Aluminum castings have become a root of modern industry, shaping countless applications and driving innovation across diverse sectors. Their unique combination of properties – from exceptional lightweight design to remarkable durability – makes them a highly sought-after material for a wide range of metal components.
But what exactly are aluminum castings, and how do they impact industrial applications? Let’s delve deeper and explore the fascinating world of these versatile components.
From Molten Metal to Manufactured Marvels
Aluminum castings are metal components formed by pouring molten aluminum into a pre-shaped mold. This manufacturing process allows for the creation of complex shapes with exceptional design flexibility. Unlike other metalworking techniques like machining solid blocks of metal, casting offers the advantage of near-net-shape production, minimizing material waste and production time.
There are several types of aluminum casting processes, each with its own advantages and ideal for different production requirements:
- Sand Casting – This traditional method utilizes sand molds, which are relatively inexpensive to create. This makes sand casting a cost-effective option for low-volume production runs or prototypes. However, sand molds are not reusable, so this method is less suitable for high-volume production.
- Die Casting – Ideal for high-volume production runs, die casting utilizes permanent metal dies that can be reused for thousands of castings. This allows for fast production times and consistent part quality. Die casting is well-suited for creating complex shapes with good dimensional accuracy.
- Investment Casting (Lost-Wax) – This process is perfect for intricate and complex shapes, creating high-quality components with a smooth surface finish. Lost-wax casting utilizes a wax pattern that is encased in a ceramic mold. Once the ceramic mold hardens, the wax melts away, leaving a cavity for the molten aluminum. This method is ideal for low to moderate production volumes due to the investment required in creating the wax patterns and ceramic molds.
Aluminum Properties that Power Performance
The unique properties of aluminum make it a excellent choice for a wide range of industrial applications. Here are some key characteristics that contribute to its widespread adoption:
- Lightweight – Aluminum has significantly lower density compared to other commonly used metals like steel. This translates to lighter final products, improving fuel efficiency in transportation applications and reducing overall weight in machinery.
- Durability – Don’t be fooled by its lightness. Aluminum castings offer exceptional durability and corrosion resistance. This makes them ideal for demanding industrial environments.
- Excellent Thermal Conductivity – Aluminum efficiently conducts heat, making it a valuable material for applications requiring heat dissipation, such as engine components and heat sinks.
- Machinability– Aluminum castings are readily machinable, allowing for precise post-processing and customization to meet specific application requirements.
- Recyclability – Aluminum is one of the most recyclable metals, making it an environmentally friendly choice and contributing to sustainable manufacturing practices.
How is Frigate helping various industries?
Frigate revolutionizes industries by providing tailored casting solutions that optimize performance and efficiency. With expertise in aluminum casting, Frigate collaborates closely with clients across diverse sectors, offering innovative solutions to meet their specific needs. From automotive to aerospace and beyond, Frigate’s casting expertise enhances product quality, reduces costs, and drives overall competitiveness in the global market.
Revolutionizing the Automotive Industry – Lighter, Sleeker, Greener
Frigate understands the constant pursuit of efficiency and performance in the automotive industry. We offer a comprehensive suite of aluminum casting solutions specifically tailored to meet the demanding needs of automakers. Our expertise in casting processes like sand casting and die casting allows us to produce high-quality, lightweight components like:
- Engine blocks and cylinder heads – Frigate’s aluminum castings contribute to significant weight reduction in engines, translating into improved fuel efficiency and reduced emissions. Our commitment to quality ensures these castings meet the stringent performance and durability requirements of modern engines.
- Wheels and suspension parts – Lightweight aluminum wheels from Frigate not only enhance a vehicle’s aesthetics but also contribute to better handling and fuel economy. Our suspension components, meticulously crafted using aluminum castings, offer exceptional strength-to-weight ratios, optimizing vehicle performance.

By partnering with Frigate, automotive manufacturers gain access to a reliable source of top-notch aluminum castings that contribute to lighter, sleeker, and more environmentally friendly vehicles.
Reaching to New Heights – Aluminum Castings Take Flight in the Aerospace Industry
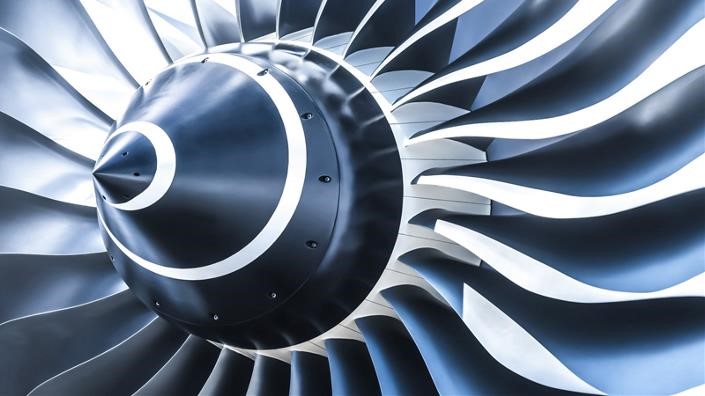
The aerospace industry thrives on innovation and a constant pursuit of lightweight, high-strength materials. Frigate steps in as a trusted partner, providing aluminum casting solutions that meet the rigorous demands of aircraft manufacturing. Our expertise in investment casting (lost wax) allows us to produce intricate and complex aerospace components like:
- Airframes – Frigate’s precisely crafted aluminum castings contribute to the lightweight construction of airframes, maximizing fuel efficiency and flight range.
- Landing gear – Our high-strength aluminum castings ensure the exceptional durability and reliability required for landing gear, a critical component for safe aircraft operation.
By leveraging Frigate’s advanced casting capabilities, aerospace companies can achieve significant weight reduction in their aircraft, leading to improved fuel efficiency, longer flight ranges, and ultimately, a more sustainable air travel experience.
Building on a Solid Foundation – Aluminum Castings for the Construction Industry
The construction industry is constantly seeking innovative materials that offer a balance of lightweight design, durability, and weather resistance. Aluminum castings, expertly crafted by Frigate, provide the perfect solution for a wide range of building applications:
- Window frames and building facades – Frigate’s lightweight aluminum window frames offer several advantages. They reduce strain on building structures, improve energy efficiency, and resist corrosion, ensuring a long-lasting, aesthetically pleasing exterior.
- Roofing components – Our aluminum roof components are not only lightweight but also boast exceptional weather resistance, making them ideal for diverse climates.
By partnering with Frigate, construction companies gain access to high-quality aluminum castings that contribute to lighter, more sustainable, and visually appealing buildings.
Aluminum Castings in Everyday Products
The impact of aluminum castings extends far beyond heavy industries. Frigate’s expertise in aluminum casting finds applications in a surprising range of consumer goods, contributing to both functionality and aesthetics:
- Electronics enclosures – Our lightweight aluminum castings provide a sturdy and reliable housing for electronic devices like laptops and smartphones, while also aiding in heat dissipation.
- Sporting equipment – From baseball bats to bicycle frames, Frigate’s aluminum castings contribute to the lightweight design and superior performance of various sporting equipment.
These are just a few examples of how Frigate’s aluminum casting solutions reach into the everyday lives of consumers, enhancing the design, functionality, and user experience of countless products.
The Future of Aluminum Castings
The future of aluminum castings is bright, with ongoing advancements in casting techniques promising even greater design flexibility and improved performance. Frigate remains at the forefront of this innovation, continuously investing in research and development to explore new aluminum alloys and casting methods. We believe in a collaborative approach, working closely with clients across various industries to develop customized aluminum casting solutions that meet their specific needs and push the boundaries of what’s possible.
Frigate – Your Trusted Partner in Aluminum Casting Solutions
If you’re looking to leverage the power of aluminum castings in your industry, Frigate can be your one-stop shop. We possess extensive experience in all aspects of aluminum casting, from selecting the most suitable process to ensuring the highest quality standards. Our team of experts can guide you through every step of the process, ensuring you receive aluminum castings that meet your exact specifications and contribute to the success of your projects.
Work with Frigate for your next project and Unleash the Potential of Aluminum Castings
The possibilities with aluminum castings are endless. By partnering with Frigate, you gain access to a team of experts who can help you leverage this versatile material to achieve your design goals, enhance product performance, and ultimately, achieve success in your industry. Contact Frigate today to discuss your specific requirements and explore how our aluminum casting solutions can empower your next project.