Pharmaceutical Contract Manufacturing Services
Frigate offers advanced pharmaceutical contract manufacturing with precision and compliance. We specialize in API synthesis, formulation, and scalable production for diverse therapeutic needs.
Our Clients





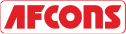

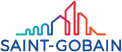


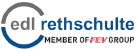

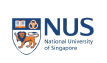
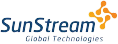

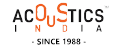




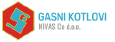
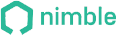
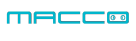












Advantages of Pharmaceutical Contract Manufacturing Services
Advanced Technology
Pharmaceutical contract manufacturers utilize state-of-the-art equipment and automation to ensure precise control over production processes and enhance overall product quality.
Faster Time-to-Market
Contract manufacturing accelerates production timelines by leveraging existing infrastructure and expertise, allowing faster entry into competitive pharmaceutical markets.
Risk Mitigation
Outsourcing manufacturing reduces the risk of regulatory non-compliance, quality control issues, and production delays, thanks to the expertise of specialized manufacturers.
Process Validation
Contract manufacturers conduct rigorous process validation to confirm that each step in the production process meets predefined quality and performance standards.
Custom Pharmaceutical Contract Manufacturing
Custom pharmaceutical contract manufacturing offers precision in production, ensuring compliance with global standards and regulatory requirements. With expertise in API synthesis, formulation, and packaging, pharmaceutical needs are met efficiently and accurately. Advanced technologies and specialized facilities streamline processes, enabling scalable production to handle varying volumes. The focus on quality control and process validation ensures consistent product quality while flexible solutions adapt to market demands. Tailored manufacturing services ensure that each phase, from development to final packaging, is optimized for cost and performance.

Get Your Quote Now
- Instant Quotation
- On-Time Delivery
- Affordable Cost
Our Pharmaceutical Contract Manufacturing Process






The process begins with detailed discussions to define product requirements, including formulation, dosage forms, and regulatory standards.
Experts develop the optimal formulation by selecting suitable ingredients, ensuring stability, bioavailability, and compliance with pharmacological standards.
A scalable manufacturing process is designed with considerations for equipment, batch size, and process optimization to ensure efficiency in large-scale production.
All processes and products undergo rigorous testing to meet regulatory guidelines (FDA, EMA, etc.), ensuring they are safe and market-ready.
The production phase involves strict quality control, where each batch is tested for consistency, potency, and purity according to predetermined specifications.
Final products are packaged according to industry standards, ensuring safe handling and distribution. They are prepared for shipment to clients or directly to markets.
Industries We Serve

The process begins with detailed discussions to define product requirements, including formulation, dosage forms, and regulatory standards.
Experts develop the optimal formulation by selecting suitable ingredients, ensuring stability, bioavailability, and compliance with pharmacological standards.
A scalable manufacturing process is designed with considerations for equipment, batch size, and process optimization to ensure efficiency in large-scale production.
All processes and products undergo rigorous testing to meet regulatory guidelines (FDA, EMA, etc.), ensuring they are safe and market-ready.
The production phase involves strict quality control, where each batch is tested for consistency, potency, and purity according to predetermined specifications.
Final products are packaged according to industry standards, ensuring safe handling and distribution. They are prepared for shipment to clients or directly to markets.
Our Pharmaceutical Contract Manufacturing Process
Mitigating Compliance Risks Through Rigorous Process Control
Pharmaceutical manufacturing requires adherence to complex global regulations, including FDA, EMA, and ICH standards. Frigate ensures compliance by implementing robust quality systems, documentation, and validation processes throughout production. Every stage, from raw material sourcing to final product packaging, is monitored to meet these stringent requirements. This structured approach minimizes the risk of non-compliance and ensures that all products are safe, effective, and ready for market approval, reducing the potential for regulatory delays or recalls.

Pharmaceutical Contract Manufacturing Materials
Pharmaceutical contract manufacturing requires precise control over production processes and quality. Each step must adhere to rigorous standards to ensure product consistency and safety.
APIs are biologically active substances that provide a therapeutic effect. These materials require precise synthesis, purification, and testing for potency, stability, and bioavailability. Techniques such as crystallization, chromatography, and drying ensure the highest purity levels.
Excipients serve as the vehicle for the API, aiding in the formulation's stability, release profile, and patient compliance. Common excipients include lactose (for tablet compression), hydroxypropyl methylcellulose (as a binder), and magnesium stearate (as a lubricant), all of which must meet stringent regulatory standards.
Solvents such as ethanol, methanol, and isopropyl alcohol are used in the extraction and purification. The selection of solvents is critical for achieving solubility without compromising API integrity, and they must comply with pharmacopeial standards for residual solvent limits.
Polymers, such as polyvinylpyrrolidone (PVP) and ethylcellulose, are used for tablet coatings or sustained-release formulations. Their molecular weight and solubility properties are carefully controlled to achieve desired release kinetics, whether for immediate or controlled release.
Coating agents, such as hydroxypropyl methylcellulose (HPMC) and ethylcellulose, protect the API from degradation due to environmental factors. Enteric coatings, for example, use polymers that are insoluble in acidic environments but dissolve in the intestines, ensuring targeted drug delivery.
Primary packaging materials, such as polyethylene (PE) and polypropylene (PP) for bottles or aluminum for blister packs, are chosen based on the drug's sensitivity to light, moisture, and air. These materials must also meet regulatory standards for leachability and interaction with the drug formulation.
Surfactants, like polysorbates and cetyl alcohol, enhance solubility and improve the bioavailability of poorly soluble drugs. They facilitate uniform mixing and prevent aggregation, ensuring consistent drug delivery and performance.
Enhancing Biopharmaceutical Manufacturing with Scalable Contract Solutions
Biopharmaceutical companies often encounter difficulties managing complex production processes and maintaining stringent quality controls. Pharmaceutical contract manufacturing offers an efficient solution by providing specialized expertise in developing and producing biological components. With Frigate’s advanced technologies, such as automated filling systems, real-time quality monitoring, and precision formulation, manufacturers can ensure optimal performance and compliance with FDA and EMA standards.
- Solid Progress
Our Manufacturing metrics
Frigate brings stability, control, and predictable performance to your sourcing operations through a structured multi-vendor system.
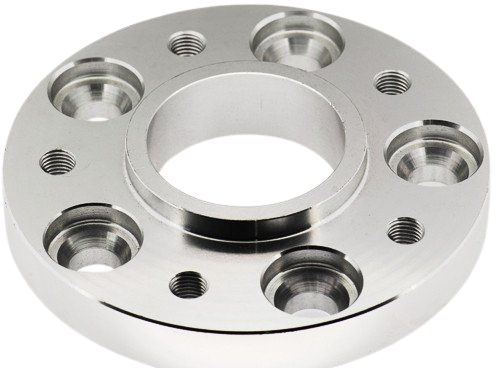
2.8X
Sourcing Cycle Speed
Frigate’s pre-qualified network shortens decision time between RFQ and PO placement.
94%
On-Time Delivery Rate
Structured planning windows and logistics-linked schedules improve project-level delivery reliability.
4X
Multi-Part Consolidation
We enable part family batching across suppliers to reduce fragmentation.
22%
Quality Rejection Rate
Multi-level quality checks and fixed inspection plans lower non-conformities.
30%
Procurement Costs
Optimized supplier negotiations and bulk order strategies reduce your overall sourcing expenses.
20%
Manual Processing Time
Automation of sourcing and supplier management significantly reduces time spent on manual tasks.
Scaling Production Without Compromising Quality or Performance
Scaling production while maintaining consistent quality can be a challenge in pharmaceutical manufacturing. Frigate addresses this by employing optimized processes and advanced technologies that ensure uniformity across all production scales. Detailed validation protocols and real-time monitoring systems are used to maintain product integrity and consistency. This approach ensures that both small and large batches meet the same high standards for quality, bioavailability, and stability, facilitating smooth transitions between different production volumes without compromising product performance.

Get Clarity with our Manufacturing Insights
- Real Impact
Words from Clients
See how global OEMs and sourcing heads describe their experience with our scalable execution.
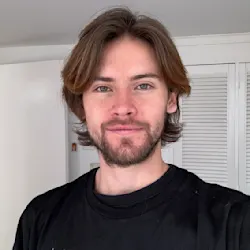
“Quick turnaround and solid quality.”
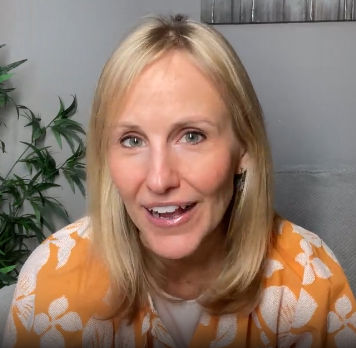
“The instant quote tool saved us time, and the parts were spot-on. Highly recommend Frigate!”
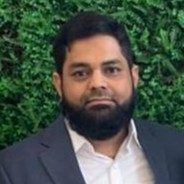
“I would strongly recommend Frigate to anyone who wants to do Rapid Prototyping, and take their ideas to manufacturing. One firm doing all kinds of Product Development!”
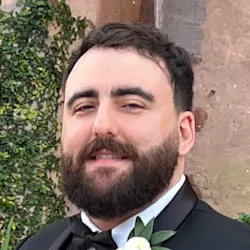
“Great service, fair price, and the parts worked perfectly in our assembly.”
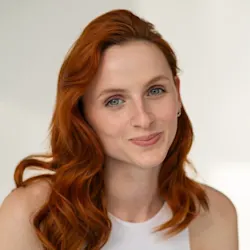
“Top-notch machining and fast shipping. Very satisfied with the results.”
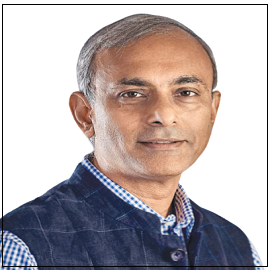
“The next disruption is happening in Prototyping & Manufacturing on-demand and Frigate is leading the way! I personally believe the Frigate's way of IIOT enabled cloud platform with Al.”
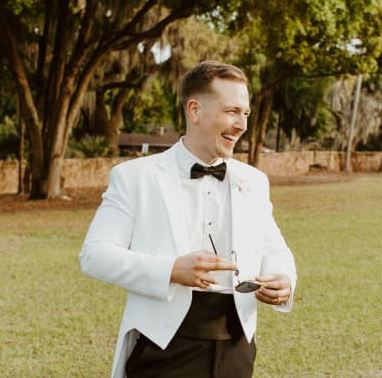
“Frigate delivered high-quality parts at a competitive price. The instant quote tool is a huge plus for us!”

“We appreciate the precision and quality of the machined components in the recent delivery—they meet our specifications perfectly and demonstrate Frigate’s capability for excellent workmanship.”
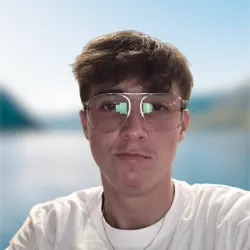
“Flawless execution from quote to delivery.”

“I am absolutely happy to work with supplier like Frigate who were quite proactive & result oriented . Frigate has high willingness team who has strong know how & their passion towards the products & process were absolutely thrilling.”
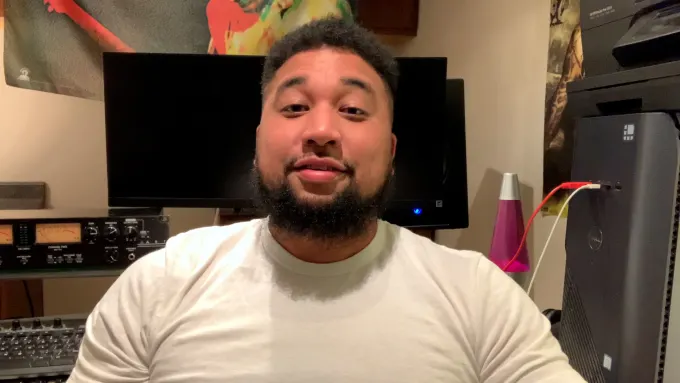
“The precision on these parts is impressive, and they arrived ahead of schedule. Frigate’s process really stands out!”
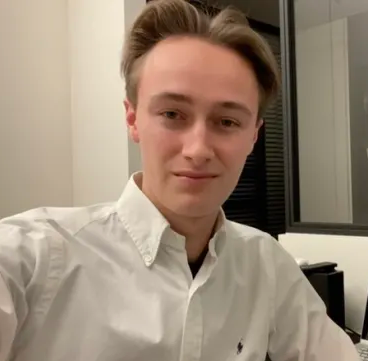
“Parts were exactly as spec’d, and the instant quote made budgeting a breeze.”
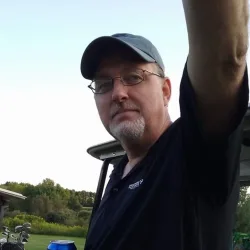
“Good value for the money.”
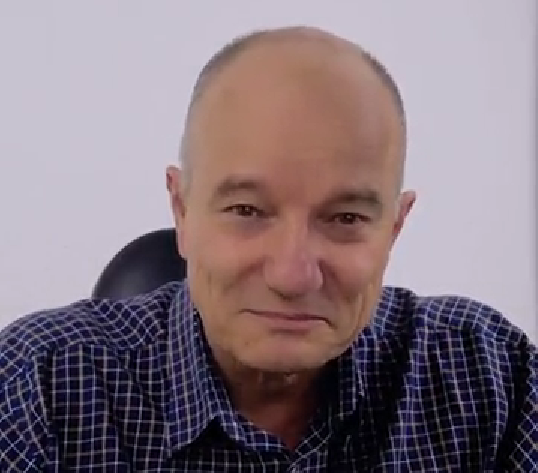
“The finish was perfect, and the team was easy to work with.”

“Working with Frigate has been great. Their proactive, results-driven approach and expertise shine through in every project. It's been a pleasure collaborating with them.”

"We are highly satisfied with the timely delivery and quality of the MIG Welding Cable from Frigate. Their attention to detail, secure packaging, and quick responsiveness stood out. We confidently recommend Frigate Engineering Services Pvt. Ltd. as a reliable manufacturing partner."
Having Doubts? Our FAQ
Check all our Frequently Asked Question
Frigate employs advanced formulation techniques, including particle size reduction, and uses stabilizers and excipients to optimize API solubility and bioavailability. Rigorous testing and validation at every production stage ensure the stability of APIs under various storage conditions.
Frigate strictly adheres to international guidelines such as GMP, ICH, and FDA standards. All processes, from raw material sourcing to final packaging, undergo comprehensive validation, ensuring regulatory compliance and quality assurance throughout production.
Frigate utilizes process optimization and equipment flexibility to ensure smooth scale-up. By conducting trial runs and in-depth process validation, Frigate minimizes batch variability and ensures consistent product quality across different production volumes.
Frigate implements stringent contamination control protocols, including cleanroom environments, air filtration systems, and sterilization procedures. Regular audits and monitoring are conducted to meet the highest standards of cleanliness and prevent cross-contamination.
Frigate uses advanced technologies like high-shear mixing, encapsulation, and automated filling systems to ensure precision in drug formulation. Real-time monitoring and data analytics ensure process control and minimize human error, improving overall manufacturing efficiency.
We'd love to Manufacture for you!
Submit the form below and our representative will be in touch shortly.
LOCATIONS
Global Sales Office
818, Preakness lane, Coppell, Texas, USA – 75019
Registered Office
10-A, First Floor, V.V Complex, Prakash Nagar, Thiruverumbur, Trichy-620013, Tamil Nadu, India.
Operations Office
9/1, Poonthottam Nagar, Ramanandha Nagar, Saravanampatti, Coimbatore-641035, Tamil Nadu, India. ㅤ
Other Locations
- Bhilai
- Chennai
- Texas, USA