Cold Chamber Casting Services
Frigate’s cold chamber casting delivers excellent corrosion resistance and durability for your finished products. We focus on using the best methods and materials to achieve the best results for your projects.
Our Clients





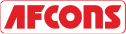

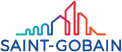


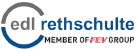

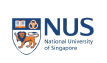
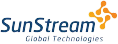

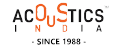




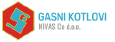
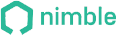
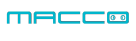












Advantages of Cold Chamber Casting Services
Rapid Production Rates
Cold chamber die casting has longer cycle times because metal is ladled manually. However, it still supports fast production and is ideal for large-scale manufacturing.
Strong and Durable Casting
You get parts with exceptional strength and durability. High pressure is used to force the metal into intricate molds, producing dense and microstructured castings.
Excellent Dimensional Accuracy
Get exceptional dimensional accuracy and stability with precise molds and a specialized production process. Parts maintain tight tolerances, making this method ideal for creating intricate shapes with high precision.
Thinner Walls
We use high pressure to produce complex parts with thin walls. This method ensures that the parts maintain strong, reliable properties even with intricate designs.
Frigate Cold Chamber Die Casting For Strong and Durable Parts
Frigate’s cold chamber die casting process is perfect for creating thicker metal castings. The process separates the melting pot from the injector, reducing corrosion.
You benefit from cost-efficient and effective methods that produce various shapes and elements. Parts made through this process are highly durable and long-lasting.

Get Your Quote Now
- Instant Quotation
- On-Time Delivery
- Affordable Cost
Our Cold Chamber Die Casting Process






The process begins by melting the metal in a separate furnace outside the casting machine. This setup differs from hot chamber casting, where the metal is melted within the machine.
Once molten, the metal is ladled into the cold chamber, a cylinder within the casting machine.
A plunger or piston forces the molten metal into the die (mold) at high pressure. This pressure ensures that the metal fills every cavity and detail of the die.
The metal solidifies quickly as it cools within the die, forming the desired shape. The cooling time can depend on the metal and the thickness of the part.
After metal solidification, the die opens, and the cast part is ejected. Any excess metal, like flash or sprues, is removed.
To achieve the final product, the cast part may undergo additional finishing processes. These can include trimming, machining, or surface treatments.
Post Processing Services in Cold Chamber Casting
Cold chamber casting produces high-strength, complex metal parts, but post-processing is essential to enhance quality, durability, and functionality. Various techniques refine surface finish, improve mechanical properties, and ensure corrosion resistance.
Automotive (Engine Blocks), Aerospace (Structural Parts)
Aerospace (Brackets), Automotive (Transmission Housings)
Consumer Electronics (Casings), Medical Devices (Implants)
Automotive (Gear Housings), Industrial Equipment (Pumps)
Aerospace (Airframe Parts), Marine (Corrosion Resistance)
Automotive (Brackets), Electronics (Heat Sinks)
Consumer Goods (Appliance Parts), Defense (Covers)
Electrical (Connectors), Automotive (Trim Parts)
Hydraulic Components (Pumps), Aerospace (Valves)
Industrial (Motor Housings), Defense (Weapon Components)
Methoding in Cold Chamber Casting
Automotive (Engine Blocks, Transmission Housings)
Aerospace (Structural Brackets, Gearbox Casings)
Industrial Equipment (Hydraulic Components, Pumps)
Electronics (Heat Sinks, Enclosures)
Consumer Goods (Power Tool Casings, Appliance Housings)
Defense (Weapon Components, Armor Fittings)
Renewable Energy (Wind Turbine Frames, Battery Enclosures)
Marine (Propeller Hubs, Corrosion-Resistant Parts)
Heavy Machinery (Compressor Housings, Bearings)
High-Precision Automotive & Aerospace Components

Cold Chamber Die Casting Materials
There are multiple materials that can be used for cold chamber casting services. The choice of casting materials depends upon specific properties and suitability.
Aluminum alloys are commonly used. They offer a good balance of strength, are lightweight, and are corrosion-resistant, making them ideal for automotive and aerospace applications.
Magnesium alloys are known for being lightweight and strong. They are used in industries where reducing weight is important. Electronics and automotive parts are examples of such industries.
Copper alloys provide excellent electrical conductivity and corrosion resistance. This makes them perfect for electrical components.
Brass alloys are durable and attractive. They are often used for decorative parts and applications where aesthetics matter.
Precision and Speed with Frigate's Cold Chamber Casting
Cold chamber casting services is perfect for aluminum and magnesium alloys. It produces durable parts with high precision. We excel in creating components with tight tolerances and thin walls. Our process uses high pressure and speed to fill the die completely. This results in parts with minimal porosity.

Compliance for Cold Chamber Casting Services
We adhere strictly to industry standards for Cold Chamber Casting, ensuring top-tier precision, safety, and environmental responsibility. Our processes are rigorously tested and monitored to meet regulatory compliance, from quality control to sustainable practices. We guarantee the highest performance and product reliability by aligning with international standards. Below are the specific certifications and compliance measures that support our technical excellence:
This certification confirms that Frigate Die Casting Services adheres to global standards for quality management systems. It ensures consistent product quality, continuous improvement, and customer satisfaction across all our Cold Chamber Casting processes.
A key standard for aluminum alloy die castings, ASTM B85 outlines the specifications for the material properties of aluminum alloys used in our Cold Chamber Casting. It ensures that the alloys meet the required mechanical, chemical, and dimensional properties, which are crucial for producing high-strength, reliable cast components.
Frigate complies with the European Union’s REACH (Registration, Evaluation, Authorization, and Restriction of Chemicals) regulation. This ensures that the materials used in our Cold Chamber Casting are safe for human health and the environment, reducing the risk of harmful substances in our products.
This directive restricts using certain hazardous substances in electrical and electronic equipment. By following RoHS standards, Frigate ensures that all castings used in electronic components are free from lead, mercury, cadmium, and other restricted materials, making our products safer and more sustainable.
This certification establishes a framework for effective environmental management systems. It demonstrates Frigate’s commitment to reducing the environmental impact of our Cold Chamber Casting processes by managing resources efficiently, reducing waste, and minimizing emissions.
The Occupational Safety and Health Administration (OSHA) standards are followed to maintain a safe working environment. These regulations focus on preventing workplace hazards and ensuring Frigate’s casting operations protect workers and the surrounding environment.
This standard is specific to the automotive and aerospace industries, focusing on die-casting specifications. By adhering to SAE J438, Frigate ensures that all cast components meet the performance standards required for high-stress, high-performance applications in these sectors.
Tonnage / Capacity in Cold Chamber Casting
Cold chamber die casting requires precise tonnage selection based on material properties, part complexity, projected area, and production volume to ensure part integrity and prevent defects. The right tonnage optimizes clamping force, reduces flash formation, extends die life, and enhances production efficiency.
Automotive (Engine Blocks, Transmission Housings)
Aerospace (Structural Brackets, Gearbox Housings)
Industrial Equipment (Pumps, Valves)
Heavy Machinery (Hydraulic Components, Motor Housings)
Defense (Weapon Components, Armor Fittings)
Consumer Electronics (Heat Sinks, Casings)
Medical Devices (Implants, Surgical Tools)
Marine (Propeller Hubs, Corrosion-Resistant Parts)
Heavy Machinery (Compressor Housings, Bearings)
High-Volume Automotive & Aerospace Production
Dimensions in Cold Chamber Casting
Cold chamber die casting involves precise dimensional control to achieve high-quality, defect-free parts. The key parameters include mold size, shot capacity, and wall thickness, all of which affect casting accuracy, mechanical properties, and overall performance.
Automotive (Transmission Housings, Engine Blocks)
Aerospace (Structural Brackets, Gearbox Casings)
Medical Devices (Implants, Surgical Tools)
Industrial Equipment (Hydraulic Components, Pumps)
Consumer Electronics (Heat Sinks, Casings)
Defense (Weapon Components, Armor Fittings)
Heavy Machinery (Compressor Housings, Bearings)
Marine (Propeller Hubs, Corrosion-Resistant Parts)
Electronics (Connectors, Enclosures)
High-Precision Automotive & Aerospace Components

Tolerance for Cold Chamber Casting Services
The pressure exerted on the material inside the mold cavity. Affects material flow and final part density.
Speed at which molten metal is injected into the mold cavity. Impacts fill efficiency and defect occurrence (e.g., air entrapment).
Duration for which molten metal is injected into the mold. Affects the final shape, surface quality, and material distribution.
The speed at which the molten metal cools and solidifies. Affects the hardness, strength, and grain structure of the casting.
The temperature of the mold during casting. Ensures that the metal solidifies at the correct rate, minimizing defects.
The maximum stress a material can withstand while being stretched or pulled before breaking. Essential for structural integrity in critical applications.
The stress at which a material begins to deform plastically. Important for maintaining the shape and durability of the casting under load.
The extent to which the casting material can stretch before breaking. A critical parameter for ensuring ductility and preventing brittle fractures.
Measures the hardness of the casting material. A higher value indicates greater resistance to indentation and wear.
The ability of the material to withstand repeated loading and unloading. Important for components subjected to cyclic stresses.
Measures the material's ability to conduct heat. Important for components exposed to high temperatures or thermal cycling.
The ability of the casting to retain its dimensions under temperature changes and mechanical stress. Crucial for tight-fitting parts.
Rate at which the casting expands or contracts with temperature changes. Critical for components exposed to varying thermal conditions.
The microstructure of the casting, which influences the mechanical properties, such as strength and toughness. Fine grains are typically preferred for high-strength applications.

Quality Testing Standards for Cold Chamber Casting Services
Measures the pressure exerted on the molten metal during injection to ensure optimal material flow and fill efficiency.
Monitors the speed at which molten metal is injected into the mold, ensuring it meets precise flow requirements.
Records the exact duration of molten metal injection to ensure the casting process is optimized for each part.
Measures the cooling rate of the metal within the mold to control the solidification process and minimize defects like shrinkage.
Tests the rate at which heat travels through the material, impacting the cooling and solidification process.
Determines the material's ductility by measuring its elongation before failure, which is vital for impact resistance and fatigue life.
Measures the material’s stiffness or resistance to deformation under tensile stress, important for load-bearing applications.
Determines the rate of crack propagation under cyclic loading, essential for evaluating the longevity of parts under repeated stress.
Measures changes in hardness over multiple loading cycles, indicating the material's response to fatigue or wear.
Analyzes the consistency of the microstructure, ensuring uniform grain distribution and phase formation for superior material properties.
Evaluates the material's resistance to sudden force or shock, crucial for components exposed to high impact stresses.
Identifies any remaining solvents or volatile materials in the casting, ensuring that the product is free of harmful residues.
Provides detailed hardness measurements across the surface and interior of the casting to evaluate uniformity and quality.
Assesses long-term dimensional stability under varying temperature and mechanical stress conditions, ensuring the casting retains its shape.
Tests the ability of the casting material to be welded without experiencing failure, such as cracking or porosity.
Detects subsurface defects, such as cracks or voids, in the casting material that could impact its structural integrity.
Measures the casting’s ability to conduct magnetic fields, important for parts used in electromagnetic applications.
Determines the porosity caused by trapped gases, ensuring castings have minimal internal voids or defects.
Provides high-resolution imaging of the internal and external dimensions of the casting to identify any inconsistencies or defects.
Inspection Techniques in Cold Chamber Casting
Value/Range - Defect detection up to 0.01 mm
Aerospace (Jet Engine Housings, Brackets)
Frequency - 0.5 - 15 MHz
Automotive (Transmission Housings, Wheels)
Crack depth - 0.1 - 2 mm
Medical (Implant Casings, Surgical Tools)
Crack detection - 0.01 - 3 mm
Defense (Weapon Components, Armor Parts)
Accuracy - ±0.01 mm
Electronics (Heat Sinks, Enclosures)
Tolerance: ±0.005 mm
Industrial Equipment (Hydraulic Pumps, Gear Housings)
Value/Range - 50 - 150 HB (Al), 80 - 200 HB (Brass)
Marine (Propeller Hubs, Corrosion-Resistant Parts)
Value/Range - 150 - 400 MPa (Al), 200 - 600 MPa (Brass)
Heavy Machinery (Compressor Casings, Bearings)


Industry Applications of Cold Chamber Casting
High strength-to-weight ratio, complex geometries
Heat resistance, lightweight, dimensional stability
High wear resistance, excellent mechanical properties
High thermal conductivity, EMI shielding
Biocompatibility, corrosion resistance, precision casting
High impact resistance, lightweight, long-term durability
Saltwater resistance, non-magnetic properties
High fatigue resistance, conductivity, long-term reliability
Structural strength, vibration damping
Precision engineering, dimensional stability, high repeatability
Frigate Cold Chamber Casting for the Aerospace Industry
Frigate provides specialized cold chamber casting services tailored to the aerospace industry. Our process delivers high-precision components that adhere to stringent aerospace standards, using advanced technology to achieve tight tolerances and superior quality.
Cold chamber casting services is ideal for producing durable, high-strength parts from aluminum, magnesium, and other non-ferrous alloys. These materials offer the required strength-to-weight ratio essential for aerospace applications. Our process ensures excellent surface finishes and precise dimensions, making it perfect for aircraft engine components, housings, and structural elements.









Industries We Serve
- Solid Progress
Our Manufacturing metrics
Frigate brings stability, control, and predictable performance to your sourcing operations through a structured multi-vendor system.
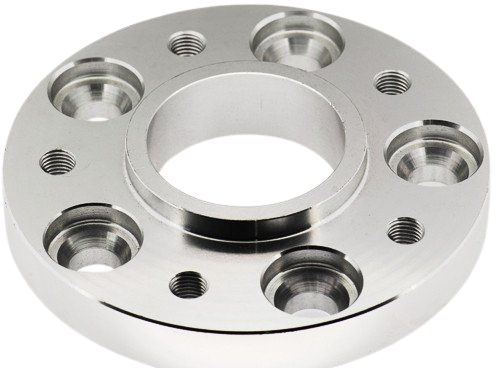
2.8X
Sourcing Cycle Speed
Frigate’s pre-qualified network shortens decision time between RFQ and PO placement.
94%
On-Time Delivery Rate
Structured planning windows and logistics-linked schedules improve project-level delivery reliability.
4X
Multi-Part Consolidation
We enable part family batching across suppliers to reduce fragmentation.
22%
Quality Rejection Rate
Multi-level quality checks and fixed inspection plans lower non-conformities.
30%
Procurement Costs
Optimized supplier negotiations and bulk order strategies reduce your overall sourcing expenses.
20%
Manual Processing Time
Automation of sourcing and supplier management significantly reduces time spent on manual tasks.
Frigate offers customized casting solutions to optimize your project and save on costs. Our responsive team ensures timely support and efficient service.
We use top-notch testing instruments like chemical analyzers and spectrometers for precise quality control.
From prototyping to mass production, you can cast components using all types of metal alloys.
Our skilled engineers provide innovative solutions and high-quality production.
Along with cold chamber die casting you can also contact us for sand casting, lost foam casting, shell mold casting, and lost wax investment casting.

Get Clarity with our Manufacturing Insights
- Real Impact
Words from Clients
See how global OEMs and sourcing heads describe their experience with our scalable execution.
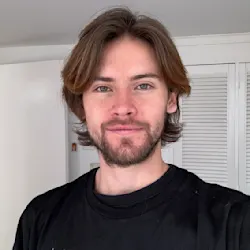
“Quick turnaround and solid quality.”
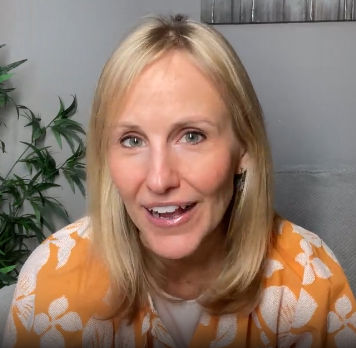
“The instant quote tool saved us time, and the parts were spot-on. Highly recommend Frigate!”
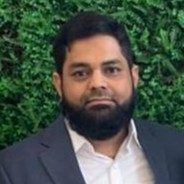
“I would strongly recommend Frigate to anyone who wants to do Rapid Prototyping, and take their ideas to manufacturing. One firm doing all kinds of Product Development!”
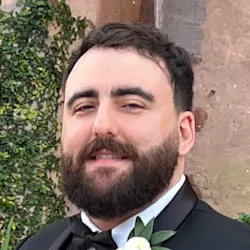
“Great service, fair price, and the parts worked perfectly in our assembly.”
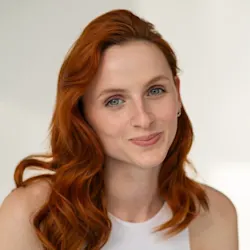
“Top-notch machining and fast shipping. Very satisfied with the results.”
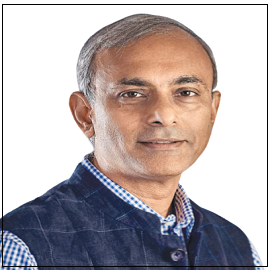
“The next disruption is happening in Prototyping & Manufacturing on-demand and Frigate is leading the way! I personally believe the Frigate's way of IIOT enabled cloud platform with Al.”
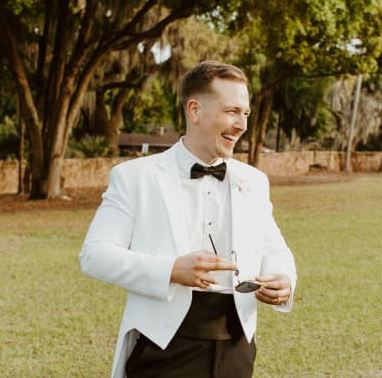
“Frigate delivered high-quality parts at a competitive price. The instant quote tool is a huge plus for us!”

“We appreciate the precision and quality of the machined components in the recent delivery—they meet our specifications perfectly and demonstrate Frigate’s capability for excellent workmanship.”
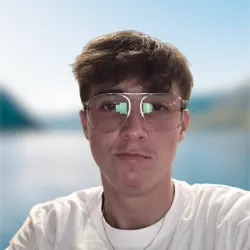
“Flawless execution from quote to delivery.”

“I am absolutely happy to work with supplier like Frigate who were quite proactive & result oriented . Frigate has high willingness team who has strong know how & their passion towards the products & process were absolutely thrilling.”
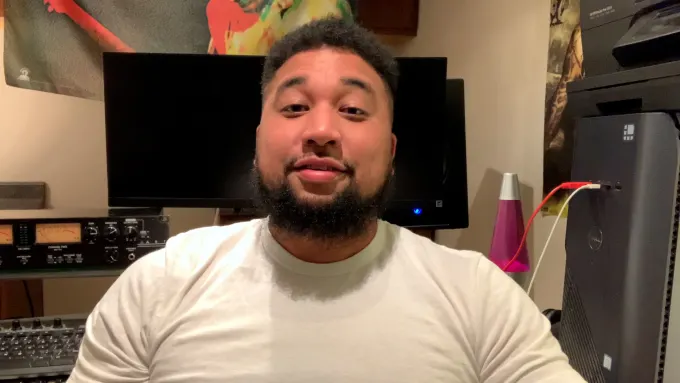
“The precision on these parts is impressive, and they arrived ahead of schedule. Frigate’s process really stands out!”
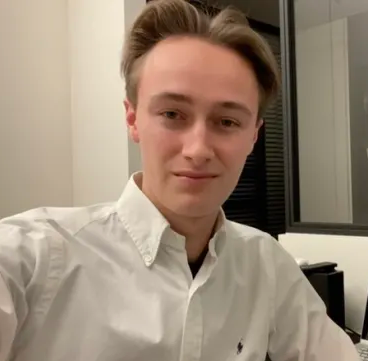
“Parts were exactly as spec’d, and the instant quote made budgeting a breeze.”
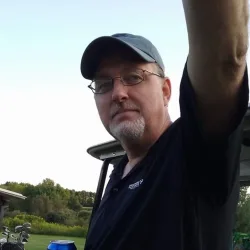
“Good value for the money.”
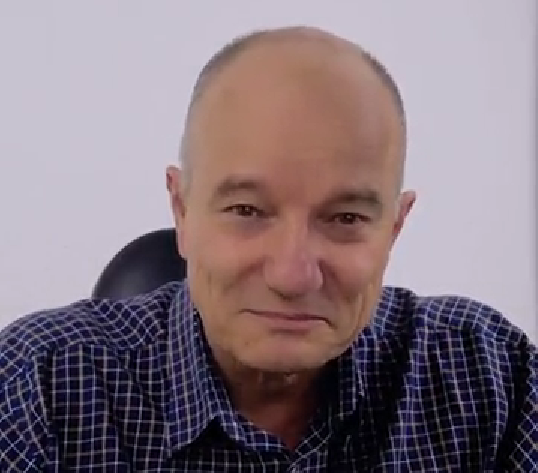
“The finish was perfect, and the team was easy to work with.”

“Working with Frigate has been great. Their proactive, results-driven approach and expertise shine through in every project. It's been a pleasure collaborating with them.”

"We are highly satisfied with the timely delivery and quality of the MIG Welding Cable from Frigate. Their attention to detail, secure packaging, and quick responsiveness stood out. We confidently recommend Frigate Engineering Services Pvt. Ltd. as a reliable manufacturing partner."
Having Doubts? Our FAQ
Check all our Frequently Asked Question
The cold chamber is a part of the die-casting machine where molten metal is injected into the mold. Unlike hot chamber casting, where the injection unit is molten, the cold chamber system melts the metal in a separate furnace. This setup helps when using metals with high melting points, like aluminum.
In cold chamber casting, the molten metal is first ladled from the furnace into the injection chamber. Then, a plunger pushes the metal into the mold at high pressure. This quick injection helps create precise shapes and improves surface quality, which is crucial for complex designs.
Cooling time is the period the metal needs to solidify in the mold. The cooling time can affect the final part's quality and dimensions in cold chamber casting. A cooling time that is too short may lead to defects like warping, while a cooling time that is too long can reduce production efficiency. Finding the right balance is key.
Cold chamber casting is ideal for high-temperature aluminum, magnesium, and copper alloys. These metals need the cold chamber process because their melting points are too high for hot chamber casting, ensuring quality parts without damaging the machine.
The cycle time in cold chamber casting is usually longer than in hot chamber casting. This is because the metal must be ladled into the chamber before injection. However, the precise nature of cold chamber casting can lead to fewer defects, making the overall process more efficient for certain applications.
We'd love to Manufacture for you!
Submit the form below and our representative will be in touch shortly.
LOCATIONS
Global Sales Office
818, Preakness lane, Coppell, Texas, USA – 75019
Registered Office
10-A, First Floor, V.V Complex, Prakash Nagar, Thiruverumbur, Trichy-620013, Tamil Nadu, India.
Operations Office
9/1, Poonthottam Nagar, Ramanandha Nagar, Saravanampatti, Coimbatore-641035, Tamil Nadu, India. ㅤ
Other Locations
- Bhilai
- Chennai
- Texas, USA