Extrusion Services
Frigate excels in the precision extrusion of thermoplastic and thermoset materials. Our advanced technology ensures consistent accuracy and high-performance characteristics.
Get Your Quote Now
- Instant Quotation
- On-Time Delivery
- Affordable Cost
Custom Extrusions Tailored to Your Needs
Custom extrusions are tailored to meet specific user requirements. This process involves creating precise shapes for various applications across industries. Frigate is a leading provider of custom extrusions, offering expert guidance and personalized services.
Our team ensures your designs are reusable and optimized for their intended environments. With decades of experience, Frigate meets all your custom extrusion needs with exceptional care and quality.

Minimize Lead Time Challenges
Utilizing a streamlined production schedule helps optimize workflow and minimize delays. This ensures efficient resource use and better alignment with customer timelines.
Implementing effective inventory management practices ensures the availability of essential materials. This reduces lead times by streamlining the procurement process and mitigating material shortages.
Regular updates on production status and potential delays keep customers informed. This proactive approach enhances transparency and allows for better planning on both sides.

Streamline Cost Management Processes
Providing clear and detailed cost breakdowns allows customers to understand pricing structures. This helps them make informed decisions and manage budgets effectively.
Collaborating on design to identify cost-effective alternatives without compromising quality can lead to significant savings. This approach enhances the overall efficiency of the extrusion process.
Implementing lean manufacturing principles reduces waste and enhances efficiency. This continuous improvement approach can lead to lower operational costs, benefiting customers.

Optimize Technical Assistance and Interaction
Offering specialized support throughout the design and production phases ensures customer needs are met accurately. This dedicated approach minimizes misunderstandings and production errors.
Providing consistent communication on project progress keeps customers informed. This allows for timely adjustments and fosters a collaborative relationship.
Delivering detailed documentation on processes and specifications ensures clarity. This comprehensive approach helps customers understand all aspects of the extrusion process, enhancing confidence in the final product.

Extrusion Materials
The extrusion process is a vital method for manufacturing complex shapes. It forces the material through a die to achieve precise dimensions and properties.
Aluminum alloys are widely used in extrusion due to their lightweight and high strength-to-weight ratio. Common alloys, such as 6061 and 6063, offer excellent corrosion resistance and good machinability, making them suitable for various applications, including automotive and construction.
Copper alloys, including brass and bronze, are also suitable for extrusion. They provide good electrical and thermal conductivity. Applications often include electrical components and plumbing fixtures, where conductive properties are essential.
Thermoplastics, such as polyethylene (PE), polypropylene (PP), and polyvinyl chloride (PVC), are frequently extruded into various shapes. These materials are known for their versatility and durability, making them ideal for packaging, construction, and automotive applications.
Carbon and stainless steel can be extruded to produce components that require high strength and durability. Steel extrusion is commonly used in construction, automotive, and heavy machinery applications, where structural integrity is critical.
Magnesium alloys offer a lightweight alternative for high-strength and low-density applications. Their use in aerospace and automotive industries is increasing, as they contribute to weight reduction without compromising performance.
Zinc alloys are also used in extrusion, particularly for applications that require corrosion resistance. They are often used in die-casting processes but can also be extruded for specific components.
Composite materials can be extruded to achieve tailored properties by combining different substrates. These materials can enhance performance, offering benefits such as increased strength, reduced weight, and improved thermal resistance.
Certain applications may require specialty alloys, such as titanium or high-strength aluminum alloys. Depending on the specific application requirements, these materials are selected for their unique properties, such as high-temperature resistance or enhanced mechanical strength.
Enhancing Efficiency in Post-Extrusion Processing
After extrusion, additional processing steps are often required to meet final product specifications. These steps may include machining, finishing, and assembly, which enhance functionality and appearance. Machining removes material to achieve precise dimensions, while finishing processes, such as anodizing and polishing, improve surface properties and visual appeal.
Coordinating these processes can be complex and may lead to increased costs and longer timelines. Effective communication between extrusion and post-processing teams is essential for minimizing delays. Frigate supports the management of these processes, optimizing machining, finishing, and assembly to efficiently meet specific customer requirements.

- Real Impact
Words from Clients
See how global OEMs and sourcing heads describe their experience with our scalable execution.
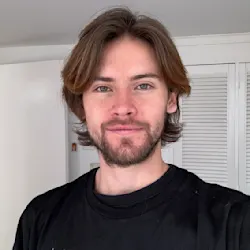
“Quick turnaround and solid quality.”
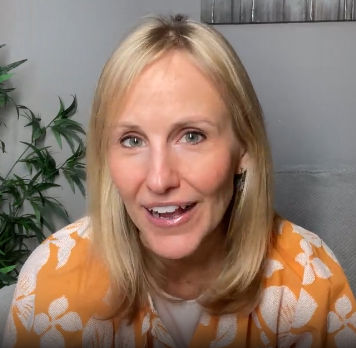
“The instant quote tool saved us time, and the parts were spot-on. Highly recommend Frigate!”
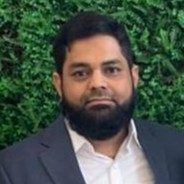
“I would strongly recommend Frigate to anyone who wants to do Rapid Prototyping, and take their ideas to manufacturing. One firm doing all kinds of Product Development!”
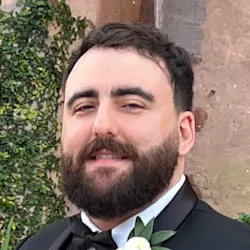
“Great service, fair price, and the parts worked perfectly in our assembly.”
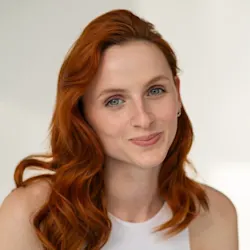
“Top-notch machining and fast shipping. Very satisfied with the results.”
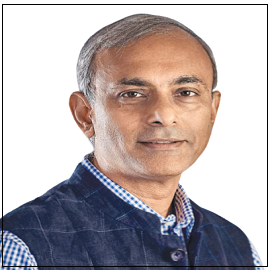
“The next disruption is happening in Prototyping & Manufacturing on-demand and Frigate is leading the way! I personally believe the Frigate's way of IIOT enabled cloud platform with Al.”
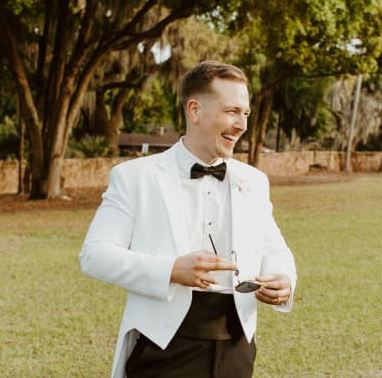
“Frigate delivered high-quality parts at a competitive price. The instant quote tool is a huge plus for us!”

“We appreciate the precision and quality of the machined components in the recent delivery—they meet our specifications perfectly and demonstrate Frigate’s capability for excellent workmanship.”
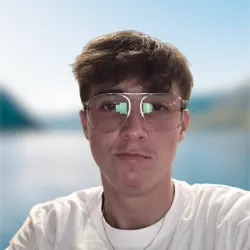
“Flawless execution from quote to delivery.”

“I am absolutely happy to work with supplier like Frigate who were quite proactive & result oriented . Frigate has high willingness team who has strong know how & their passion towards the products & process were absolutely thrilling.”
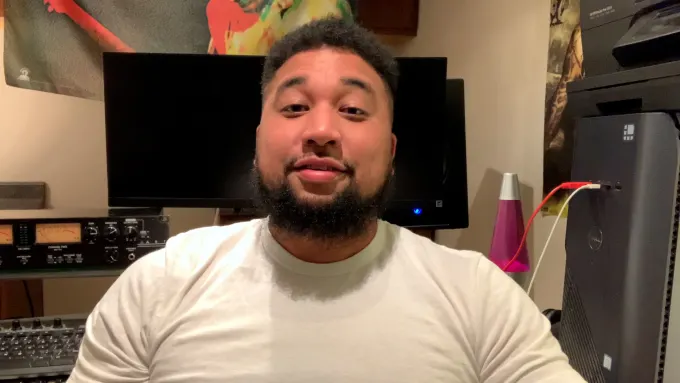
“The precision on these parts is impressive, and they arrived ahead of schedule. Frigate’s process really stands out!”
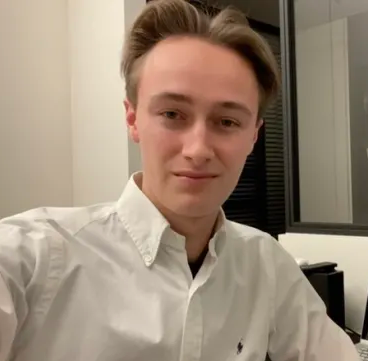
“Parts were exactly as spec’d, and the instant quote made budgeting a breeze.”
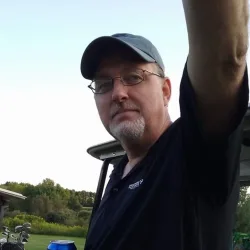
“Good value for the money.”
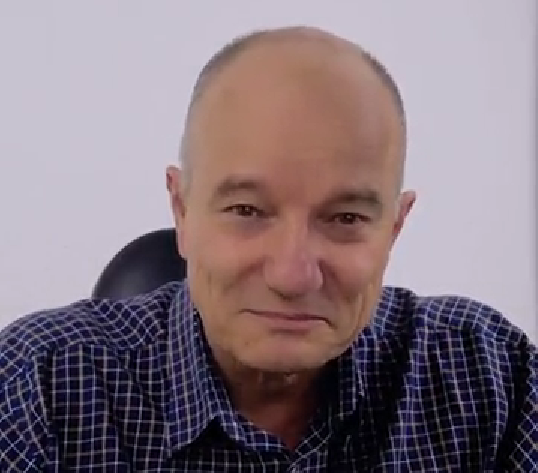
“The finish was perfect, and the team was easy to work with.”

“Working with Frigate has been great. Their proactive, results-driven approach and expertise shine through in every project. It's been a pleasure collaborating with them.”

"We are highly satisfied with the timely delivery and quality of the MIG Welding Cable from Frigate. Their attention to detail, secure packaging, and quick responsiveness stood out. We confidently recommend Frigate Engineering Services Pvt. Ltd. as a reliable manufacturing partner."
Having Doubts? Our FAQ
Check all our Frequently Asked Question
Frigate employs precise die design and advanced extrusion techniques to maintain tight tolerances. This minimizes variation in dimensions, ensuring that each profile meets customer specifications consistently.
Frigate implements rigorous quality control processes during extrusion. This includes real-time monitoring of temperature, pressure, and material flow, along with thorough inspections to identify and rectify defects early in production.
Frigate coordinates closely with customers to streamline post-extrusion processes like machining and finishing. By managing these steps effectively, Frigate helps reduce lead times and ensure that final products meet specific functional and aesthetic requirements.
Frigate offers expertise in selecting appropriate aluminum alloys based on application needs. For example, 6061 alloy is ideal for structural applications, while 6063 is better suited for architectural features due to its excellent finish and workability.
Frigate maintains transparent communication about material costs and potential changes during the extrusion process. By providing detailed cost estimates and alternatives, Frigate helps customers manage budgets effectively while ensuring high-quality outcomes.
Manufacturing Capability/Capacity
Ferrous casting
Mold size(max): 1m X 1m
Weight Range: 1 KG ~ 30 KGS
Mold size(max): 1.5m X 1.5m
Weight Range: 30 KG ~ 150 KGS
Mold size(max): 3m X 3m
Weight Range: 100 KG ~ 1000 KGS
Mold size(max): 500 MM X 500 MM
Weight Range: 0.250 KG ~ 20 KGS
Mold size(max): 500 MM X 500 MM
Weight Range: 0.100 KG X 20 KGS
Non-ferrous casting
Capacity: 5000 MT/a
Range of weight: 100 gm to 20 KGS
Mold size(max): 1 M X 1 M
Weight Range: 0.5 KG X 50 KGS
Mold size(max): 1 M X 1 M
Weight Range: 0.5 KG X 50 KGS
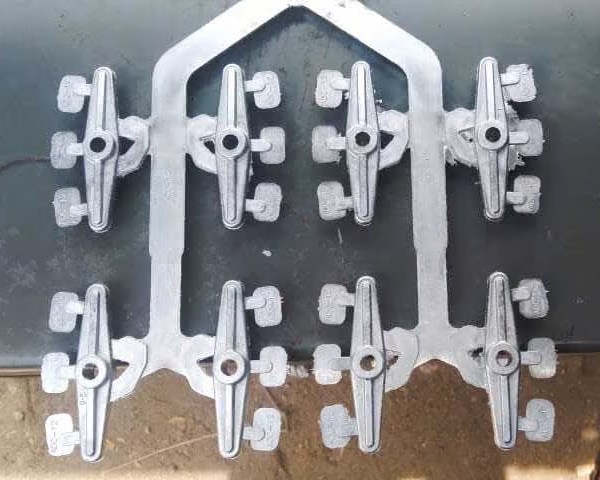
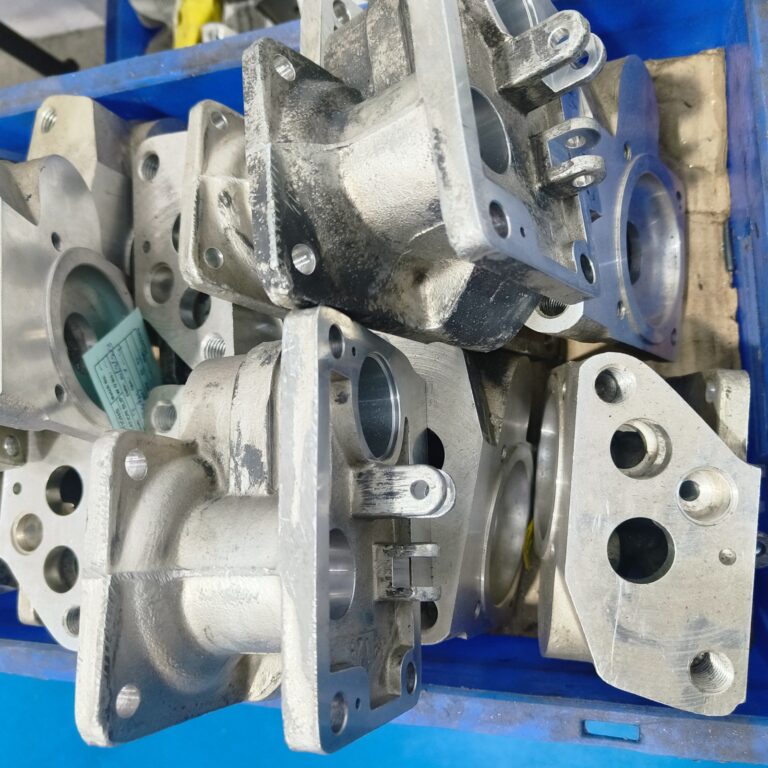
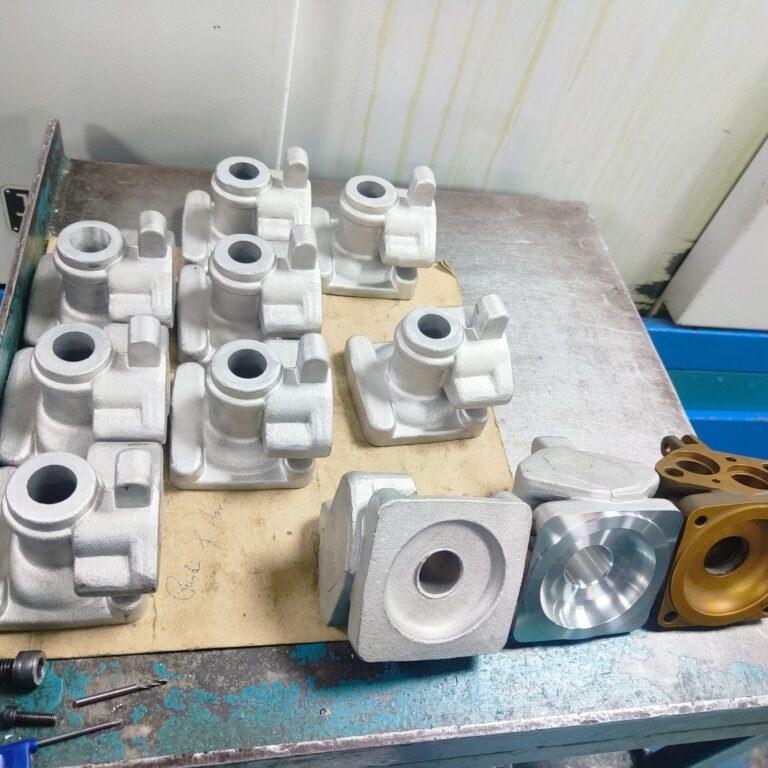
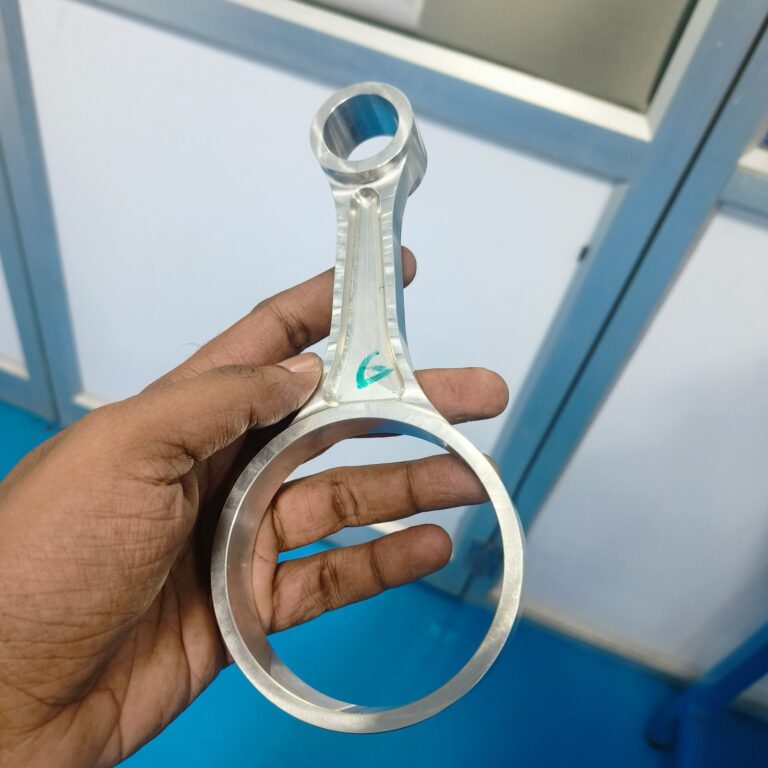
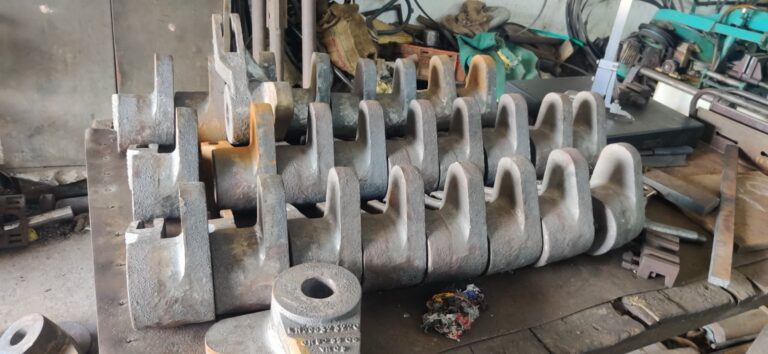
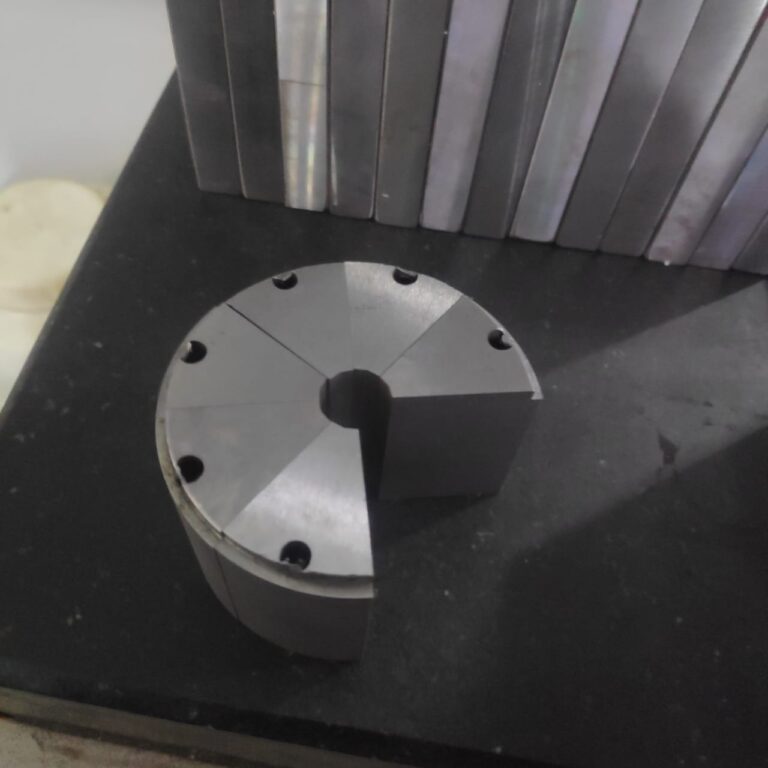
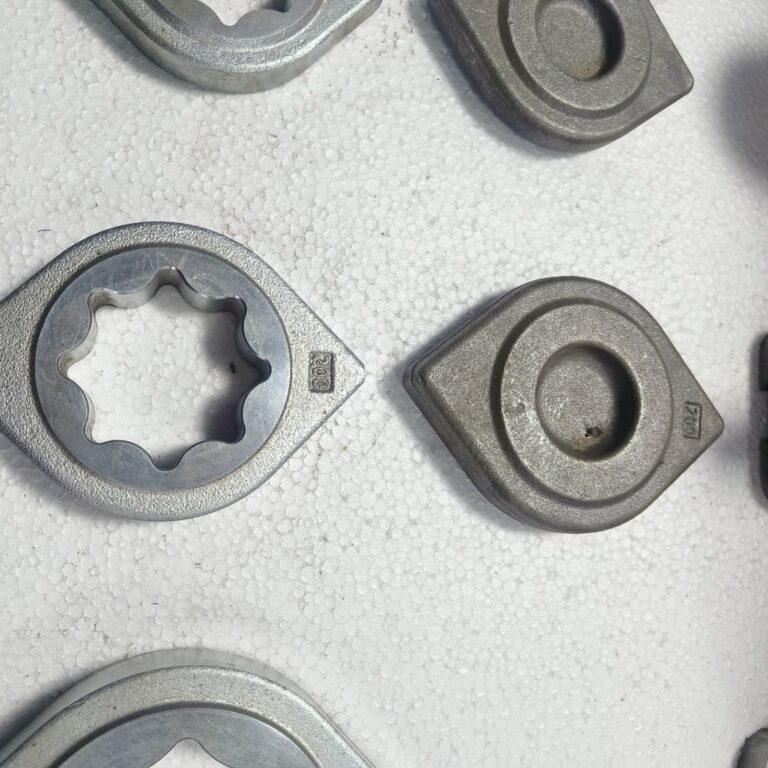
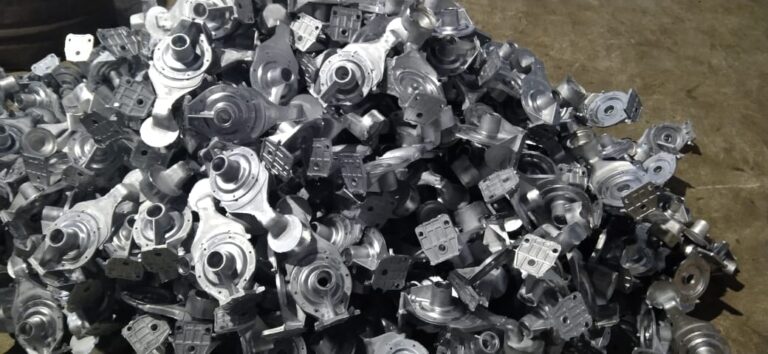
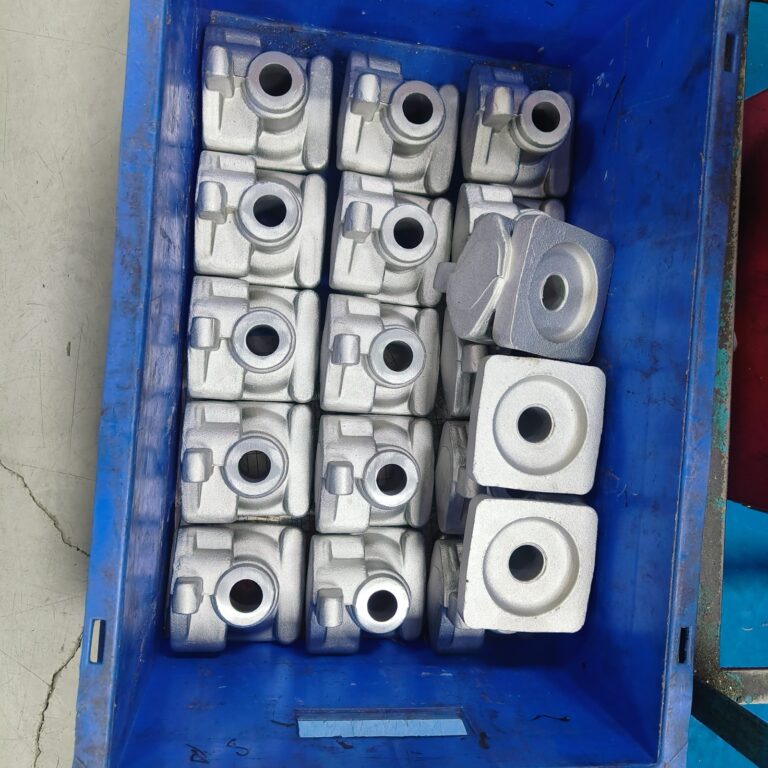
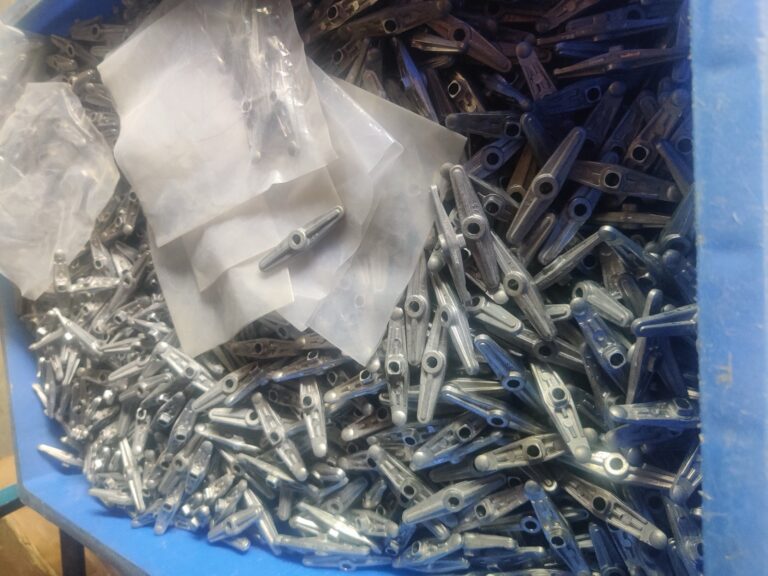
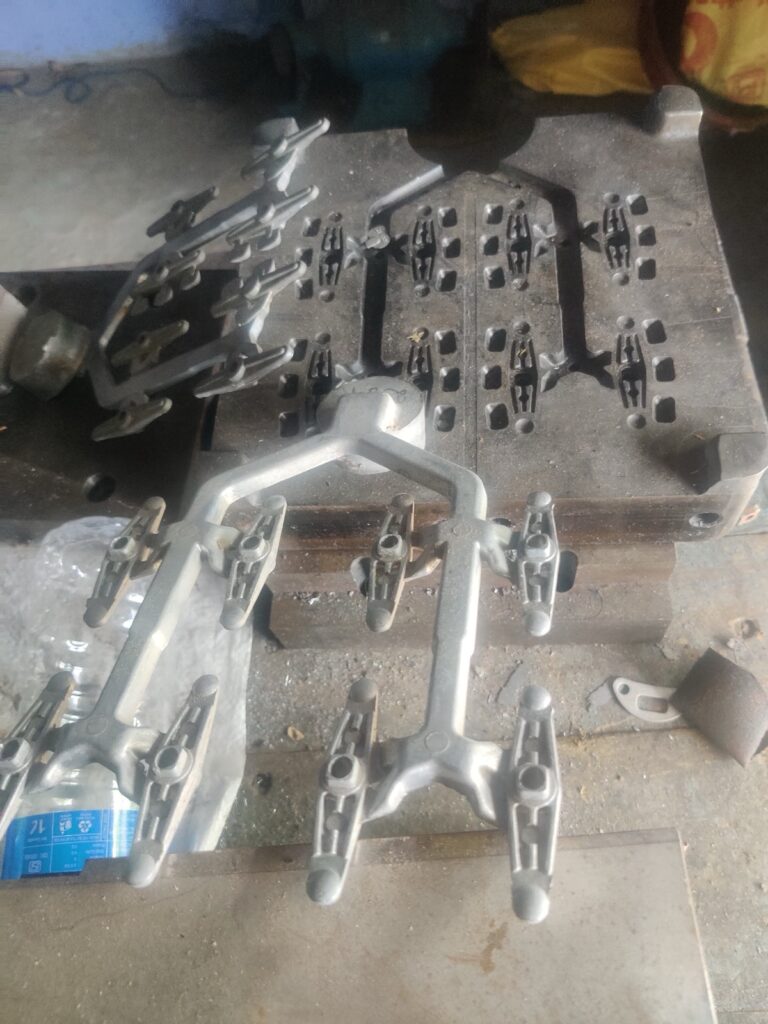
Forging
Capacity: 20,000 Tons per Annum
Range of weight: 300 KG to 1 Ton
Hammering: 5 Ton
Range of weight: 0.2 KG to 200 KGS
Hammering: 1600 Ton Hydraulic press
Ring size: 350 MM OD to 3000 MM OD
Range of weight: 15 KGS to 3200 KGS
Materials
Carbon Steel, Stainless Steel (AUSTENITE), Alloy Steel, Stainless Steel (MARTENSITE), etc.
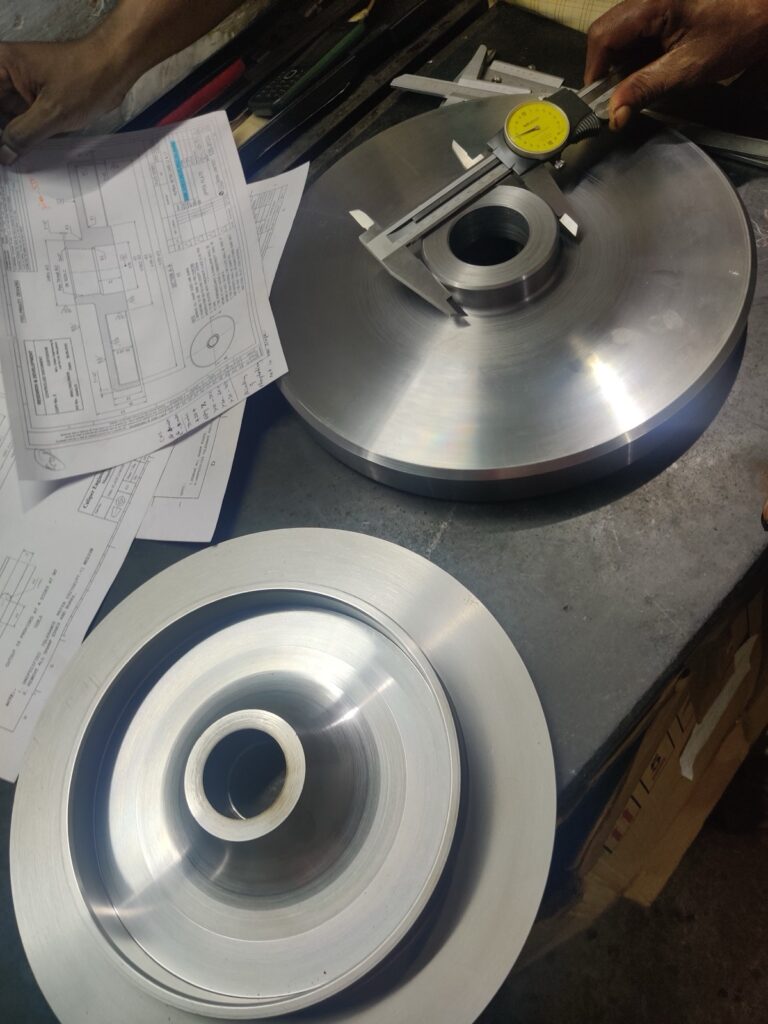
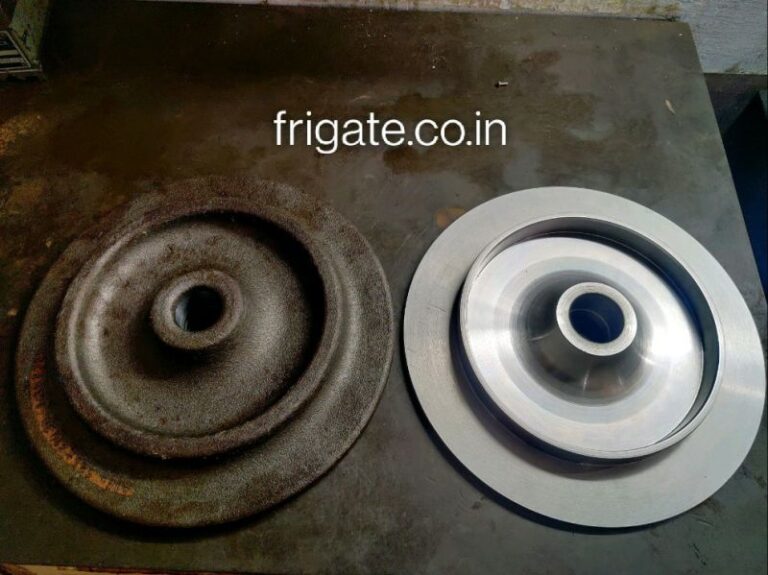
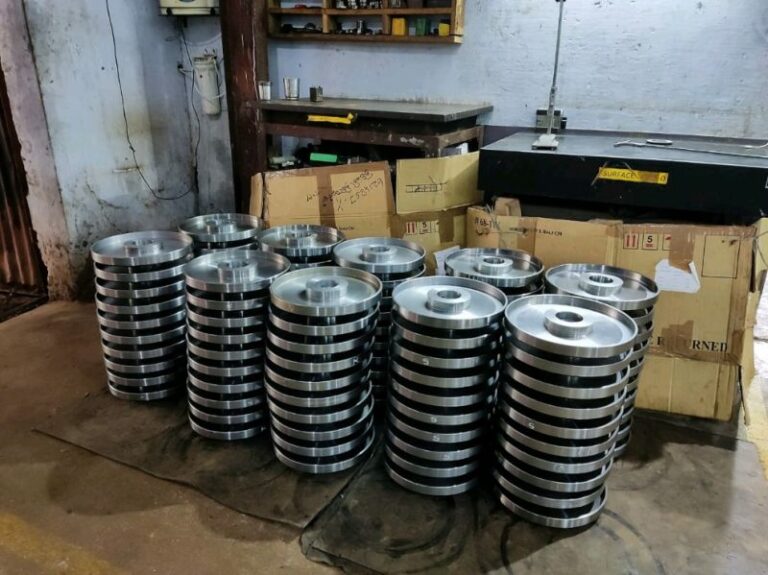
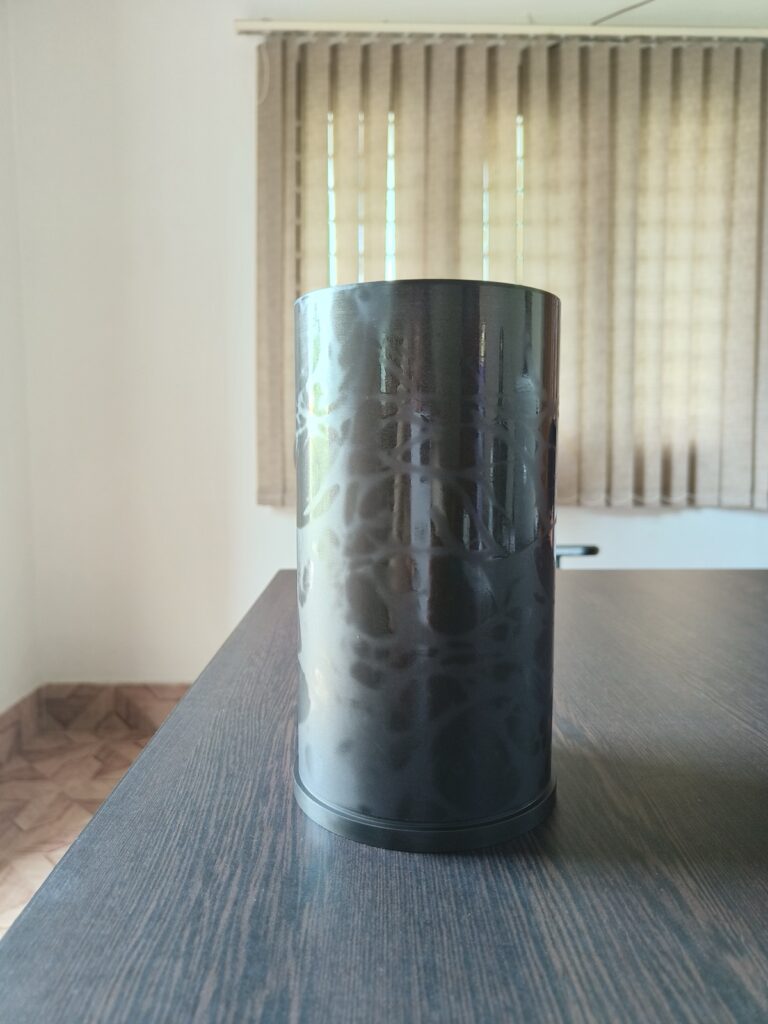
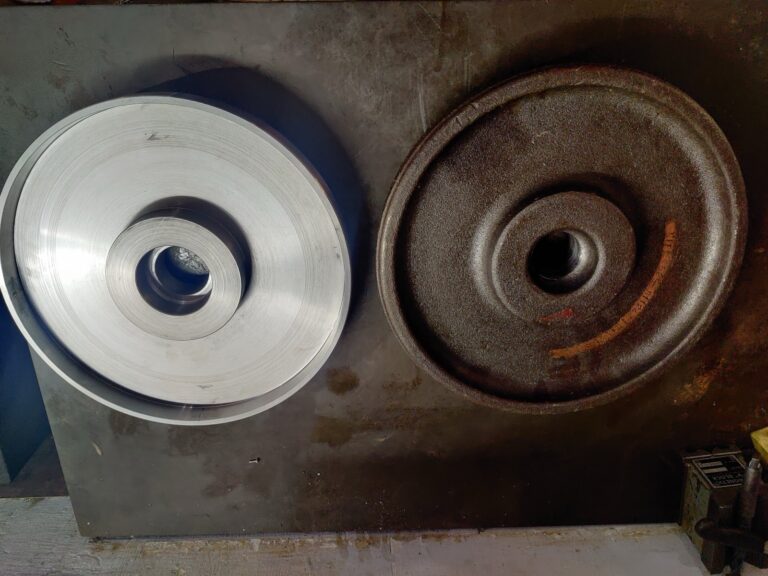
Machining
1 to 1000 MM
1 to 1000 MM
1 to 1000 MM
Materials
Steel, Aluminum, Brass, Copper, Titanium, Nickel Alloys, Tungsten Carbide, etc.
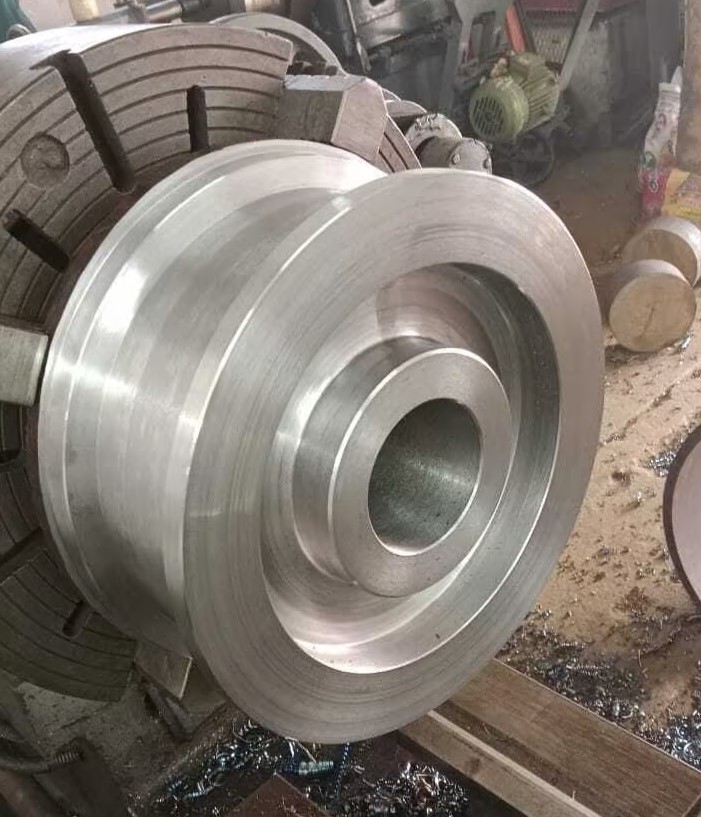
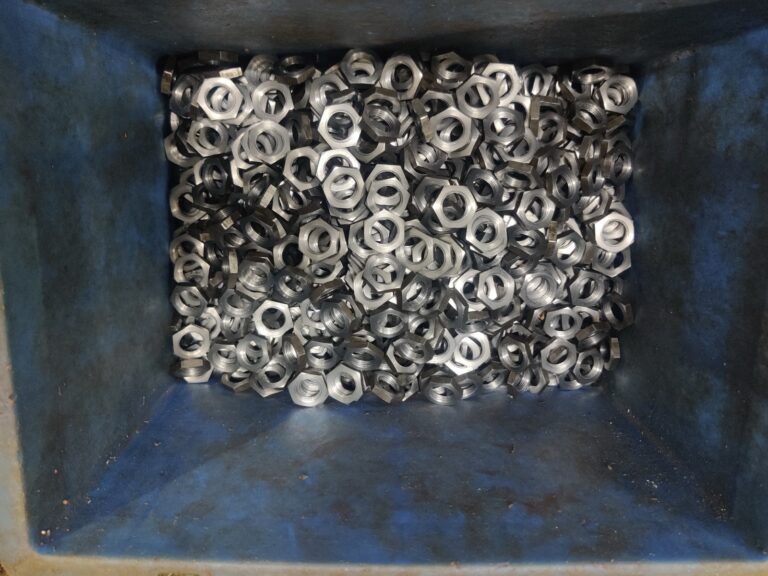
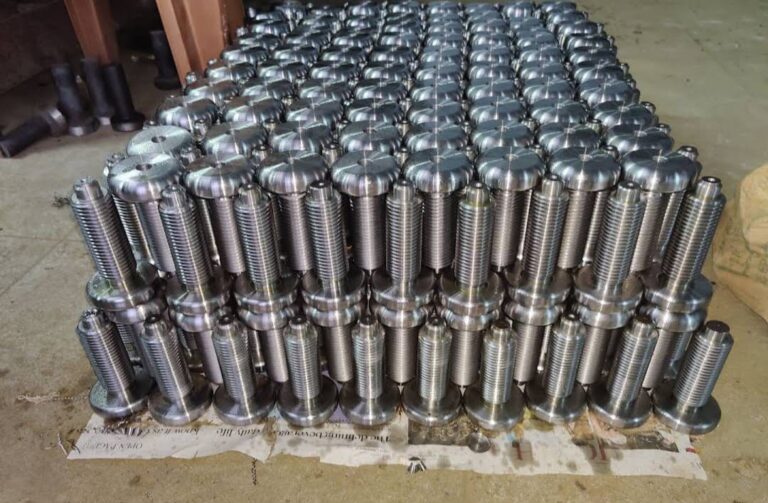
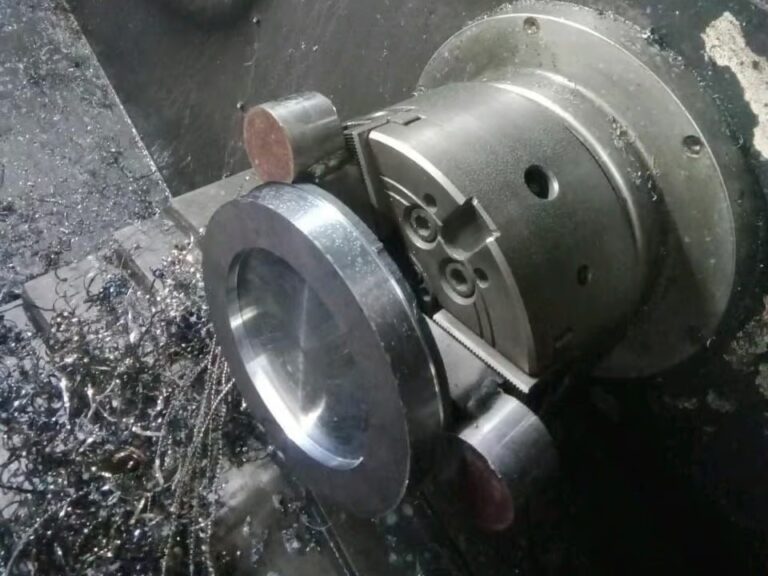
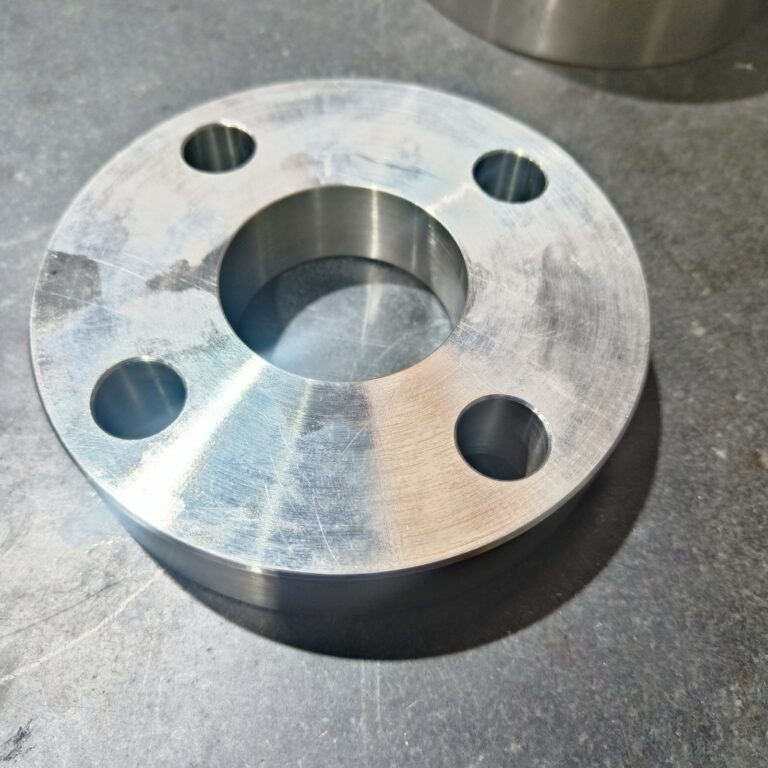
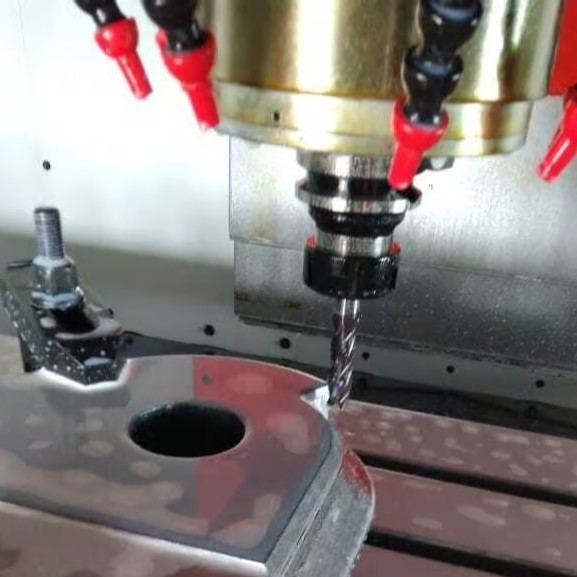
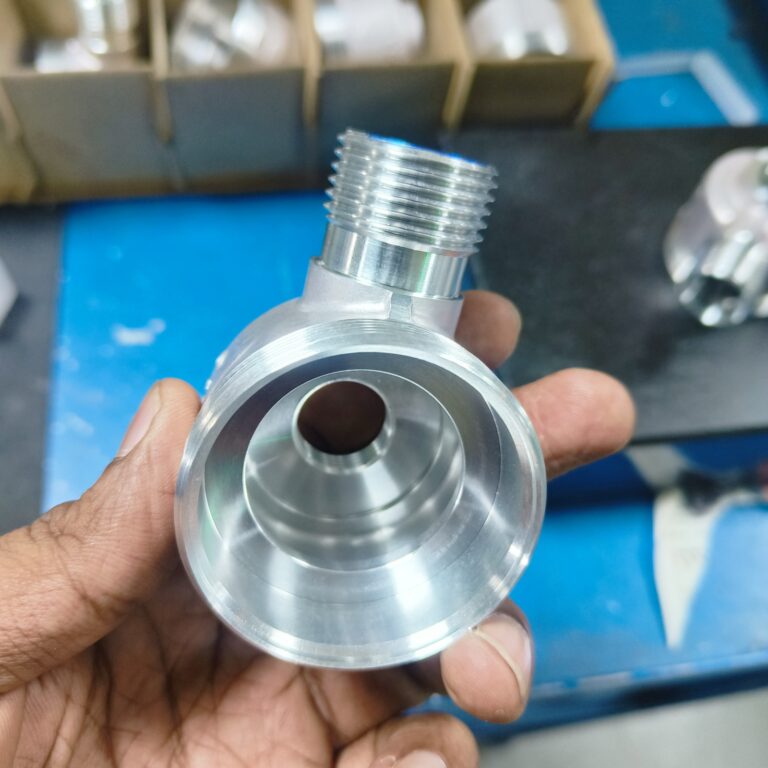
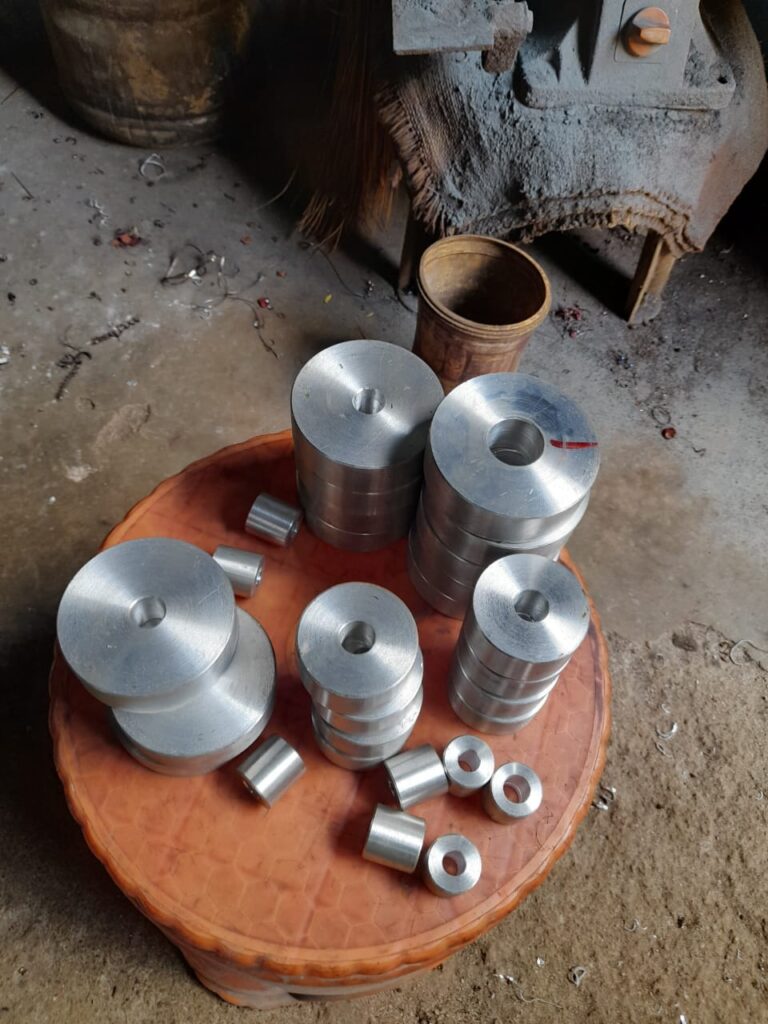
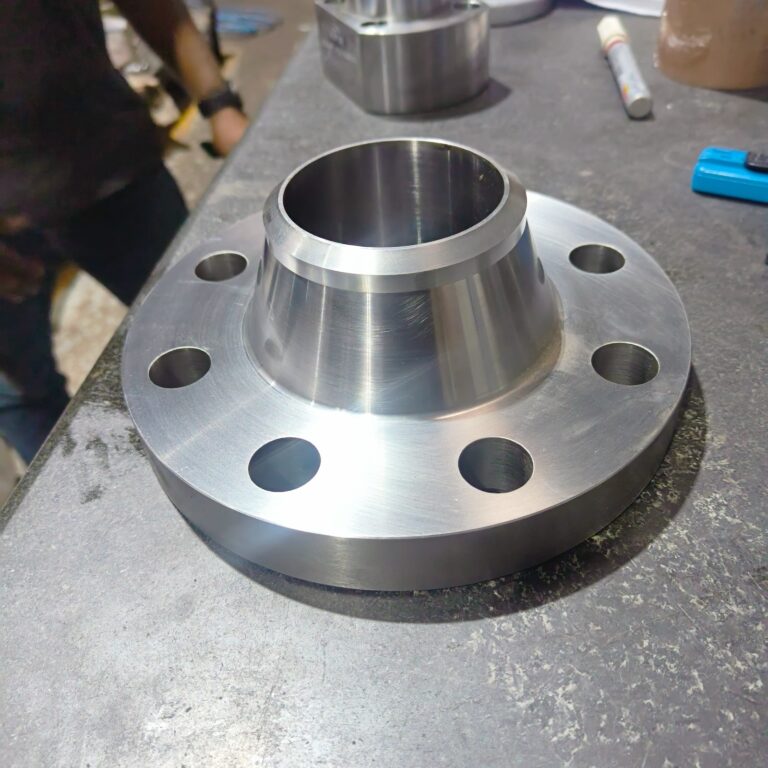
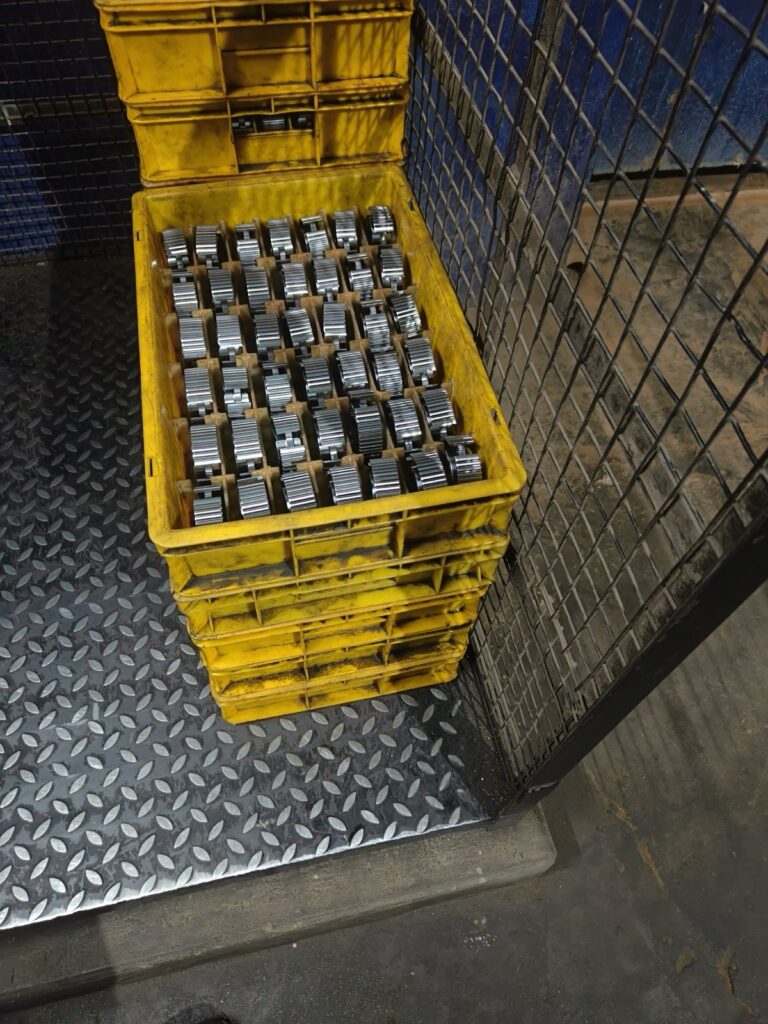
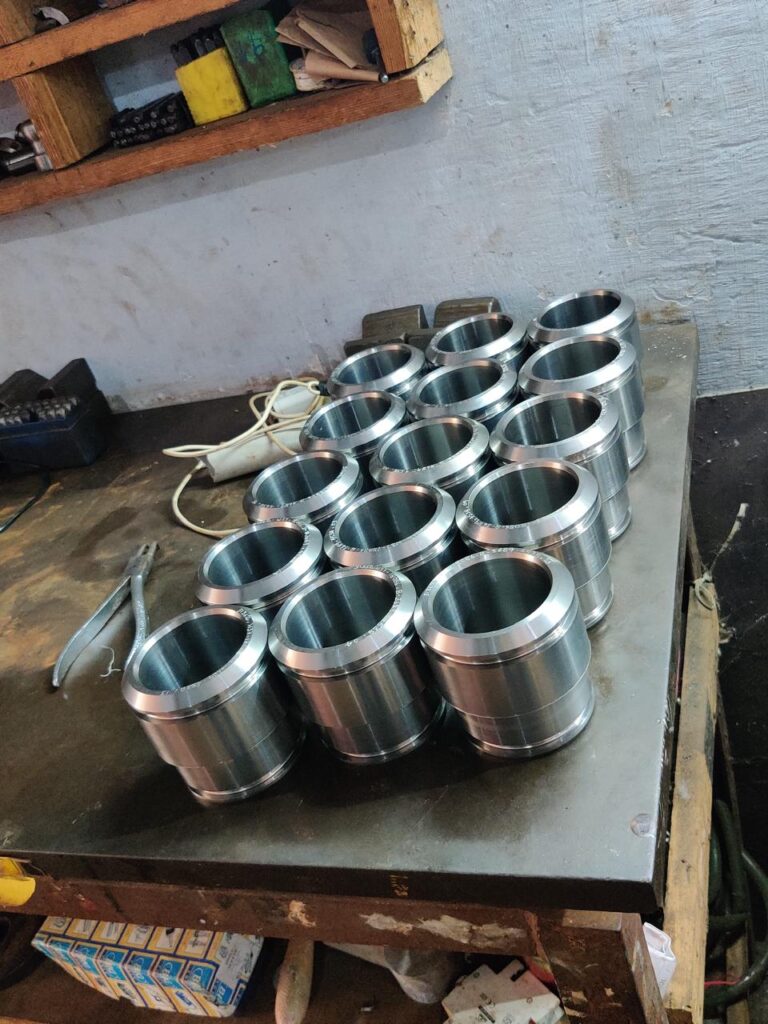
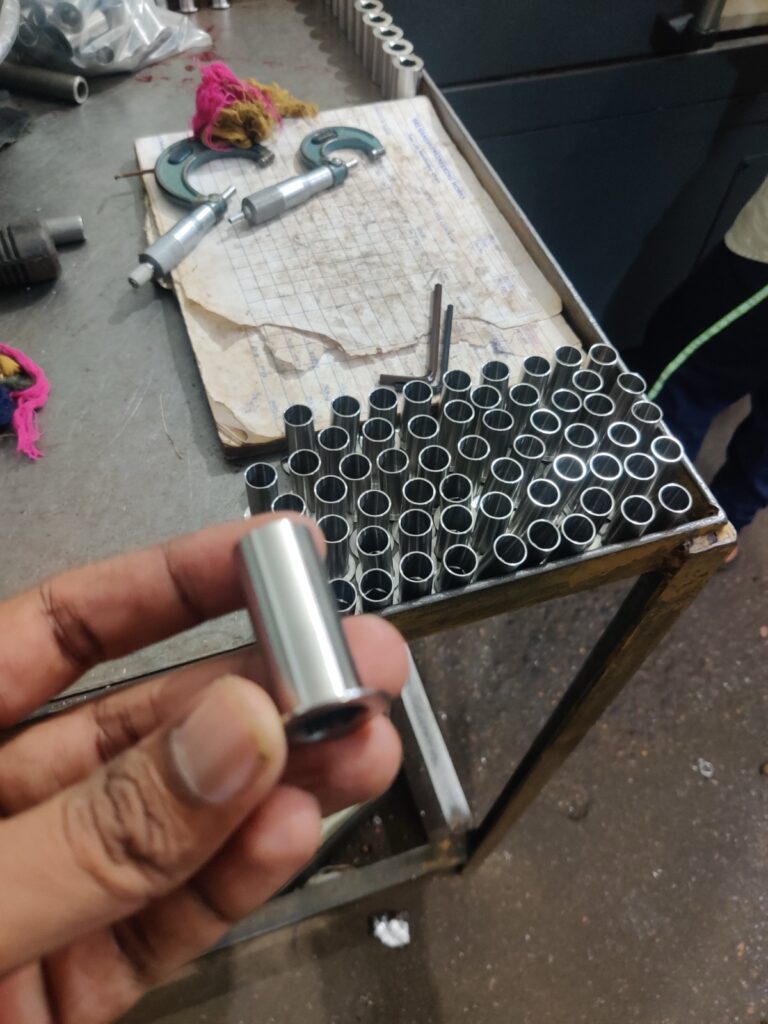
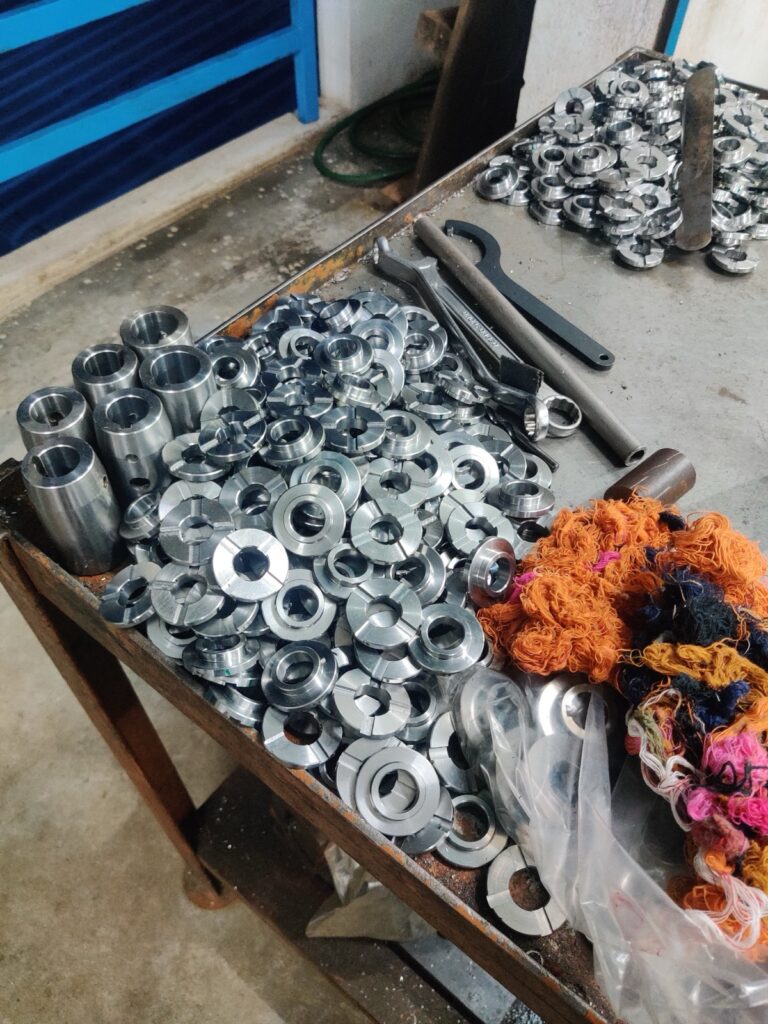
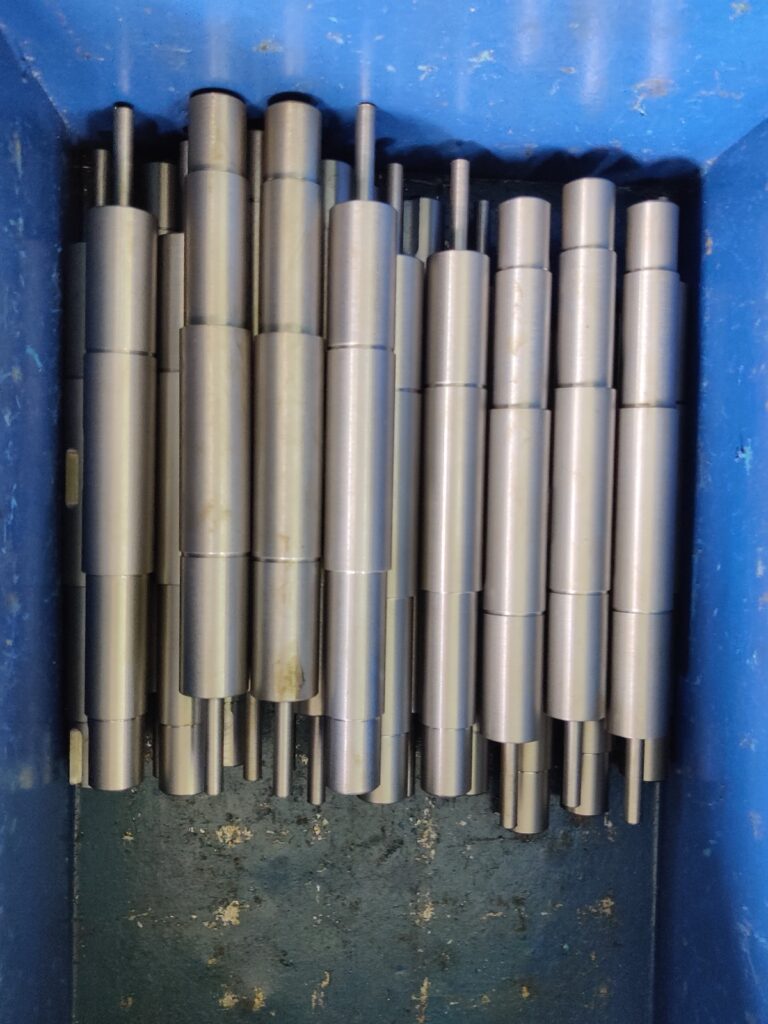
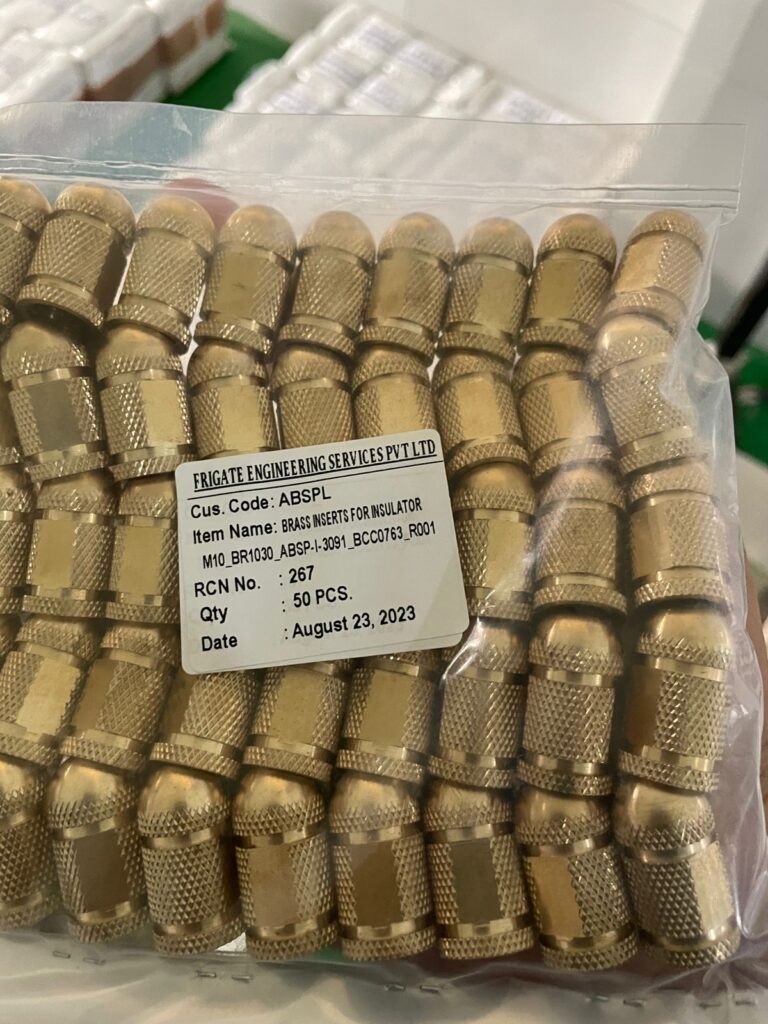
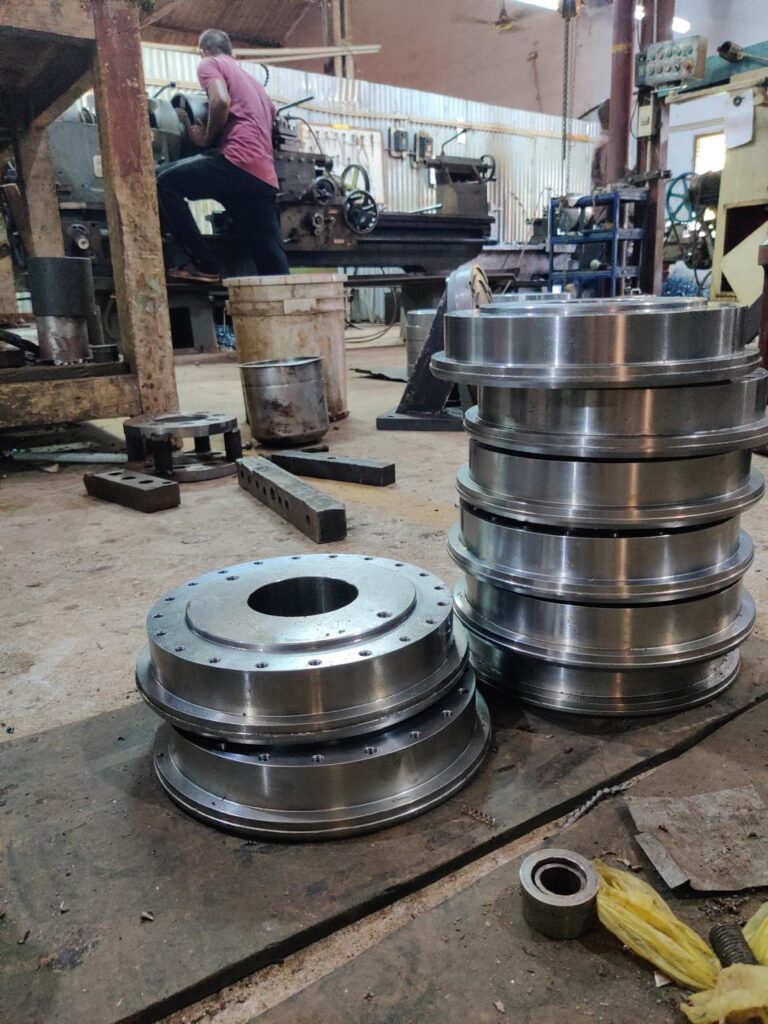
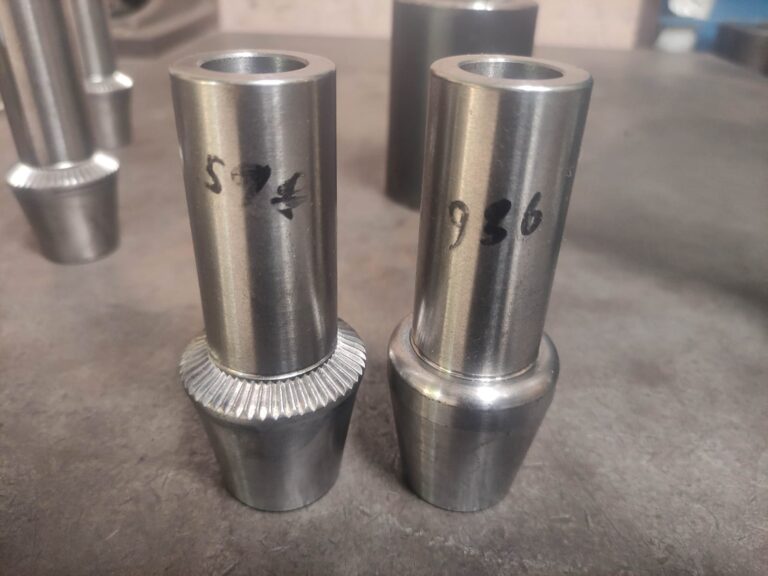
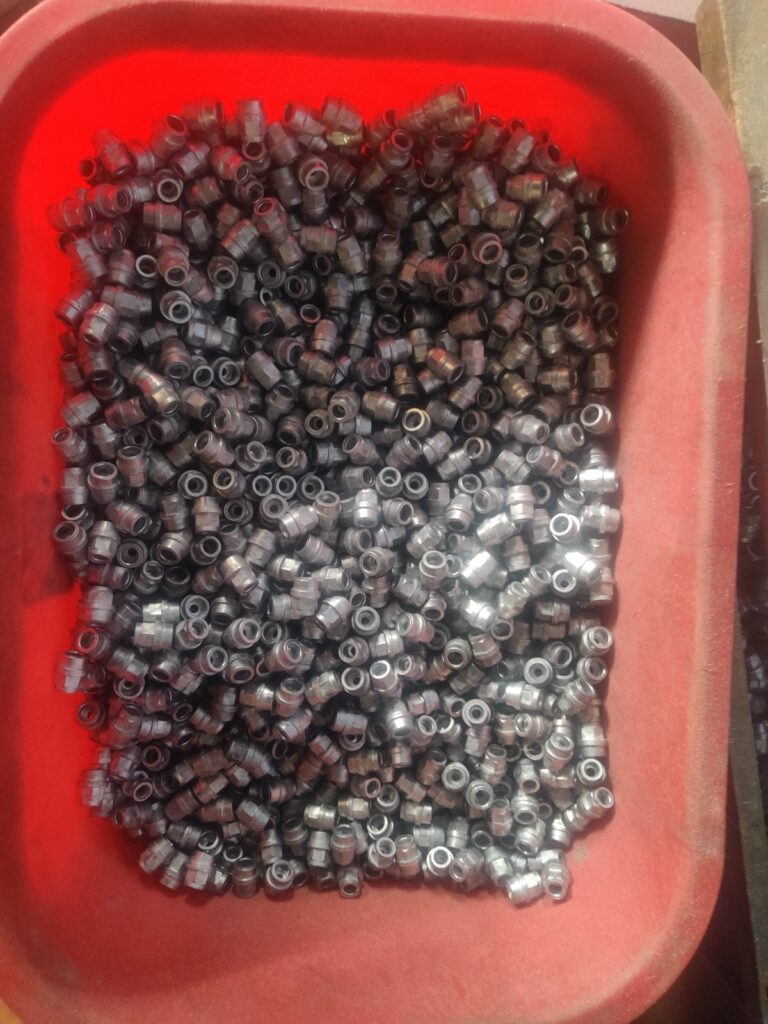
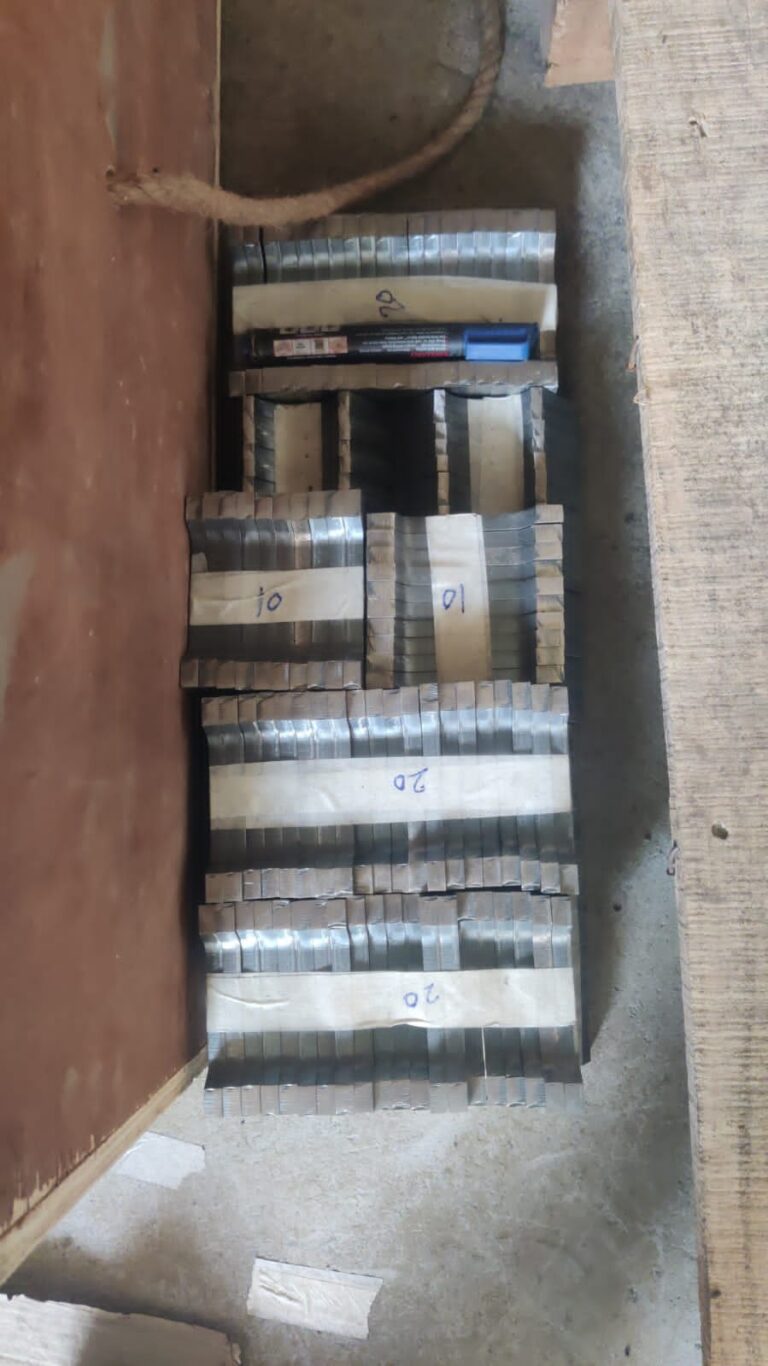
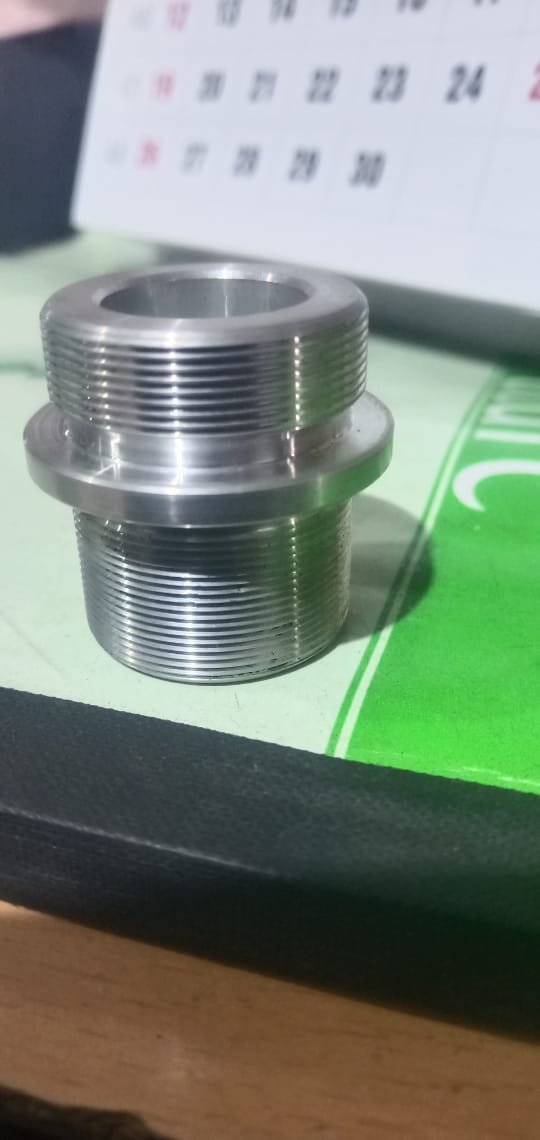
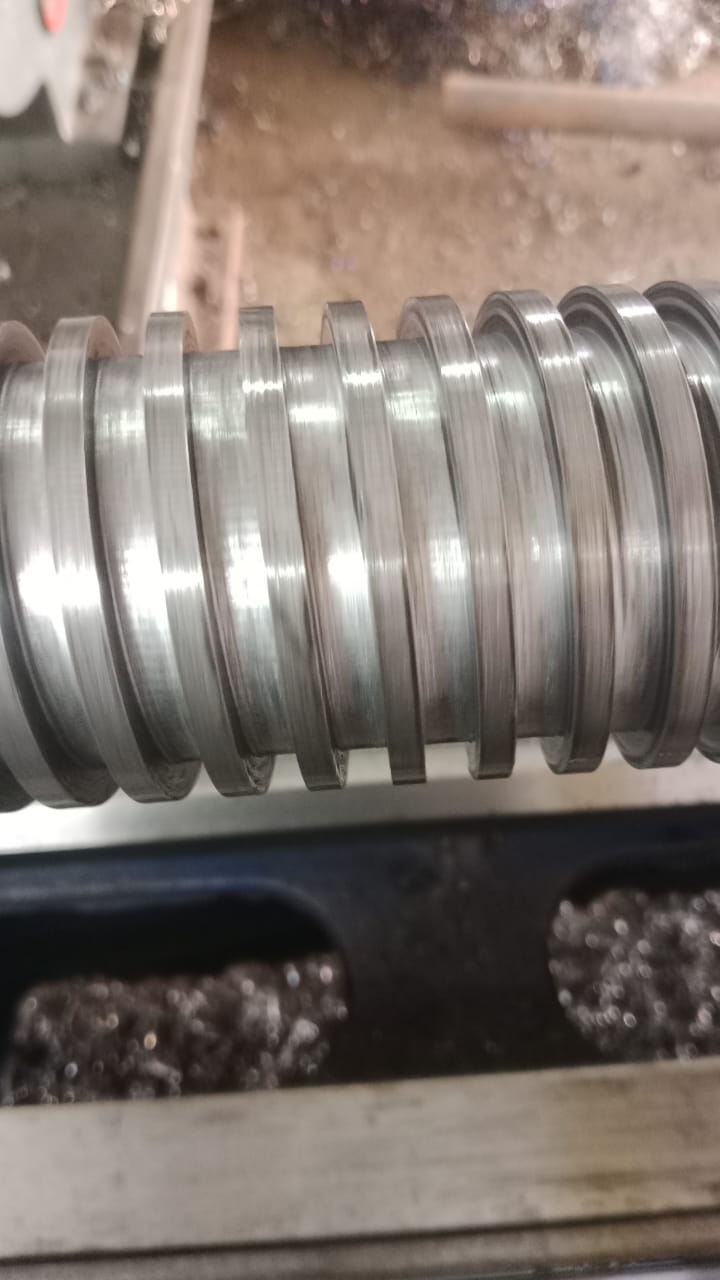
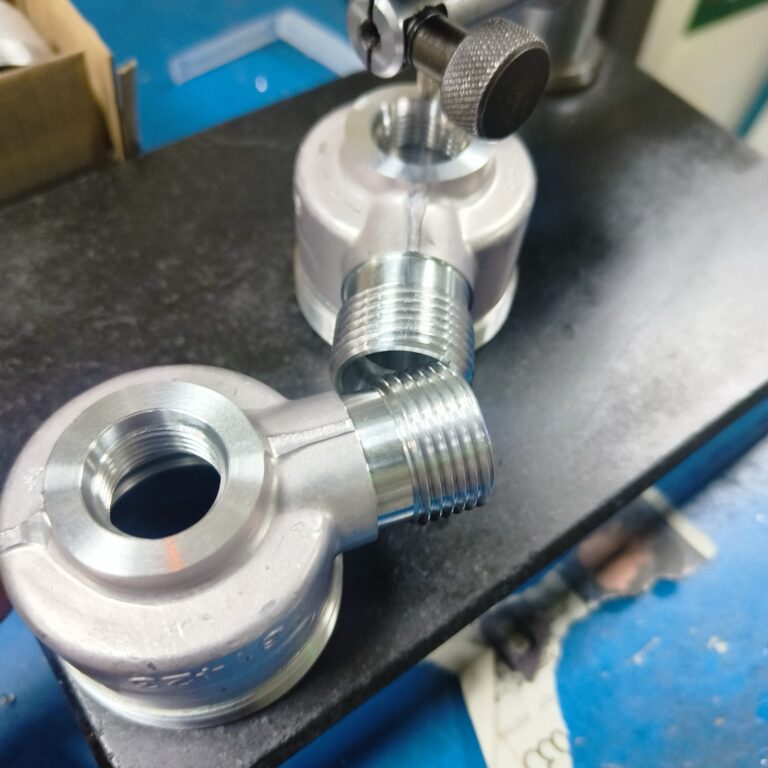
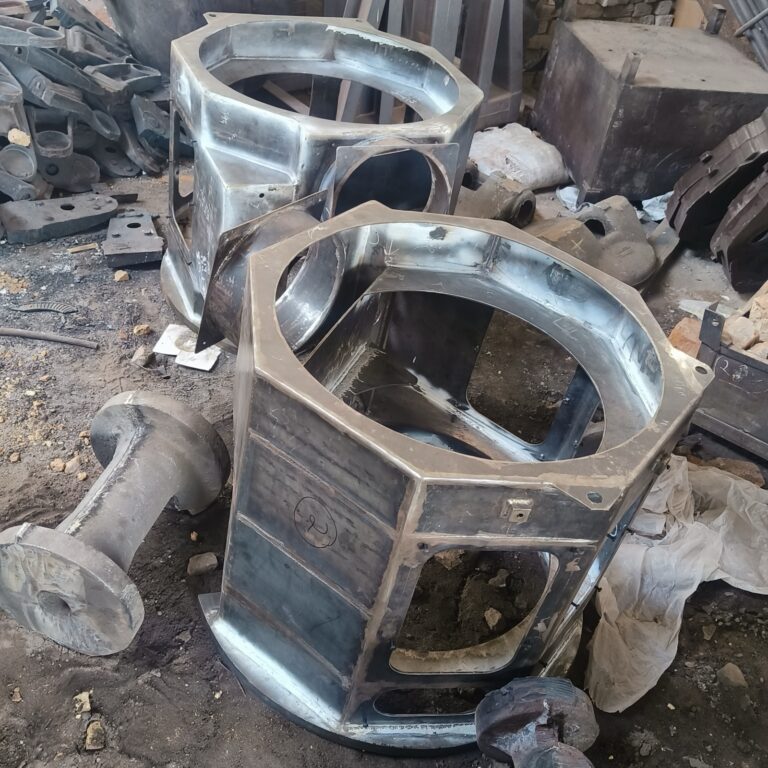
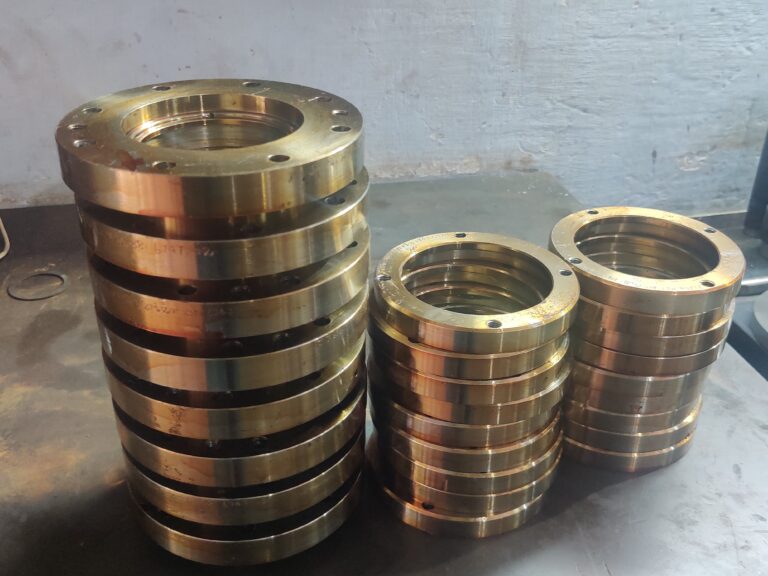
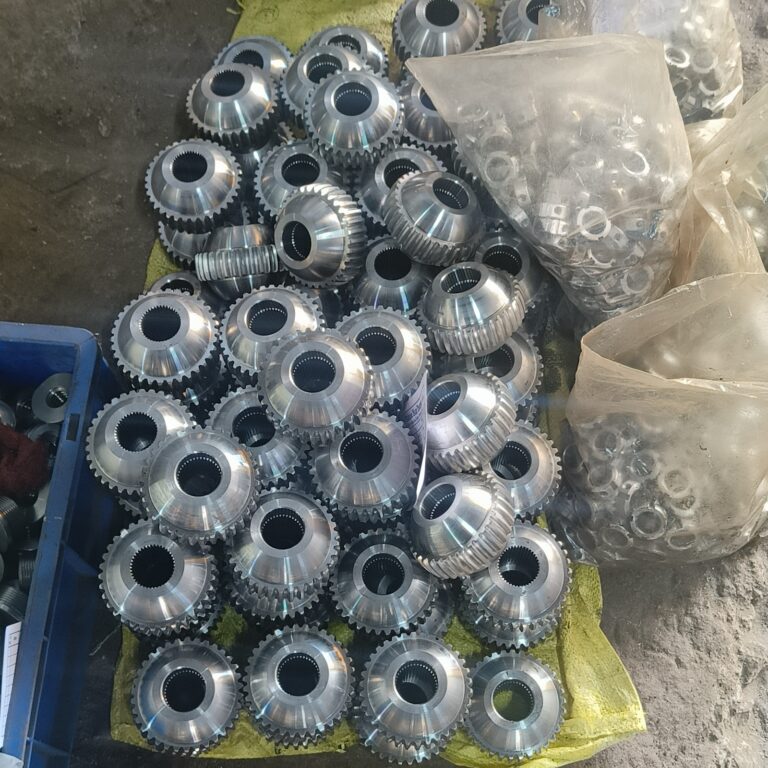
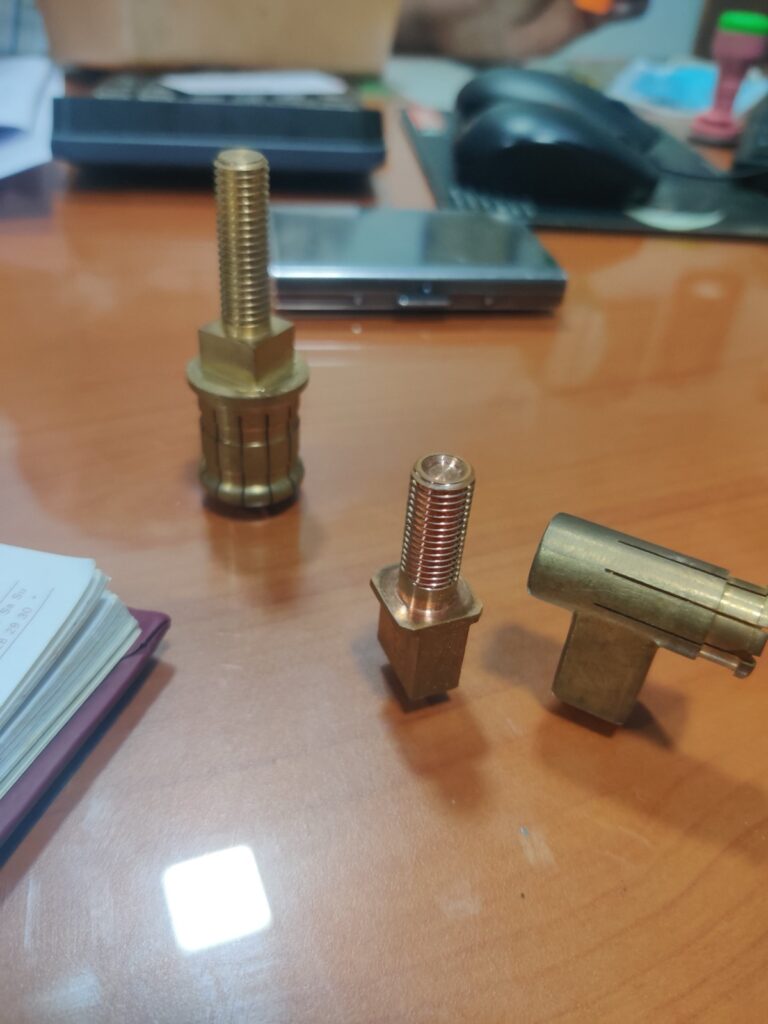
Plastics
Materials
1250 X 1250 MM
Within 10 microns
Engineering Plastics, Polyethylene, Polypropylene, Polyvinyl chloride, Polyethylene terephthalate, Bioplastics, etc.
Rubber
Materials
Natural rubber, Styrene-Butadiene Rubber, Nitrile Butadiene Rubber, Silicone Rubber, Fluorocarbon Rubber, Recycled Rubber, etc.
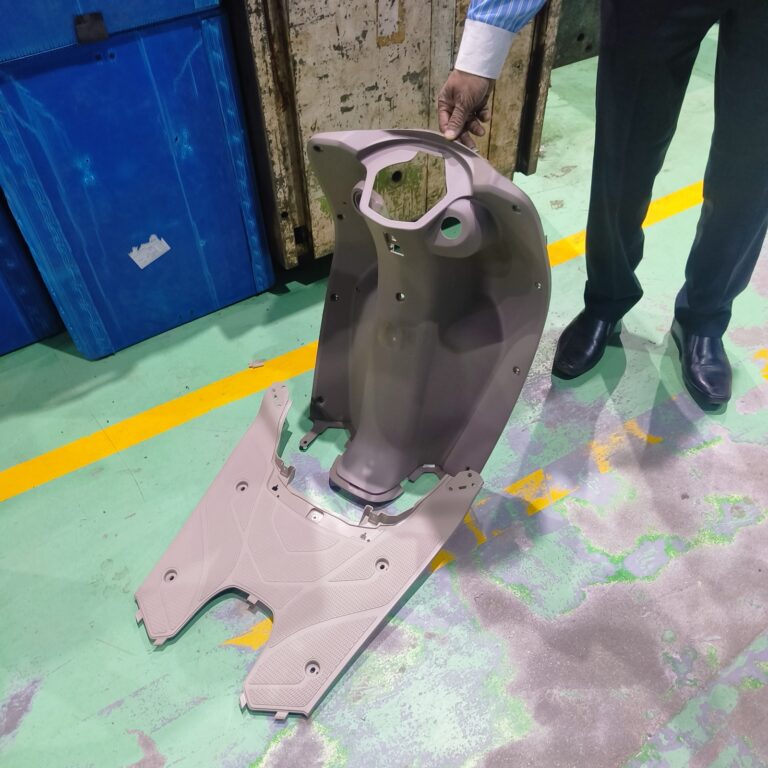
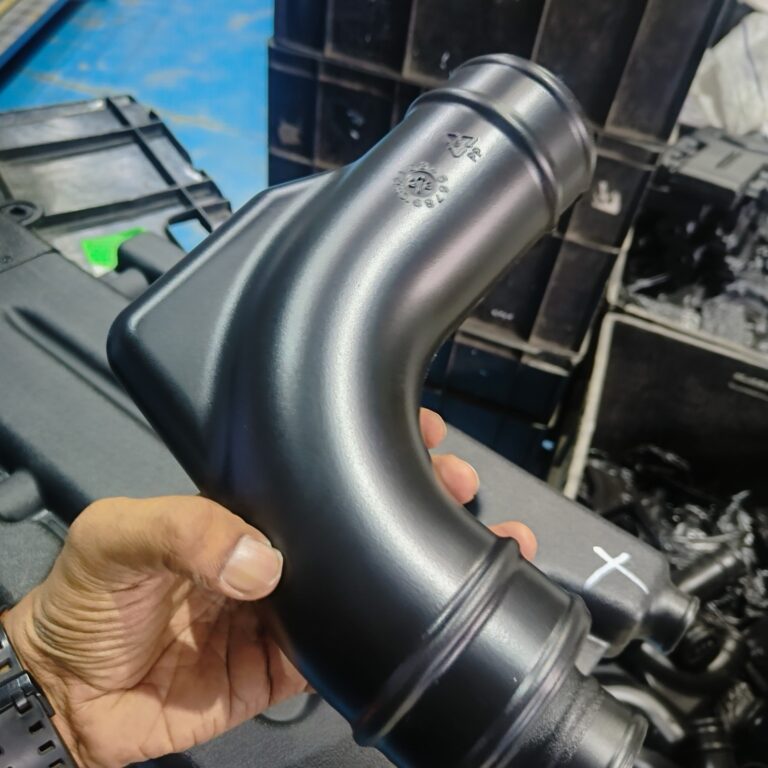
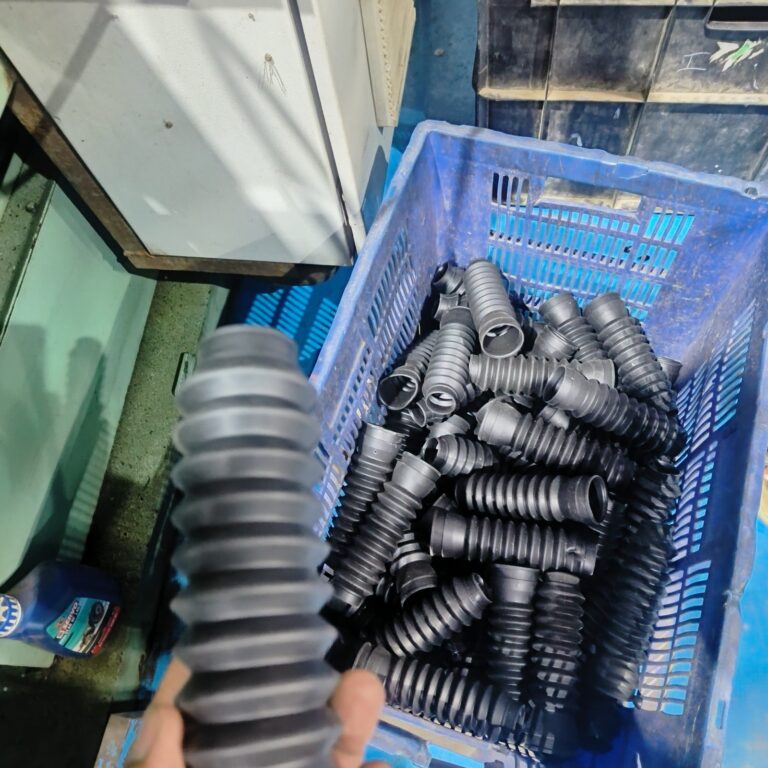
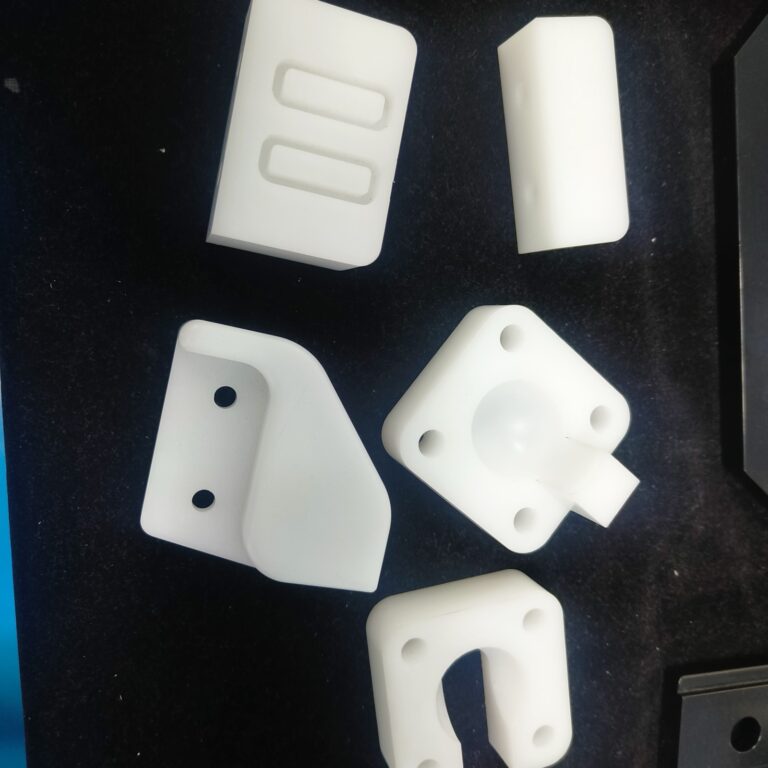
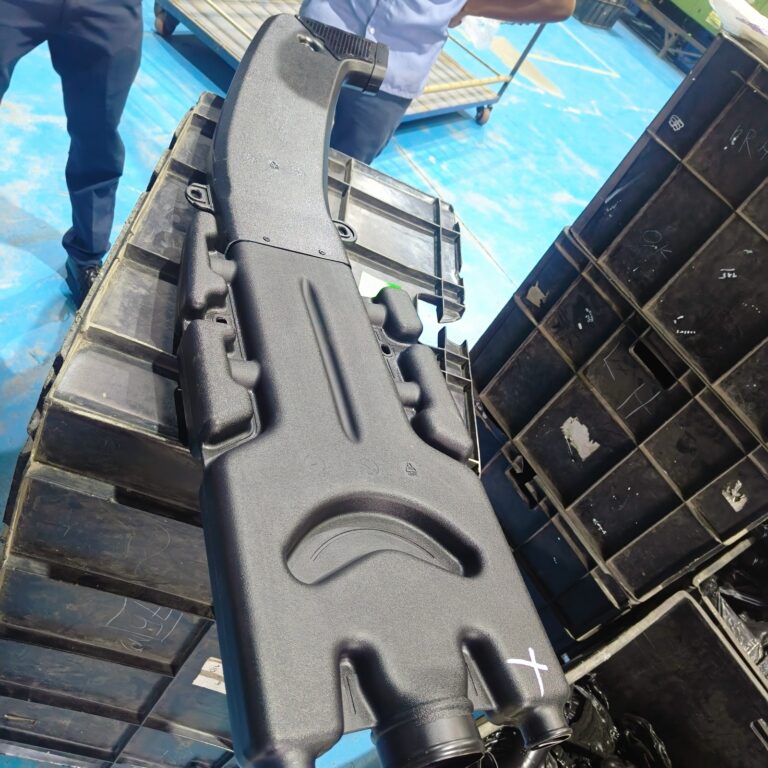
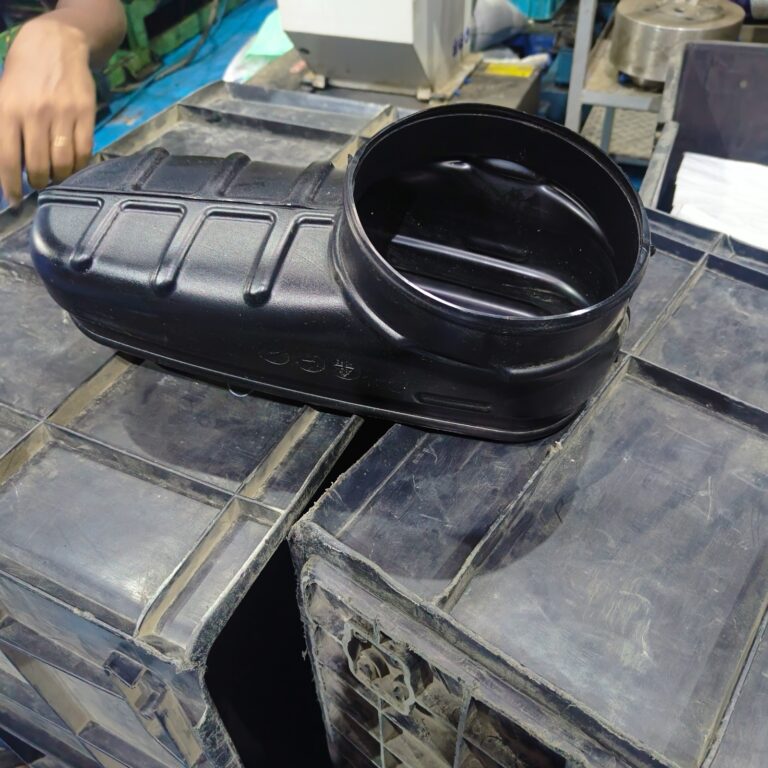
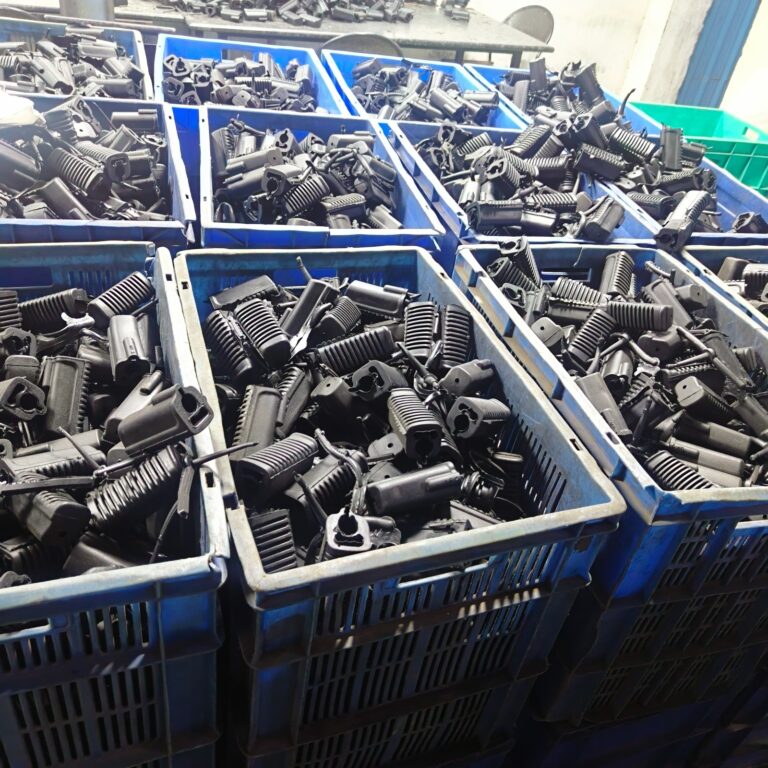
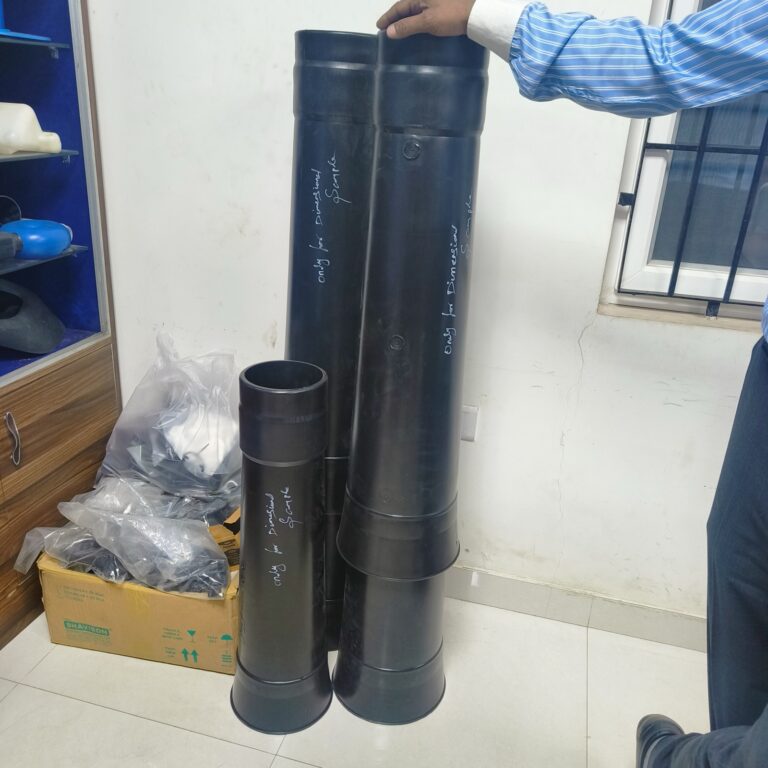
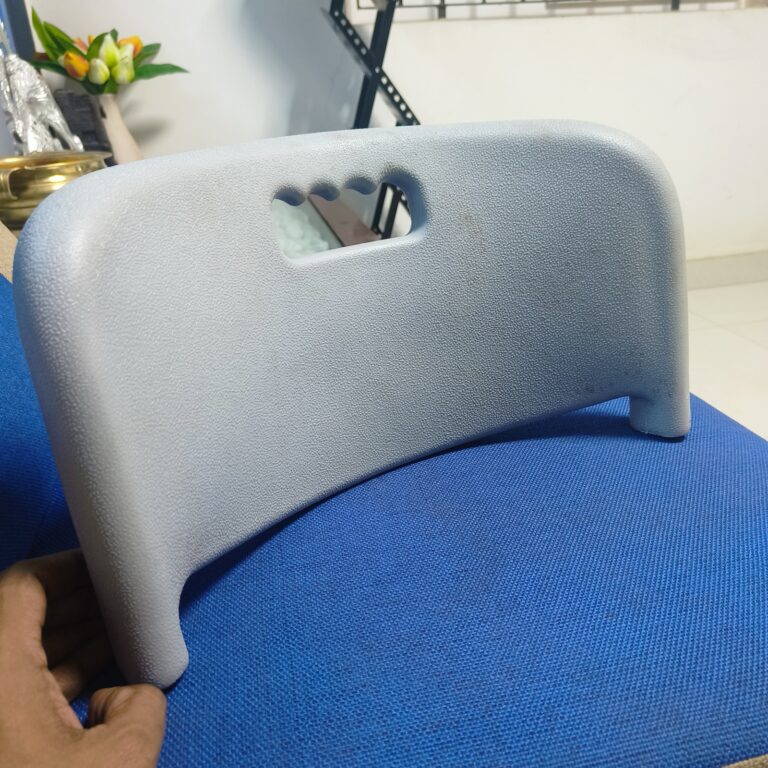
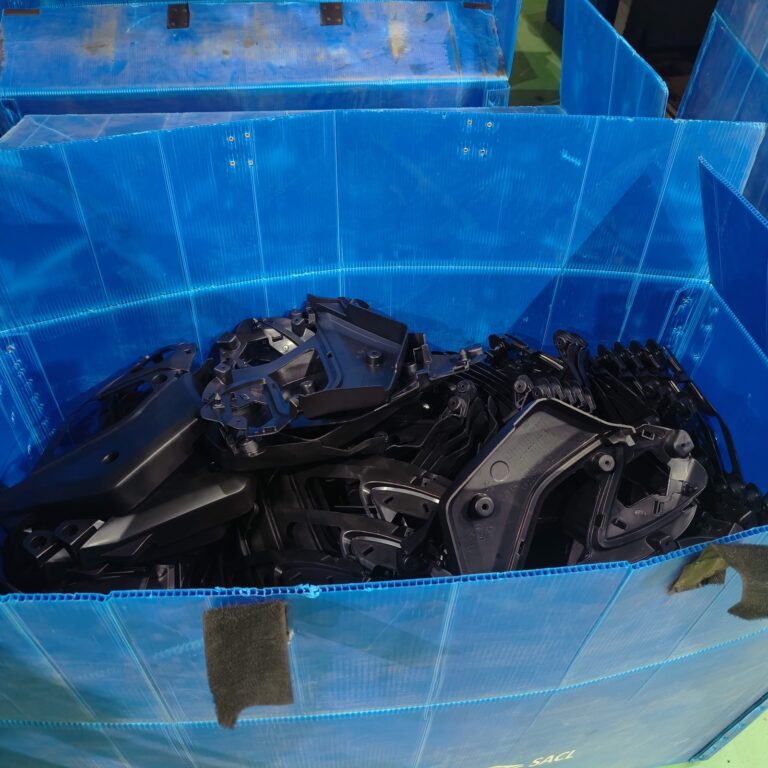
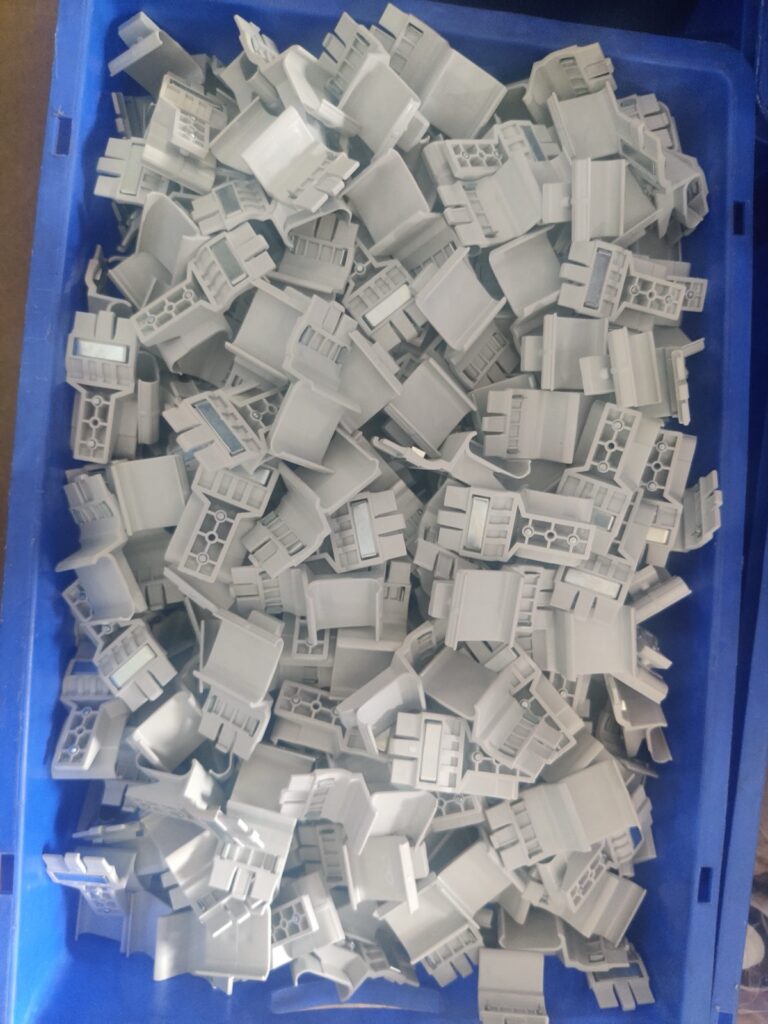
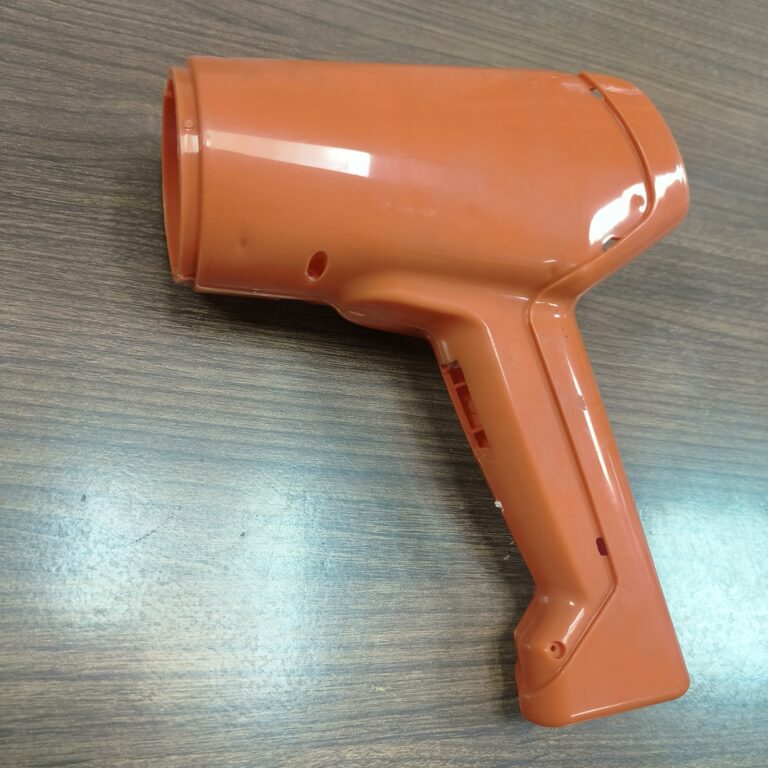
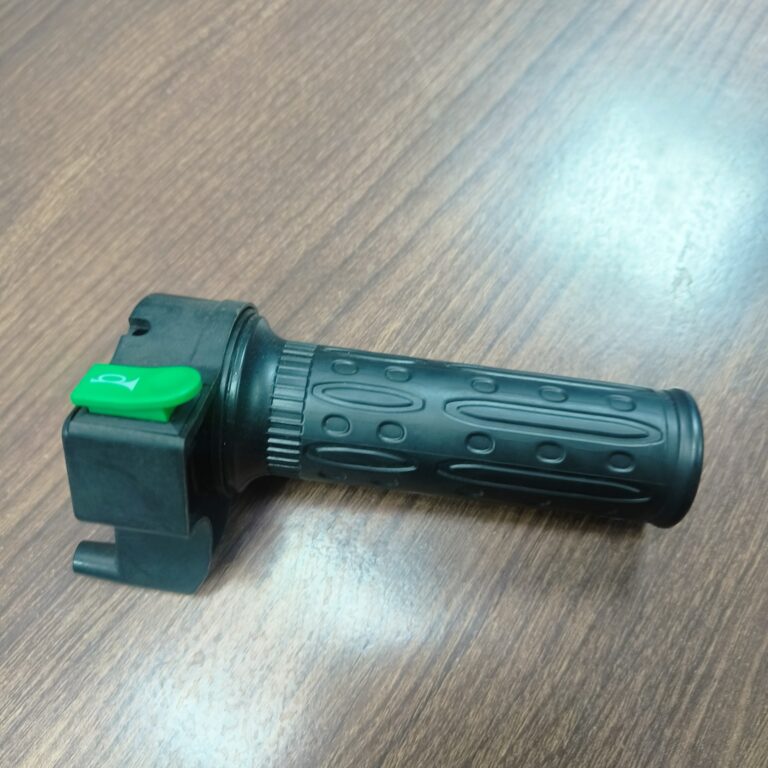
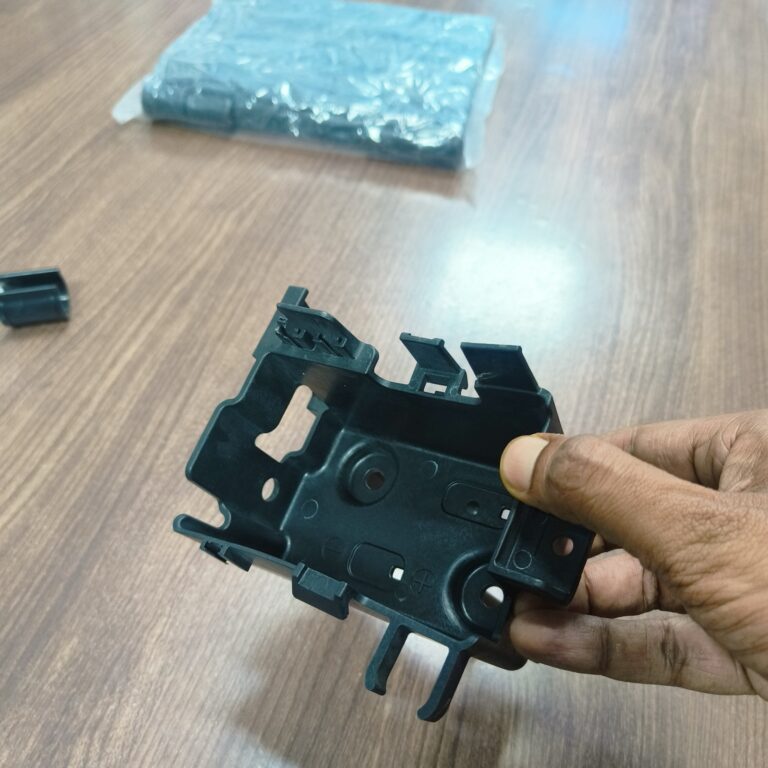
Heavy Fabrication
24000 MT/a
Materials
CS / MS, Alloy steel, Stainless Steel, etc.
Sheet Metal Fabrication
0.8 to 25 mm
Materials
Mild Steel, Stainless Steel, Aluminum, Brass, Copper, etc.


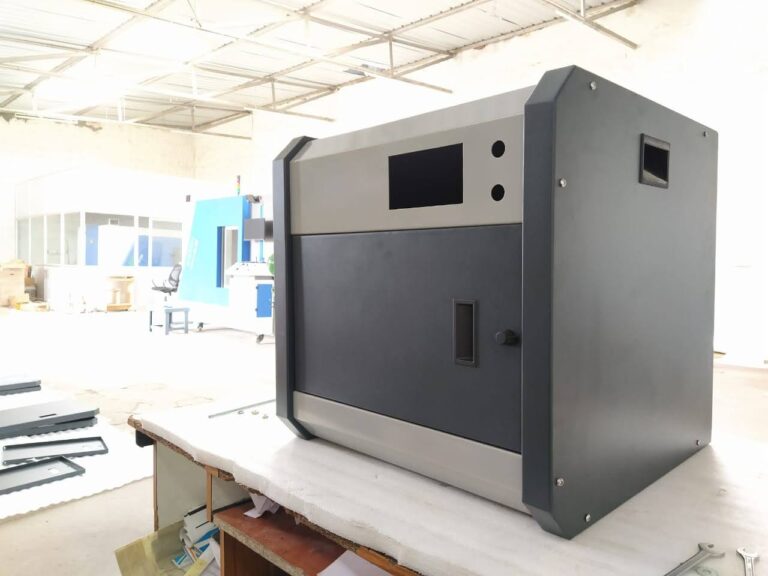


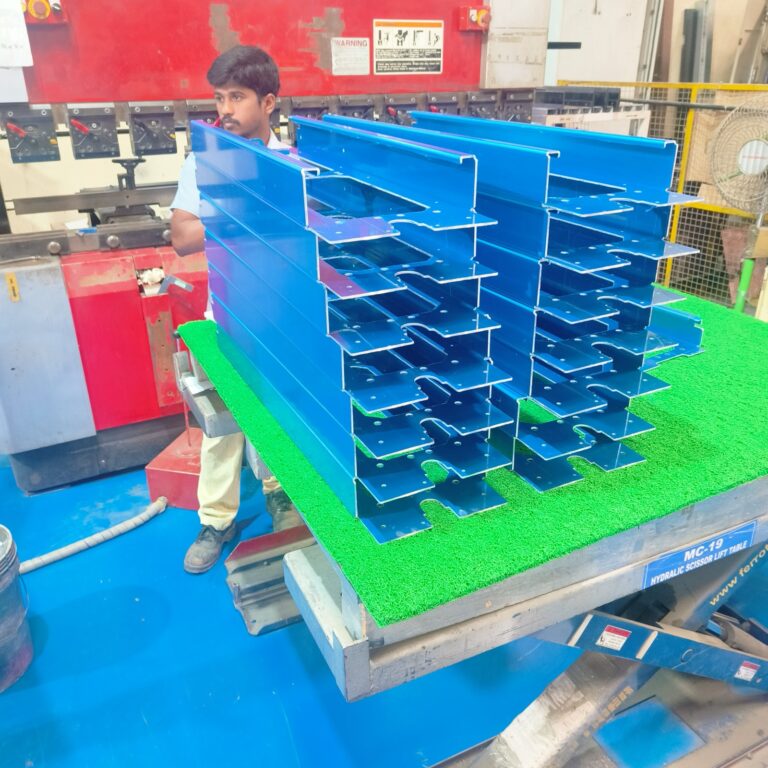
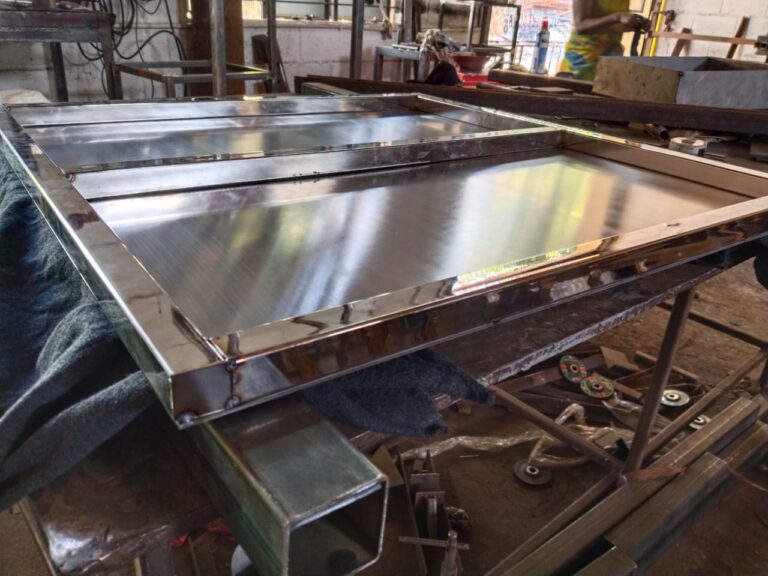
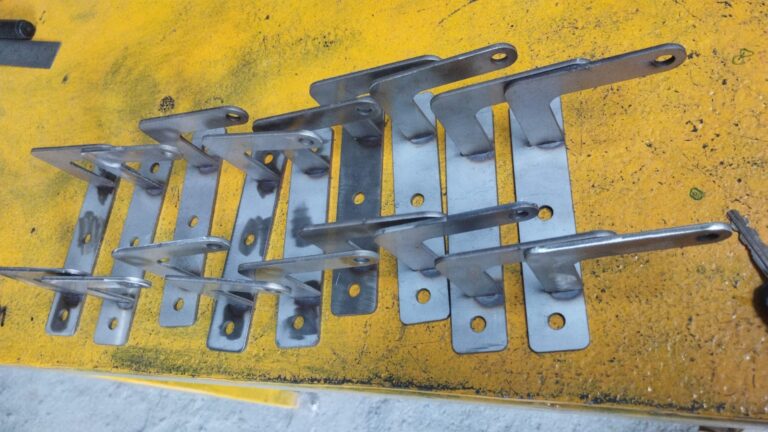
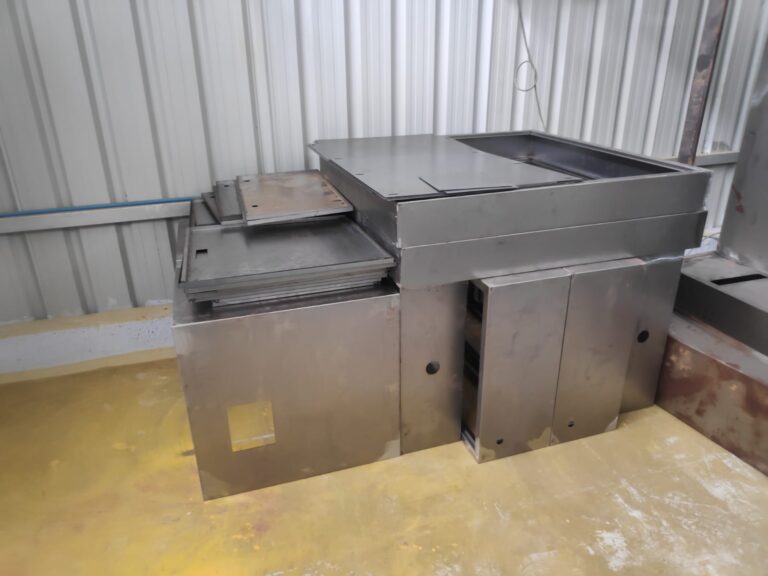
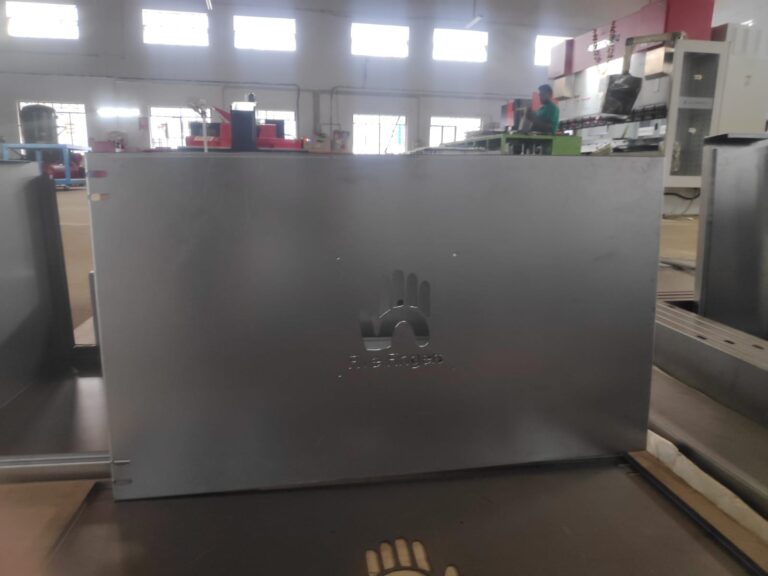
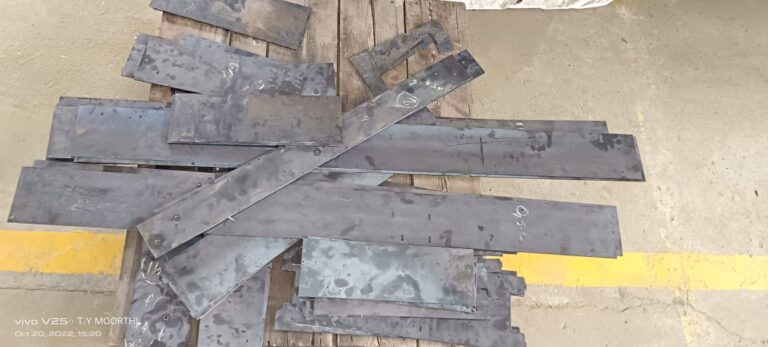
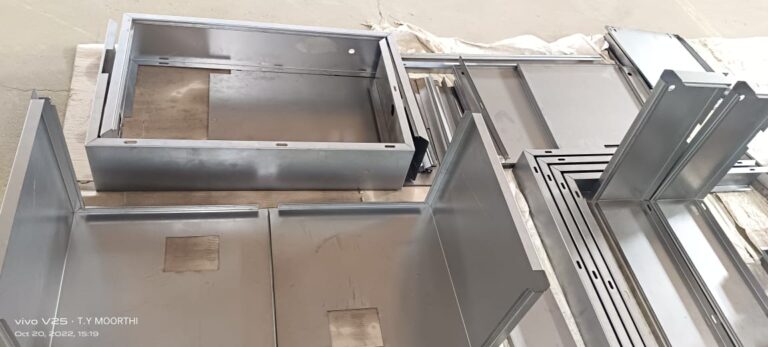
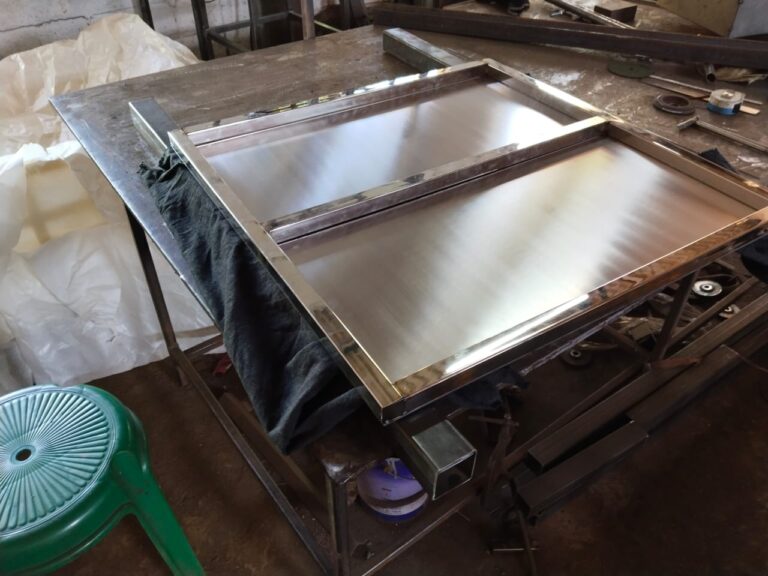
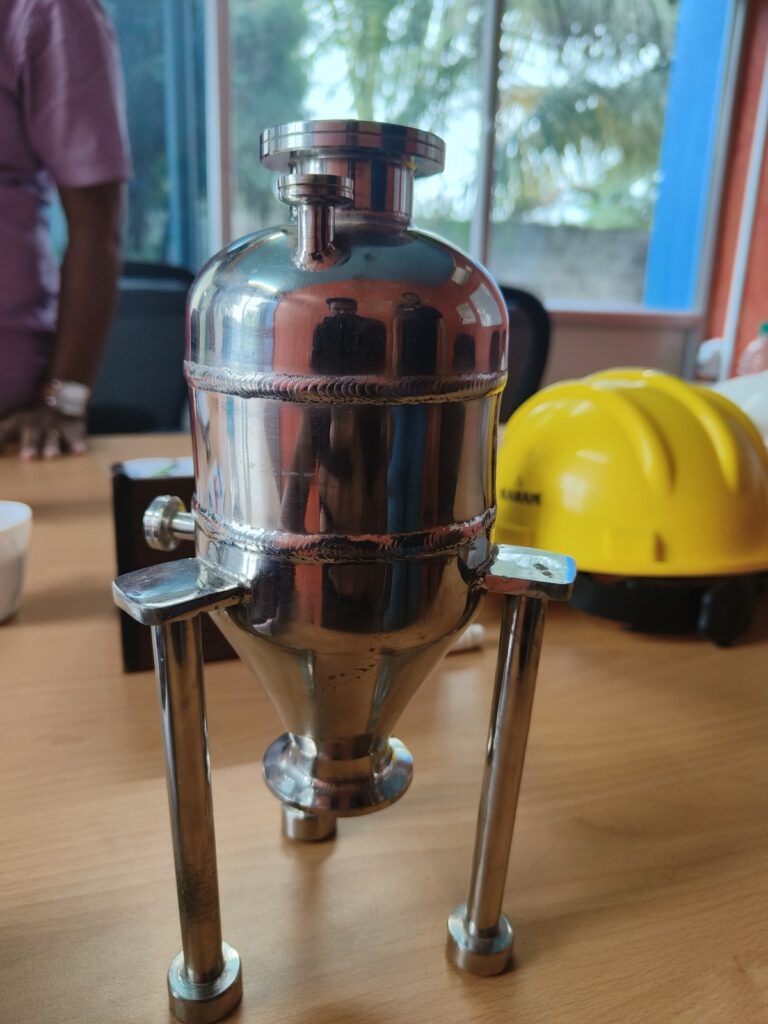
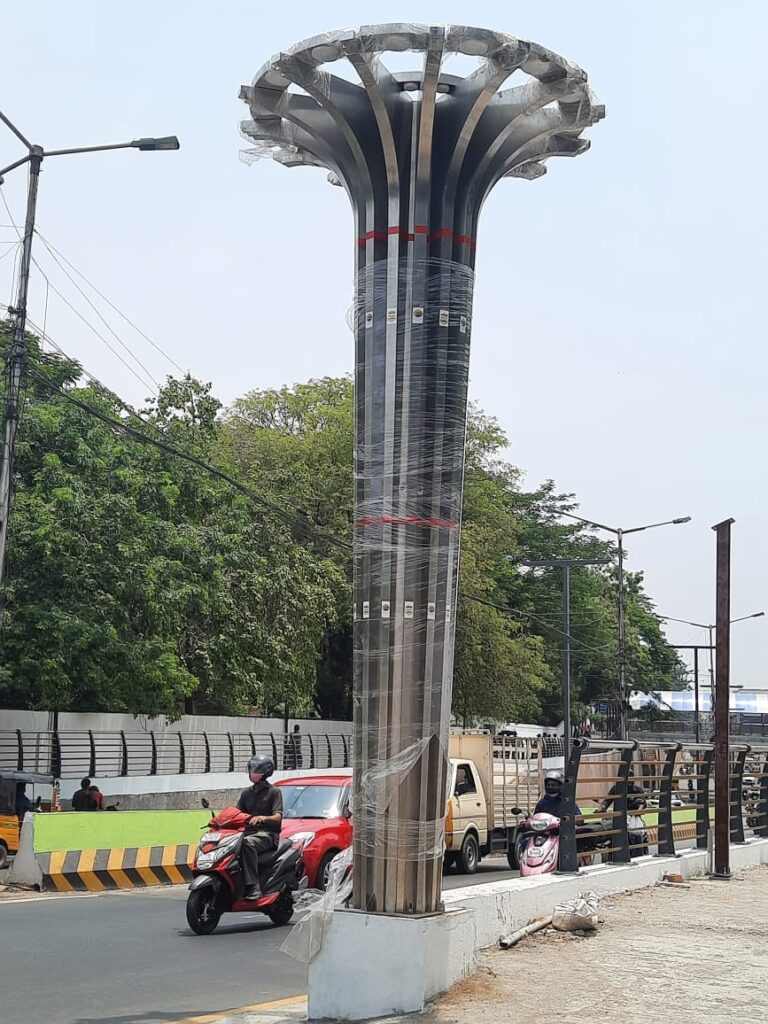
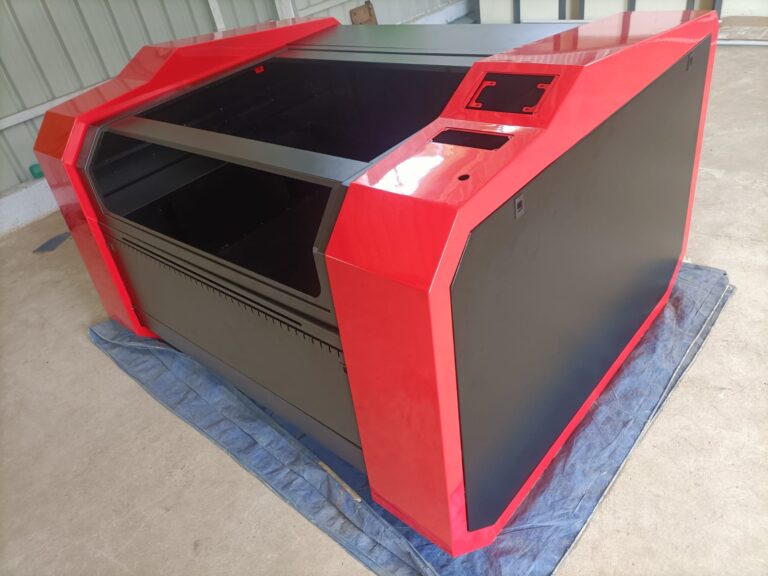
We'd love to Manufacture for you!
Submit the form below and our representative will be in touch shortly.
LOCATIONS
Global Sales Office
818, Preakness lane, Coppell, Texas, USA – 75019
Registered Office
10-A, First Floor, V.V Complex, Prakash Nagar, Thiruverumbur, Trichy-620013, Tamil Nadu, India.
Operations Office
9/1, Poonthottam Nagar, Ramanandha Nagar, Saravanampatti, Coimbatore-641035, Tamil Nadu, India. ㅤ
Other Locations
- Bhilai
- Chennai
- Texas, USA