3D Printing Services
Frigate provides advanced 3D printing services for complex geometries. Our technology enables rapid prototyping and customized component production.
Get Your Quote Now
- Instant Quotation
- On-Time Delivery
- Affordable Cost
Innovative 3D Printing Technologies for Custom Parts
Frigate offers an industry-leading online 3D printing service for prototypes and production parts on demand. The latest additive manufacturing technologies produce over 60 functional parts of metals and plastics. Capabilities include eight high-quality 3D printing processes, including selective laser sintering, fused deposition modeling, stereolithography, and direct metal laser sintering. Advanced printers like the Stratasys Fortus 900mc, EOS SLS, and Concept Laser are utilized for optimal results.

Achieving High Precision and Quality Standards
Utilizing state-of-the-art additive manufacturing technologies enhances precision and accuracy in 3D printing processes. This ensures that parts meet the exact specifications required by customers.
Implementing comprehensive quality control throughout the manufacturing process helps maintain high standards. Regular inspections and testing verify that dimensions and tolerances align with customer requirements.
Offering customization options allows for iterative prototyping. This enables customers to refine designs based on initial feedback, ensuring the final product meets quality expectations.

Accelerating Production for Quick Turnaround
Optimizing production workflows enhances manufacturing efficiency. Streamlined processes reduce bottlenecks, allowing quicker turnaround times on prototypes and production parts.
Effective resource management ensures that materials and equipment are readily available. This minimizes delays and keeps projects on schedule, facilitating timely delivery of parts.
Implementing flexible scheduling practices allows for rapid response to urgent customer needs. This adaptability ensures that tight deadlines are met while maintaining high-quality standards.

Ensuring Confidentiality of Intellectual Property
Establishing strict confidentiality agreements protects customers' designs and proprietary information. These agreements create a secure framework for collaboration and ensure the safeguarding of sensitive information.
Implementing secure data handling practices protects intellectual property throughout the manufacturing process. Robust cybersecurity measures prevent unauthorized access to customer designs and data.
Maintaining transparency in processes fosters trust with customers. Clear communication regarding how designs will be managed and protected reassures customers about the confidentiality of their intellectual property.

3D Printing Materials
3D printing has transformed manufacturing through precise and complex component production. This additive process enables rapid prototyping and iterative design for various industries.
Thermoplastics are widely used in 3D printing due to their versatility and ease of use. Common types include PLA, ABS, and PETG. Each type offers different properties, including strength, flexibility, and heat resistance, making it suitable for various applications.
Metal 3D printing utilizes materials like stainless steel, titanium, and aluminum. These metals provide high strength and durability and are suitable for critical applications in the aerospace and automotive industries. Techniques such as Direct Metal Laser Sintering (DMLS) and Electron Beam Melting (EBM) create complex geometries.
Composite materials combine thermoplastics with reinforcing fibers, such as carbon or glass. This results in parts with enhanced strength-to-weight ratios, making composites ideal for applications requiring high mechanical properties and reduced weight.
Ceramic materials offer high heat resistance and excellent chemical stability. They are commonly used for applications in medical and dental fields. Advanced 3D printing techniques allow for creating complex shapes and fine details.
Elastomers like TPU (Thermoplastic Polyurethane) provide flexibility and resilience. These materials are suitable for applications requiring rubber-like properties, such as seals, gaskets, and protective components.
Bio-compatible materials are essential for medical applications, such as implants and prosthetics. These materials are designed to integrate with biological tissues, ensuring safety and functionality. Techniques like 3D bioprinting enable the creation of complex tissue structures.
Specialty materials, including high-temperature plastics and fire-retardant materials, address specific application requirements. These materials offer unique properties, such as flame resistance or the capability to withstand extreme temperatures, making them suitable for specialized industries.
Multi-material printing techniques allow the use of different materials in a single print. This capability enhances functionality by combining one component's properties, such as rigidity and flexibility. Frigate employs advanced 3D printing methods to achieve this complexity.
Customizing Post-Processing Approaches
Many 3D-printed parts undergo post-processing to achieve optimal finishes and functional characteristics. Common methods include sanding, polishing, painting, and coating, which enhance aesthetics and improve mechanical properties such as strength and durability. Frigate specializes in various post-processing techniques, providing customers tailored guidance for each project. Expert advice ensures the selection of appropriate methods, resulting in components that meet functional and quality standards. Frigate helps customers achieve their design goals efficiently and effectively by streamlining the post-processing phase.

- Real Impact
Words from Clients
See how global OEMs and sourcing heads describe their experience with our scalable execution.
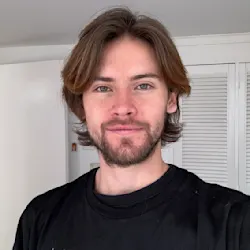
“Quick turnaround and solid quality.”
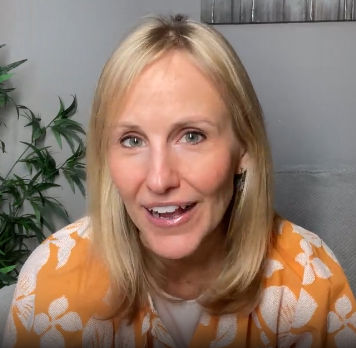
“The instant quote tool saved us time, and the parts were spot-on. Highly recommend Frigate!”
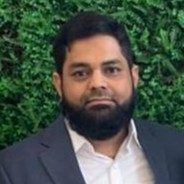
“I would strongly recommend Frigate to anyone who wants to do Rapid Prototyping, and take their ideas to manufacturing. One firm doing all kinds of Product Development!”
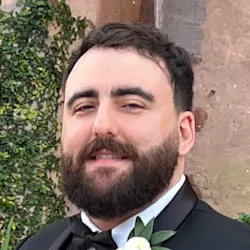
“Great service, fair price, and the parts worked perfectly in our assembly.”
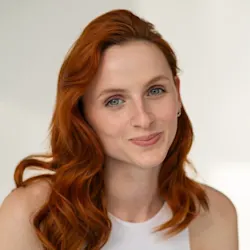
“Top-notch machining and fast shipping. Very satisfied with the results.”
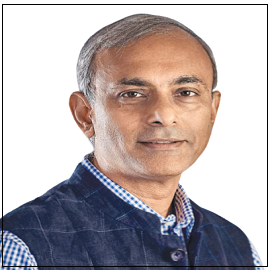
“The next disruption is happening in Prototyping & Manufacturing on-demand and Frigate is leading the way! I personally believe the Frigate's way of IIOT enabled cloud platform with Al.”
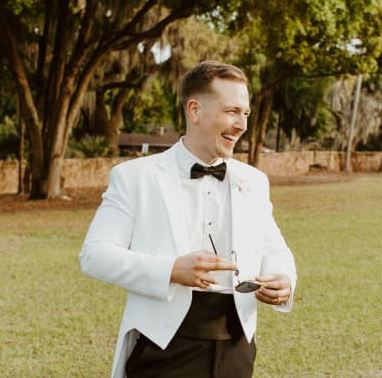
“Frigate delivered high-quality parts at a competitive price. The instant quote tool is a huge plus for us!”

“We appreciate the precision and quality of the machined components in the recent delivery—they meet our specifications perfectly and demonstrate Frigate’s capability for excellent workmanship.”
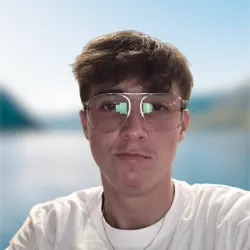
“Flawless execution from quote to delivery.”

“I am absolutely happy to work with supplier like Frigate who were quite proactive & result oriented . Frigate has high willingness team who has strong know how & their passion towards the products & process were absolutely thrilling.”
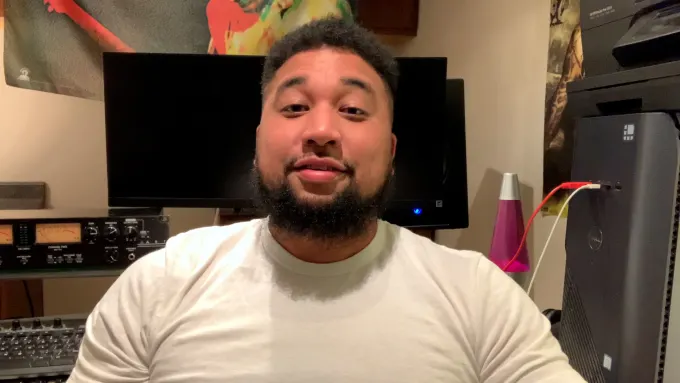
“The precision on these parts is impressive, and they arrived ahead of schedule. Frigate’s process really stands out!”
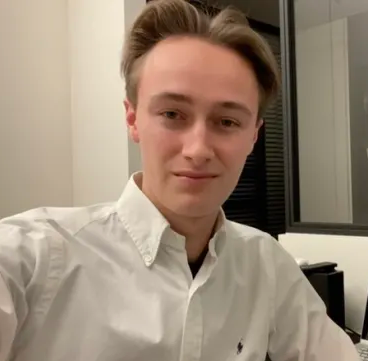
“Parts were exactly as spec’d, and the instant quote made budgeting a breeze.”
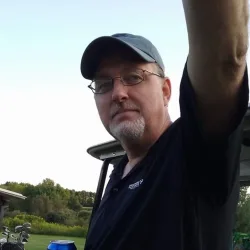
“Good value for the money.”
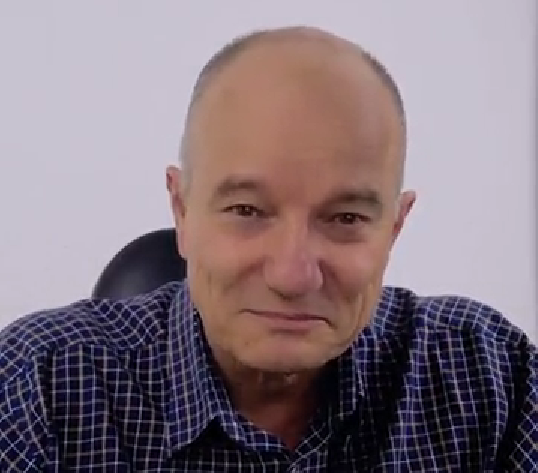
“The finish was perfect, and the team was easy to work with.”

“Working with Frigate has been great. Their proactive, results-driven approach and expertise shine through in every project. It's been a pleasure collaborating with them.”

"We are highly satisfied with the timely delivery and quality of the MIG Welding Cable from Frigate. Their attention to detail, secure packaging, and quick responsiveness stood out. We confidently recommend Frigate Engineering Services Pvt. Ltd. as a reliable manufacturing partner."
Having Doubts? Our FAQ
Check all our Frequently Asked Question
The choice of technology depends on the part's geometry, material requirements, and desired mechanical properties. Frigate evaluates each project to select the most suitable process, such as FDM, SLA, or DMLS.
Frigate utilizes advanced multi-material printing techniques, combining different materials in a single build. This capability enables manufacturing parts with different properties, such as rigidity and flexibility.
Frigate implements a multi-step quality control process, including real-time monitoring of print parameters, visual inspections, and dimensional verification. These measures ensure that all parts meet stringent quality standards.
Frigate assesses each application's specific requirements, including load-bearing capacity and environmental conditions. This analysis guides material selection and design adjustments to enhance compatibility and performance.
Frigate offers various post-processing options, including heat treatment, surface hardening, and chemical finishing. These techniques enhance strength, durability, and resistance to wear, making parts suitable for demanding applications.
Manufacturing Capability/Capacity
Ferrous casting
Mold size(max): 1m X 1m
Weight Range: 1 KG ~ 30 KGS
Mold size(max): 1.5m X 1.5m
Weight Range: 30 KG ~ 150 KGS
Mold size(max): 3m X 3m
Weight Range: 100 KG ~ 1000 KGS
Mold size(max): 500 MM X 500 MM
Weight Range: 0.250 KG ~ 20 KGS
Mold size(max): 500 MM X 500 MM
Weight Range: 0.100 KG X 20 KGS
Non-ferrous casting
Capacity: 5000 MT/a
Range of weight: 100 gm to 20 KGS
Mold size(max): 1 M X 1 M
Weight Range: 0.5 KG X 50 KGS
Mold size(max): 1 M X 1 M
Weight Range: 0.5 KG X 50 KGS
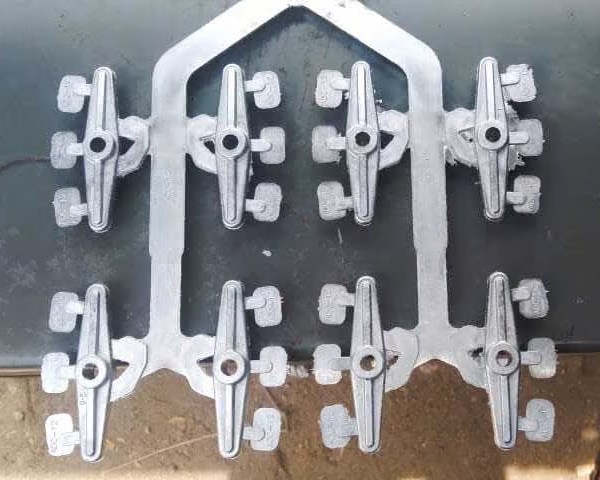
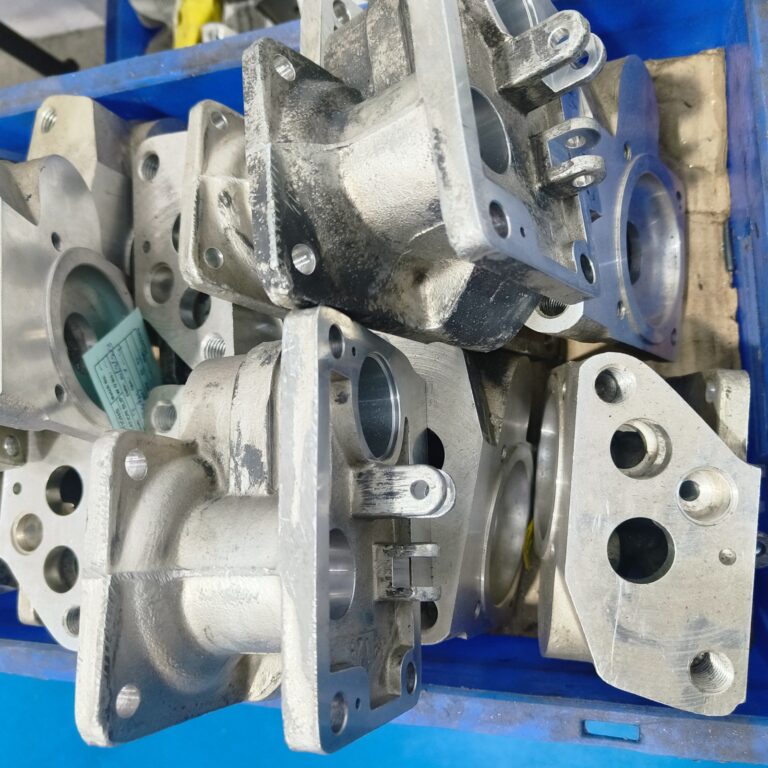
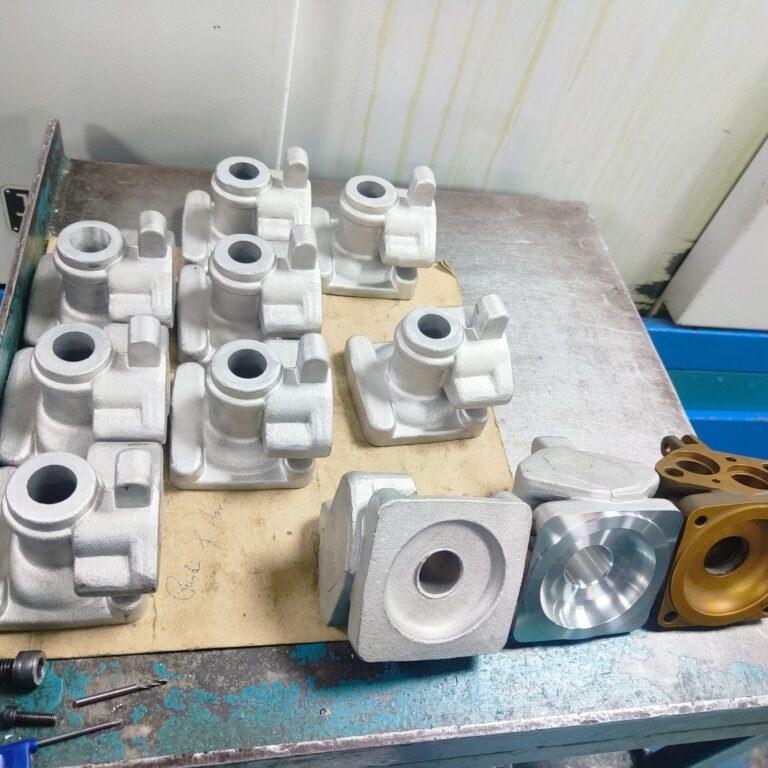
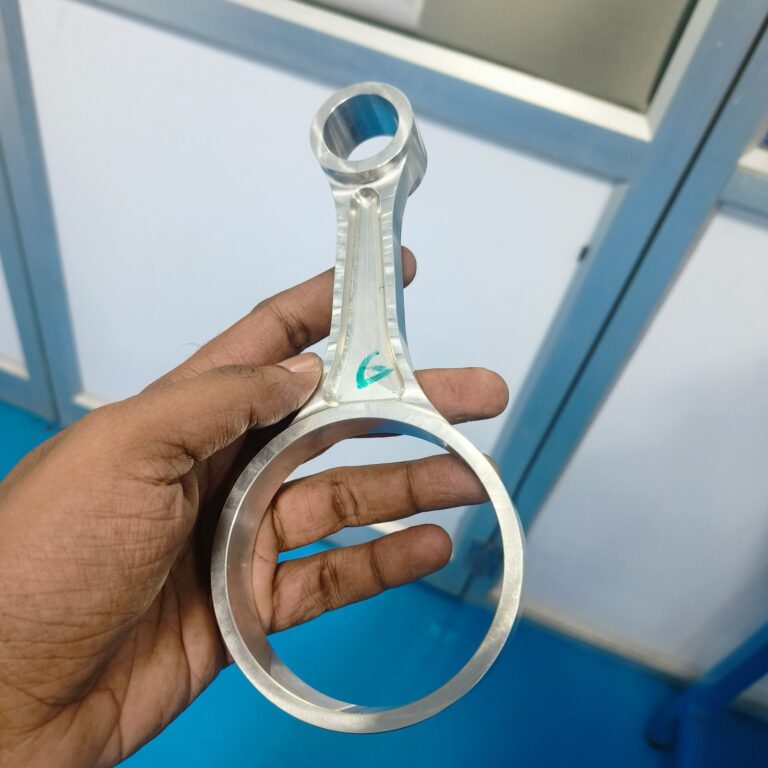
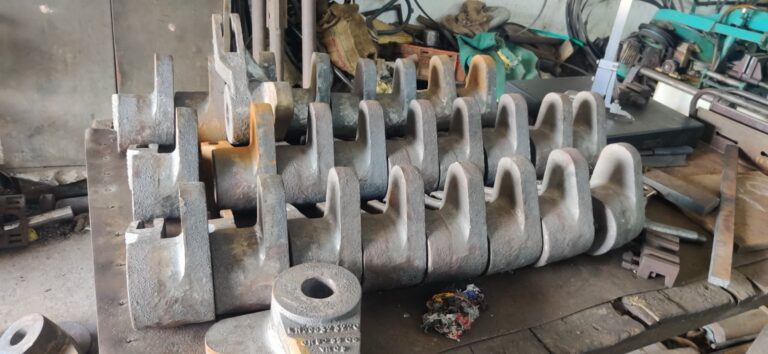
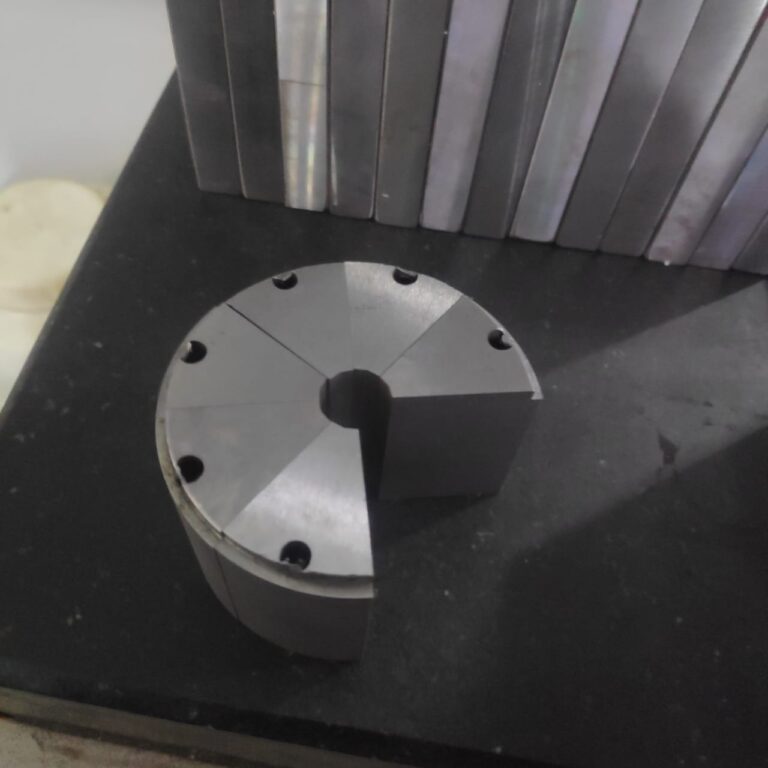
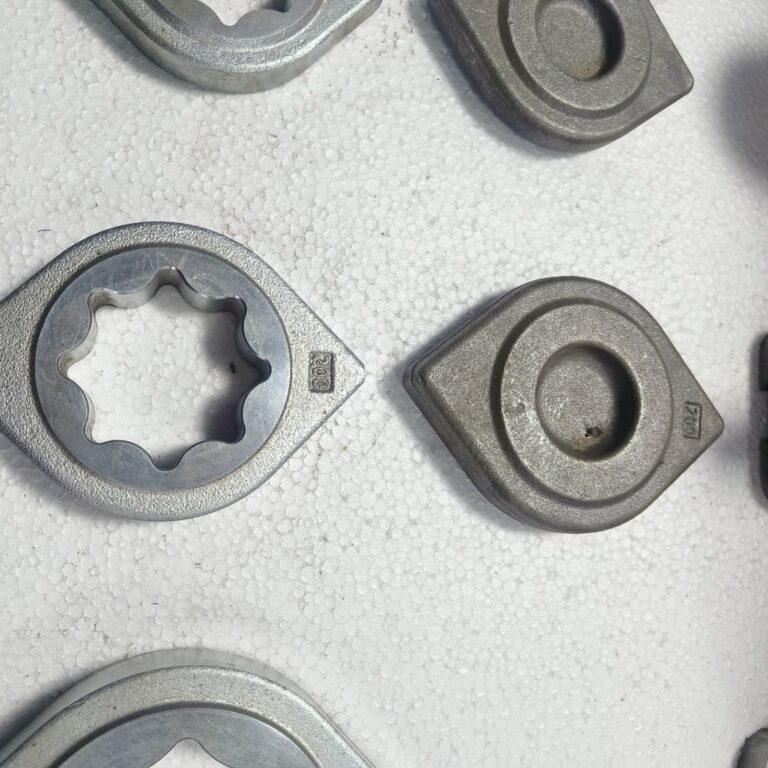
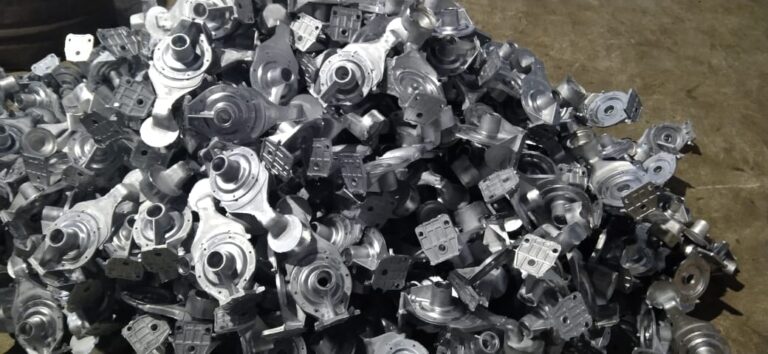
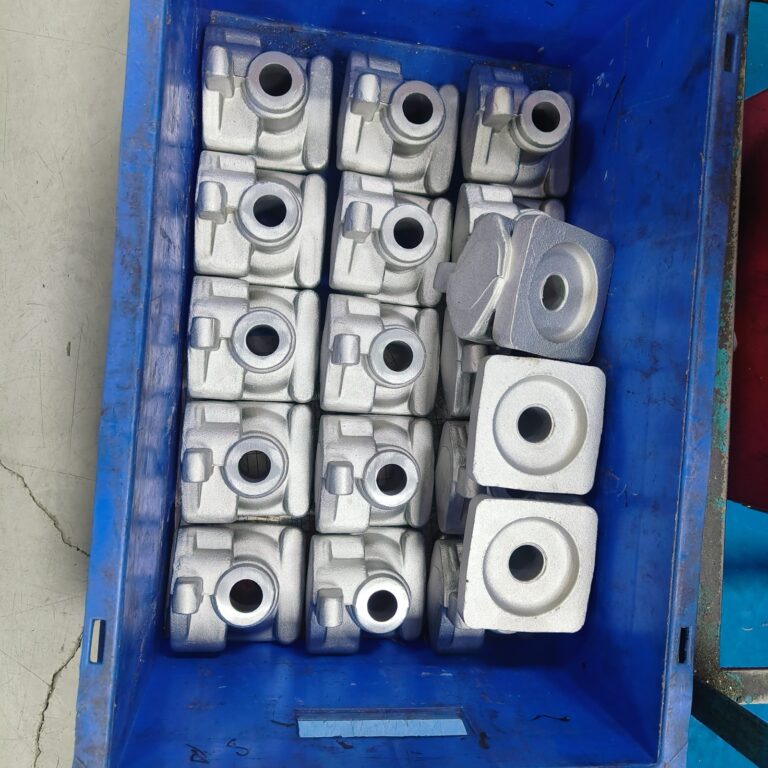
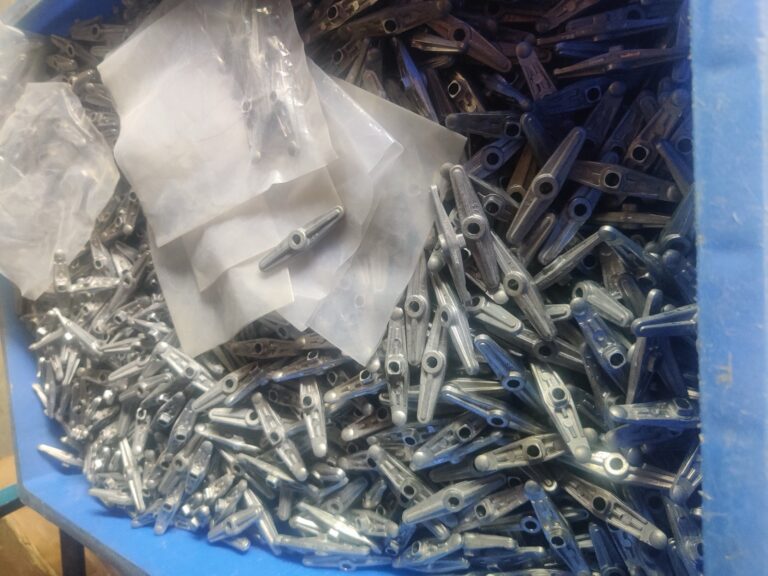
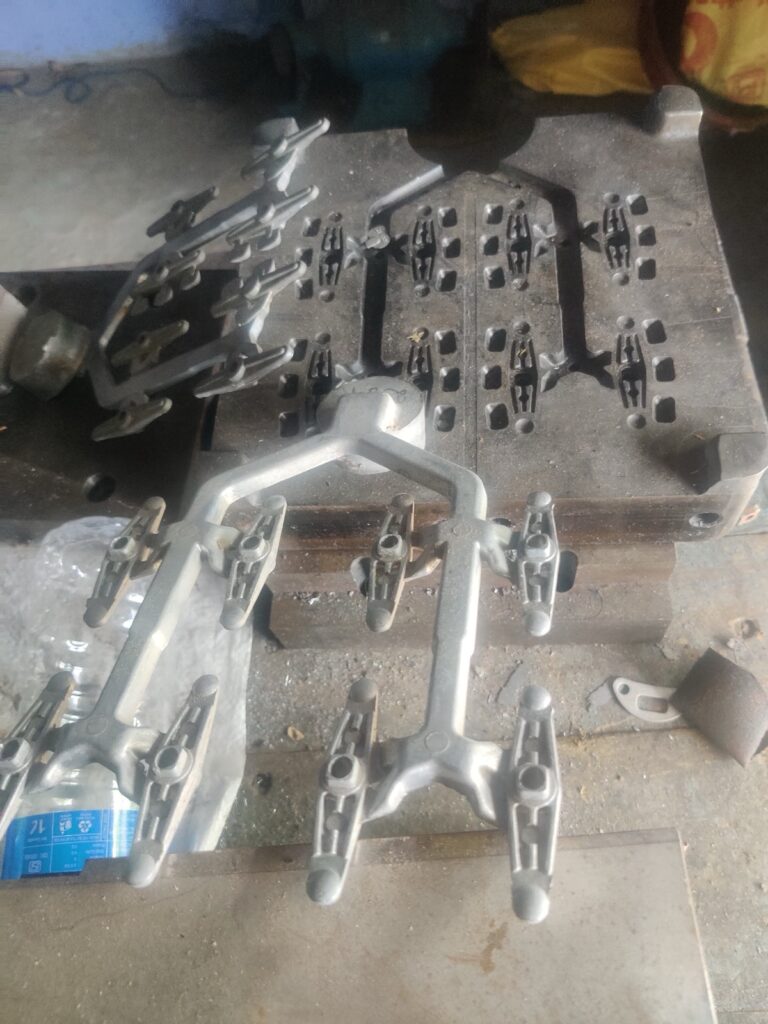
Forging
Capacity: 20,000 Tons per Annum
Range of weight: 300 KG to 1 Ton
Hammering: 5 Ton
Range of weight: 0.2 KG to 200 KGS
Hammering: 1600 Ton Hydraulic press
Ring size: 350 MM OD to 3000 MM OD
Range of weight: 15 KGS to 3200 KGS
Materials
Carbon Steel, Stainless Steel (AUSTENITE), Alloy Steel, Stainless Steel (MARTENSITE), etc.
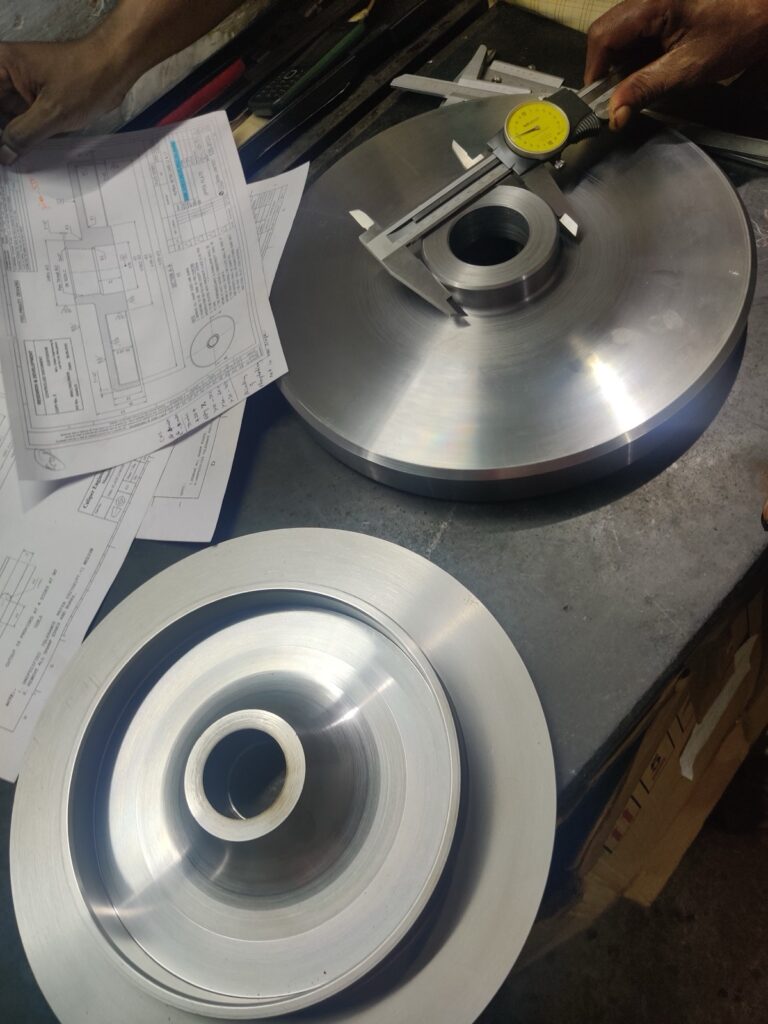
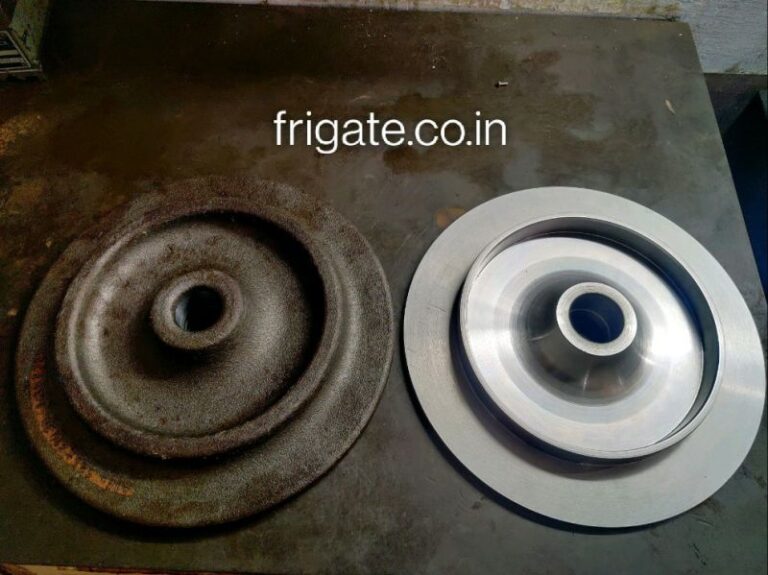
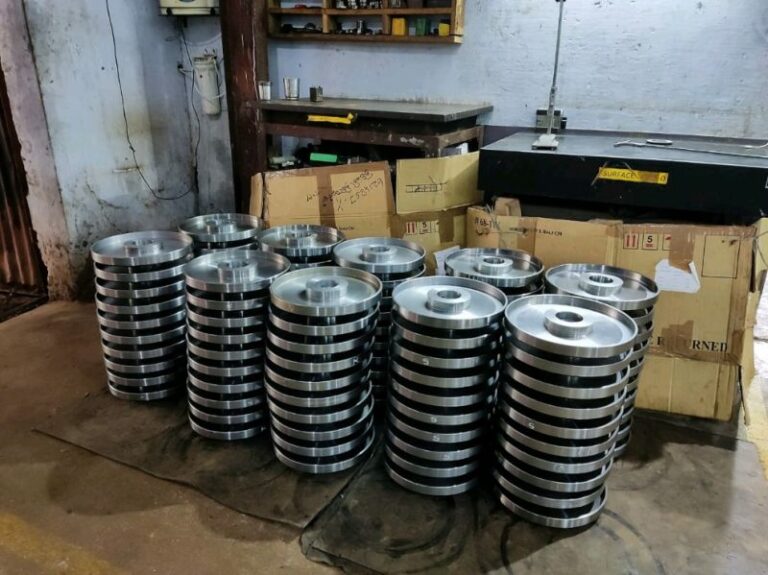
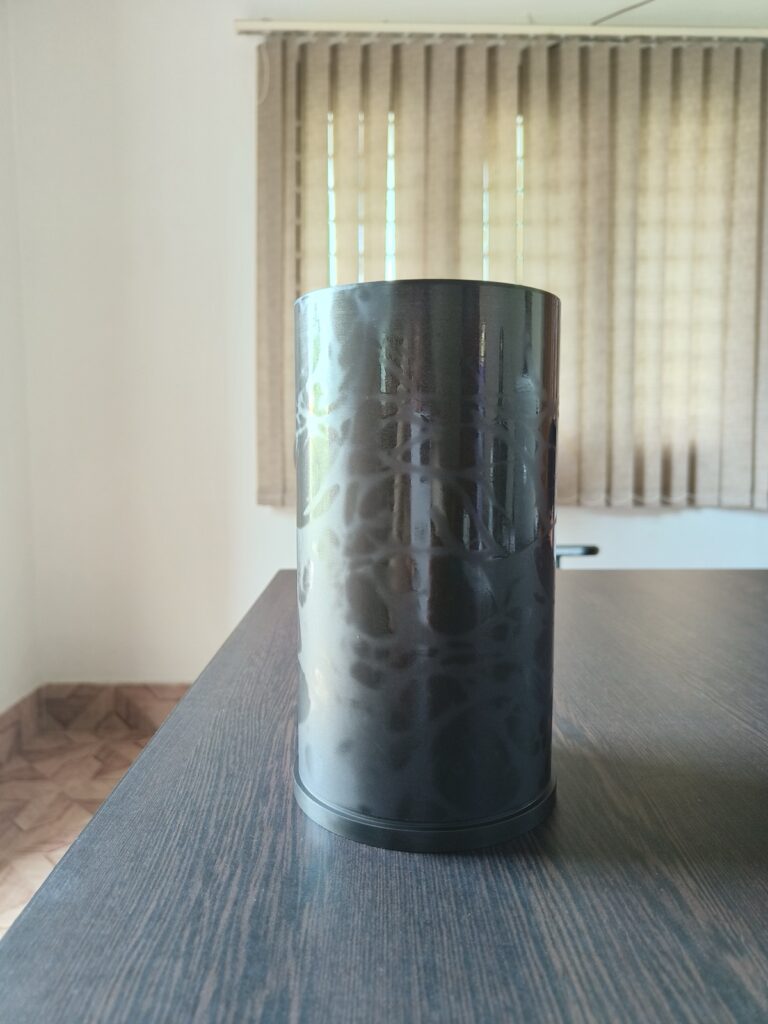
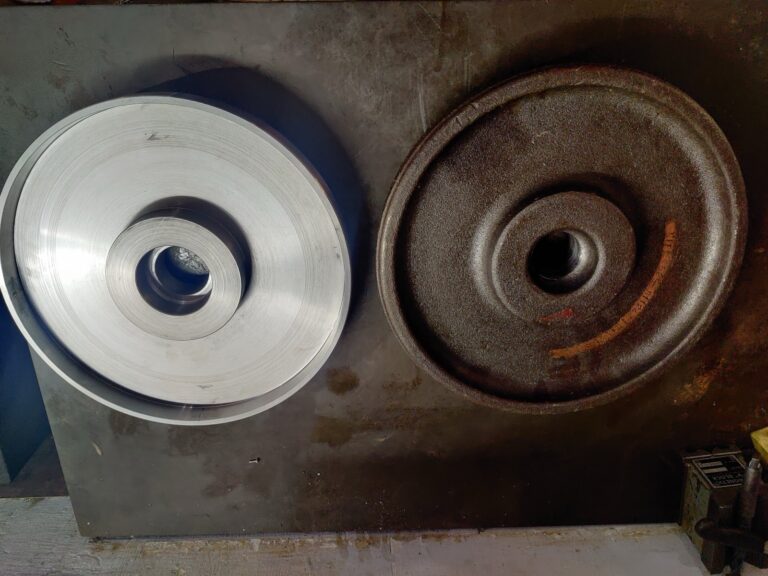
Machining
1 to 1000 MM
1 to 1000 MM
1 to 1000 MM
Materials
Steel, Aluminum, Brass, Copper, Titanium, Nickel Alloys, Tungsten Carbide, etc.
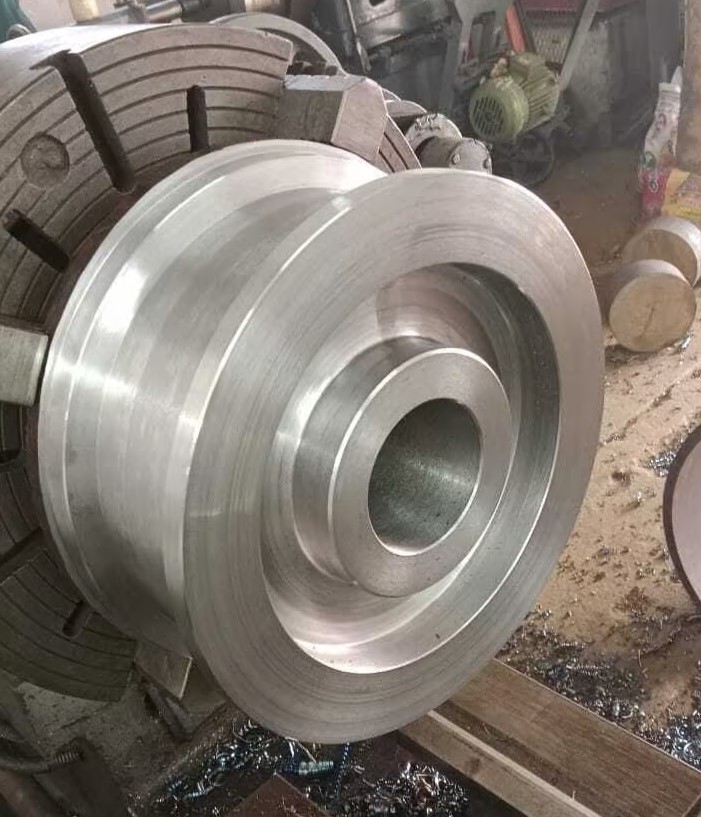
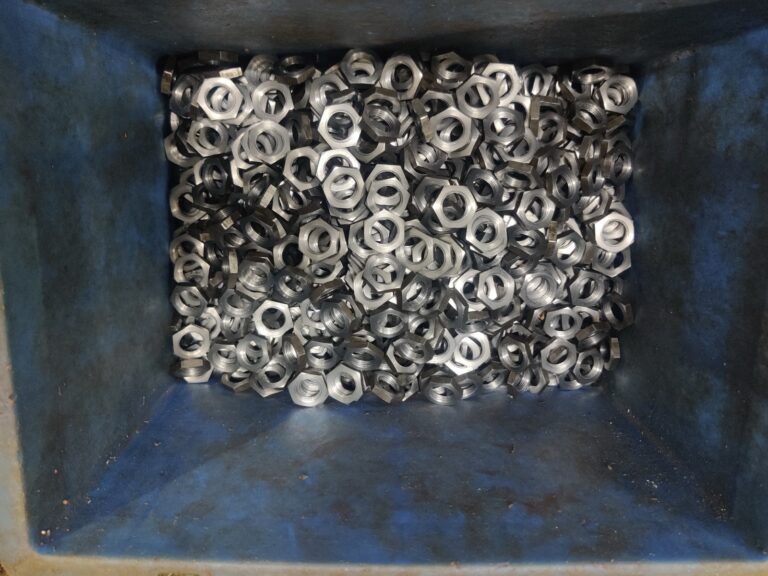
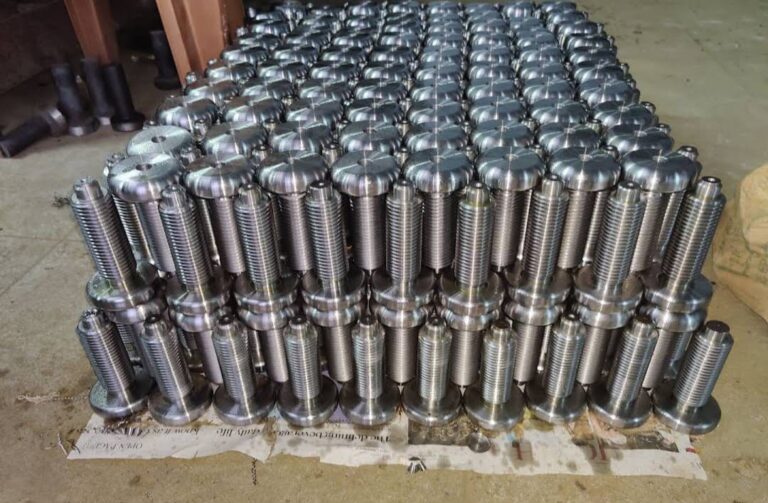
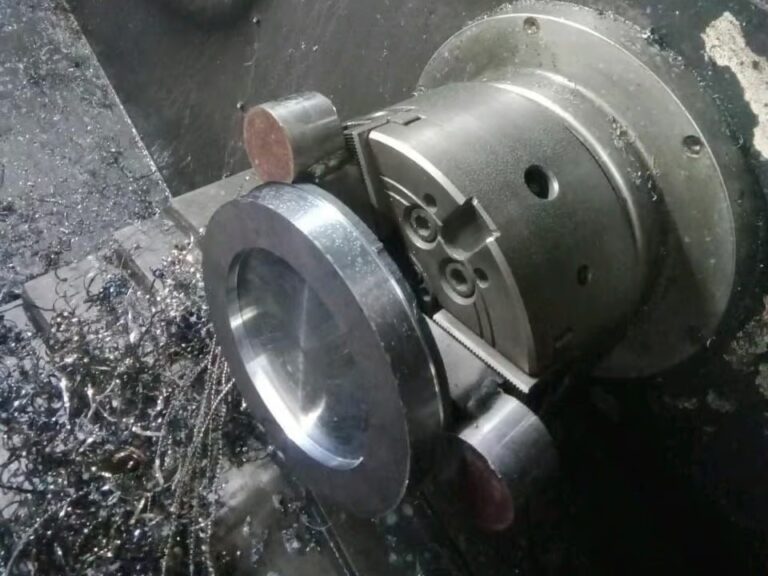
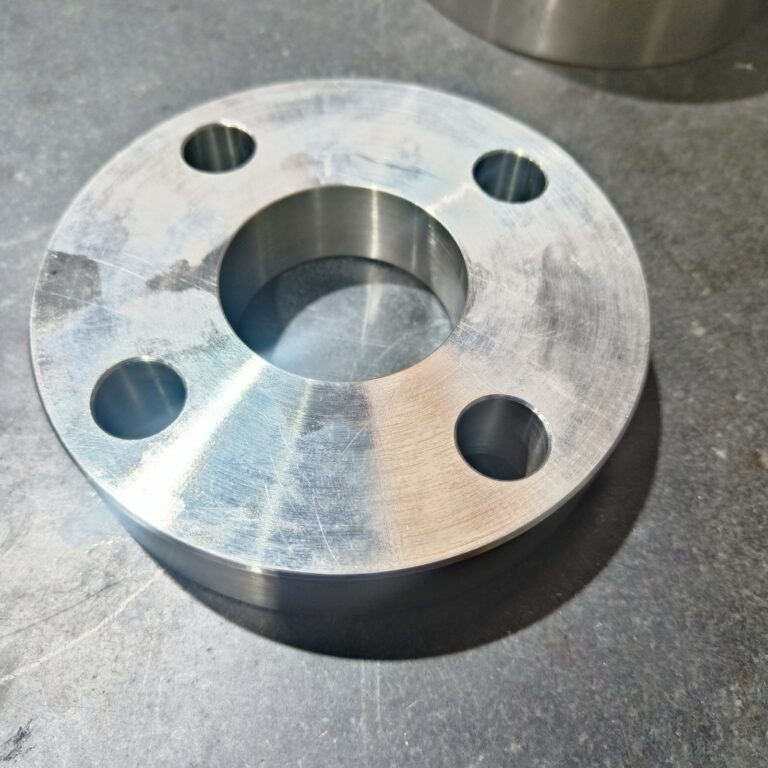
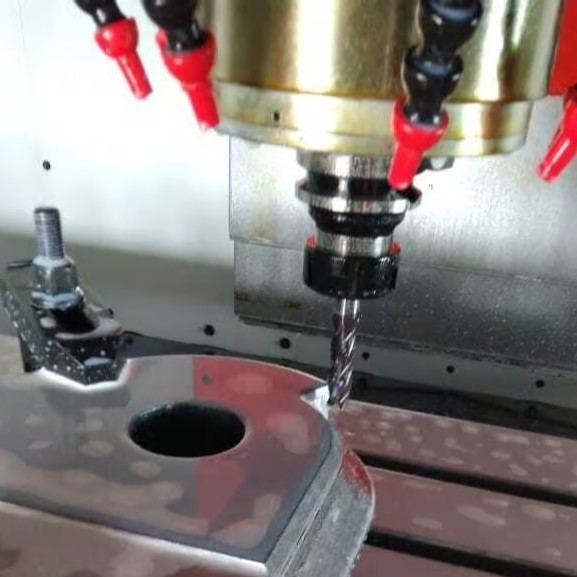
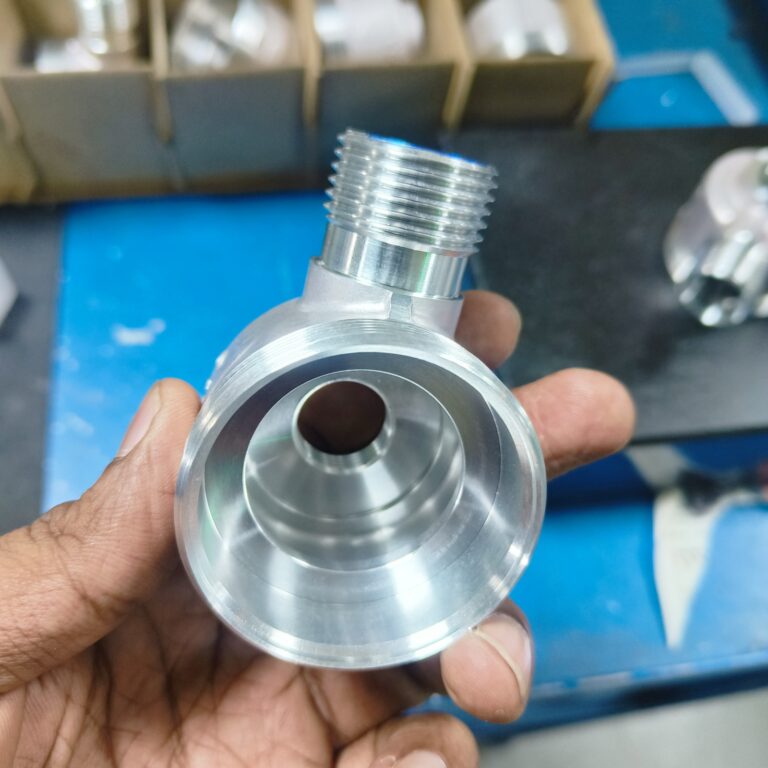
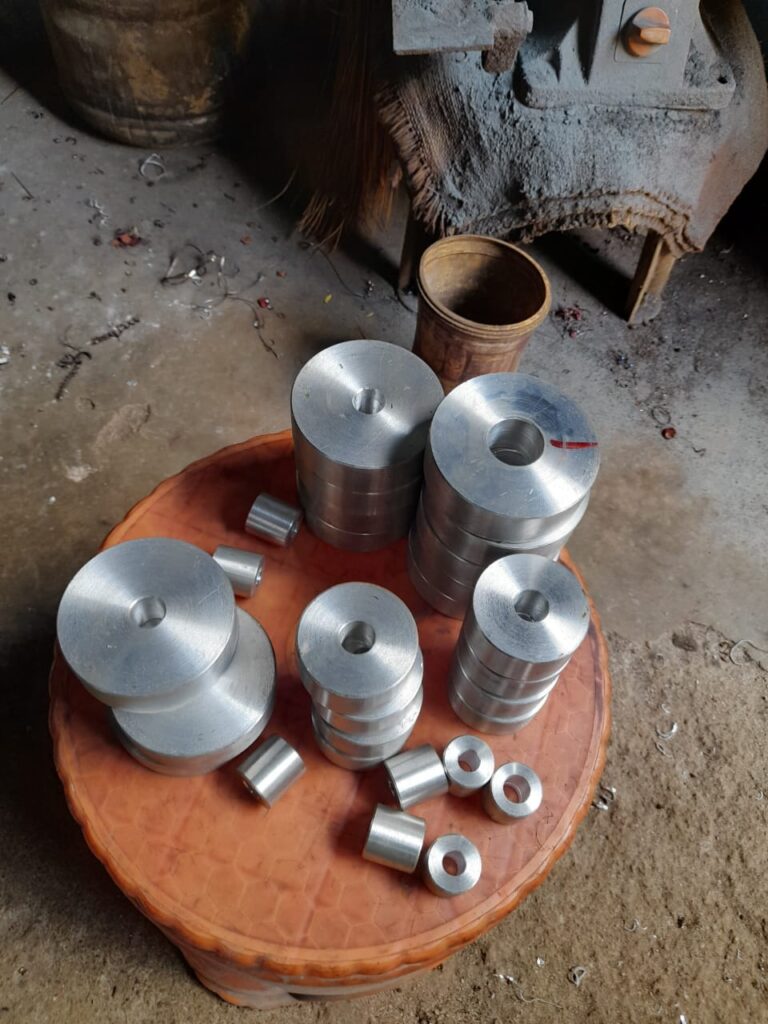
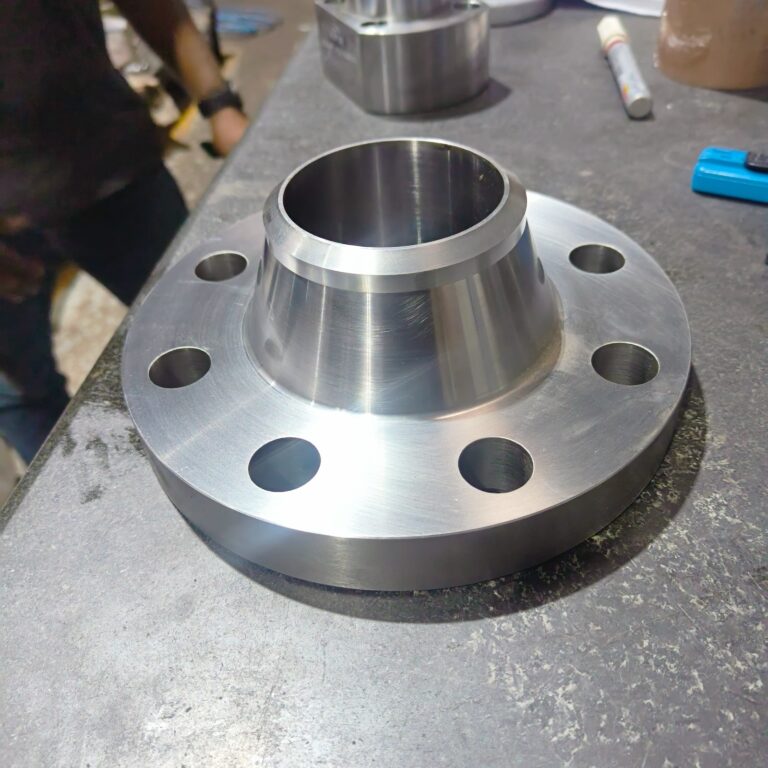
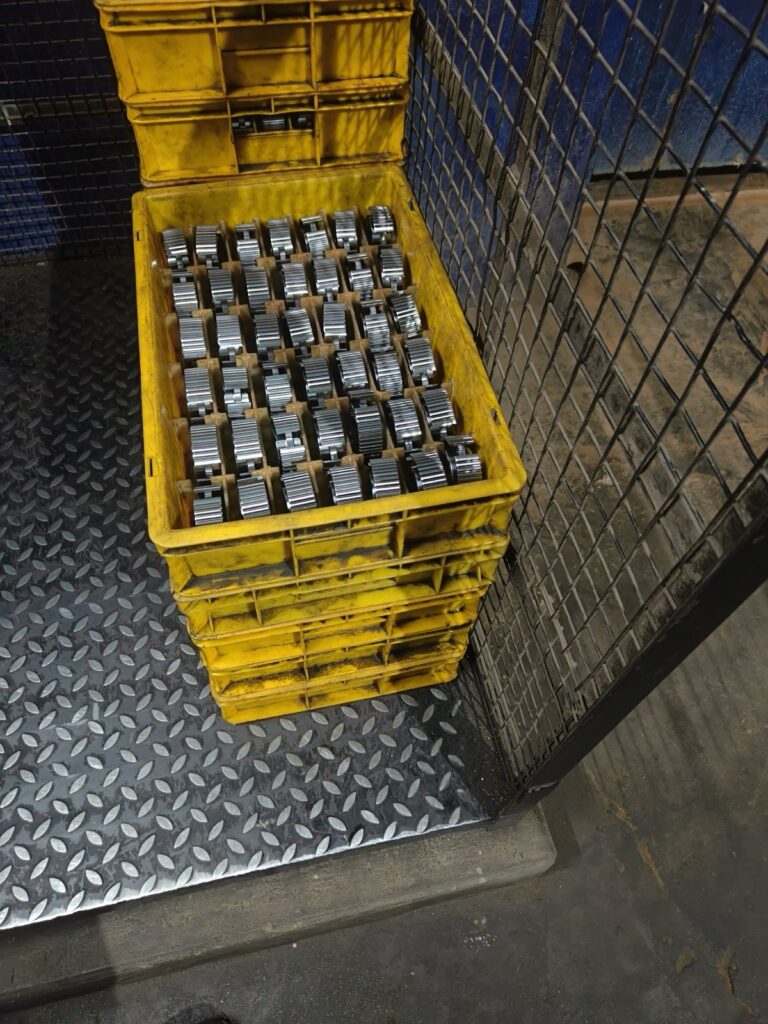
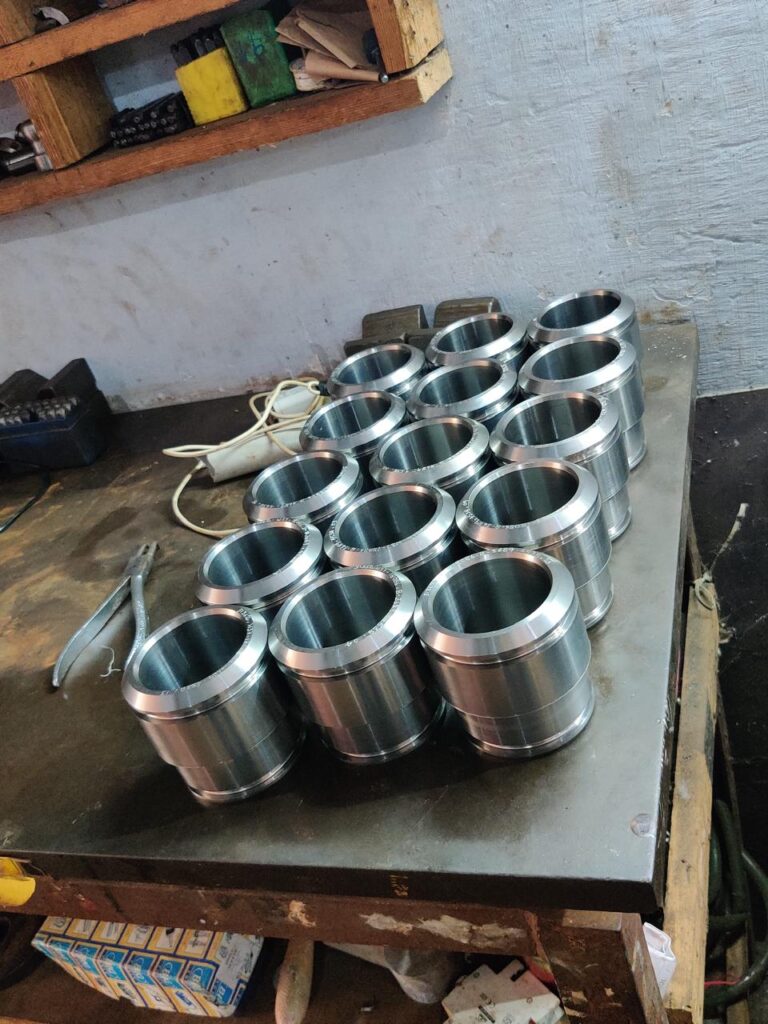
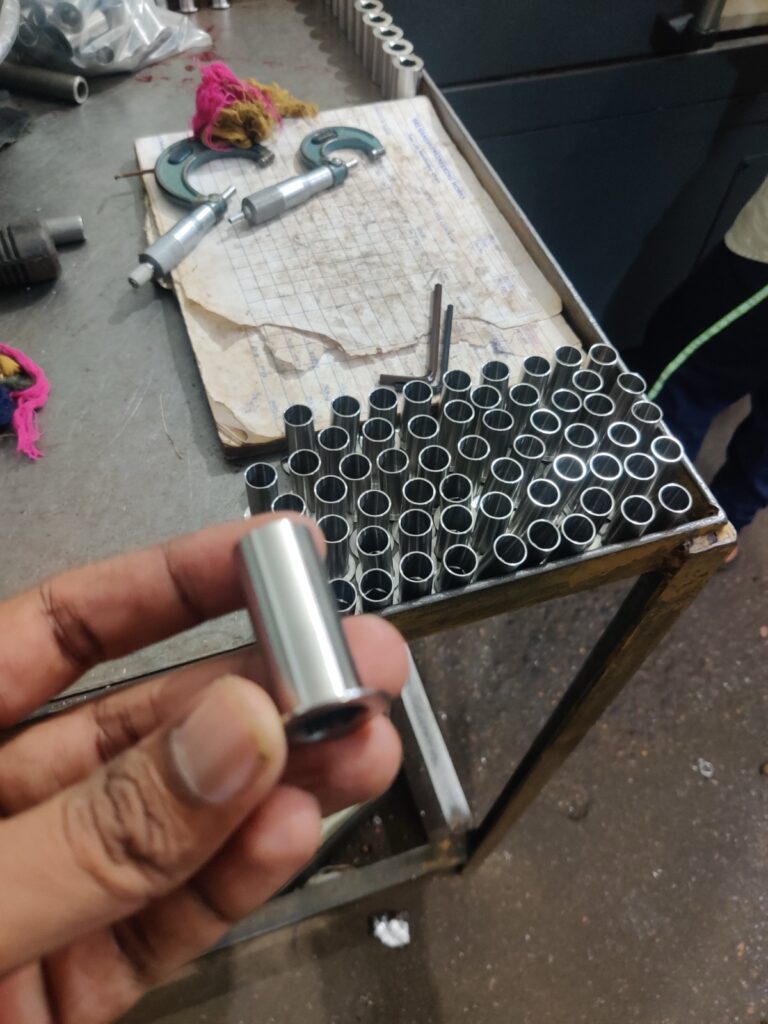
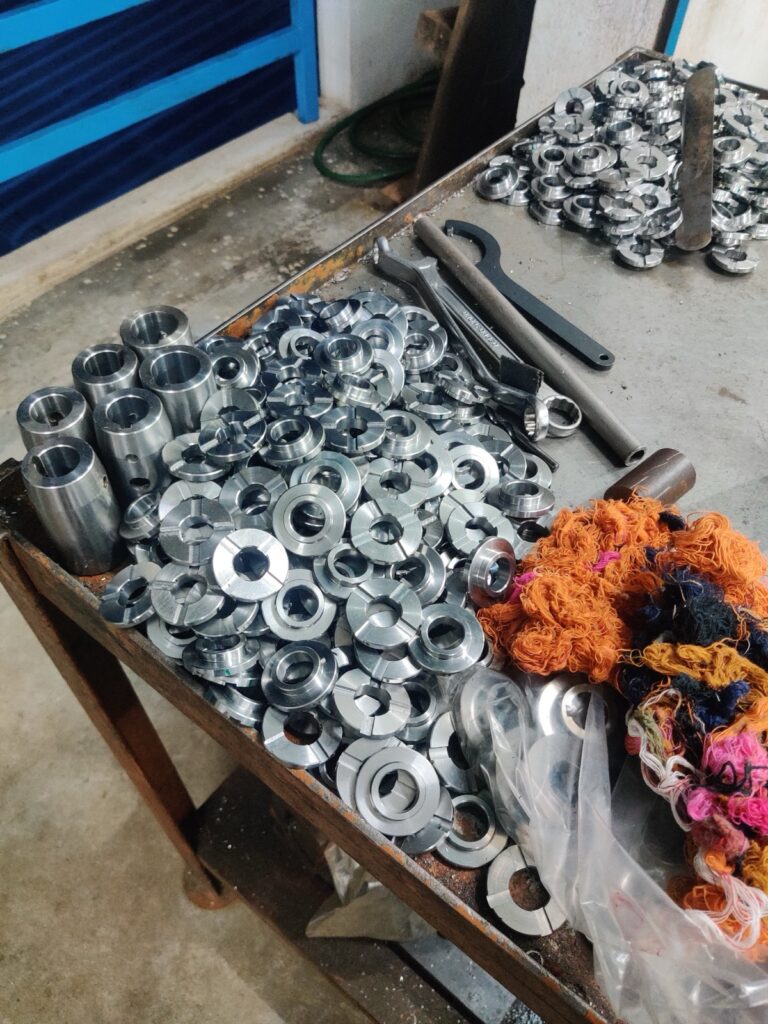
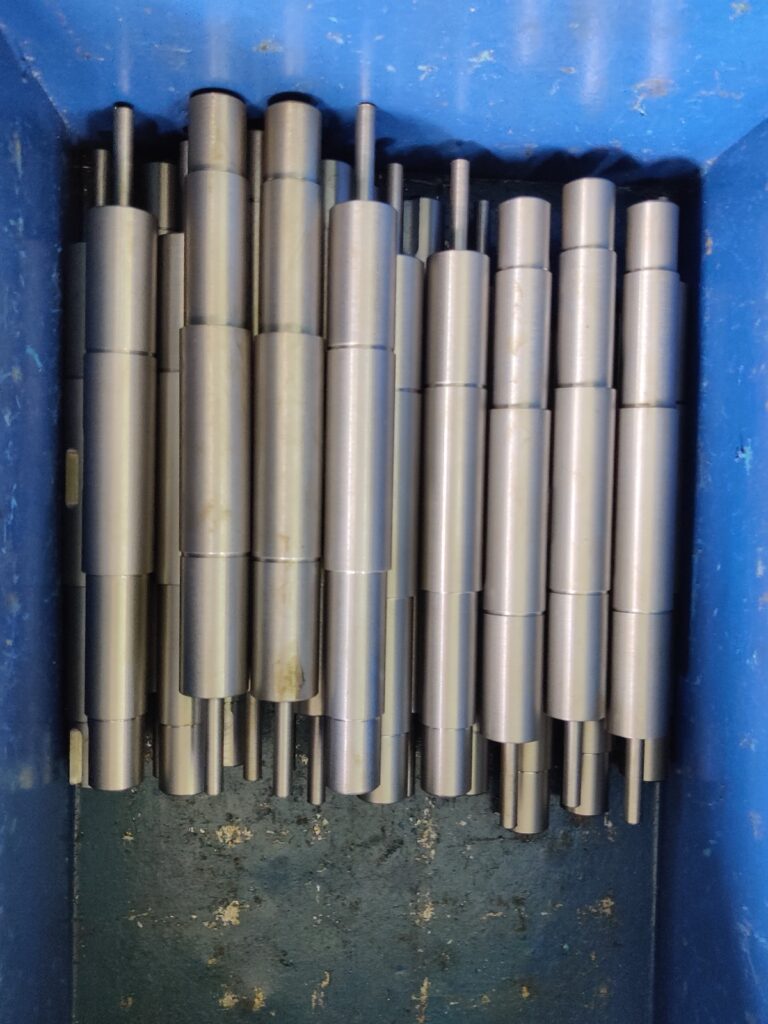
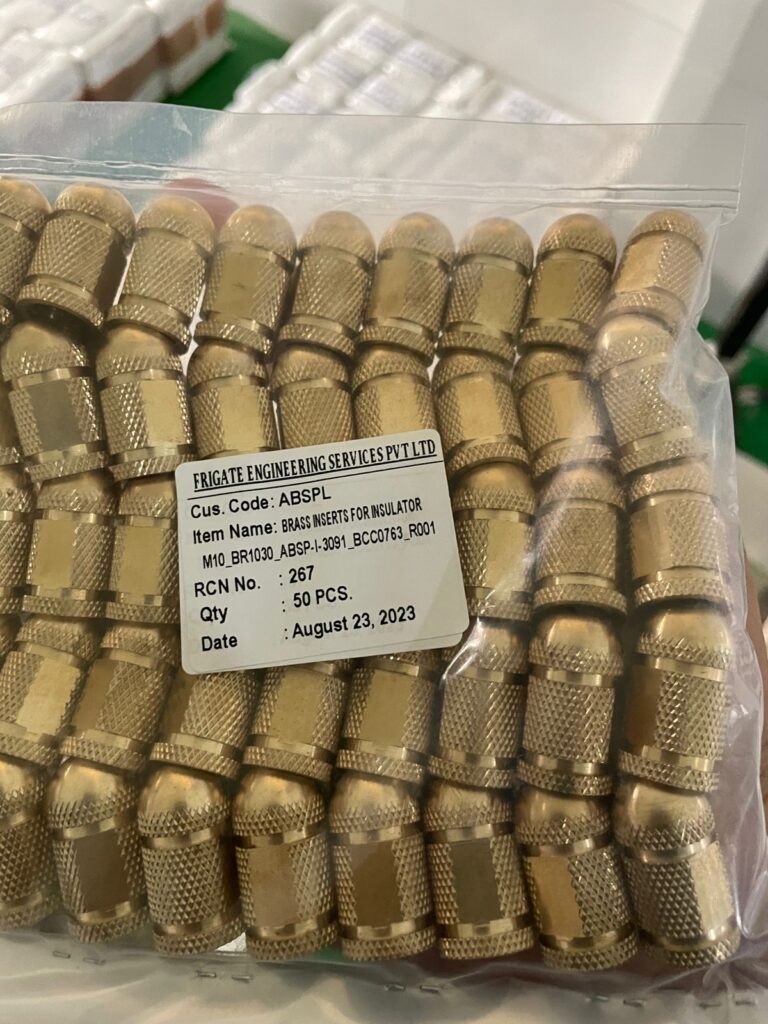
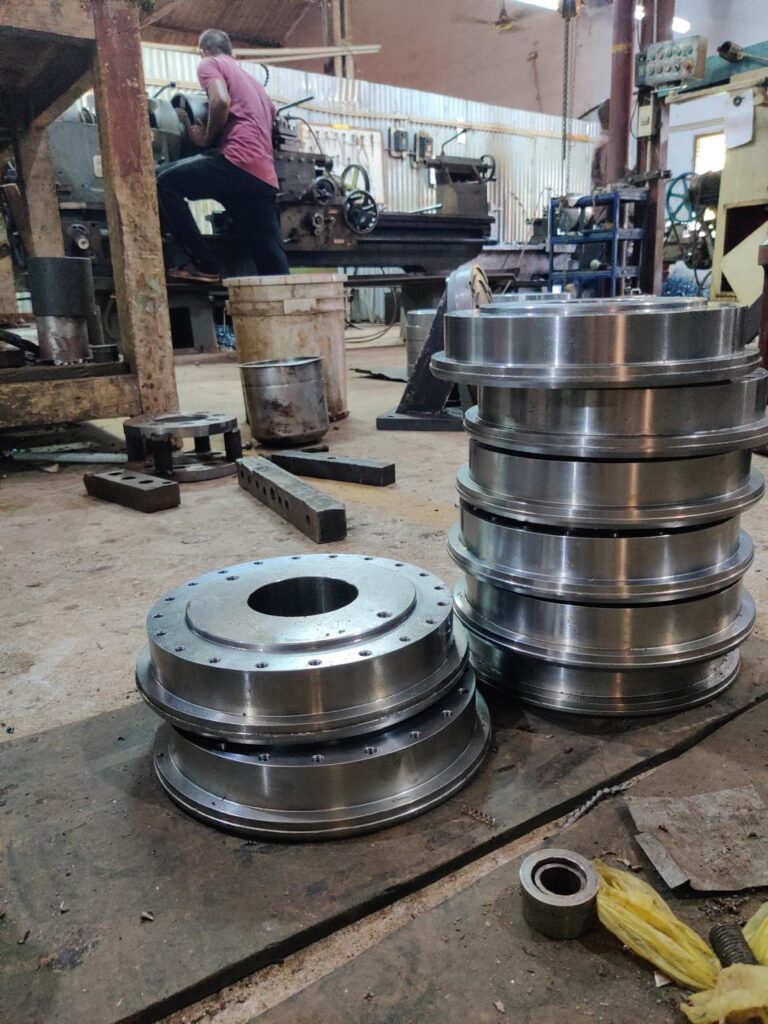
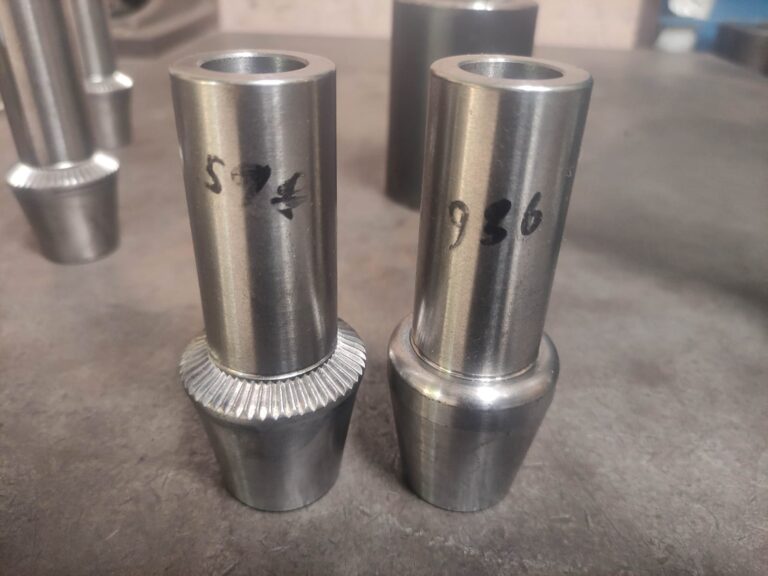
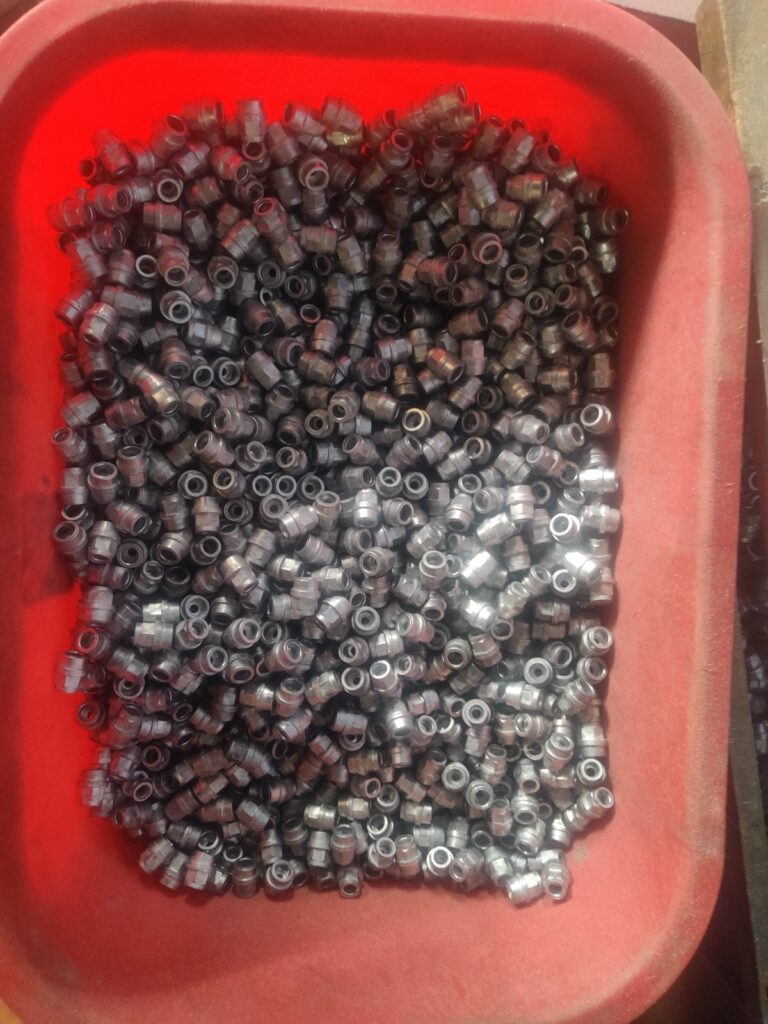
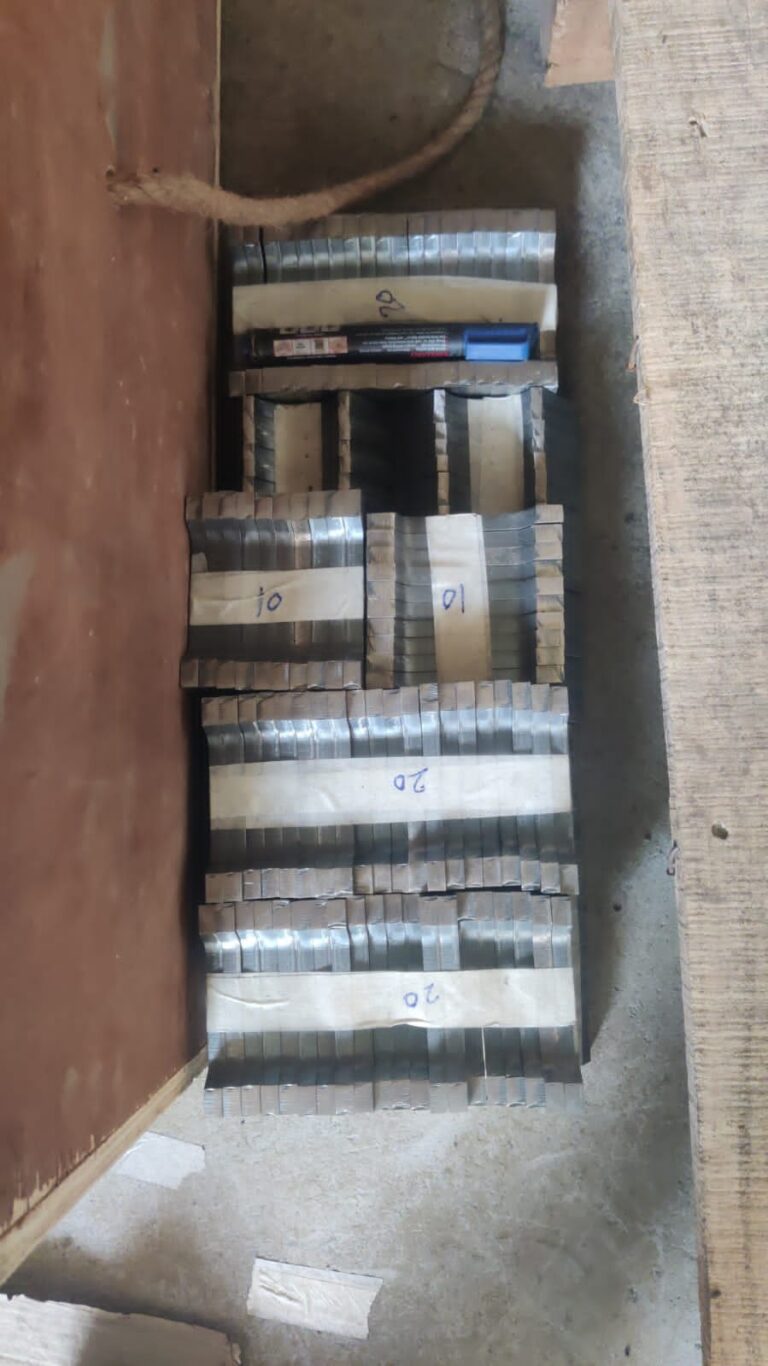
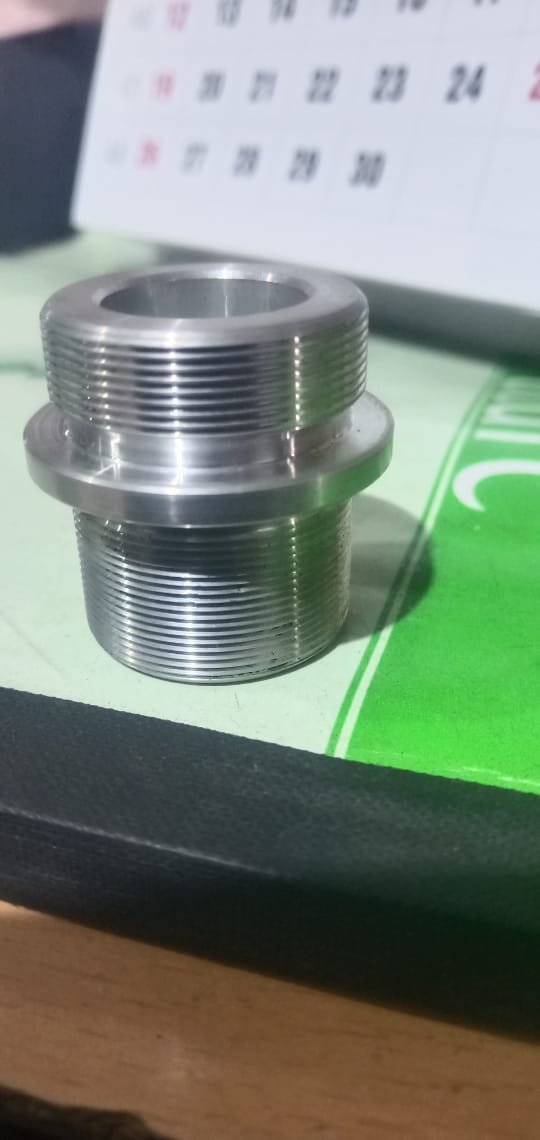
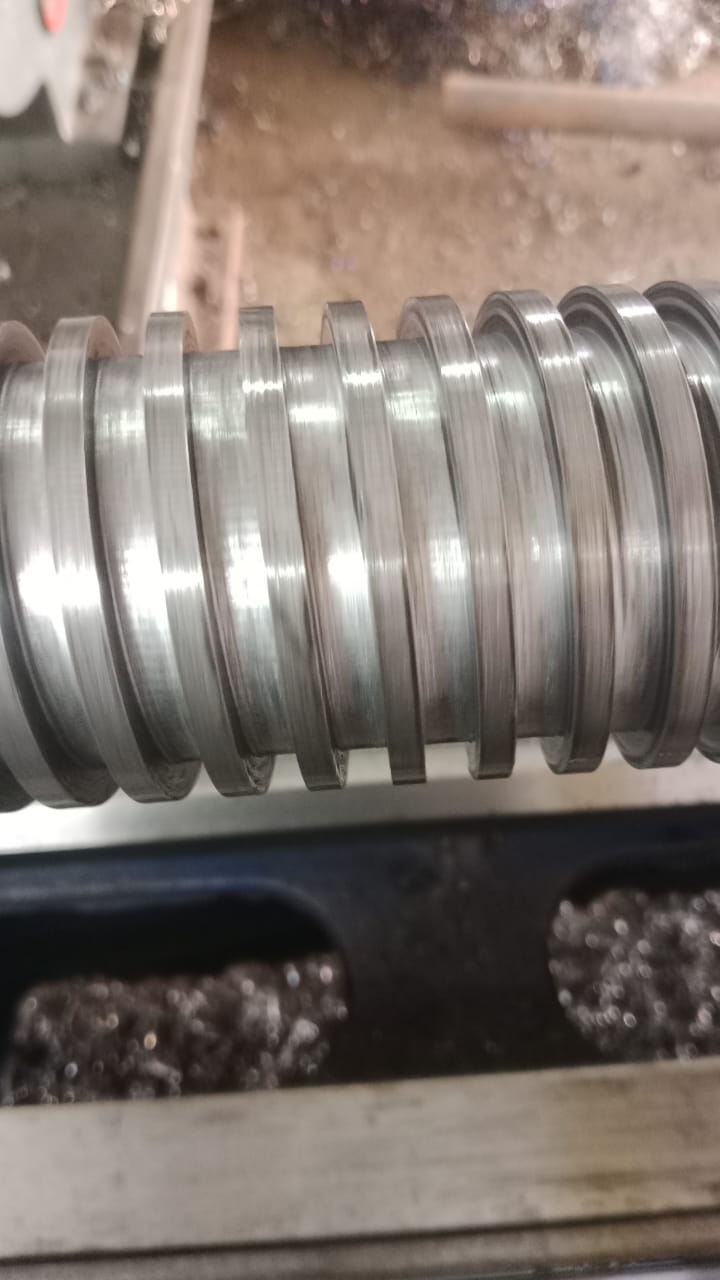
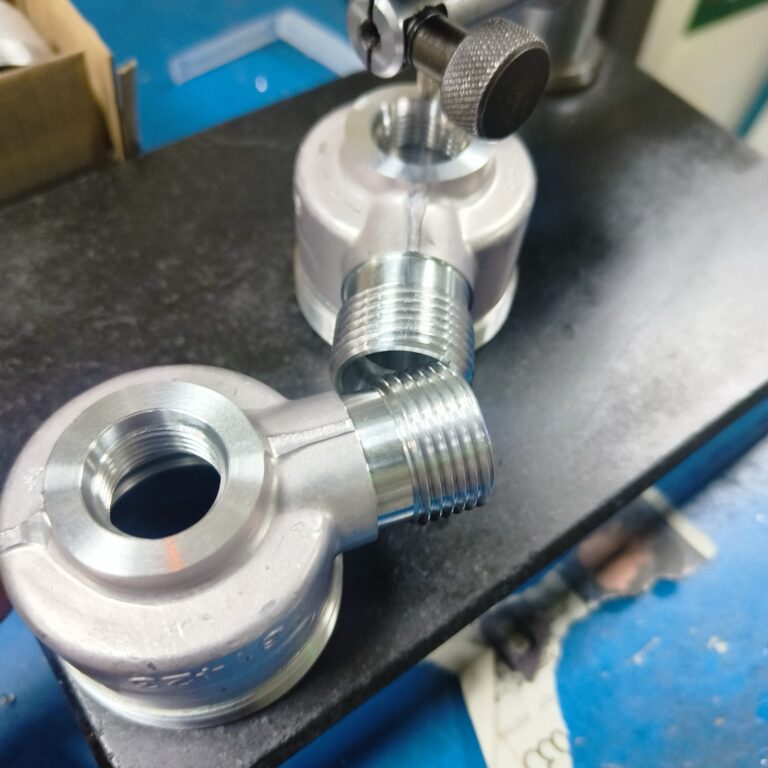
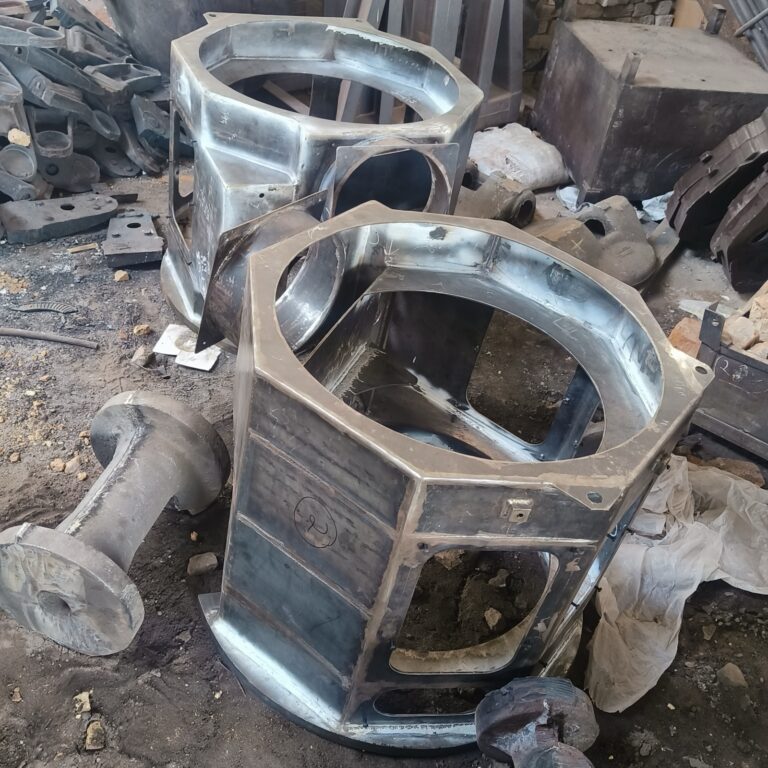
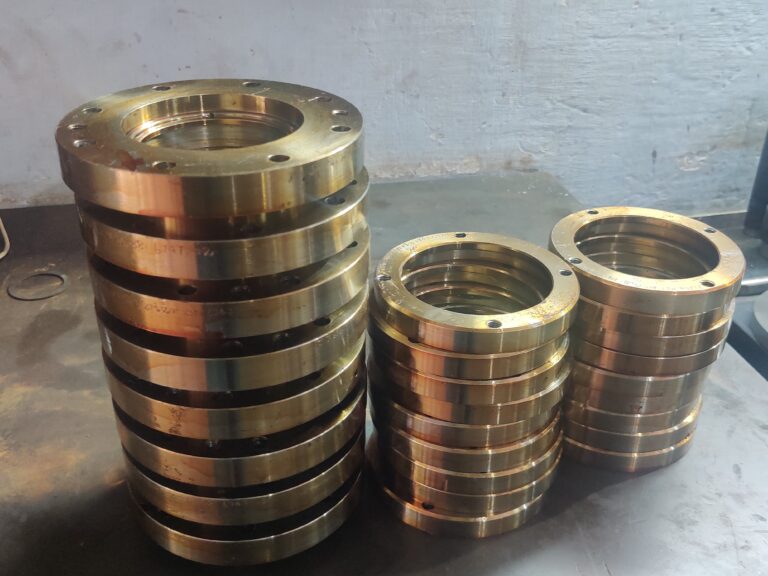
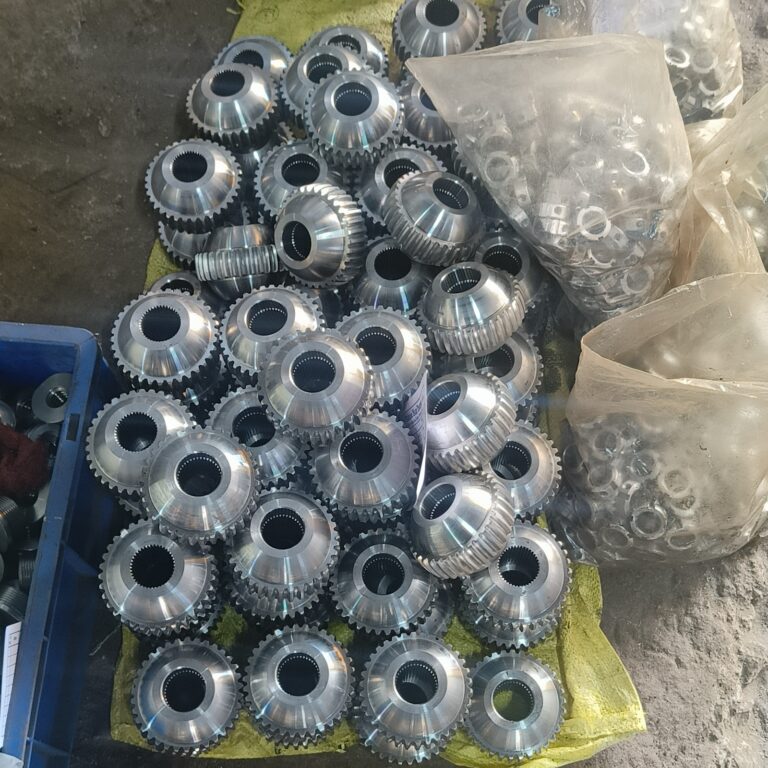
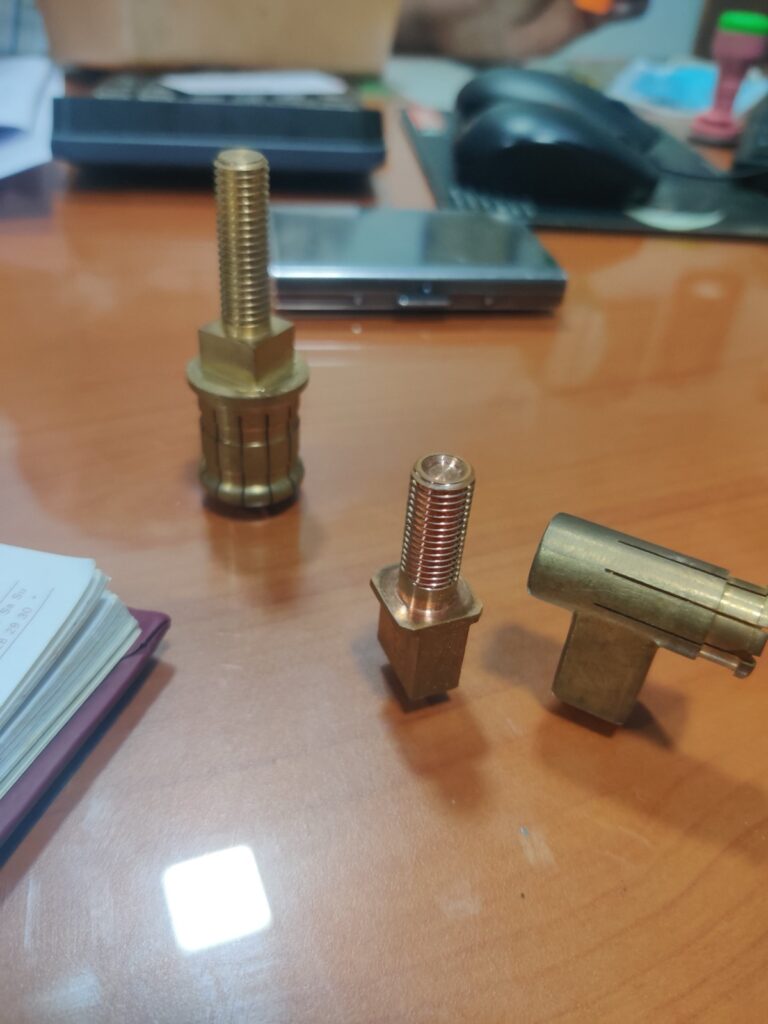
Plastics
Materials
1250 X 1250 MM
Within 10 microns
Engineering Plastics, Polyethylene, Polypropylene, Polyvinyl chloride, Polyethylene terephthalate, Bioplastics, etc.
Rubber
Materials
Natural rubber, Styrene-Butadiene Rubber, Nitrile Butadiene Rubber, Silicone Rubber, Fluorocarbon Rubber, Recycled Rubber, etc.
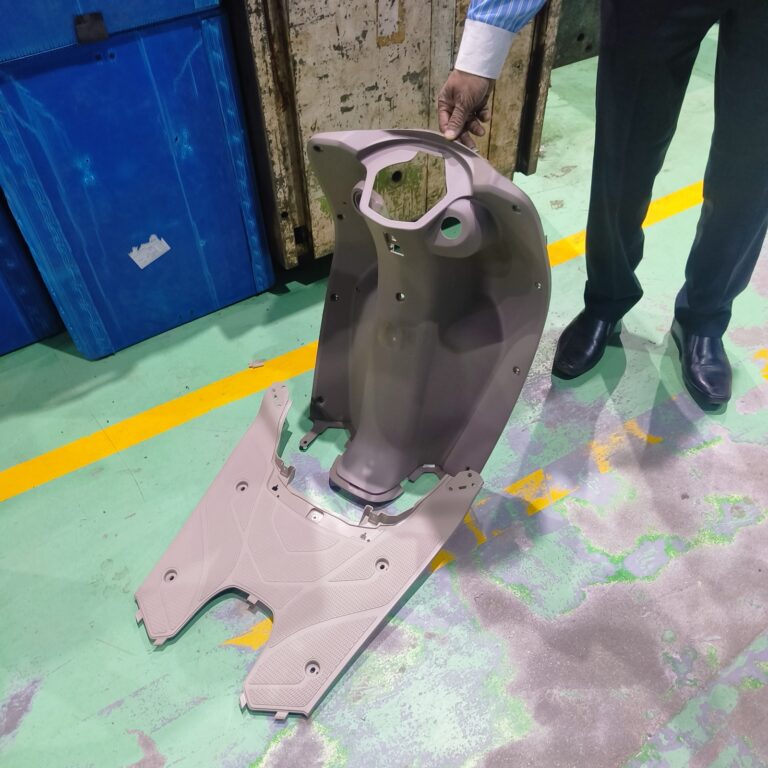
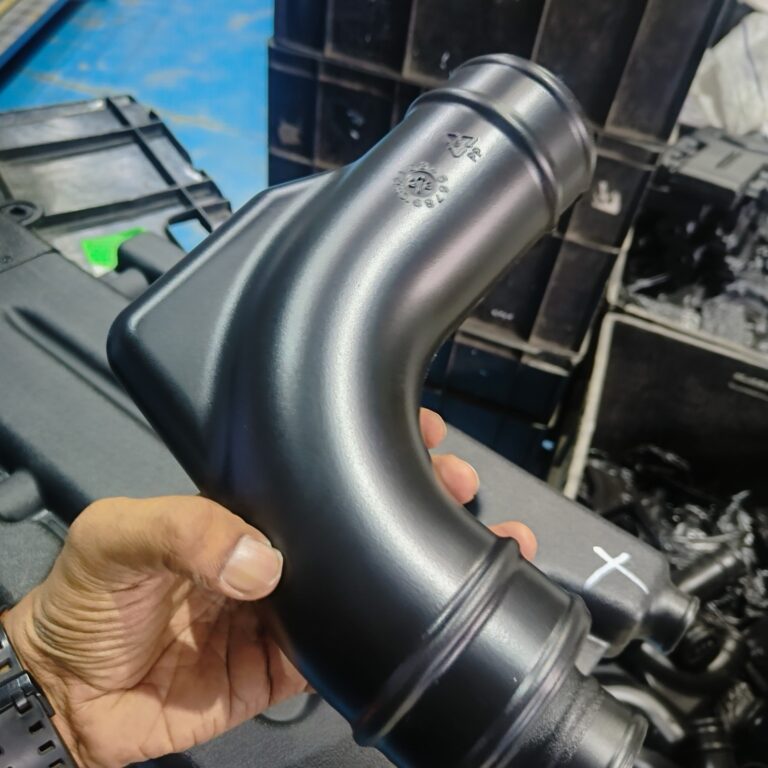
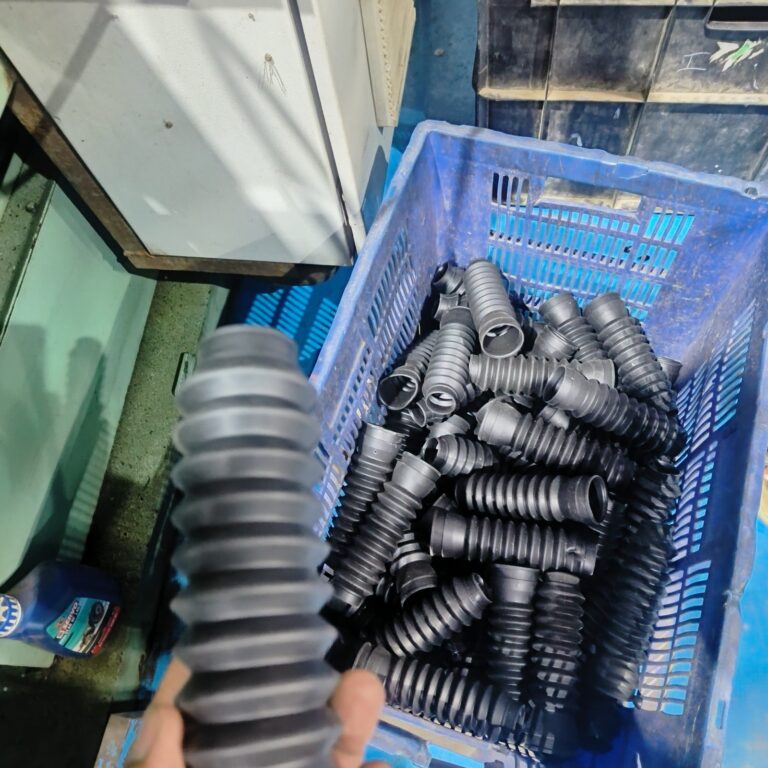
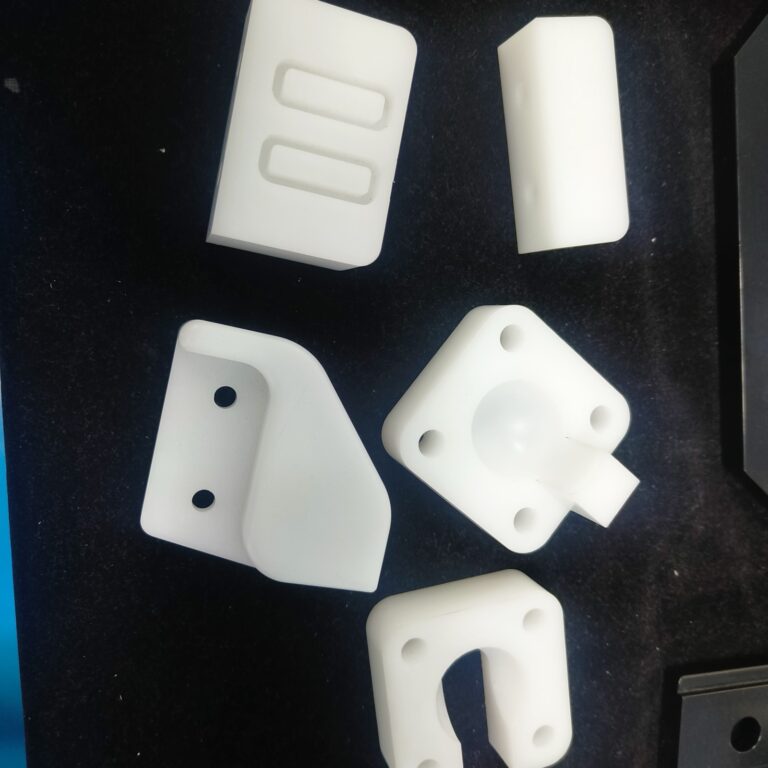
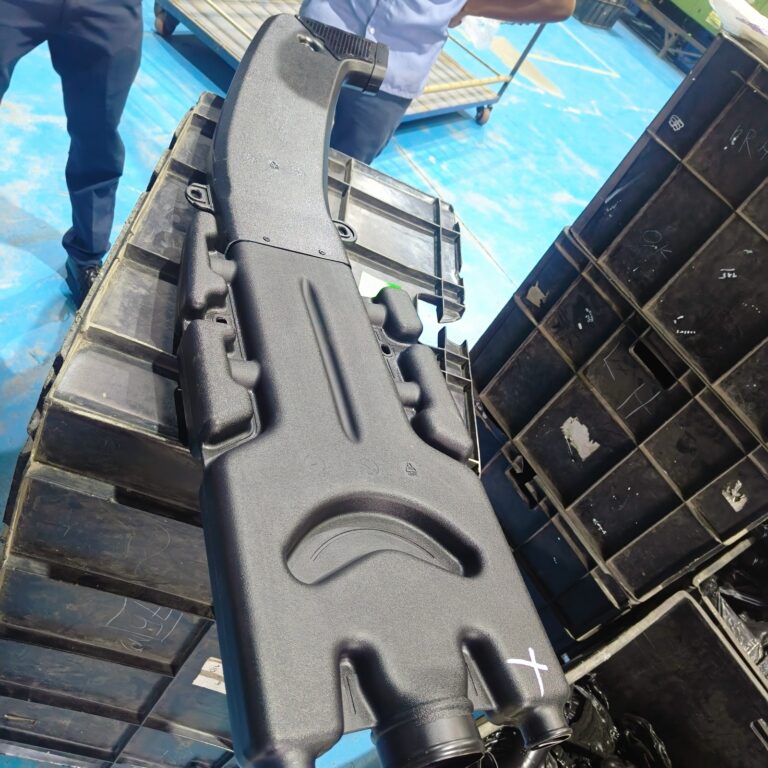
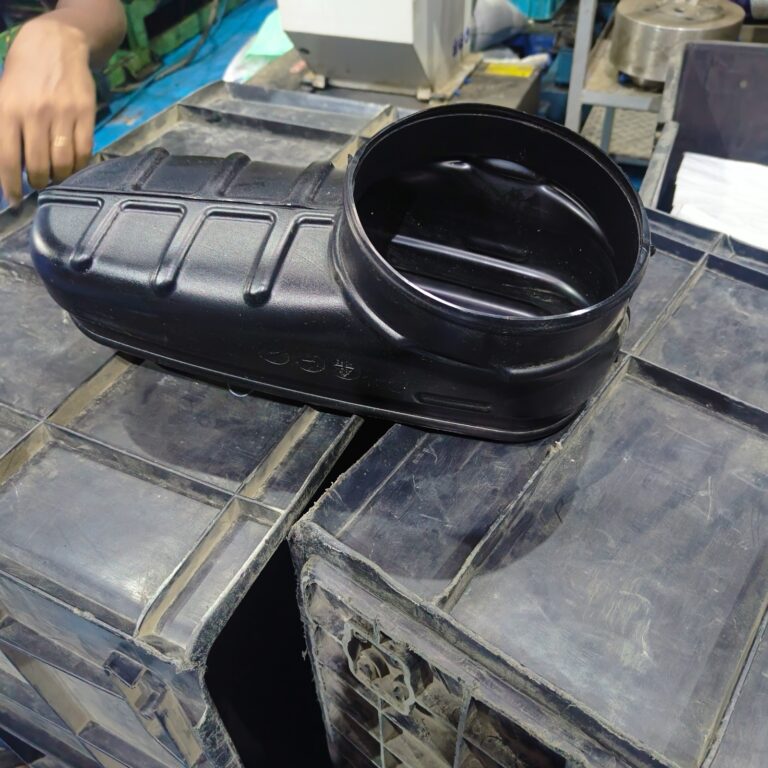
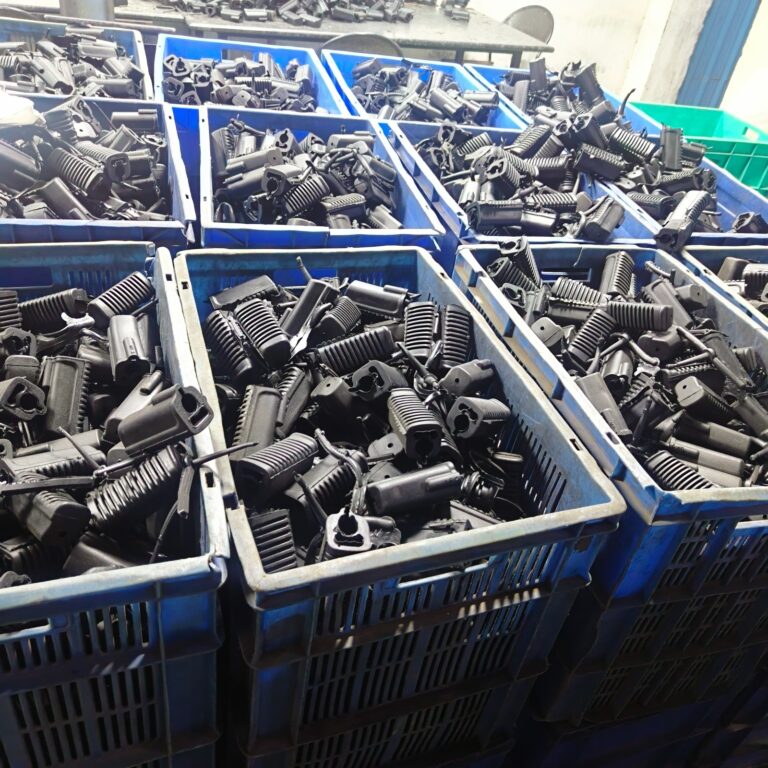
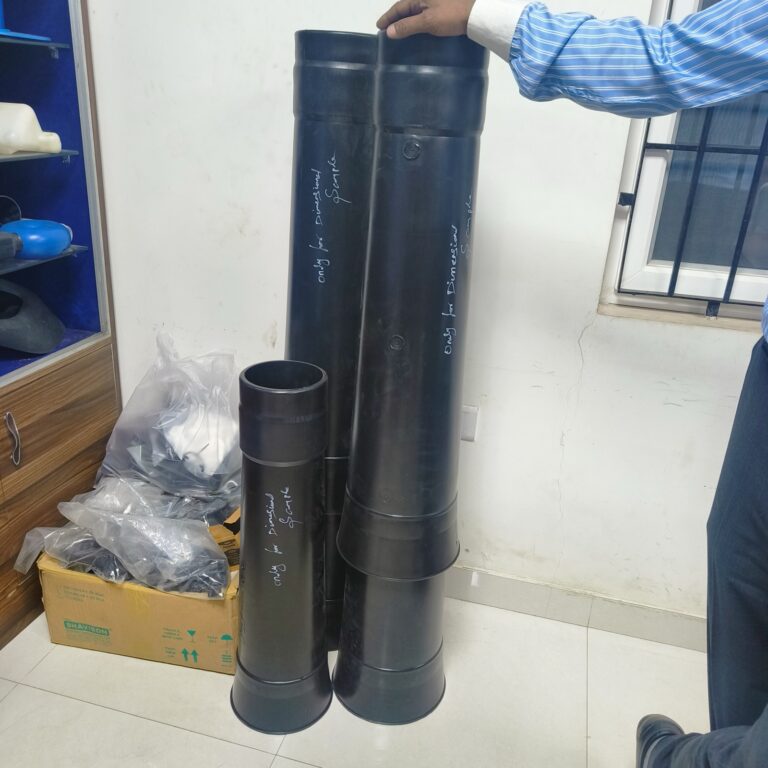
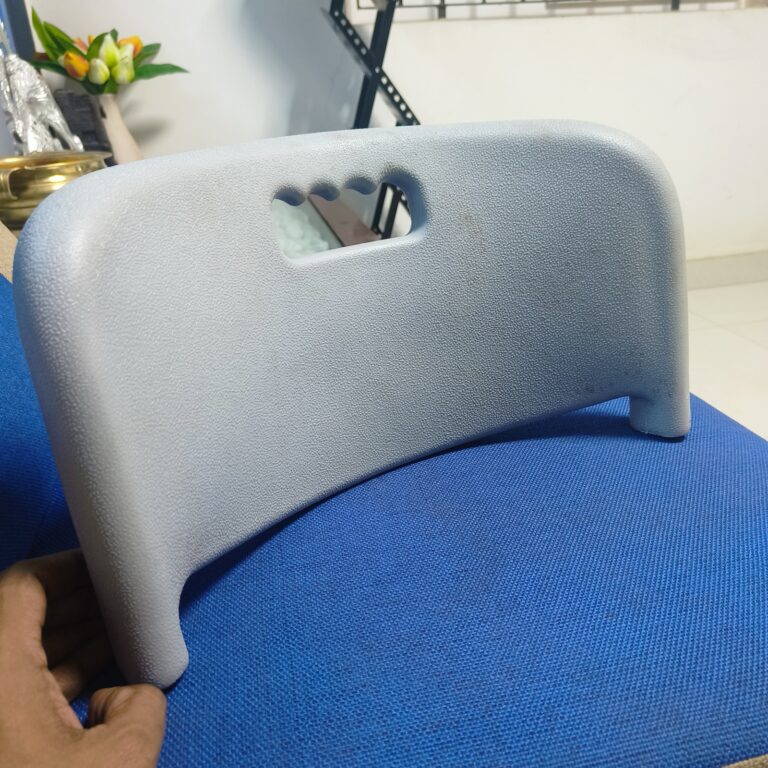
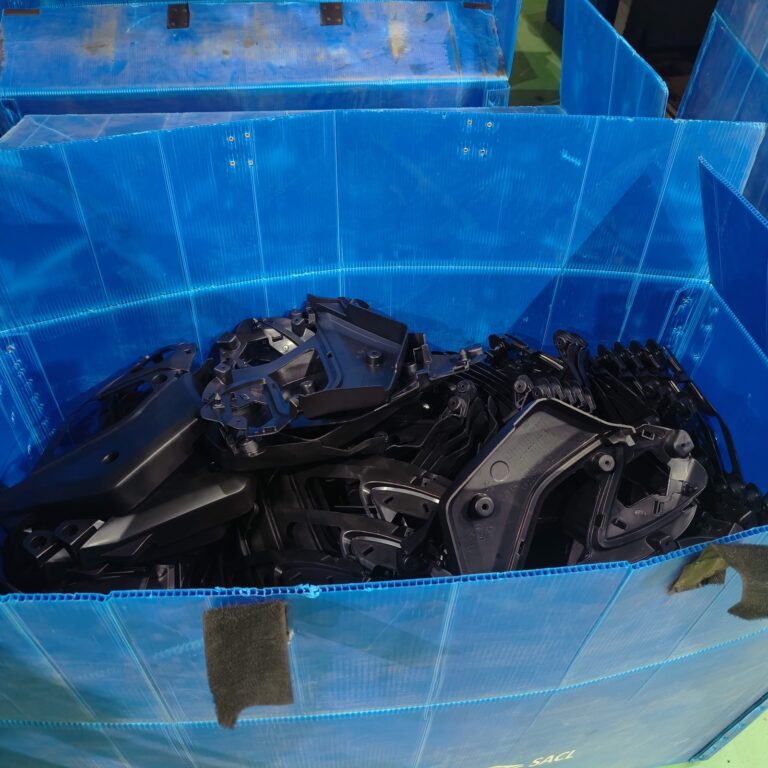
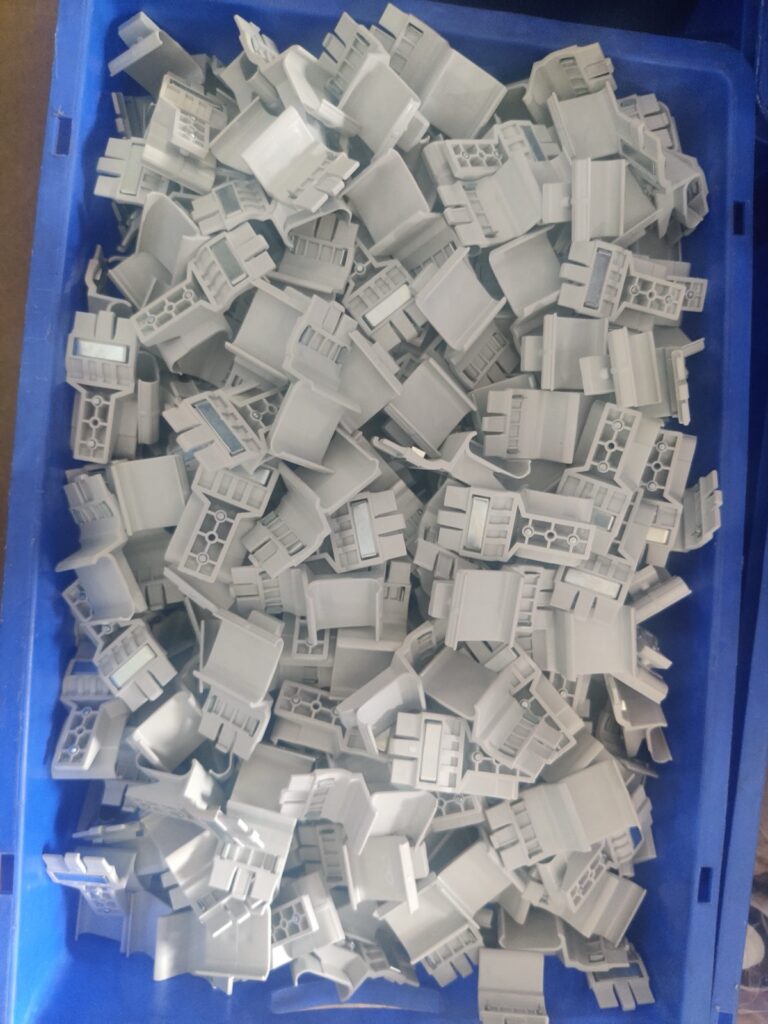
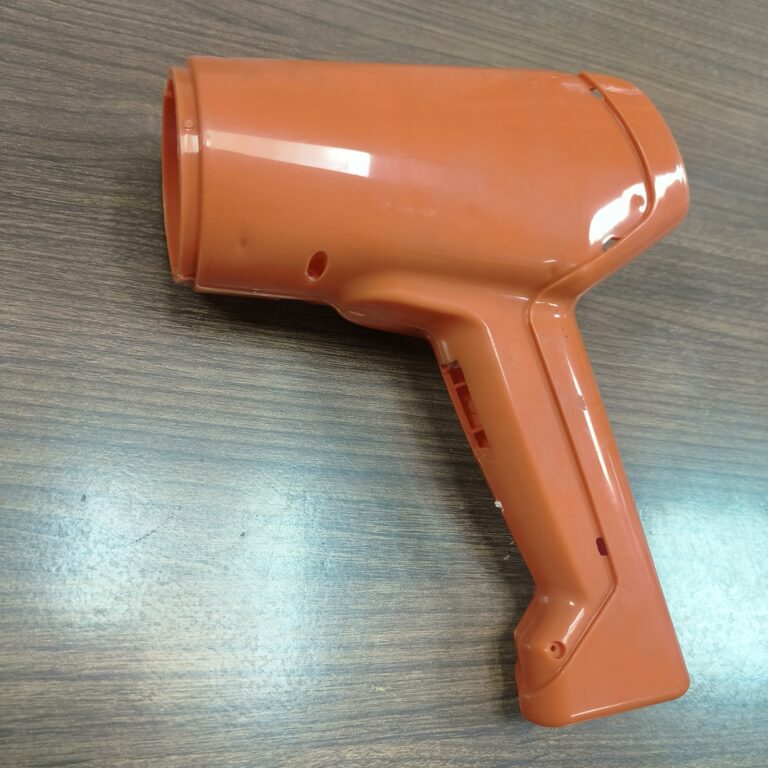
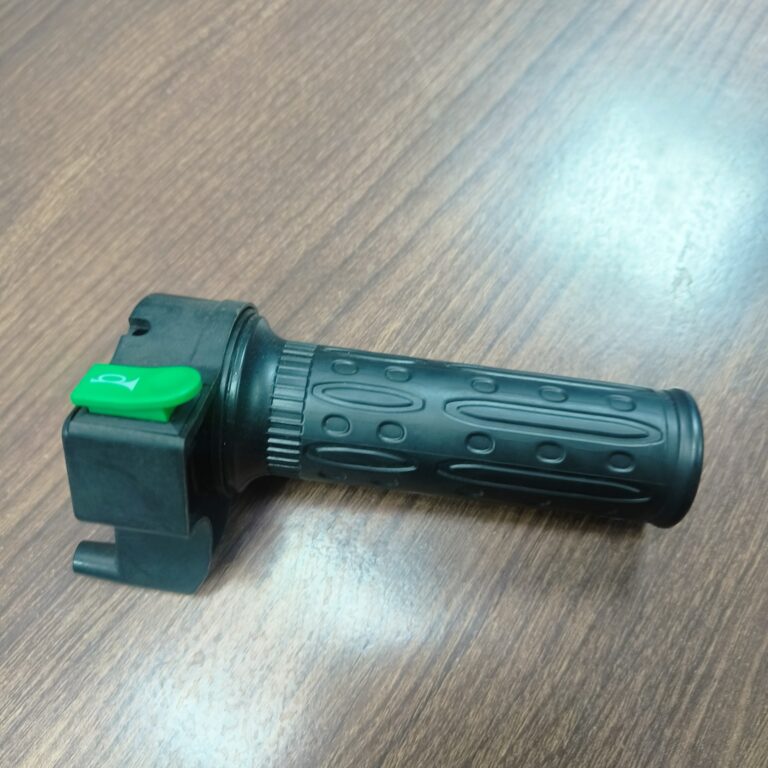
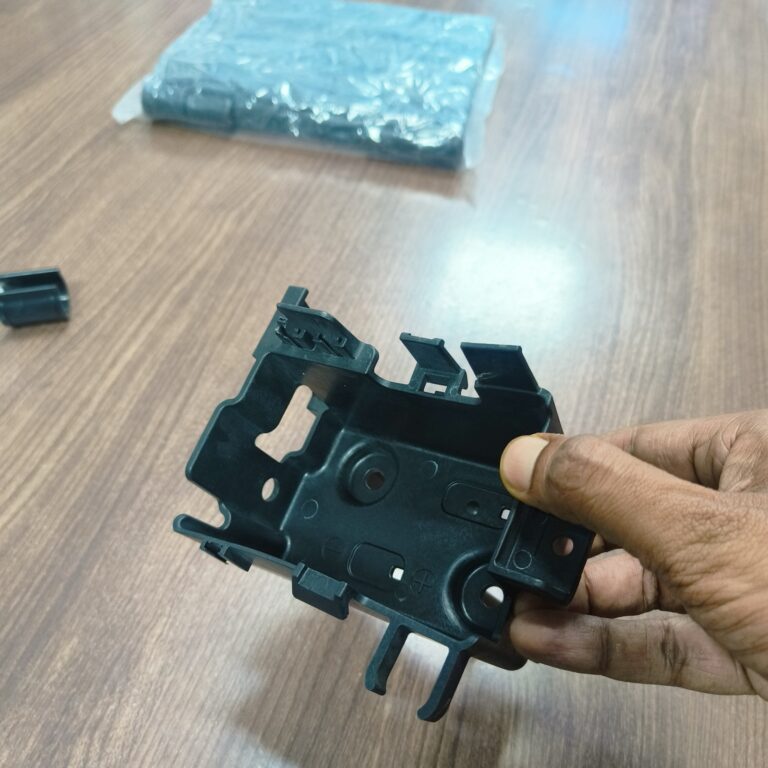
Heavy Fabrication
24000 MT/a
Materials
CS / MS, Alloy steel, Stainless Steel, etc.
Sheet Metal Fabrication
0.8 to 25 mm
Materials
Mild Steel, Stainless Steel, Aluminum, Brass, Copper, etc.


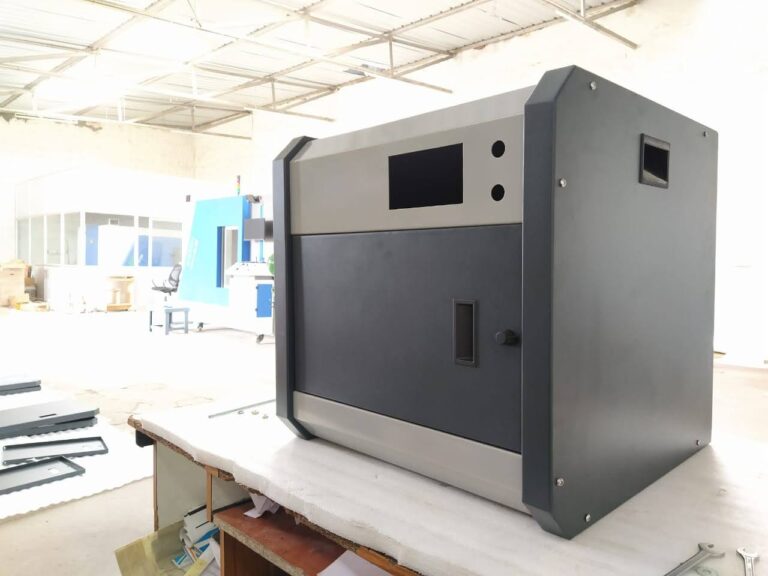


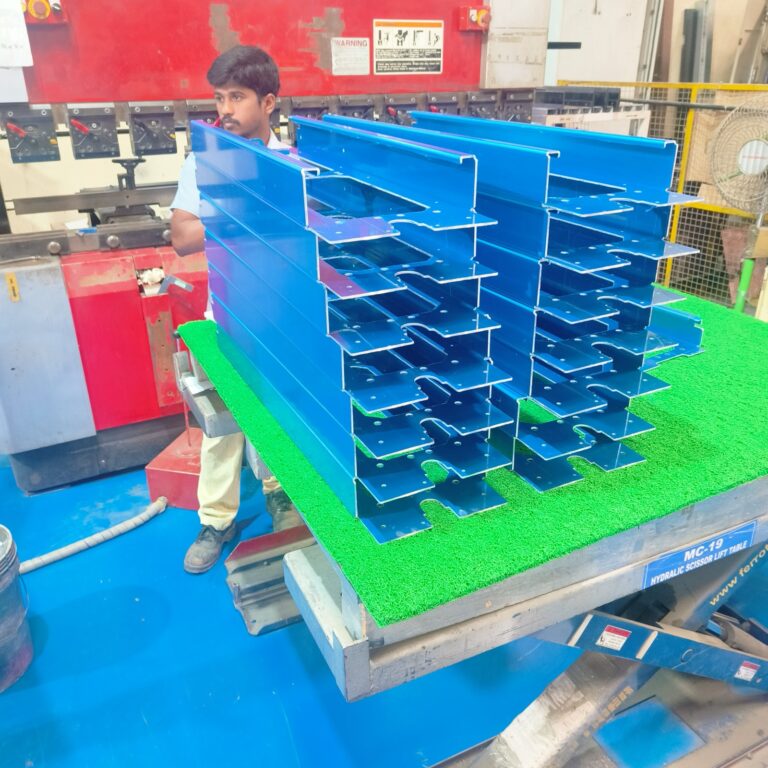
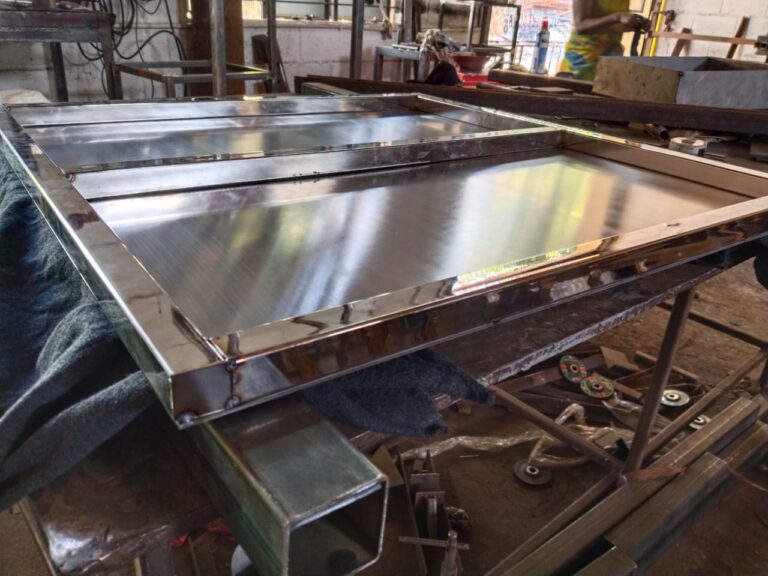
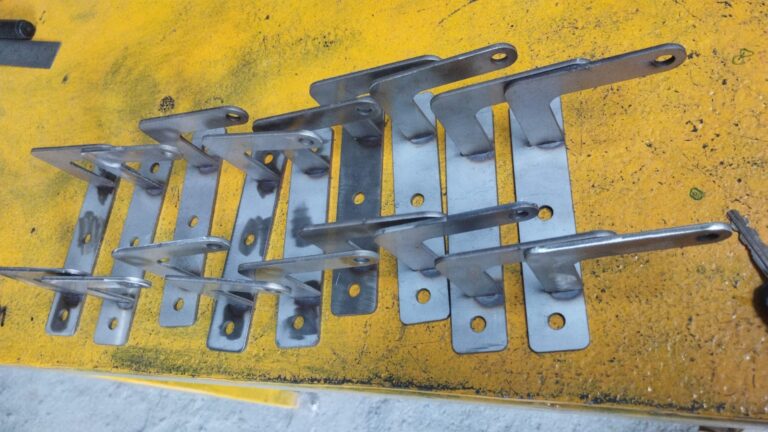
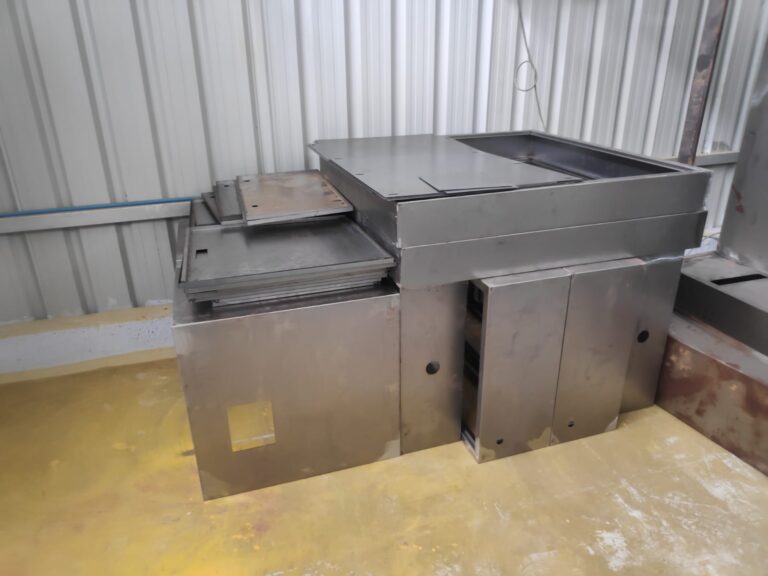
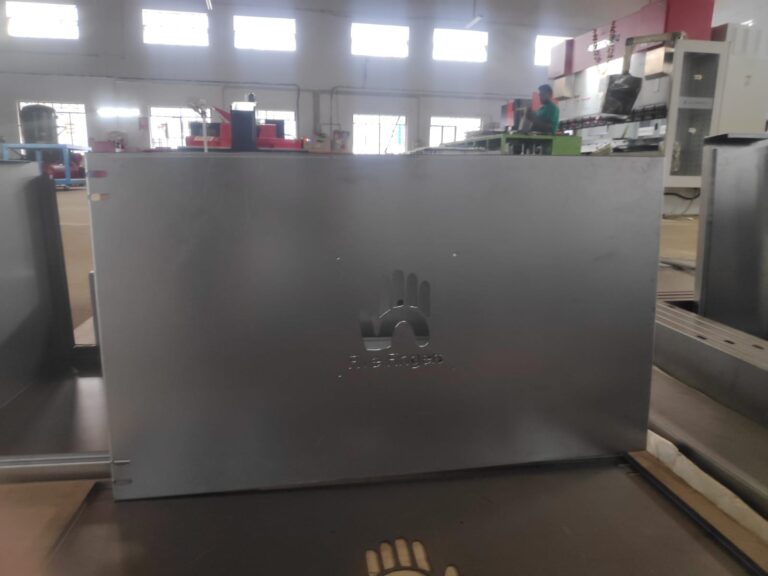
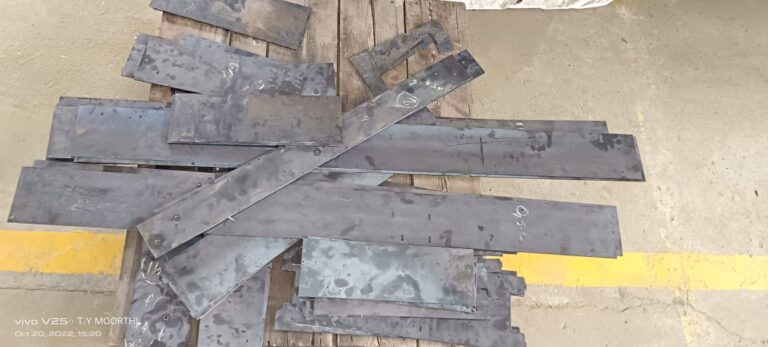
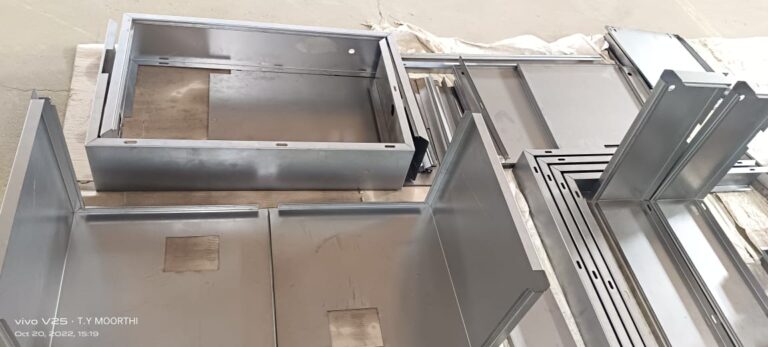
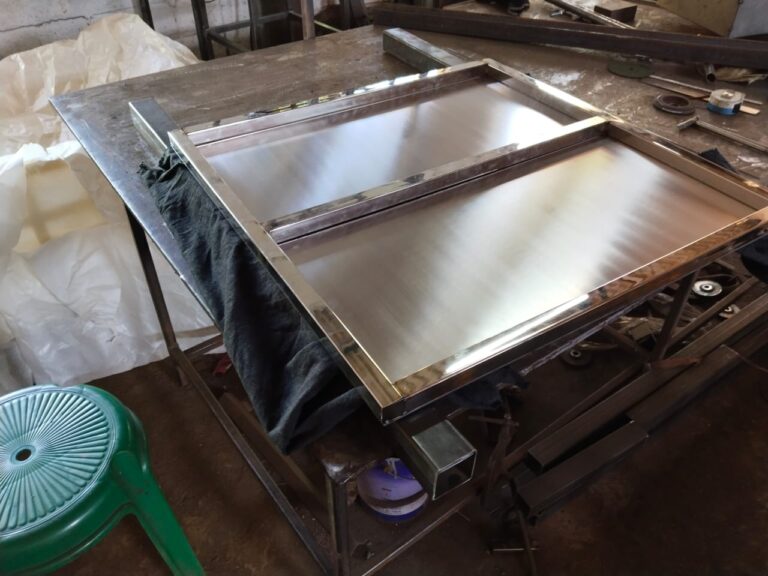
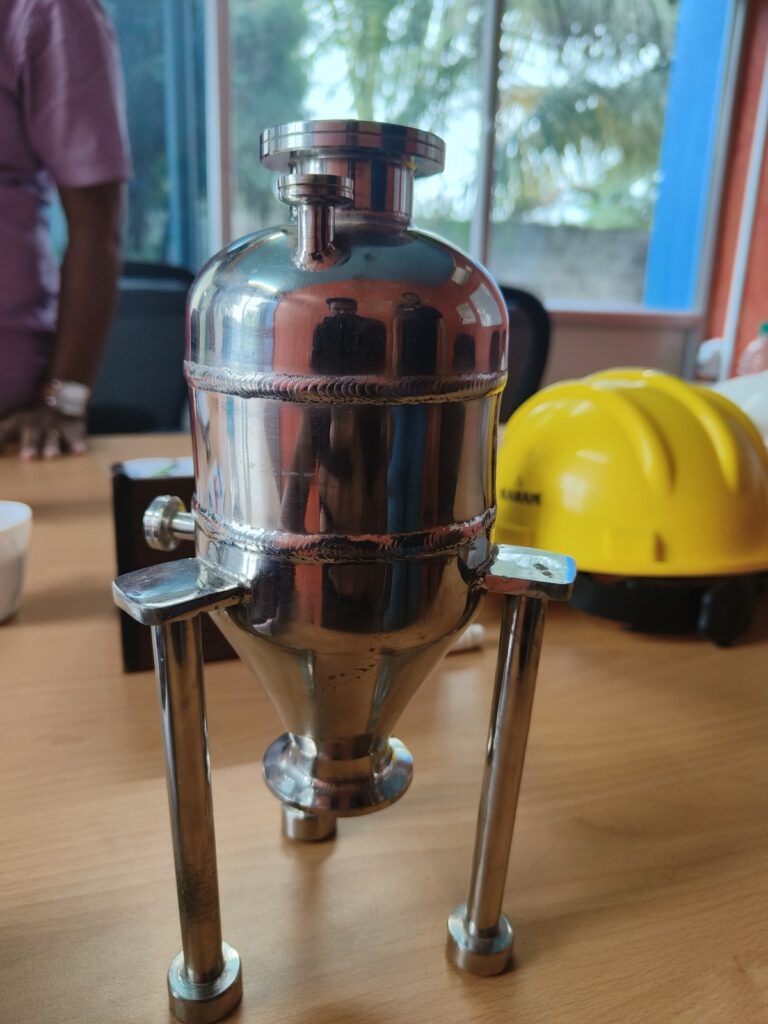
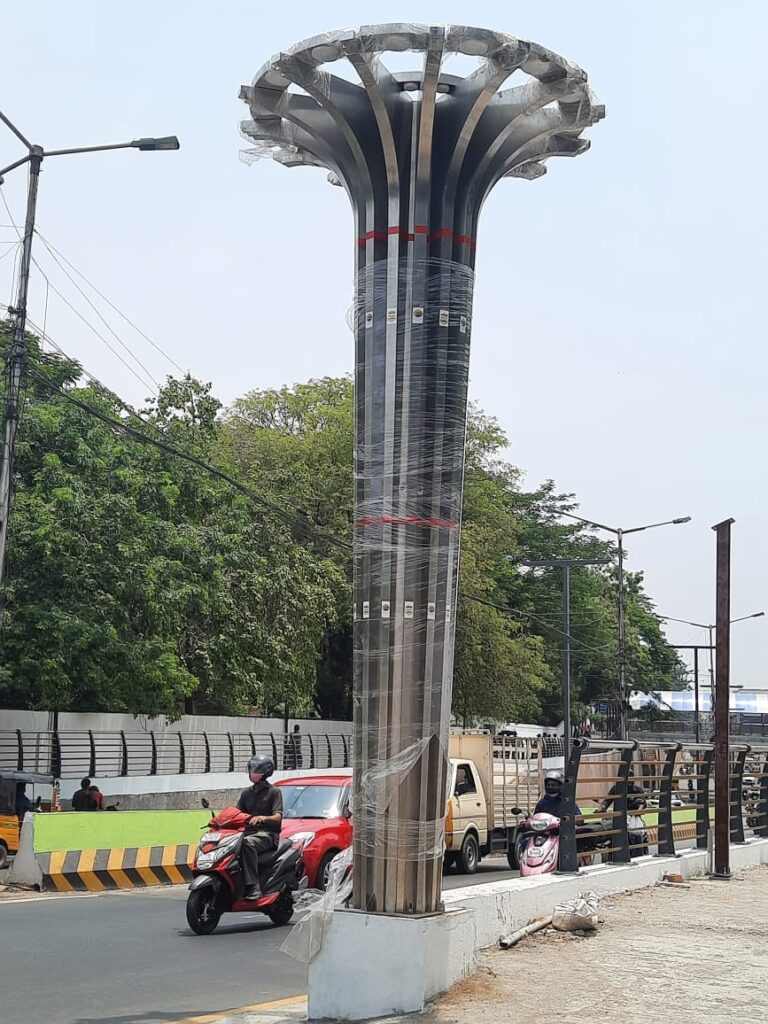
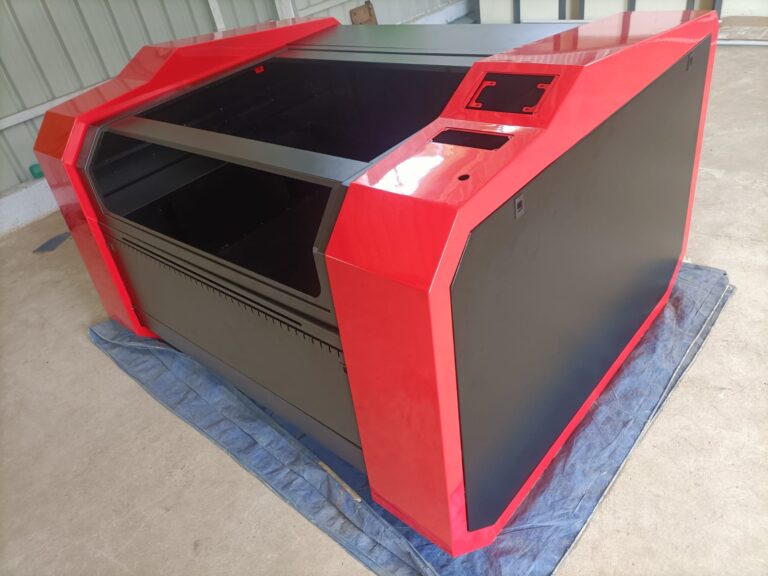
We'd love to Manufacture for you!
Submit the form below and our representative will be in touch shortly.
LOCATIONS
Global Sales Office
818, Preakness lane, Coppell, Texas, USA – 75019
Registered Office
10-A, First Floor, V.V Complex, Prakash Nagar, Thiruverumbur, Trichy-620013, Tamil Nadu, India.
Operations Office
9/1, Poonthottam Nagar, Ramanandha Nagar, Saravanampatti, Coimbatore-641035, Tamil Nadu, India. ㅤ
Other Locations
- Bhilai
- Chennai
- Texas, USA