How many companies have seen their bottom line suffer due to inefficiencies in HDPE molding production? Lead time issues are often overlooked but pivotal factors that impact everything from production costs to client relationships. The complexity of HDPE (High-Density Polyethylene) molding involves high precision in materials, machinery, and processes. However, most businesses face persistent HDPE molding problems that result in extended lead times, missed deadlines, and inflated costs. These issues, if unresolved, can severely disrupt the manufacturing supply chain, slow down time-to-market, and erode profitability.
By addressing these core problems, businesses can mitigate lead time delays, streamline operations, and ensure high-quality, cost-effective production. Let’s delve into these HDPE molding problems, explore their root causes, and outline actionable solutions that can drastically reduce lead time while maintaining the necessary product quality.
The Deep-Rooted Causes of Lead Time Delays in HDPE Molding
Dissecting the multiple factors contributing to lead time delays is essential to effectively address HDPE molding problems. These are not merely operational issues but interconnected and require a comprehensive approach.
Raw Material Sourcing and Management Challenges
While HDPE is widely used due to its excellent chemical properties and high strength-to-density ratio, the material presents significant challenges in large-scale molding. The sourcing of HDPE material is often delayed due to supply chain disruptions, fluctuations in raw material availability, and quality control issues.
For instance, HDPE molding problems arise when the grade of polyethylene required for specific applications does not match. Different grades of HDPE exhibit distinct melting points, tensile strength, and molding flow characteristics. Supply chain issues, exacerbated by global disruptions in recent years, may also lead to stockouts or delays in obtaining high-quality polyethylene, further impacting production timelines.
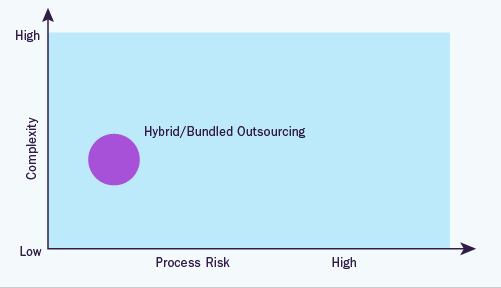
Solution
Manufacturers must establish long-term, reliable partnerships with trusted suppliers to counteract these challenges. Additionally, implementing real-time material tracking and AI-based forecasting tools can help mitigate risks by anticipating potential shortages and adjusting procurement schedules accordingly.
Molding Equipment and Machine Efficiency
A significant cause of delays stems from inefficiencies in the molding equipment itself. Many manufacturers continue to use outdated machines, unable to leverage technological advancements in speed, precision, and automation. Aging machines can suffer from unpredictable downtime, prolonged cycle times, and maintenance issues that disrupt production flow.
Further, HDPE molding problems can occur when machines are not optimized for specific material characteristics, leading to inconsistent part quality, higher rejection rates, and longer cycle times. This problem is compounded when the machines are not fitted with data collection or monitoring systems, preventing real-time performance analysis and predictive maintenance.
Solution
Advanced injection molding machines, equipped with automated mold changeover capabilities and real-time data analytics, can improve cycle time efficiency by 30% (source: The Machinery Research Institute). Additionally, predictive maintenance powered by machine learning algorithms can proactively identify potential failures, reducing downtime by 20% and extending the equipment’s lifespan.
Molding Design Complexity and Tooling Constraints
Another significant challenge with HDPE molding problems involves the increasing complexity of designs. Clients often request intricate shapes, thin walls, and multi-material parts, which strain the tooling and molding process immensely. These complex designs require advanced molding tools and higher precision, increasing tooling lead times and additional setup time.
Moreover, designing and maintaining molds for specialized applications (such as automotive or medical device components) requires significant expertise and frequent mold adjustments. This results in a bottleneck that compounds lead time delays and requires skilled labor to handle these complex operations, increasing overall costs.
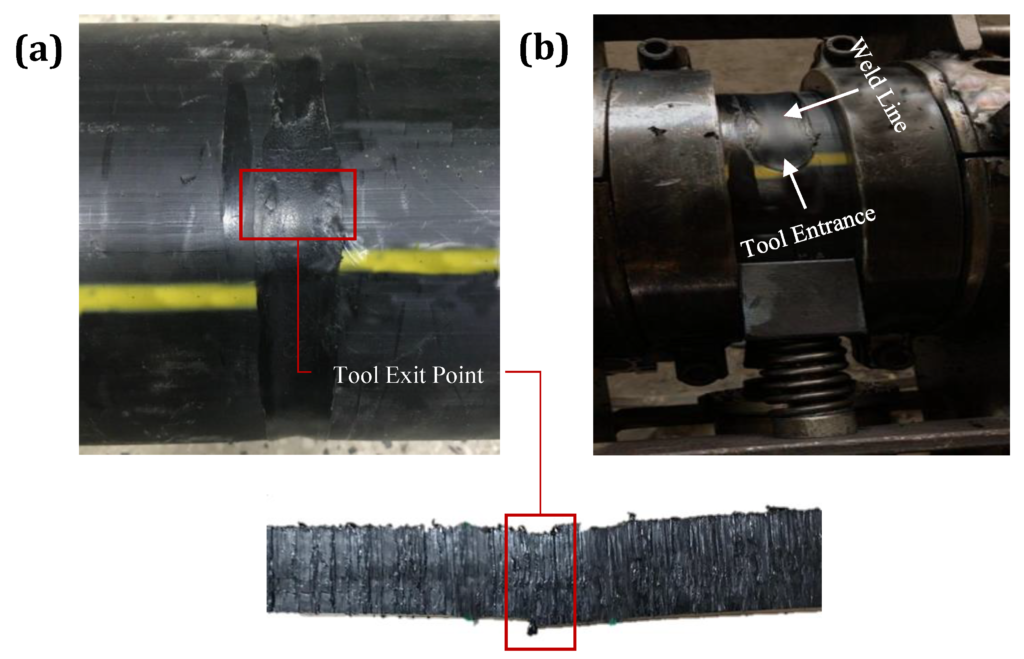
Solution
Manufacturers can speed up the design and production stages by adopting modular tooling systems and automating the mold design phase through CAD (Computer-Aided Design) integration. Rapid prototyping technologies such as 3D printing can also be leveraged for faster mold iterations, reducing mold development time by as much as 40%.
Process Variability and Lack of Optimization
Process variability is a core reason behind HDPE molding problems that extend lead times. Variability can arise at any stage—whether during material preparation, injection molding, or post-processing. Even slight temperature control, injection pressure, or cooling time inconsistencies can lead to defects, part warping, or dimensional inaccuracies.
Despite significant advancements in molding technologies, the lack of comprehensive process optimization leads to cycle times and quality management inefficiencies. With legacy systems or manual oversight, ensuring consistent process control across all production runs becomes increasingly difficult, further extending lead times.
Solution
One of the most effective ways to reduce process variability is to implement Statistical Process Control (SPC) systems to monitor and regulate key variables in real-time. Through continuous data collection, SPC ensures that all molding parameters are maintained within optimal ranges, significantly reducing defect rates and material waste and shortening lead time.
Lack of Real-Time Data and Integration Between Processes
Lead time increases in the absence of effective integration between production stages, such as material handling, injection molding, and post-molding finishing. Communication breakdowns between departments and poor data flow result in missed production targets and poor alignment between manufacturing resources and schedules.
The lack of integration between enterprise resource planning (ERP) systems and molding machines causes even minor adjustments to cause significant delays. Manual intervention often becomes necessary, leading to increased human error and inefficiencies.
Solution
The solution implements a fully integrated manufacturing system that connects design, procurement, molding, and post-processing functions. IoT-enabled machinery and an advanced ERP platform can facilitate seamless information exchange, allowing for better planning, fewer delays, and improved decision-making.
Technologies to Overcome HDPE Molding Problems
To combat these multifaceted HDPE molding problems, it is imperative to adopt cutting-edge technologies that reduce lead time while ensuring precision and consistency. Below are the high-level technologies that address these challenges:
Additive Manufacturing for Mold Development
For low-volume, high-complexity parts, additive manufacturing (3D printing) of molds can drastically reduce lead times compared to traditional tooling methods. This approach enables manufacturers to produce functional molds for testing quickly, speeding up the prototyping phase and reducing tooling costs.
Moreover, 3D printing can produce molds with intricate geometries that traditional machining cannot achieve, which is especially beneficial for HDPE molding, where precision is critical.
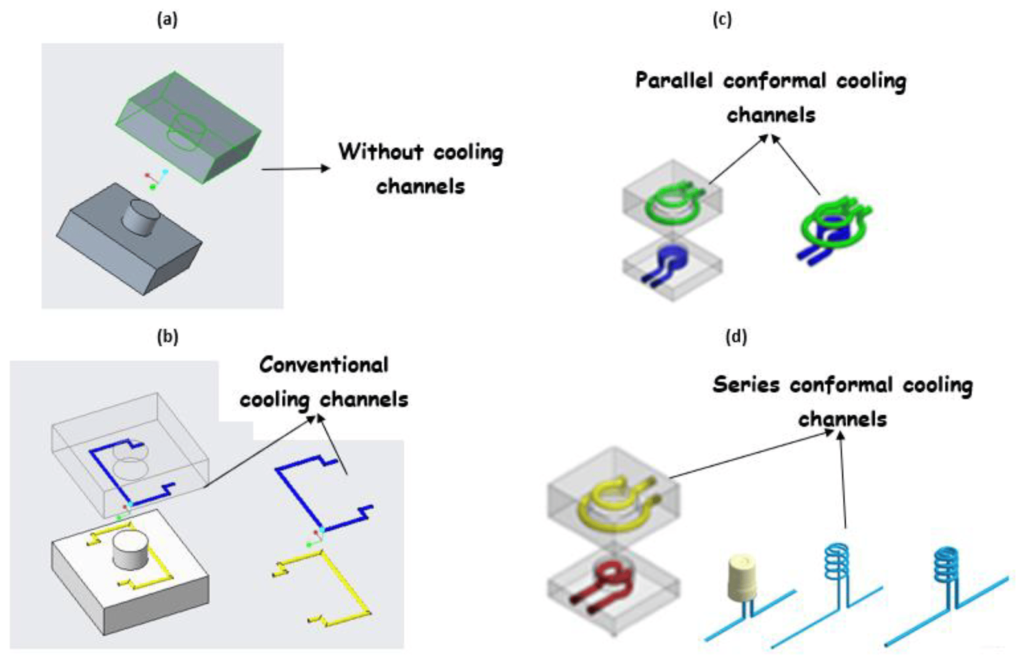
Machine Learning for Predictive Maintenance
Machine learning algorithms can analyze historical machine data to predict potential failures before they occur, optimizing maintenance schedules and reducing downtime. This predictive maintenance approach reduces lead time by up to 20% and ensures that machines operate at peak efficiency without unexpected breakdowns.
Digital Twin Technology
Digital twin technology allows manufacturers to create a virtual model of the molding process, simulating various operational scenarios. Manufacturers can optimize the molding process by testing different process parameters in the virtual environment without physically reworking the equipment or setup. This approach minimizes the trial-and-error phase and accelerates time-to-market.
Real-Time Data Analytics and IoT Integration
With IoT sensors embedded in machines, real-time data can be collected and analyzed to monitor every aspect of the molding process—from material temperature to machine pressure. This continuous data stream allows for immediate process adjustments, reducing the chances of defects and enabling faster decision-making.
How Frigate Tackles Common HDPE Molding Problems?
At Frigate, we tackle HDPE molding problems by applying innovative, advanced technologies and streamlined systems that enhance efficiency, reduce lead times, and ensure high-quality outputs. Here’s how we do it:
Advanced Automation and Robotics for Optimized Production Cycles
Frigate uses fully automated injection molding machines equipped with robotic part removal and real-time cycle time adjustments. Machine learning algorithms continuously optimize parameters to maintain cycle time and quality, reducing human error and material waste. This automation accelerates production, cutting lead times by up to 25% without compromising quality.
AI-Driven Process Optimization for Predictive Maintenance and Quality Assurance
Frigate integrates AI into our molding process to monitor KPIs in real-time, enabling predictive maintenance. AI anticipates equipment failures before they occur, reducing downtime and ensuring consistent product quality. Our AI-driven system also adjusts processing parameters on the fly, minimizing defects and material wastage and enhancing uptime by 30%.
AI-Integrated Supply Chain and Real-Time Material Tracking
We utilize AI-powered supply chain management to forecast demand and mitigate disruptions. Our system tracks material availability in real time, ensuring steady access to high-quality HDPE and continuous production flow. This reduces material sourcing delays and supports uninterrupted production schedules, ensuring on-time delivery despite global supply chain fluctuations.
Modular Tooling Systems and Advanced Mold Design Capabilities
Frigate accelerates mold design with modular tooling systems and 3D printing. Rapid prototyping and tooling adjustments reduce development time by 40%. This allows us to quickly adapt to custom HDPE molding requests, minimizing lead times and enabling faster production of specialized parts with a 30% reduction in custom order turnaround.
Real-Time Data Integration and Smart Manufacturing Systems
Frigate’s IoT-enabled machines collect real-time data across the molding process and integrate it into a central monitoring system. This allows for immediate adjustments, improves process accuracy, and identifies bottlenecks early. Our Big Data integration ensures that production schedules are optimized, reducing lead time by 20% and enhancing overall production efficiency.
Conclusion
In the highly competitive manufacturing landscape, lead time is often the deciding factor in success. Businesses can streamline their operations, reduce costs, and significantly improve product quality by addressing HDPE molding problems with cutting-edge technology, integrated systems, and optimized processes.
Contact us today to learn how we can optimize your HDPE molding processes and accelerate your production timelines.