Staying ahead of the competition requires agility and innovation. This is where rapid prototyping casting comes in. Rapid prototyping casting offers a game-changing solution for businesses looking to accelerate product development and streamline their manufacturing processes. This innovative technique allows businesses to create functional prototypes of their designs rapidly, facilitating essential design verification and design iteration before committing to full-scale production. Let’s explore how partnering with Frigate for rapid prototyping casting can propel your business to new heights.

What is Rapid Prototyping Casting?
Traditional casting involves creating a mold and then using that mold to produce large quantities of identical parts. Rapid prototyping casting, on the other hand, utilizes 3D printing casting patterns to expedite the creation of functional prototypes. These 3D printed patterns are then used to create molds for casting the prototypes.
This method offers several advantages over traditional methods, making it a valuable tool for businesses across various industries. Let’s delve deeper into how rapid prototyping casting can benefit your business.
Advantages of Rapid Prototyping Casting with Frigate
Frigate’s rapid prototyping casting service offers a game-changing approach to product development, empowering businesses to bring their visions to life faster and more efficiently. Let’s delve into the key benefits you can unlock with Frigate’s expertise-
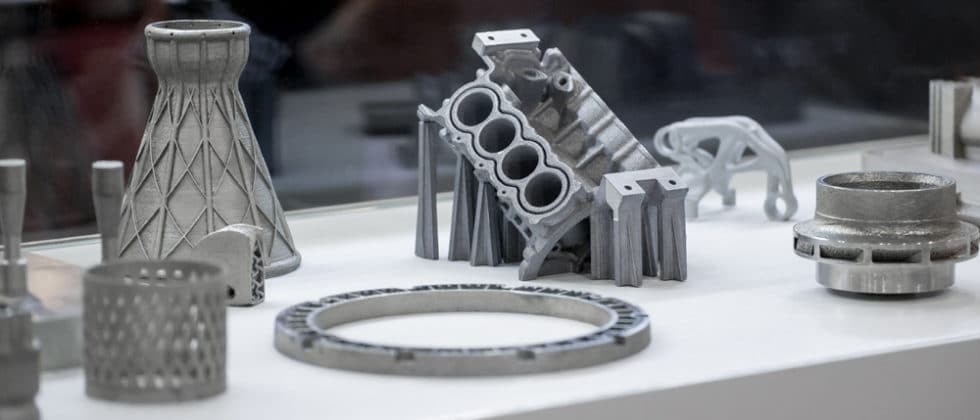
1. Expedited Design Verification
Traditional casting methods often require lengthy prototype turnaround times. Frigate’s rapid prototyping casting eliminates this hurdle. By leveraging 3D-printed casting patterns, we enable the swift creation of functional prototypes. This allows for early testing of your design’s functionality, form, and fit. Identifying and addressing potential issues early on saves you from costly tooling mistakes.
2. Streamlined Design Iteration
Rapid design iteration is crucial for product success. Frigate’s rapid prototyping casting facilitates this process by enabling the quick production of multiple prototypes. This empowers you to explore various design options and incorporate valuable stakeholder feedback. This iterative approach ensures your final product is optimized for performance, usability, and manufacturability.
3. Reduced Production Lead Times
You can significantly shorten your overall production lead time by catching and resolving design flaws early with Frigate’s rapid prototyping casting. This translates to a faster time-to-market, giving you a crucial competitive edge. With Frigate, you can capitalize on market opportunities quickly and efficiently.
4. Cost Savings Through Efficiency
While the initial cost of rapid prototyping casting might seem higher due to the 3D printed patterns, Frigate’s process delivers substantial long-term savings. Identifying and rectifying design flaws early prevents costly mistakes during mass production. Rapid prototyping casting can also minimize the need for extensive machining, reducing overall production costs.
5. Material Exploration Made Easy
Frigate’s rapid prototyping casting allows you to experiment with various casting materials during the prototyping stage. This empowers you to select the optimal material for your final product based on critical factors like strength, weight, and aesthetics. With Frigate, you can explore different materials to ensure your product meets all your specifications.
6. Enhanced Communication and Collaboration
Frigate’s rapid prototyping casting provides tangible, functional prototypes that are a powerful communication tool. These prototypes foster better collaboration between design teams, engineers, and potential investors. Everyone involved can visualize the design intent, leading to a more streamlined development process.
Applications of Rapid Prototyping Casting
Rapid prototyping casting is a versatile technique that can be applied across various industries. Here are some specific examples-
- Automotive- Rapid prototyping casting is used extensively in the automotive industry to create prototypes for engine components, transmission parts, and interior trim pieces. Experimenting with different designs and materials helps optimize performance, weight, and aesthetics.
- Aerospace—In the demanding aerospace industry, rapid prototyping casting is utilized to produce functional prototypes for complex aircraft components, such as turbine blades, landing gear parts, and satellite housings. Casting’s high strength and heat resistance make it an ideal choice for these applications.
- Consumer Goods- The consumer goods industry benefits from rapid prototyping casting by rapidly creating prototypes for new product designs, from smartphone housings to appliance components. This allows quick design iteration and user testing to ensure the final product meets market demands.
- Medical Devices- Rapid prototyping casting plays a vital role in the medical device industry by enabling the creation of prototypes for surgical instruments, prosthetic limbs, and implant devices. The ability to produce complex geometries with high precision and biocompatible materials makes rapid prototyping casting a valuable tool for medical device development.
- Industrial Equipment- Rapid prototyping casting is used in the industrial equipment sector to create prototypes for machine parts, fluid handling components, and heavy-duty tools. The durability and dimensional accuracy achievable through casting make it suitable for these demanding applications.
Unleash the Power of Rapid Prototyping Casting with Frigate
Rapid prototyping casting offers a powerful and efficient way to streamline your product development process. By enabling rapid design verification, fostering design iteration, and reducing production lead times, this innovative technique can give your business a significant competitive advantage.
If you’re looking to leverage the benefits of rapid prototyping casting for your industry, Frigate is your ideal partner. We possess extensive expertise in casting materials and investment casting processes, ensuring you receive high-quality, functional prototypes that meet your exact specifications.
Contact Frigate today to discuss how rapid prototyping casting can accelerate your product development journey and bring your design visions to life quickly and efficiently.