Thermoplastic Injection Molding Services
Frigate provides high-tolerance thermoplastic injection molding for complex, durable component designs. Our process uses controlled cooling and optimized fill rates for maximum material integrity.
Our Clients





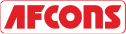

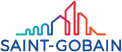


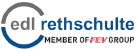

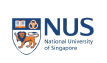
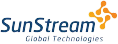

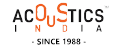




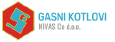
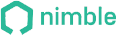
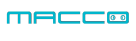












Advantages of Thermoplastic Injection Molding Services
Consistent Part Repeatability
Precision molding techniques ensure each part is identical, maintaining uniformity and reducing variability in high-volume production runs.
Superior Heat Resistance
Thermoplastics withstand elevated temperatures, making them suitable for components in demanding applications, including automotive and electronic housings.
Reduced Material Waste
The injection process minimizes excess material, as only the required amount fills each mold, leading to cost-efficient and eco-friendly production.
Enhanced Structural Integrity
Controlled injection pressure and mold design ensure parts have excellent mechanical strength, supporting load-bearing applications without compromising material properties.
Enhance Component Quality with Custom Thermoplastic Injection Molding
Precision and material consistency are crucial for parts with complex designs and tight tolerances. Custom thermoplastic injection molding provides high-accuracy solutions for industries requiring reliable, high-quality components. It enables quick production cycles, supports a wide range of polymers, and minimizes material waste, reducing costs and improving sustainability. Advanced tooling and temperature control ensure excellent dimensional stability and smooth finishes, even in high-volume production.

Get Your Quote Now
- Instant Quotation
- On-Time Delivery
- Affordable Cost
Our Thermoplastic Injection Molding Process






Thermoplastic pellets are chosen based on the final product's required properties, such as strength, flexibility, and heat resistance.
The pellets are fed into a heated barrel, melting and plasticizing to achieve a smooth, flowable consistency.
The molten thermoplastic is injected into a mold cavity at high pressure, ensuring the material fills even intricate mold features.
The mold cools to solidify the thermoplastic, helping the part retain its precise dimensions and structural integrity.
Once solidified, the molded part is ejected from the mold by an ejector system, minimizing any potential for part deformation.
The part may undergo secondary processes, like trimming or surface finishing, to meet specific quality and aesthetic requirements.
Thermoplastic Injection Molding Materials
Thermoplastic injection molding offers precision and versatility for complex part production. Its ability to meet strict performance, durability, and dimensional requirements is unmatched.
Known for excellent chemical resistance and flexibility, polypropylene is lightweight & resistant to impact. This makes it ideal for parts that require durability under stress, like automotive components and consumer goods.
Available in multiple densities, polyethylene is tough and resistant to moisture and chemicals. Due to its excellent barrier properties, it’s commonly used in packaging, containers, and plumbing applications.
ABS offers high-impact resistance and strength with good dimensional stability. Its toughness and ease of molding make it suitable for automotive interiors, electronics housings, and consumer appliances.
Polycarbonate is known for its transparency and impact resistance. It also withstands high temperatures and UV exposure, making it ideal for optical lenses, lighting covers, and safety equipment.
Nylon exhibits high tensile strength, wear resistance, and low friction, making it suitable for mechanical parts like gears, bushings, and automotive components that need long-term durability.
With excellent chemical resistance and rigidity, PET is commonly used for food containers and beverage bottles. Its transparency and strength also make it suitable for optical applications.
Polystyrene is lightweight and easy to mold, offering good rigidity but limited flexibility. It’s often used in disposable items, packaging, and lightweight applications.
TPU is highly elastic, wear-resistant, and flexible, making it a good choice for applications requiring flexibility and durability, such as seals, gaskets, and protective coatings.
Achieving Precision with High-Strength Alloys
Forming high-strength alloys is challenging due to inconsistent pressure and force. Frigate addresses this using advanced pneumatic systems to regulate pressure and speed, ensuring better material flow. Tooling and process parameters are customized for each alloy, applying optimal force for precise results. Simulations and testing predict material behavior, allowing for proactive adjustments and ensuring consistent quality, even with difficult alloys.

Compliance for Thermoplastic Injection Molding Services
Frigate’s thermoplastic injection molding process strictly follows industry compliance standards. We ensure precision, safety, and environmental responsibility with each part produced. Our focus on advanced technologies and top-tier materials guarantees that all components meet regulatory standards.
Ensures a robust Quality Management System for consistent, high-quality manufacturing processes.
Restricts the use of hazardous substances in electrical and electronic equipment.
Certifies materials used in medical devices, ensuring safety and effectiveness in healthcare applications.
Confirms compliance with stringent flammability safety standards for plastic materials.
Ensures chemical safety in materials used within the European market by restricting hazardous substances.
Verifies an effective Environmental Management System to reduce environmental impact.
Specifies quality management standards for automotive industry components, ensuring superior performance and reliability.

Tolerance for Thermoplastic Injection Molding Services
Ensures precise positioning of the gate in relation to the part for consistent flow.
Defines the accurate placement of ejection pin marks to ensure consistent part removal.
Tolerance on cavity pressure to ensure uniform material distribution during injection.
Precision in controlling the speed of injection to avoid defects like flow lines.
Controls the dimensional change of the part during cooling, ensuring consistency.
Ensures precise alignment between core and cavity to avoid part distortion.
Tolerance on the distance the plastic flows inside the mold to maintain part integrity.
Ensures precise control over the injection molding temperature to avoid warping.
Control over the cooling rate to prevent uneven cooling and ensure part consistency.
Precision on the angle of draft to allow for easy part ejection without damage.
Controls the part’s tendency to warp during cooling, ensuring accuracy and stability.
Tolerance on the thickness of ribs for proper strength without risk of breakage.
Specifies the roughness of molded surfaces for both aesthetic and functional parts.
Ensures high-quality surface finish in areas that require detailed texturing.
Ensures that material properties, like viscosity, are consistent for uniform parts.

Quality Testing Standards for Thermoplastic Injection Molding Services
Predicts how the material flows inside the mold, optimizing part design and reducing defects.
Measures the temperature at which the material begins to soften under a specified load.
Assesses the material's tendency to deform under constant load over time.
Tests the rate at which a material absorbs moisture, affecting its mechanical properties.
Measures the material’s stiffness under tension to understand its deformation behavior.
Tests the material’s ability to resist burning when exposed to flame.
Measures the material’s ability to conduct heat, important for heat-sensitive applications.
Measures the rate at which gases permeate through the molded material.
Measures how much the material expands or contracts with temperature changes.
Evaluates how the material’s stress decreases over time under a constant strain.
Measures how much the material can elongate before breaking, indicating ductility.
Assesses the hardness of the molded material to ensure it meets the specified durability.
Evaluates the part's ability to maintain shape under a defined load over time.
Measures the material's resistance to cracking under stress in harsh environments.
Tests the strength of the part at weld lines to ensure that mold flow paths are optimized.
Optimizing Automotive Component Manufacturing
The automotive industry demands cost-effective, high-quality components with complex geometries and tight tolerances. Thermoplastic injection molding offers a solution by enabling efficient production of lightweight, durable parts that meet these requirements. Frigate utilizes this process, ensuring precise molding and rapid production cycles. With advanced control over material flow and temperature, Frigate consistently delivers parts with excellent surface finishes and minimal waste. The ability to work with various thermoplastic materials, from high-performance plastics to specialized composites, meets the diverse needs of automotive applications. This enhances both performance and production efficiency.








Industries We Serve
- Solid Progress
Our Manufacturing metrics
Frigate brings stability, control, and predictable performance to your sourcing operations through a structured multi-vendor system.
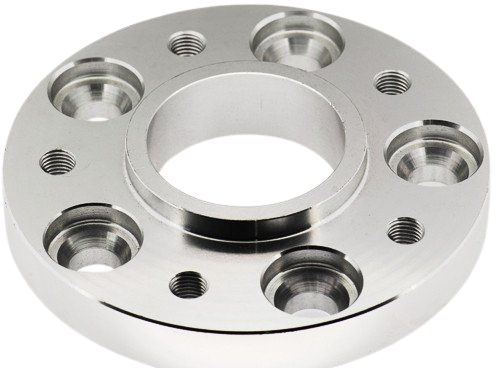
2.8X
Sourcing Cycle Speed
Frigate’s pre-qualified network shortens decision time between RFQ and PO placement.
94%
On-Time Delivery Rate
Structured planning windows and logistics-linked schedules improve project-level delivery reliability.
4X
Multi-Part Consolidation
We enable part family batching across suppliers to reduce fragmentation.
22%
Quality Rejection Rate
Multi-level quality checks and fixed inspection plans lower non-conformities.
30%
Procurement Costs
Optimized supplier negotiations and bulk order strategies reduce your overall sourcing expenses.
20%
Manual Processing Time
Automation of sourcing and supplier management significantly reduces time spent on manual tasks.
Maximizing Tool Life and Reducing Downtime
Pneumatic systems often cause rapid die wear due to repetitive pressure. Frigate counters this by selecting durable, wear-resistant die materials and incorporating advanced cooling systems to reduce thermal expansion. Optimized cycle times and controlled pressure minimize stress on dies, extending tool life and reducing maintenance needs. Real-time monitoring further reduces downtime, ensuring consistent production and improved operational efficiency.

Get Clarity with our Manufacturing Insights
- Real Impact
Words from Clients
See how global OEMs and sourcing heads describe their experience with our scalable execution.
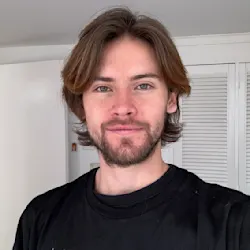
“Quick turnaround and solid quality.”
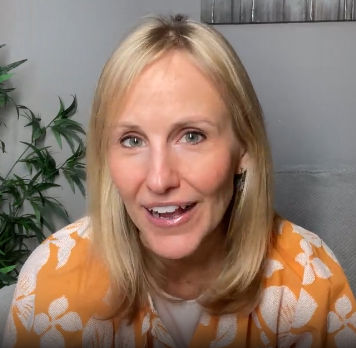
“The instant quote tool saved us time, and the parts were spot-on. Highly recommend Frigate!”
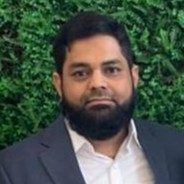
“I would strongly recommend Frigate to anyone who wants to do Rapid Prototyping, and take their ideas to manufacturing. One firm doing all kinds of Product Development!”
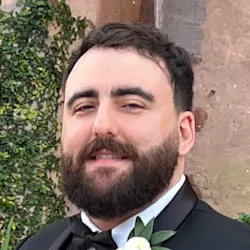
“Great service, fair price, and the parts worked perfectly in our assembly.”
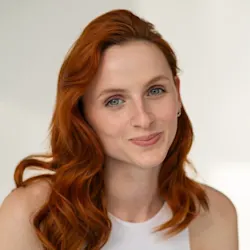
“Top-notch machining and fast shipping. Very satisfied with the results.”
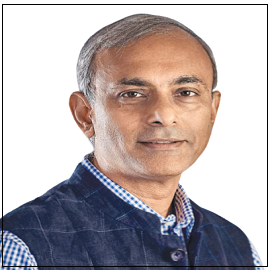
“The next disruption is happening in Prototyping & Manufacturing on-demand and Frigate is leading the way! I personally believe the Frigate's way of IIOT enabled cloud platform with Al.”
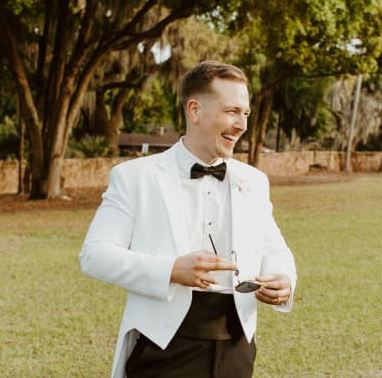
“Frigate delivered high-quality parts at a competitive price. The instant quote tool is a huge plus for us!”

“We appreciate the precision and quality of the machined components in the recent delivery—they meet our specifications perfectly and demonstrate Frigate’s capability for excellent workmanship.”
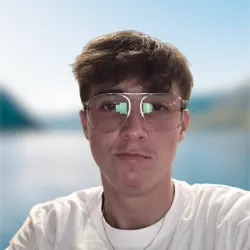
“Flawless execution from quote to delivery.”

“I am absolutely happy to work with supplier like Frigate who were quite proactive & result oriented . Frigate has high willingness team who has strong know how & their passion towards the products & process were absolutely thrilling.”
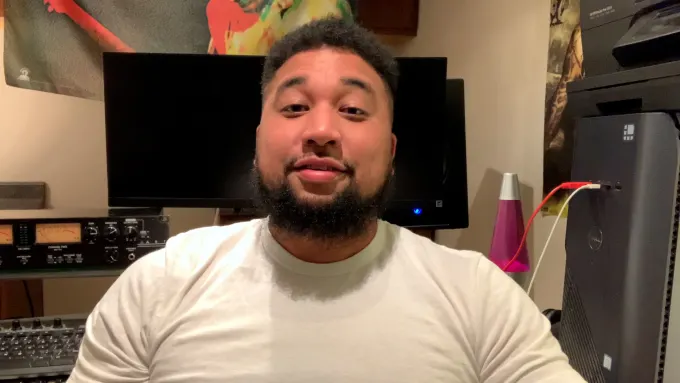
“The precision on these parts is impressive, and they arrived ahead of schedule. Frigate’s process really stands out!”
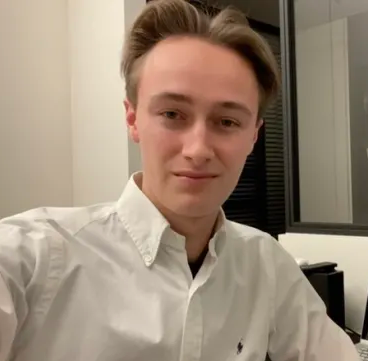
“Parts were exactly as spec’d, and the instant quote made budgeting a breeze.”
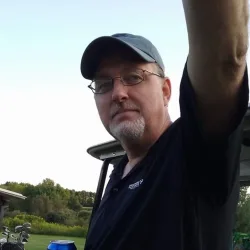
“Good value for the money.”
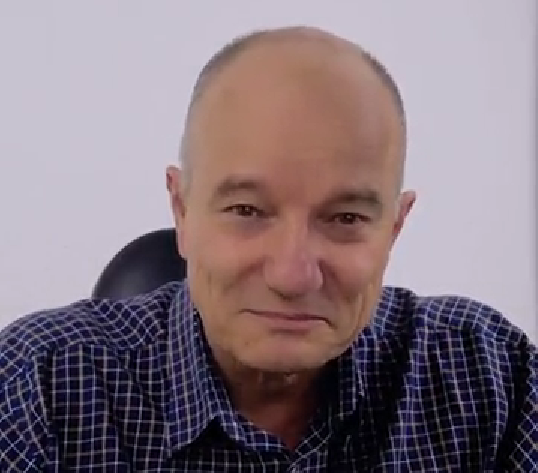
“The finish was perfect, and the team was easy to work with.”

“Working with Frigate has been great. Their proactive, results-driven approach and expertise shine through in every project. It's been a pleasure collaborating with them.”

"We are highly satisfied with the timely delivery and quality of the MIG Welding Cable from Frigate. Their attention to detail, secure packaging, and quick responsiveness stood out. We confidently recommend Frigate Engineering Services Pvt. Ltd. as a reliable manufacturing partner."
Having Doubts? Our FAQ
Check all our Frequently Asked Question
Frigate uses precise barrel heating, optimized screw speeds, and real-time melt flow monitoring to ensure uniformity and prevent variations in part quality.
Frigate controls cooling rates, optimizes mold design, and carefully selects materials to reduce internal stresses and prevent warping during the cooling phase.
Frigate implements efficient cooling channels and thermal management systems to maintain consistent mold temperatures, improving cycle time efficiency and durability.
Frigate employs continuous monitoring, automated inspection, and strict material traceability to ensure that each batch meets specifications for consistent part quality.
Frigate optimizes injection pressure profiles and cooling systems to ensure rapid solidification and consistent wall thickness, maintaining strength in thin-walled parts.
We'd love to Manufacture for you!
Submit the form below and our representative will be in touch shortly.
LOCATIONS
Global Sales Office
818, Preakness lane, Coppell, Texas, USA – 75019
Registered Office
10-A, First Floor, V.V Complex, Prakash Nagar, Thiruverumbur, Trichy-620013, Tamil Nadu, India.
Operations Office
9/1, Poonthottam Nagar, Ramanandha Nagar, Saravanampatti, Coimbatore-641035, Tamil Nadu, India. ㅤ
Other Locations
- Bhilai
- Chennai
- Texas, USA