In manufacturing, companies constantly face pressure to deliver high-quality parts while keeping production costs low and meeting tight deadlines. But when traditional casting methods fall short, they create bottlenecks, drive up costs, and hamper innovation. These issues can result in delays, defects, and, ultimately, lost market share. How can manufacturers overcome these obstacles and maintain a competitive edge?
The answer lies in advanced casting services. These modern methods solve many issues with traditional casting and offer significant advantages that can give businesses an edge in the marketplace. By leveraging competitive casting techniques, companies can improve production efficiency, product quality, and their bottom line. In this blog, we’ll explore how Frigate casting advantages can help manufacturers gain a competitive edge by addressing key pain points.
Why Do Traditional Casting Methods Lead to Increased Production Costs?
While widely used, traditional casting methods come with their own challenges that hinder productivity and quality. From material inefficiencies to long production times, manufacturers often face numerous hurdles when relying on older casting techniques.
One of the primary issues is achieving consistency in the quality of cast parts. Even the smallest variation can result in defects or costly rework in many industries. Additionally, working with traditional casting methods is time-consuming, limiting a company’s ability to meet tight delivery deadlines. Material constraints, inflexible designs, and high production costs also complicate operations. These challenges contribute to significant delays in production and higher costs, which can negatively impact a company’s ability to remain competitive.
Inconsistent Quality and Dimensional Accuracy
One of the biggest challenges with traditional casting methods is achieving consistent quality and precise dimensions. In aerospace, automotive, and electronics industries, the slightest variation in part quality can lead to major issues. Whether it’s a defect in material strength or a dimensional discrepancy, these imperfections can cause parts to fail prematurely, resulting in costly rework and delays.
Long Production Lead Times
Another major pain point is the long production times associated with older casting methods. Traditional methods often fall short when parts need to be produced quickly to meet deadlines, causing supply chain disruptions. Companies that can’t meet customer demand promptly risk losing business to competitors with more efficient processes.
Limited Material and Design Flexibility
Many traditional casting methods also limit material choices and design complexity. This can be a significant drawback when manufacturers need to work with new, advanced materials or create parts with intricate designs. The lack of flexibility in material selection can also prevent manufacturers from optimizing product performance.
Cost Overruns and Inefficiencies
Lastly, traditional casting processes often involve higher material waste and energy consumption, increasing costs. Whether it’s from inefficiencies in mold preparation or excess scrap, these cost overruns reduce profit margins and make it harder for businesses to stay competitive.
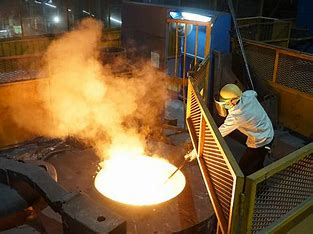
What Benefits Do Advanced Casting Services Offer to Overcome Manufacturing Delays?
Shifting to advanced casting services can resolve many of the pain points that come with traditional methods. Today’s advanced casting techniques are designed to be faster, more cost-effective, and produce higher-quality results with greater precision. These services are tailored to meet the needs of industries that demand fast turnaround times, high tolerances, and complex designs. By adopting advanced methods, manufacturers can meet and exceed customer expectations.
1. Precision and Consistency
One key advantage of advanced casting services is their precision. Modern casting techniques like die casting and precision casting allow for extremely tight tolerances and minimal variation in dimensions. This ensures that parts are consistently high quality, which is essential for industries like aerospace and automotive, where even small defects can lead to failure.
Example:
In die casting, high-pressure molds inject molten metal into a precisely formed mold. This process produces parts with excellent surface finishes and high dimensional accuracy. According to a North American Die Casting Association study, die casting provides tolerances as tight as ±0.005 inches, ensuring parts meet exact specifications with minimal rework.
By using advanced casting services, manufacturers can ensure uniformity across all parts, reducing scrap rates and the need for rework. This not only saves money but also increases product reliability, improving customer satisfaction.
2. Faster Time-to-Market
Time-to-market is crucial in today’s competitive environment. Advanced casting services offer rapid production times compared to traditional methods. For example, die-casting molds can be produced in a matter of days, and parts can be produced in high volumes without sacrificing quality. This is essential when customers need products quickly or when manufacturers face tight deadlines.
With Frigate’s competitive casting solutions, companies can quickly turn prototypes into finished products to meet market demand faster. Faster production means faster delivery to customers, which is a significant advantage in industries like automotive, where time-sensitive components are needed for assembly lines.
3. Material Versatility and Customization
One significant advantage of advanced casting methods is their ability to work with a wide variety of materials. Whether it’s aluminum, zinc, magnesium, or specialized alloys, advanced casting techniques like die casting and sand casting can easily handle different metals. This versatility allows manufacturers to choose the right material for the job, improving product performance.
Additionally, these methods allow for greater design flexibility. Advanced casting processes can produce complex geometries and intricate designs that would be difficult or impossible to achieve with traditional casting. This capability enables manufacturers to create innovative products that meet specific performance requirements.
Example:
Frigate’s casting services offer custom alloy combinations tailored to meet unique performance criteria. Whether you’re designing lightweight components for the aerospace industry or durable parts for heavy machinery, Frigate casting advantages allow for optimized material choices that enhance product longevity and performance.
4. Cost Efficiency Through Streamlined Processes
With traditional casting methods, manufacturers often face inefficiencies in material usage and high energy consumption. Advanced casting methods, on the other hand, are designed to minimize waste and optimize energy usage. For example, die casting minimizes scrap material by ensuring that the mold is filled precisely, reducing the amount of excess material that needs to be recycled.
By leveraging competitive casting, manufacturers can significantly lower production costs. This is particularly beneficial for high-volume production runs, where the cost savings can be substantial. Advanced casting services also streamline the entire production process, reducing the time spent on each part and allowing manufacturers to produce more in less time.
Example:
A study by the Cast Metals Federation found that die casting can reduce material waste by as much as 90% compared to traditional sand casting methods, which translates into cost savings for manufacturers.
5. Improved Product Lifecycle Management
Another crucial factor for manufacturers is the durability of cast parts. Advanced casting services ensure that parts are built to last. With superior material properties and tight tolerances, products produced through advanced casting are less likely to fail prematurely, reducing the need for repairs or replacements. This translates to a longer product lifecycle and lower maintenance costs.
For industries like aerospace, where parts are subjected to extreme conditions, the strength and reliability of cast components are crucial. Advanced casting methods ensure that these parts can withstand the test of time, reducing failure rates and boosting customer confidence.
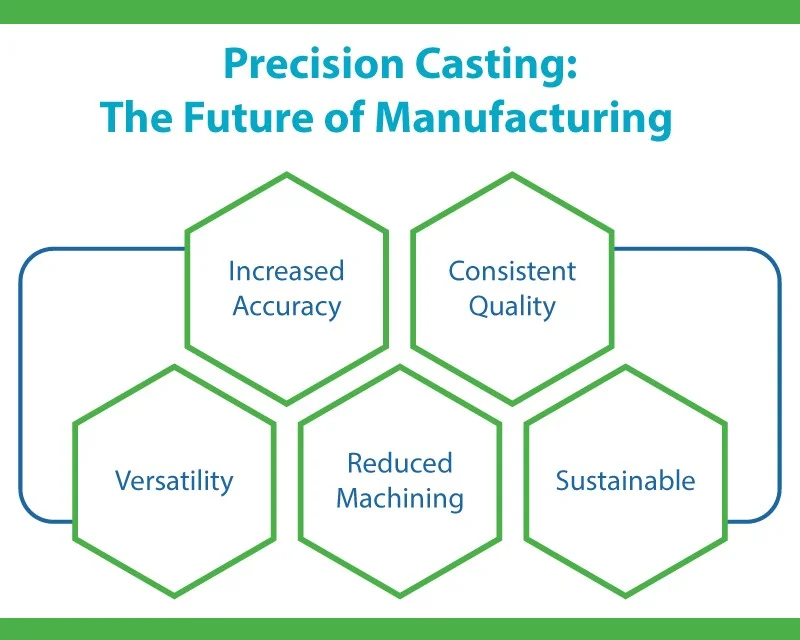
How Can Frigate’s Advanced Casting Capabilities Improve Your Manufacturing Process?
Frigate has invested in a comprehensive set of advanced casting services designed to address the most common challenges faced by modern manufacturers. With extensive experience and expertise in casting technology, Frigate provides highly efficient, precise, and flexible casting solutions to meet the unique needs of various industries.
Advanced Technologies and Equipment
Frigate utilizes the latest casting technologies, including precision, sand, and pressure die casting. These technologies ensure high accuracy, excellent surface finishes, and fast cycle times. Frigate’s advanced equipment allows for the production of parts with minimal variation, ensuring each piece meets the required specifications.
Expertise in Complex Designs
Frigate specializes in handling complex geometries and intricate designs. With the ability to produce parts with tight tolerances and complex shapes, Frigate’s competitive casting solutions help manufacturers create cutting-edge products.
Comprehensive Materials Expertise
Frigate offers casting services for various industries, including various industries, with a wide range of metals and alloys, including aluminum, zinc, magnesium, and specialty materials. Whether you need high-strength components for automotive or lightweight materials for aerospace, Frigate can deliver the right solution for your needs.
Quality Assurance and Precision
Frigate’s advanced quality control processes ensure that every part meets the highest standards. From material testing to dimensional analysis, Frigate takes every step necessary to ensure that products are defect-free and perform reliably in their intended application.
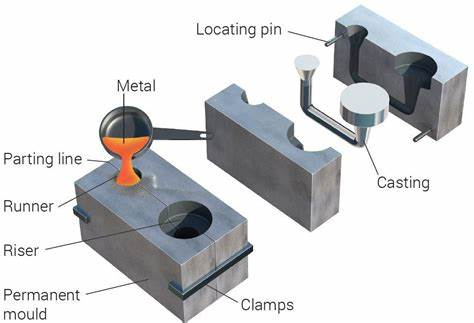
How Can Frigate’s Advanced Casting Services Solve Key Industry Challenges?
Frigate’s advanced casting services address the pain manufacturers often encounter with traditional casting. These services are tailored to improve efficiency, reduce costs, and enhance product quality, providing businesses with the tools to stay competitive.
Reducing Scrap and Rework Costs
One of the most significant advantages of using advanced casting methods is the reduction of scrap and rework costs. Frigate’s casting services produce parts with exceptional dimensional accuracy, minimizing the need for corrections or replacements. This results in lower material waste and fewer delays, directly translating into cost savings.
Shortening Production Lead Times
Frigate’s advanced casting processes are faster and more efficient than traditional methods. Frigate can significantly reduce production lead times using automated equipment and optimized workflows, ensuring that parts are delivered on schedule without compromising quality.
Greater Flexibility to Meet Market Demands
Frigate’s ability to quickly adapt to new material requirements, design changes, and customer specifications provides manufacturers greater flexibility. This ability to pivot and customize solutions ensures businesses can stay ahead of market trends and meet changing customer needs.
Enhancing Product Durability and Performance
Manufacturers can produce more durable parts that are better suited for harsh environments with advanced casting services. For example, aerospace components often require exceptional strength-to-weight ratios, which can be achieved through precision casting. Frigate’s ability to tailor casting methods to meet specific industry needs ensures that parts are built to last.
Conclusion
In today’s competitive marketplace, manufacturing companies need every advantage. By leveraging Frigate casting advantages, manufacturers can reduce costs, improve quality, and speed up production timelines. With advanced casting services, companies can meet the rising demands of modern industries while staying ahead of the competition.
Frigate’s expertise, technology, and commitment to quality provide manufacturers with the tools they need to thrive. If you’re ready to explore how advanced casting services can benefit your business, contact Frigate today for a consultation.