Conventional Molding Casting Services
Frigate’s Conventional Molding Casting provides precise control over material flow and cooling. We utilize advanced techniques to achieve optimal dimensional accuracy and consistent metallurgical properties.
Our Clients





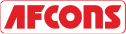

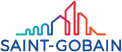


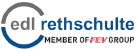

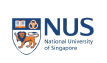
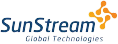

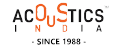




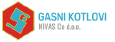
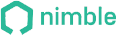
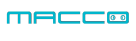












Advantages of Conventional Molding Casting Services
Efficient Heat Transfer
The process ensures uniform heat distribution during solidification, promoting consistent material properties and reducing internal stresses in cast components.
Reduced Material Waste
Conventional Molding Casting minimizes scrap material through efficient mold filling, resulting in a more sustainable and cost-effective manufacturing process.
Rapid Production Cycles
The technique allows for faster cycle times than other casting methods, improving overall production speed without compromising quality.
Scalability
It is highly scalable, allowing manufacturers to produce low—and high-volume components with consistent quality and performance.
Custom Conventional Molding Casting Services
Custom Conventional Molding Casting offers a precise and efficient solution for producing high-quality components. This method accommodates a wide range of metals and alloys, ensuring versatility in material selection. It delivers tight dimensional tolerances, reducing the need for secondary finishing processes. Complex geometries can be molded with high accuracy, offering design flexibility. The process is scalable and suitable for both small and large production runs.

Get Your Quote Now
- Instant Quotation
- On-Time Delivery
- Affordable Cost
Our Conventional Molding Casting Process






A precise pattern is made from metal, sand, or a composite material, designed to withstand the pouring temperature and ensure detailed feature replication.
The pattern is coated with a fine sand mixture, bonded with a binder, and compacted to form a rigid mold shell capable of withstanding thermal expansion.
The sand mold is dried in a controlled environment to remove moisture and hardened through heat treatment, ensuring structural integrity during pouring.
Metals are melted in a furnace, with temperature and alloy composition closely monitored to achieve uniform fluidity and minimize material defects during casting.
Molten metal is poured into the mold under controlled conditions, ensuring accurate filling of intricate cavities and preventing air entrapment or cold shuts.
After the metal solidifies, the mold is carefully broken apart, and the casting is extracted. Excess material, such as gates or runners, is machined for final finishing.
Post Processing Services in Conventional Molding Casting
Post-processing in conventional molding casting refines components for optimal quality, ensuring precise dimensions, improved surfaces, and defect correction. Key techniques like deburring, machining, and heat treatment are used across industries to enhance durability and performance.
Aerospace (Turbine Components, Structural Frames), Automotive (Engine Components, Transmission Parts)
Aerospace (Engine Housings, Structural Components), Automotive (Transmission Housings, Engine Blocks)
Aerospace (Aircraft Engine Parts), Medical (Surgical Instruments, Implantable Devices)
Aerospace (Landing Gear, Structural Components), Automotive (Brake Discs, Crankshafts)
Automotive (Chassis, Suspension Components), Electronics (Enclosures, Housings)
Aerospace (Wing Structures, Engine Parts), Automotive (Exhaust Systems, Chassis)
Aerospace (Airframe, Turbines), Automotive (Cylinders, Engine Blocks)
Aerospace (Aircraft Frames, Turbine Components), Automotive (Body Parts, Transmission Components)
Aerospace (Engine Casings, Brackets), Automotive (Gear Housings, Differential Cases)
Automotive (Small Engine Components, Bearings), Consumer Goods (Tools, Fasteners)
Methoding in Conventional Molding Casting
Automotive (Engine Blocks, Transmission Housings), Aerospace (Turbine Casings)
Aerospace (Turbine Blades, Engine Components), Industrial (Pump Casings, Valve Bodies)
Automotive (Chassis, Cylinder Heads), Aerospace (Landing Gear)
Automotive (Transmission Parts, Engine Blocks), Industrial (Valve Components)
Aerospace (Engine Casings, Turbine Blades), Automotive (Exhaust Systems)
Automotive (Body Parts, Brackets), Electronics (Connectors, Housings)
Automotive (Engine Parts, Suspension Components), Aerospace (Structural Parts)
Automotive (Transmission Housings, Crankshafts), Aerospace (Structural Frames)
Automotive (Engine Blocks, Body Panels), Aerospace (Fuel Tanks, Compressor Parts)
Automotive (Chassis Parts, Gearboxes), Aerospace (Aircraft Components)

Conventional Molding Casting Materials
Conventional Molding Casting requires precise control over material properties during production. This ensures optimal performance, dimensional accuracy, and structural integrity in the final components.
Aluminum alloys, such as 356 and 380, are favored for their excellent fluidity and low shrinkage. Their high thermal conductivity ensures rapid cooling, reducing cycle times. Commonly used in high-precision applications, they offer a balance of strength, corrosion resistance, and lightweight properties.
Zinc alloys, like Zamak 3 and Zamak 5, provide high tensile strength, superior surface finish, and excellent castability. These alloys are ideal for intricate parts requiring high dimensional accuracy and are often used in high-pressure die-casting for automotive and electronics industries.
Steel alloys, including carbon and low-alloy steels, offer high tensile strength, hardness, and wear resistance. Their robust mechanical properties make them suitable for heavy-duty industrial applications like gears, shafts, and structural components where high stress and fatigue resistance are essential.
Brass alloys, such as C260 and C360, are characterized by their good machinability, high strength, and corrosion resistance. With a wide range of mechanical properties, they are ideal for precision parts in plumbing, electrical connectors, and decorative applications requiring both durability and aesthetic appeal.
Gray and ductile iron alloys, such as ASTM A48 and ASTM A536, exhibit excellent castability and machinability. Gray iron offers good wear resistance for engine blocks, while ductile iron’s enhanced toughness makes it ideal for high-strength components like automotive suspension parts and heavy-duty machinery.
Magnesium alloys, such as AZ91D and ZK60, are lightweight and possess excellent strength-to-weight ratios. These alloys exhibit superior creep resistance and high thermal conductivity, making them suitable for aerospace and automotive applications that require lightweight, high-performance parts with tight tolerances.
Minimize Lead Times with Efficient Custom Mold Design
Custom molds for specific parts require careful design, material selection, and testing, which can lead to longer lead times. Frigate addresses this by utilizing advanced mold design techniques and simulation software to streamline the process. By optimizing mold geometry and material selection upfront, lead times are minimized without sacrificing precision. Frigate’s efficient testing protocols ensure molds are functional from the start, reducing the need for revisions and accelerating overall production timelines.

Compliance for Conventional Molding Casting Services
Frigate’s Conventional Molding Casting services adhere strictly to industry standards and regulations. We follow established procedures to meet all quality, safety, and environmental requirements. Our processes are regularly audited to ensure compliance with relevant certifications, ensuring high precision and reliability in every casting. By maintaining these certifications, Frigate ensures that each product meets stringent industry demands, from material composition to dimensional accuracy.
Quality management system certification ensuring consistent product quality and customer satisfaction.
Specification for ductile iron castings with precise mechanical properties and tolerances.
Restricting hazardous substances to meet the EU directive for electronic and electrical equipment.
Adhering to EU regulations on using chemicals in materials to protect human health and the environment.
Compliance with Occupational Safety and Health Administration standards for a safe working environment.
Ensuring all relevant materials meet FDA standards for safety in food-contact applications.
Tonnage/Capacity in Conventional Molding Casting
Tonnage and capacity in conventional molding casting are crucial factors in determining the efficiency and quality of the casting process. These parameters ensure that the right amount of force, pressure, and material flow is applied to achieve precise, high-quality components.
Automotive (Engine Blocks, Cylinder Heads), Aerospace (Turbine Components)
Automotive (Transmission Housings, Crankshafts), Aerospace (Aircraft Structural Parts)
Automotive (Wheel Hubs, Brake Discs), Industrial (Pump Casings, Valve Bodies)
Automotive (Interior Panels, Engine Parts), Consumer Goods (Appliance Components)
Automotive (Small Engine Components, Exhaust Systems), Electronics (Connectors, Housings)
Aerospace (Aircraft Frames, Landing Gear Components), Industrial (Industrial Pumps, Actuators)
Automotive (Chassis Parts, Body Panels), Aerospace (Fuel Tanks, Structural Frames)
Automotive (Engine Blocks, Transmission Parts), Electronics (Precision Housings, Connectors)
Automotive (Cylinder Heads, Engine Components), Aerospace (Turbine Casings, Compressor Blades)
Automotive (Suspension Parts, Gearboxes), Aerospace (Structural Brackets, Wing Components)
Dimensions in Conventional Molding Casting
Dimensions in conventional molding casting are essential for ensuring precise, high-quality components. Key parameters, from mold size to part tolerances, are tailored to meet industry standards for performance and durability.
Automotive (Chassis, Body Panels), Aerospace (Wing Structures, Engine Casings)
Aerospace (Turbine Blades, Structural Frames), Automotive (Engine Blocks, Housings)
Automotive (Brackets, Gear Housings), Industrial (Pumps, Valve Bodies)
Aerospace (Structural Components), Automotive (Transmission Parts, Cylinder Heads)
Automotive (Crankshafts, Wheel Hubs), Aerospace (Large Aircraft Components)
Automotive (Chassis, Engine Parts), Electronics (Housings, Connectors)
Aerospace (Compressor Blades, Structural Elements), Automotive (Exhaust Systems)
Automotive (Body Parts, Engine Blocks), Electronics (Connectors, Housings)
Aerospace (Landing Gear, Aircraft Components), Automotive (Engine Parts, Brackets)
Automotive (Suspension Parts, Engine Housings), Aerospace (Landing Gear, Brackets)

Tolerance for Conventional Molding Casting Services
Precision in part dimensions to meet exact specifications for fitting and function.
Consistent wall thickness to ensure strength and uniform material distribution.
Tolerance for surface roughness to meet specific functional or aesthetic requirements.
Ensures castings are within the required weight limits, balancing material cost and performance.
Ensures the casting is free from cracks, porosity, inclusions, and other defects affecting structural integrity.
Deviation in the flatness of a part's surface to ensure proper fit in assembly or functionality.
Ensures correct alignment between surfaces, critical for parts requiring tight fit tolerances.
Variation in roundness to ensure uniformity in cylindrical components, preventing misalignment.
Tolerance for the misalignment of cores in the mold, ensuring accuracy in part formation.
Precision in cavity depth, critical for maintaining part integrity and functionality.
Tolerance for hole diameters in cast parts, ensuring proper fit for bolts or other assembly components.
Ensuring concentric alignment of holes or features within cylindrical parts.
Tolerance for variation in thickness across the part to manage heat flow and reduce distortion.
Tolerance for angles between surfaces, crucial for parts with complex geometries or those needing precise alignment.
Tolerance for smooth, consistent radii or fillet transitions to avoid stress concentration.
Allowable porosity in castings to ensure strength and reliability while preventing structural issues.
Compensation for material shrinkage during cooling to maintain part dimensions.

Quality Testing Standards for Conventional Molding Casting Services
Verifies part dimensions with high precision using 3D coordinate measurements to ensure compliance with tight tolerances.
Measures and ensures uniform wall thickness throughout the casting to avoid weak spots and ensure material consistency.
Measures surface roughness to ensure it falls within the specified Ra value, critical for both aesthetic and functional requirements.
Detects internal and external defects like cracks, porosity, and inclusions that could affect structural integrity or functionality.
Measures the maximum amount of tensile stress a material can withstand before failure, ensuring the material meets the required strength standards.
Determines the material’s ability to elongate before breaking, providing insights into its ductility and suitability for specific applications.
Determines the hardness of the casting material, which is critical for evaluating wear resistance and performance under mechanical stress.
Examines microstructures at high magnification to identify material composition, grain structure, and any inclusions or impurities.
Assesses the material’s resistance to cyclic loading, simulating real-world stress conditions and helping to predict its lifespan.
Checks for concentric alignment of holes and other features, ensuring precision in rotational and assembly applications.
Ensures that mold cavities are free from defects and accurately reflect the intended design of the casting.
Measures residual internal stresses that could lead to distortion, cracking, or warping post-casting.
Analyzes the grain flow of the material to ensure that it aligns properly, enhancing strength and reducing the potential for defects.
Measures the casting's thermal conductivity to ensure it meets the requirements for heat dissipation in specific applications.
Tests the material's resistance to high-velocity impact, ensuring it can withstand shock loads without failure.
Ensures proper shrinkage compensation is implemented during casting and checks for dimensional accuracy post-cooling.
Detects surface and slightly subsurface cracks and defects in ferromagnetic castings, ensuring the integrity of critical parts.
Ensures castings can endure vibrations from machinery or transportation without structural failure.
Confirms the integrity of welded joints or heat-treated areas to ensure they meet mechanical and safety standards.
Inspection Techniques in Conventional Molding Casting
Value/Range - 0.1 mm - 5 mm precision for internal defects
Aerospace (Turbine Blades, Engine Casings), Automotive (Transmission Housings)
Value/Range - 5 mm to 2000 kHz frequency, 1-10 mm resolution
Aerospace (Structural Frames, Engine Components), Industrial (Pump Bodies)
Value/Range - Tolerance of ±0.05 mm for surface issues
Automotive (Body Panels, Engine Parts), Consumer Goods (Appliance Components)
Value/Range - 0.001 mm - 0.1 mm accuracy
Aerospace (Engine Parts), Automotive (Engine Blocks, Cylinders)
Value/Range - 0.1 mm - 5 mm crack size detection
Automotive (Chassis, Gear Housings), Aerospace (Aircraft Parts)
Frequency: 20 - 1000 kHz, depth penetration: 0.1 - 10 mm
Aerospace (Turbine Blades, Landing Gear), Industrial (Valve Bodies)
Value/Range -Magnetic field strength, 1-2 mm defect detection
Automotive (Suspension Components), Aerospace (Structural Parts)
Vickers Hardness: 100 - 800 HV, Rockwell Hardness: 20 - 70 HRB
Automotive (Crankshafts, Engine Parts), Industrial (Machinery Components)
Value/Range - ±0.1°C detection accuracy, resolution: 0.5 - 5 mm
Aerospace (Turbine Casings), Automotive (Exhaust Systems)
Value/Range - Pressure range: 0.1 - 10 bar, Leak rate: 0.1 - 2 ml/min a
Aerospace (Fuel Tanks), Automotive (Engine Blocks)


Industry Applications for Conventional Molding Casting
Powertrain, Suspension Systems, Exhaust Systems, Fuel Systems
Engine Components, Hydraulic Systems, Aircraft Landing Gear
Consumer Electronics, Power Distribution, Electrical Enclosures
Power Generation, Robotics, Industrial Automation
Military Equipment, Ballistic Protection, Heavy Machinery
Renewable Energy Systems, Oil & Gas Exploration, Electrical Grid Infrastructure
Diagnostic Tools, Implants, Medical Robotics
Household Goods, Personal Electronics, Fitness Equipment
Building Materials, Infrastructure, Heavy Equipment Parts
Offshore Equipment, Commercial Vessels, Marine Propulsion
Mining Equipment, Material Handling, Drilling Machinery
Locomotives, Passenger Cars, Rail Signaling Equipment
Chemical Processing, Oil Refining, Gas Transport
Communication Infrastructure, Network Equipment
Agricultural Machinery, Equipment for Crop Management
Optimizing Automotive Component Manufacturing with Conventional Molding Casting
Precision and material efficiency are key challenges in automotive component manufacturing. Conventional molding casting delivers robust solutions by producing complex parts with tight dimensional tolerances and high mechanical strength. Components such as engine blocks, transmission housings, and suspension parts benefit from this process, reducing post-casting machining needs. Advanced mold designs and precise pouring and cooling control ensure consistent part quality, making it a cost-effective solution for automotive applications where performance and reliability are crucial.






Industries We Serve
- Solid Progress
Our Manufacturing Metrics
Frigate brings stability, control, and predictable performance to your sourcing operations through a structured multi-vendor system.
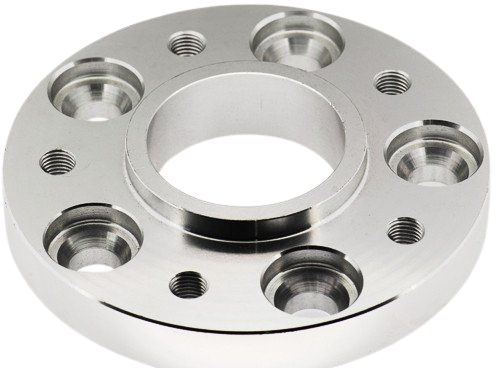
2.8X
Sourcing Cycle Speed
Frigate’s pre-qualified network shortens decision time between RFQ and PO placement.
94%
On-Time Delivery Rate
Structured planning windows and logistics-linked schedules improve project-level delivery reliability.
4X
Multi-Part Consolidation
We enable part family batching across suppliers to reduce fragmentation.
22%
Quality Rejection Rate
Multi-level quality checks and fixed inspection plans lower non-conformities.
30%
Procurement Costs
Optimized supplier negotiations and bulk order strategies reduce your overall sourcing expenses.
20%
Manual Processing Time
Automation of sourcing and supplier management significantly reduces time spent on manual tasks.
Reduce Material Waste and Lower Production Costs
Inaccurate mold designs or inefficient pouring techniques often result in increased material waste. To mitigate this, Frigate employs state-of-the-art design and simulation tools to optimize material flow and minimize waste during the casting process. Precise temperature control and pouring techniques are also implemented to ensure only the necessary material is used. This reduces scrap rates, enhances material efficiency, and ultimately lowers production costs, providing clients with more cost-effective and high-quality results.

Get Clarity with Our Manufacturing Insights
- Real Impact
Words from Clients
See how global OEMs and sourcing heads describe their experience with our scalable execution.
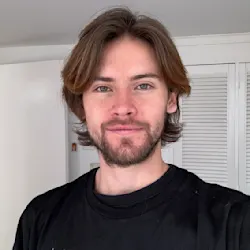
“Quick turnaround and solid quality.”
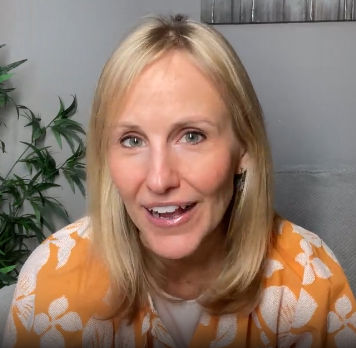
“The instant quote tool saved us time, and the parts were spot-on. Highly recommend Frigate!”
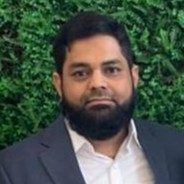
“I would strongly recommend Frigate to anyone who wants to do Rapid Prototyping, and take their ideas to manufacturing. One firm doing all kinds of Product Development!”
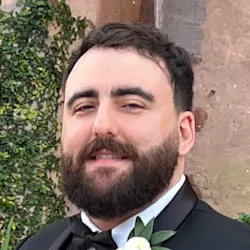
“Great service, fair price, and the parts worked perfectly in our assembly.”
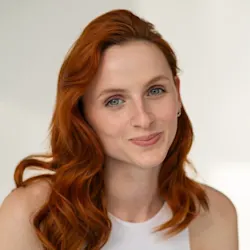
“Top-notch machining and fast shipping. Very satisfied with the results.”
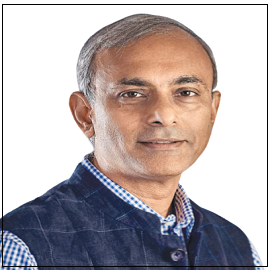
“The next disruption is happening in Prototyping & Manufacturing on-demand and Frigate is leading the way! I personally believe the Frigate's way of IIOT enabled cloud platform with Al.”
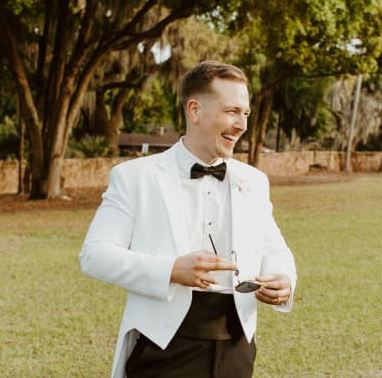
“Frigate delivered high-quality parts at a competitive price. The instant quote tool is a huge plus for us!”

“We appreciate the precision and quality of the machined components in the recent delivery—they meet our specifications perfectly and demonstrate Frigate’s capability for excellent workmanship.”
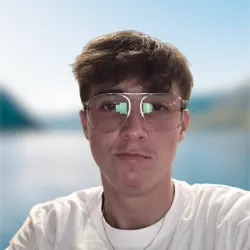
“Flawless execution from quote to delivery.”

“I am absolutely happy to work with supplier like Frigate who were quite proactive & result oriented . Frigate has high willingness team who has strong know how & their passion towards the products & process were absolutely thrilling.”
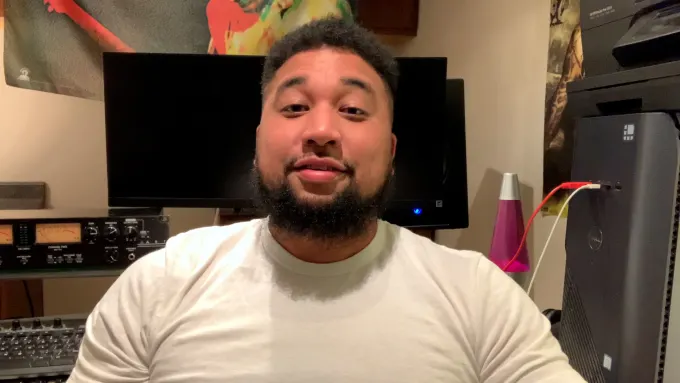
“The precision on these parts is impressive, and they arrived ahead of schedule. Frigate’s process really stands out!”
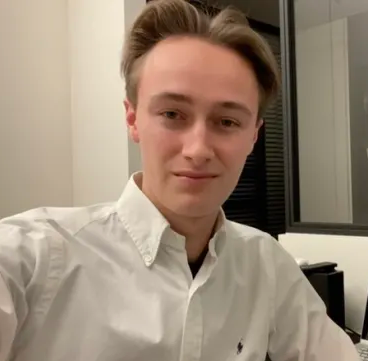
“Parts were exactly as spec’d, and the instant quote made budgeting a breeze.”
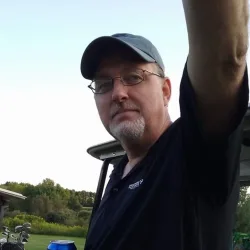
“Good value for the money.”
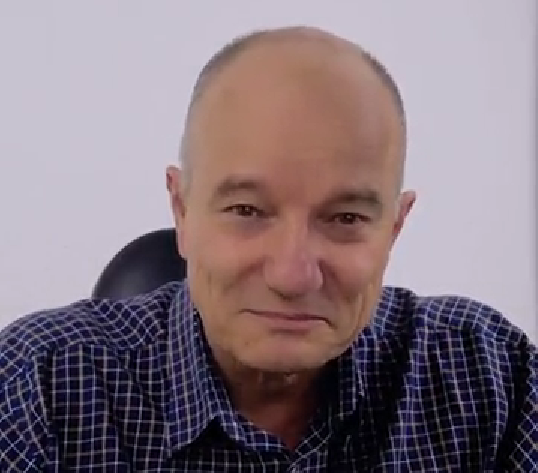
“The finish was perfect, and the team was easy to work with.”

“Working with Frigate has been great. Their proactive, results-driven approach and expertise shine through in every project. It's been a pleasure collaborating with them.”

"We are highly satisfied with the timely delivery and quality of the MIG Welding Cable from Frigate. Their attention to detail, secure packaging, and quick responsiveness stood out. We confidently recommend Frigate Engineering Services Pvt. Ltd. as a reliable manufacturing partner."
Having Doubts? Our FAQ
Check all our Frequently Asked Question
The gating system controls the flow rate and distribution of molten metal. Proper design minimizes turbulence, ensures uniform filling, and promotes consistent solidification, which reduces defects like cold shuts or gas entrapment.
Thermal expansion and contraction affect mold integrity and part dimensions. Proper mold material selection, pre-heating, and controlled cooling mitigate distortion and ensure part accuracy while avoiding cracking or misalignment.
Alloying elements affect hardness, tensile strength, corrosion resistance, and wear resistance. Careful control of these elements ensures the final product meets specific performance requirements, like high strength or improved machinability for complex applications.
Advanced coatings and surface treatments, such as ceramic or chrome plating, increase mold durability. Additionally, precise heat treatment of mold components prevents excessive wear and extends mold life, improving efficiency in high-volume production.
Mold permeability impacts gas venting and metal flow. Using materials with optimized permeability ensures proper venting, preventing air pockets or gas entrapment that can lead to defects like porosity, especially in intricate or thin-walled castings.
We'd love to Manufacture for you!
Submit the form below and our representative will be in touch shortly.
LOCATIONS
Registered Office
10-A, First Floor, V.V Complex, Prakash Nagar, Thiruverumbur, Trichy-620013, Tamil Nadu, India.
Operations Office
9/1, Poonthottam Nagar, Ramanandha Nagar, Saravanampatti, Coimbatore-641035, Tamil Nadu, India. ㅤ
Other Locations
- Bhilai
- Chennai
- USA
- Germany