Plastic Fabrication Services
Frigate provides advanced plastic fabrication services using thermoforming and injection molding. Our cutting-edge materials enhance chemical resistance and dimensional stability for demanding applications.
Get Your Quote Now
- Instant Quotation
- On-Time Delivery
- Affordable Cost
Precision Custom Plastic Fabrication Services
Frigate specializes in custom plastic fabrication, utilizing extensive knowledge of plastics and polymers to produce high-quality parts and components. It stocks various materials, accommodating everything from prototyping to large production runs.
Built on a foundation of quality, all custom fabrications meet laboratory standards. Welds are exceptionally smooth for easy cleaning, ensuring no product leaves the facility with saw-cut or sharp edges. Each piece is precisely cut using high-tech CNC dual-head routers. We also provide custom acrylic fabrication and other specialized services.

Reducing Lead Times and Enhancing Flexibility
Advanced manufacturing techniques such as additive manufacturing and precision CNC machining can significantly reduce lead times. These methods allow for rapid production without sacrificing quality, enabling faster delivery of prototypes and final products.
Implementing efficient workflow management systems enhances flexibility in production schedules. Streamlined processes can adapt to changing customer demands and urgent requests, ensuring timely order completion.
Engaging in collaborative planning with customers can improve responsiveness to urgent needs. This approach allows for better forecasting and resource allocation, reducing lead times and improving service levels.

Achieving Precision Tolerances and Dimensional Accuracy
Investing in precision machining equipment ensures tight tolerances and high dimensional accuracy. Advanced technology minimizes variations in fabrication processes, which is critical for meeting stringent specifications.
Establishing stringent quality control measures throughout the fabrication process can identify deviations early. This proactive approach allows for timely corrections, ensuring that parts meet the required standards before delivery.
Implementing continuous process improvement initiatives can enhance dimensional accuracy over time. Regularly reviewing and refining fabrication methods contributes to consistent performance and reduced errors in production.

Integrating Processes and Ensuring Scalability
Developing standardized processes can facilitate the integration of fabrication techniques into existing workflows. Standardization simplifies training and enhances consistency, making it easier to scale operations as demand increases.
Utilizing modular production systems allows for flexible operation scaling. This approach enables quick adjustments to production capacity while maintaining quality, accommodating small batches and large production runs.
Implementing comprehensive training programs for personnel can improve the integration of fabrication processes. Skilled operators are essential for maintaining quality and efficiency, particularly during prototyping to mass production transitions.

Plastic Fabrication Materials
Frigate utilizes manufacturing processes that greatly influence plastic fabrication quality and precision. Techniques such as injection molding & CNC machining ensure efficient production and tight tolerances.
Polyethylene is a versatile thermoplastic known for its excellent chemical resistance and impact strength. Due to its lightweight nature, it is widely used in applications such as packaging, containers, and chemical tanks.
Polypropylene has a high melting point and is resistant to chemical solvents, making it suitable for automotive and industrial applications. Its low density and flexibility allow easy molding and fabrication into various shapes.
Polyvinyl chloride is a durable material often used in plumbing, electrical cable insulation, and signage. Its rigidity and resistance to environmental degradation make it ideal for long-lasting applications.
ABS is known for its toughness resistance, making it suitable for consumer products & automotive components. This thermoplastic can be easily machined and provides high dimensional stability.
Polystyrene is a low-cost, lightweight, and easy-to-mold material. Due to its insulation properties, it is commonly used in packaging, disposable cutlery, and insulation applications.
Polycarbonate is a transparent thermoplastic known for its high impact resistance and optical clarity. It is often used in safety glasses, electronic components, and protective barriers.
Acrylic offers superior optical clarity and weather resistance, making it a popular choice for signage, displays, and lighting fixtures. Its lightweight nature and ease of fabrication enhance its application versatility.
Thermoplastic elastomers combine the properties of rubber and plastic, providing flexibility and durability. They are commonly used in cushioning applications, such as grips and seals.
HDPE is known for its high strength-to-density ratio, making it suitable for heavy-duty containers and industrial applications. Its resistance to impact and chemicals makes it a reliable choice in harsh environments.
Ensuring Consistent Quality in Plastic Fabrication
Rigorous process control is essential to address inconsistent quality in plastic fabrication. Implementing standardized manufacturing protocols helps minimize variations that impact functionality. Regular equipment calibration ensures precise measurements and uniformity in production, reducing the likelihood of defects in final products.
Conducting thorough material testing is critical for maintaining quality. Assessing batch composition and monitoring environmental factors help identify inconsistencies in material properties. Adopting stringent quality assurance measures at multiple production stages allows for early defect detection. By employing this proactive strategy, Frigate enhances reliability and upholds high standards in plastic fabrication.

Compliance for Plastic Fabrication Services
Frigate’s plastic fabrication process is designed to meet the highest industry standards. We integrate precise regulatory controls to deliver products with superior performance and long-term reliability. Our adherence to global certifications ensures products are engineered to optimize functionality, minimize risks, and comply with stringent safety protocols.
Establishes systematic processes for consistent quality, reducing variability and enhancing product reliability.
Enforces elimination of toxic substances in plastics, ensuring sustainable production and minimizing environmental impact.
Certifies plastic materials for safe use in food-contact and medical devices, meeting critical health standards.
Verifies plastic products for potable water applications, ensuring they meet regulatory requirements for safety and durability.
Defines tensile strength parameters, ensuring plastic components meet necessary mechanical performance criteria.
Assesses plastic flammability, ensuring products used in critical applications meet fire safety standards.
Guarantees compliance with chemical safety regulations, ensuring plastics are safe for human and environmental health.
Ensures plastic components in defense applications meet national security and export control requirements.

Tolerance for Plastic Fabrication Services
Tolerances for parts that are crucial for assembly or functional performance.
Precision in hole sizes, essential for fitment with pins, screws, or inserts.
Tolerance for hole placement for precise alignment with inserted components.
Tolerances on the radii of curved features, ensuring smooth transitions.
Precision in edge detailing to ensure seamless assembly and performance.
Deviation of flat surfaces to maintain accurate assembly and sealing.
Tolerances on tapered features that require uniformity for proper fitment.
Deviation in the geometry of features like angularity, straightness, and flatness, to maintain precise alignment.
Ensures that threads are within spec for proper engagement of fasteners or inserts.
Precision in the angle of chamfers and bevels for uniform part function and appearance.
Ensures concentric alignment of internal and external features for assembly accuracy.
Tolerance for optical clarity in plastic components such as lenses or covers.
Tolerance for variation in wall thickness, ensuring uniform strength distribution.
Tolerance to control depth and appearance of sink marks from cooling stresses.
Control of dimensional changes due to internal stresses during cooling.

Quality Testing Standards for Plastic Fabrication Services
Measures the ability of a plastic material to conduct heat, crucial for heat-sensitive applications.
Evaluates the ability of plastic to return to its original shape after deformation, important for flexible applications.
Tests the plastic’s ability to maintain mechanical properties after prolonged exposure to environmental factors.
Assesses the stiffness of a plastic material under tensile stress, crucial for structural integrity.
Evaluates the plastic's resistance to compressive forces, important for load-bearing components.
Measures the insulating properties of plastics used in electrical applications to ensure they can withstand voltage.
Determines the minimum concentration of oxygen required for the material to sustain combustion, critical for fire safety.
Evaluates the material’s ability to resist damage or deformation under dynamic vibrations, crucial for automotive and aerospace.
Tests the stress at which plastic materials yield or begin to deform plastically, ensuring strength for load-bearing applications.
Measures the percentage of water absorbed by plastic materials, critical for understanding performance in humid environments.
Measures the force required to propagate a tear in the material, important for impact-resistant plastics.
Tests the surface wettability of plastics, affecting adhesion properties for coatings or bonding.
Assesses how plastic materials withstand repeated cyclic loading, important for dynamic applications such as automotive parts.
Evaluates the bond strength of welded plastic joints to ensure reliable assembly in welded components.
Measures the plastic’s ability to resist degradation from ultraviolet light exposure, ensuring durability in outdoor applications.
- Real Impact
Words from Clients
See how global OEMs and sourcing heads describe their experience with our scalable execution.
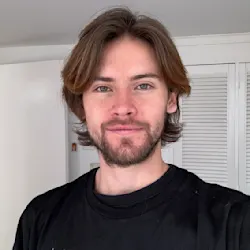
“Quick turnaround and solid quality.”
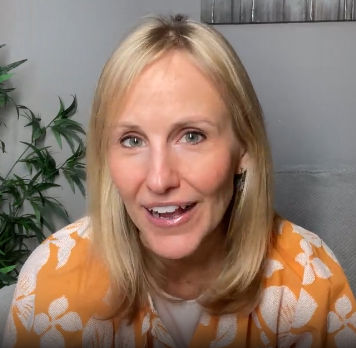
“The instant quote tool saved us time, and the parts were spot-on. Highly recommend Frigate!”
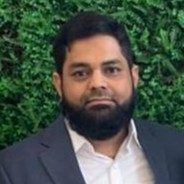
“I would strongly recommend Frigate to anyone who wants to do Rapid Prototyping, and take their ideas to manufacturing. One firm doing all kinds of Product Development!”
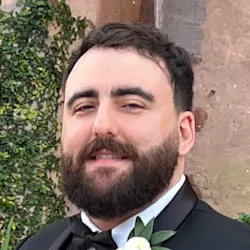
“Great service, fair price, and the parts worked perfectly in our assembly.”
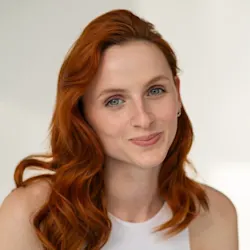
“Top-notch machining and fast shipping. Very satisfied with the results.”
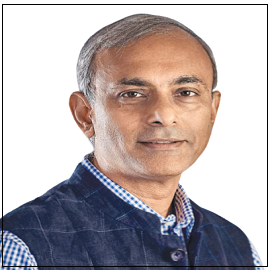
“The next disruption is happening in Prototyping & Manufacturing on-demand and Frigate is leading the way! I personally believe the Frigate's way of IIOT enabled cloud platform with Al.”
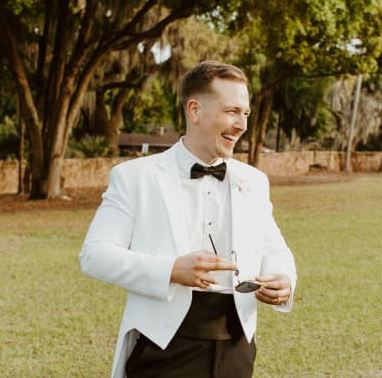
“Frigate delivered high-quality parts at a competitive price. The instant quote tool is a huge plus for us!”

“We appreciate the precision and quality of the machined components in the recent delivery—they meet our specifications perfectly and demonstrate Frigate’s capability for excellent workmanship.”
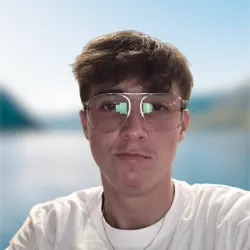
“Flawless execution from quote to delivery.”

“I am absolutely happy to work with supplier like Frigate who were quite proactive & result oriented . Frigate has high willingness team who has strong know how & their passion towards the products & process were absolutely thrilling.”
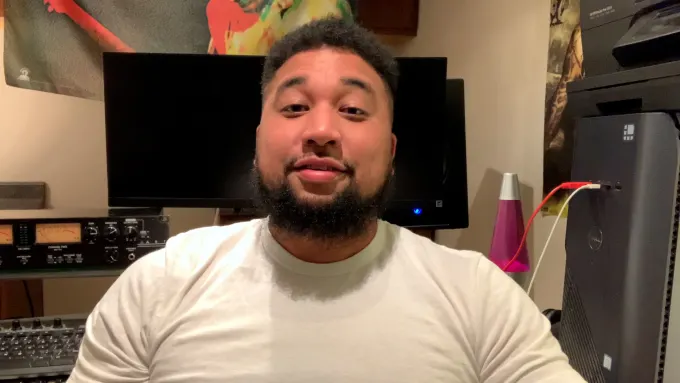
“The precision on these parts is impressive, and they arrived ahead of schedule. Frigate’s process really stands out!”
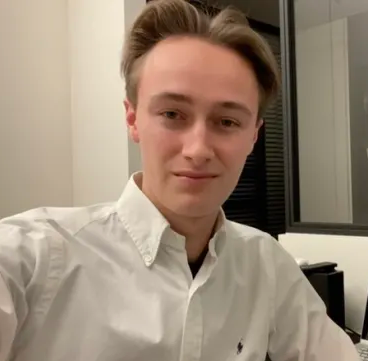
“Parts were exactly as spec’d, and the instant quote made budgeting a breeze.”
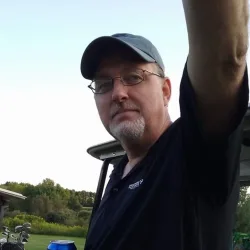
“Good value for the money.”
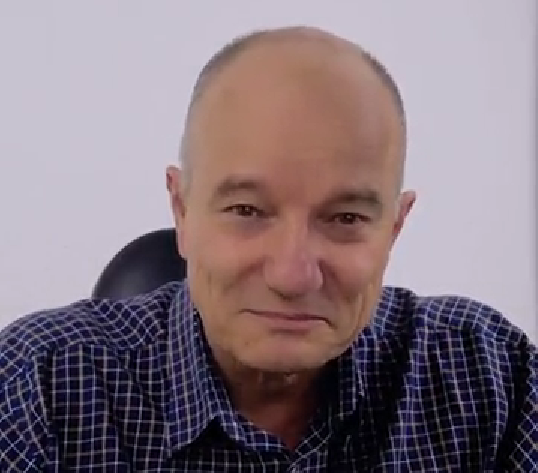
“The finish was perfect, and the team was easy to work with.”

“Working with Frigate has been great. Their proactive, results-driven approach and expertise shine through in every project. It's been a pleasure collaborating with them.”

"We are highly satisfied with the timely delivery and quality of the MIG Welding Cable from Frigate. Their attention to detail, secure packaging, and quick responsiveness stood out. We confidently recommend Frigate Engineering Services Pvt. Ltd. as a reliable manufacturing partner."
Having Doubts? Our FAQ
Check all our Frequently Asked Question
Frigate utilizes precision CNC machining and laser cutting technologies. These methods facilitate tight tolerances and ensure that components adhere to specified dimensions throughout fabrication.
Frigate implements a combination of thorough material testing and controlled processing conditions. This approach minimizes thermal distortion and mechanical stress, preserving the inherent properties of the plastics used.
Frigate adopts lean manufacturing principles and advanced scheduling software. These strategies streamline operations, allowing for efficient resource allocation and minimizing idle time, thus expediting production cycles.
Frigate employs computer-aided design (CAD) and finite element analysis (FEA) to predict material behavior and performance. This predictive modeling allows for the early identification of potential issues, improving design efficacy and reducing errors.
Frigate adheres to industry-specific standards and regulations through rigorous documentation and quality audits. This commitment ensures that all fabricated products meet their intended applications' safety and performance criteria.
Manufacturing Capability/Capacity
Ferrous casting
Mold size(max): 1m X 1m
Weight Range: 1 KG ~ 30 KGS
Mold size(max): 1.5m X 1.5m
Weight Range: 30 KG ~ 150 KGS
Mold size(max): 3m X 3m
Weight Range: 100 KG ~ 1000 KGS
Mold size(max): 500 MM X 500 MM
Weight Range: 0.250 KG ~ 20 KGS
Mold size(max): 500 MM X 500 MM
Weight Range: 0.100 KG X 20 KGS
Non-ferrous casting
Capacity: 5000 MT/a
Range of weight: 100 gm to 20 KGS
Mold size(max): 1 M X 1 M
Weight Range: 0.5 KG X 50 KGS
Mold size(max): 1 M X 1 M
Weight Range: 0.5 KG X 50 KGS
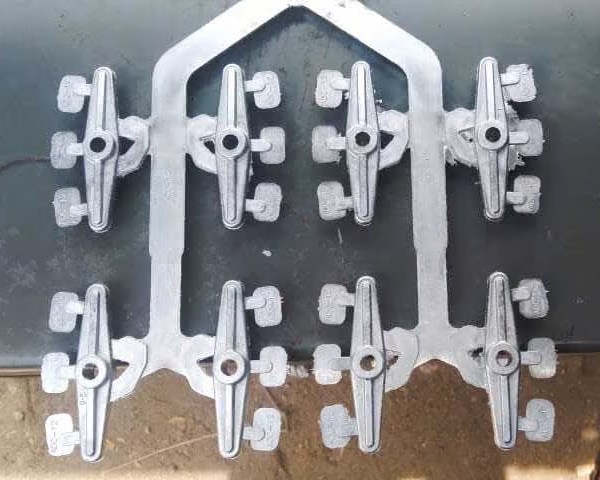
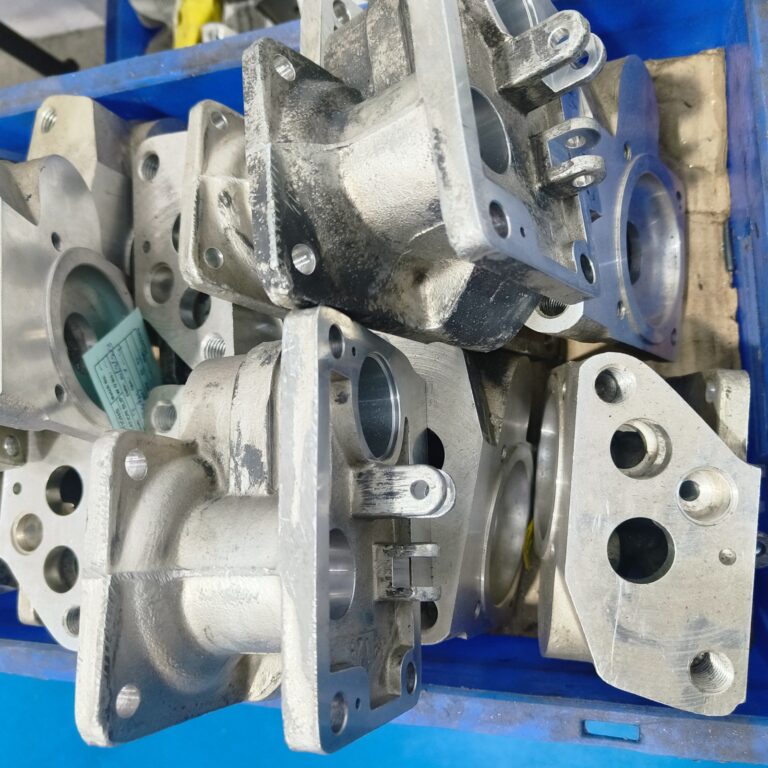
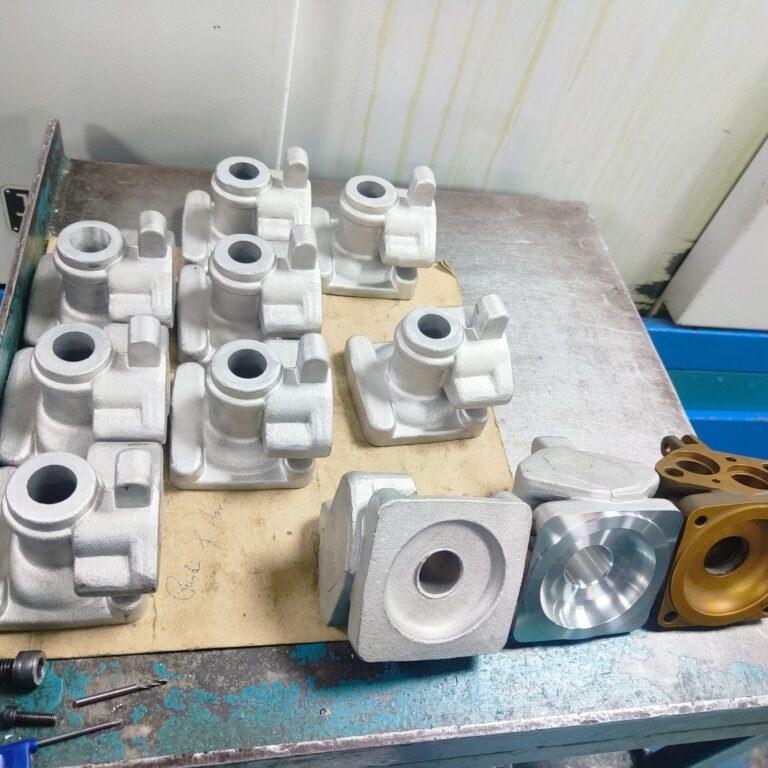
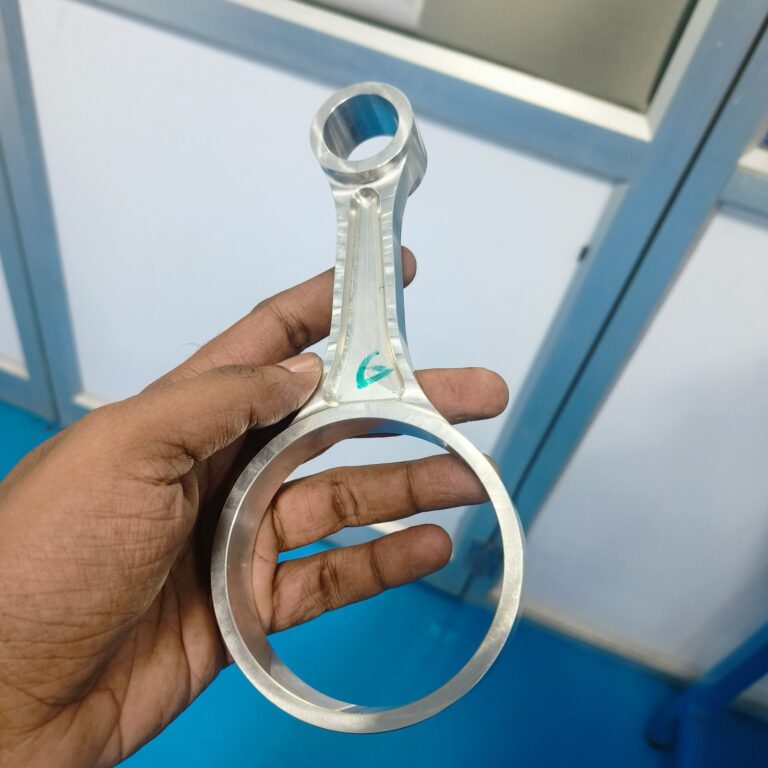
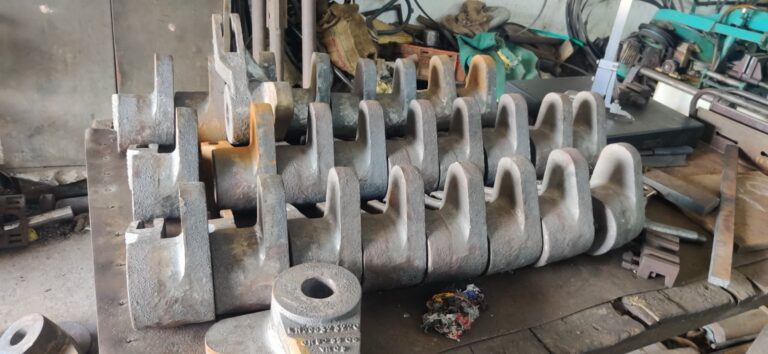
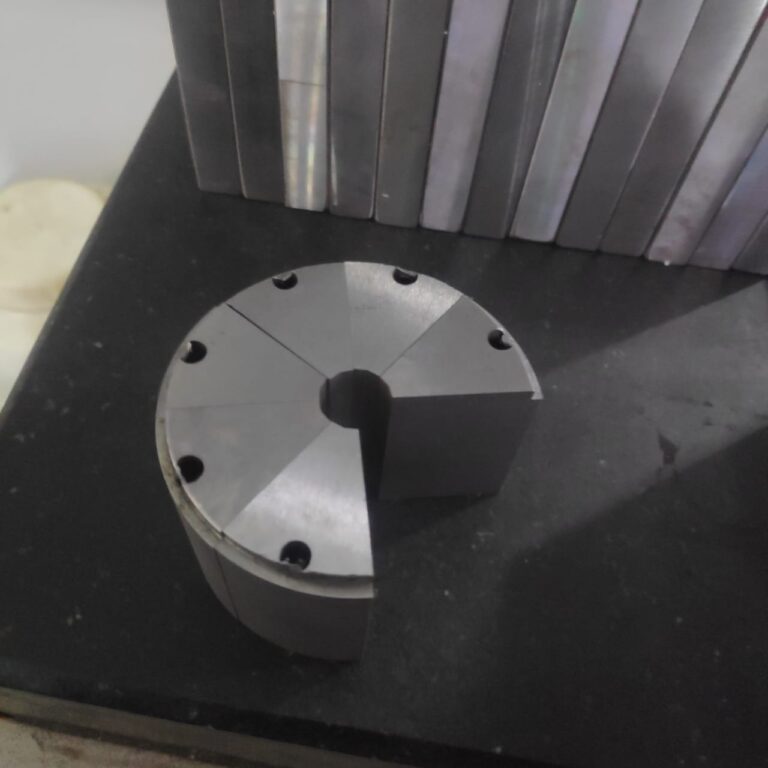
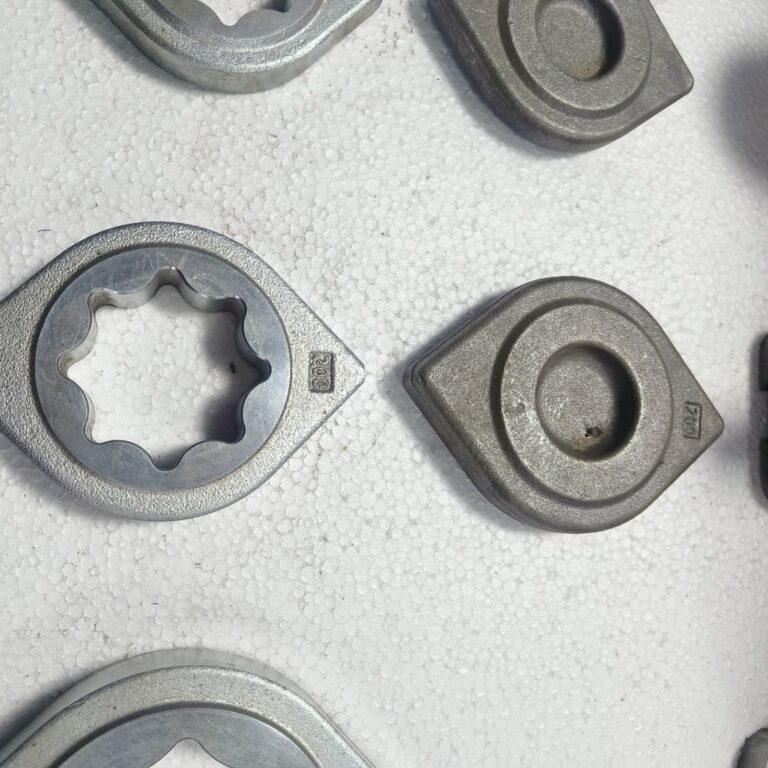
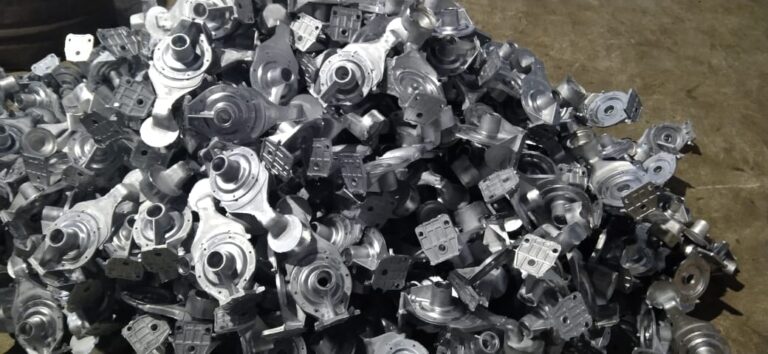
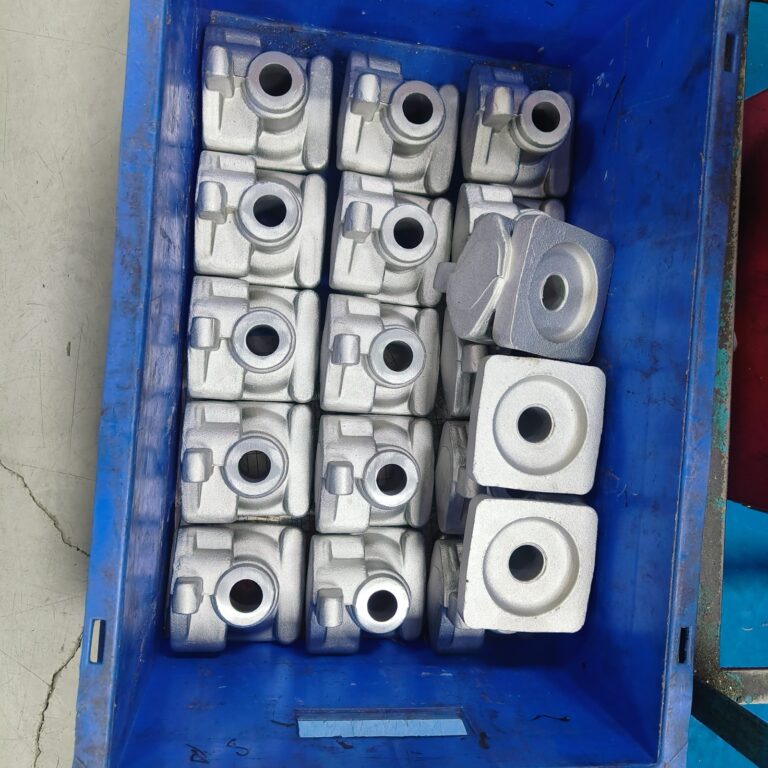
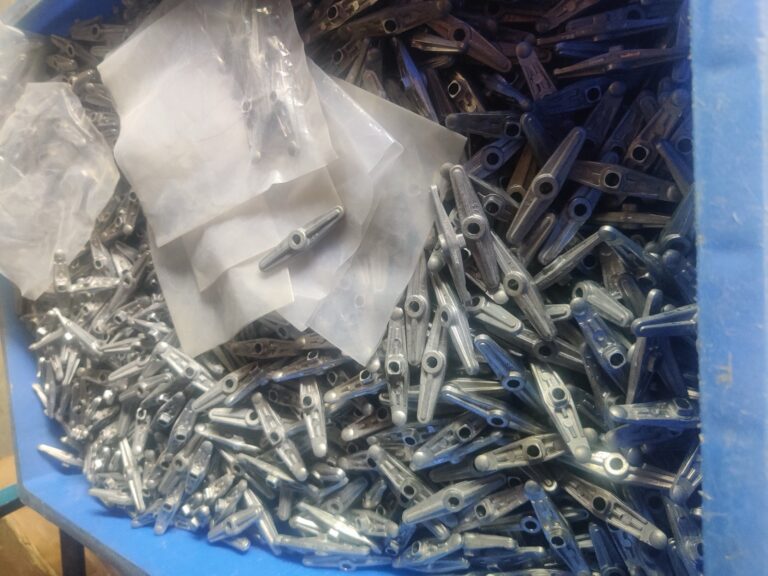
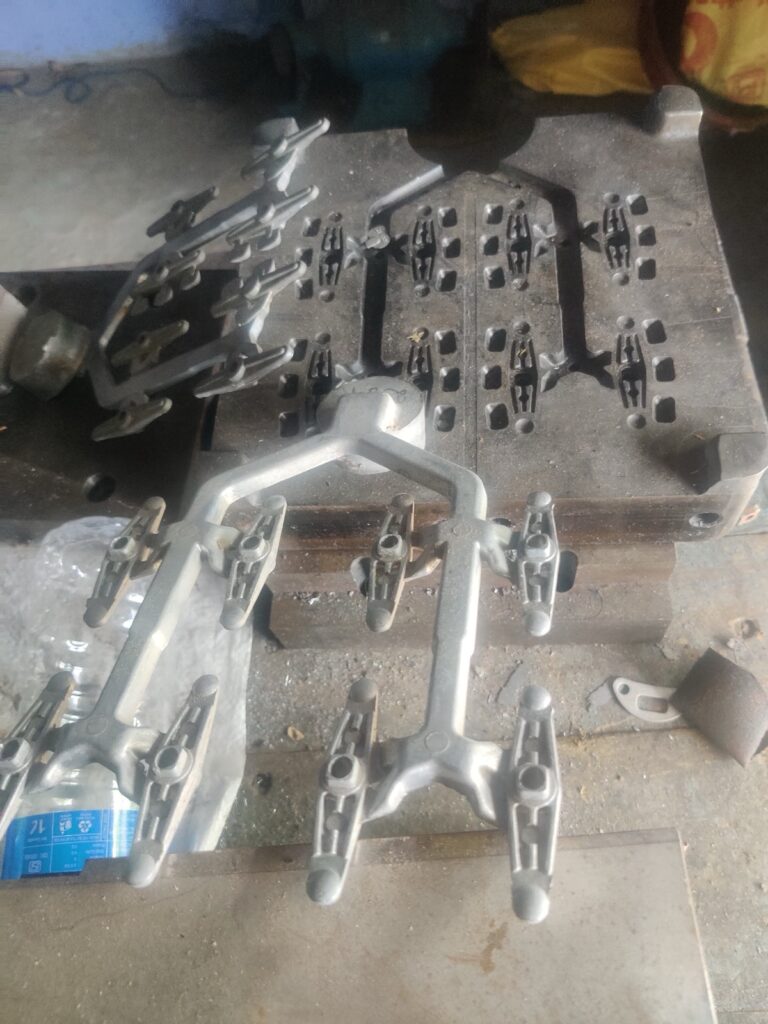
Forging
Capacity: 20,000 Tons per Annum
Range of weight: 300 KG to 1 Ton
Hammering: 5 Ton
Range of weight: 0.2 KG to 200 KGS
Hammering: 1600 Ton Hydraulic press
Ring size: 350 MM OD to 3000 MM OD
Range of weight: 15 KGS to 3200 KGS
Materials
Carbon Steel, Stainless Steel (AUSTENITE), Alloy Steel, Stainless Steel (MARTENSITE), etc.
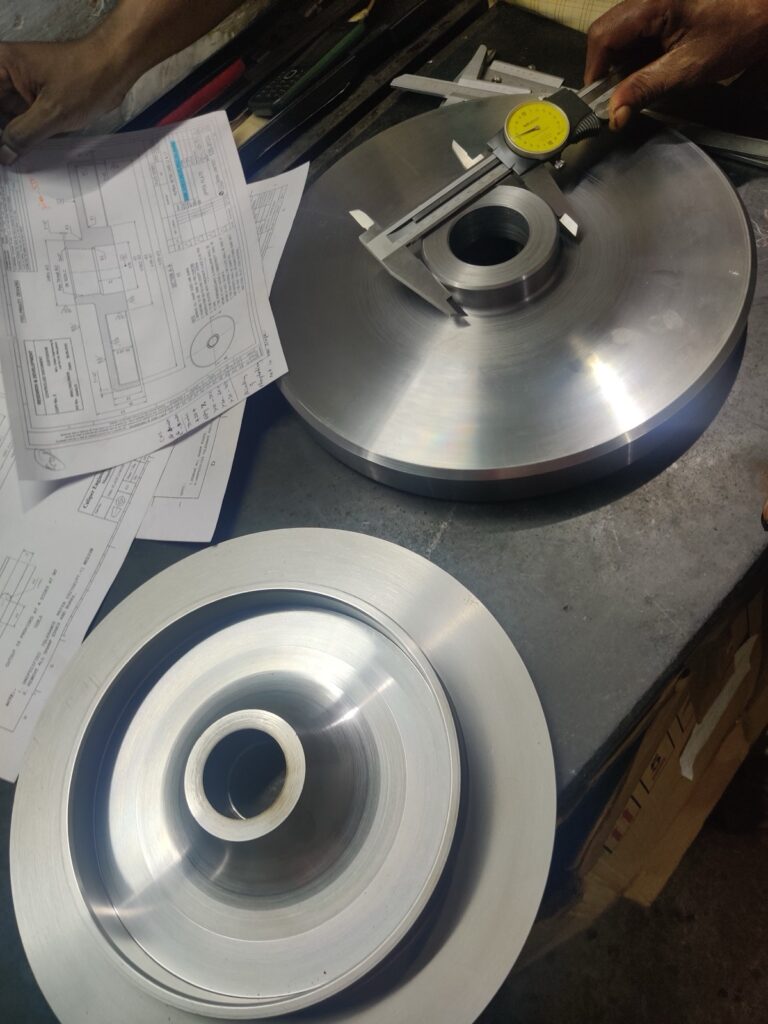
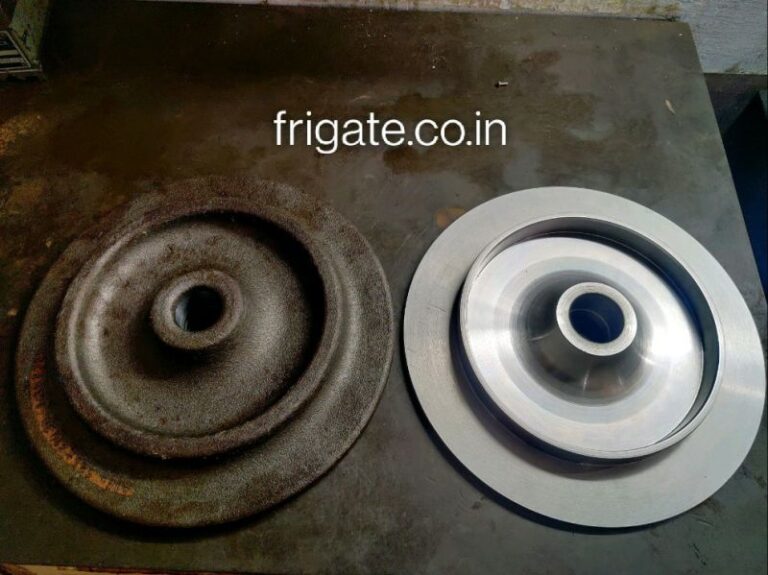
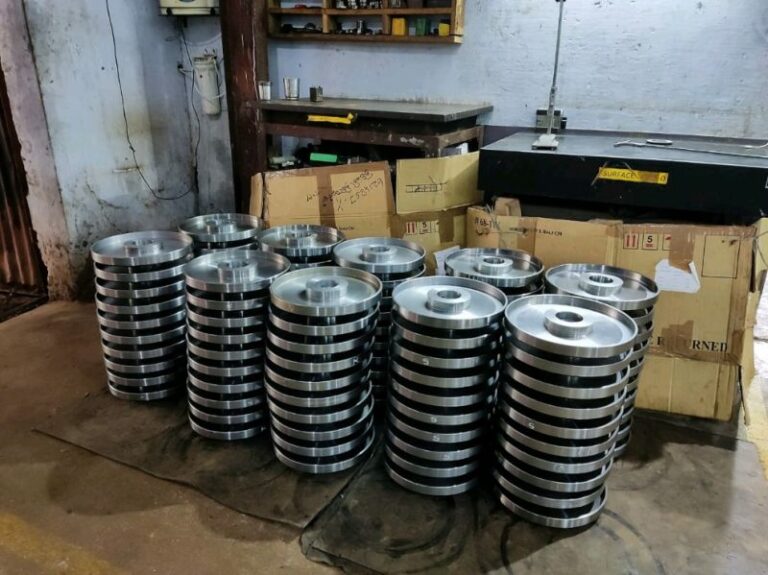
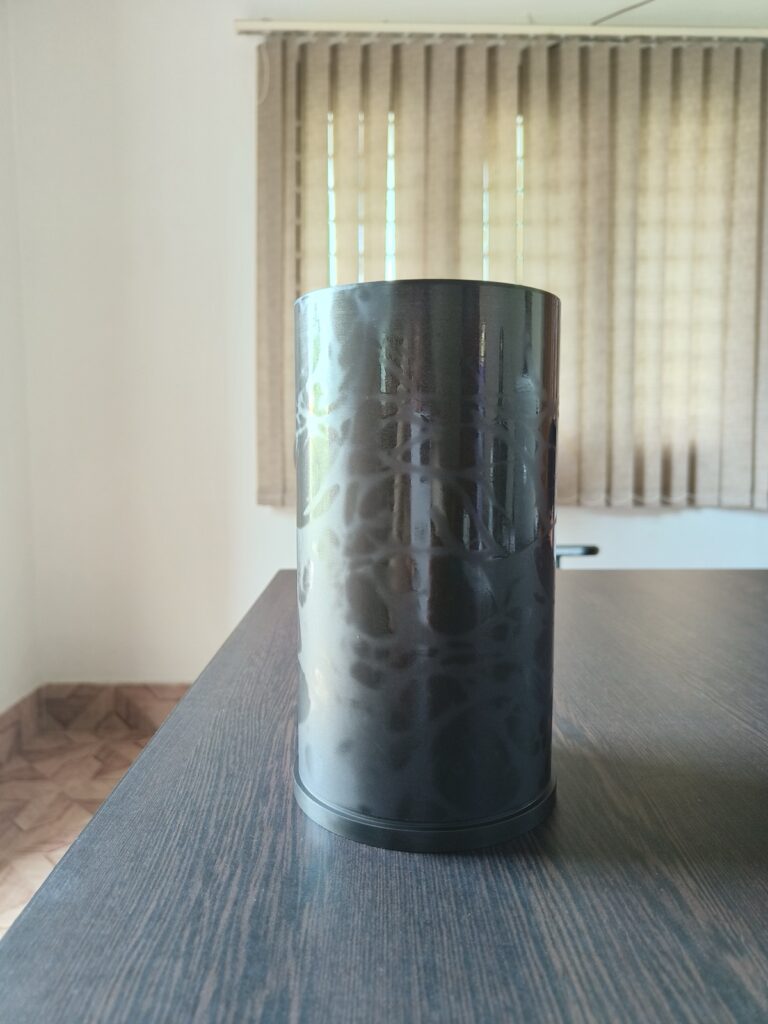
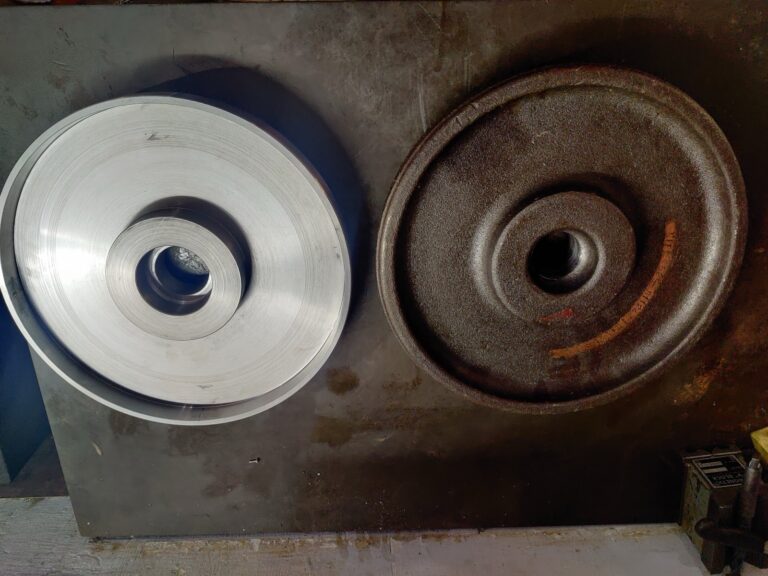
Machining
1 to 1000 MM
1 to 1000 MM
1 to 1000 MM
Materials
Steel, Aluminum, Brass, Copper, Titanium, Nickel Alloys, Tungsten Carbide, etc.
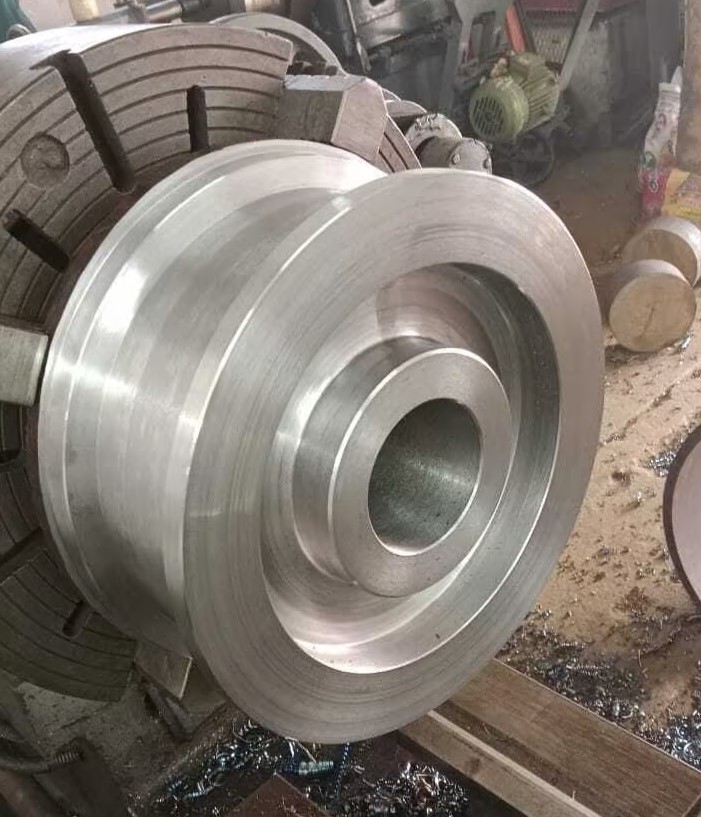
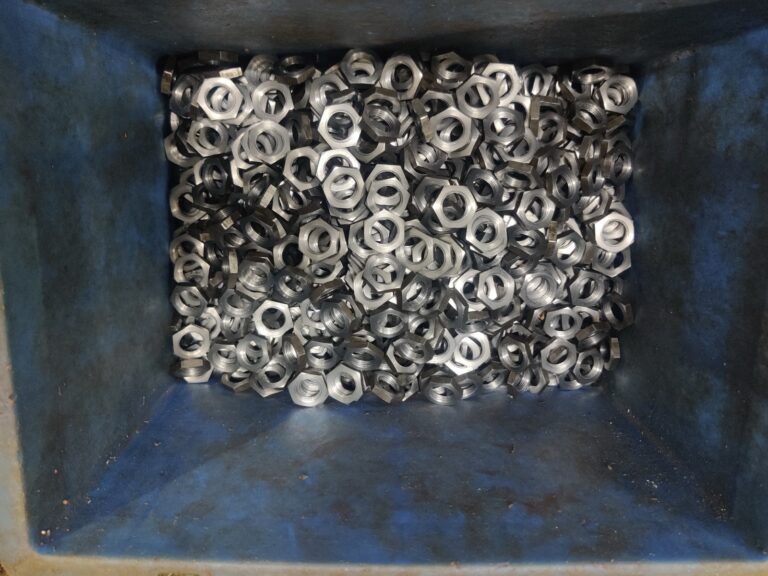
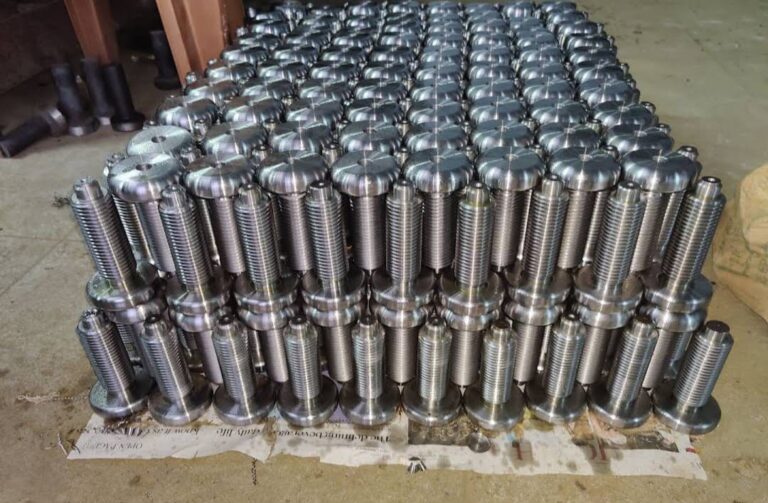
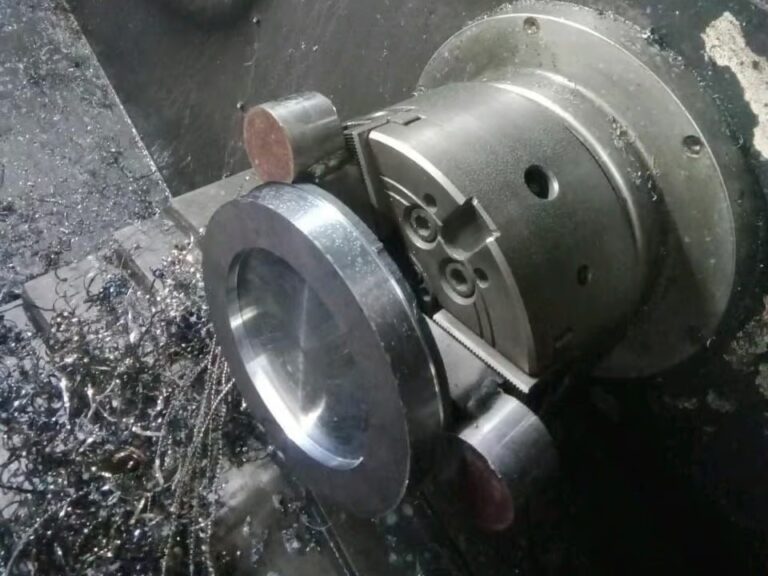
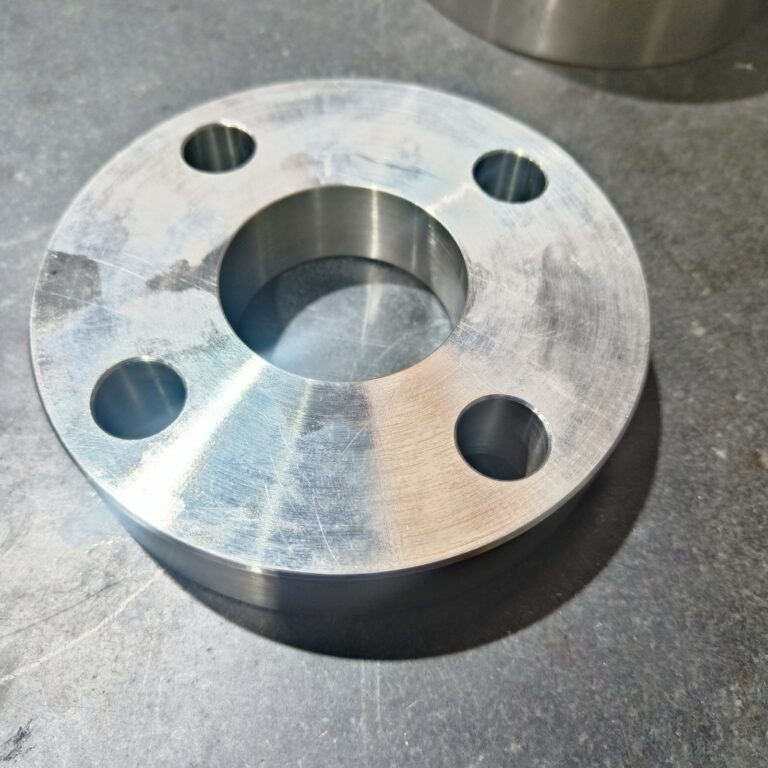
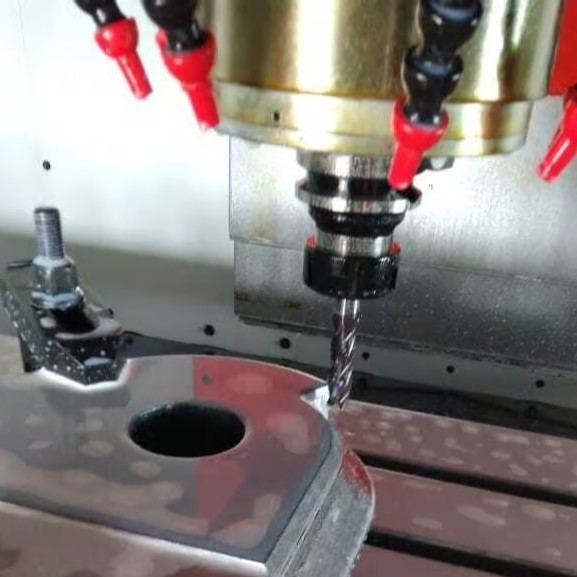
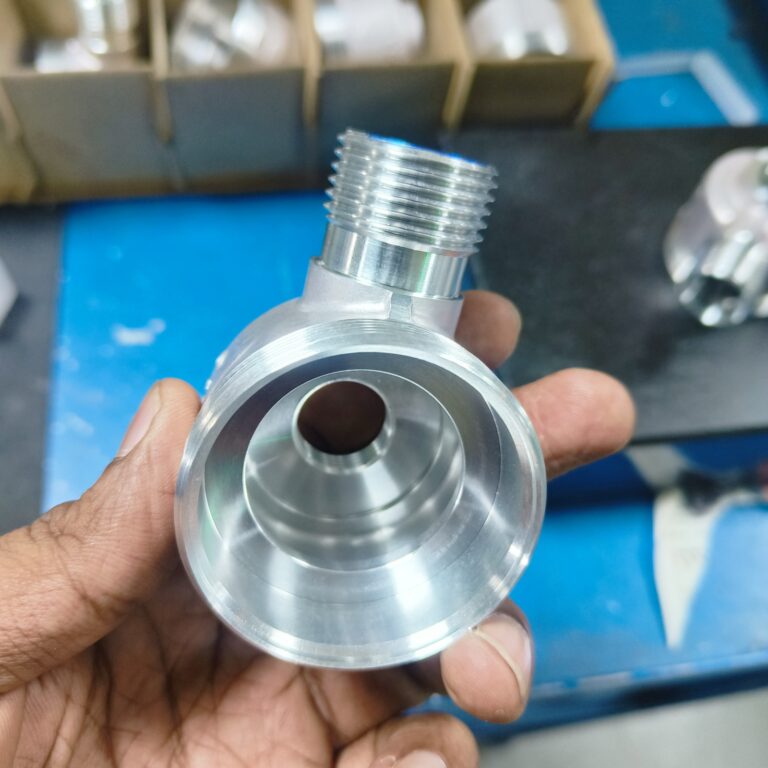
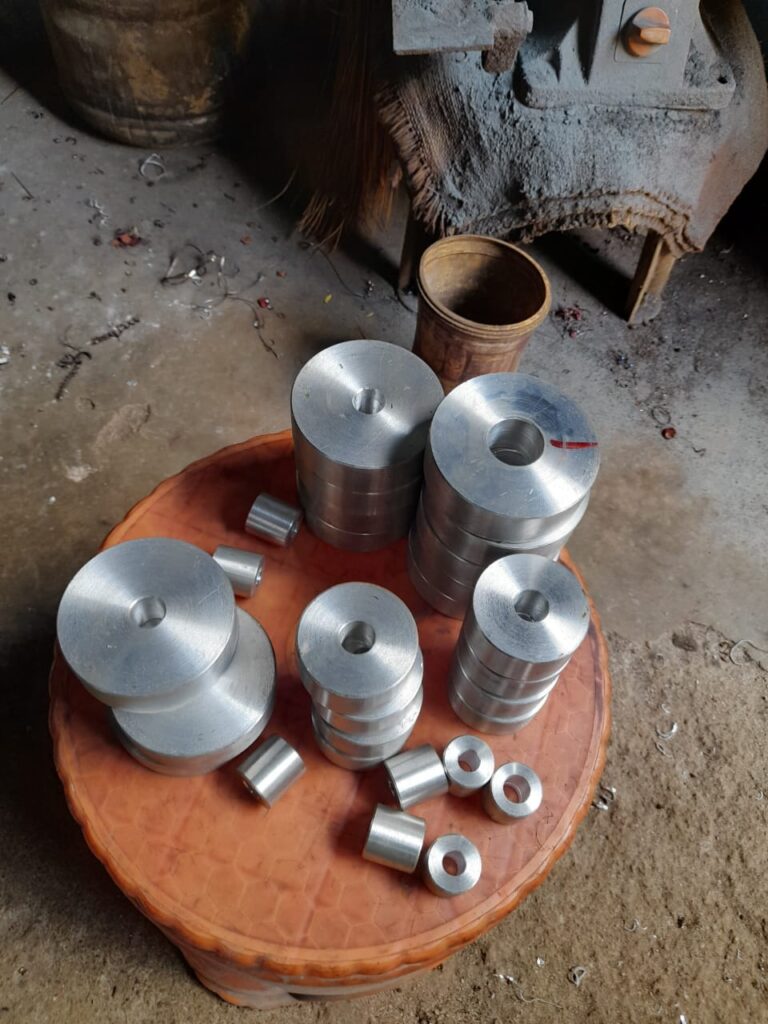
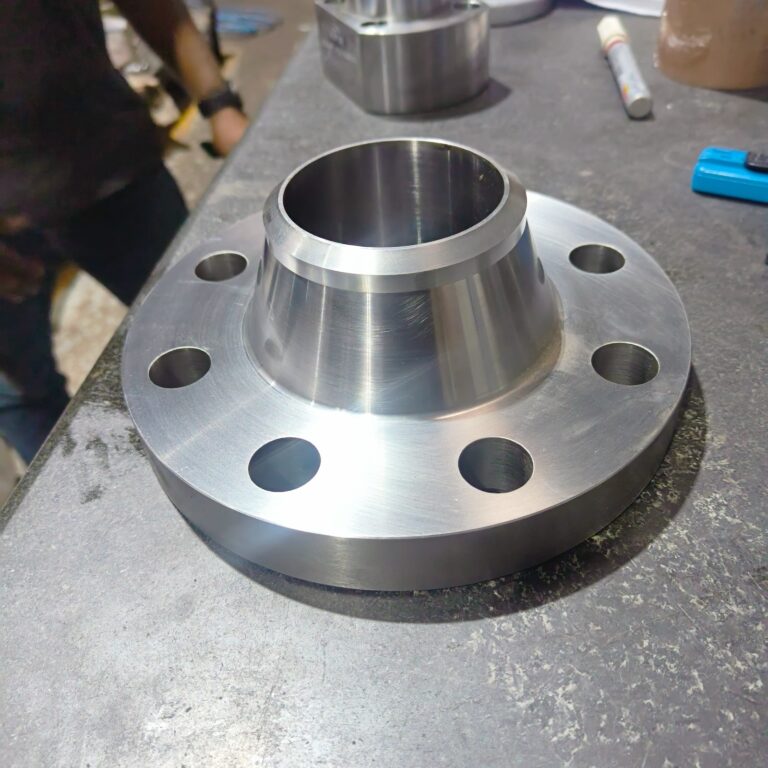
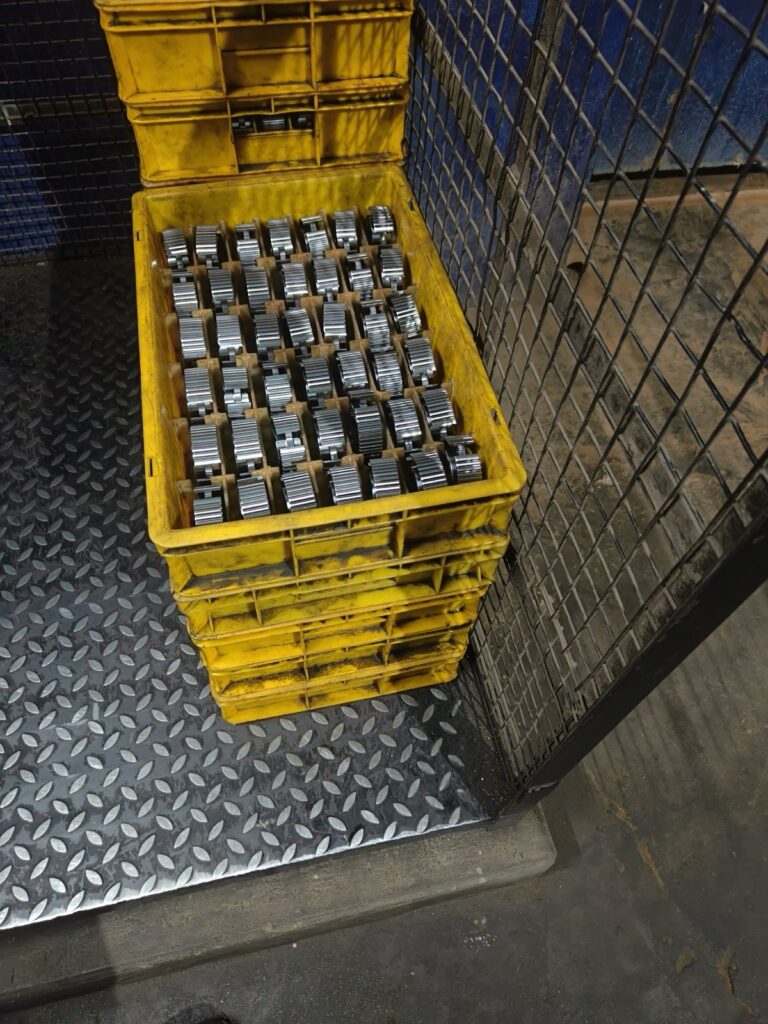
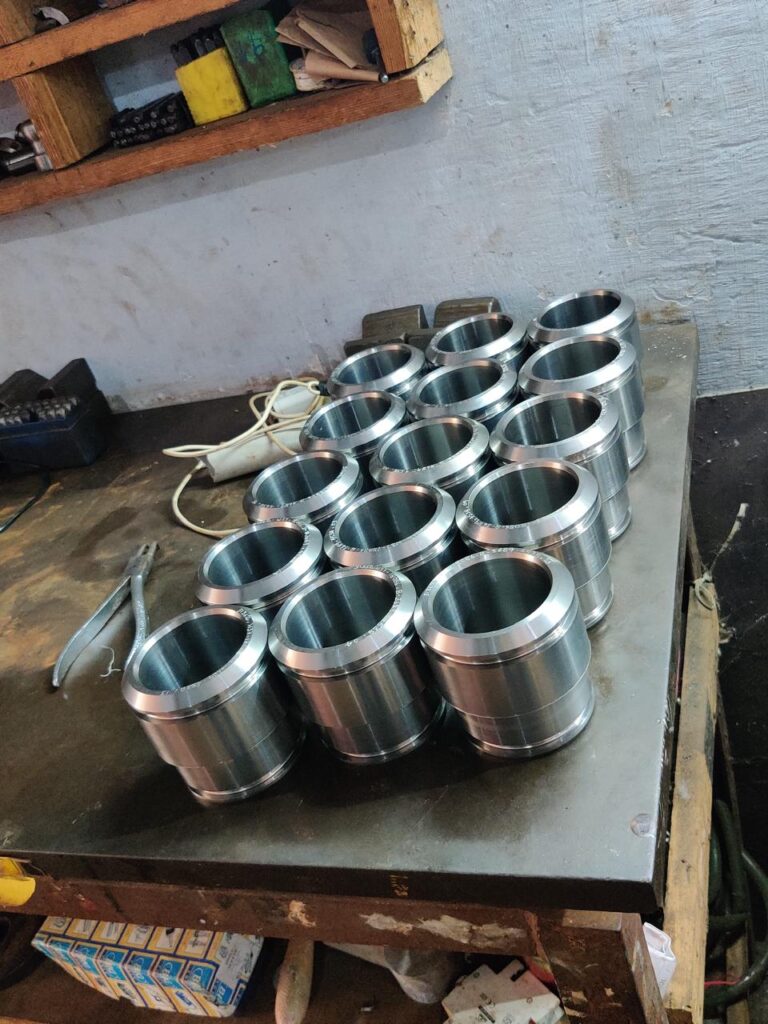
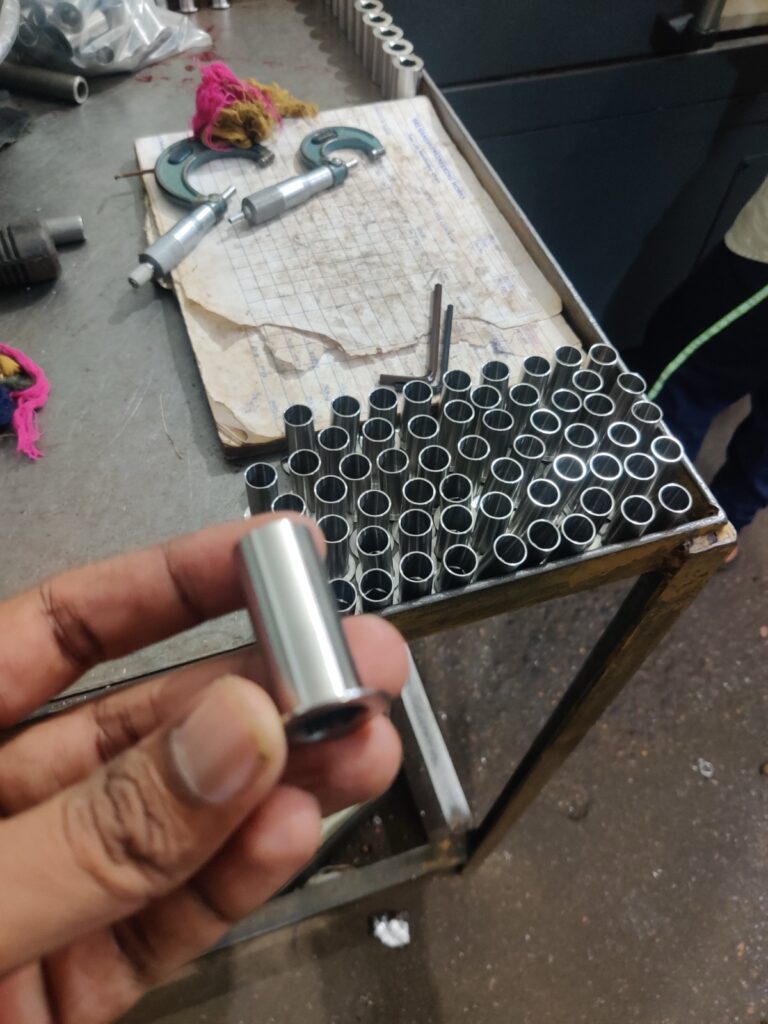
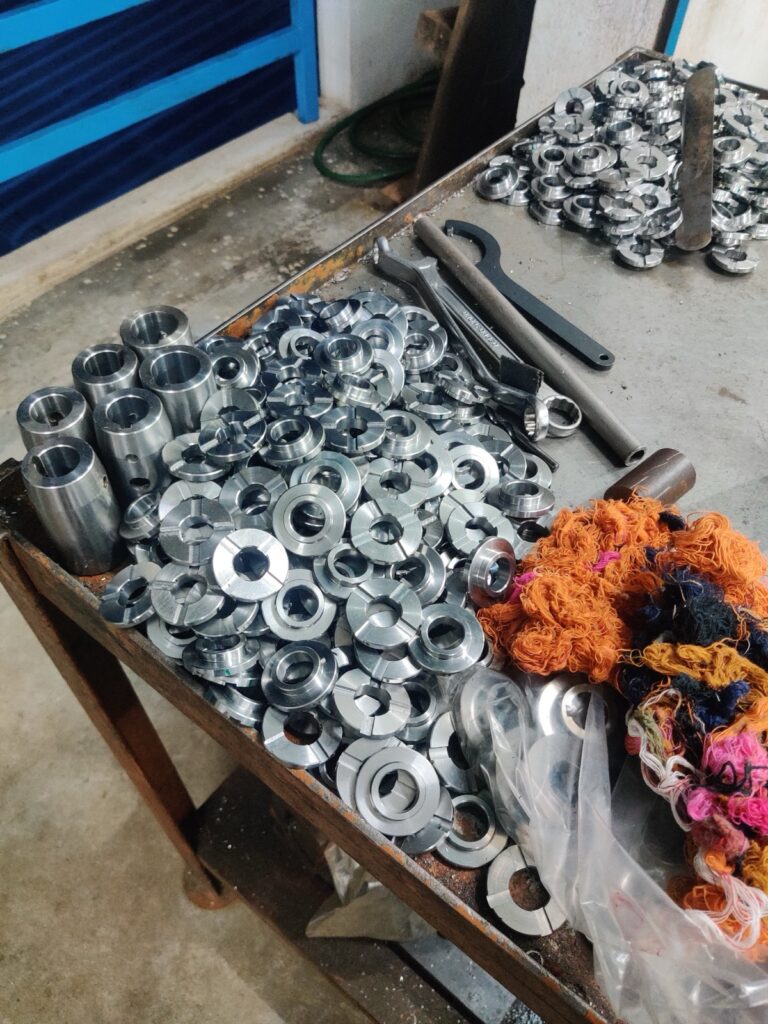
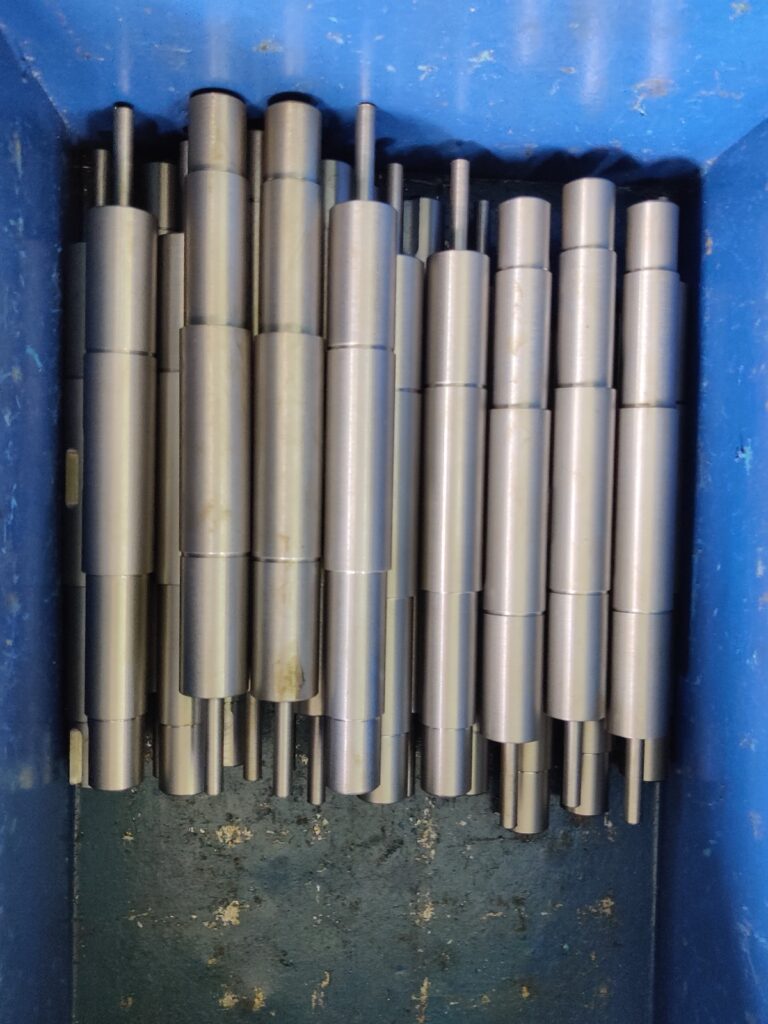
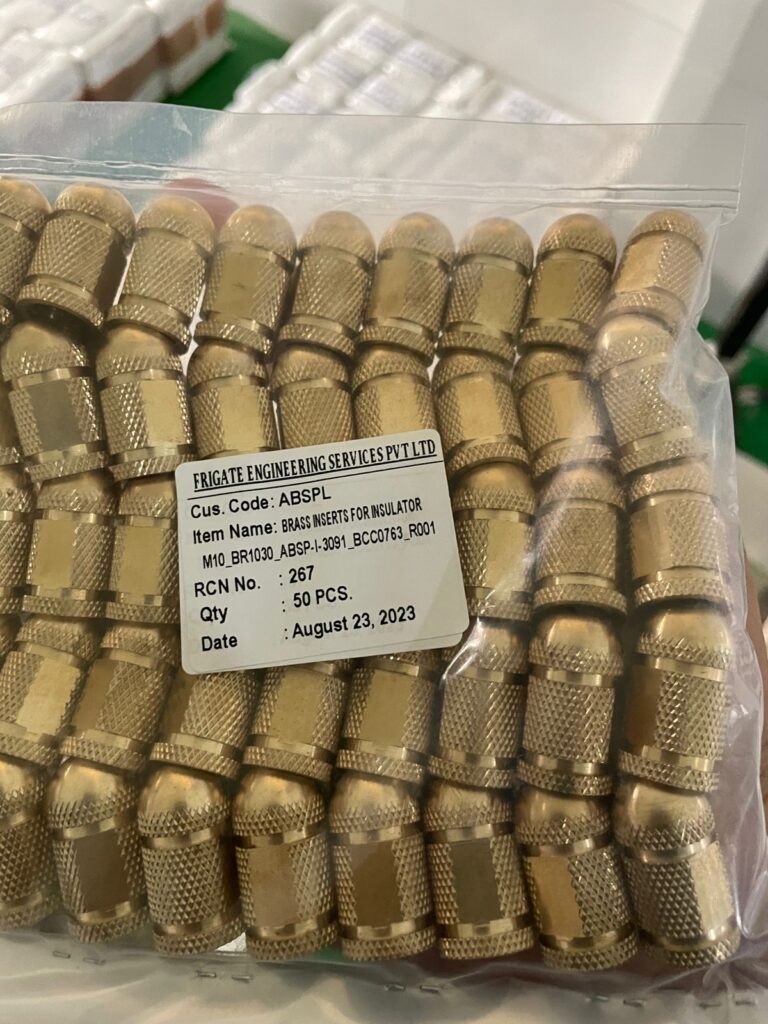
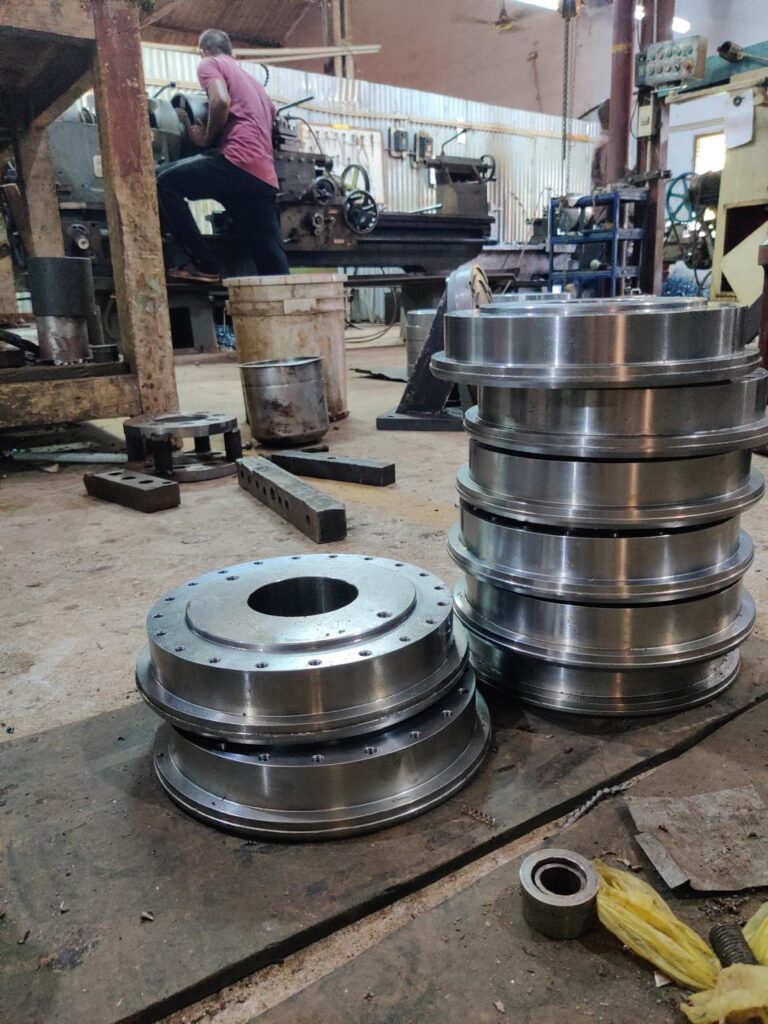
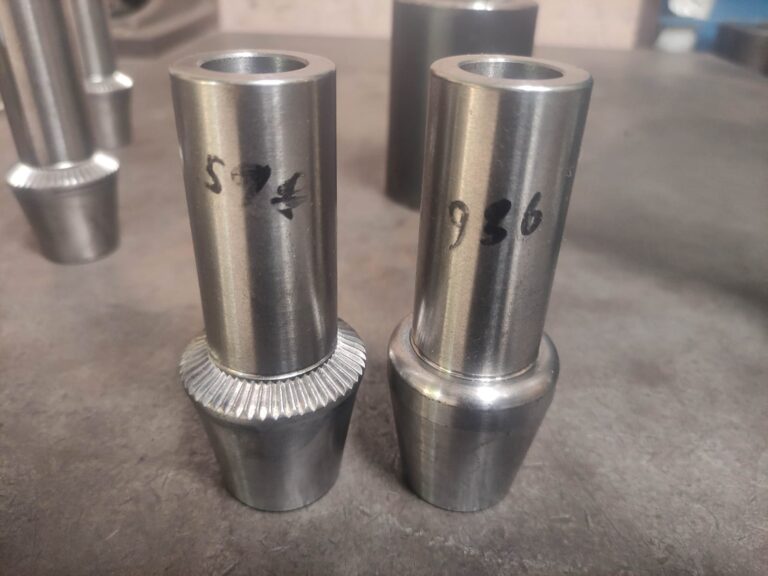
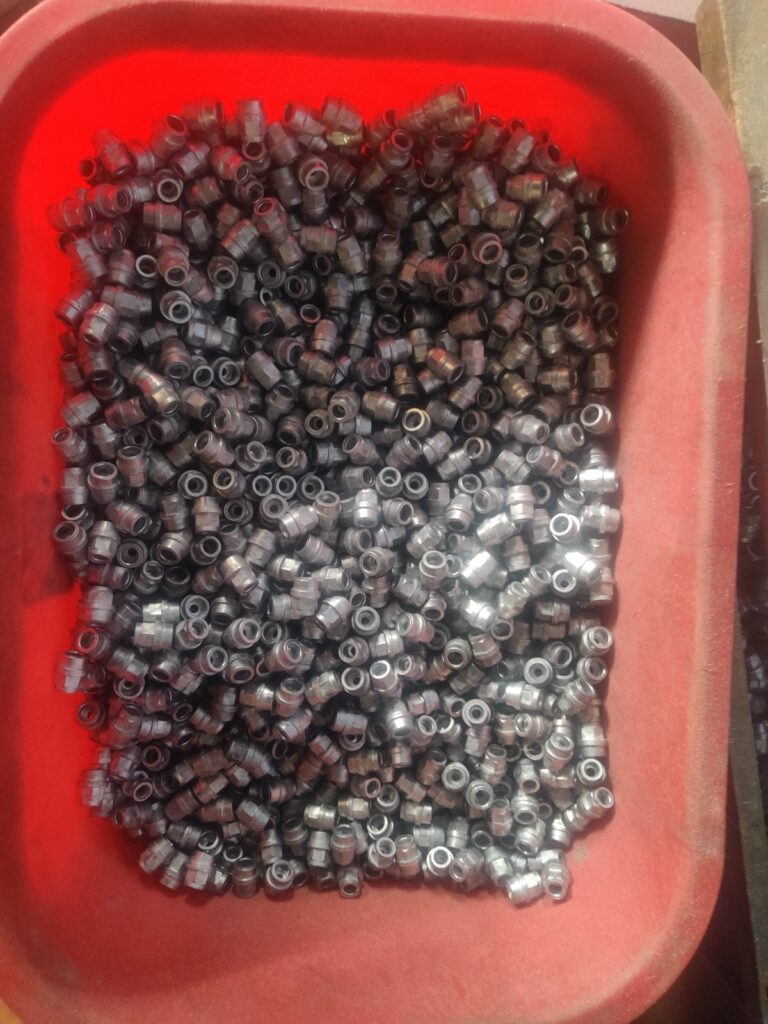
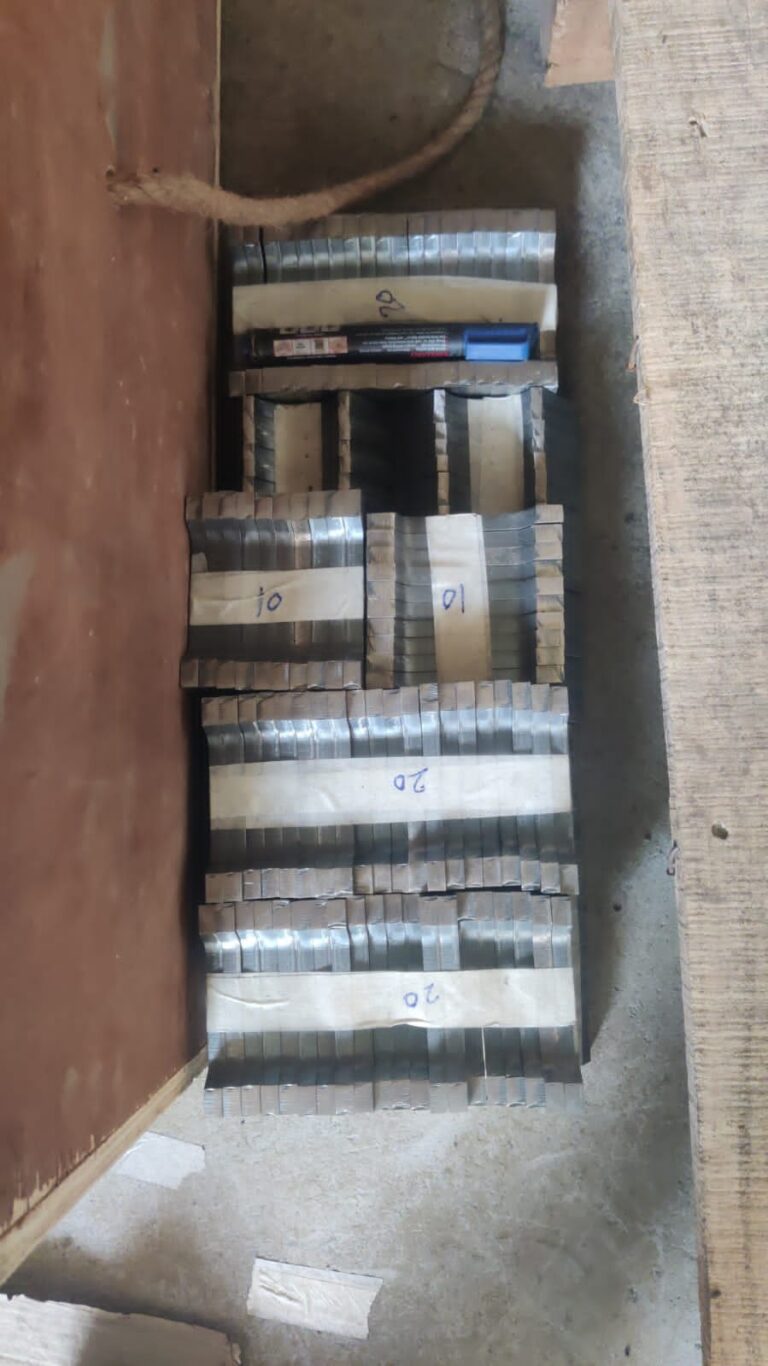
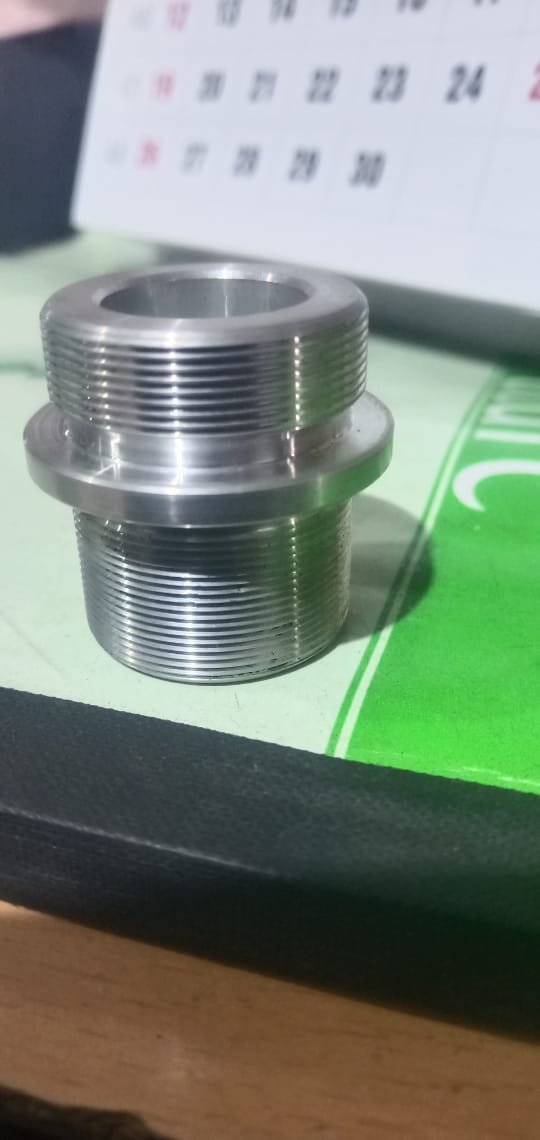
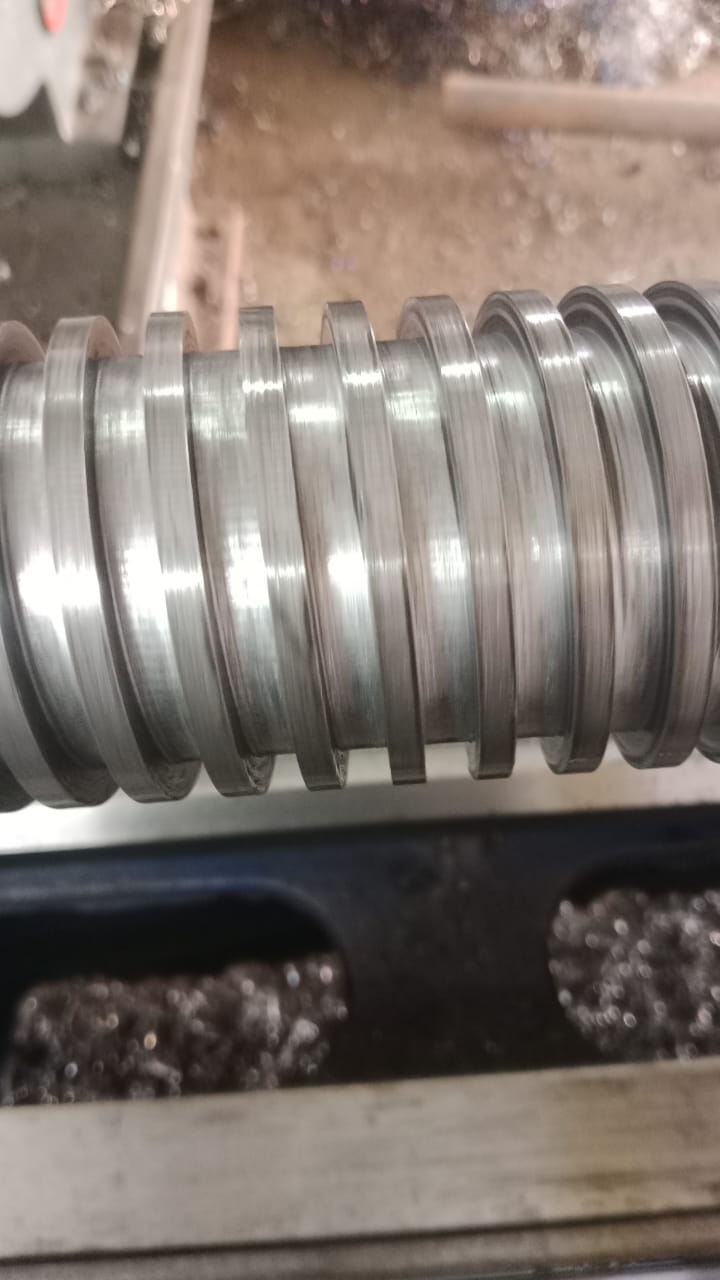
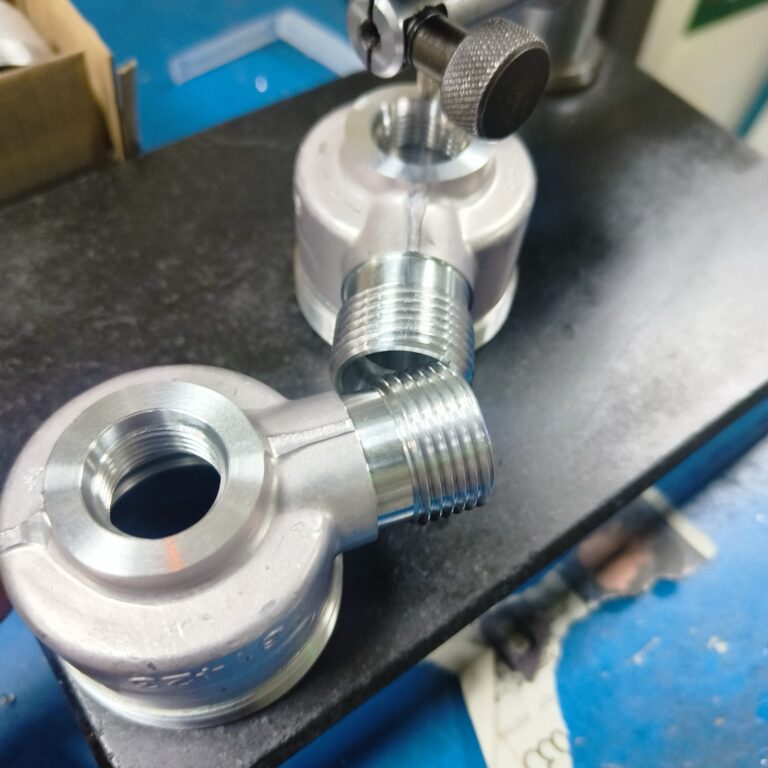
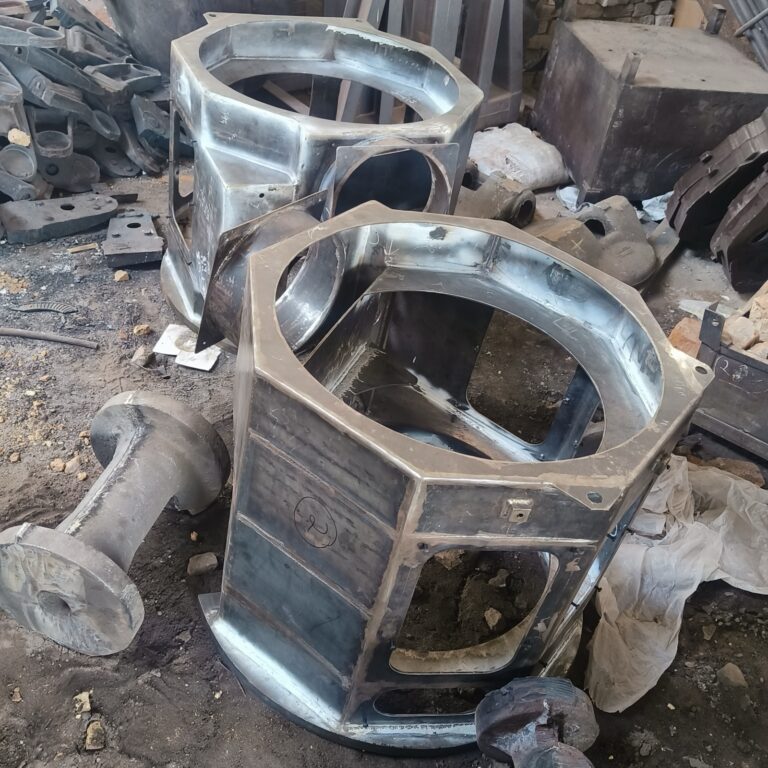
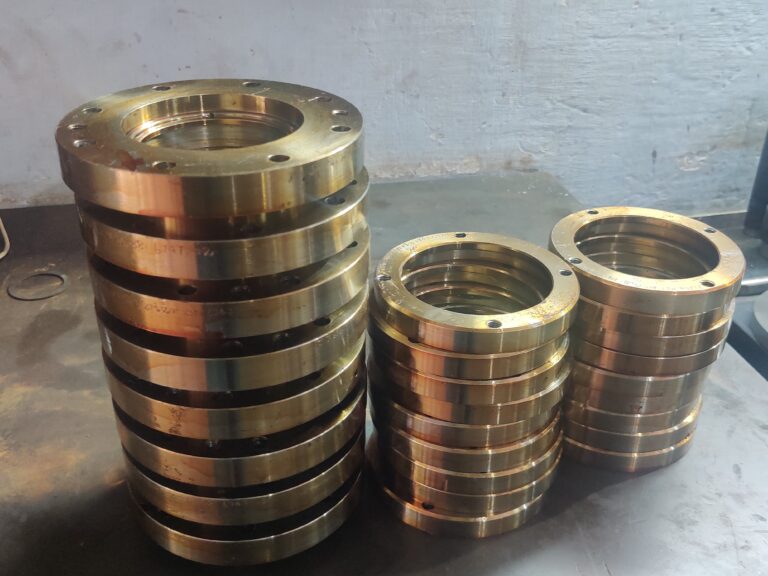
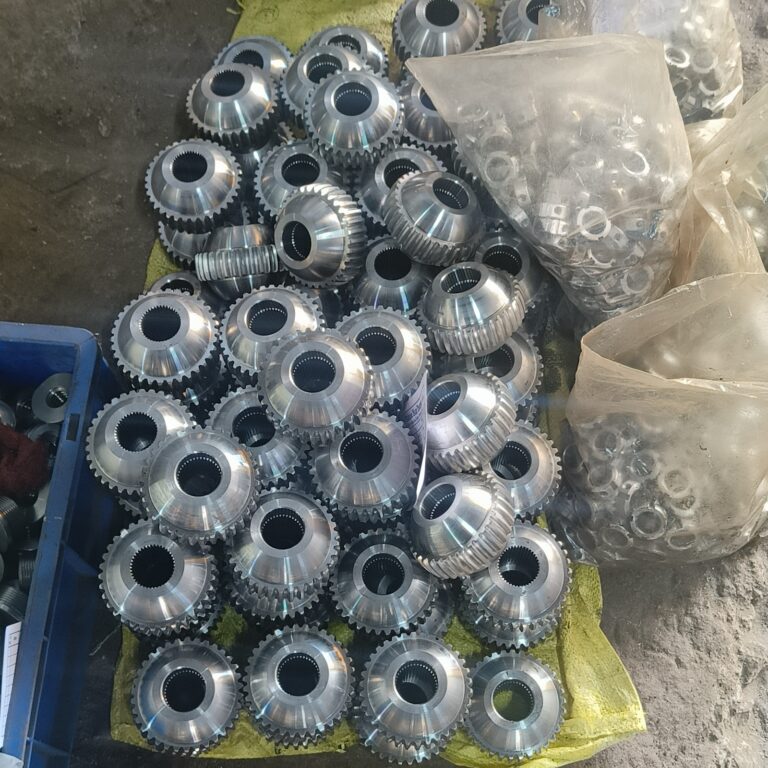
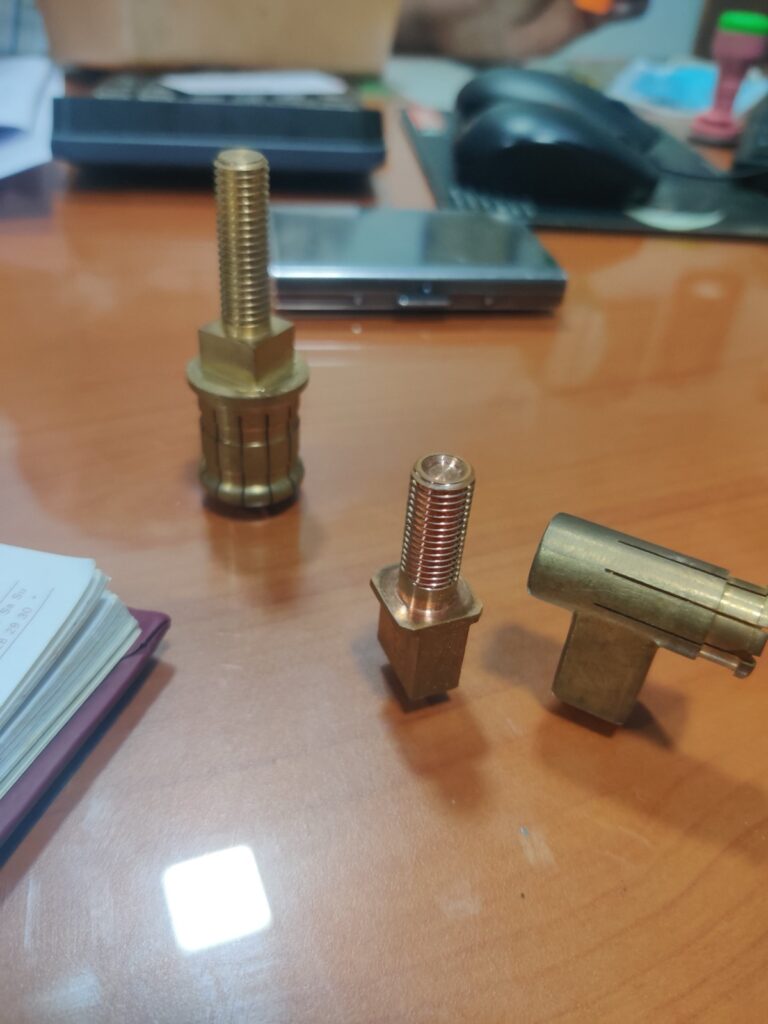
Plastics
Materials
1250 X 1250 MM
Within 10 microns
Engineering Plastics, Polyethylene, Polypropylene, Polyvinyl chloride, Polyethylene terephthalate, Bioplastics, etc.
Rubber
Materials
Natural rubber, Styrene-Butadiene Rubber, Nitrile Butadiene Rubber, Silicone Rubber, Fluorocarbon Rubber, Recycled Rubber, etc.
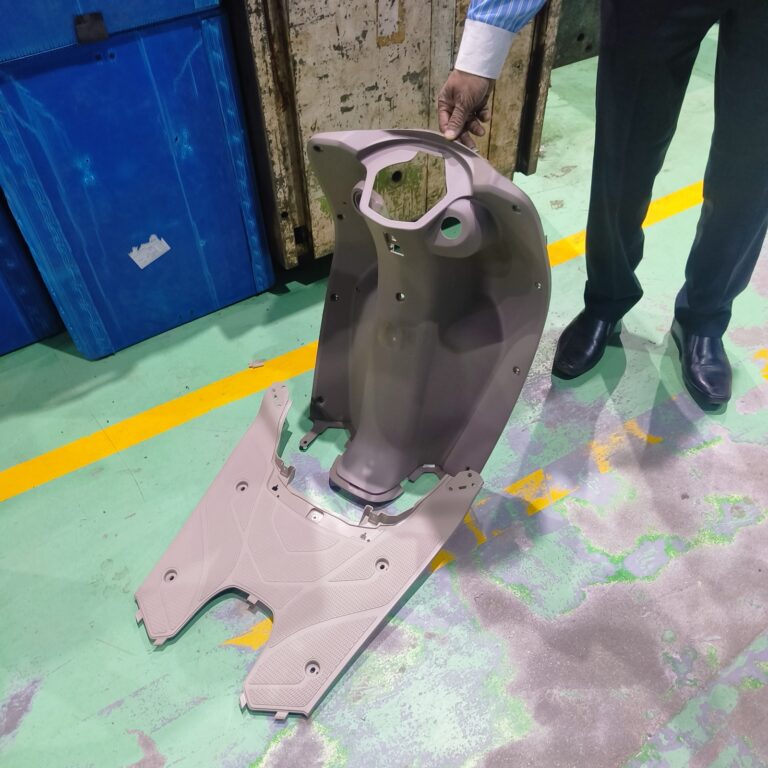
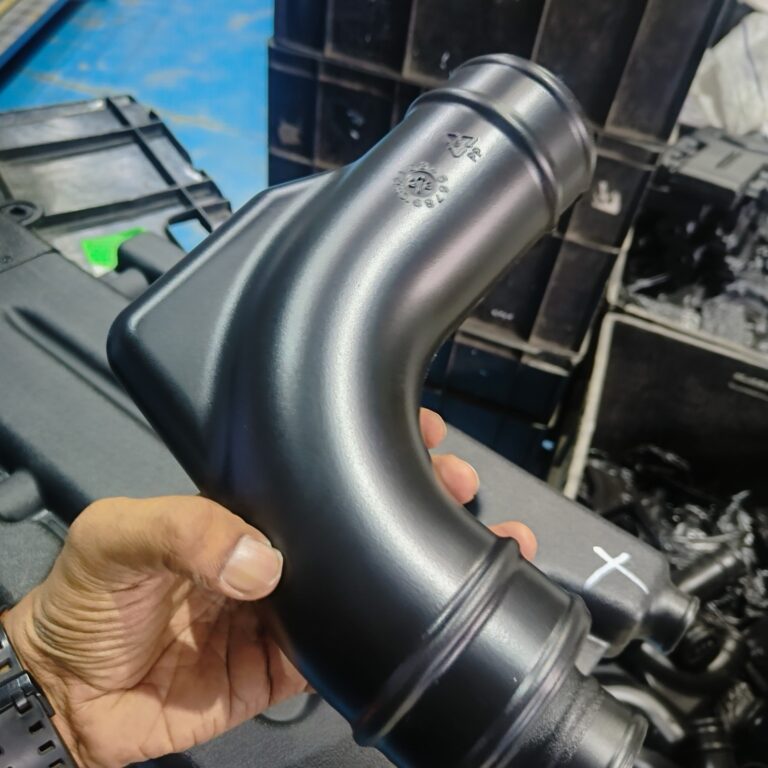
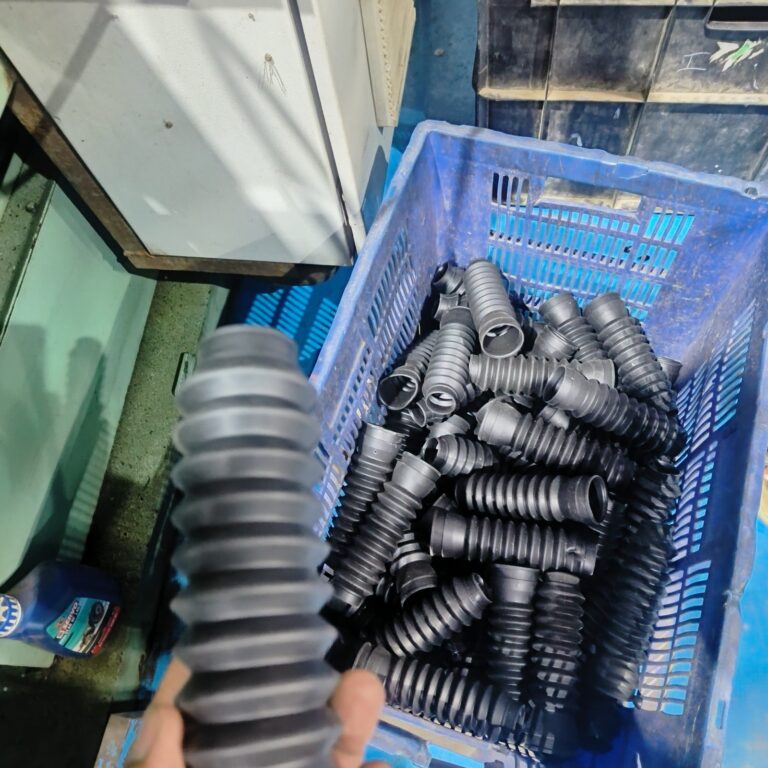
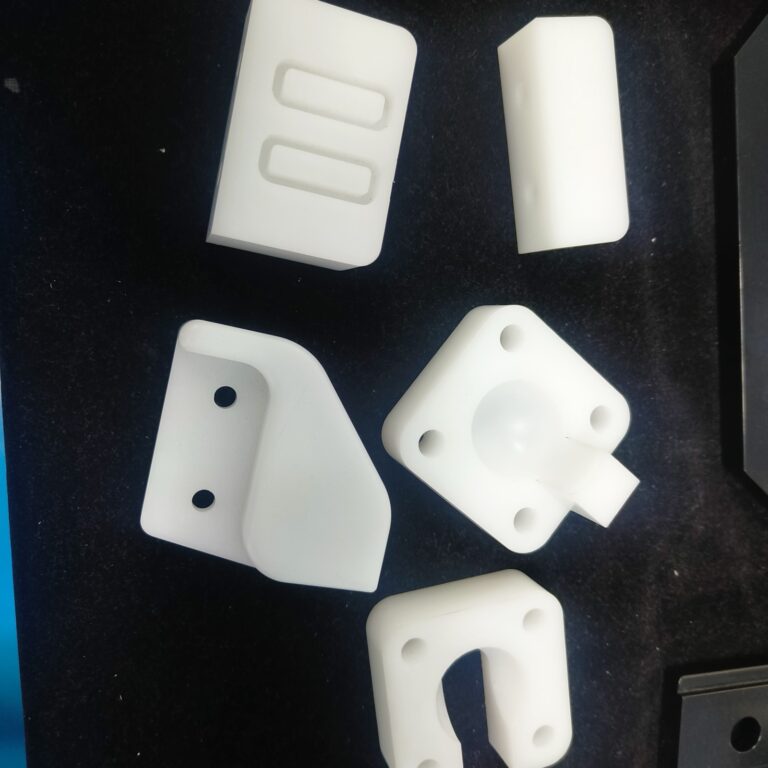
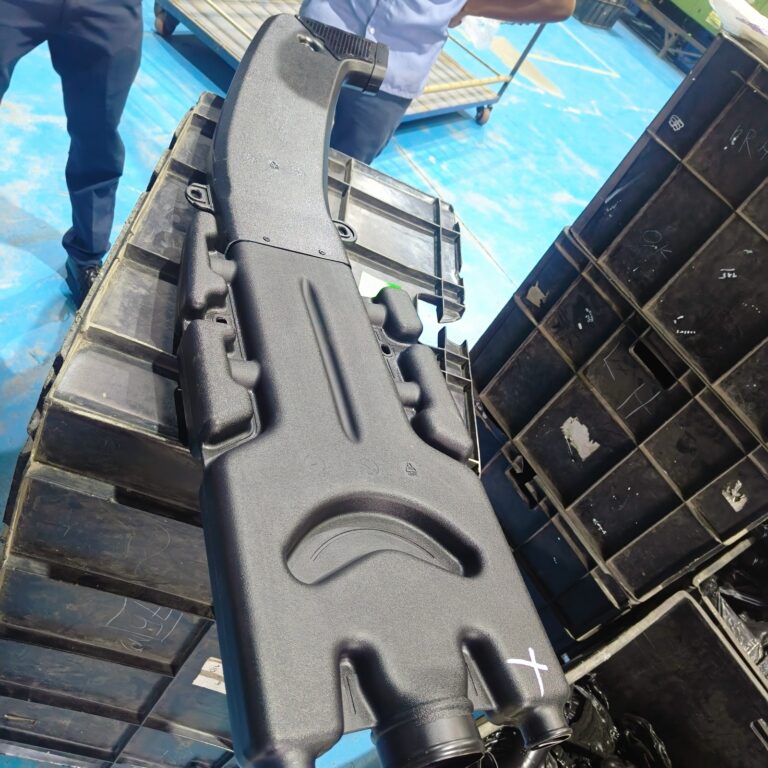
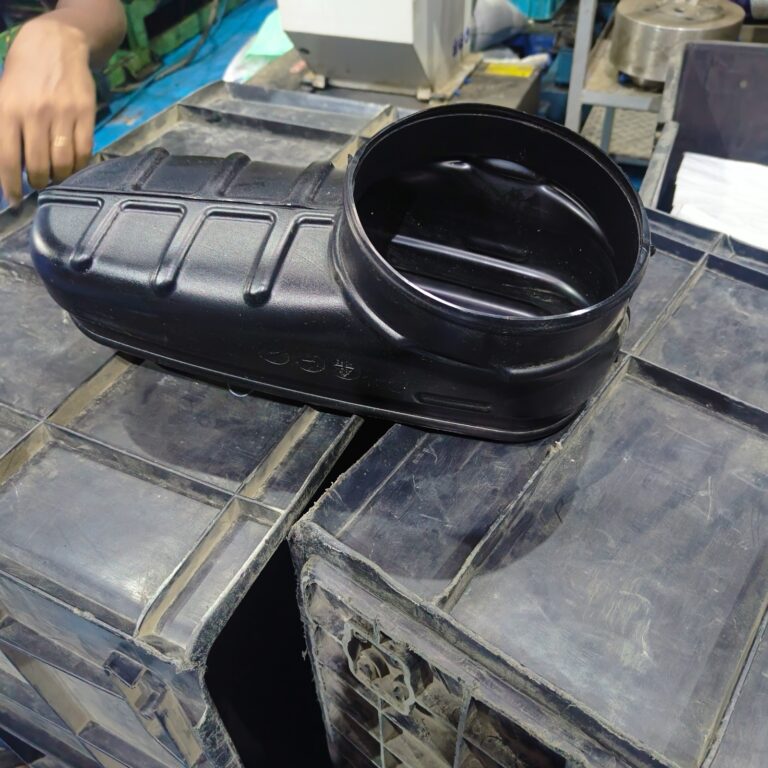
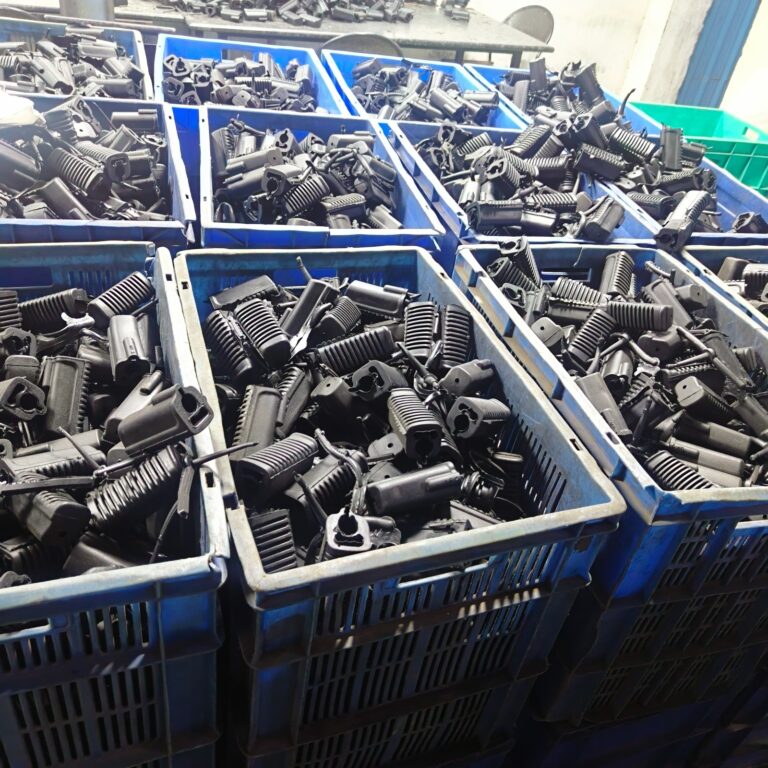
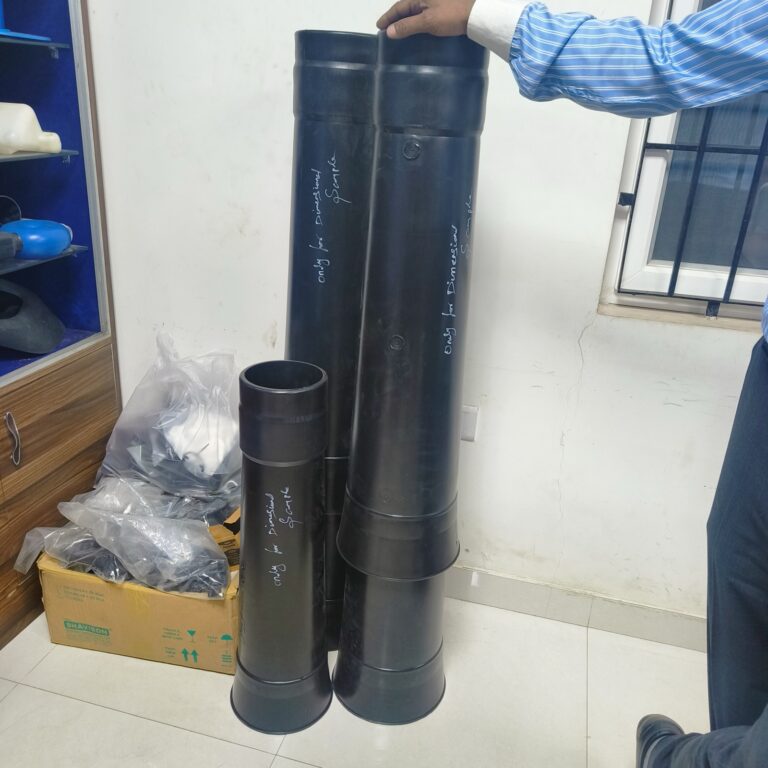
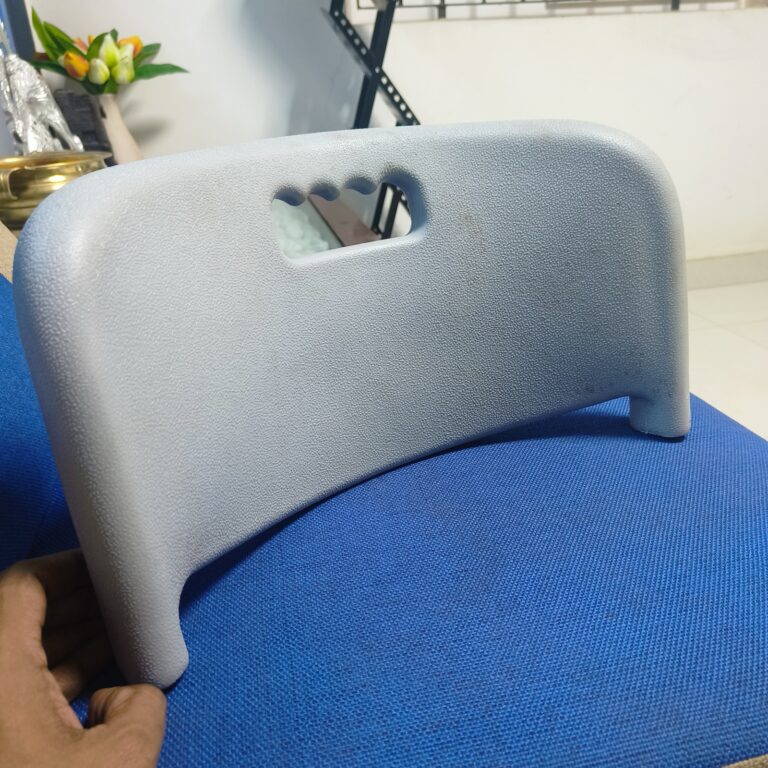
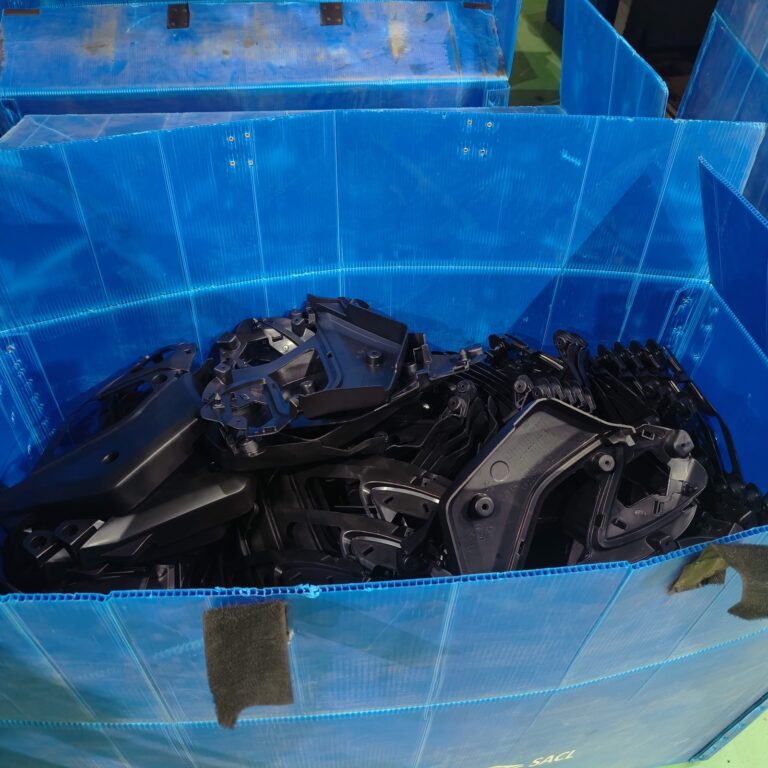
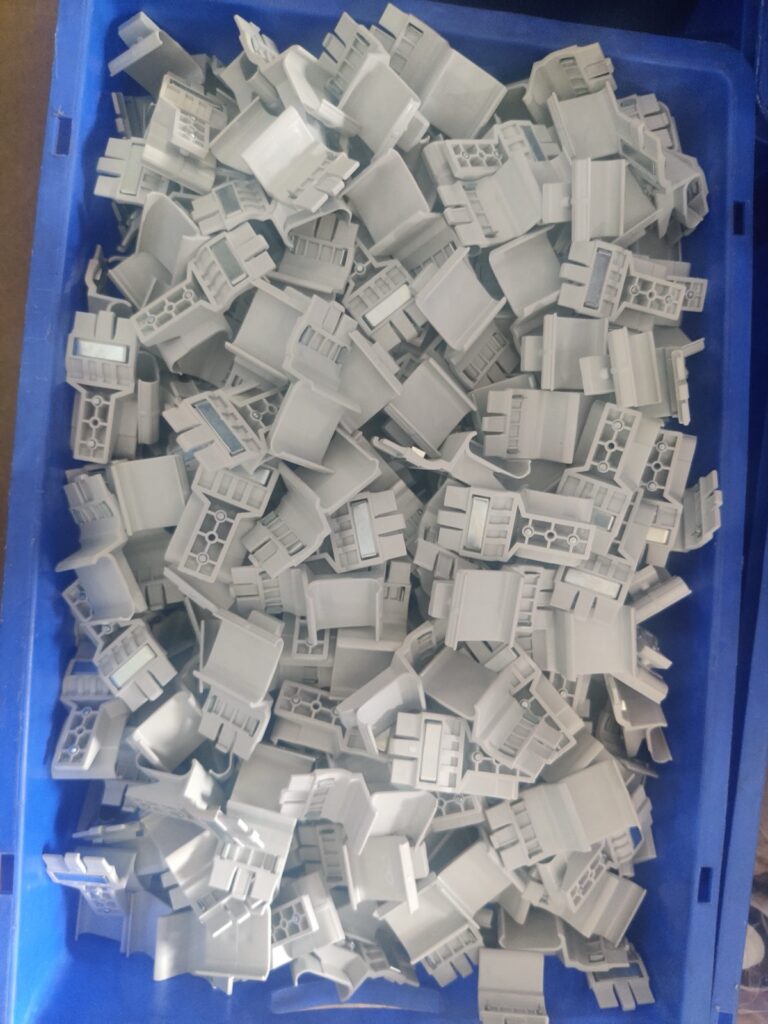
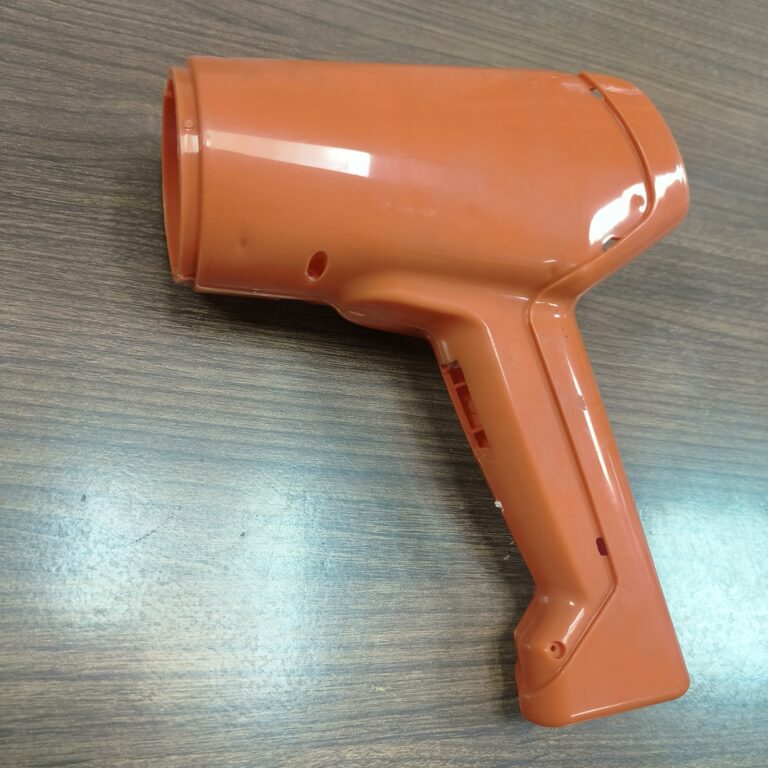
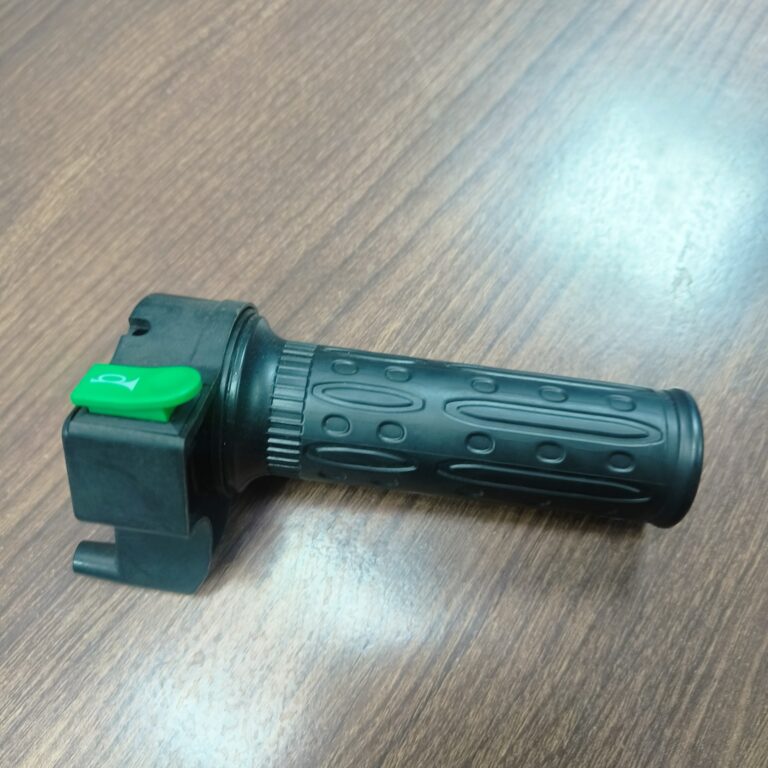
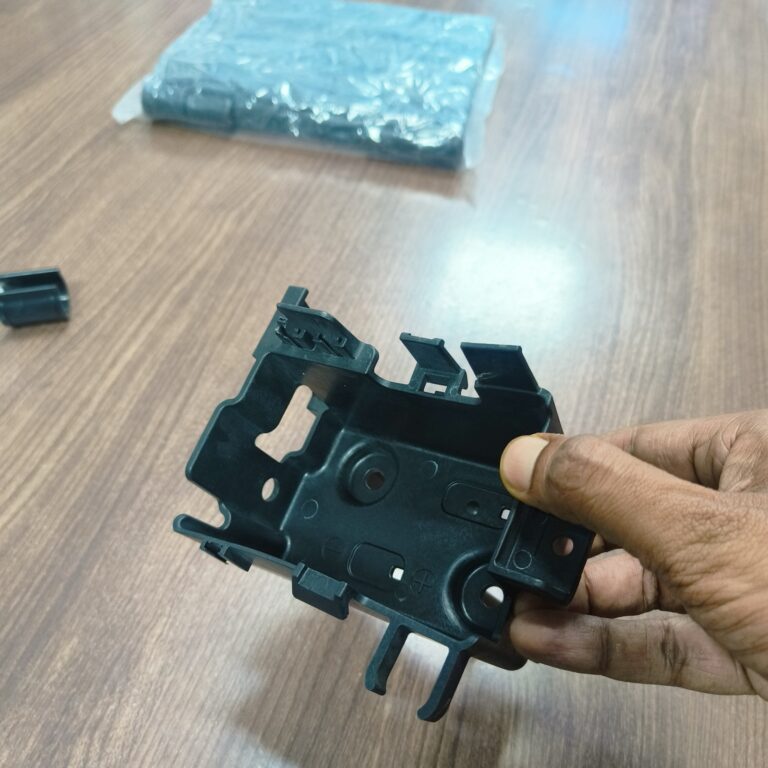
Heavy Fabrication
24000 MT/a
Materials
CS / MS, Alloy steel, Stainless Steel, etc.
Sheet Metal Fabrication
0.8 to 25 mm
Materials
Mild Steel, Stainless Steel, Aluminum, Brass, Copper, etc.


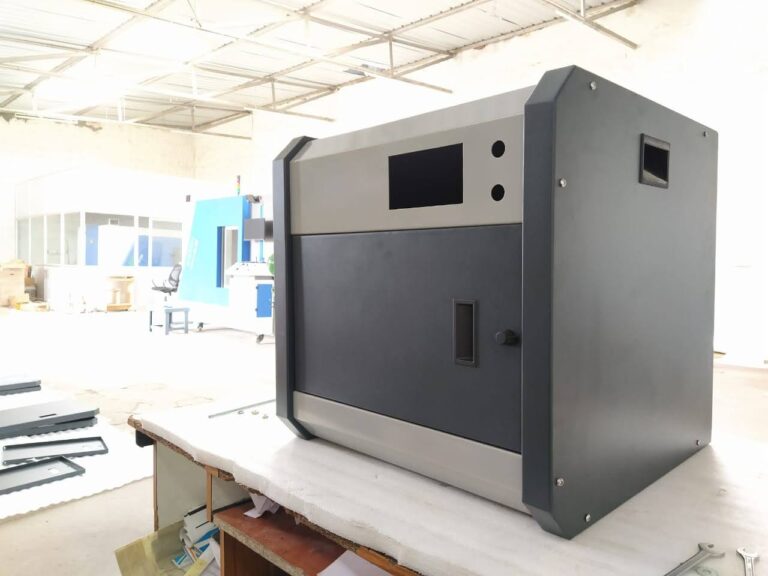


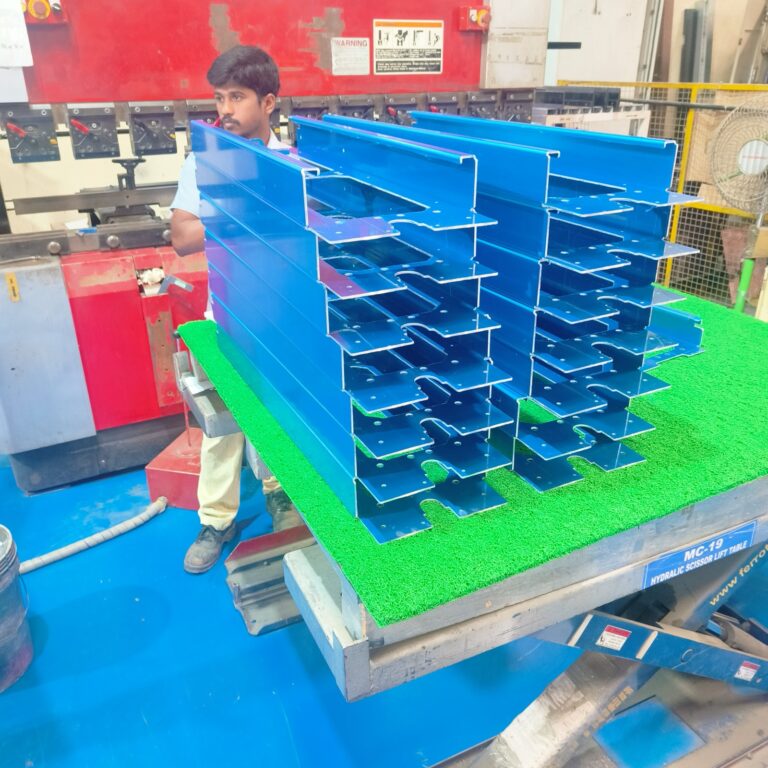
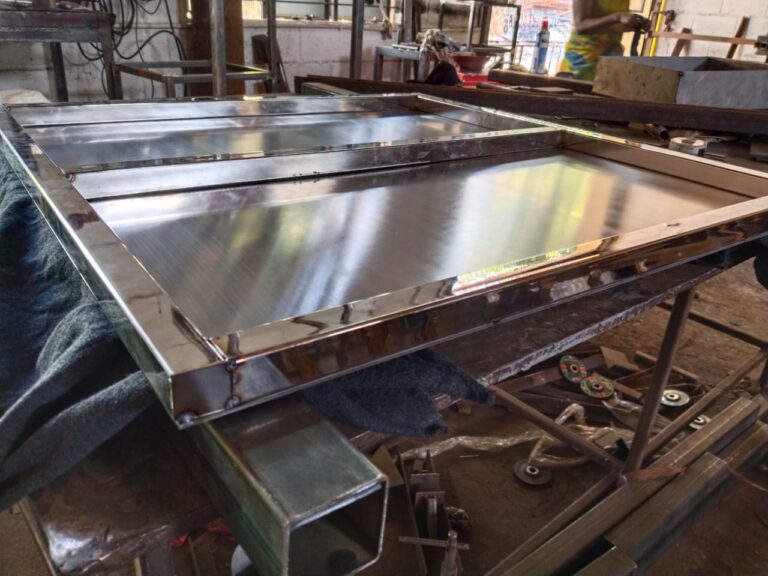
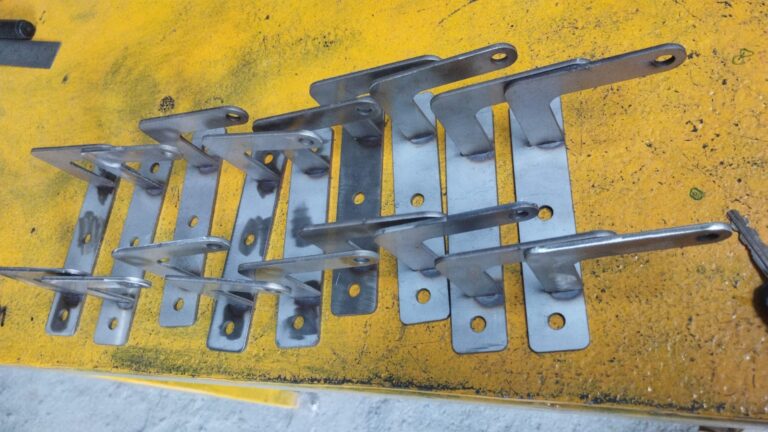
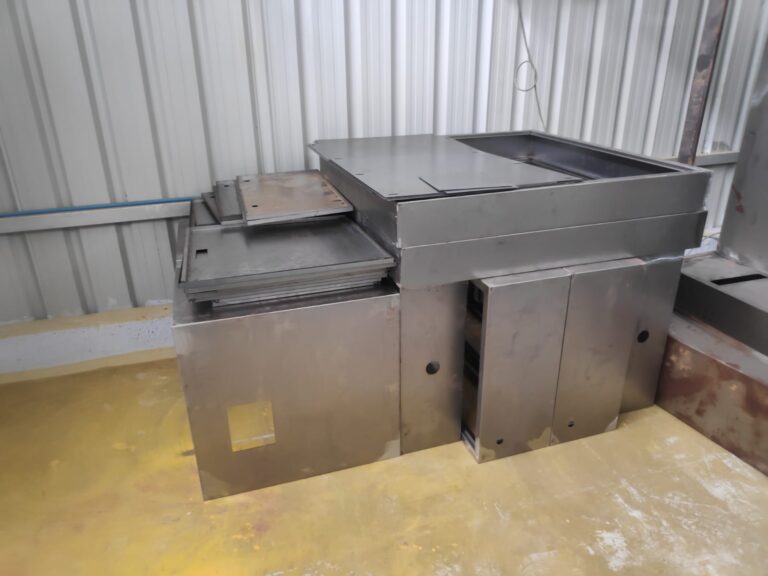
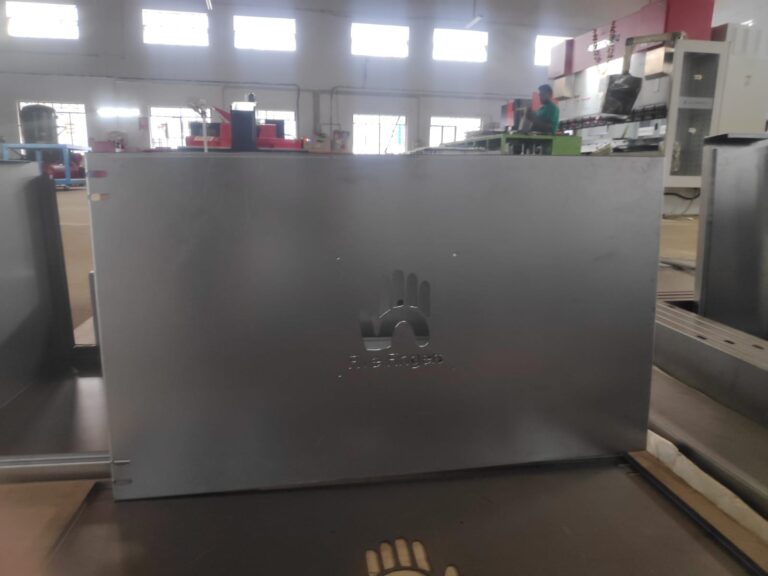
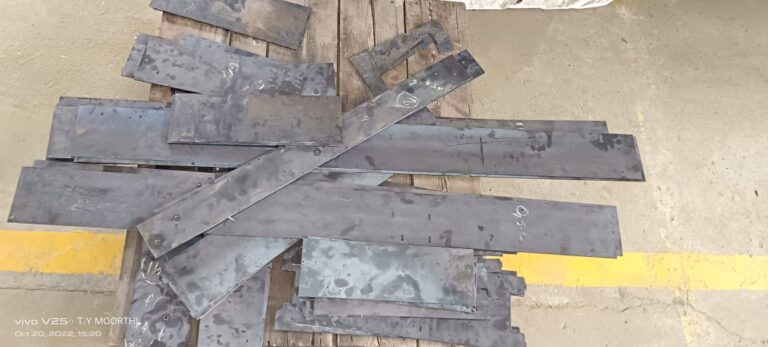
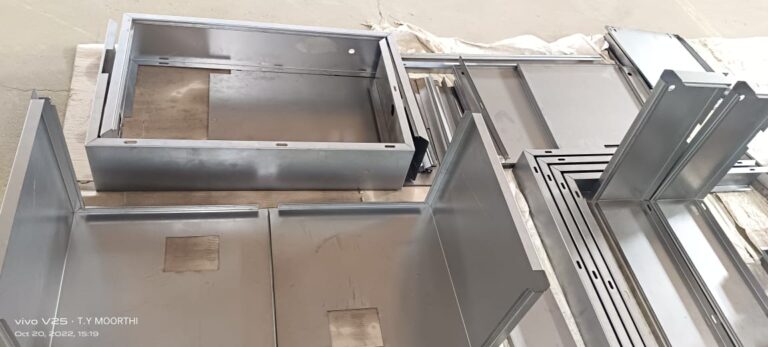
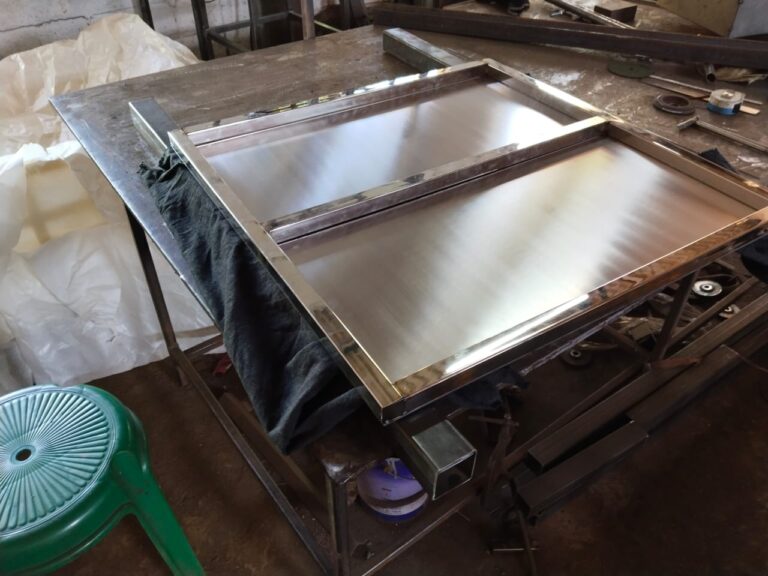
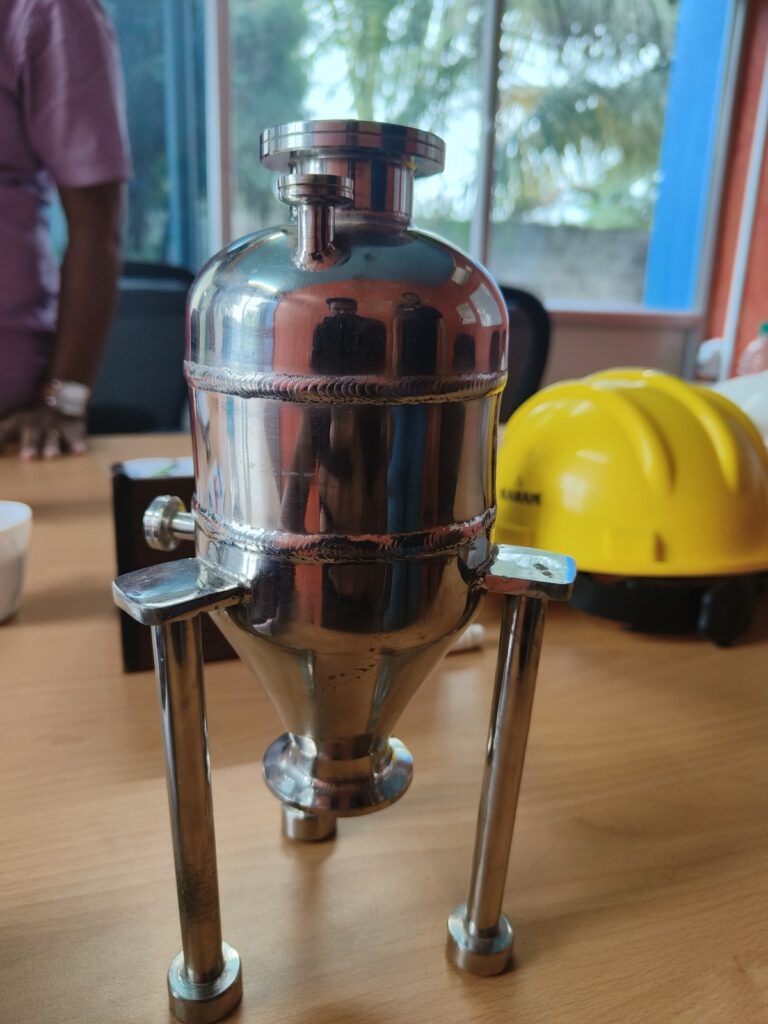
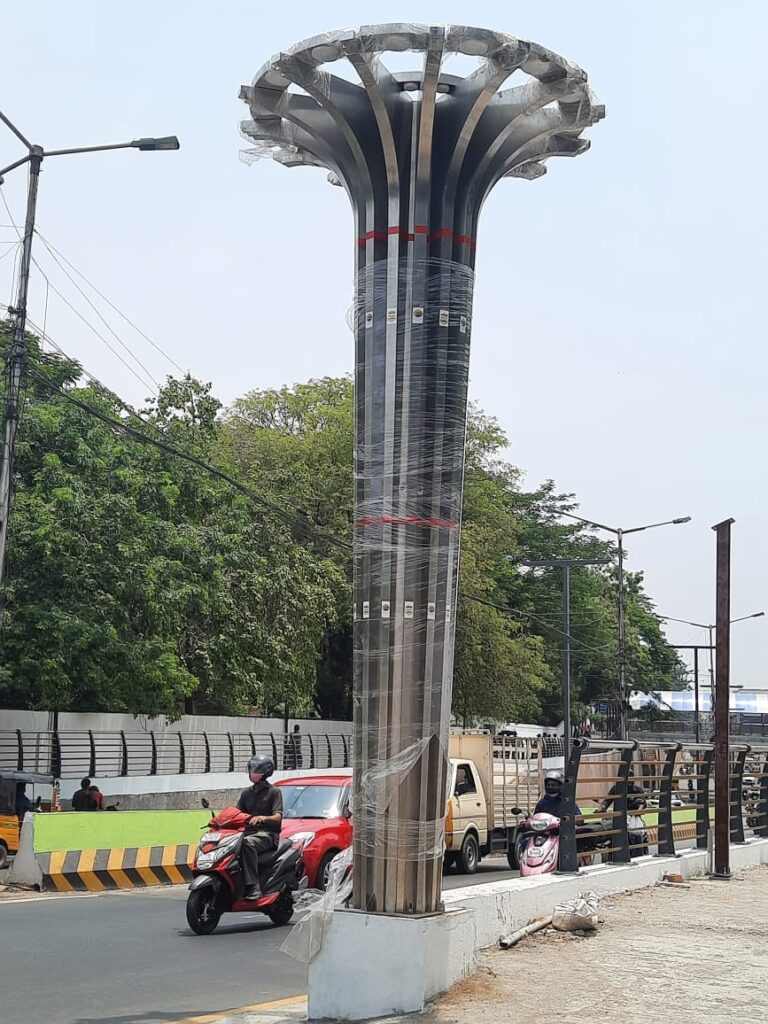
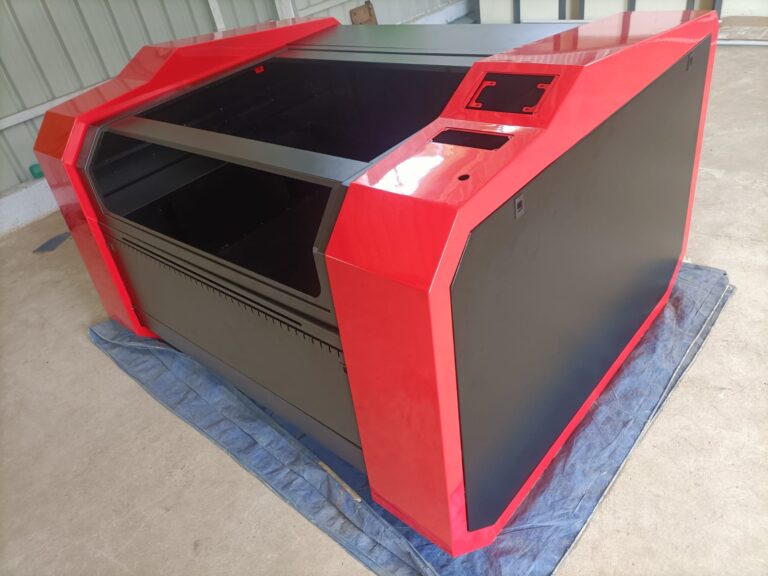
We'd love to Manufacture for you!
Submit the form below and our representative will be in touch shortly.
LOCATIONS
Registered Office
10-A, First Floor, V.V Complex, Prakash Nagar, Thiruverumbur, Trichy-620013, Tamil Nadu, India.
Operations Office
9/1, Poonthottam Nagar, Ramanandha Nagar, Saravanampatti, Coimbatore-641035, Tamil Nadu, India. ㅤ
Other Locations
- Bhilai
- Chennai
- USA
- Germany