Cable & Wiring Harness Assembly Services
Frigate excels in precision cable and wiring harness assembly for diverse industries. We utilize advanced signal integrity techniques and custom connectors for optimized electrical performance.
Our Clients





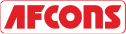

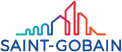


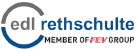

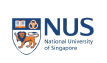
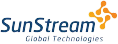

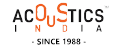




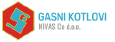
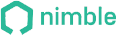
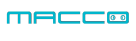












Advantages of Cable & Wiring Harness Assembly Services
Improved Signal Integrity
Cable and wiring harness assemblies are designed to minimize electromagnetic interference, ensuring stable and reliable signal transmission across systems.
Customizable Designs
Harnesses can be tailored to specific configurations, accommodating unique space constraints and electrical requirements for various industrial applications.
Enhanced Durability
High-quality materials and precise construction techniques increase the lifespan of wiring harnesses, making them resistant to wear, corrosion, and environmental factors.
Streamlined Manufacturing Process
Pre-assembled cable and wiring harnesses reduce assembly time, improving production efficiency and ensuring consistent quality and performance in final products.
Custom Cable & Wiring Harness Assembly
Custom cable and wiring harness assemblies offer tailored solutions for precise, reliable connections. They are designed to meet specific electrical and spatial requirements and enhance performance across various applications. With high-quality materials and expert engineering, these assemblies provide durability and protection against wear, corrosion, and interference. Custom designs streamline assembly processes, reduce production time, and ensure consistent quality. They are ideal for complex wiring systems and are built to handle diverse environmental conditions while maintaining optimal functionality.

Get Your Quote Now
- Instant Quotation
- On-Time Delivery
- Affordable Cost
Our Cable & Wiring Harness Assembly Process






The assembly process begins with a detailed design based on the specific electrical requirements, space constraints, and environmental factors.
Appropriate wires are chosen based on voltage, current capacity, insulation type, and flexibility to ensure optimal performance.
Wires are accurately cut to length and stripped of insulation at both ends, ensuring proper connections without damaging the wire.
Terminals, connectors, and pins are securely attached to the wires using crimping or soldering techniques, ensuring strong electrical connections.
The wires are carefully routed and arranged in harnesses, with proper spacing and organization to prevent interference and damage.
Each assembly is thoroughly tested for electrical continuity, signal integrity, and mechanical strength to meet stringent quality standards.
Ensuring Long-Term Reliability and Durability in Wiring Harnesses
Wiring harnesses must withstand harsh environmental conditions such as moisture, high temperatures, and mechanical stress to ensure long-term performance. Frigate addresses this using high-quality, durable materials and specialized coatings for added protection. Rigorous testing procedures, including electrical continuity, insulation resistance, and mechanical strength tests, are conducted on each harness to validate its reliability. These measures ensure that the assembly performs consistently, reducing the risk of failure and enhancing the lifespan of critical systems.

Our Cable & Wiring Harness Assembly Process
At Frigate, we ensure optimal machinery performance through precise engineering. Our components are designed to withstand high stress, wear, and harsh conditions.
The assembly process begins with a detailed design based on the specific electrical requirements, space constraints, and environmental factors.
Appropriate wires are chosen based on voltage, current capacity, insulation type, and flexibility to ensure optimal performance.
Wires are accurately cut to length and stripped of insulation at both ends, ensuring proper connections without damaging the wire.
Terminals, connectors, and pins are securely attached to the wires using crimping or soldering techniques, ensuring strong electrical connections.
The wires are carefully routed and arranged in harnesses, with proper spacing and organization to prevent interference and damage.
Each assembly is thoroughly tested for electrical continuity, signal integrity, and mechanical strength to meet stringent quality standards.
Industries We Serve
Advanced Cable & Wiring Harness Solutions for Automotive Applications
Automotive systems rely on high-performance electrical connections to maintain functionality and safety. Poorly designed wiring can lead to signal degradation, interference, or electrical failures, compromising system reliability. Cable and wiring harness assemblies address these concerns by providing a robust, organized, and efficient method of delivering power and data across various vehicle components. Engineered to withstand the demanding automotive environment—high temperatures, vibrations, and moisture—these assemblies ensure reliable performance in critical systems like engine control units, lighting, infotainment, and sensors. The precise design and selection of materials ensure optimal electrical performance, enhancing overall vehicle durability and safety.






- Solid Progress
Our Manufacturing Metrics
Frigate brings stability, control, and predictable performance to your sourcing operations through a structured multi-vendor system.
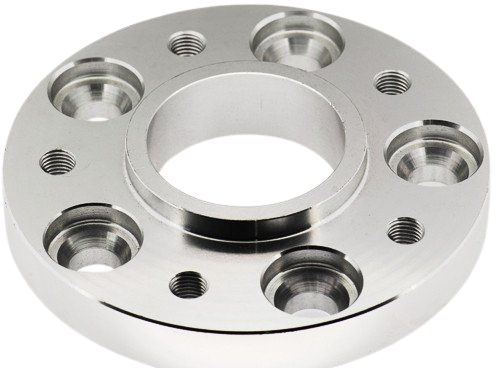
2.8X
Sourcing Cycle Speed
Frigate’s pre-qualified network shortens decision time between RFQ and PO placement.
94%
On-Time Delivery Rate
Structured planning windows and logistics-linked schedules improve project-level delivery reliability.
4X
Multi-Part Consolidation
We enable part family batching across suppliers to reduce fragmentation.
22%
Quality Rejection Rate
Multi-level quality checks and fixed inspection plans lower non-conformities.
30%
Procurement Costs
Optimized supplier negotiations and bulk order strategies reduce your overall sourcing expenses.
20%
Manual Processing Time
Automation of sourcing and supplier management significantly reduces time spent on manual tasks.
Optimized Solutions for Complex Cable & Wiring Harness Designs
Cable and wiring harness assemblies require precise designs to meet specific operational, electrical, and spatial needs. This includes accommodating varying voltage, temperature extremes, and space limitations. At Frigate, the design process focuses on selecting the appropriate materials, connectors, and wire types that align with the requirements. Advanced CAD tools and in-depth engineering analysis create efficient, space-optimized solutions, ensuring the final assembly integrates seamlessly into the intended application.

Get Clarity with Our Manufacturing Insights
- Real Impact
Words from Clients
See how global OEMs and sourcing heads describe their experience with our scalable execution.
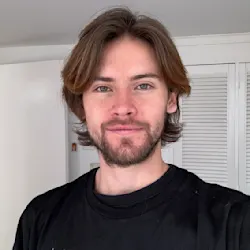
“Quick turnaround and solid quality.”
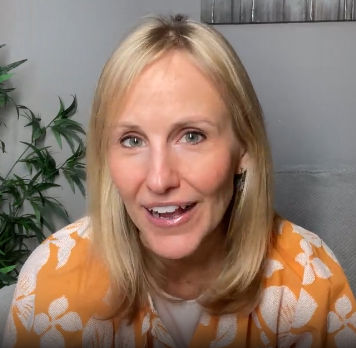
“The instant quote tool saved us time, and the parts were spot-on. Highly recommend Frigate!”
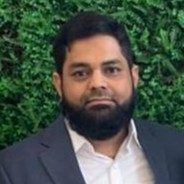
“I would strongly recommend Frigate to anyone who wants to do Rapid Prototyping, and take their ideas to manufacturing. One firm doing all kinds of Product Development!”
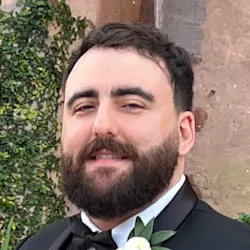
“Great service, fair price, and the parts worked perfectly in our assembly.”
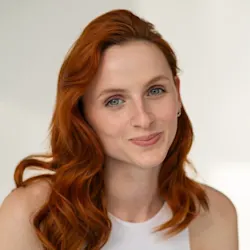
“Top-notch machining and fast shipping. Very satisfied with the results.”
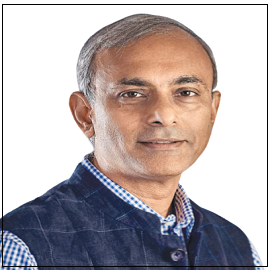
“The next disruption is happening in Prototyping & Manufacturing on-demand and Frigate is leading the way! I personally believe the Frigate's way of IIOT enabled cloud platform with Al.”
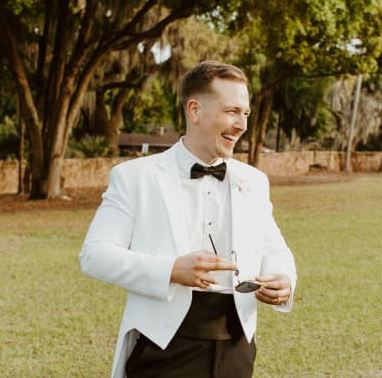
“Frigate delivered high-quality parts at a competitive price. The instant quote tool is a huge plus for us!”

“We appreciate the precision and quality of the machined components in the recent delivery—they meet our specifications perfectly and demonstrate Frigate’s capability for excellent workmanship.”
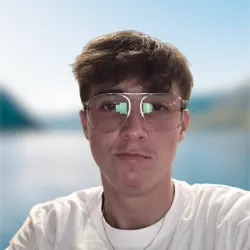
“Flawless execution from quote to delivery.”

“I am absolutely happy to work with supplier like Frigate who were quite proactive & result oriented . Frigate has high willingness team who has strong know how & their passion towards the products & process were absolutely thrilling.”
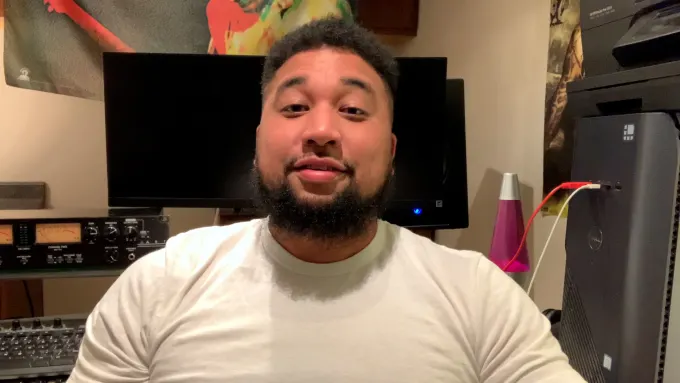
“The precision on these parts is impressive, and they arrived ahead of schedule. Frigate’s process really stands out!”
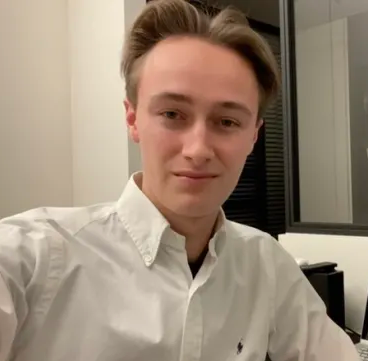
“Parts were exactly as spec’d, and the instant quote made budgeting a breeze.”
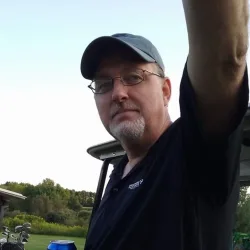
“Good value for the money.”
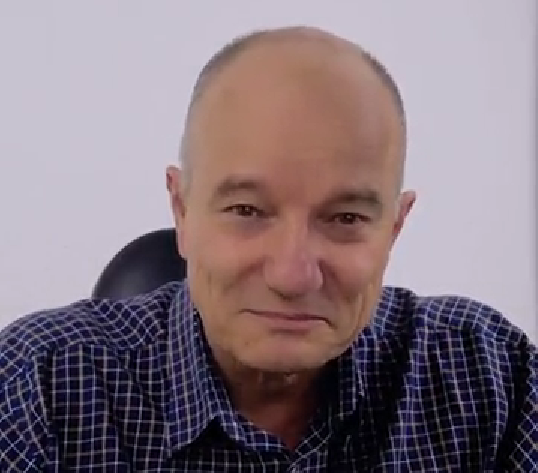
“The finish was perfect, and the team was easy to work with.”

“Working with Frigate has been great. Their proactive, results-driven approach and expertise shine through in every project. It's been a pleasure collaborating with them.”

"We are highly satisfied with the timely delivery and quality of the MIG Welding Cable from Frigate. Their attention to detail, secure packaging, and quick responsiveness stood out. We confidently recommend Frigate Engineering Services Pvt. Ltd. as a reliable manufacturing partner."
Having Doubts? Our FAQ
Check all our Frequently Asked Question
Signal integrity is maintained by carefully selecting low-resistance and high-shielding wires. Routing is designed to minimize electromagnetic interference, and connectors are chosen for their superior conductivity and durability.
The wire gauge and insulation type depend on the voltage, current requirements, and environmental conditions. For high-voltage or high-temperature applications, specialized insulation materials and thicker gauge wires are used to ensure safety and performance.
Custom harnesses are built with materials resistant to temperature extremes, moisture, abrasion, and chemicals. Special coatings, jacketing, and sealing techniques protect the harnesses in environments such as automotive, aerospace, or industrial settings.
Testing includes electrical continuity checks, insulation resistance testing, high-voltage testing, and mechanical stress testing. Harnesses are also evaluated for signal integrity and to ensure compliance with industry standards and customer specifications.
In space-constrained applications, harnesses are designed with compact routing, reduced wire lengths, and miniaturized connectors. Custom configurations allow for a streamlined layout, minimizing the space required while maintaining functionality and reliability.
We'd love to Manufacture for you!
Submit the form below and our representative will be in touch shortly.
LOCATIONS
Registered Office
10-A, First Floor, V.V Complex, Prakash Nagar, Thiruverumbur, Trichy-620013, Tamil Nadu, India.
Operations Office
9/1, Poonthottam Nagar, Ramanandha Nagar, Saravanampatti, Coimbatore-641035, Tamil Nadu, India. ㅤ
Other Locations
- Bhilai
- Chennai
- Texas, USA