A Guide to Quick Turn Molding vs. Bridge Molding
Get your product to market quickly is crucial in the fast paced manufacturing world. But what if you need physical parts before committing to expensive production tooling? This is where quick turn molding comes in. However, there’s another option to consider, bridge molding. Both techniques offer advantages for different situations. Let’s delve into the world of quick turn molding vs. bridge molding to help you decide which method is best for your project.
What is Quick Turn Molding?
Quick turn molding (QTM) is a rapid manufacturing process that creates functional prototypes or low-volume production parts using specialized techniques to reduce lead time. Compared to traditional production molding, QTM utilizes materials like aluminum or epoxy that can be machined faster than steel. This allows manufacturers to create mold quicker, resulting in a shorter lead time for your parts. QTM is ideal for situations where you need prototypes for,
- Design Iteration- Test and refine your design before investing in high-volume production tooling.
- Functional Parts- Create real-world parts to assess functionality, fit, and form.
- Material Testing- Evaluate how different materials perform with your design.
Benefits of Quick Turn Molding
- Fast Lead Time- Get prototypes or parts in your hands much quicker than traditional production molding.
- Cost-Effective for Low Volumes- Ideal for smaller production runs where the cost of high-end tooling isn’t justified.
- Design Flexibility- Allows for design changes and iterations without significant delays.
- Functional Parts- Produce parts with similar properties to production parts for thorough testing.
- Material Testing- Experiment with different materials before committing to a specific option.
Things to Consider with Quick Turn Molding
- Limited Material Options- QTM materials might not be suitable for all applications compared to production-grade materials.
- Lower Durability- Molds created with QTM techniques may not be as durable as steel production molds, limiting the number of parts that can be produced.
- Higher Unit Cost per Part- While QTM is cost-effective overall for low volumes, the cost per individual part might be higher compared to high-volume production molding.

What is Bridge Molding?
Bridge molding acts as a bridge between prototyping and high-volume production molding. It uses techniques similar to QTM to create molds faster than traditional methods, but the materials and processes used are more robust, allowing for higher production volumes than standard QTM. Bridge molding is perfect for.
- Low-Volume Production Runs- Produce parts in quantities that wouldn’t justify the cost of production tooling but are too high for QTM.
- Market Testing- Manufacture a limited run of parts to gauge market interest before full-scale production.
- Production Delays- Bridge tooling can be used to produce parts while high-volume production tooling is being created.
Benefits of Bridge Molding
- Faster Lead Time- Bridge molding offers quicker turnaround times compared to production molding.
- Higher Production Volumes- Produce more parts than with QTM while maintaining a faster lead time than production molding.
- Production-Grade Materials- Bridge molds can utilize materials suitable for production parts, ensuring functional testing with realistic material properties.
- Market Testing- Bridge molding allows for limited production runs to test market reception.
- Production Stopgaps- Bridge tooling can be a temporary solution while production tooling is being manufactured.
Things to Consider with Bridge Molding
- Higher Cost Than QTM- Bridge molding is more expensive than QTM due to more robust materials and processes.
- Not as Fast as QTM- While faster than production molding, bridge molding doesn’t offer the same lightning-fast turnaround times as QTM.
- Limited Production Volume Compared to Production Molding- Bridge molding cannot compete with the high-volume capabilities of production tooling.
Choosing Between Quick Turn Molding and Bridge Molding
The choice between quick turn molding and bridge molding depends on your specific needs. Here’s a quick breakdown to help you decide
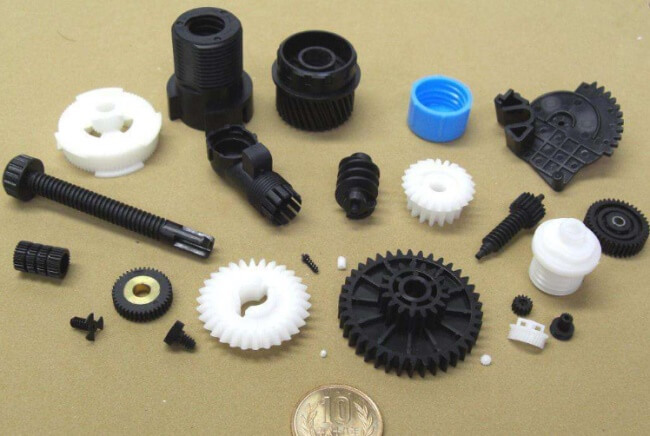
Prioritize Speed and Early Design Validation – Go for QTM
If your primary objective is to get functional parts in your hands as quickly as possible for design iteration and initial testing, then QTM shines. Its rapid turnaround time allows you to test form, fit, and basic functionality early in the development cycle. This enables you to identify and address design flaws quickly, saving valuable time and resources down the road. Additionally, QTM’s cost-effectiveness for low volumes makes it ideal for situations where you only need a handful of prototypes for initial testing.
Focus on Low-Volume Production and Market Validation – Bridge Molding
When you need to move beyond prototypes and produce a limited run of parts for market testing or to bridge a gap in production while high-volume tooling is being built, bridge molding steps up. It offers a significant advantage over QTM in terms of production volume. Bridge molds can produce hundreds or even thousands of parts, allowing you to gather valuable market feedback and gauge customer interest before committing to full-scale production. This “real-world” testing phase with production-grade materials helps refine your product and ensure a smoother transition to high-volume manufacturing.
Additional Considerations- Complexity and Material Needs
Beyond speed and volume, consider the complexity of your design and the materials required. While QTM can handle many designs, intricate details might require production molding for optimal results. Similarly, if your parts require specific material properties for functionality, bridge molding’s ability to utilize production-grade materials is a clear advantage.
The Right Tool for the Job
Ultimately, the best choice between QTM and bridge molding depends on your unique project needs. By carefully evaluating factors like turnaround time, production volume, design complexity, and material requirements, you can select the molding process that propels your project forward efficiently and effectively.
Contact Frigate for Your Molding Needs
Regardless of whether you require quick turn molding or bridge molding, Frigate can be your one-stop shop for all your molding needs. We are a leading provider of advanced manufacturing solutions, equipped with the latest technologies and expertise to deliver high-quality parts efficiently. Our team of experienced engineers will work closely with you to understand your project requirements and recommend the most suitable molding process for your application. We offer a wide range of materials and finishes to meet your specific needs, and our commitment to quality ensures that you receive parts that meet the highest standards.
Here at Frigate, we understand the importance of speed and cost-effectiveness in today’s competitive market. Whether you need prototypes for design iteration or low-volume production runs for market testing, we can provide you with the Injection molding solutions you need to get your product to market quickly and efficiently.
Contact us today to discuss your project requirements and learn more about how quick turn molding or bridge molding can benefit your business. We look forward to partnering with you to bring your vision to life.