The Power of Plastic Injection Molding for Your Business
Markets are competitive, businesses are constantly seeking ways to improve efficiency, reduce costs, and deliver high-quality products. One manufacturing process that stands out for its ability to meet these needs is plastic injection molding. This versatile technique offers many benefits that can transform your business operations.
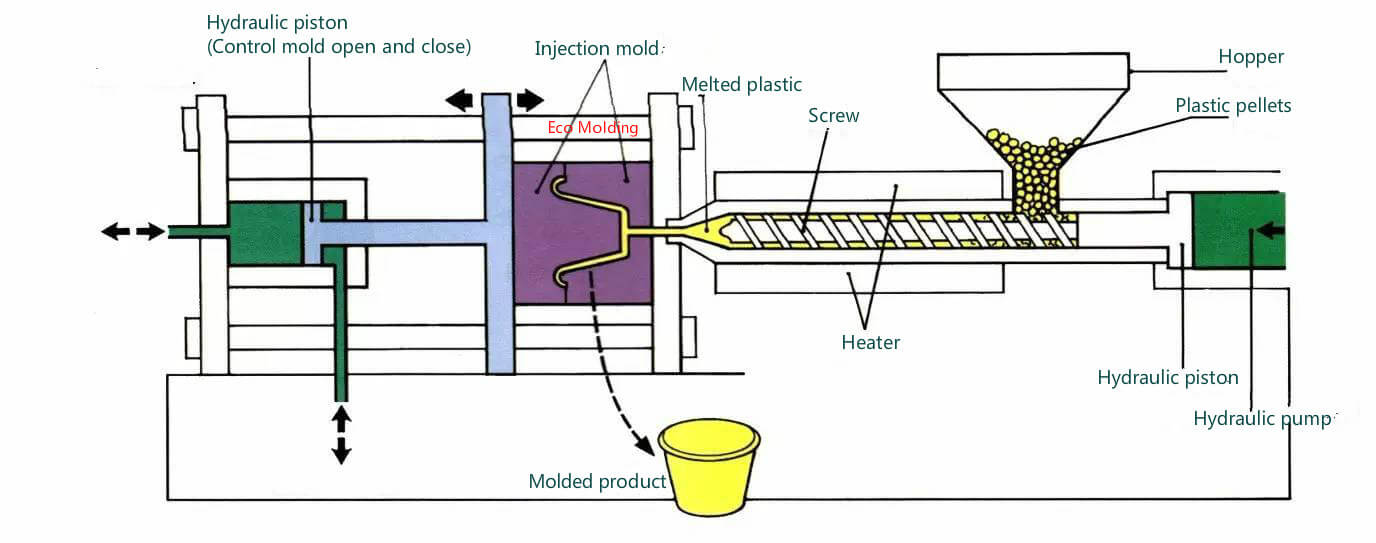
Mass Production Made Easy
At the core of plastic injection molding lies its exceptional capability for mass production. Imagine needing thousands of identical parts for your product. With injection molding, molten plastic is precisely injected into a mold cavity, creating a consistent and repeatable outcome. This eliminates the inconsistencies and limitations of manual production, ensuring a steady stream of parts to meet your business demands.
Unleashing Design Flexibility
Plastic injection molding isn’t just about churning out identical parts. The process boasts remarkable design flexibility, allowing you to create intricate and complex shapes with ease. Unlike some manufacturing methods, injection molding isn’t limited by simple geometries. This opens doors for innovative product design, giving you the freedom to bring your unique concepts to life.

Cost-Effective Manufacturing
When it comes to cost-effectiveness, plastic injection molding proves to be a winner. While the initial investment in mold creation can be significant, the benefits over time outweigh the upfront cost. Injection molding allows for rapid production of large quantities at a lower per-unit cost compared to manual or alternative methods. Furthermore, minimal material waste contributes to overall cost savings.
Delivering High-Quality Products
Every business strives to deliver high-quality products to its customers. Plastic injection molding is renowned for its precision and consistency, resulting in parts with exceptional uniformity and dimensional accuracy. This translates to reliable products that function flawlessly and meet your customers’ expectations.
Rapid Prototyping for Faster Development
The road to product development can be long and arduous. Plastic injection molding offers a solution through rapid prototyping. By creating functional prototypes quickly and efficiently, you can test and refine your designs before committing to mass production. This significantly reduces development time and allows you to bring your product to the market faster.
Producing Complex Parts with Precision
Many products require intricate and complex parts. Plastic injection molding excels in this area. The process can handle a wide range of complexities, including tight tolerances, thin walls, and intricate details. This makes it ideal for a vast array of industries, from automotive and electronics to medical devices and consumer goods.
Optimizing Lead Times with Efficiency
Lead times can be a major bottleneck in product development and manufacturing. Plastic injection molding streamlines the process, significantly reducing lead times compared to traditional methods. The ability to produce parts quickly and efficiently ensures you can meet tight deadlines and deliver products to your customers on time.
Material Selection for Diverse Applications
A significant advantage of plastic injection molding is the vast array of material selection available. From robust and durable plastics to lightweight and flexible options, there’s a material perfectly suited for your specific application. This allows you to tailor the properties of your parts to meet the functional and aesthetic needs of your product.
Customization Options for a Unique Brand Identity
Don’t settle for generic products. Plastic injection molding allows for a high degree of customization. You can incorporate logos, branding elements, and even specific colors into your parts, creating a unique and recognizable brand identity. This level of customization fosters brand recognition and sets your products apart from the competition.
Durability that Stands the Test of Time
The parts produced through plastic injection molding are known for their exceptional durability. The high-quality materials and precise manufacturing process result in parts that can withstand wear and tear, ensuring your products have a long lifespan. This translates to satisfied customers and a positive brand reputation.
Partnering with Frigate for Your Plastic Injection Molding Needs
Plastic injection molding offers a powerful combination of efficiency, quality, and versatility. If you’re looking to streamline your manufacturing process, reduce costs, and deliver high-quality products, then plastic injection molding might be the perfect solution for your business.
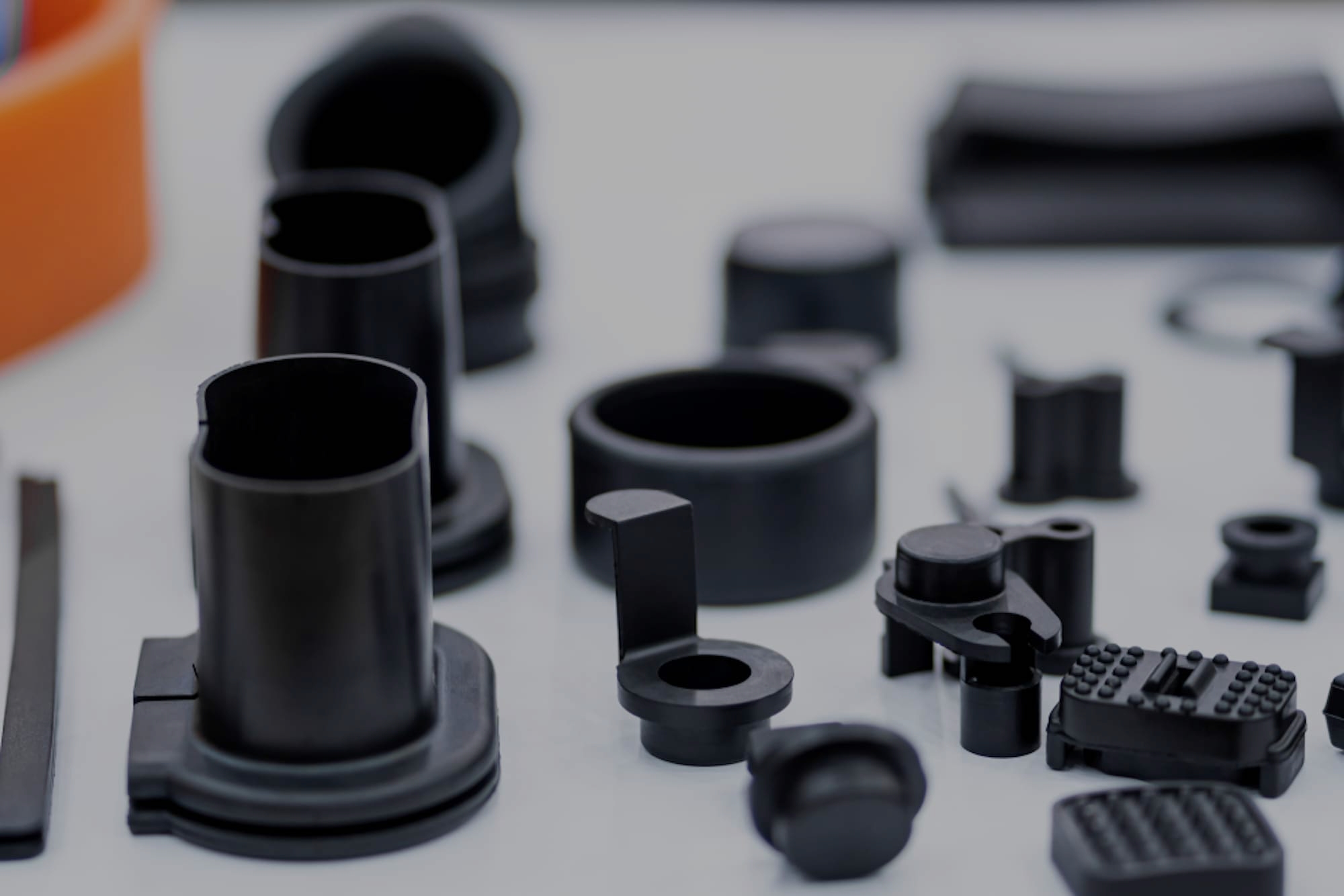
Frigate isn’t just another injection molding company. We understand the unique challenges and opportunities that businesses face in today’s competitive landscape. Our team of experienced professionals provides you with comprehensive support throughout the entire injection molding process.
From the initial design phase to high-volume production, Frigate is your one-stop shop for all your injection molding needs. We offer,
- Mold creation- We utilize cutting-edge technology and highly skilled Moldmakers to create high-quality, durable molds that can withstand the rigors of mass production.
- Material selection- Our team will help you select the perfect plastic material for your application, considering factors like strength, flexibility, heat resistance, and chemical compatibility.
- Production expertise- Our state-of-the-art injection molding machines and experienced operators ensure consistent, high-quality parts are produced efficiently, meeting your exact specifications and lead time requirements.
- Quality control- We maintain a rigorous quality control program to ensure every part meets your standards and specifications. This minimizes defects and ensures your products deliver exceptional performance.
Partnering with Frigate for your injection molding needs offers several advantages
- Reduced costs- Through efficient production processes and minimal material waste, we can help you achieve significant cost savings compared to alternative manufacturing methods.
- Faster time-to-market- Our expertise in rapid prototyping and efficient production helps you bring your products to market faster, giving you a competitive edge.
- Improved product quality- Our commitment to quality ensures you receive consistent, high-quality parts that enhance the functionality and longevity of your products.
- Enhanced scalability- Injection molding is ideal for both low-volume and high-volume production runs. As your business grows, Frigate can scale up production to meet your increasing demands.
Don’t settle for anything less than the best. Contact Frigate today and discover how our comprehensive injection molding services can revolutionize your business. We are confident that we can help you achieve your manufacturing goals and deliver exceptional products to your customers.