Shaping Industries Across the Globe
Injection molding is a versatile and widely used manufacturing process that allows for the creation of high-quality plastic parts in a cost-effective and efficient manner. From the intricate components of medical devices to the durable parts of automobiles, applications of injection molding in a vast array of industries. Let’s know more about the applications of injection molding, exploring its impact on various sectors and highlighting the key benefits it offers.

Mass Production with Unwavering Consistency
One of the most significant injection molding is its ability to produce large quantities of identical plastic parts with exceptional consistency. This mass production capability makes it ideal for industries that require a steady stream of components, such as
- Automotive- Applications of Injection molding are extensively used in the automotive industry to create a multitude of parts, including dashboards, door panels, and instrument bezels. The process ensures that each component precisely matches the specifications, contributing to the overall quality and functionality of the vehicle.
- Consumer Electronics- The world of consumer electronics relies heavily on injection molding for the production of housings, buttons, and other intricate parts for devices like smartphones, laptops, and televisions. The high precision achievable through injection molding guarantees a seamless user experience.
Design Flexibility- From Simple to Complex
Applications of Injection molding offers remarkable design flexibility, allowing for the creation of parts with both simple and intricate geometries. This adaptability makes it suitable for a wide range of industries, including-
- Medical Devices- The medical field utilizes injection molding for the production of various critical components, such as syringes, inhalers, and prosthetic limbs. The ability to create complex shapes with tight tolerances is crucial for ensuring the functionality and sterility of these medical devices.
- Packaging- The packaging industry leverages injection molding to manufacture a diverse range of containers, caps, and closures. The design flexibility of the process allows for the creation of unique and functional packaging solutions that enhance product appeal and security.
Cost-Effective Manufacturing for Every Need
Applications of Injection molding is a cost-effective manufacturing solution, particularly for high-volume production runs. The initial investment in mold creation is offset by the efficiency and speed of the process, resulting in lower per-unit costs. This advantage makes injection molding an attractive option for industries like-
- Construction- Injection molding is used in construction to produce electrical components, plumbing fixtures, and various building materials. The process ensures consistent quality and dimensional accuracy while maintaining affordability.
- Aerospace- The aerospace industry utilizes injection molding for the creation of lightweight and durable aircraft components. The cost-effectiveness of the process allows for the production of these parts without compromising on quality or performance.
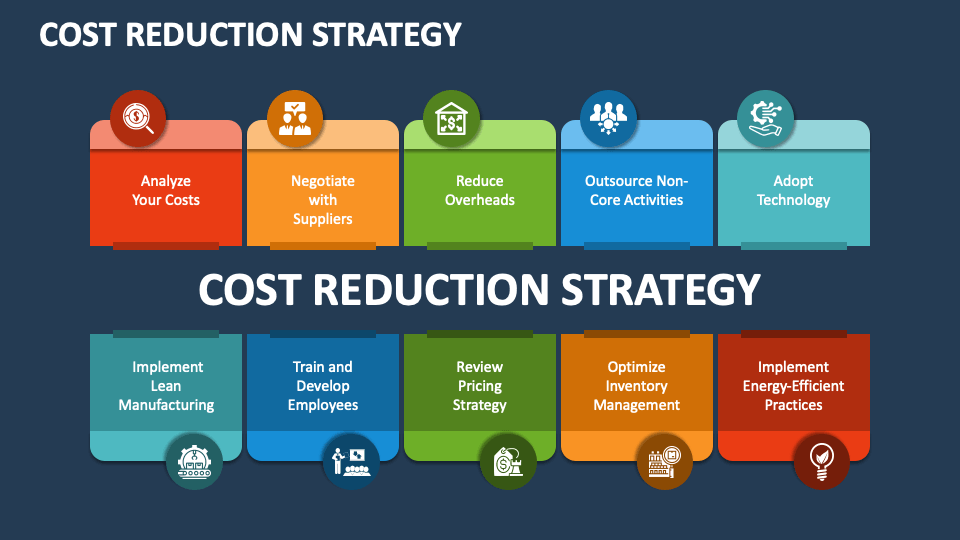
The Power of Prototyping and Customization
While applications of injection molding excel in mass production, it also offers advantages for prototyping and customization. Through rapid prototyping techniques, manufacturers can create functional prototypes quickly and efficiently, allowing for design iterations and product testing before committing to large-scale production. Additionally, injection molding can be adapted to accommodate a certain degree of customization, enabling the creation of parts with variations in color, texture, or surface finish.
Endless Possibilities with Injection Molding
Injection molding boasts a significant advantage – the ability to work with a wide range of materials. This versatility allows manufacturers to select the most suitable material for their specific application, considering factors like strength, flexibility, heat resistance, and chemical compatibility. Some of the commonly used materials in injection molding include-
- Thermoplastics- These versatile materials soften when heated and solidify upon cooling, making them ideal for injection molding. Common thermoplastics used include ABS, polypropylene, and polyethylene.
- Thermosets- Unlike thermoplastics, thermosets undergo a permanent chemical change when heated, resulting in a rigid and non-meltable final product. Epoxy resins and polyester are examples of thermosets used in injection molding.
Streamlining Manufacturing with Injection Molding
Applications Injection molding is an efficient manufacturing process that minimizes waste and optimizes production time. The precise nature of the process allows for minimal material usage, reducing scrap and environmental impact. Additionally, the high production speeds of injection molding enable manufacturers to meet demanding deadlines and fulfill large orders efficiently.
Frigate – Your Partner in Injection Molding Success
Injection molding isn’t just technology; it’s a revolution. It’s a transformation of the manufacturing landscape, empowering businesses across industries to achieve never-before-seen levels of efficiency, quality, and versatility. At Frigate, we understand the immense potential of injection molding, and we’re here to be your partner in navigating this transformative journey.
Frigate has been at the forefront of injection molding innovation. We possess a wealth of experience and expertise in crafting high-quality, complex plastic parts for a diverse range of applications. Whether you’re in the medical field requiring intricate surgical instruments, the automotive industry needing durable car components, or the consumer electronics space demanding sleek and functional device housings, Frigate has the knowledge and capabilities to meet your specific needs.

Our commitment to excellence extends beyond just experience. We leverage cutting-edge technology and utilize a vast array of materials to ensure your injection molded parts are not only functional but also meet the highest standards of quality and performance. Our team of skilled engineers and technicians meticulously design and manufacture molds, ensuring exceptional precision and repeatability in every part produced.
Here’s how Frigate can be your partner in achieving injection molding success-
- Unwavering Consistency in Mass Production- Injection molding shines in its ability to produce large quantities of identical plastic parts with remarkable consistency. At Frigate, we ensure this consistency through meticulous process control and rigorous quality assurance measures. This translates to a reliable and predictable production flow, allowing you to meet even the most demanding supply chain requirements.
- Design Flexibility that Knows No Bounds- Gone are the days of limitations in part design. Injection molding, with Frigate’s expertise, allows you to create intricate and complex geometries while maintaining exceptional functionality. Our team works closely with you to translate your design vision into reality, pushing the boundaries of what’s possible with plastic components.
- Cost-Effective Manufacturing Solutions- We understand the importance of cost efficiency in today’s competitive market. Injection molding, with its streamlined processes and minimal material waste, offers a significant cost advantage compared to traditional manufacturing methods. At Frigate, we optimize production processes further, ensuring you get the most value out of your investment.
- Strength and Durability You Can Rely On- Many industries require components that can withstand demanding environments. Injection molding, when combined with Frigate’s material selection expertise, allows us to create parts with exceptional strength and durability. We carefully analyze your application needs and recommend the most suitable material to ensure your parts can perform flawlessly for years to come.
Frigate isn’t just a provider of injection molding services; we’re your trusted partner in transforming your manufacturing process. Contact us today to discuss your specific needs and explore how our expertise can propel your business toward a future of efficiency, quality, and innovation. Together, let’s navigate the exciting world of injection molding and steer your manufacturing success.