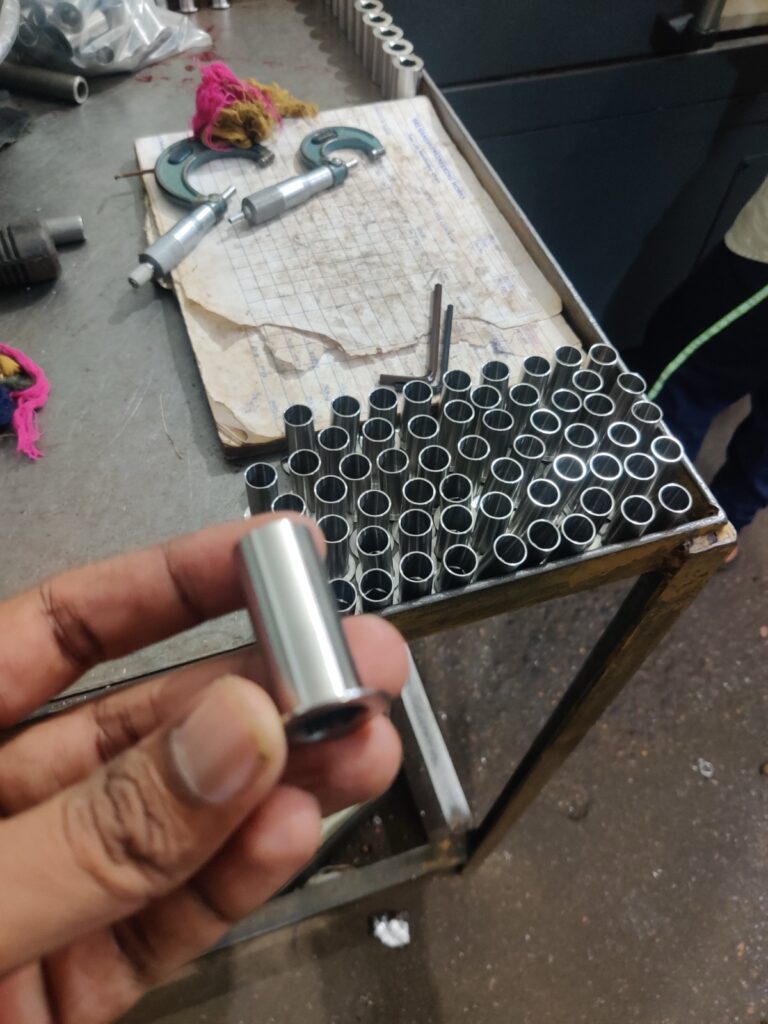
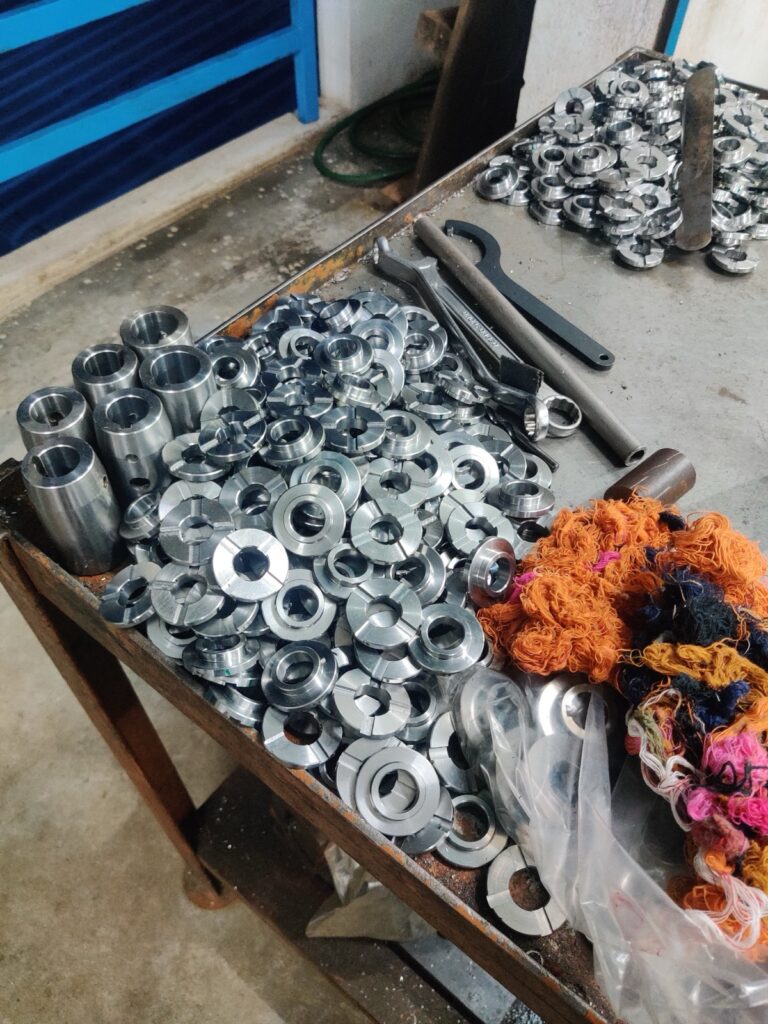
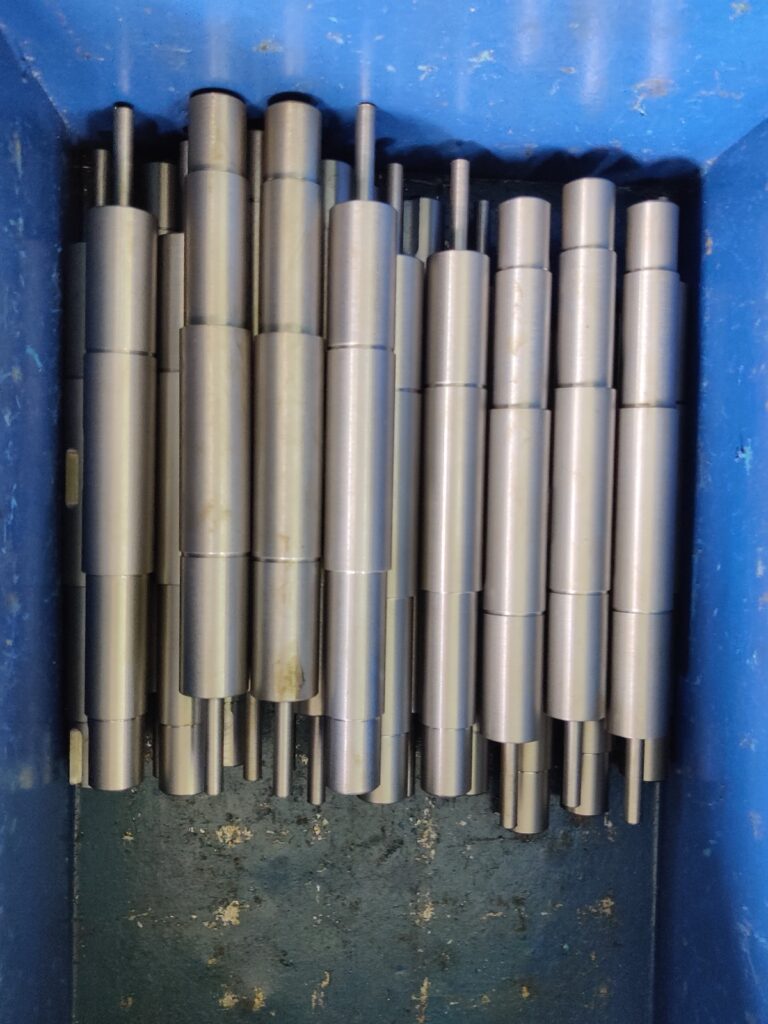
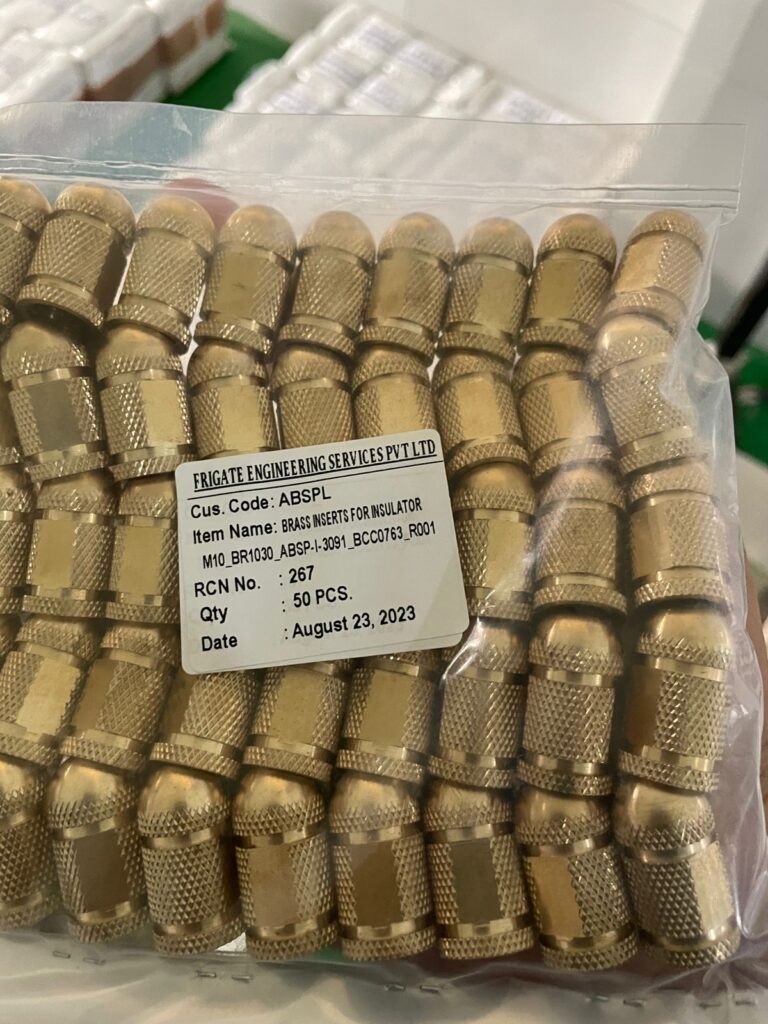
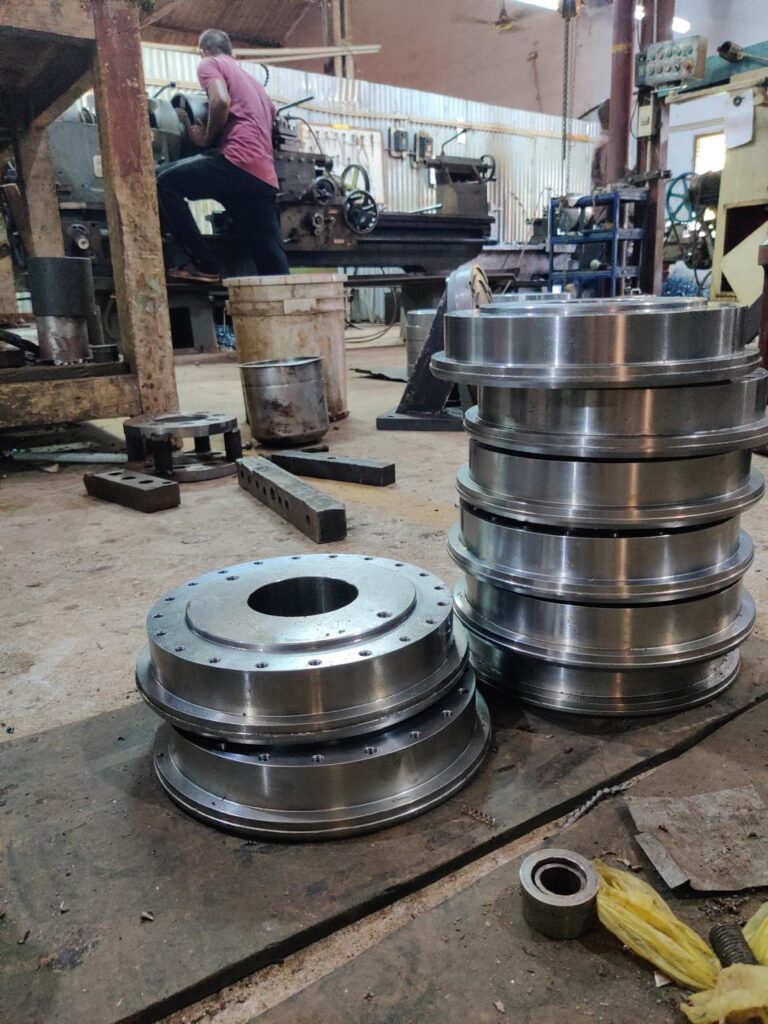
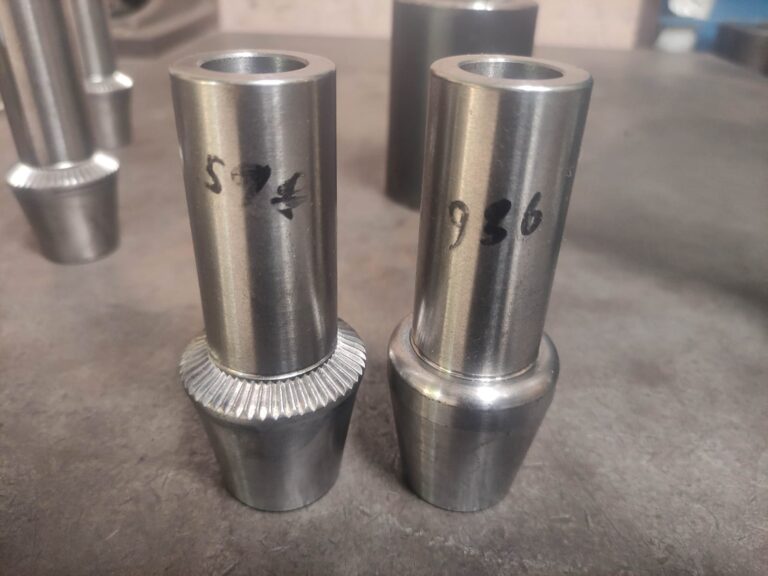
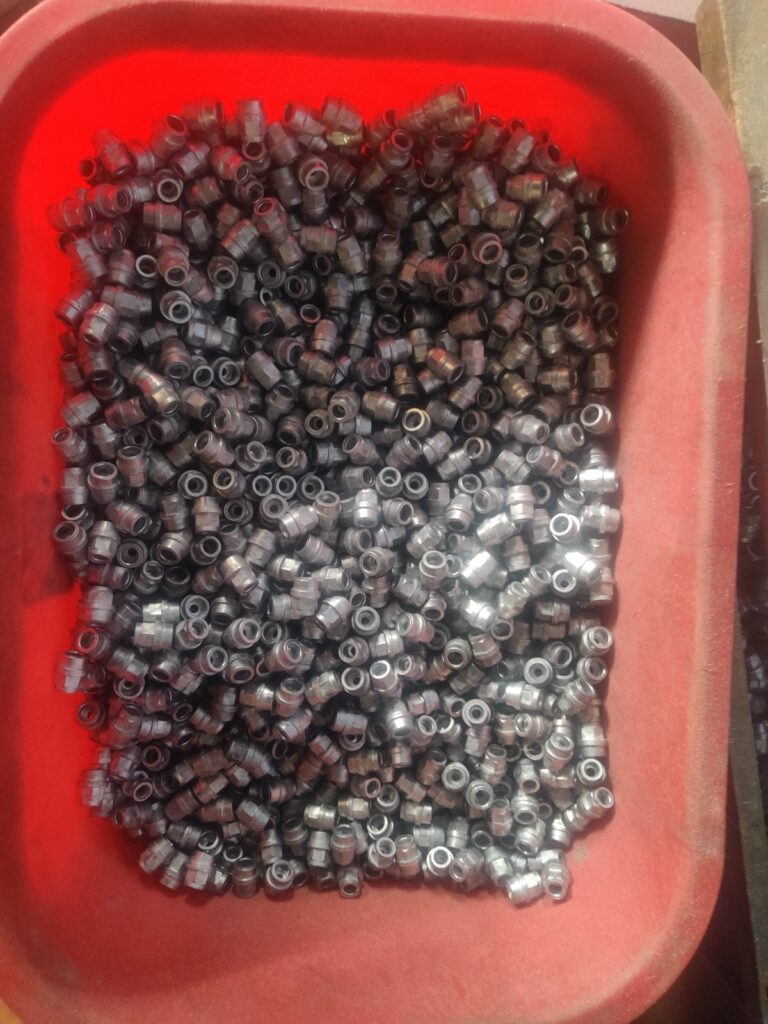
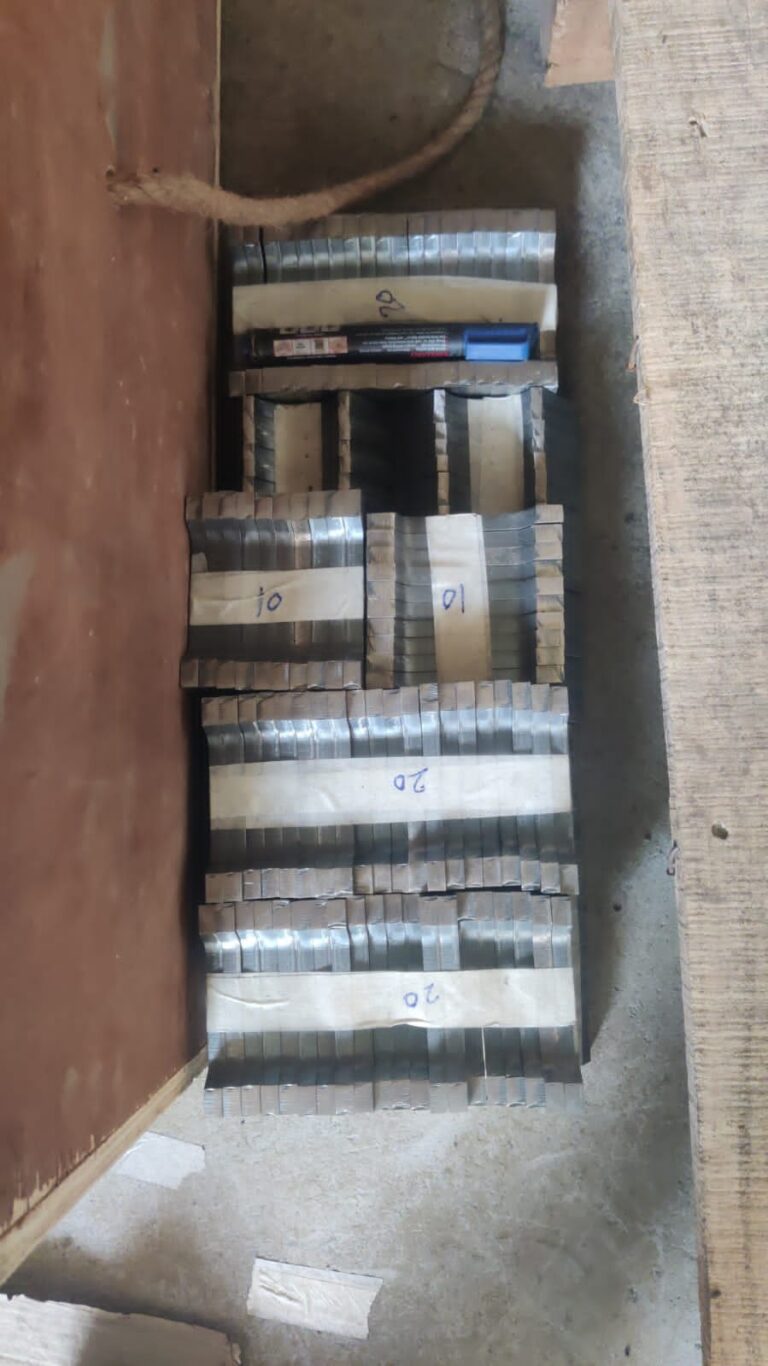
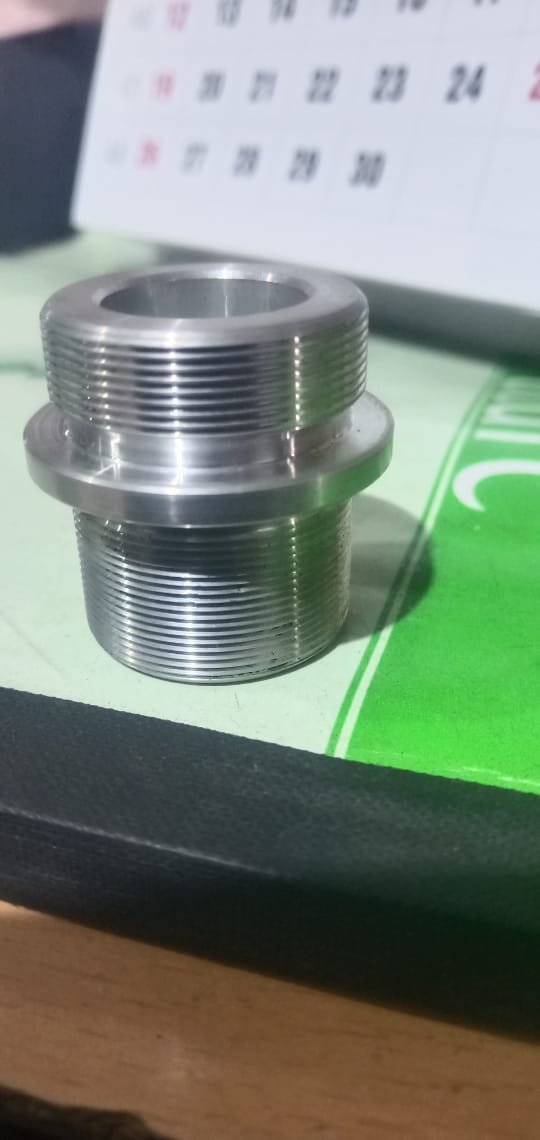
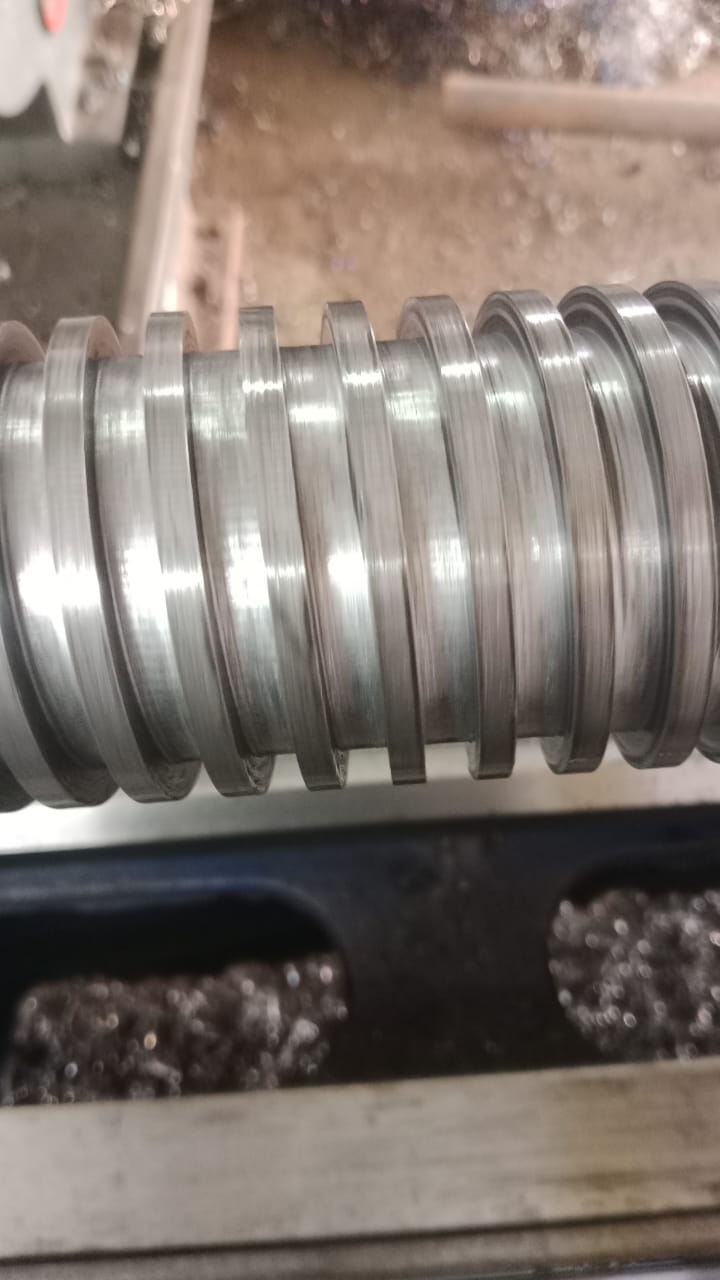
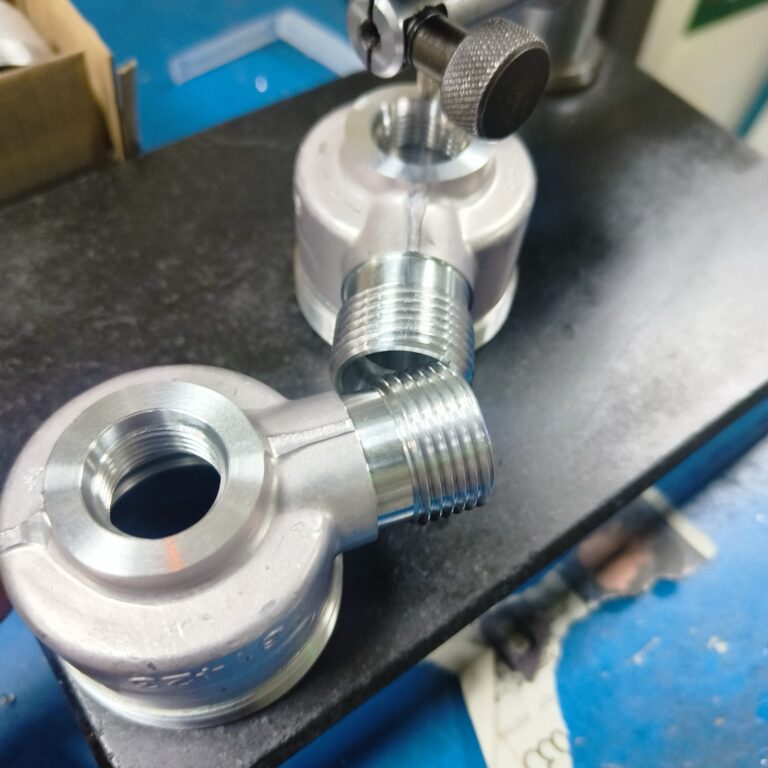
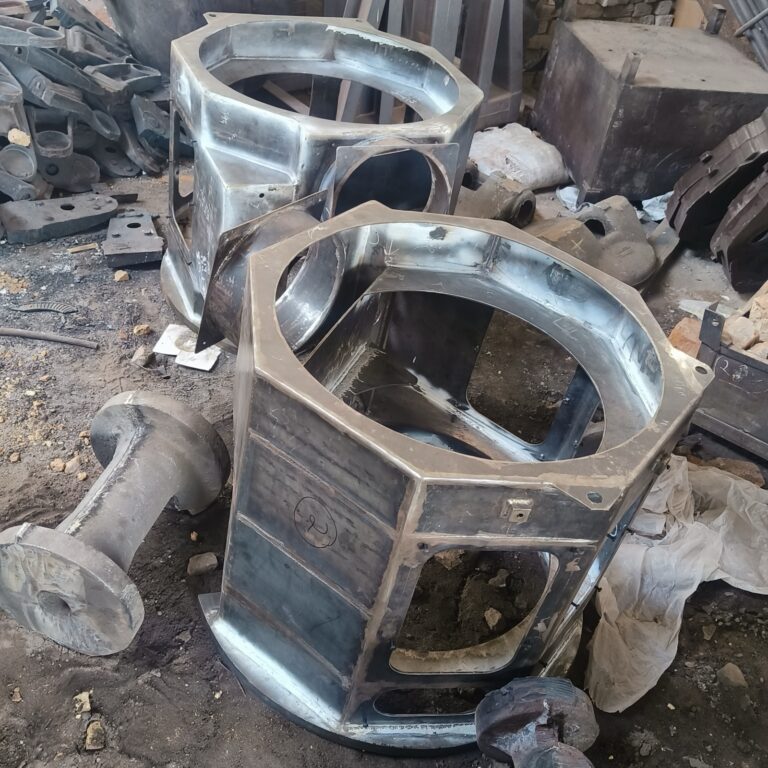
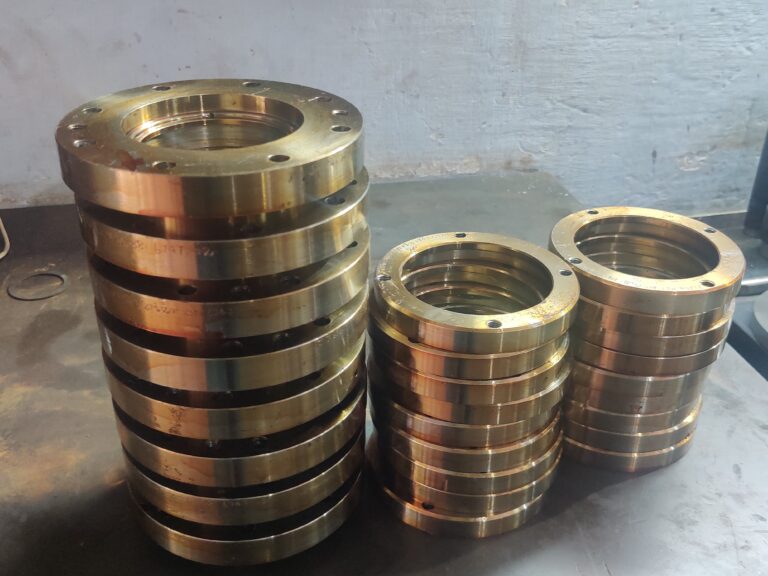
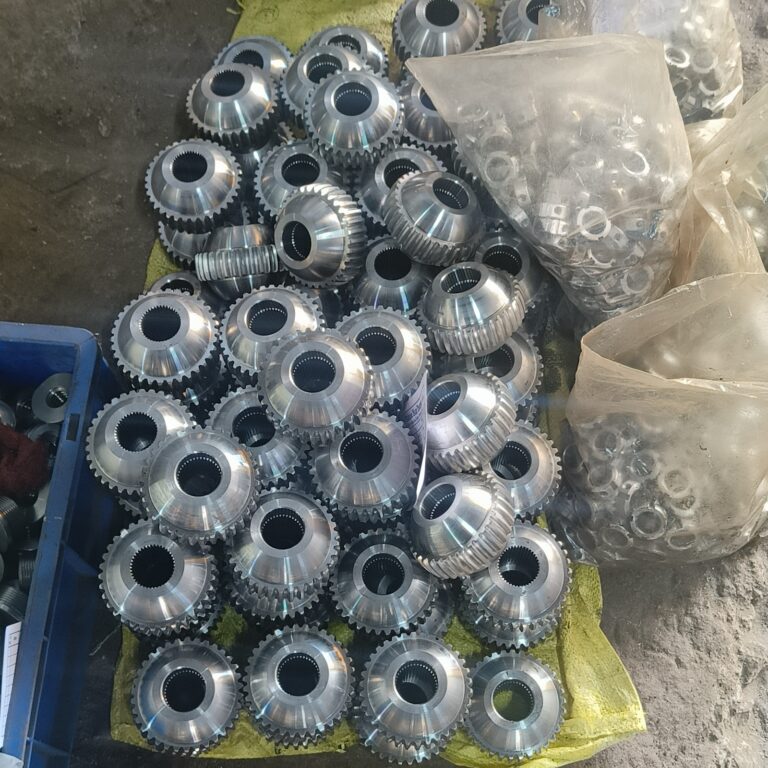
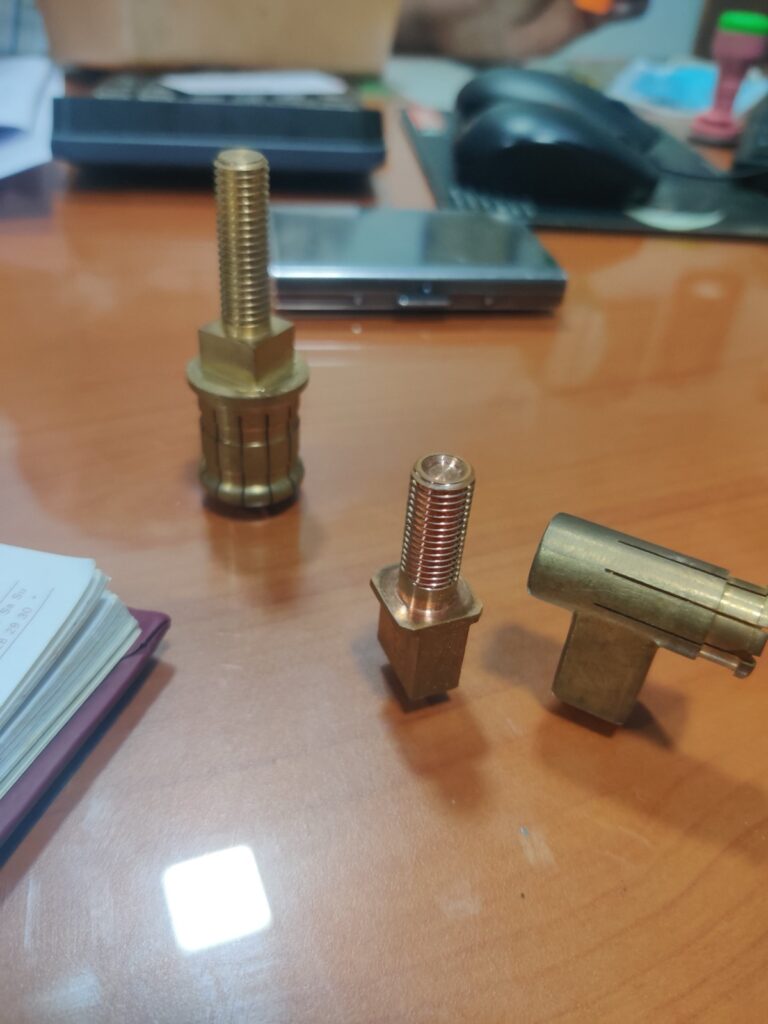
Plastics
Materials
1250 X 1250 MM
Within 10 microns
Engineering Plastics, Polyethylene, Polypropylene, Polyvinyl chloride, Polyethylene terephthalate, Bioplastics, etc.
Rubber
Materials
Natural rubber, Styrene-Butadiene Rubber, Nitrile Butadiene Rubber, Silicone Rubber, Fluorocarbon Rubber, Recycled Rubber, etc.
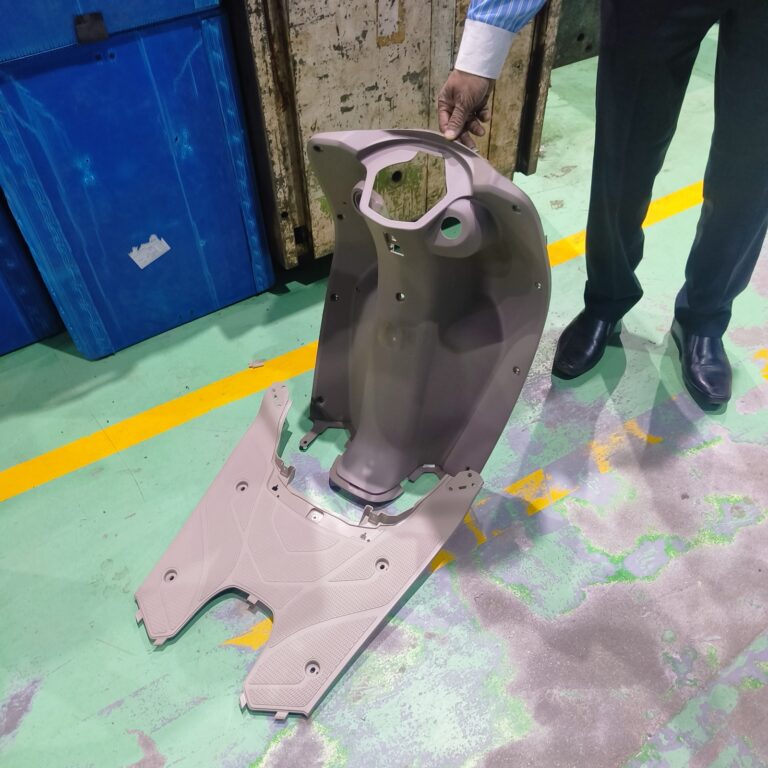
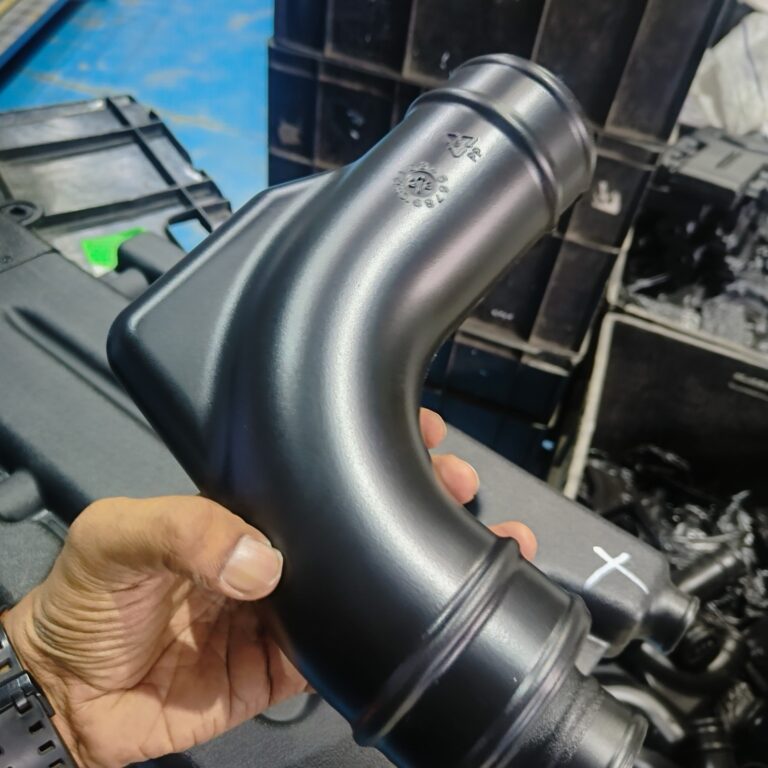
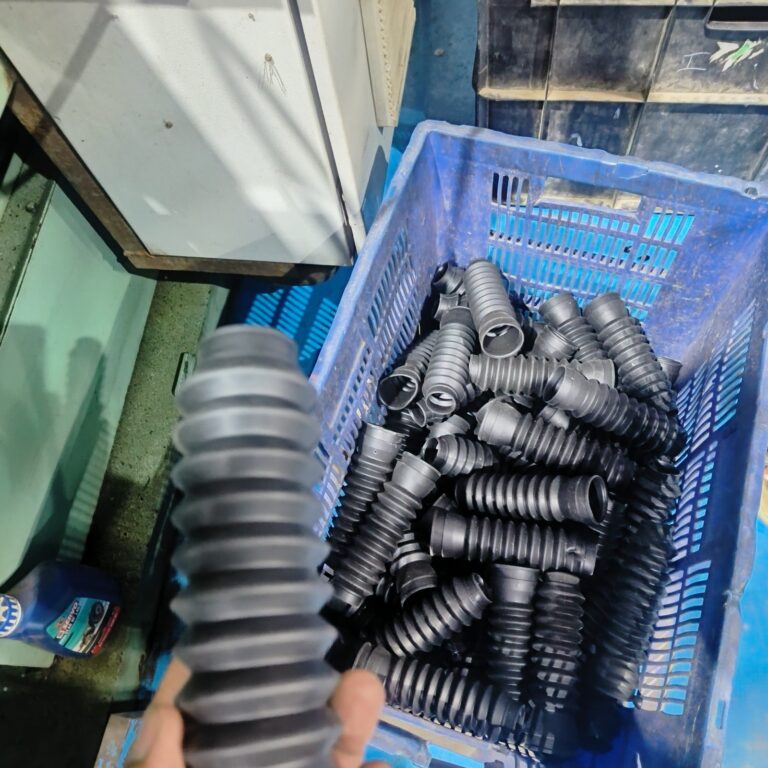
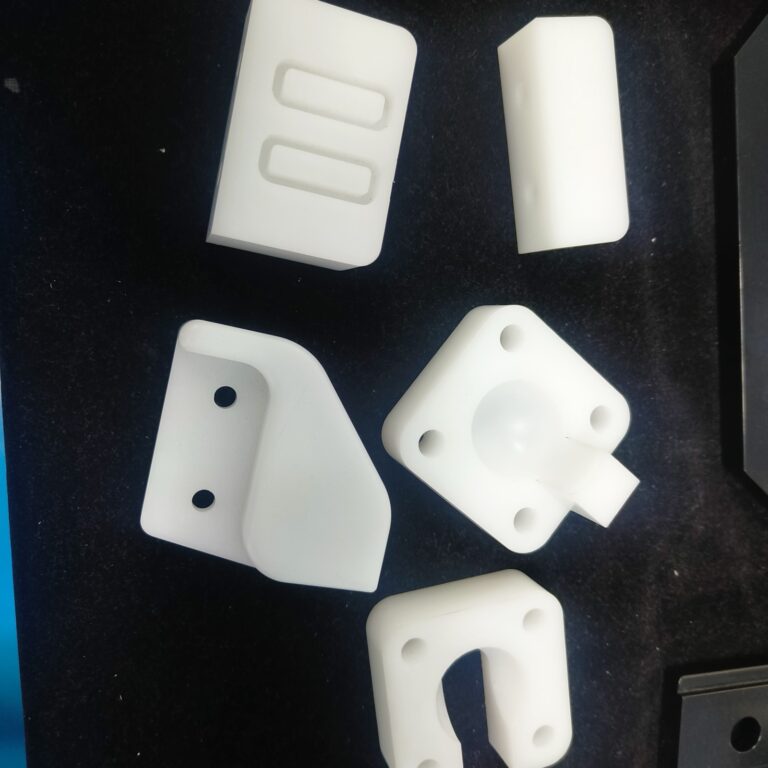
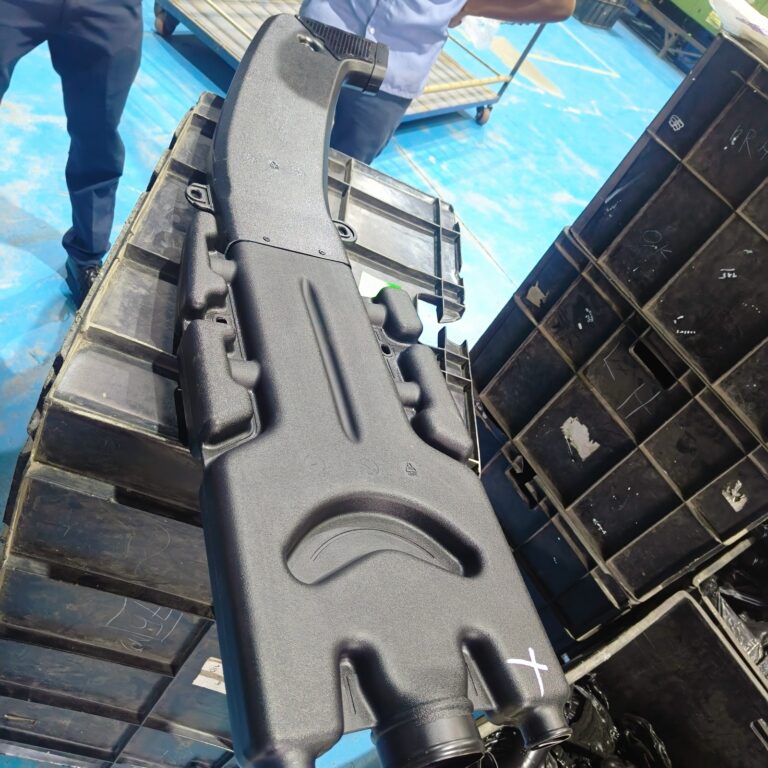
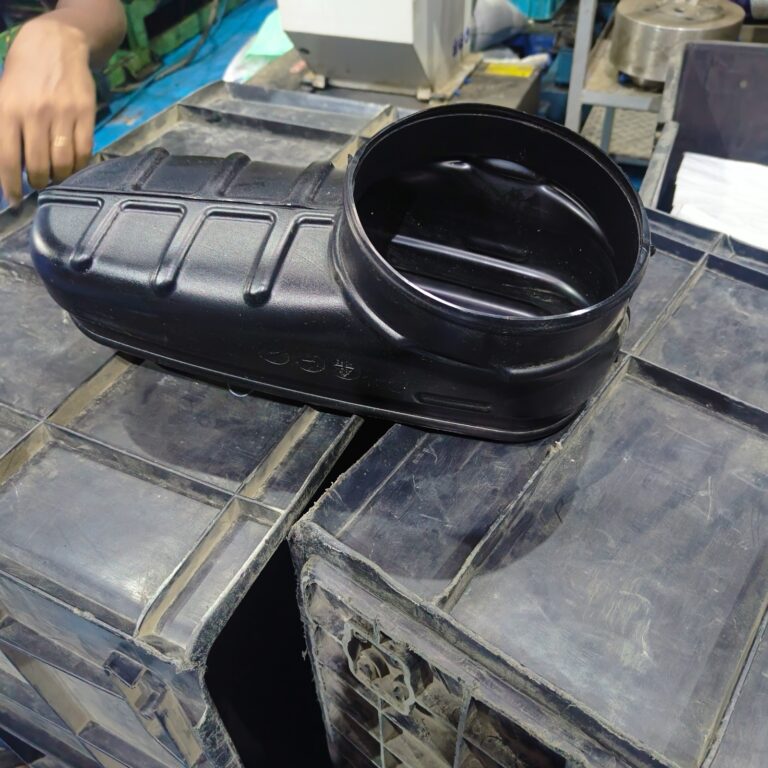
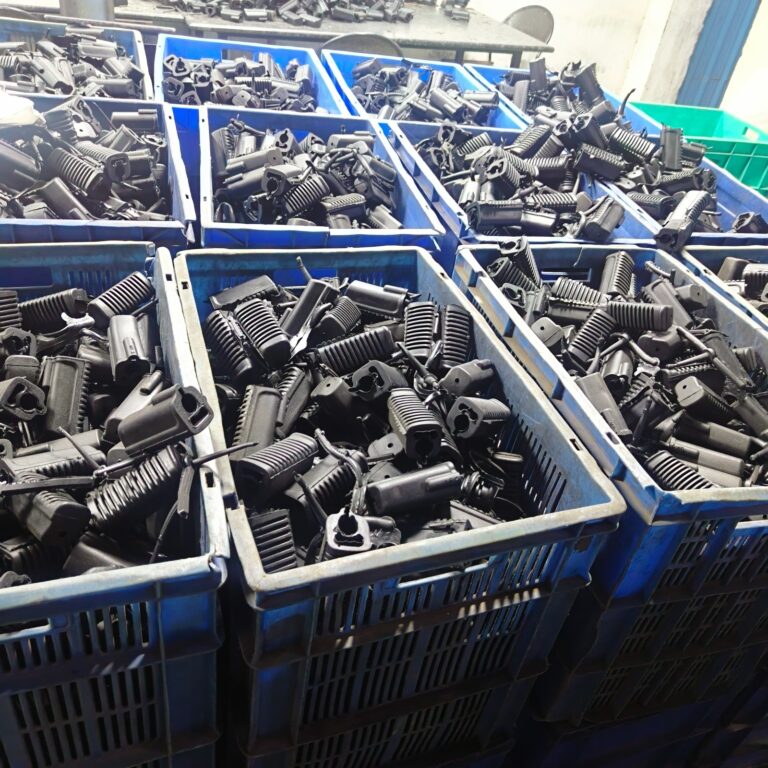
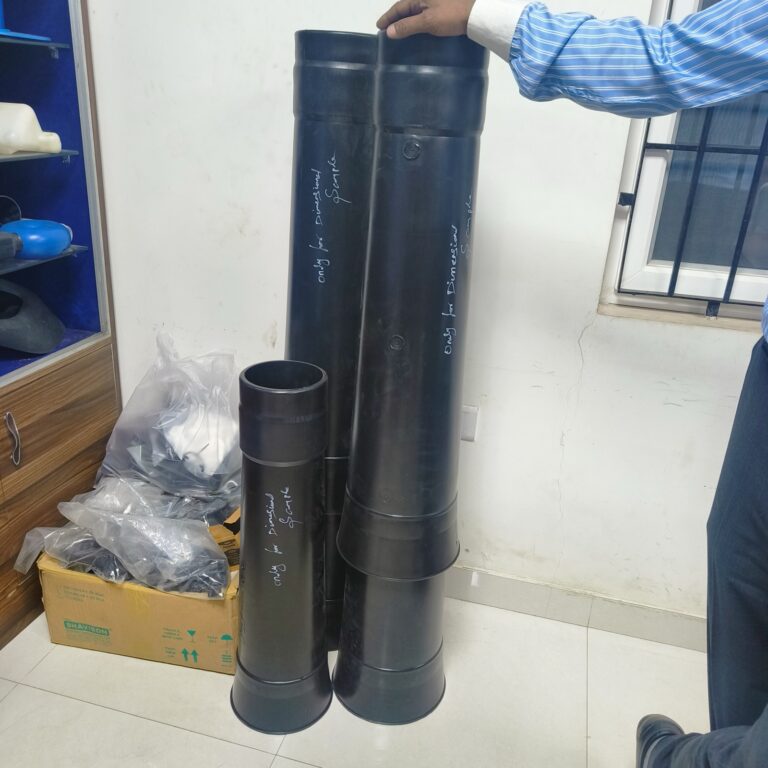
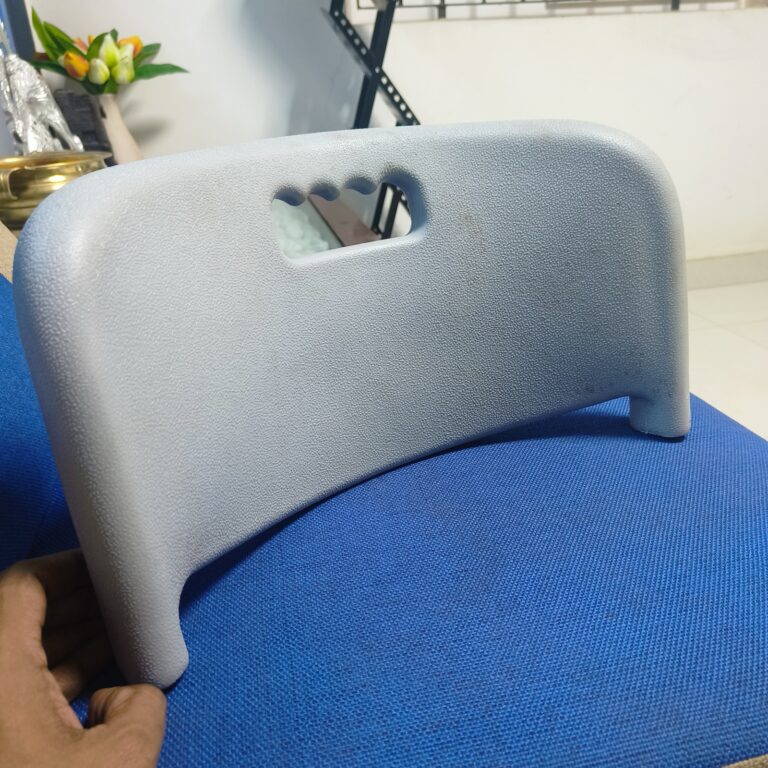
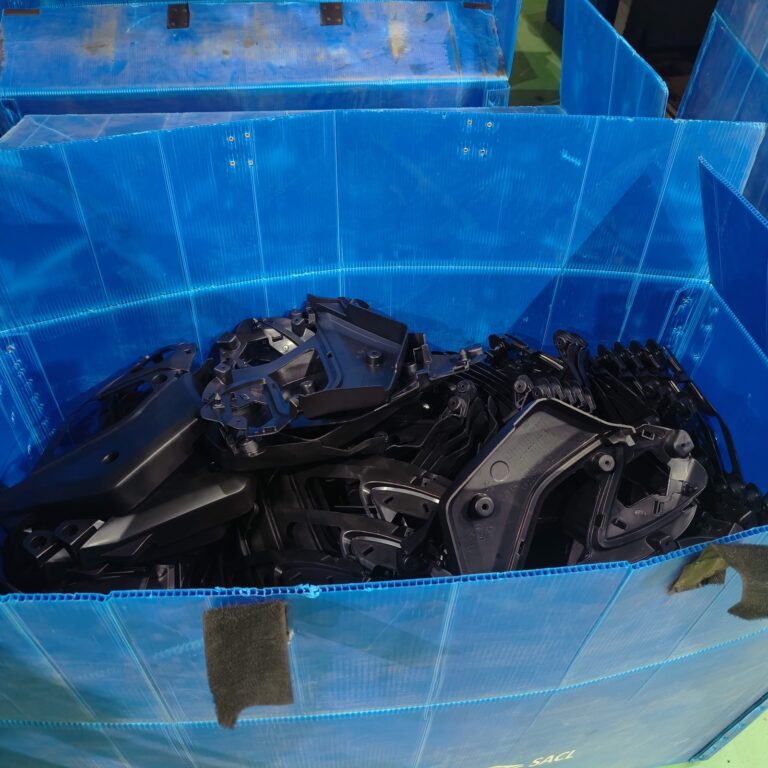
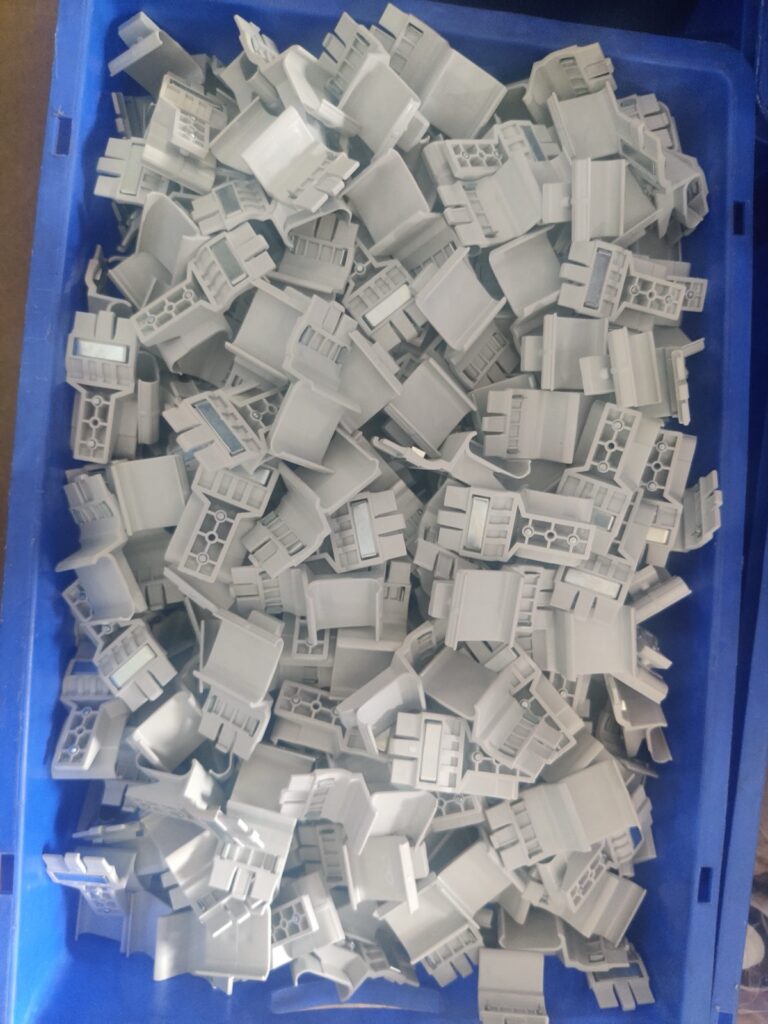
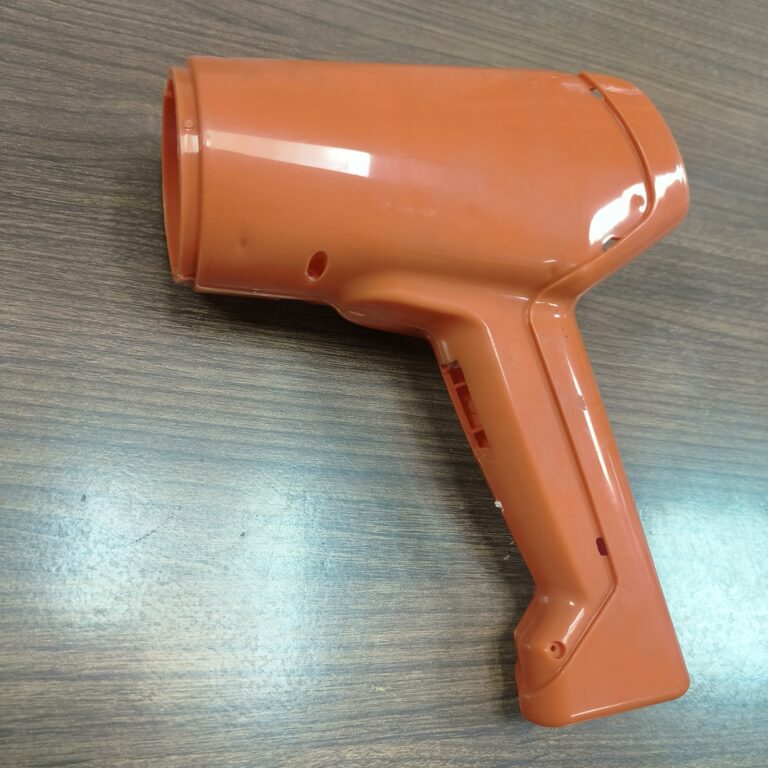
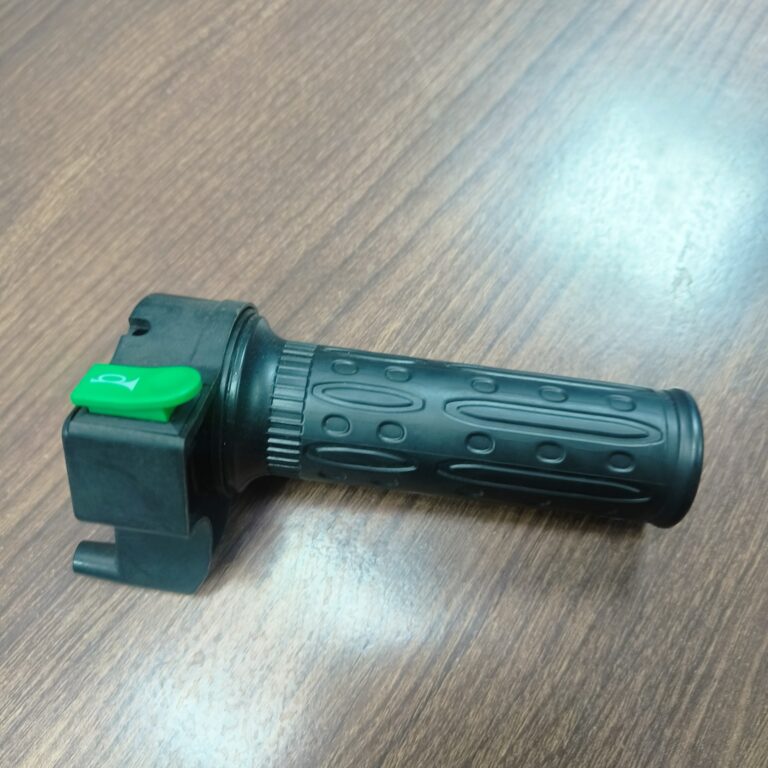
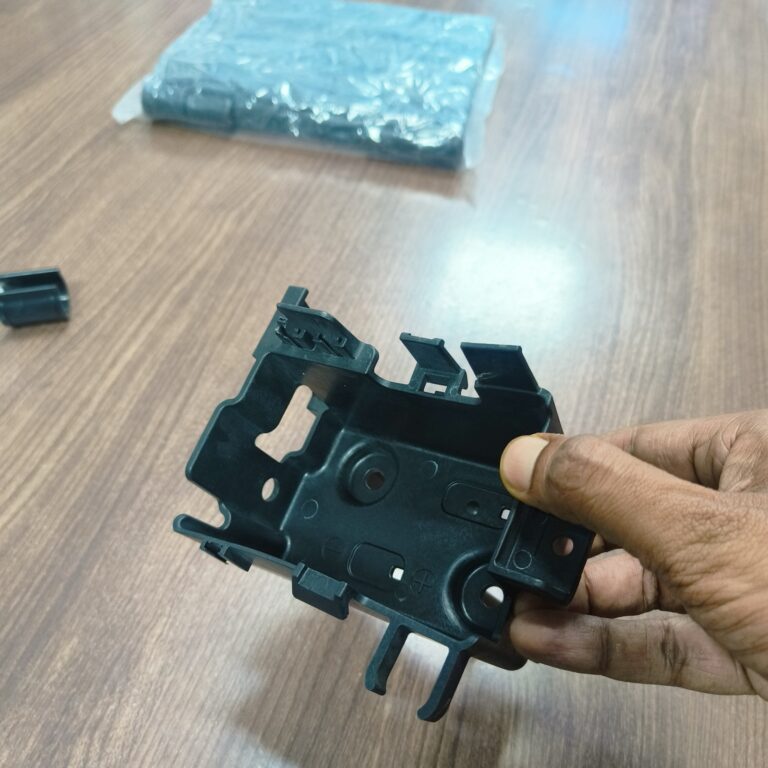
Heavy Fabrication
24000 MT/a
Materials
CS / MS, Alloy steel, Stainless Steel, etc.
Sheet Metal Fabrication
0.8 to 25 mm
Materials
Mild Steel, Stainless Steel, Aluminum, Brass, Copper, etc.


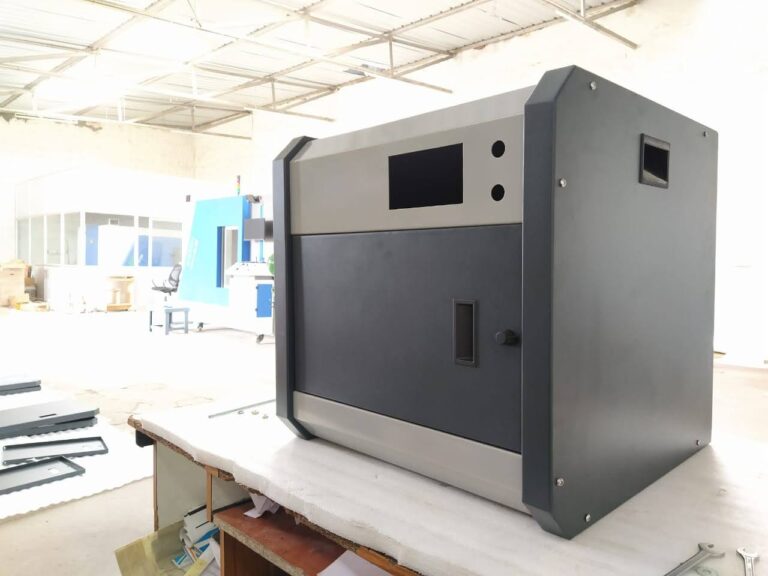


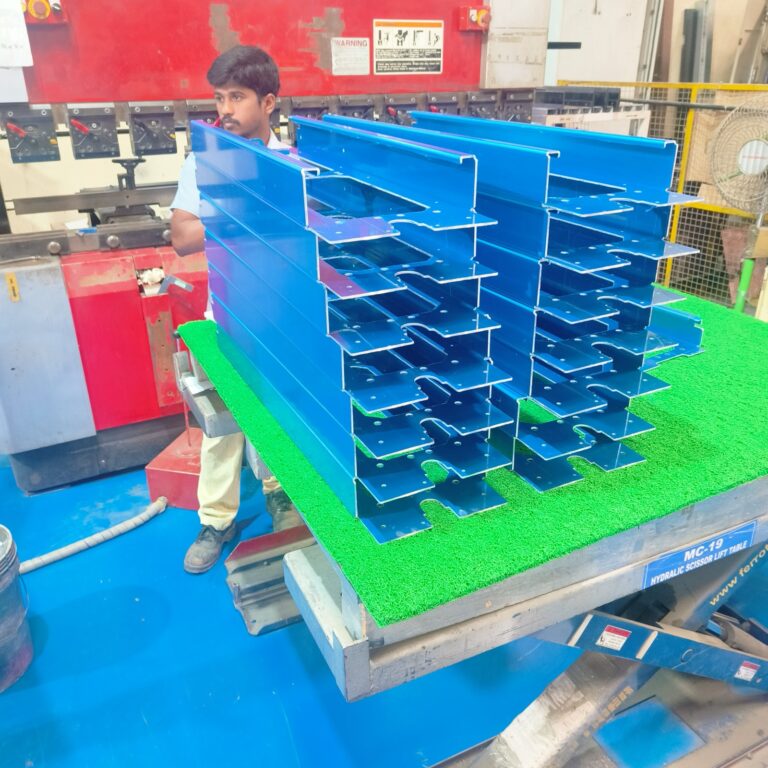
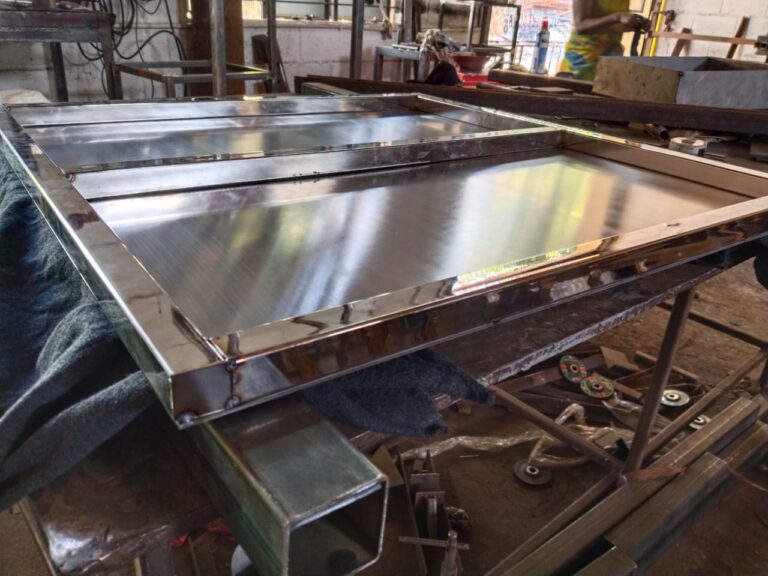
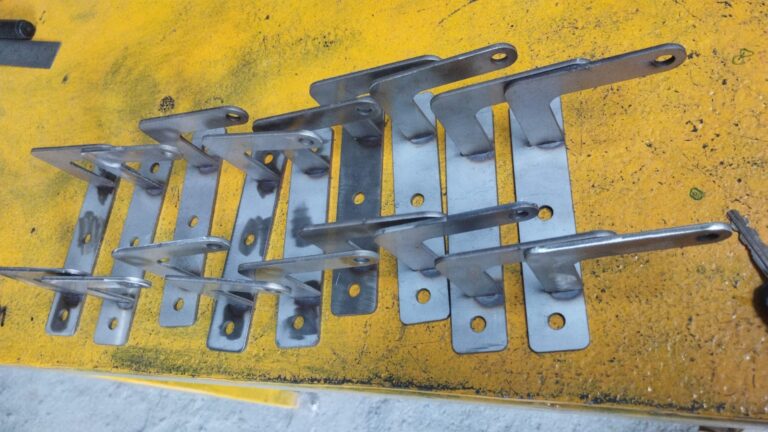
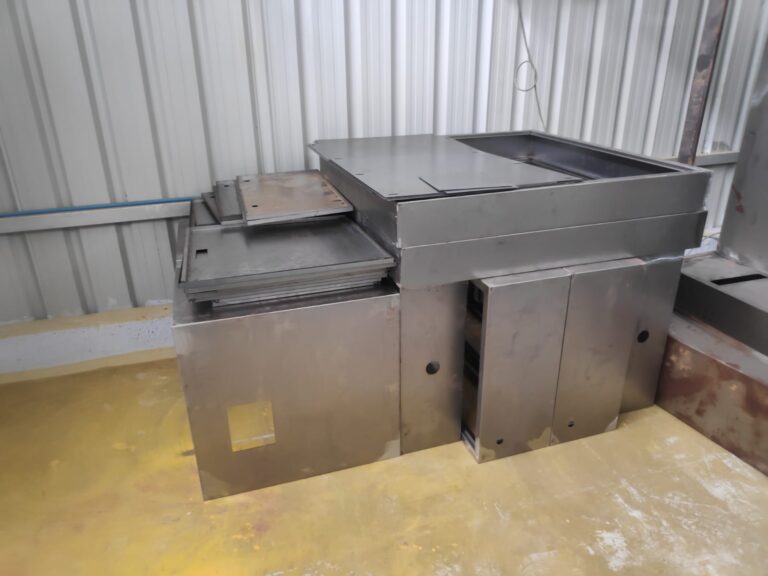
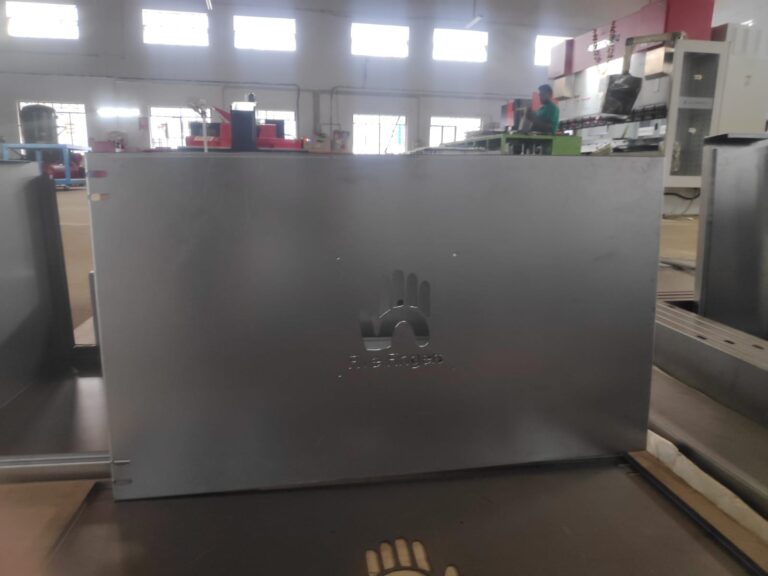
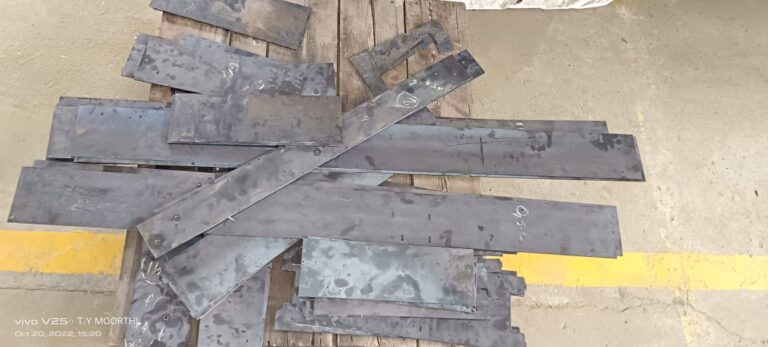
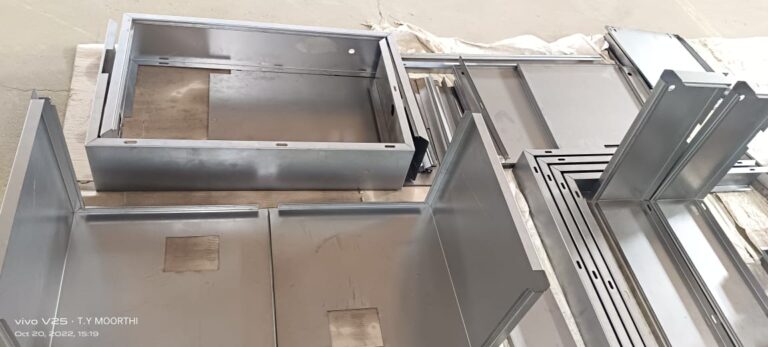
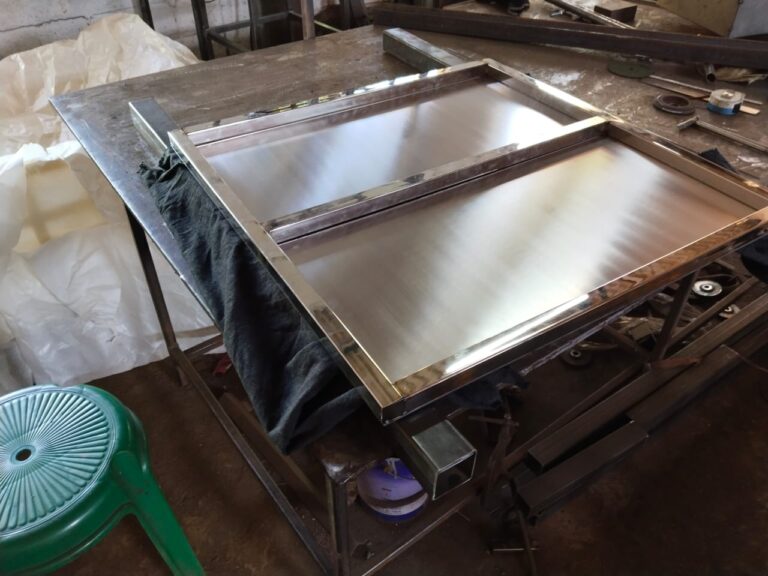
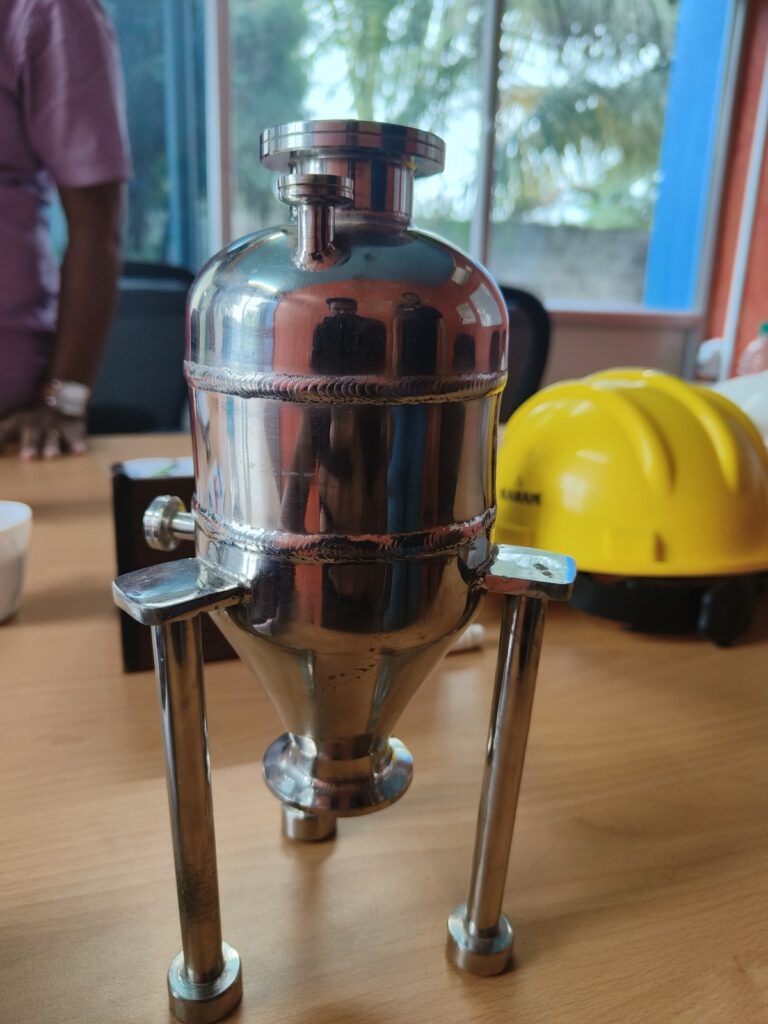
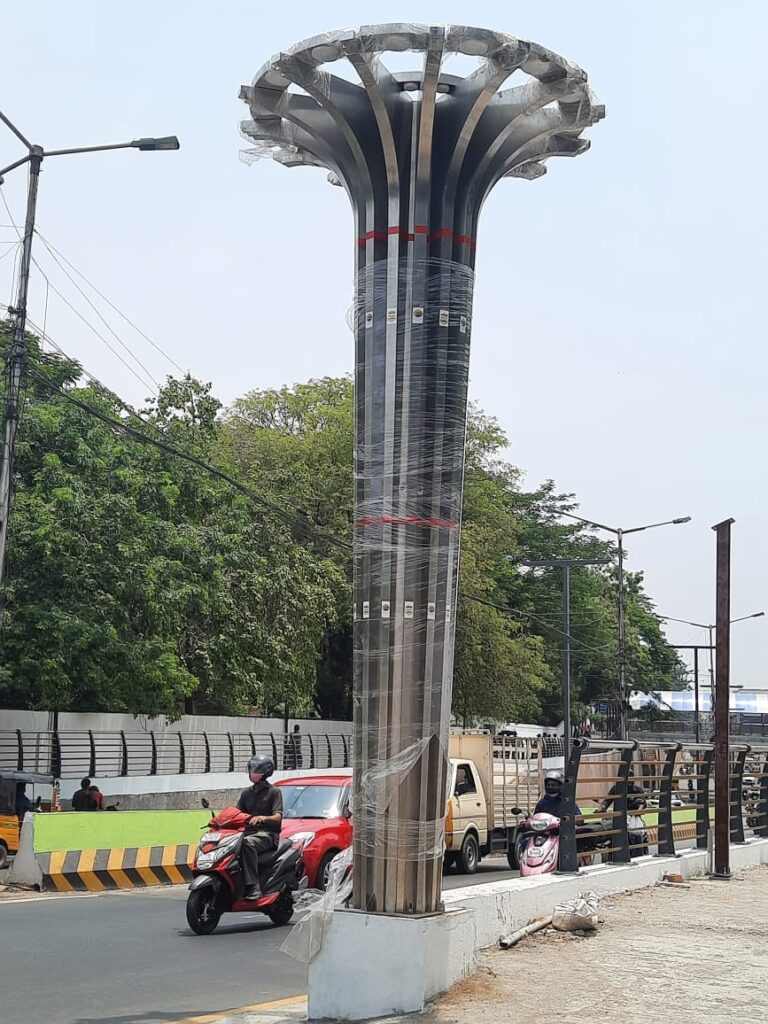
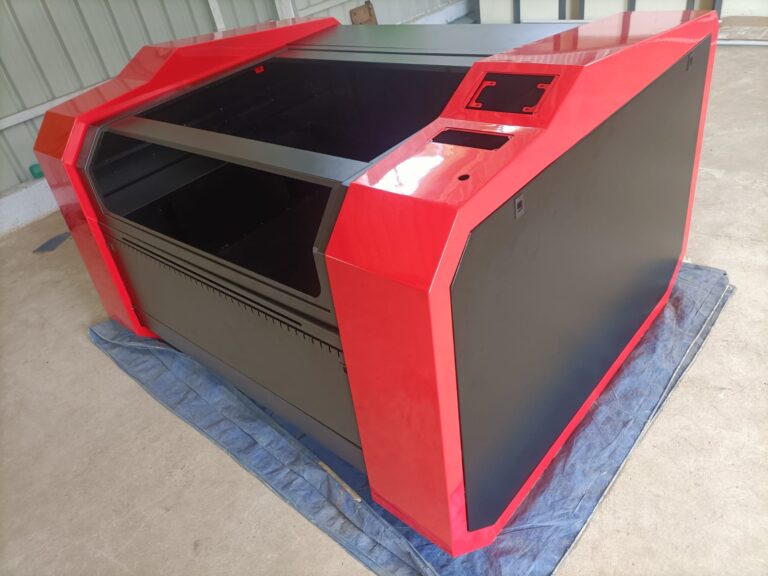
We'd love to Manufacture for you!
Submit the form below and our representative will be in touch shortly.
LOCATIONS
Global Sales Office
818, Preakness lane, Coppell, Texas, USA – 75019
Registered Office
10-A, First Floor, V.V Complex, Prakash Nagar, Thiruverumbur, Trichy-620013, Tamil Nadu, India.
Operations Office
9/1, Poonthottam Nagar, Ramanandha Nagar, Saravanampatti, Coimbatore-641035, Tamil Nadu, India. ㅤ
Other Locations
- Bhilai
- Chennai
- Texas, USA