Forging is a crucial process that shapes metal by applying pressure, creating strong and durable components. However, many companies encounter significant challenges with poor design choices that lead to waste, defects, and weak parts. These issues can be especially frustrating when there are tight deadlines and high production costs.
Therefore, understanding the design considerations for forging is essential for creating effective and efficient components. This blog will explore key aspects of design Therefore, understanding the design considerations for forging is essential for creating effective and efficient components. And illustrate how these elements impact forged products across various industries.
Material Selection and Its Impact on Design
Choosing the right material is one of the most critical design considerations for forging. Common materials used in forging include steel, aluminum, and titanium, each possessing unique properties that can greatly affect the design.
- Steel: Known for its high strength, toughness, and wear resistance, steel is often the material of choice for various forging applications. Different steel grades, such as carbon steel and alloy steel, have specific characteristics that influence their suitability for particular applications. For example, high-carbon steel offers excellent hardness but may be more brittle, while low-carbon steel provides good ductility but lower strength.
- Aluminum: Aluminum is lightweight and corrosion-resistant, making it ideal for aerospace and automotive applications. Its lower density allows for weight savings, which can enhance fuel efficiency. However, aluminum has lower strength than steel, so designers must carefully consider wall thickness and overall geometry to maintain structural integrity.
- Titanium: Titanium is prized for its high strength-to-weight ratio and excellent corrosion resistance. However, it is more expensive than both steel and aluminum. Because of its special qualities can be used in high-performance industries like the medical and aeronautical ones. The design considerations for forging must account for titanium’s higher forging temperatures and potential for work hardening during deformation.
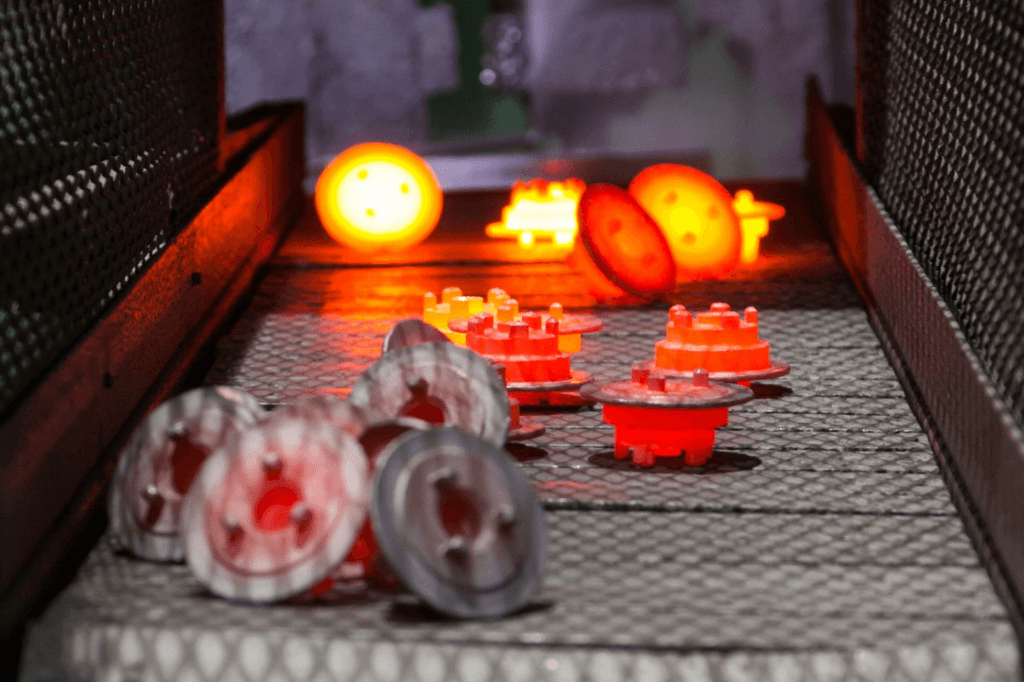
Selecting the appropriate material directly influences the component’s strength, durability, and performance in its intended application. Studies show that using the correct alloy can improve strength by up to 30%, highlighting the importance of material selection in the design process.
Design Geometry: Shape and Size Considerations
The geometry of a forged component significantly impacts its performance and manufacturability. Careful consideration of shape and size during the design phase can enhance performance while reducing costs.
Shape Complexity
While complex shapes may appear desirable for aesthetic or functional reasons, they can complicate the forging process. Intricate designs can increase costs due to higher tooling requirements and longer production times. A simpler design is often more efficient, leading to fewer defects and reduced machining time. For example, a crankshaft used in engines must be carefully designed to accommodate specific dimensions and curves to function correctly. A well-optimized crankshaft can improve engine performance by up to 15%.
Size Considerations
The size of the component affects the choice of forging type and the amount of material required. Larger components may require open-die forging, while smaller parts with precise shapes are best suited for closed-die forging. Additionally, designers must consider the effects of shrinkage and distortion during the cooling process. Designing with optimal geometry ensures the forging process runs smoothly and efficiently, avoiding unnecessary material waste.
Tolerances and Dimensional Accuracy
Tolerance refers to the allowable variations in the dimensions of a forged part. They are crucial for ensuring that components fit together correctly. Poor tolerance can lead to assembly issues, increased costs, and reduced performance.
Setting Proper Tolerances
Setting the right tolerances is one of the critical design considerations for forging. Tighter tolerances often lead to higher production costs due to increased machining and inspection requirements. However, for high-precision applications, such as medical devices, tolerances may need to be stringent to ensure functionality and safety.
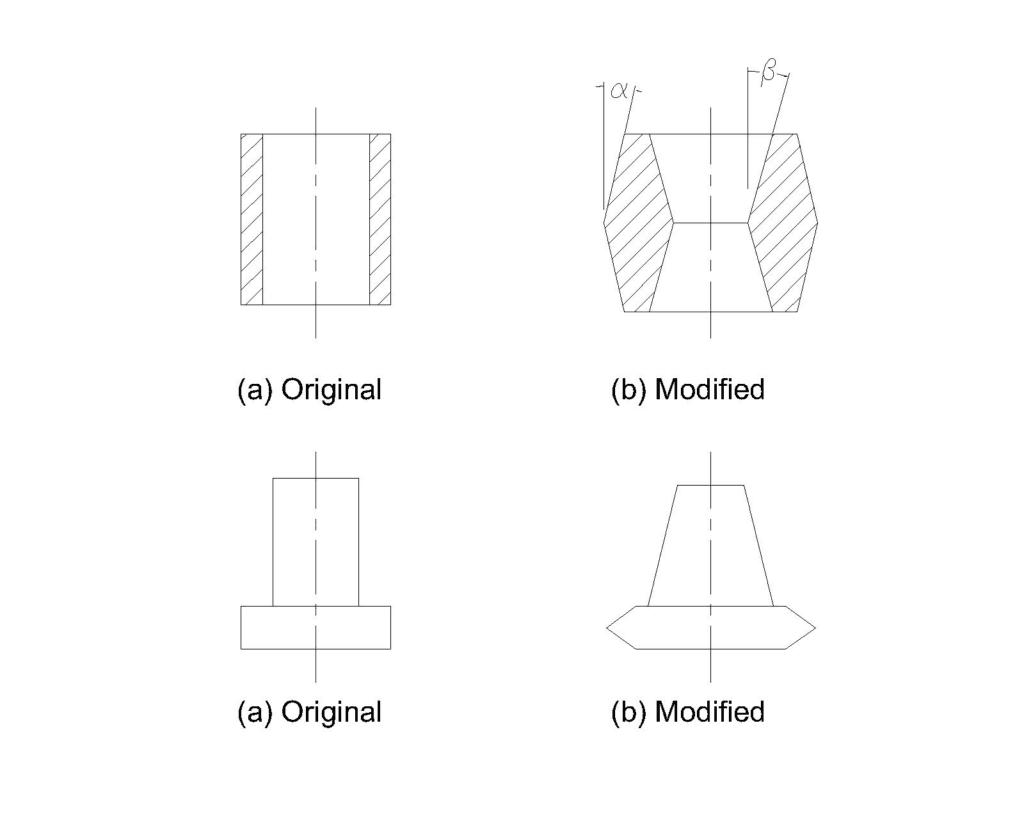
Industry-Specific Examples
For instance, components used in aerospace applications must meet strict dimensional tolerances to ensure safety and performance. Studies indicate that components with precise tolerances can enhance performance and reliability by 25%. Conversely, looser tolerances may be acceptable in industries where components are less critical, like construction, allowing for reduced costs.
Balancing Cost and Accuracy
Designers must understand the balance between cost and accuracy. Implementing advanced inspection technologies, such as coordinate measuring machines (CMM), can help achieve tighter tolerances without significant cost increases.
Draft Angles and Wall Thickness
Draft angles and wall thickness are critical design considerations for forging that affect manufacturability and performance.
Draft Angles
Draft angles are slight slopes added to the walls of a forged part. They facilitate the easy removal of the part from the die without damaging it. Insufficient draft angles can lead to difficulties during ejection, causing defects or even failure of the die.
The recommended draft angle varies by material and part geometry but typically ranges from 1 to 5 degrees. Increasing the draft angle can enhance the manufacturability of complex shapes, ensuring that parts are released smoothly from the dies.
Wall Thickness
Wall thickness is another important consideration that impacts the strength and weight of the forged component. Thicker walls can provide greater strength but add weight, which is particularly critical in industries like automotive and aerospace.
Weight Reduction in the Automotive Industry
Weight reduction is crucial for improving fuel efficiency and performance in the automotive industry. A lighter vehicle can enhance fuel efficiency by up to 10%. Designers must focus on achieving optimal wall thickness while maintaining strength. Techniques such as hollow sections or strategically placed material can achieve this balance.
Finishing Processes and Surface Quality
The surface finish of a forged component significantly impacts its performance, particularly in applications subject to friction, wear, and fatigue. The design must consider the required surface finish to avoid complications later.
Surface Finish Requirements
Surface roughness affects friction and wear properties. Parts with a rough surface may experience higher friction, leading to accelerated wear and potential failure. Designers should specify surface finish requirements early in the design process to avoid additional machining or polishing later.
Post-Forging Processes
Post-forging processes such as machining, shot blasting, or polishing can improve surface quality and increase costs and lead times. The choice of finishing process should be aligned with the component’s design requirements and intended application.
Stress Analysis and Design Validation
Stress analysis is an essential part of the design process. It helps engineers understand how a forged part will react under load. This analysis is crucial for ensuring a component can withstand the forces it encounters in real-world applications.
Importance of Stress Analysis
Finite Element Analysis (FEA) is a common tool for stress analysis. It allows designers to simulate loads on a part and identify potential weak points in the design. This proactive approach can prevent costly failures in production or during the component’s use.
Reducing the Risk of Failure
For instance, using FEA to analyze a forging design can reduce the risk of failure by up to 40%. By validating designs through stress analysis, manufacturers can ensure that components meet performance requirements and industry standards.
Implementing Stress Analysis Early
Incorporating stress analysis early in the design phase allows for adjustments before forging begins, reducing the likelihood of costly errors later.
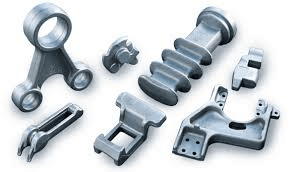
Industry-Specific Design Considerations for Effective Forging
Different industries have unique requirements that significantly influence the design considerations for forging. Understanding these specific needs is crucial for creating effective forged components that perform optimally and comply with industry regulations and standards. Below are detailed insights into the design considerations for forging relevant to three key industries: aerospace, automotive, and medical devices.
Aerospace Industry
The aerospace industry has stringent requirements due to the critical nature of components used in aircraft and spacecraft. The safety and reliability of these components are paramount, leading to unique design considerations:
Weight Reduction
- Importance: Weight is a significant factor in aerospace design. Reducing weight directly impacts fuel efficiency and payload capacity. Even small reductions can yield substantial cost savings over an aircraft’s lifetime.
- Design Implications: Designers often use advanced materials such as titanium and aluminum alloys, which provide high strength-to-weight ratios. The choice of material must also consider the forging process to retain the desired properties.
- Optimization Techniques: Techniques like topology optimization can help identify material layouts that reduce weight while maintaining structural integrity. For instance, using lattice structures or hollow sections in design considerations for forging can achieve considerable weight savings without compromising strength.
High-Temperature Performance
- Challenges: Components in aerospace applications are often subjected to extreme temperatures and pressures, especially in engines and turbine assemblies.
- Material Selection: Choosing materials that can withstand high temperatures without losing mechanical properties is essential. Superalloys and advanced ceramic composites are commonly used for high-temperature applications due to their excellent thermal stability and strength.
- Thermal Analysis: During the design phase, thermal analysis helps predict how materials will behave under operational conditions, enabling designers to make informed choices about material and design.
Fatigue Resistance
- Criticality: Aircraft components experience repeated loading and unloading cycles, making fatigue resistance a key design consideration.
- Stress Analysis: Utilizing Finite Element Analysis (FEA) can identify areas susceptible to fatigue failure. Designers can implement design modifications such as fillets and radii to reduce stress concentrations, enhancing fatigue life.
- Testing Standards: Components must meet rigorous fatigue testing standards set by regulatory bodies, such as the FAA (Federal Aviation Administration) and EASA (European Union Aviation Safety Agency), which dictate design safety factors.
Automotive Industry
High production volumes and the need for cost-effective manufacturing processes characterize the automotive sector. Design considerations for forging in this industry often focus on performance, safety, and manufacturability.
Impact Resistance
- Safety Requirements: Components like axles, crankshafts, and suspension parts must be designed to absorb and withstand impacts, especially in crash scenarios.
- Material Properties: High-strength steel or alloy steels are often preferred for their ability to resist deformation and failure under load. These materials can undergo heat treatment processes to enhance toughness and yield strength.
- Simulation and Testing: Conducting impact simulation tests helps evaluate how well components will perform in real-world scenarios. Adjustments can be made in the design considerations for forging to improve impact resistance where necessary.
Precision and Tolerances
- Assembly Fit: Forged components in automotive applications must fit together with high precision to ensure efficient assembly and operation.
- Design Considerations: Setting appropriate tolerances during the design phase is critical. Tighter tolerances may be necessary for components that engage directly with others, such as gears and bearings.
- Statistical Process Control: Implementing statistical process control (SPC) techniques can monitor the manufacturing process to maintain required tolerances and ensure consistent quality.
Cost Efficiency
- Production Techniques: The automotive industry often employs high-volume production techniques such as closed-die forging to minimize costs while maintaining quality.
- Material Utilization: Effective design must also focus on material utilization. Reducing scrap during the forging process saves costs and minimizes waste, aligning with sustainability goals.
- Lifecycle Cost Analysis: Designers should conduct lifecycle cost analysis to understand the long-term implications of design decisions, factoring in production, maintenance, and replacement costs.
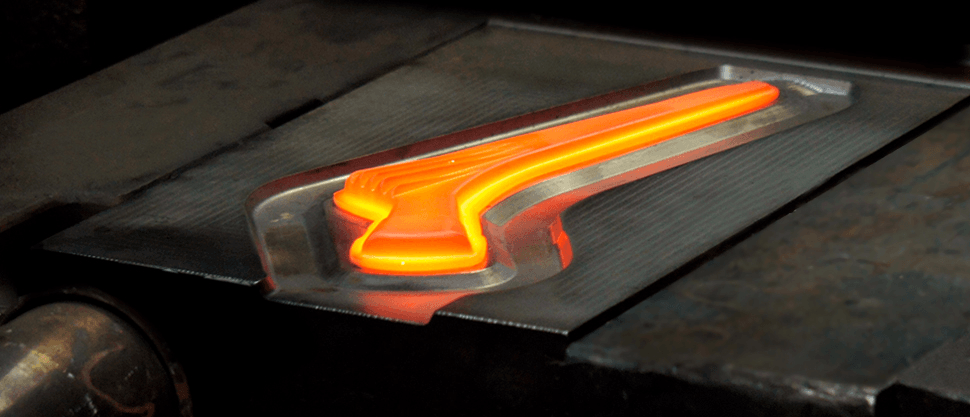
Medical Devices
Strict regulations govern the medical device industry to ensure the safety and efficacy of components. Designing forged components for medical applications requires a unique focus on precision, biocompatibility, and compliance.
Precision Engineering
- Critical Tolerances: Medical devices often require precise dimensions, especially for components like surgical instruments or implants.
- Machining and Finishing: Designers must account for post-forging machining processes to achieve tolerances and surface finishes. This may include CNC machining or polishing to meet specific regulatory requirements.
- Measurement Techniques: Advanced measurement techniques such as laser scanning or optical inspection can be employed to verify dimensional accuracy, ensuring compliance with medical standards.
Biocompatibility
- Material Selection: Materials used in medical devices must be biocompatible to avoid adverse reactions when implanted in the body. Common materials include titanium, stainless steel, and certain polymers.
- Regulatory Standards: Compliance with standards such as ISO 10993 is essential, dictating materials testing for cytotoxicity and other biological effects.
- Design Considerations: Designers must consider the surface finish and geometry of medical components to minimize the risk of infection and facilitate easier cleaning and sterilization.
Regulatory Compliance
- FDA Approval: In the United States, many medical devices require FDA approval, necessitating thorough documentation and testing during the design process.
- Design Controls: Implementing design control processes ensures that every design aspect, from concept to production, is documented and validated according to regulatory standards.
- Quality Management Systems: Adopting a robust quality management system (QMS) helps manufacturers comply with ISO 13485, specifically tailored to the medical device industry.
Conclusion
Design considerations for forging vary by industry. Aerospace prioritizes weight reduction, high-temperature performance, and fatigue resistance. The automotive sector focuses on impact resistance, precision, and cost efficiency, while the medical device industry emphasizes precision, biocompatibility, and regulatory compliance.
Understanding these needs allows manufacturers to produce effective forged components that meet performance standards and regulations. For expert support in optimizing your forging processes, contact Frigate Die Casting Services today!