- Reverse Protection
Check and One-Way Valves
Frigate’s check and one-way valves eliminate the risk of reverse fluid movement in high-speed, pressure-sensitive systems. The engineered sealing technology ensures immediate response to backpressure, protecting pumps, compressors, and metering equipment from hydraulic shock and reverse surge.

Our Clients
Trusted by Engineers and Purchasing Leaders
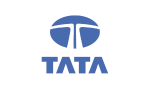
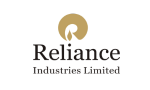


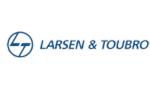
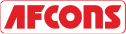


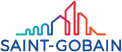

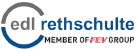

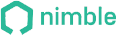
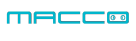









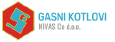
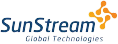

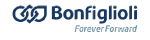


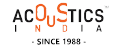
- Versatile Offerings
Our Check and One-Way Valves Products
Explore our range of high-quality Check and One-Way Valves today.
- Real Impact
Words from Clients
See how global OEMs and sourcing heads describe their experience with our scalable execution.
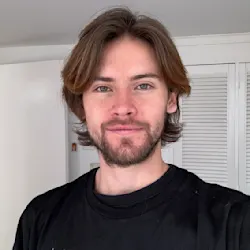
“Quick turnaround and solid quality.”
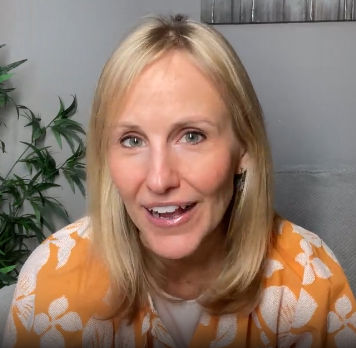
“The instant quote tool saved us time, and the parts were spot-on. Highly recommend Frigate!”
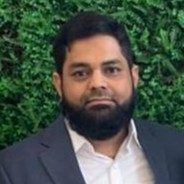
“I would strongly recommend Frigate to anyone who wants to do Rapid Prototyping, and take their ideas to manufacturing. One firm doing all kinds of Product Development!”
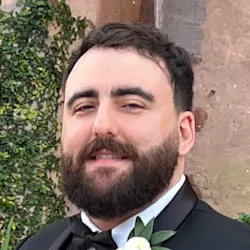
“Great service, fair price, and the parts worked perfectly in our assembly.”
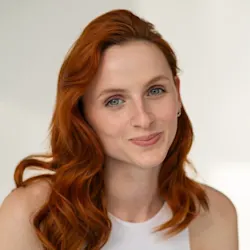
“Top-notch machining and fast shipping. Very satisfied with the results.”
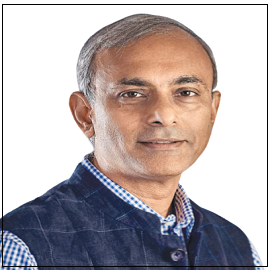
“The next disruption is happening in Prototyping & Manufacturing on-demand and Frigate is leading the way! I personally believe the Frigate's way of IIOT enabled cloud platform with Al.”
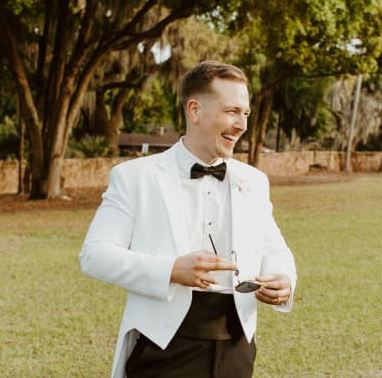
“Frigate delivered high-quality parts at a competitive price. The instant quote tool is a huge plus for us!”

“We appreciate the precision and quality of the machined components in the recent delivery—they meet our specifications perfectly and demonstrate Frigate’s capability for excellent workmanship.”
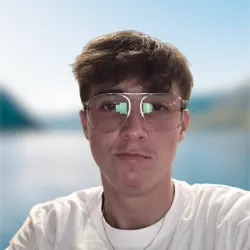
“Flawless execution from quote to delivery.”

“I am absolutely happy to work with supplier like Frigate who were quite proactive & result oriented . Frigate has high willingness team who has strong know how & their passion towards the products & process were absolutely thrilling.”
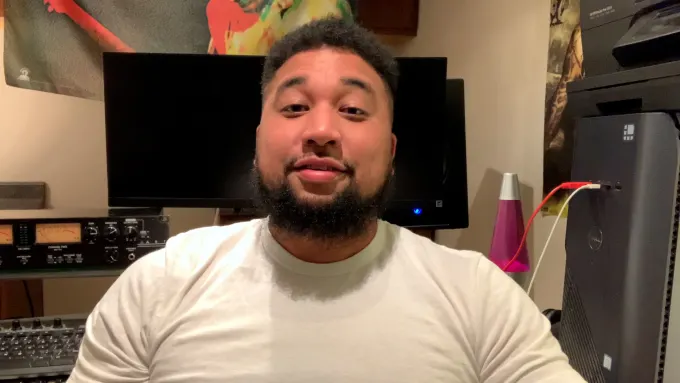
“The precision on these parts is impressive, and they arrived ahead of schedule. Frigate’s process really stands out!”
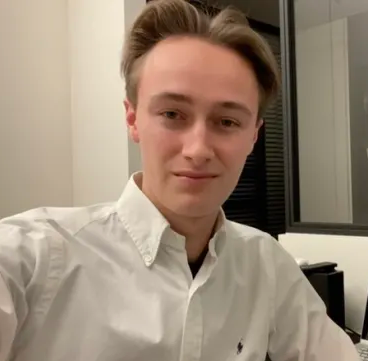
“Parts were exactly as spec’d, and the instant quote made budgeting a breeze.”
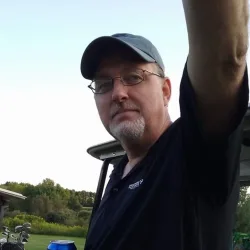
“Good value for the money.”
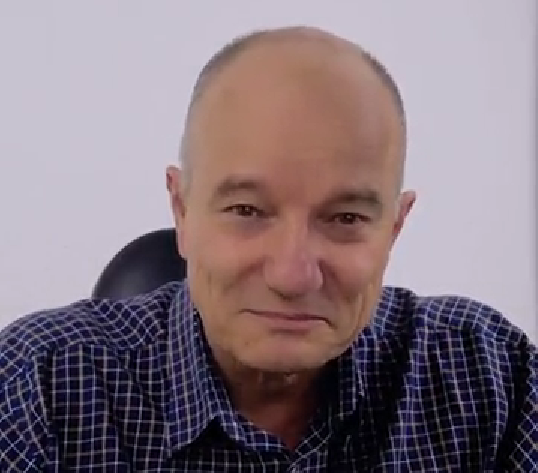
“The finish was perfect, and the team was easy to work with.”

“Working with Frigate has been great. Their proactive, results-driven approach and expertise shine through in every project. It's been a pleasure collaborating with them.”

"We are highly satisfied with the timely delivery and quality of the MIG Welding Cable from Frigate. Their attention to detail, secure packaging, and quick responsiveness stood out. We confidently recommend Frigate Engineering Services Pvt. Ltd. as a reliable manufacturing partner."
We export to 10+ countries
Frigate’s Global Presence
Frigate takes pride in facilitating “Make in India for the globe“. As our global network of Frigaters provides virtually limitless capacity, and through our IoT enabled platform your parts go directly into production. By digitally and technologically enabling “the silent pillars of the economy” MSME and SME manufacturing industries, we are able to tap the huge potential for manufacturing to bring the best results for our clients.

100,000+
Parts Manufactured
250+
Frigaters
2000+
Machines
450+
Materials
25+
Manufacturing Process
Industry Applications
Used to enforce unidirectional flow in complex piping networks handling liquids or gases across industrial, municipal, and commercial infrastructure.
Prevents backflow and hydraulic shock in centrifugal and positive displacement pump systems, ensuring operational safety and consistent flow performance.
Enables directional control in automated fluid circuits, integrating with actuators and sensors to maintain precise flow sequencing and isolation.
Protects against reverse steam or condensate flow in high-temperature lines, reducing risk of water hammer and equipment damage.
Maintains proper coolant direction, preventing reverse heat transfer and thermal inefficiencies in closed-loop and open-loop cooling systems.
Ensures safe, one-way fuel flow in high-pressure injection, distribution, or return lines within industrial, transportation, and power applications.




- Noise Reduction
Quiet Performance at High Velocity
Excessive noise from turbulent flow can exceed 85 dB(A), risking operator safety and system interference. Advanced valve designs reduce turbulence, control closure impact, and maintain flow stability even at velocities above 3 m/s and pressures up to 50 bar.
- Contoured flow paths reduce turbulence and aerodynamic noise by up to 40% in systems operating above 3 m/s velocity
- Spring-loaded poppets with radial guides prevent high-frequency vibration above 1,000 Hz during transient flow conditions
- Valves with Cv ≥ 10 enable high flow rates at minimal differential pressure, reducing jet velocity and noise
- Elastomeric seat cushions dampen closing forces up to 70%, minimizing mechanical impact sounds
- Internal polymer liners combined with 316 stainless steel bodies reduce acoustic transmission in systems up to 50 bar
Valve springs must be engineered with precise wire diameter, pitch, and material properties to withstand millions of cycles without fatigue failure. Using high-grade alloys like Inconel X-750 or stainless steel reduces creep and stress relaxation under dynamic loads. Incorrect spring tension can cause valve flutter or premature wear of seals and seats. Optimized spring geometry also minimizes resonance with system pulsations, extending valve life significantly.
Flow-induced vibration generates oscillatory forces that accelerate wear on valve seats, especially at turbulent high Reynolds numbers (>10,000). This vibration can cause micro-pitting and crack propagation in soft sealing materials like PTFE or rubber. Valves incorporate flow straighteners or streamlined internals that reduce turbulence intensity to mitigate this. Material selection for seats often includes hardened alloys or composite coatings to resist erosion.
Thermal gradients create differential expansion between valve components, leading to seal gap variations and potential leakage. Materials with matched coefficients of thermal expansion (CTE) minimize distortion across temperatures ranging from -40°C to 200°C. Advanced designs use floating or spring-loaded seats that adapt dynamically to thermal movement. Without such features, thermal cycling can cause seal fatigue and early failure.
Cracking pressure calibration depends on precise spring preload and disc weight, set during manufacturing with tolerance under ±3%. Over time, fatigue and material creep can alter spring tension, shifting cracking pressure by up to 10%. Regular maintenance and replacement of springs or seals restore original performance in critical systems. Some valves integrate adjustable spring mechanisms to fine-tune cracking pressure in the field.
Multi-stage valves employ sequential sealing elements or dual poppets to open and close gradually, smoothing flow transitions. This staged action reduces hydraulic shock, pressure surges, and water hammer effects that single-stage valves cannot mitigate effectively. Distributing load across multiple seals reduces wear and increases valve longevity and dynamic pressures. These valves are preferred in rapid start-stop cycles or highly pulsatile flow. applications
We'd love to Manufacture for you!
Submit the form below and our representative will be in touch shortly.
LOCATIONS
Registered Office
10-A, First Floor, V.V Complex, Prakash Nagar, Thiruverumbur, Trichy-620013, Tamil Nadu, India.
Operations Office
9/1, Poonthottam Nagar, Ramanandha Nagar, Saravanampatti, Coimbatore-641035, Tamil Nadu, India. ㅤ
Other Locations
- Bhilai
- Chennai
- USA
- Germany